Автоклавное моделирование коррозионных процессов, происходящих в газопроводе при транспортировке неподготовленной многофазной среды, содержащей CO2
- 1 — заместитель директора научно-технологического комплекса Санкт-Петербургский политехнический университет Петра Великого ▪ Orcid
- 2 — канд. техн. наук ведущий инженер Санкт-Петербургский политехнический университет Петра Великого ▪ Orcid
- 3 — тьютор Санкт-Петербургский политехнический университет Петра Великого ▪ Orcid
- 4 — инженер Санкт-Петербургский политехнический университет Петра Великого ▪ Orcid
- 5 — д-р техн. наук руководитель департамента Инжиниринговая компания ООО «ИТ-Сервис» ▪ Orcid
- 6 — заместитель генерального директора Инжиниринговая компания ООО «ИТ-Сервис» ▪ Orcid
Аннотация
Рассматривается проблема подбора способа обеспечения надежности функционирования объектов транспорта неподготовленного флюида в условиях присутствия углекислого газа. Углекислотная коррозия является одним из опасных видов повреждения промысловых и магистральных трубопроводов. Показано, что при проведении постановочных лабораторных испытаний с целью определения интенсивности протекания углекислотной коррозии и выбора оптимального способа защиты необходимо проводить динамические автоклавные испытания. Выдвинута и подтверждена гипотеза о несовершенстве существующих общепризнанных подходов к проведению динамических коррозионных испытаний. Предложена методика проведения испытаний, основанная на применении автоклава с верхнеприводной мешалкой, разработанного с использованием элементов математического моделирования. Потоки, создаваемые в автоклаве, обеспечивают коррозионный износ поверхности образца подобно износу внутренних поверхностей элементов трубопроводов обвязки газоконденсатных скважин. Автоклав позволяет моделировать влияние органической фазы на скорость протекания и характер коррозионных поражений поверхности металла, а также влияние скорости вращения мешалки и, соответственно, касательного напряжения сечения на скорость коррозии в присутствии/отсутствии ингибитора коррозии. Приведенные результаты постановочных испытаний позволяют судить о высокой эффективности разработанной методики испытаний.
Введение
В настоящее время газовая отрасль имеет стратегическое значение для развития экономики России [1]. Крупнейший источник пополнения государственного бюджета (около 50 %) – природный газ – играет огромную роль в жизнеобеспечения населения [2], выступая в качестве важнейшей структурной составляющей развития производственных сил страны [3] и ее регионов [4, 5].
Единая система газоснабжения (ЕСГ) – ключевая инфраструктура российской экономики, разветвленная сеть магистральных трубопроводов, которая объединяет 66 субъектов Российский Федерации, обеспечивая свыше 60 % потребности в энергоресурсах. Доля российского газа в потреблении Европы достигает, по данным Газпрома, 35-40 %.
Эффективность работы ЕСГ РФ в значительной степени зависит от надежного функционирования промысловых трубопроводов, а также их комплексной безопасности и сокращения возможного ущерба в результате аварийных ситуаций. Согласно анализу статистических данных по аварийности промысловых и магистральных трубопроводов транспорта неподготовленного газа, одной из основных причин отказов являются повреждения, вызванные углекислотной коррозией [6].
Углекислому газу (CO2, диоксид углерода, ангидрид угольной кислоты) как коррозионно-активному компоненту среды в процессе добычи газа ранее отводили не слишком значительную роль по сравнению с сероводородом (H2S) [7-9]. Проблема углекислотной коррозии стала приобретать все большее значение с началом разработки глубоко залегающих газоконденсатных месторождений с пластовыми температурами более 80 °С, давлениями свыше 30 МПа и содержанием CO2 в газе более 1 об.% [10-12].
Механизм углекислотной коррозии в достаточной степени изучен и в общем виде состоит из следующих этапов: активное растворение металла с образованием несплошного слоя продуктов коррозии; локальное, вызванное физическими (абразивное воздействие содержащимися в потоке частицами, гидравлическое воздействие потока) или химическими факторами, удаление пленки продуктов коррозии с поверхности металла дефектных участков [13, 14]; превращение данных участков в активные аноды, способствующие возникновению локальной коррозии с зарождением питингов, язв и, как следствие, мейза-коррозии [15-17].
Различные исследователи [18-20] указывают основные факторы, влияющие на интенсивность СО2-коррозии: температуру; наличие водной фазы, в которой будет растворяться CO2; скорость потока; минерализация воды; pH [7].
Для обеспечения надежности промысловых трубопроводов транспорта неподготовленного газа, снижения скорости СО2-коррозии до допустимого в соответствии с НД «Газпром» уровня (0,1 мм/год) используются различные методы защиты, основанные на применении новых материалов для строительства газотранспортной инфраструктуры, ингибиторной защиты, оптимальных режимов работы оборудования и т.д. [22-24]. Для выбора наиболее эффективного способа используют расчетные и (или) лабораторные методы по утвержденным методикам [25, 26].
Одной из методик прогнозирования углекислотной коррозии и оценки эффективности методов защиты от нее являются статические лабораторные испытания в ячейках Дрекселя в водной среде в присутствии CO2. Испытания проводят согласно рекомендациям ГОСТ Р 9.905-2007, ГОСТ Р 9.908-85 с помощью гравиметрического метода оценки скорости коррозии [27-29]. Существенным недостатком данного подхода является то, что он не учитывает влияния гидродинамики газожидкостного потока на коррозионный процесс [30]. Получаемые с его помощью прогнозные скорости коррозии отвечают наблюдаемым только в том случае, если металл находится в постоянном контакте с водной фазой, а скорость движения потока мала. Очевидно, что это условие не всегда выполняется для скважин и трубопроводов [31]. В связи с тем, что режим течения газожидкостной смеси существенно влияет на скорость углекислотной коррозии, что подтверждено многочисленными исследованиями [32-34], при проведении лабораторных испытаний по прогнозированию углекислотной коррозии это необходимо учитывать.
Известны подходы к оценке скорости углекислотной коррозии в динамических условиях при воздействии двухфазной жидкой среды в присутствии CO2 [35]. Испытания проводят на установке с постоянным перемешиванием водно-углеводородной рабочей среды, имитирующей обводненный газовый конденсат при атмосферном давлении и варьируемой температуре. Основным недостатком данного подхода является то, что в нем не учитывается парциальное давление углекислого газа, существенно влияющее на интенсивность коррозионного процесса.
Наиболее точно воспроизводящей условия коррозионных процессов в трубопроводе, возникающих при транспорте многофазной среды, с углекислым газом, является методика моделирования полевых условий в автоклавном комплексе (RCA) [36, 37]. СТО Газпром 9.3-007-2010 «Методика лабораторных испытаний ингибиторов коррозии для оборудования добычи, транспортировки и переработки коррозионноактивного газа» базируется на определении касательных напряжений (КНнС) на поверхности образца от воздействия потока, приводящего при определенных гидродинамических условиях к интенсификации коррозионных процессов. Установлено, что высокие значения КНнС на внутренней поверхности трубы приводят к непрерывному удалению продуктов коррозии (карбонатных отложений), тем самым подвергая «свежую» поверхность металла воздействию среды, что приводит к увеличению локальной скорости коррозии.
Аппараты RCA-типа являются разновидностью аппаратов с мешалкой, где на вращающемся держателе (клетке) закреплены образцы исследуемого материала. В настоящее время не существует стандартной, общепризнанной конструкции RCA [38]. Однако известно достаточно большое количество модификаций [39-41], которые создают определенные сложности при сравнении и интерпретации данных, полученных в разных лабораториях.
Проведенные в работе [26] исследования эффективности работы нескольких наиболее распространенных типов RCA методами численного моделирования с последующей валидацией результатов на стендовом автоклавном комплексе показали асимметричность распределения потока внутри автоклава, приводящую к неравномерному износу поверхности образцов.
Анализ полученных результатов позволяет сделать вывод о том, что испытания по измерению скорости коррозии с использованием автоклавов с вращающейся клеткой (RCA) очень чувствительны к конструкции. Поскольку неравномерный износ поверхности образцов не соответствует картине реальной деградации материала трубопроводов, объектов газотранспортной инфраструктуры, некорректно проводить количественную интерпретацию результатов подобных испытаний при прогнозировании скорости коррозии. Целью данной работы является разработка конструкции автоклава, обеспечивающей равномерное распределение КНнС по поверхности образца в ходе исследований и проведение серии испытаний, позволяющих подтвердить гипотезу о несовершенстве существующих общепризнанных подходов к проведению динамических испытаний.
Методология и методы исследования
Проектирование автоклава с мешалкой
Поскольку классическое проектирование с учетом всего многообразия заложенных параметров очень трудоемко и дорого, а необходимость создания методики постановки экспериментов, обеспечивающей сходимость получаемых результатов с реальными промысловыми условиями, требует выполнения большого объема вычислений, использовались методы численного (CFD) моделирования в программном комплексе ANSYS.
Первым этапом моделирования автоклава являлась проработка вариантов технического исполнения его конструкции. Поскольку основным недостатком известного аппарата с вращающейся клеткой является неравномерность распределения потока по поверхности образца, было решено в новой конструкции закрепить образцы неподвижно у стенок автоклава, а поток создавать вращающейся в центре крыльчаткой.
Математическое моделирование проводилось на упрощенной (параметрической) модели автоклава с образцами и мешалкой с постоянной скоростью вращения (2000 об/мин) в заданной расчетной области. Параметрическая модель состоит из внешнего цилиндра, который имитирует корпус автоклава; образцов-свидетелей (пластин), располагающихся по образующей вдоль стенок корпуса автоклава; внутреннего цилиндра, имитирующего лопасти мешалки.
Форма автоклава такова, что в его параметрическую модель можно заложить условие периодичности, что позволяет разбить модель на несколько секторов и выполнить расчет только для одного из них. Подобное упрощение позволяет существенно снизить вычислительную сложность модели.
Поскольку количество образцов определяет геометрию конструкции автоклава и характер распределения потока по поверхности образцов, задачей математического моделирования было установление зависимости между этими факторами.
В ходе моделирования варьировали геометрическими размерами образцов, их количеством, а также расстоянием между поверхностью образцов и лопастями мешалки. При этом отслеживали значения касательных напряжений (характеризующих равномерность распределения потока по образцу) на четырех гранях образца-свидетеля (боковые, передняя, верхняя) – как максимальные, так и средние значения (рис.1).
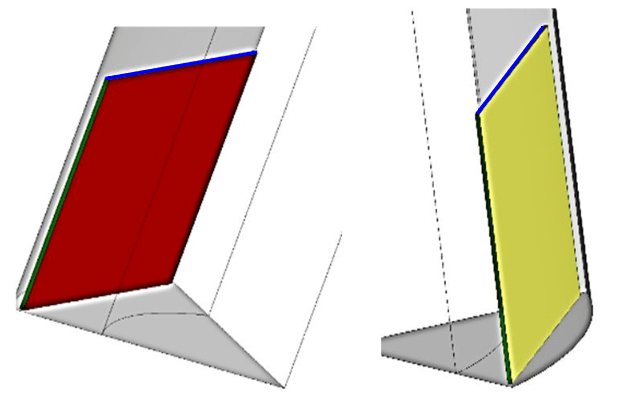
Рис.1. Образец-свидетель: красным выделена передняя плоскость, желтым – задняя, зеленым – боковые грани, синим – верхняя грань
Методика проведения коррозионных испытаний
Описанный автоклав использовался для оценки влияния гидродинамики потока коррозионно-активной среды и ее фазового состава на скорость и характер протекания СО2-коррозии. Был проведен ряд экспериментов:
- Температура процесса 105 °С, избыточное давление 6 МПа. В качестве модельной среды использовалась газожидкостная углеводородная смесь: газовая фаза N2+ CO2 в соотношении, обеспечивающем парциальное давление углекислого газа 0,2 МПа; в качестве органической фазы был использован керосин; водная фаза – вода с минерализацией 4,75 г/л. Отношение жидкой фазы к газообразной 90:10 об.%. Частота вращения крыльчатки составила 750 об/мин, длительность испытаний – 15 сут. В данном эксперименте моделировалась коррозия хвостовиков газоконденсатных скважин в случае появления свободной водной фазы на забое.
- Температура процесса 42-46 °С, избыточное давление 6 МПа. В качестве модельной среды использовалась газожидкостная смесь: газовая фаза N2+ CO2 в соотношении, обеспечивающем парциальное давление углекислого газа 0,2 МПа; водная фаза – вода с минерализацией 4,75 г/л. Отношение жидкой фазы к газообразной 90:10 об.%. Используемая концентрация ингибитора коррозии «Сонкор 9020» составила 100 мг/л. Частота вращения крыльчатки 150-670 об/мин, длительность испытаний 24-360 ч. В данном случае моделировалось влияние степени закрытия углового дросселя фонтанной арматуры газоконденсатной скважины, а значит скорости и направления потока транспортируемой среды, на скорость СО2-коррозии внутренней поверхности трубопроводов обвязки в присутствии/отсутствии ингибитора коррозии.
Для оценки скоростей коррозии образцы-свидетели – пластины 30 x 50 x 5 мм из стали 09Г2С – после извлечения из автоклава очищались, обезжиривались и взвешивались на весах с классом точности 0,0001 г. Очистка производилась согласно ГОСТ 9.907-2007. Скорость коррозии определяли по потере массы и пересчитывали в мм/год.
Обсуждение результатов
Результаты численного моделирования автоклава
Результаты (табл.1) показали, что чем больше образцов используется в его конструкции, тем меньше отношение между максимальным и средним значениями касательных напряжений, что говорит о меньшей неравномерности распределения потока. Таким образом, для создания равномерной картины распределения КНнС (рис.2) по поверхности образца и, соответственно, получения равномерного коррозионного износа необходимо располагать образцы таким образом, чтобы разница расстояний между образцом-свидетелем и корпусом автоклава была минимальной. В табл.1 приведены отношения максимального значения КНнС к среднему, которые показывают, что чем выше это значение, тем больше неоднородность распределения потока по поверхности образца и, соответственно, выше вероятность возникновения неравномерного смачивания его поверхности и коррозионного износа.
Таблица 1
Результаты численного моделирования автоклава
Количество |
Отношение КНнС |
|||
Левая боковая грань |
Правая боковая грань |
Верхний торец |
Передняя (лицевая) плоскость |
|
12 |
4,064 |
8,379 |
1,533 |
9,212 |
9 |
11,428 |
9,659 |
1,796 |
15,083 |
6 |
9,963 |
23,041 |
1,785 |
30,492 |
По результатам расчета дополнительно можно сделать следующие выводы:
- Поскольку на структуру формирующегося в автоклаве потока кроме скорости вращения существенно влияют геометрические параметры образца-свидетеля (размер, расстояния между купонами и мешалкой), то их необходимо контролировать, предварительно указав корреляционные зависимости между задаваемыми условиями и прогнозируемыми результатами коррозионного износа;
- В конструкции автоклава образцы-свидетели необходимо располагать таким образом, чтобы зазор между ними был минимальным и изолированным от воздействия потока. Поскольку математическое моделирование предсказывает возникновение высоких значений КНнС на торцах отдельных образцов, это может привести к повышенному износу не важных с точки зрения оценки интенсивности коррозионного износа поверхностей.
Кроме геометрических параметров автоклава при конструировании необходимо задать граничные технические условия: рабочую температуру ≤ 150 °C, рабочее давление 10 МПа, скорость потока 1-10 м/с.

Рис.2. Распределение касательных напряжений по поверхности образца
Кроме автоклава 1, в состав испытательной установки (рис.3) входят магнитная муфта 2, клиноременная передача 3 и электродвигатель 4. Основным преимуществом данной конструкции является простота и универсальность. Использование клиноременной передачи позволяет выбирать нужную скорость вращения изменением передаточного отношения, для чего достаточно заменить шкив. Электродвигатель с частотным регулятором обеспечивает необходимую скорость вращения на протяжении всего испытания. Использование электромагнитной муфты позволяет решить проблему уплотнений движущихся частей при большом перепаде давления.
Конструкция автоклава приведена на рис.4. Вращательный момент от электродвигателя передается через магнитную муфту 4 внутрь автоклава, на вал 5. Движение потока в автоклаве создается путем сообщения вращательного движения жидкости крыльчаткой 6. В барабане 7 закреплены девять образцов 1, они находятся на одном уровне с крыльчаткой. Для уменьшения потерь и повышения срока службы вал закреплен в подшипниках скольжения 3, 8. Для ввода и отвода газов предусмотрены три фитинга 2.
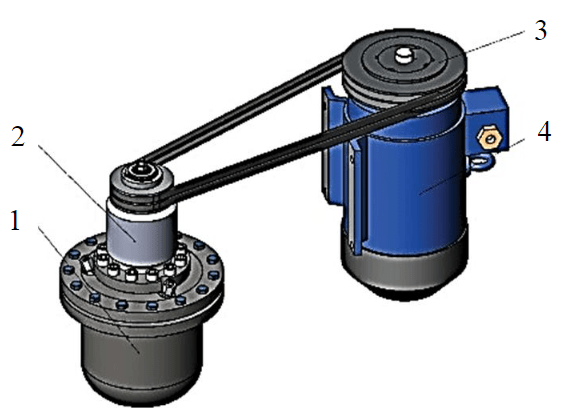
Рис.3. Общий вид испытательной установки
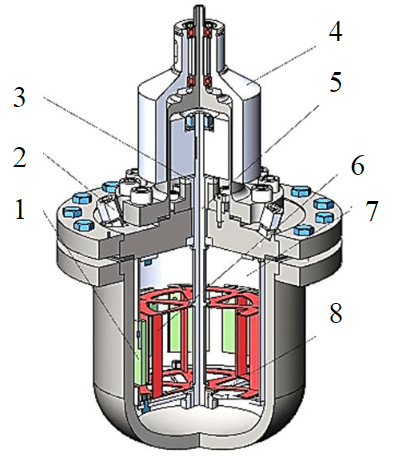
Рис.4. Автоклав

Рис.5. Автоклав для проведения динамических коррозионных испытаний

Рис.6. Образцы после автоклавных испытаний

Рис.7. Поверхность (а) и сечение (б) образца с продуктами коррозии после автоклавных испытаний (электронная микроскопия)
Для получения различных касательных напряжений, создаваемых средой на поверхности образца, предусмотрена возможность изменения расстояния между образцами и крыльчаткой, что позволяет максимально приблизиться к реальным условиям. Сконструированный автоклав для проведения динамических коррозионных испытаний представлен на рис.5.
Результаты коррозионных испытаний и их анализ
Внешний вид образцов после испытаний приведен на рис.6. Средняя скорость коррозии по результатам испытаний составила 0,011 мм/год. Образовавшиеся на поверхности образцов продукты коррозии распределены неравномерно, в основном имеют вид полос, вытянутых по направлению потока. Фазовый состав поверхности, определенный на рентгенофазовом дифрактометре, показал наличие FеСO3 – основного продукта углекислотной коррозии. На рис.7, а представлена фотография поверхности с продуктами коррозии, выполненная на сканирующем электронном микроскопе. Отложения имеют характерную для CO2-коррозии кристаллическую структуру. Микрорентгеноспектральный анализ подтвердил наличие Fe, C и O в стехиометрическом соотношении, сопоставимом с найденной фазой. На рис.7, б показано сечение образца после автоклавных испытаний. Видно, что продукты коррозии формируются не только на поверхности в виде кристаллов, но и проникают в основной металл образца, формируя небольшие язвы.
Профиль коррозионных повреждений на поверхности образцов можно сравнить с графиком распределения КНнС (см. рис.2). Образцы с коррозионными повреждениями показывают симметричный профиль повреждений, аналогичный профилю напряжения сдвига, предсказанный в ходе CFD-моделирования.
По результатам гидродинамических расчетов максимальное (в точке) значение КНнС наблюдается на расстоянии 200 мм от углового дросселя (УД), открытого на 7,4 % и составляет 16,69 Па. Выравнивание потока и стабилизация КНнС на уровне 8 Па происходит на расстоянии от УД, большем 600 мм. В случае полностью открытого дросселя КНнС составляют 2 Па.
Исходя из полученных значений КНнС, был проведен ряд экспериментов, обобщенные результаты указаны в табл.2.
Выявленные в ходе автоклавных испытаний закономерности согласуются с общепризнанными законами описания механизма углекислотной коррозии: в начале процесса происходит активное растворение металла – скорость коррозии максимальная (обычно процесс занимает несколько суток). Затем образуется несплошный слой продуктов коррозии (карбонатов железа), выступающий в качестве защитной пленки – скорость коррозии замедляется. При увеличении скорости потока происходит смыв слоя продуктов коррозии – скорость коррозии растет.
Высокие значения касательных напряжений приводят к срыву защитной пленки карбонатов железа, увеличивая скорость коррозионного процесса, что было подтверждено экспериментально (см. табл.1). При КНнС = 2 Па (дроссель открыт полностью) в отсутствии ингибитора скорость коррозии составляет 0,30 мм/год. При КНнС = 16 Па (дроссель открыт на 7,4 %) в аналогичных условиях скорость коррозии составляет уже 0,54 мм/год. Наблюдается увеличение скорости примерно в два раза.
Таблица 2
Обобщенные результаты испытаний
Номер |
КНнС, Па |
Продолжительность, ч |
Наличие |
Скорость коррозии, мм/год |
1 |
16 |
360 |
– |
0,14 |
2 |
16 |
360 |
+ |
0,04 |
3 |
26 |
360 |
+ |
0,02 |
4 |
16 |
24 |
– |
0,54 |
5 |
16 |
24 |
+ |
0,54 |
6 |
2 |
24 |
+ |
0,07 |
7 |
8 |
24 |
+ |
0,10 |
8 |
2 |
24 |
– |
0,30 |
Повышение КНнС влияет на эффективность действия ингибитора коррозии, что было подтверждено экспериментально. При КНнС = 2 Па (дроссель полностью открыт) в присутствии ингибитора (100 мг/л) скорость коррозии составляет 0,07 мм/год, а эффективность реагента 73 %. При КНнС = 16 Па (дроссель открыт на 7,4 %) скорость коррозии составляет 0,54 мм/год, т.е. равна скорости коррозии неингибируемого процесса. При промежуточном значении КНнС = 8 Па в присутствии ингибитора скорость коррозии составляет 0,10 мм/год, значит реагент еще эффективен. Таким образом, смыв защитной пленки ингибитора коррозии происходит при КНнС, находящихся в интервале 8-16 Па.
Выводы
Разработанная конструкция динамического автоклава с верхнеприводной мешалкой обеспечивает моделирование заданных условий эксплуатации для исследуемых образцов материалов. Создаваемые в автоклаве потоки обеспечивают коррозионный износ поверхности образца, аналогичный тому, что наблюдается на внутренней поверхности элементов трубопроводов обвязки газоконденсатных скважин.
Полученный в ходе испытаний равномерный износ поверхности образца подтверждает результаты математического моделирования, применяемые в ходе проектирования конструкции аппарата. Гипотеза о несовершенстве существующих подходов к проведению динамических испытаний подтверждена. Учтенные в ходе проектирования и последующих испытаний факторы, действительно оказывают существенное влияние на равномерность износа образца.
Автоклав позволяет моделировать влияние присутствия органической фазы на скорость протекания и характер коррозионных поражений на поверхности металла, а также влияние скорости вращения мешалки и, соответственно, КНнС, на скорость коррозии в присутствии/отсутствии ингибитора коррозии.
Литература
- Litvinenko V. The Role of Hydrocarbons in the Global Energy Agenda: The Focus on Liquefied Natural Gas // Resources. 2020. Vol. 9. Iss. 5. № 59. DOI: 10.3390/resources9050059
- Tcvetkov P., Cherepovitsyn A., Makhovikov A. Economic assessment of heat and power generation from small-scale liquefied natural gas in Russia // Energy Reports. 2020. Vol. 6 (2). P. 391-402. DOI: 10.1016/j.egyr.2019.11.093
- Zhukovskiy Y.L., Batueva D.E., Buldysko A.D. et al. Fossil Energy in the Framework of Sustainable Development: Analysis of Prospects and Development of Forecast Scenarios // Energies. 2021. Vol. 14 (17). № 5268. DOI: 10.3390/en14175268
- Cherepovitsyn A., Rutenko E., Solovyova V. Sustainable Development of Oil and Gas Resources: A System of Environmental, Socio-Economic, and Innovation Indicators // Journal of Marine Science and Engineering. 2021. Vol. 9 (11). № 1307. DOI: 10.3390/jmse9111307
- Цветков П.С., Федосеев С.В. Анализ специфики организации проектов малотоннажного производства СПГ // Записки Горного института. 2020. Т. 246. С. 678-686. DOI: 10.31897/PMI.2020.6.10
- Litvinenko V.S., Kozlov A.V., Stepanov V.A. Hydrocarbon potential of the Ural–African transcontinental oil and gas belt // Journal of Petroleum Exploration and Production Technology. 2017. Vol. 7 (1). P. 1-9. DOI: 10.1007/s13202-016-0248-4
- Li K., Zeng Y., Luo J.L. Influence of H2S on the general corrosion and sulfide stress cracking of pipelines steels for supercritical CO2 transportation // Corrosion Science. 2021. Vol. 190. № 109639. DOI: 10.1016/j.corsci.2021.109639
- Smith S.N., Joosten M.W. Corrosion of carbon steel by H2S in CO2 containing oilfield environments // CORROSION 2006, 12-16 March 2006, San Diego, California. NACE International, 2006. № 06115.
- Devyaterikova N., Nurmukhametova M., Kharlashin A., Popov Y. Types of corrosion damage of tubing in the oilfield // Corrosion in the Oil & Gas Industry. 2019. Vol. 121. № 03001. DOI: 10.1051/e3sconf/201912103001
- АртеменковВ.Ю., КорякинА.Ю., ДикамовД.В. идр. Организация коррозионного мониторинга на объектах второго участка Ачимовских отложений Уренгойского нефтегазоконденсатного месторождения // Газовая промышленность. 2017. № S 2. С. 74-78.
- Корякин А.Ю., Кобычев В.Ф., Колинченко И.В., Юсупов А.Д. Условия протекания углекислотной коррозии на объектах добычи Ачимовских отложений, методы контроля и прогнозирования // Газовая промышленность. 2017. №12 (761). С. 84-89.
- Алексеева Е.Л., Альхименко А.А., Ковалев М.А. и др. Оценка коррозионных свойств стальных двухслойных насосно-компрессорных труб для нефтедобычи // Материаловедение. 2021. №4. С. 10-16. DOI: 10.1134/S207511332201004X
- Федоров А.С., Алексеева Е.Л., Альхименко А.А. и др. Исследование влияния параметров испытаний на оценку стойкости сталей к углекислотной коppозии // Заводская лаборатория. Диагностика материалов. 2021. T. 87. № 12. C. 36-41. DOI: 10.26896/1028-6861-2021-87-12-42-47
- Choi Y.-S., Nešić S., Jung H.-G. Effect of Alloying Elements on the Corrosion Behavior of Carbon Steel in CO2 Environments // Corrosion. 2018. Vol. 74. № 5. P. 566-576. DOI: 10.5006/2705
- Han J. Brown B.N., Nešić S. Investigation of the Galvanic Mechanism for Localized Carbon Dioxide Corrosion Propagation Using the Artificial Pit Technique // Corrosion. 2010. Vol. 66. Iss. 9. P. 095003-095003-12. DOI: 10.5006/1.3490308
- Wang Z.M., Han X., Zhang J., Wang Z.L. In situ observation of CO2 corrosion under high pressure // The International Journal of Corrosion Processes and Corrosion Control. 2014. Vol. 49. Iss. 5. P. 352-356. DOI: 10.1179/1743278213Y.0000000144
- Kostitsyna I., Shakhmatov A., Davydov A. Study of corrosion behavior of carbon and low-alloy steels in CO2-containing environments // E3S Web of Conferences. 2019. Vol. 121. № 04006. DOI: 10.1051/e3sconf/201912104006
- ВыбойщикМ.А., ИоффеА.В., ТетюеваТ.В. идр. Деградация и разрушение нефтегазопроводных труб в средах с высоким содержанием углекислого газа и ионов хлора // Деформация и разрушение материалов. 2020. № 4. С. 29-36. DOI: 10.31044/1814-4632-2020-4-29-36
- Кашковский Р.В., Ибатуллин К.А. Некоторые аспекты углекислотной коррозии стального оборудования и трубопроводов нефтегазовых промыслов // Наука и техника в газовой промышленности. 2016. № 3 (67). С. 71-91.
- Маркин А.Н., Низамов Р.Э. CO2-коррозия нефтепромыслового оборудования. М.: Всероссийский научно-исследовательский институт организации, управления и экономики нефтегазовой промышленности, 2003. 188 с.
- Князькин С.А., Иоффе А.В., Выбойщик М.А., Зырянов А.О. Особенности коррозионного разрушения насосно-компрессорных труб при эксплуатации в средах с повышенным содержанием углекислого газа // Металловедение и термическая обработка металлов. 2012. № 10 (688). С. 10-14.
- Mazumder M.A.J., Al-Muallem H.A., Faiz M., Ali S.A. Design and synthesis of a novel class of inhibitors for mild steel corrosion in acidic and carbon dioxide-saturated saline media // Corrosion Science. 2014. Vol. 87. P. 187-198. DOI: 10.1016/j.corsci.2014.06.026
- Kovalev M., Alekseeva E., Shaposhnikov N. Investigation of hydroabrasive resistance of internal anti-corrosion coatings used in the oil and gas industry // IOP Conference Series: Materials Science and Engineering. 2020. Vol. 889. № 012020. DOI: 10.1088/1757-899X/889/1/012020
- Sun C., Liu J., Sun J. et al. Probing the initial corrosion behavior of X65 steel in CCUS-EOR environments with impure supercritical CO2 fluids // Corrosion Science. 2021. Vol. 189. № 109585. DOI: 10.1016/j.corsci.2021.109585
- Альхименко А.А., Давыдов А.Д., Харьков А.А. и др. Методы коррозионных испытаний, применяемые при разработке и промышленном освоении новых судостроительных сталей и сплавов и технологий их производства. Часть I. Лабораторные коррозионные испытания // Известия высших учебных заведений. Черная металлургия. 2022. № 65 (1). C. 48-56. DOI: 10.17073/0368-0797-2022-1-48-56
- Golubev I.A., Laptev A.B., Alekseeva E.L. et al. The effect of magnetic treatment on the effectiveness of inhibition in oilfields // E3S Web of Conferences. 2019. Vol. 121. № 02006. DOI: 10.1051/e3sconf/201912102006
- Owen J., Ducker E., Huggan M. et al. Design of an elbow for integrated gravimetric, electrochemical and acoustic emission measurements in erosion-corrosion pipe flow environments // Wear. 2019. Vol. 428. P. 76-84. DOI: 10.1016/j.wear.2019.03.010
- Ingham B., Ko M., Kear G. et al. In situ synchrotron X-ray diffraction study of surface scale formation during CO2 corrosion of carbon steel at temperatures up to 90 °C // Corrosion Science. 2010. Vol. 52. Iss. 9. P. 3052-3061. DOI: 10.1016/j.corsci.2010.05.025
- Sk M.H., Abdullah A.M., Ko M. et al. Local supersaturation and the growth of protective scales during CO2 corrosion of steel: Effect of pH and solution flow // Corrosion Science. 2017. Vol. 126. P. 26-36. DOI: 10.1016/j.corsci.2017.05.026
- Ingham B., Ko M., Laycock N. et al. In situ synchrotron X-ray diffraction study of scale formation during CO2 corrosion of carbon steel in sodium and magnesium chloride solutions // Corrosion Science. 2012. Vol. 56. P. 96-104. DOI: 10.1016/j.corsci.2011.11.017
- Kermani B., Martin J.W., Esaklul K.A. Materials Design Strategy: Effects of H2S/CO2 Corrosion on Materials Selection // CORROSION 2006, 12-16 March 2006, San Diego, California. NACE International, 2006. № NACE-06121.
- Kermani B. Depiction of Metallurgical Parameters as Governing CO2 corrosion // CORROSION 2014, 9-13 March 2014, San Antonio, Texas, USA. NACE International, 2014. № NACE-2014-3813.
- Tröger M., Bosch C., Meuser H. et al. New alloying concepts for increased corrosion resistance of welded linepipe steels in CO2 containing aqueous media // Conference EUROCORR 2013, 1-5 September 2013, Estoril, Portugal.
- Onyeji L.I., Kale G.M., Kermani M.B. Comparative Studies of the Effects of Microstructures on the Corrosion Behavior of Micro-Alloyed Steels in Unbuffered 3.5 Wt % NaCl Saturated with CO2 // International Journal of Chemical and Molecular Engineering. 2017. Vol. 11. № 2. P. 154-161. DOI: 10.5281/zenodo.1128925
- Bosch C., Poepperling R.K. Influence of Chromium Contents of 0.5 to 1.0 % on the Corrosion Behavior of Low Alloy Steel for Large Diameter Pipes in CO2 Containing Aqueous Media // CORROSION 2003, 16-20 March 2003, San Diego, California. NACE International, 2003. № 03118.
- Ali A.E.A., Cioncolini A., Laurence D., Iacovides H. Liquid lead flow-accelerated corrosion testing with the rotating cage set-up: A CFD optimization // Annals of Nuclear Energy. 2022. Vol. 165. № 108620. DOI: 10.1016/j.anucene.2021.108620
- Nesic S. Effects of Multiphase Flow on Internal CO2 Corrosion of Mild Steel Pipelines // Energy & Fuels. 2012. Vol. 26. № 7. P. 4098-4111. DOI: 10.1021/ef3002795
- Ige O.O., Barker R., Hu X. et al. Assessing the influence of shear stress and particle impingement on inhibitor efficiency through the application of in-situ electrochemistry in a CO2-saturated environment // Wear. 2013. Vol. 304. Iss. 1-2. P. 49-59. DOI: 10.1016/j.wear.2013.04.013
- Kumar A., Pacheco J.L., Desai S.K. et al. Effects of Rotating Cage Autoclave Design on Shear Stress and Flow Pattern // CORROSION 2013, 17-21 March 2013, Orlando, Florida. NACE International, 2013. № 2013-2294.
- Liu H., Feng Y., Yao Y. et al. Effect of the 345 °C and 16.5 MPa autoclave corrosion on theoxidation behavior of Cr-coated zirconium claddings in the high-temperature steam // Corrosion Science. 2021. Vol. 189. № 109608. DOI: 10.1016/j.corsci.2021.109608
- Zhao Y., Li X., Zhang C. et al. Investigation of the rotation speed on corrosion behavior of HP-13Cr stainless steel in the extremely aggressive oil field environment by using the rotating cage test // Corrosion Science. 2018. Vol.145. P. 307-319. DOI: 10.1016/j.corsci.2018.10.011