Минералого-технологические особенности и закономерности селективного разрушения железистых кварцитов Михайловского месторождения
Аннотация
Растущая потребность в продукции черной металлургии обуславливает необходимость внедрения технологий, повышающих эффективность обогатительного передела железосодержащего сырья. Перспективным направлением в этой области является внедрение решений, основанных на возможности селективной дезинтеграции руд. Целью данной работы являлось установление закономерностей селективного разрушения железистых кварцитов на основании результатов исследования минералого-технологических свойств сырья. Представлены данные по изучению минералого-технологических особенностей железистых кварцитов Михайловского месторождения методами рентгено-флуоресцентного анализа и автоматизированного минералогического анализа. На основании исследований характера вкрапленности и размеров зерен породных и рудных минералов сформулированы задачи рудоподготовительного передела. В результате изучения измельчения руды установлены параметры распределения железа и оксида кремния по классам крупности в продуктах измельчения. На основании эмпирических зависимостей спрогнозирована крупность измельчения, при которой должно достигаться максимально эффективное раскрытие сростков рудных минералов и их минимальный переход в класс крупности –44 мкм.
Введение
Основной тенденцией, характеризующей развитие мировой железорудной промышленности в последние десятилетия, является несоразмерное с приростом запасов разведанных месторождений возрастание объемов потребления продукции [1-3]. В Российской Федерации по состоянию на 01.01.2021 балансовые запасы железных руд составили 112,4 млрд т, а общие запасы разрабатываемых месторождений – 29,4 млрд т [4]. Соотношение прироста запасов за счет разведки к добыче в 2020 г. составило 0,21 (табл.1). В настоящее время пристальное внимание исследователей привлекают проблемы рационального использования базы железорудного сырья [5] как на этапе горных работ [6-8], так и на стадии металлургии [9-11]. Одним из ключевых факторов повышения эффективности производства остается внедрение цифровых технологий [12-14].
Таблица 1
Состояние сырьевой базы железных руд Российской Федерации в 2018-2020 гг. [4]
Год |
Прирост запасов категорий А + В + С1 за счет разведки, млн т |
Прирост/убыль запасов категорий А + В + С1 за счет переоценки, млн т |
Добыча руды, млн т |
2018 |
22,3 |
1146,6 |
357,3 |
2019 |
59,0 |
–73,8 |
366,0 |
2020 |
37,3 |
80,4 |
376,1 |
Большая часть запасов российской железорудной базы приурочена к месторождениям железистых кварцитов, расположенных в пределах Курской магнитной аномалии. Крупнейшим по запасам является Михайловское месторождение, относящееся к гематит-магнетитовому геологическому типу [15]. Несмотря на высокие объемы запасов руды в месторождениях, около 38 % из них относится к категории С2 [16]. Дополнительно железистые кварциты Михайловского месторождения относятся к труднообогатимым по ряду факторов: высокая крепость руды, абразивность, тесная ассоциация рудных и нерудных минералов [17]. Совокупность данных факторов обуславливает необходимость внедрения технологических решений, повышающих полноту извлечения железа из данных руд [18, 19]. Однако полупромышленные испытания новых технологических решений на обогатительных и металлургических переделах весьма затратны, что вызывает необходимость проведения предварительных комплексных исследований физико-химических свойств сырья.
Различия минералогического состава и текстурно-структурных особенностей железных руд обуславливают вариативность схем обогащения [20]. Основными критериями выбора технологии обогащения являются вещественный состав железных руд, характер вкрапленности компонентов, контрастность разделительных свойств и прогнозируемая эффективность обогатительного передела [21, 22]. На сегодняшний день, помимо основного передела железных руд – магнитного обогащения, применяют комбинированные схемы. Подтвердило свою эффективность применение гравитационного метода обогащения и флотации для доизвлечения железосодержащих минералов из хвостов магнитного обогащения [23, 24].
Перспективным направлением модернизации схем переработки железистых кварцитов является совершенствование технологий рудоподготовки [25, 26]. Стандартным проектным решением является стадиальный вывод немагнитной фракции на дообогащение и доизмельчение магнитной фракции. Основными проблемами в таком случае являются переизмельчение рудных минералов железа и загрязнение концентратов минералами пустой породы вследствие их механического захвата на стадии магнитного обогащения. Значения микротвердости кварца, гематита, магнетита и гидрогетита подтверждают склонность рудных минералов к переизмельчению [27].
Переизмельчение сырья ведет к повышенным энергозатратам и, как следствие, к снижению рентабельности производства концентрата. Решением данной проблемы может служить получение продукта с заданным распределением компонентов по крупности за счет различной скорости разрушения рудных и породных минералов. Данный принцип лежит в основе технологий селективного разрушения [28-30]. Решения в этой области должны быть обоснованы исследованиями минералого-технологических особенностей руды. Основными являются исследования минеральной текстуры: изучение особенностей границ срастания рудных и породных минералов, оценка распределения минеральных зерен по размеру, расчет параметров удельной площади межфазного контакта и трещиноватости [31, 32]. Текстура тесно связана со степенью раскрытия сростков, и, как следствие, с перераспределением химических элементов по классам крупности в процессе рудоподготовки [33, 34].
Таким образом, целью работы являлось установление закономерностей селективного разрушения железистых кварцитов на основании результатов исследования минералого-технологических свойств сырья.
Методология
Объектом исследования являлись пробы богатой руды Михайловского месторождения после мелкого дробления, P80 для исследованной пробы составило 1477,67 мкм. Основными железосодержащими минералами в руде являются магнетит, гематит, мартит, гидроокислы железа, селадонит и сидерит. В зависимости от преобладания одного из компонентов выделяют два технологических типа руд: гематит-магнетитовые и карбонатно-мартитовые. Породообразующие минералы в пробе в основном представлены различными силикатами и карбонатами.
Серии экспериментальных исследований измельчения железистых кварцитов производились в лабораторной шаровой мельнице. Крупность измельчения оценивалась по показателю P80. Исследования были проведены для четырех значений P80: 692,81; 160,08; 124,69; 80,00 мкм. Для исключения случайных ошибок каждый опыт повторялся три раза. Данные по гранулометрическому составу проб и распределению анализируемых компонентов после измельчения были получены путем рассева на ситах с ячейками размерами 2000, 1000, 500, 250, 100 и 44 мкм. Полученные классы взвешивались, после чего из них были выделены представительные пробы для анализа элементного состава. Анализ химического состава исходной пробы и продуктов измельчения проводился на аппарате для рентгенофлуоресцентного анализа EDX 7000 Shimadzu, автоматизированный минералогический анализ осуществлялся на инструментальном автоматическом комплексе MLA 650 (FEI Company).
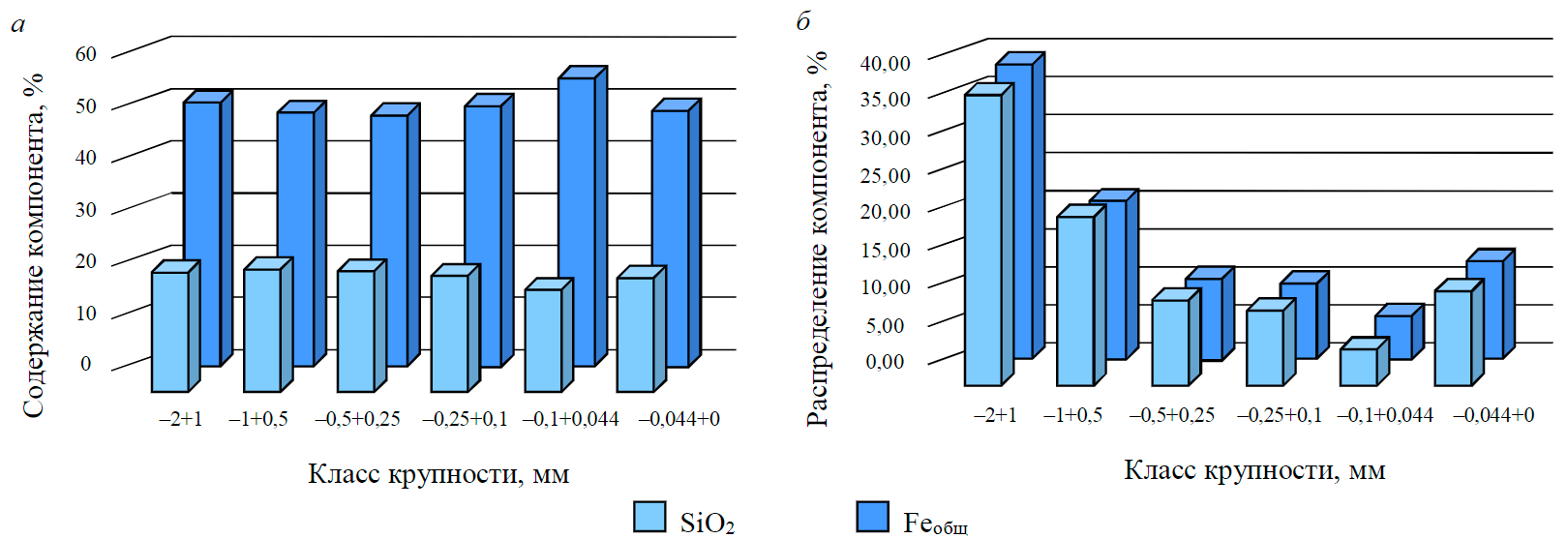
Рис.1. Значения содержаний (а) и распределений (б) железа и оксида кремния в классах крупности исходной пробы [36]
Значения содержаний основных компонентов в исходной пробе железистых кварцитов по результатам РФА: SiO2 23,00; TiO2 0,06; Al2O3 1,90; Feобщ 50,24; MnO 0,02; МgO 0,30; CaO 0,51; Na2O < 0,1; K2O 0,22 %.
На основании изучения результатов химического анализа (рис.1) установлено, что основными компонентами пробы являются кремний, представленный в расчете на оксид кремния, и железо, рассчитанное как железо общее. Также в исследованной пробе установлено присутствие карбонатов железа.
Анализ содержаний компонентов в классах крупности исследованной пробы показал, что наибольшее содержание железа общего соответствует классу крупности –0,1+0,044 мм, а наибольшее содержание оксида кремния соответствует классу крупности –1+0,5 мм (рис.1, а). Значения содержаний железа общего в классах крупности изменяется в диапазоне от 48,3 до 55,7 %. Значения содержаний оксида кремния – в диапазоне от 20,06 до 23,80 %.
При исследовании распределения оксида кремния и железа общего по классам крупности в пробе установлено, что максимальные значения распределения компонентов соответствуют классу крупности –2+1 мм (рис.1, б). С уменьшением крупности класса до 0,044 мм значения распределений компонентов убывают. В классе крупности –0,044+0 мм установлено повышение значений распределения для оксида кремния до 12,91 %, для железа общего – до 13,20 %.
В работе [35] предложено обоснование селективности операций рудоподготовки по распределению компонентов сырья по классам крупности. Аналогичный принцип использован в данной статье. Для количественной характеристики распределения компонентов в продуктах измельчения по классам крупности в работе применялась интегральная функция гамма-распределения. Аргументом функции являлась крупность в микрометрах, а значением функции являлось значение суммарного распределения компонента «по минусу» в процентах:
где β, α – параметры гамма-распределения;
Выбор гамма-распределения для характеристики распределения компонентов по крупности в продуктах измельчения обусловлено высокой сходимостью расчетов экспериментальных значений распределений. Параметры α, β характеризуют математическое ожидание функции распределения и интервал значений крупности, для которого характерны максимальные значения распределения компонента, а также форму графической зависимости распределения в зависимости от крупности.
Параметр α характеризует эксцесс функции – меру остроты пика функции. Параметр β характеризует дисперсию значений функции распределения компонента относительно значения математического ожидания.
При измельчении параметр β будет монотонно возрастать с уменьшением P80 продукта измельчения. В то же время α с уменьшением крупности продукта измельчения будет незначительно убывать, достигнув минимума, затем резко возрастать. На этапе грубого измельчения переход материала в более мелкие классы обуславливает увеличение остроты пика функции распределения и уменьшение значения параметра α. При тонком измельчении сокращается предельная крупность материала, что повышает равномерность распределения компонентов по существующим классам крупности и обуславливает рост параметра α.
Значения параметров β, α распределений определялись с использованием метода наименьших квадратов. Производилась итерация этих значений до достижения минимума параметра ψ:
где εэкс(tn), εрас(tn) – экспериментальное и расчетное значения суммарного распределения компонента по крупности материала соответственно.
Обсуждение
Для анализа характера вкраплений и срастания рудных и породных минералов в исходной пробе проведен комплекс минералогических исследований, результаты которых представлены в табл.2 и на рис.2, а.
Таблица 2
Элементный состав сростков
Минерал |
Содержание, % |
Точка |
|||||||||||||
Fe |
Si |
Mn |
Mg |
Ca |
O |
Сумма |
|||||||||
Магнетит |
69,88 |
1,56 |
– |
– |
– |
28,56 |
100,00 |
3 |
|||||||
70,23 |
1,19 |
– |
– |
– |
28,58 |
100,00 |
4 |
||||||||
69,26 |
1,29 |
– |
– |
– |
29,45 |
100,00 |
6 |
||||||||
69,55 |
1,46 |
– |
– |
– |
28,99 |
100,00 |
9 |
||||||||
Гематит |
68,10 |
0,66 |
– |
– |
– |
31,24 |
100,00 |
2 |
|||||||
68,31 |
0,68 |
– |
– |
– |
31,01 |
100,00 |
7 |
||||||||
Минерал |
Содержание, % |
Точка |
|||||||||||||
SiO2 |
Al2O3 |
Fe2O3 |
MgO |
CaO |
K2O |
CO2 |
Сумма |
||||||||
Селадонит |
50,83 |
1,77 |
29,19 |
4,32 |
– |
13,29 |
– |
100,00 |
1 |
||||||
Кварц |
96,39 |
0,05 |
0,42 |
– |
– |
3,14 |
– |
100,00 |
5 |
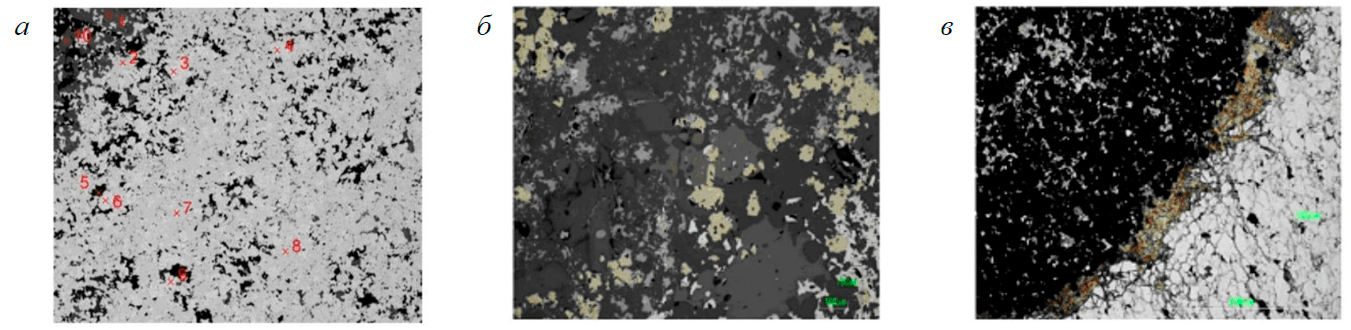
Рис.2. Результаты минералогических исследований проб железистых кварцитов Михайловского месторождения: а – магнетит в тесном срастании с гематитом и кварцем, изображение в обратно рассеянных электронах; б – гематит-магнетит-гидрогетит-карбонат-селадонит-кварцевые прослои в железистых кварцитах; в – контакт безрудного кварцевого прослоя (светлый) с рудным гематит-магнетитовым прослоем (черный) с прожилком карбоната (коричневый)
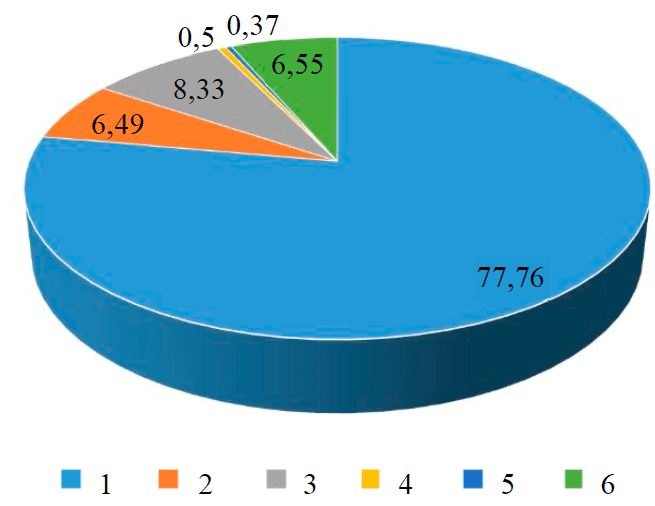
Рис.3. Распределение железа по минералам в исходной пробе железистых кварцитов и классифицированном материале 1 – гематит; 2 – магнетит; 3 – гидрогетит; 4 – прочие минералы; 5 – селадонит; 6 – сидерит
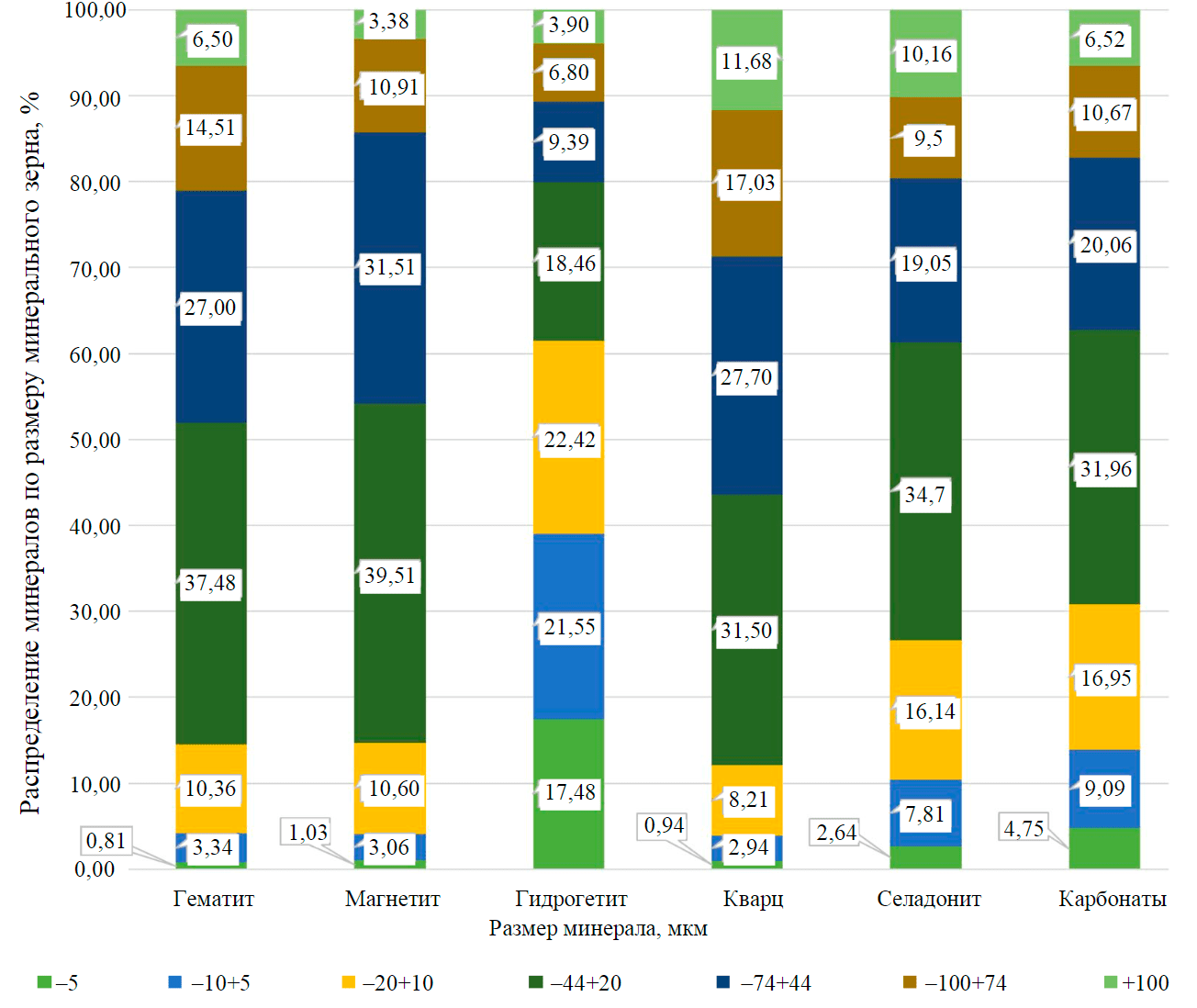
Рис.4. Результаты анализа характера срастания минеральных зерен в пробе мелкодробленной руды Михайловского месторождения
Установлено, что текстура образцов исследованных руд в основном тонкополосчатая и тонкослоистая (рис.2, в). Наиболее часто встречаются сростки гематита, магнетита и кварца (табл.2). Меньшее содержание характерно для сростков магнетита и гематита с селадонитом и гидрогетитом. Для магнетита и гематита характерна тесная ассоциация. Гематит расположен ближе к контакту с породообразующими минералами. В пробе гематит присутствует в виде двух морфологических форм выделений: изометричной и удлиненно-пластинчатой, что обусловлено природой его образования. Гидрогетит в пробах железистых кварцитов образуется как продукт окисления оксидов, карбонатов и силикатов железа (магнетита, сидерита, селадонита). Наибольшая концентрация гидрогетита отмечается в гематит-магнетит-гидрогетит-карбонат-селадонит-кварцевых прослоях (рис.2, б) и на контакте кварц-магнетит-гематитовых прослоев с карбонатными прожилками. В пробе руды контакт железосодержащих минералов характеризуется ровными протяженными границами срастаний. Граница контактов породных и рудных минералов характеризуется сложным взаимопроникновением границ одного минерала в другой.
Исследование распределения железа по основным минералам пробы и оценка раскрытия минеральных сростков проведены с применением автоматизированного минералогического анализа, проба была измельчена до крупности –0,12 мм (рис.3).
Анализ характера срастания минеральных зерен (рис.4) показывает, что 84,25 % железа в пробе ассоциировано с гематитом и магнетитом, 14,88 % железа приходится на продукты окисления основных рудных минералов – гидрогетит и сидерит, остальная часть железа ассоциирована с минералами вмещающей породы.
На основании полученных данных (рис.4) установлено, что преобладающим классом крупности минеральных частиц железосодержащих минералов является класс –44+20 мкм. Исключение составляет гидрогетит, для зерен которого преобладающим классом крупности являются классы –20+10 и –10+5 мкм. Преобладание низкоразмерных зерен окисленных минералов железа связано с их генезисом. Характер их вкрапленности и низкая твердость, вероятно, будут обуславливать их склонность к переизмельчению в процессе рудоподготовки.
Распределение размеров минеральных зерен гематита и магнетита коррелируется, что подтверждает их тесную ассоциацию в исследуемой руде. По сравнению с ними для минералов вмещающей породы характерны более высокие значения распределения в классы крупности +100,–100+74, –74+44 мкм; 56,41 % массы минеральных зерен кварца, 38,71 % массы минеральных зерен селадонита имеют крупность больше 44 мкм. Преобладание зерен минералов вмещающей породы больше +44 мкм, вероятно будет способствовать более быстрому раскрытию в процессе измельчения. Их повышенная прочность по сравнению с рудными минералами является предпосылкой к селективному разрушению компонентов руды.
Минералы вмещающей породы, в отличие от рудных минералов, предположительно, должны иметь более низкую скорость измельчения и оставаться в крупных классах продуктов измельчения. Однако, значительная часть рудных минералов пробы вкраплена в минералы вмещающей породы, преимущественно в кварц. Их тесная ассоциация не позволит эффективно обогатить руду магнитными методами, требуется тонкое измельчение для раскрытия сростков. В то же время необходимо не допустить высокой степени переизмельчения железосодержащих минералов и их перехода в класс крупности –44 мкм. С уменьшением размера сростки железосодержащих минералов будут иметь меньшую магнитную восприимчивость, что снизит их обогатимость основным магнитным переделом [37]. Таким образом, селективное разрушение должно обеспечивать раскрытие сростков рудных минералов и их минимальное распределение в класс крупности –44 мкм.
Графическая интерпретация результатов исследования распределения железа и оксида кремния по классам крупности –2000+200, –200+44 и –44 мкм в продуктах измельчения приведена на рис.5.
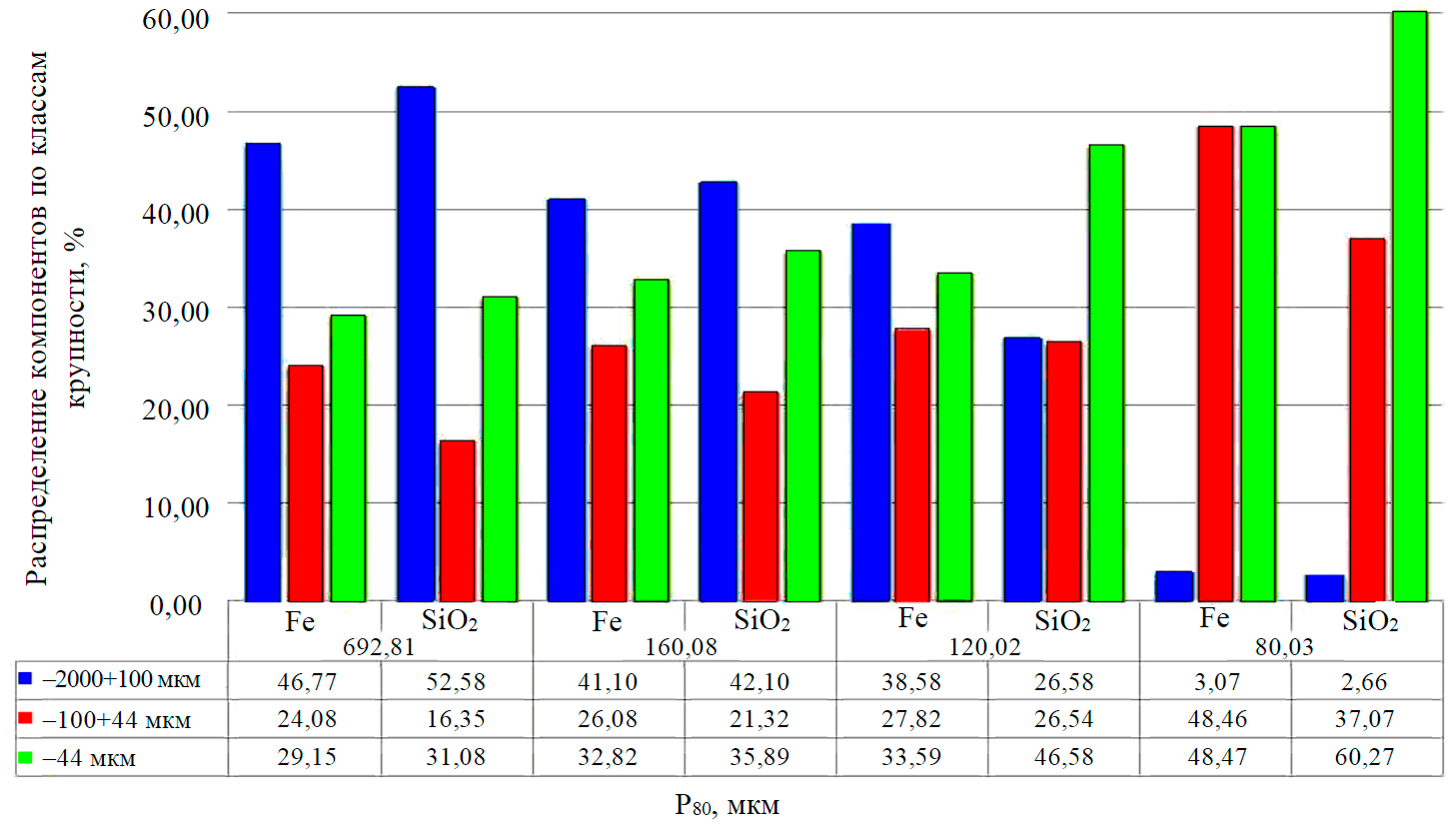
Рис.5. Распределение железа и оксида кремния по классам крупности в продуктах измельчения
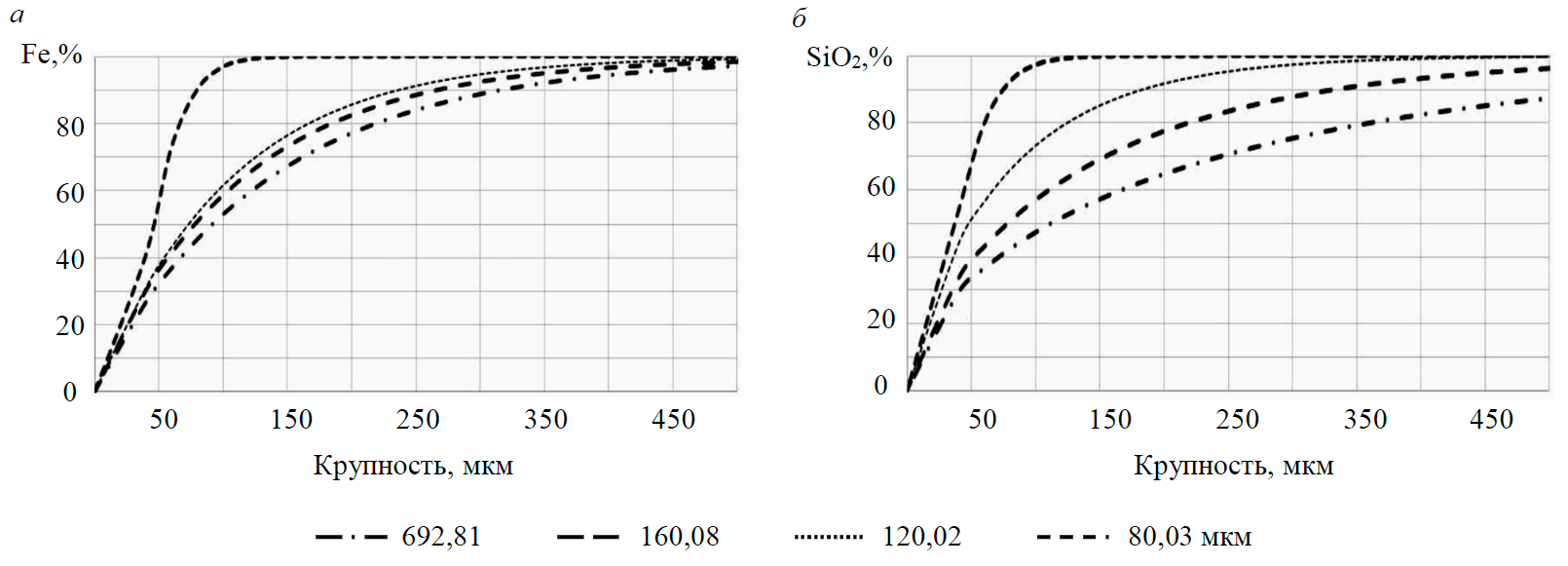
Рис.6. Суммарные распределения железа (а) и оксида кремния (б) по крупности в продуктах измельчения в зависимости от параметра P80
Установлено, что максимальные значения распределения железа и оксида кремния в класс –100+44 мкм получены при значении P80, равном 80,03 мкм, и составили 48,46 и 37,07 % соответственно. Наибольший прирост железа и оксида кремния в класс крупности –44 мкм составил 14,88 и 13,69 % соответственно при изменении значения P80 от 120 до 80 мкм. Значения распределения железа в класс –44 мкм около 29 % при крупности измельчения P80 = 692,81 мкм обусловлен переизмельчением раскрытых сростков окисленных минералов железа. Резкий прирост железа в класс крупности –44 мкм при достижении крупности измельчения P80 = 80,03 мкм, вероятно, обусловлен разрушением сростков минералов вмещающей породы и переизмельчением раскрытых рудных минералов. При грубом измельчении низкие значения прироста распределения железа в тонкие классы связаны с возможным разрушением раскрытых железосодержащих породных минералов.
Для количественной характеристики экспериментальных значений суммарных распределений железа общего и оксида кремния установлены параметры гамма-распределения в зависимости от параметра P80 по формуле (1) (табл.3). Графическая интерпретация суммарных распределений компонентов по крупности в зависимости от параметра P80 приведена на рис.6.
Таблица 3
Параметры функции распределения железа и оксида кремния в зависимости от параметра P80
Компонент |
P80, мкм |
|||||||
692,81 |
160,08 |
120,02 |
80,03 |
|||||
Fe |
SiO2 |
Fe |
SiO2 |
Fe |
SiO2 |
Fe |
SiO2 |
|
a |
0,94 |
0,58 |
0,96 |
0,71 |
1,06 |
0,84 |
4,36 |
3,07 |
b |
141,61 |
376,72 |
116,82 |
187,93 |
99,74 |
91,09 |
11,08 |
13,79 |
Для кривых распределения железа при значениях P80 692,81, 160,08 и 120,02 мкм (рис.6) характерно незначительное изменение выпуклости функции, в отличие от распределения оксида кремния, что подтверждает незначительное перераспределение железа внутри класса для данных крупностей измельчения. Дополнительно для железа наблюдается незначительное изменение показателя a для параметров P80. Поскольку параметр α характеризует меру остроты пика функции распределения, его увеличение свидетельствует о концентрировании в узком классе крупности. При тонком измельчении это объясняется переходом компонента в самый мелкий класс крупности. Тогда для обеспечения максимальной селективности при классификации продукта измельчения показатель αFe должен быть минимальным, а αSiO2 – максимальным.
На основании полученных экспериментальных данных установлены эмпирические зависимости, связывающие показатель P80 и параметр распределения α компонентов в продуктах измельчения:
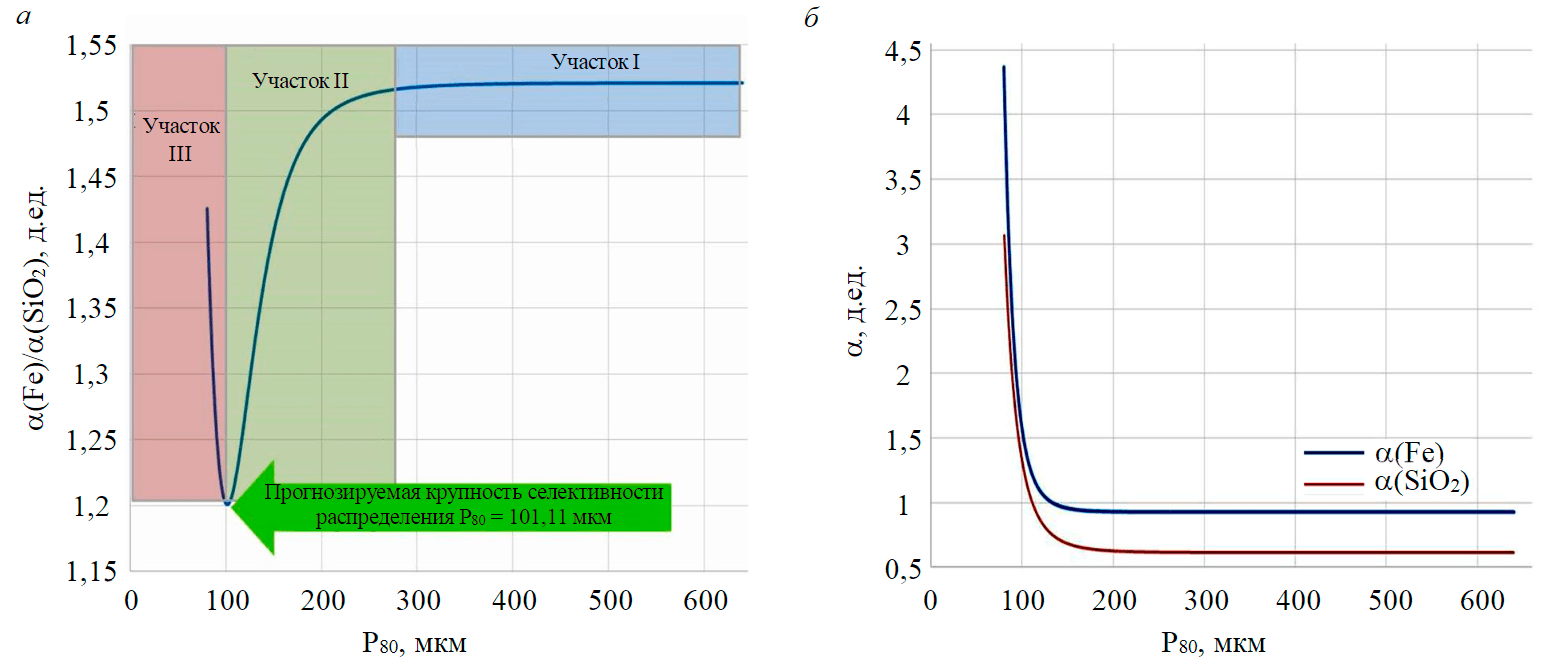
Рис.7. Зависимость αFe, αSiO2 и их отношения от значения P80
Расхождения между рассчитанными значениями и экспериментальными значениями показателя α не превысили 5 %.
Для оценки селективности распределения компонентов по крупности для диапазона P80 рассчитаны отношения αFe к αSiO2 (рис.7).
Характер изменения зависимостей (рис.7, а) можно разделить на три участка. На первом участке изменение показателей незначительно и может быть объяснено постепенным переходом компонентов из класса –2000+100 мкм. Второй участок характеризуется резким возрастанием показателя αSiO2, что, вероятно, обусловлено разрушением сростков минералов вмещающей породы и их переходом в класс –44 мкм. Третий участок характеризуется началом роста показателя αFe и, вероятно, связан с освобождением вкрапленных в массив пустой породы зерен рудных минералов и их более интенсивном измельчением.
Селективность разрушения характерна для минимума функции αFe/αSiO2, который был определен, исходя из равенства нулю первой производной функции отношения:
Отношение αFe/αSiO2 достигает своего минимума при значении P80 = 101,11 мкм. Данное значение крупности измельчения является прогнозным для максимально эффективного раскрытия сростков железосодержащих минералов и их минимальном переизмельчении. Полученные данные можно использовать для дальнейших исследований обогатимости железистых кварцитов Михайловского месторождения.
Выводы
Растущий спрос на продукцию черной металлургии в различных отраслях промышленности обуславливает потребность повышения эффективности переработки железорудного сырья и полноты извлечения железа. Основные запасы железосодержащего сырья Российской Федерации приурочены к месторождениям железистых кварцитов. Тонкая вкрапленность рудных минералов, высокая абразивность и крепость пород обуславливают высокие затраты на этапе рудоподготовки. Перспективным направлением модернизации операций дробления и измельчения является применение технологий, основанных на селективном разрушении. В исследовании установлены закономерности селективного разрушения железистых кварцитов на основании результатов изучения их минералого-технологических свойств.
Установлено, что рудные минералы и минералы вмещающей породы железистых кварцитов Михайловского месторождения в исследованной пробе преимущественно сконцентрированы в классах крупности –2+1, –1+0,5 и –0,044 мм. Контакт рудных и породных минералов в пробе отличается сложным характером взаимопрорастания. По результатам автоматизированного минералогического анализа пробы руды установлено, что 84,25 % железа в пробе ассоциировано с гематитом и магнетитом, 14,88 % железа приходится на продукты окисления основных рудных минералов – гидрогетит и сидерит. Установлено преобладание минеральных зерен кварца и селадонита крупностью больше 77 мкм. Основная крупность зерен рудных минералов составляет –44 мкм.
Различие в прочности рудных и породных минералов является предпосылкой для применения технологий селективного разрушения (контроля распределения компонентов по классам крупности в продуктах измельчения). Характер вкрапленности рудных минералов в массив вмещающей породы обуславливает затруднение раскрытия железосодержащих минералов в процессе рудоподготовки и их переизмельчения.
На основании интерпретации результатов исследования измельчения установлены закономерности селективного разрушения железистых кварцитов спрогнозировано значение крупности измельчения, при которой должно обеспечиваться раскрытие рудных минералов и их минимальный переход в класс крупности –44 мкм.
Литература
- Литвиненко В.С., Сергеев И.Б. Инновационное развитие минерально-сырьевого сектора // Проблемы прогнозирования. 2019. № 6 (177). С. 60-72.
- Чантурия В.А., Вайсберг Л.А., Козлов А.П. Приоритетные направления исследований в области переработки минерального сырья // Обогащение руд. 2014. № 2(350). С. 3-9. DOI: 10.17580/or.2014.02.01
- Bisweswar D., Swagat S.R. Existing and New Processes for Beneficiation of Indian Iron ores // Transactions of the Indian Institute of Metals. 2020. №3 (73). C. 505-514. DOI: 10.1007/s12666-020-01878-z
- Государственный доклад о состоянии и использовании минерально-сырьевых ресурсов Российской Федерации в 2020 году. URL (дата обращения 06.04.2022).
- Помельников И.И. Состояние и перспективы развития железорудной промышленности при устойчивом снижении мировых цен на железорудное сырье // Горный журнал. 2015. № 7. С. 78-88. DOI: 10.17580/gzh.2015.07.11
- Баженов И.Н., Басов О.О. Метод индукционного контроля массовой доли железа в магнетитовой руде // Записки Горного института. 2018. Т. 230. С. 123-130. DOI: 10.25515/PMI.2018.2.123
- Юнгмейстер Д.А., Судариков С.М., Киреев К.А. Обоснование типов глубоководной техники для добычи морских железомарганцевых конкреций // Записки Горного института. 2019. Т. 235. С. 88-95. DOI: 10.31897/PMI.2019.1.88
- Whitworth A.J., Forbes E., Verster I. et al. Review on advances in mineral processing technologies suitable for critical metal recovery from mining and processing wastes // Cleaner Engineering and Technology. 2022. Vol. 7. № 100451. DOI: 10.1016/j.clet.2022.100451
- Авдохин В.М., Губин С.Л. Современное состояние и основные направления развития процессов глубокого обогащения железных руд // Горный журнал. 2007. № 2. С. 58-64.
- Корнев А.В., Кусков В.Б., Бажин В.Ю. Окускование железных руд экструзионным методом // Черные металлы. 2019. № 11. С. 4-10.
- Cheremisina E., Cheremisina O., Ponomareva M. et al. Kinetic features of the hydrogen sulfide sorption on the ferro-manganese material // Metals. 2021. Vol. 11. № 1. P. 1-12. DOI: 10.3390/met11010090
- Litvinenko V.S., Tsvetkov P.S., Molodtsov K.V. The social and market mechanism of sustainable development of public companies in the mineral resource sector // Eurasian Mining. 2020. № 1. P. 36-41. DOI: 10.17580/em.2020.01.07
- Litvinenko V.S. Digital Economy as a Factor in the Technological Development of the Mineral Sector // Natural Resources Research. 2020. Vol. 29. № 3. P. 1521-1541. DOI: 10.1007/s11053-019-09568-4
- Savchenkov S.A., Bazhin V.Yu., Volkova O. Tendencies of innovation development of the russian iron and steel industry on the base of patent analytics for the largest national metallurgical companies // CIS Iron and Steel Review. 2020. Vol.20. P. 76-82. DOI: 10.17580/cisisr.2020.02.16
- Чернышов Н.М., Петров С.В., Молотков С.П. Особенности распределения и формы нахождения благородных металлов в железистых кварцитах Михайловского месторождения КМА и их техногенных продуктах (Центральная Россия) // Вестник Воронежского государственного университета. Серия: Геология. 2003. № 1. С. 93-104.
- Варичев А.В. От добычи руды к производству металла: развитие Михайловского ГОКа с 2000 до 2010 г. // Горный журнал. 2006. № 7. С. 6-9.
- Исмагилов Р.И., Козуб А.В., Гридасов И.Н., Шелепов Э.В. Современные направления повышения эффективности переработки железистых кварцитов на примере АО «Михайловский ГОК им. А.В.Варичева» // Горная промышленность. 2020. № 4. С. 98-103. DOI: 10.30686/1609-9192-2020-4-98-103
- Кретов С.И., Губин С.Л., Потапов С.А. Совершенствование технологии переработки руд Михайловского месторождения // Горный журнал. 2006. № 7. С. 71-74.
- Трушко В.Л., Трушко О.В. Комплексное освоение железорудных месторождений на основе конкурентоспособных подземных геотехнологий // Записки Горного института. 2021. Т. 250. С. 569-577. DOI: 10.31897/PMI.2021.4.10
- 20. Юшина Т.И., Чантурия Е.Л., Думов А.М., Мясков А.В. Современные тенденции в развитии технологий переработки железных руд // Горный журнал. 2021. № 11. C. 75-83. DOI: 10.17580/gzh.2021.11.10
- Кусков В.Б., Сищук Ю.М. Совершенствование технологий обогащения железных руд различных типов и вещественного состава // Горный журнал. 2016. № 2. С. 70-74. DOI: 10.17580/gzh.2016.02.14
- Пелевин А.Е. Тонкое грохочение и его место в технологии обогащения железных руд // Известия вузов. Горный журнал. 2011. № 4. С. 110-117.
- Игнатова Т.В., Шелепов Э.В. Особенности процесса колонной флотации для железных руд сложного вещественного состава Михайловского месторождения // Горный информационно-аналитический бюллетень. 2011. № 4. С. 241-245.
- Filippov L.O., Severov V.V., Filippova I.V. An overview of the beneficiation of iron ores via reverse cationic flotation // International Journal of Mineral Processing. 2014. №127. DOI: 10.1016/j.minpro.2014.01.002
- Бирюков В.В., Олейник А.Г., Опалев А.С., Щербаков А.В. Модернизация технологии обогащения железных руд на ОАО «Олкон» с использованием имитационного моделирования // Труды Кольского научного центра РАН. 2013. № 5 (18). С. 183-188.
- Kuskov V. B., Lvov V.V., Yushina T.I. Increasing the recovery ratio of iron ores in the course of preparation and processing // CIS Iron and Steel Review. 2021. Vol. 1. P. 4-8. DOI: 10.17580/cisisr.2021.01.01
- Гзогян Т.Н. Состав и свойства магнетита Михайловского месторождения // Горный информационно-аналитический бюллетень. 2001. № 12. С. 20-25.
- Хопунов Э.А. Основы дезинтеграции руд и техногенных материалов (теория, эксперимент, технологии). М.: Русайнс, 2016. 474 с. DOI: 10.15216/978-5-4365-1445-1
- França J.R.O., Barrios G.K., Turrer H.D., Tavares L.M. Comminution and liberation response of iron ore types in a low-grade deposit // Minerals Engineering. 2020. № 158. № 106590. DOI: 10.1016/j.mineng.2020.106590
- Hesse M., Popov O., Lieberwirth H. Increasing efficiency by selective comminution // Minerals Engineering. 2017. № 103. P. 112-126. DOI: 10.1016/j.mineng.2020.106590
- ЧантурияЕ.Л., ВишковаА.А., АнаньевП.П. идр. Интенсификация измельчения руд с использованием энергетических воздействий // Горный журнал. 2014. № 12. С. 63-69.
- Donskoi E., Poliakov A., Holmes R. et al. Iron ore textural information is the key for prediction of downstream process performance // Minerals Engineering. 2016. № 86. P. 10-23. DOI: 10.1016/j.mineng.2015.11.009
- Jankovic A. Developments in iron ore comminution and classification technologies of iron ore // Metals and Surface Engineering, Woodhead Publishing, 2022. P. 269-308. DOI: 10.1016/B978-1-78242-156-6.00008-3
- Schulz B., Merker G., Gutzmer J. Automated SEM Mineral Liberation Analysis (MLA) with Generically Labelled EDX Spectra in the Mineral Processing of Rare Earth Element Ores // Minerals. 2019. Vol. 9. № 527.DOI: 10.3390/min9090527
- Aleksandrova T.N., Nikolaeva N., Afanasova A. et al. Selective Disintegration Justification Based on the Mineralogical and Technological Features of the Polymetallic Ores // Minerals. 2021. Vol. 11. № 8. DOI: 10.3390/min11080851
- Nikolaeva N., Aleksandrova T., Chanturiya E.L., Afanasova A. Mineral and Technological Features of Magnetite-Hematite Ores and Their Influence on the Choice of Processing Technology // ACS Omega. 2021. Vol. 6. № 13. P. 9077-9085. DOI: 10.1021/acsomega.1c00129
- Jena S.K., Sahoo H., Rath S.S. et al. Characterization and Processing of Iron Ore Slimes for Recovery of Iron Values // Mineral Processing and Extractive Metallurgy Review. 2015. Vol.36. P. 174-182.