Mineralogical and technological features and patterns of selective disintegration of ferruginous quartzites of the Mikhailovskoye deposit
Abstract
The growing demand for ferrous metallurgy products necessitates the introduction of technologies that increase the efficiency of the processing of iron-bearing raw materials. A promising trend in this area is the implementation of solutions based on the possibility of selective disintegration of ores. The purpose of this work was to establish the laws of selective disintegration of ferruginous quartzites based on the results of the study of mineralogical and technological properties of raw materials. We present data on the study of mineralogical and technological features of ferruginous quartzites of the Mikhailovskoye deposit. The data were obtained using X-ray fluorescence analysis and automated mineralogical analysis. Based on studies of the nature of dissemination and the size of grains of rock-forming and ore minerals, the tasks of ore preparation are formulated. The parameters for the iron and silicon oxide distribution by grain-size classes in the grinding products were established during the study. Based on empirical dependences, the grain size of grinding was predicted, at which the most effective release of intergrowths of ore minerals and their minimum transition to the size class of –44 µm should be achieved.
Introduction
The main trend that characterizes the development of the global iron ore industry in recent decades is the increase in product consumption disproportionate with the increase in reserves of explored deposits [1-3]. In the Russian Federation, as of January 1, 2021, the balance reserves of iron ore amounted to 112.4 billion tons, and the total reserves of the developed deposits amounted to 29.4 billion tons [4]. The ratio of reserves growth due to exploration to production in 2020 was 0.21 (Table 1). Currently, the problems of rational use of iron ore raw materials [5] both at the stage of mining works [6-8] and at the stage of metallurgy attract the close attention of researchers [9-11]. One of the key factors in increasing the efficiency of production is the introduction of digital technologies [12-14].
Table 1
State of the raw material base of iron ores of the Russian Federation in 2018-2020 [4]
Year |
Increase in A + B + C1 reserves due to exploration, mmt |
Increase/loss of A + B + C1 reserves due to revaluation, mmt |
Ore production, mmt |
2018 |
22.3 |
1146.6 |
357.3 |
2019 |
59.0 |
–73.8 |
366.0 |
2020 |
37.3 |
80.4 |
376.1 |
Most of Russia's iron ore reserves are confined to ferruginous quartzite deposits located within the Kursk Magnetic Anomaly. The largest deposit in terms of reserves is Mikhailovskoye, which belongs to the hematite-magnetite geological type [15]. Despite the high volume of ore reserves in the deposits, about 38 % of them belong to C2 category [16]. In addition, the ferruginous quartzites of the Mikhailovskoye deposit are challenging to enrich due to several factors: high ore hardness, abrasiveness, and close association of ore and non-metallic minerals [17]. The combination of these factors necessitates the introduction of technological solutions that increase the completeness of iron extraction from these ores [18, 19]. However, semi-industrial testing of new technological solutions at enrichment and metallurgical process stages is very costly, which causes the need for comprehensive preliminary studies of raw materials' physical and chemical properties.
Differences in the mineralogical composition and textural and structural features of iron ores determine the variability of processing flow sheets [20]. The main criteria for selecting a processing technology are the material composition of iron ores, the nature of the components dissemination, the contrast of the separation properties, and the predicted efficiency of the processing [21, 22]. To date, in addition to magnetic enrichment – the main processing of iron ores, combined schemes are used. The use of gravity concentration and flotation for additional extraction of iron-bearing minerals from magnetic tailings has proven effective [23, 24].
A promising way to modernize ferruginous quartzite processing schemes is to improve ore preparation technology [25, 26]. The standard design solution is to take the non-magnetic fraction out for additional enrichment and additional grinding of the magnetic fraction. The main problems, in this case, are overgrinding of iron ore minerals and contamination of concentrates with waste rock minerals due to their mechanical capture at the stage of magnetic enrichment. The microhardness values of quartz, hematite, magnetite, and hydrogoethite confirm the tendency of ore minerals to overgrind [27].
Overgrinding of raw materials leads to increased energy costs and, consequently, to a decrease in the profitability of concentrate production. This problem can be solved by obtaining a product with a given distribution of components by size due to the different rates of disintegration of ore and rock minerals. This principle underlies selective disintegration technologies [28-30]. Decisions in such cases must be substantiated by studies of the mineralogical and technological characteristics of the ore. The primary studies are those of mineral texture: studying the features of the intergrowth boundaries of ore and rock minerals, assessing the size distribution of mineral grains, and calculating the parameters of the specific area of interfacial contact and fracturing [31, 32]. The texture is closely related to the degree of intergrowth release, and, as a result, to the redistribution of chemical elements by size classes in the process of ore preparation [33, 34].
Thus, the purpose of the work was to establish the patterns of selective disintegration of ferruginous quartzites based on the results of a study of the mineralogical and technological properties of raw materials.
Methodology
The object of the study was samples of rich ore from the Mikhailovskoye deposit after fine crushing, P80 for the studied sample was 1477.67 μm. The main iron-bearing minerals in the ore are magnetite, hematite, martite, iron hydroxides, celadonite, and siderite. Depending on the predominance of one of the components, two technological types of ores are distinguished: hematite-magnetite and carbonate-martite. The rock-forming minerals in the sample are mainly represented by various silicates and carbonates.
A series of experimental studies of the ferruginous quartzites grinding were carried out in a laboratory ball mill. The size of the grinding was evaluated by the P80 indicator. Studies were conducted for four P80 values: 692.81; 160.08; 124.69; and 80.00 µm. To eliminate random errors, each experiment was repeated three times. Data on the granulometric composition of samples and the distribution of the analyzed components after grinding were obtained by sieving on sieves with meshes of 2000, 1000, 500, 250, 100, and 44 µm. The obtained classes were weighed, after which representative samples were selected for the elemental composition analysis. Analysis of the chemical composition of the initial sample and grinding products was carried out on an EDX 7000 Shimadzu X-ray fluorescence analyzer. Automated mineralogical analysis was carried out on an automatic instrumental complex MLA 650 (FEI Company).
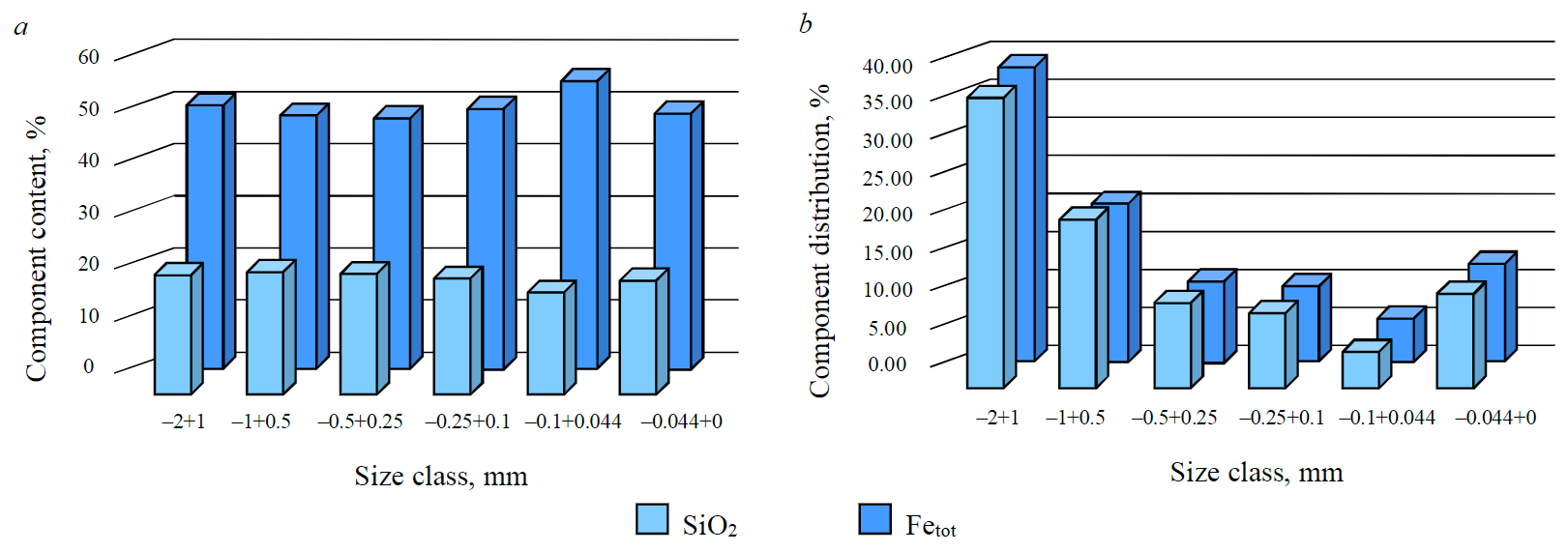
Fig.1. The values of the contents (a) and distributions (b) of iron and silicon oxide in the size classes of the initial sample [36]
The values of the main components contents in the initial ferruginous quartzites sample according to the XRF analysis are: SiO2 23.00; TiO2 0.06; Al2O3 1.90; Fetot 50.24; MnO 0.02; МgO 0.30; CaO 0.51; Na2O < 0.1; K2O 0.22 %.
Based on the study of the results of chemical analysis (Fig.1), it was found that the main components of the sample are silicon, represented as silicon oxide, and iron, calculated as total iron. The presence of iron carbonates was also found in the studied sample.
The analysis of the contents of the components in the grain-size classes of the studied sample showed that the highest content of total iron corresponds to the size class of –0.1+0.044 mm, and the highest content of silicon oxide corresponds to the size class of –1+0.5 mm (Fig.1, a). The values of the total iron content in the grain-size classes vary from 48.3 to 55.7 %. The values of silicon oxide content range from 20.06 to 23.80 %.
When studying the distribution of silicon oxide and total iron oxide by grain-size classes in the sample, we found that the maximum distribution of components corresponds to the –2+1 mm grain-size class (Fig.1, b). As the grain size of the class decreases to 0.044 mm, the values of the component distributions decrease. In the particle size class –0.044+0 mm, the distribution values for silicon oxide increased to 12.91 %, and for total iron – up to 13.20 % was found.
In [35], a rationale was proposed for the selectivity of ore preparation operations in terms of the distribution of raw material components by grain-size classes. A similar principle is used in this study. The integral gamma distribution function was used to quantitatively characterize the distribution of components in the grinding products by grain-size classes. The argument of the function was the grain size in micrometers, and the value of the function was the value of the total distribution of the “minus” component in a percent:
where β, α – parameters of the gamma distribution;
The choice of the gamma distribution to characterize the distribution of components by size in the grinding products is due to the high convergence of the calculations of the experimental values of the distributions. Parameters α and β characterize the mathematical expectation of the distribution function and the interval of size values, which are characterized by the maximum values of the distribution of the component, as well as the form of the graphical dependence of the distribution as a function of the grain size.
The parameter α characterizes the kurtosis of the function – a measure of the sharpness of the function peak. The parameter β characterizes the variance of the component distribution function values relative to the mathematical expectation value.
During grinding, the β parameter will increase monotonically with a decrease in P80 of the grinding product. At the same time α , with a decrease in the size of the grinding product, it will slightly decrease, reaching a minimum, then sharply increase. At the stage of coarse grinding, the transition of the material to smaller classes causes an increase in the peak sharpness of the distribution function and α decrease in the value of the α parameter. With fine grinding, the limiting size of the material is reduced, which increases the uniformity of the distribution of components over the existing size classes and causes an increase in the α parameter.
The values of the β, α parameters distributions were determined using the least squares method. These values were iterated until the minimum of the parameter ψ was reached:
where εexp(tn), εcal(tn) are the experimental and calculated values of the total distribution of the component by material size, respectively.
Discussion
To analyze the nature of inclusions and intergrowth of ore and rock minerals in the original sample, a complex of mineralogical studies was carried out, the results of which are presented in Table 2 and Fig.2, a.
Table 2
Elemental composition of intergrowth
Mineral |
Content, % |
The point |
|||||||||||||
Fe |
Si |
Mn |
Mg |
Ca |
O |
Total |
|||||||||
Magnetite |
69.88 |
1.56 |
– |
– |
– |
28.56 |
100.00 |
3 |
|||||||
70.23 |
1.19 |
– |
– |
– |
28.58 |
100.00 |
4 |
||||||||
69.26 |
1.29 |
– |
– |
– |
29.45 |
100.00 |
6 |
||||||||
69.55 |
1.46 |
– |
– |
– |
28.99 |
100.00 |
9 |
||||||||
Hematite |
68.10 |
0.66 |
– |
– |
– |
31.24 |
100.00 |
2 |
|||||||
68.31 |
0.68 |
– |
– |
– |
31.01 |
100.00 |
7 |
||||||||
Mineral |
Content, % |
The point |
|||||||||||||
SiO2 |
Al2O3 |
Fe2O3 |
MgO |
CaO |
K2O |
CO2 |
Total |
||||||||
Celadonite |
50.83 |
1.77 |
29.19 |
4.32 |
– |
13.29 |
– |
100.00 |
1 |
||||||
Quartz |
96.39 |
0.05 |
0.42 |
– |
– |
3.14 |
– |
100.00 |
5 |
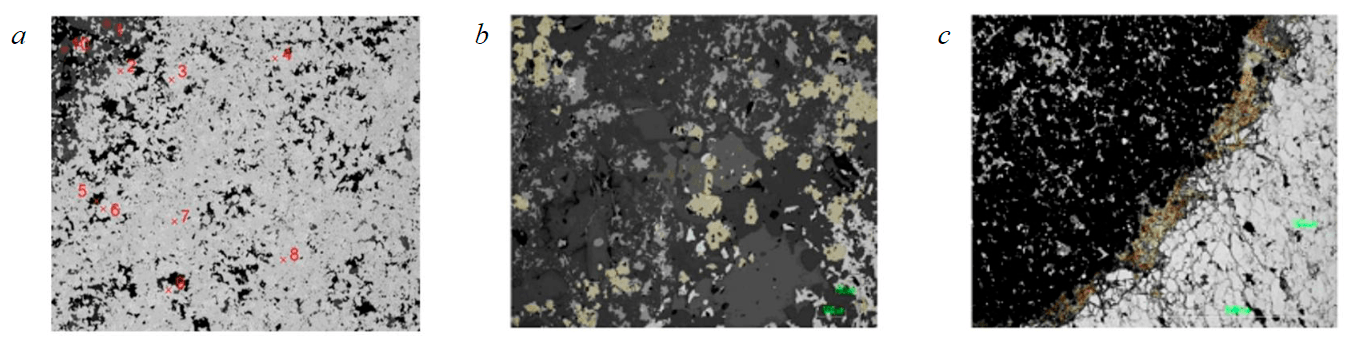
Fig.2. Results of mineralogical studies of samples of ferruginous quartzites of the Mikhailovskoye deposit: a – magnetite in close intergrowth with hematite and quartz, the image in backscattered electrons; b – hematite-magnetite-hydrogoethite-carbonate-celadonite-quartz interlayers in ferruginous quartzites; c – contact of barren quartz interlayer (light) with ore hematite-magnetite interlayer (black) with carbonate veinlet (brown)
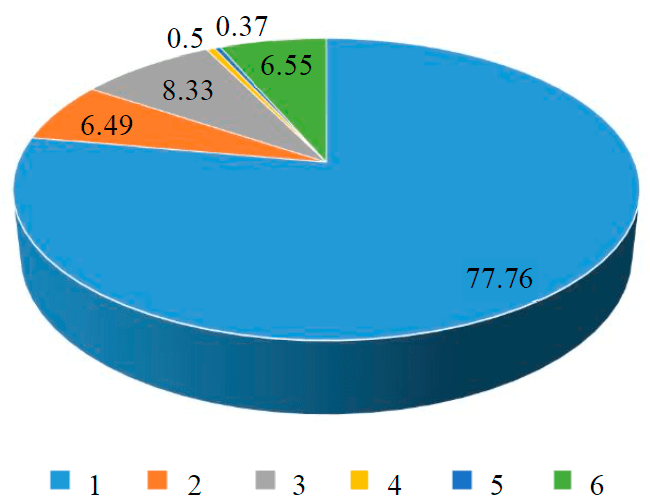
Fig.3. Distribution of iron by minerals in the initial sample of ferruginous quartzites and classified material 1 – hematite; 2 – magnetite; 3 – hydrogoethite; 4 – other minerals; 5 – celadonite; 6 – siderite
It has been established that the texture of the samples of the studied ores is mainly thin-banded and thin-layered (Fig.2, c). The most common are intergrowths of hematite, magnetite, and quartz (Table 2). A lower content is characteristic of intergrowths of magnetite and hematite with celadonite and hydrogoethite. Magnetite and hematite are characterized by a close association. Hematite is located closer to contact with rock-forming minerals. In the sample, hematite is present in the form of two morphological forms: isometric and elongated-lamellar, which is due to the nature of its formation. Hydrogoethite in samples of ferruginous quartzite is formed as a product of oxidation of iron oxides, carbonates, and silicates (magnetite, siderite, and celadonite). The highest concentration of hydrogoethite is observed in hematite-magnetite-hydrogoethite-carbonate-celadonite-quartz interlayers (Fig.2, b) and at the contact of quartz-magnetite-hematite interlayers with carbonate veinlets. In the ore sample, the contact of iron-bearing minerals is characterized by even extended intergrowth boundaries. The contact boundary of rock-forming and ore minerals is characterized by a complex interpenetration of the boundaries of one mineral into another one.
The study of iron distribution in the main minerals of the sample and evaluation of the mineral intergrowths release was carried out using automated mineralogical analysis. The sample was crushed to a fineness of –0.12 mm (Fig.3).
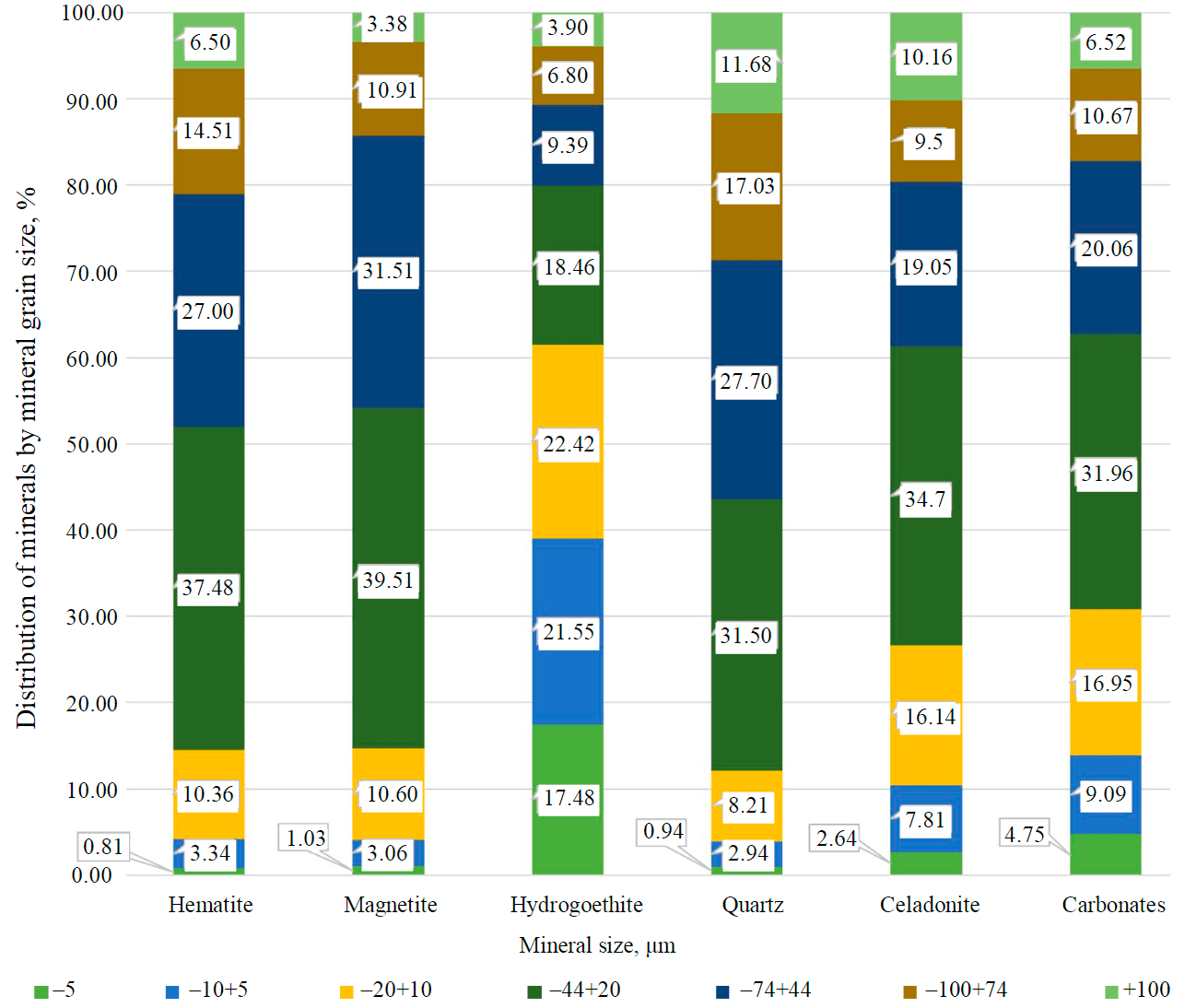
Fig.4. Results of the analysis of the nature of mineral grains intergrowth in a sample of fine-crushed ore from the Mikhailovskoye deposit
An analysis of the nature of the intergrowth of mineral grains (Fig.4) shows that 84.25 % of the iron in the sample is associated with hematite and magnetite, and 14.88 % of the iron falls on the oxidation products of the main ore minerals – hydrogoethite and siderite, the rest of the iron is associated with the minerals of the host rock.
Based on the data obtained (Fig.4), it was found that the predominant size class of mineral particles of iron-bearing minerals is the class of –44+20 μm. The exception is hydrogoethite, for whose grains the predominant size classes are –20+10 and –10+5 µm. The predominance of low-sized grains of oxidized iron minerals is associated with their genesis. The nature of their dissemination and their low hardness will probably cause their tendency to overgrind during ore preparation.
The size distribution of mineral grains of hematite and magnetite is correlated, which confirms their close association in the studied ore. As compared to them, the host rock minerals are characterized by higher values of distribution in the size classes of +100, –100+74, and –74+44 µm; 56.41 wt. % of quartz grains and 38.71 % of the celadonite grains have a size of more than 44 μm. The predominance of host rock mineral grains greater than +44 μm is likely to contribute to a more rapid release in the milling process. Their increased strength compared to ore minerals is a prerequisite for the selective disintegration of ore components.
Host rock minerals, in contrast to ore minerals, are expected to have a lower grinding rate and remain in large classes of grinding products. However, a significant part of the ore minerals of the sample is interspersed in the minerals of the host rock, mainly in quartz. Their close association will not allow efficient enrichment of the ore by magnetic methods; fine grinding is required to release the intergrowths. At the same time, it is necessary to prevent a high degree of overgrinding of iron-containing minerals and their transition to the size class of –44 μm. With a decrease in size, intergrowths of iron-bearing minerals will have a lower magnetic susceptibility, which will reduce their enrichment by the main magnetic process [37]. Thus, selective disintegration should ensure the intergrowths release of ore minerals and their minimum distribution in the size class of –44 µm.
A graphical representation of the results of a study of the iron and silicon oxide distribution by size classes –2000+200, –200+44, and –44 µm in the grinding products is shown in Fig.5.
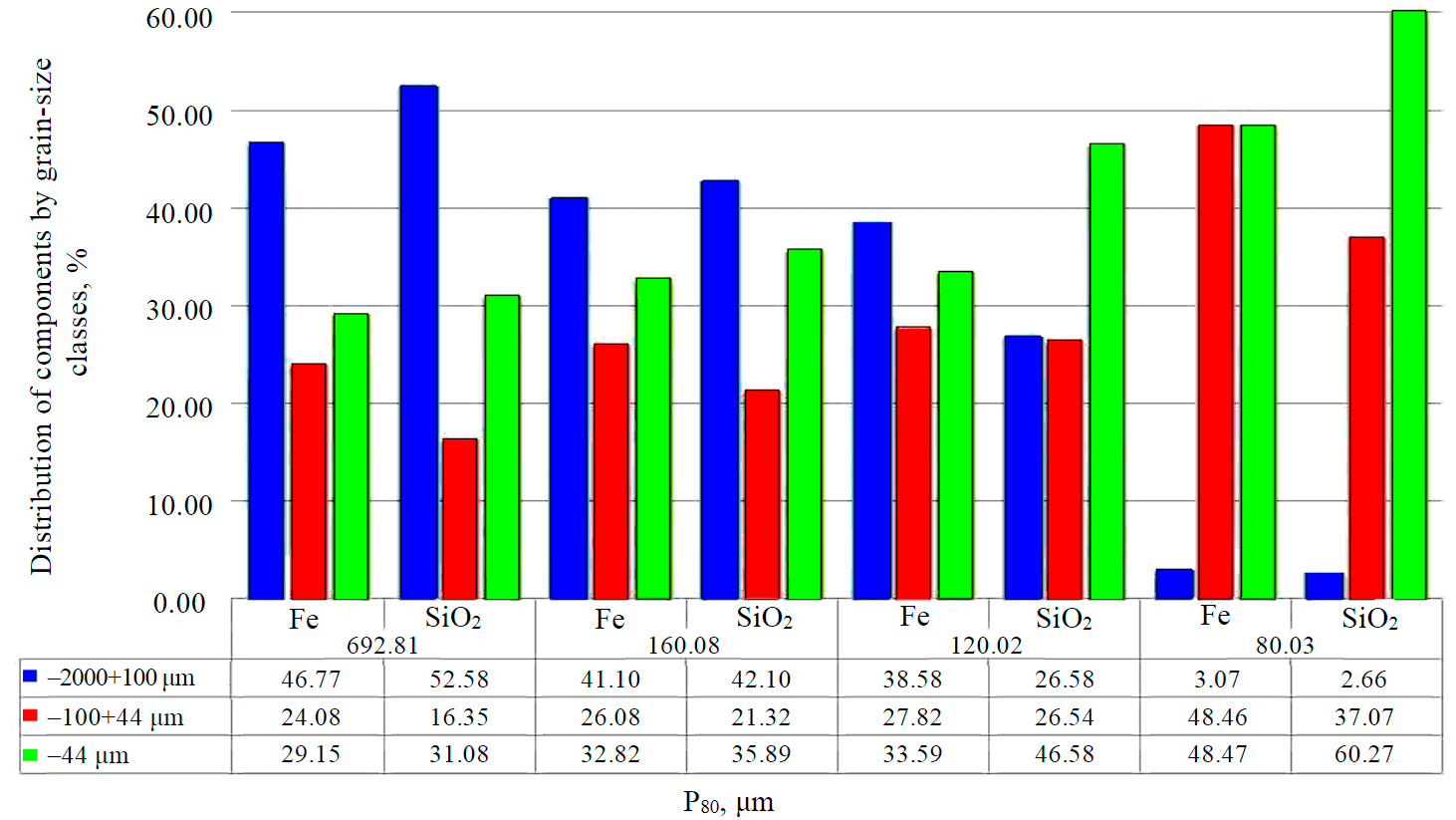
Fig.5. Distribution of iron and silicon oxide by size classes in grinding products
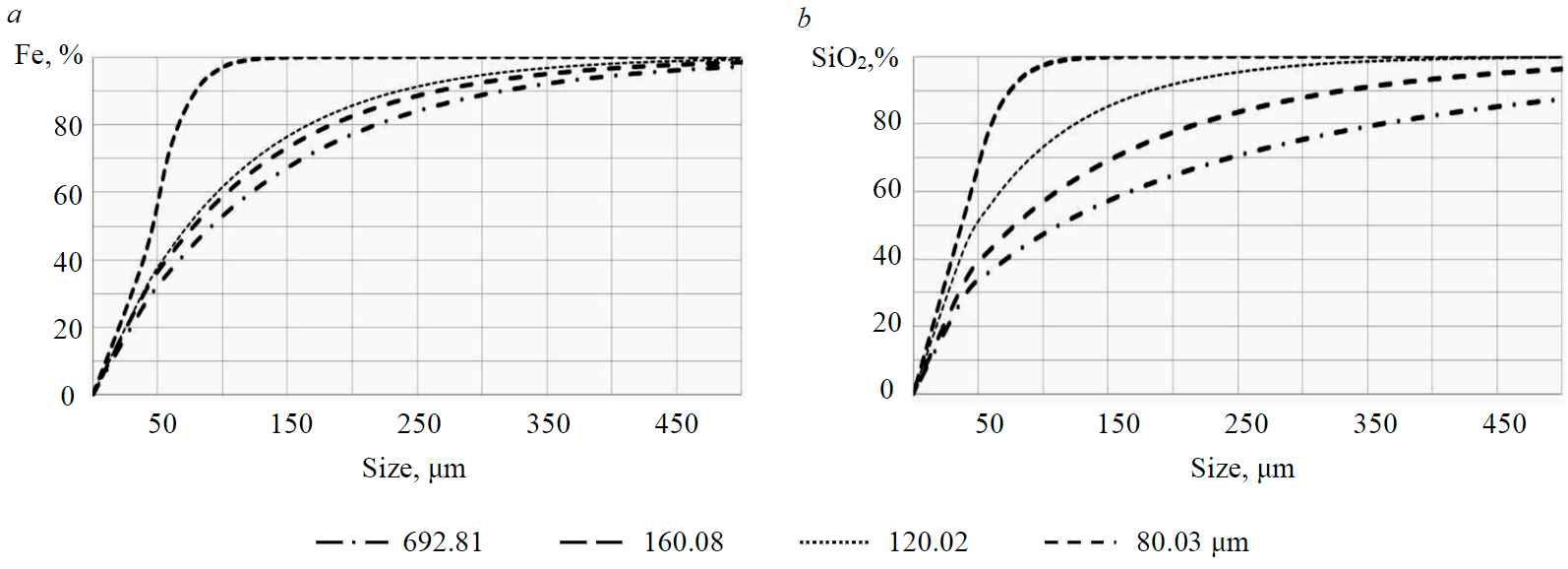
Fig.6. Total size distributions of iron (a) and silicon oxide (b) in grinding products depending on P80parameter
It has been established that the maximum values of the distribution of iron and silicon oxide in the –100+44 µm class were obtained at a P80 value of 80.03 µm and amounted to 48.46 and 37.07 %, respectively. The largest increase in iron and silicon oxide in the –44 µm grain-size class was 14.88 and 13.69 %, respectively, when the P80 value changed from 120 to 80 µm. The distribution of iron in the –44 µm class is about 29 % at a grinding size of P80 = 692.81 µm due to the overgrinding of released intergrowths of oxidized iron minerals. A sharp increase in iron in the size class of –44 µm when the grinding size P80 reaches the value of 80.03 is probably due to the disintegration of intergrowths of host rock minerals and overgrinding of released ore minerals. With coarse grinding, low values of the increase in the distribution of iron into fine classes are associated with the possible disintegration of released iron-bearing rock minerals.
To quantitatively characterize the experimental values of the total distributions of total iron and silicon oxide, the parameters of the gamma distribution were established depending on the P80 parameter according to formula (1) (Table 3). Graphical interpretation of the total size distributions of components depending on the P80 parameter is shown in Fig.6.
Table 3
Parameters of the distribution function of iron and silicon oxide depending on the P80 parameter
Component |
P80, μm |
|||||||
692.81 |
160.08 |
120.02 |
80.03 |
|||||
Fe |
SiO2 |
Fe |
SiO2 |
Fe |
SiO2 |
Fe |
SiO2 |
|
a |
0.94 |
0.58 |
0.96 |
0.71 |
1.06 |
0.84 |
4.36 |
3.07 |
b |
141.61 |
376.72 |
116.82 |
187.93 |
99.74 |
91.09 |
11.08 |
13.79 |
The distribution curves of iron at P80 values of 692.81, 160.08, and 120.02 µm (Fig.6) are characterized by a slight change in the convexity of the function, in contrast to the distribution of silicon oxide, which confirms a slight redistribution of iron within the class for these grinding sizes. Additionally, for iron, there is a slight change in the a parameter for the P80 parameters. Since parameter α characterizes the sharpness of the peak of the distribution function, its increase indicates concentration in α narrow grain-size class. With fine grinding, this is due to the transition of the component to the smallest grain-size class. Then, in order to ensure maximum selectivity in the classification of the grinding product, the αFe index should be minimal, and αSiO2 should be maximal.
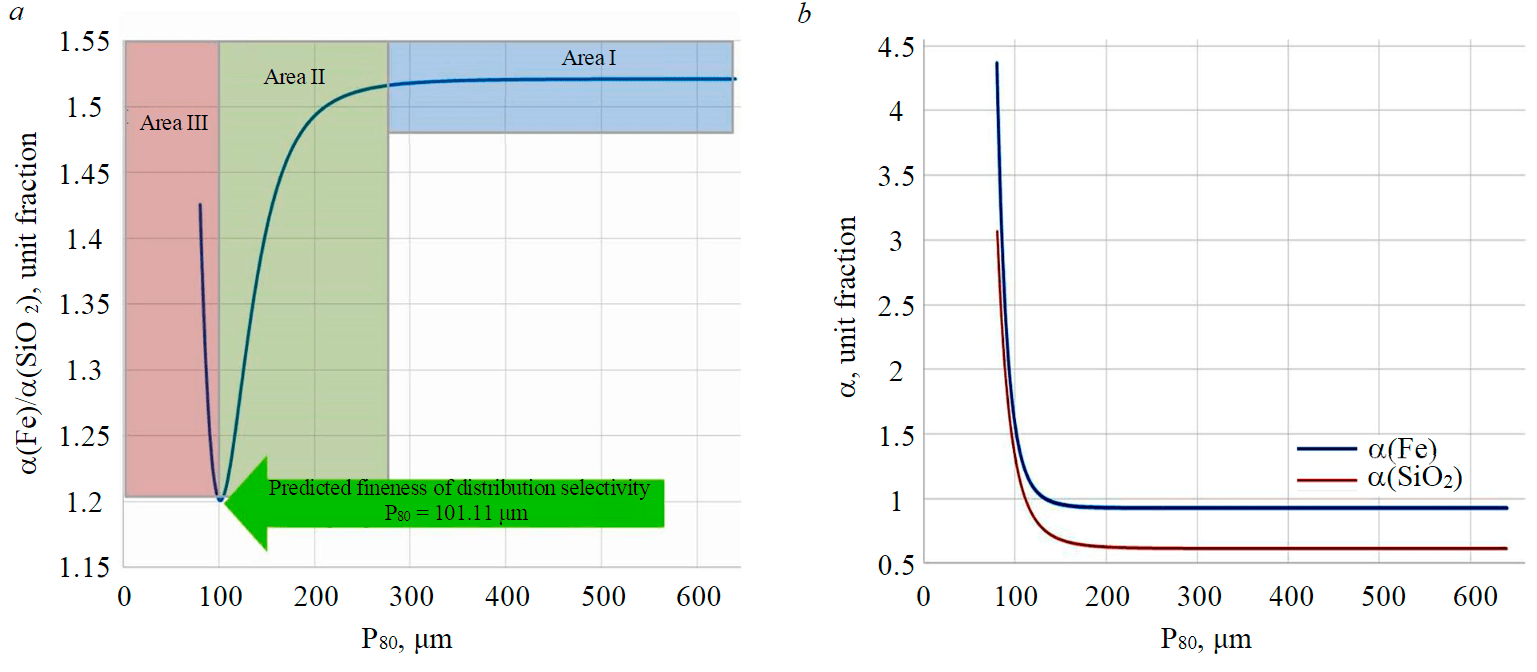
Fig.7. Dependence of αFe, αSiO2 and their ratio on the P80 value
Based on the experimental data obtained, empirical dependencies were established that link the P80 index and the α component distribution parameter in the grinding products:
The discrepancy between the calculated and experimental values of the α parameter did not exceed 5 %.
To assess the selectivity of the distribution of components by size for the P80 range, the ratios of αFe to αSiO2 were calculated (Fig.7).
The nature of the change in the dependencies (Fig.7, a) can be divided into three areas. In the first area, the change in indicators is insignificant and can be explained by the gradual transition of components from the –2000+100 µm class. The second area is characterized by a sharp increase in the αSiO2 index, which is probably due to the disintegration of mineral intergrowths of the host rock and their transition to the –44 µm class. The third area is characterized by the beginning of the growth of the αFe parameter and is probably associated with the release of ore mineral grains embedded in the waste rock massif and their more intense grinding.
The disintegration selectivity is characteristic of the minimum of the αFe/αSiO2 function, which was determined based on the equality of the first derivative of the ratio function to zero:
The αFe/αSiO2 ratio reaches its minimum at P80 = 101.11 µm. This value of the size of grinding is predicted for the most effective release of intergrowths of iron-bearing minerals and their minimal overgrinding. The obtained data can be used for further studies of the ferruginous quartzite processing of the Mikhailovskoye deposit.
Conclusions
The growing demand for ferrous metallurgy products in various industries causes the need to increase the efficiency of iron ore processing and the completeness of iron extraction. The main reserves of iron-bearing raw materials of the Russian Federation are associated with deposits of ferruginous quartzites. Fine dissemination of ore minerals, high abrasiveness, and hardness of rocks cause high costs at the stage of ore preparation. A promising direction in the modernization of crushing and grinding operations is the use of technologies based on selective disintegration. The study established the patterns of selective disintegration of ferruginous quartzites based on the results of studying their mineralogical and technological features.
It has been determined that ore minerals and minerals of the host rock of ferruginous quartzites of the Mikhailovskoye deposit in the studied sample are predominantly concentrated in size classes of –2+1, –1+0.5, and –0.044 mm. The contact of ore and rock-forming minerals in a sample is characterized by a complex nature of intergrowth. According to the results of the automated mineralogical analysis of the ore sample, it was found that 84.25 % of the iron in the sample is associated with hematite and magnetite, and 14.88 % of the iron falls on the oxidation products of the main ore minerals – hydrogoethite and siderite. The predominance of mineral grains of quartz and celadonite with a particle size of more than 77 μm is established. The main grain size of ore minerals is –44 µm.
The difference in the strength of ore and rock-forming minerals is a prerequisite for the use of selective disintegration technologies (controlling the distribution of components by size classes in grinding products). The nature of the dissemination of ore minerals in the host rock mass makes it difficult for the release of iron-bearing minerals in the process of ore preparation and their regrinding.
Based on the interpretation of the results of the study of grinding, the patterns of selective disintegration of ferruginous quartzites were established. The value of the grinding size was predicted, at which the release of ore minerals and their minimum transition to the size class of –44 μm should be ensured.
References
- Litvinenko V.S., Sergeev I.B. Innovations as a factor in the development of the natural resources sector. Studies on Russian Economic Development. 2019. Vol. 30. N 6, p. 637-645 (in Russian). DOI: 10.1134/S107570071906011X
- Chanturiya V.A., Vaysberg L.A., Kozlov A.P. Promising trends in investigations aimed at all-round utilization of mineral raw materials. Obogashchenie rud. 2014. N 2 (350), p. 3-9 (in Russian). DOI: 10.17580/or.2014.02.01
- Bisweswar D., Swagat S.R. Existing and New Processes for Beneficiation of Indian Iron ores. Transactions of the Indian Institute of Metals. 2020. N 3 (73), p. 505-514. DOI: 10.1007/s12666-020-01878-z
- State Report on the State and Use of Mineral Resources of the Russian Federation in 2020. URL (date of access 06.04.2022) (in Russian).
- Pomelnikov I.I. Title State and prospects of iron-ore industry development with stable decrease of global iron ore prices. Gornyi zhurnal. 2015. N 7, p. 78-88 (in Russian). DOI: 10.17580/gzh.2015.07.11
- Bazhenov I.N., Basov O.O. Method of Induction Control of Iron Weight Fraction in Magnetite Ore. Journal of Mining Institute. 2018. Vol. 230, p. 123-130. DOI: 10.25515/PMI.2018.2.123
- Yungmeister D.A., Sudarikov S.M., Kireev K.A. Feasibility of type of deep-water technologies for the extraction of marine ferro-manganese nodules. Journal of Mining Institute. 2019. Vol. 235, p. 88-95. DOI: 10.31897/PMI.2019.1.88
- Whitworth A.J., Forbes E., Verster I. et al. Review on advances in mineral processing technologies suitable for critical metal recovery from mining and processing wastes. Cleaner Engineering and Technology. 2022. Vol. 7. N 100451. DOI: 10.1016/j.clet.2022.100451
- Avdokhin V.M., Gubin S.L. Up-To-Date State and Main Directions of Development of the Processes of Deep Concentration of Iron Ores. Gornyi zhurnal. 2007. № 2, p. 58-64 (in Russian).
- Kornev A.V., Kuskov V.B., Bazhin V.Yu. Iron Ore Agglomeration by Extrusion. Chernye metally. 2019. N 11, p. 4-10.
- Cheremisina E., Cheremisina O., Ponomareva M. et al. Kinetic features of the hydrogen sulfide sorption on the ferro-manganese material. Metals. 2021. Vol. 11. N 1, p. 1-12. DOI: 10.3390/met11010090
- Litvinenko V.S., Tsvetkov P.S., Molodtsov K.V. The social and market mechanism of sustainable development of public companies in the mineral resource sector. Eurasian Mining. 2020. N 1, p. 36-41. DOI: 10.17580/em.2020.01.07
- Litvinenko V.S. Digital Economy as a Factor in the Technological Development of the Mineral Sector. Natural Resources Research. 2020. Vol. 29. N 3, p. 1521-1541. DOI: 10.1007/s11053-019-09568-4
- Savchenkov S.A., Bazhin V.Yu., Volkova O. Tendencies of innovation development of the russian iron and steel industry on the base of patent analytics for the largest national metallurgical companies. CIS Iron and Steel Review. 2020. Vol. 20, p. 76-82. DOI: 10.17580/cisisr.2020.02.16
- Chernyshov N.M., Petrov S.V., Molotkov S.P. Peculiarities of the distribution and occurrence of noble metals in ferruginous quartzites of the Mikhailovskoye deposit of KMA and their technogenic products (Central Russia). Vestnik Voronezhskogo gosudarstvennogo universiteta. Seriya: Geologiya. 2003. N 1, p. 93-104 (in Russian).
- Varichev A.V. From Ore Mining to Metal Production: Development of Mikhailovsky GOK from 2000 to 2010. Gornyi zhurnal. 2006. N 7, p. 6-9 (in Russian).
- Ismagilov R.I., Kozub A.V., Gridasov I.N., Shelepov E.V. Modern trends for increasing the efficiency of processing of ferruginous quartzites on the example of JSC “Mikhailovsky GOK named after. A.V.Varichev”. Gornaya promyshlennost. 2020. Vol. 4, p. 98-103 (in Russian). DOI: 10.30686/1609-9192-2020-4-98-103
- Kretov S.I., Gubin S.L., Potapov S.A. Improving the processing technology of ores from the Mikhailovskoye deposit. Gornyi zhurnal. 2006. N 7, p. 71-74 (in Russian).
- Trushko V.L., Trushko O.V. Integrated development of iron ore deposits based on competitive underground geotechnologies. Journal of Mining Institute. 2021. Vol. 250, p. 569-577. DOI: 10.31897/PMI.2021.4.10
- Yushina T.I., Chanturia E.L., Dumov A.M., Myaskov A.V. Modern trends of technological advancement in iron ore processing. Gornyi zhurnal. 2021. N 11, p. 75-83. DOI: 10.17580/gzh.2021.11.10
- Kuskov V.B., Sishchuk Yu.M. Improvement of processing technologies of iron ores of different types and material composition. Gornyi zhurnal. 2016. N 2, p. 70-74 (in Russian). DOI: 10.17580/gzh.2016.02.14
- Pelevin A.E. Fine Screening and its Place in the Technology of Iron Ores Dressing. Izvestiya vuzov. Gornyi zhurnal. 2011. N 4, p. 110-117.
- Ignatova T.V., Shelepov E.V. Features of the column flotation process for iron ores of complex composition of the Mikhailovskoye deposit. Gornyi informatsionno-analiticheskii byulleten. 2011. N 4, p. 241-245 (in Russian).
- Filippov L.O., Severov V.V., Filippova I.V. An overview of the beneficiation of iron ores via reverse cationic flotation. International Journal of Mineral Processing. 2014. N 127. DOI: 10.1016/j.minpro.2014.01.002
- Birukov V.V., Oleynik A.G., Opalev A.S., Sherbakov A.V. Upgrading of Technology for Iron Ores Concentration on JSC “Olcon” by Using Simulation. Trudy Kolʹskogo nauchnogo tsentra RAN. 2013. N 5 (18), p. 183-188.
- Kuskov V. B., Lvov V.V., Yushina T.I. Increasing the recovery ratio of iron ores in the course of preparation and processing. CIS Iron and Steel Review. 2021. Vol. 1, p. 4-8. DOI: 10.17580/cisisr.2021.01.01
- Gzogyan T.N. Composition and features of magnetite of the Mikhailovskoye deposit. Gornyi informatsionno-analiticheskii byulleten. 2001. N 12, p. 20-25 (in Russian).
- Khopunov E.A. Basics of disintegration of ores and technogenic materials (theory, experiment, and technology). Moscow: Rusains, 2016, p. 474 (in Russian). DOI: 10.15216/978-5-4365-1445-1
- França J.R.O., Barrios G.K., Turrer H.D., Tavares L.M. Comminution and liberation response of iron ore types in a low-grade deposit. Minerals Engineering. 2020. N 158. N 106590. DOI: 10.1016/j.mineng.2020.106590
- Hesse M., Popov O., Lieberwirth H. Increasing efficiency by selective comminution. Minerals Engineering. 2017. N 103, p. 112-126. DOI: 10.1016/j.mineng.2020.106590
- Chanturiya E.L., Vishkova A.A., Anan'ev P.P. et al. Intensification of ore grinding using energy effects. Gornyi zhurnal. 2014. N 12, p. 63-69 (in Russian).
- Donskoi E., Poliakov A., Holmes R. et al. Iron ore textural information is the key for prediction of downstream process performance. Minerals Engineering. 2016. N 86, p. 10-23. DOI: 10.1016/j.mineng.2015.11.009
- Jankovic A. Developments in iron ore comminution and classification technologies of iron ore. Metals and Surface Engineering, Woodhead Publishing, 2022, p. 269-308. DOI: 10.1016/B978-1-78242-156-6.00008-3
- Schulz B., Merker G., Gutzmer J. Automated SEM Mineral Liberation Analysis (MLA) with Generically Labelled EDX Spectra in the Mineral Processing of Rare Earth Element Ores. Minerals. 2019. Vol. 9. N 527. DOI: 10.3390/min9090527
- Aleksandrova T.N., Nikolaeva N., Afanasova A. et al. Selective Disintegration Justification Based on the Mineralogical and Technological Features of the Polymetallic Ores. Minerals. 2021. Vol. 11. N 8. DOI: 10.3390/min11080851
- Nikolaeva N., Aleksandrova T., Chanturiya E.L., Afanasova A. Mineral and Technological Features of Magnetite-Hematite Ores and Their Influence on the Choice of Processing Technology. ACS Omega. 2021. Vol. 6. N 13, p. 9077-9085. DOI: 10.1021/acsomega.1c00129
- Jena S.K., Sahoo H., Rath S.S. et al. Characterization and Processing of Iron Ore Slimes for Recovery of Iron Values. Mineral Processing and Extractive Metallurgy Review. 2015. Vol. 36, p. 174-182.