Научное обоснование и разработка инновационных процессов извлечения циркония и РЗЭ при глубокой и комплексной переработке эвдиалитового концентрата
- д-р техн. наук академик РАН ИПКОН имени академика Н.В.Мельникова РАН ▪ Orcid
Аннотация
На основе комплекса современных методов анализа изучено влияние различных кислот и энергетических воздействий на морфологию, элементный состав, структурно-химические преобразования поверхности минералов и эффективность процесса выщелачивания эвдиалитового концентрата. Вскрыт механизм и выявлены оптимальные условия и специфические особенности разрушения эвдиалита и породных минералов и извлечения циркония и РЗЭ при воздействии различных кислот, мощных наносекундных импульсов, диэлектрического барьерного разряда, электрохимической обработки, механохимической активации и ультразвука. Теоретически и экспериментально обоснован механизм образования и оптимальные условия диспергации силикагеля в зависимости от методов и параметров энергетических воздействий. Научно обоснована и апробирована комбинированная трехстадиальная схема азотнокислотного выщелачивания эвдиалитового концентрата с ультразуковой обработкой суспензии, обеспечивающая 97,1 % извлечения циркония и 94,5 % РЗЭ. Теоретически и экспериментально обоснованы условия селективного осаждения циркония и РЗЭ.
Введение
Большинство редких и редкоземельных металлов являются основой в создании конструкционных материалов для электроники, космической отрасли, зеленой энергетики и других изделий оборонного комплекса [1, 2].
Производство редких и РЗЭ затруднено из-за низкого содержания в рудах, нахождения их в рассеянном состоянии в других минералах и сложного вещественного состава редкометалльного сырья [3-5]. Организация такого производства должна проводиться с учетом мировой практики и перспектив создания полного технологического цикла от добычи до промышленного использования [6-8].
Технологические схемы получения редких и РЗЭ (La – лантаноиды, Y, Sc) из руд для каждого типа сырья индивидуальны и включают, как правило, следующие последовательные стадии: получение концентратов металлов с использованием флотационных и гравитационно-магнитоэлектрических схем обогащения; разложение концентратов (обжиг, сплавление, выщелачивание); получение чистых химических соединений металлов (кристаллизация, сорбция, экстракция, ионный обмен, химическое осаждение и др.) и далее металлов (цементация, электролиз и др.) [9, 12]. Вследствие близости свойств РЗЭ их селективное разделение является сложной технологической задачей [13-15]. Современные схемы разделения РЗЭ основаны на использовании процессов жидкостной экстракции и ионного обмена, а также методов избирательного окисления кислородом, хлором, пероксидом водорода и восстановления цинком, амальгамами цинка и натрия [16-19].
В России для производства редких и РЗЭ могут эффективно вовлекаться в переработку эвдиалитовые руды Ловозерского месторождения (запасы оксидов Zr – 300 млн т, РЗМ – 60-70 млн т) [20, 21].
Эвдиалитовые руды, содержащие 25-27 % эвдиалита, 52 % полевого шпата, лопарита и нефелина, 20 % эгирина, могут перерабатываться по комбинированным флотационно-гравитационно-магнитоэлектрическим схемам обогащения с получением эвдиалитового и лопаритового концентратов [22, 23]. При этом получаемые эвдиалитовые концентраты при минимальной радиоактивности содержат оксиды Si (54 %), Zr (11-13 %), РЗЭ (1,8-2,5 %), Hf (0,21-0,27 %), Ta (0,06-0,1 %), Nb и Ti (0,6-1 %), Sr (0,95-1,48 %) [24, 25].
Существующие технологии извлечения циркония и редкоземельных элементов из эвдиалитовых концентратов основаны на их многостадиальном разложения кислотами и щелочами [25, 26]. При этом, из-за высокого содержания кремния в составе концентрата, в растворе кислотного выщелачивания образуется силикатный гель. Силикатный гель сорбирует ценные компоненты, существенно снижая извлечение циркония и РЗЭ в продуктивные растворы и затрудняя их дальнейшую фильтрацию и экстракционно-сорбционную переработку [27-29].
В последние годы решение данной проблемы достигается за счет предварительной обработки минеральных суспензий мощными энергетическими воздействиями (электрохимическая обработка, ультразвук, обработка электромагнитными полями высокой напряженности, механоактивация и др.), обеспечивающих как модифицирование структурно-химических и морфологических свойств эвдиалита, разрушение силикагеля, так и интенсификацию процессов выщелачивания [30-32].
Методология
Эвдиалитовый концентрат имел следующий состав, %: ZrO2 – 11,5; РЗЭ – 2,5; SiO2 – 44,47; Na2O − 10,5; K2O – 1,37, TiO2 – 3,29; Fe2O3 – 5,2; Cl – 0,97; CaO – 5,42; SrO – 2,63; Al2O3 – 6,9; MnO – 1,66; SrO – 1,95; Nb2O5 – 0,94; MgO – 0,2; BaO − 0,15; прочее – 0,35. Общий вид концентрата и частицы эвдиалита представлены на рис.1
Концентрат также содержит 10 % полевых шпатов, нефелина, эгирина и их сростков, около 3 % сдвойникованных кристаллов лопарита-(Ce), золотисто-коричневые кристаллы лампрофиллита. В акцессорных количествах отмечаются вторичные цеолиты (натролит, гоннардит).
Вскрытие концентрата различными кислотами и щелочью проводили в автоклаве TOP120 INDUSTRIE и в реакторе, в котором используются электрохимические, термические и ультразвуковые воздействия на минеральную суспензию [30].
Материал проб измельчали в лабораторной шаровой мельнице МШЛ-1 до крупности менее 40 мкм. Для предварительной механической активации (МА) проб эвдиалитового концентрата использовали планетарную центробежную мельницу (ПЦМ) марки ЛАИР-0.015 (НИТУ МИСиС). Обработку концентрата электромагнитными полями высокой напряженности (МЭМИ) и низкотемпературной плазмой – диэлектрическим барьерным разрядом (НТП-ДБР) осуществляли на экспериментальных лабораторных стендах (ИПКОН РАН, ООО «НПП ФОН»). Технические параметры МЭМИ: напряженность электрического поля электродной системы, Е – до 107 В/м; длительность импульсного воздействия τи ~ 10-150 нс; частота повторения импульсного воздействия V = 100-1000 Гц; амплитуда напряжения импульсов U – до 70 кВ. Параметры обработки диэлектрическим барьерным разрядом (НТП-ДБР): длительность переднего фронта импульса 250-300 нс; длительность импульса 8 мкс; амплитуда напряжения 20 кВ; частота повторения импульсов 16 кГц; продолжительность обработки 30 с; расстояние между электродами 5 мм.
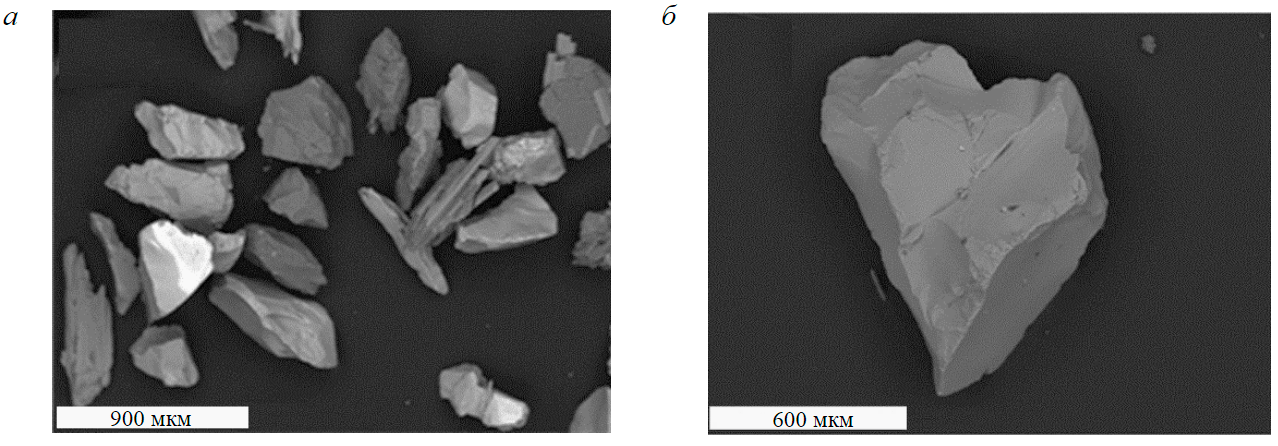
Рис.1. Микрофотографии концентрата (а) и отдельных зерен (б) эвдиалита
Ультразвуковая обработка суспензии осуществлялась с использованием диспергатора (МЭФ-15, МЭЛФИЗ) мощностью 600 Вт, рабочей частотой 22±1,65 кГц и амплитудой колебаний 25±5 мкм.
Химический и фазовый состав продуктивных растворов выщелачивания, кека и силикатного геля изучали методом масс-спектроскопии с индуктивно-связанной плазмой (ИСП-МС) (ICPE-9000, «Shimadzu») рентгенофлуоресцентным анализом (РФЛА) (ARL ADVANT’X, «Thermo Scientific»), рентгенофазовым анализом (РФА) (дифрактометр АДП-2, НПО «Буревестник»). Морфологию и элементный состав поверхности минералов исследовали методом растровой электронной микроскопии (РЭМ-РСМА) на микроскопе LEO 1420VP, оснащенном энергодисперсионным микроанализатором Oxford INCA Energy «Carl Zeiss». Для регистрации ИК-спектров минеральных частиц эвдиалита использовали Фурье-спектрометр IR-Affinity «Shimadzu» и приставку диффузного отражения DiffuseIR «PikeTechnologies». Рентгеновские фотоэлектронные спектры поверхности частиц эвдиалита регистрировали с помощью спектрометра Versa Probe II «ULVAC-PHI».
Обсуждение
Кислотное выщелачивание эвдиалитового концентрата
По данным РЭМ-РСМА эвдиалит, нефелин и лампрофиллит по-разному реагируют на воздействие кислот, а степень растворения (разрушения) их поверхности зависит от типа используемой кислоты. При этом форма частиц калиевого полевого шпата, лопарита и эгирина под воздействием кислот не изменяется.
По эффективности воздействия азотной кислотой выделены три группы минералов концентрата: хорошо растворимые эвдиалит и нефелин; поддающиеся частичному выщелачиванию лампрофиллит и водные алюмосиликаты K и Na, практически не растворимые эгирин, лопарит и полевые шпаты (каркасные алюмосиликаты K, Na и Ca). Методами РФЭС и ИК-спектроскопии установлено, что растворение эвдиалитового концентрата азотной кислотой происходит за счет разрушения структуры минералов, разрушения силикатного каркаса, перехода катионов Al, Na
и Mn и кремния в раствор. При этом кремний образует гелеобразные фазы типа силикагеля SiO2∙nH2O.
Под воздействием раствора соляной кислоты участки поверхности зерен эвдиалита активно растворяются с проникновением выщелачивающего раствора в объем зерен и появлением серий глубоких, вертикальных, параллельно ориентированных трещин (рис.2, а). Серная кислота (рис.2, б) растворяет эвдиалит более активно и равномерно как с поверхности, так и из объема частиц, образуя на поверхности нерастворившихся минералов устойчивые кристаллы гипса и целестина (рис.3).
Наиболее значимые изменения структурно-химические свойств поверхности эвдиалита наблюдаются под воздействием раствора соляной кислоты: изменяется симметрия в ИК-спектрах и развивается профиль спектральной кривой в области валентных колебаний связей Si-О-Si (800-1350 см–1) в структуре минерала. Выявленные изменения характеристик спектральных кривых являются следствием искажения каркаса минерала, обусловленного выносом из структурных мотивов эвдиалита катионов Na, Ca, Mg и т.д.

Рис.2. Частицы эвдиалита после выщелачивания в соляной (а), серной (б) и азотной (в) кислотах
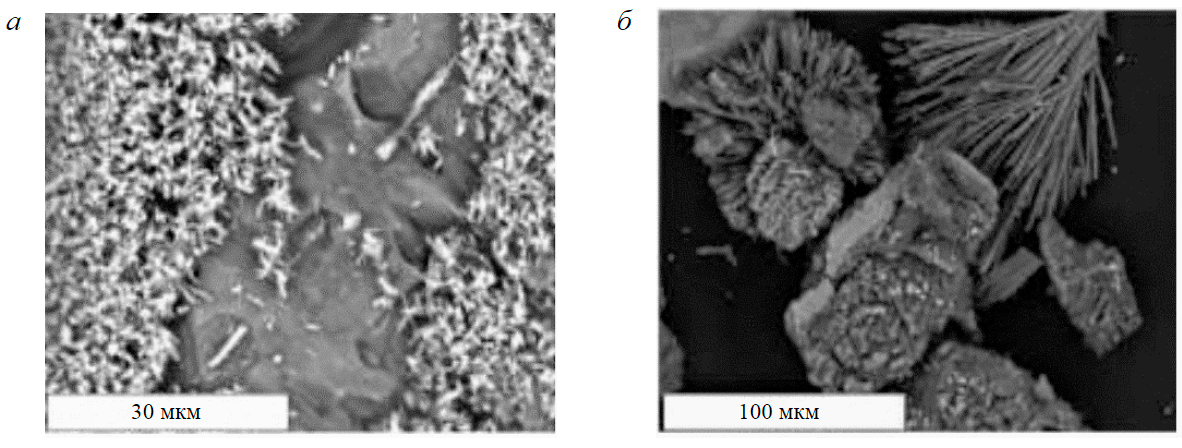
Рис.3. Целестин SrSO4 (а) и гипс CaSO4·2Н2O (б), образовавшиеся на поверхности частиц минералов эвдиалитового концентрата при выщелачивании серной кислотой
Анализ элементного состава основных элементов поверхности частиц эвдиалита методом РФЭС позволил выявить ее эффективное разрушение, сопровождающееся переводом в раствор катионов, входящих в состав минерала: Al, Na, Ca, Mg, K, Ti, Mn, Fe, Sr, Zr. В порядке убывания концентрации катионов на поверхности «исходного образца» эвдиалита воздействие кислотами можно расположить в ряд HNO3 → H2SO4 → HCl. Выявлено снижение концентрации, ат.%: Al – в 2-28 раз, Na – 3,6-61, Сa, Mg и Mn – 2,5-5, Ti – 3-9, Zr – 3-12 (табл.1).
Таблица 1
Состав поверхностного слоя частиц эвдиалита (данные рентгеновской фотоэлектронной спектроскопии)
Кислота |
Элементный состав, ат. % |
ΣMe/Si |
||||||||||||||
N |
O |
S |
F |
Na |
Mg |
Ca |
Al |
Si |
K |
Ti |
Mn |
Fe |
Sr |
Zr |
||
Без обработки |
0,6 |
60,0 |
н.о. |
0,6 |
12,2 |
0,5 |
0,5 |
2,8 |
14,8 |
0,4 |
0,9 |
0,5 |
0,7 |
0,4 |
1,2 |
1,36 |
NHO3 |
1,9 |
66,2 |
н.о. |
0,1 |
3,4 |
0,2 |
0,2 |
1,4 |
19,2 |
0,2 |
0,6 |
0,2 |
0,5 |
0,2 |
1,2 |
0,42 |
H2SO4 |
0,3 |
69,2 |
2,2 |
< 0,1 |
0,9 |
0,1 |
0,1 |
0,1 |
23,1 |
0,1 |
0,3 |
0,2 |
0,2 |
0,5 |
0,1 |
0,11 |
HCl |
0,2 |
70,2 |
н.о. |
0,1 |
0,2 |
< 0,1 |
< 0,1 |
< 0,1 |
24,6 |
н.о. |
0,1 |
< 0,1 |
0,1 |
н.о. |
0,4 |
0,05 |
Методом РФЛА установлено активное растворение эвдиалитового концентрата соляной и серной кислотами. Наиболее эффективное растворение эвдиалитового концентрата (масса навески снижается на 76 % от исходной величины) и, соответственно, максимальное общее извлечение Zr (91,5 %) и РЗЭ (82,5 %) обеспечивает серная кислота. При обработке азотной кислотой
в раствор переходит 56 % массы концентрата при извлечении Zr 76,9 % и РЗЭ 79,6 %, а в случае использования соляной кислоты в раствор переходит 46 % массы концентрата при извлечении Zr 83,91 % и РЗЭ 83,6 %.
Установлено следующее содержание силикагеля в твердом остатке выщелачивания концентрата: 45-65 % для азотной кислоты, 64 для серной и 70,5 для соляной. Данные результаты хорошо согласуются с объемами силикагеля в растворах выщелачивания.
Наиболее высокий объемный процент силикатного геля после пяти суток отстаивания наблюдается при использовании серной кислоты – 63 %, для азотной кислоты – 55 %, соляной – 48 %. После центрифугирования растворов уплотнение силикагеля увеличивается в 1,65-1,85 раз.
При кислотном выщелачивании силикатов [33, 34] выявлено взаимодействие кремниевой кислоты с сульфат-ионами через водородные связи и с ионами металлов, например Al3+, по реакциям, представленным на рис.4. На основании этих реакций можно предполагать образование большого объема силикагеля при минимальных потерях Zr в случае использования серной кислоты (рис.4, а) и более высокие потери циркония и других высокозарядных катионов, характеризующихся высоким отношением заряда к ионному радиусу, в случае азотной кислоты (рис.4, б).

Рис.4. Взаимодействия молекул кремниевой кислоты с сульфат-ионами: а – через водородные связи; б – с ионами металлов (например, Al3+)
Анализ элементного состава продуктивных растворов выщелачивания позволил установить, что абсолютные (от исходного) потери Zr и РЗЭ, связанные с силикатным гелем при сернокислотном выщелачивании, составляют около 26,9 и 70,2 %, соответственно, тогда как при азотнокислотном потери Zr и РЗЭ – 41,0 и 44,2 %, а использование соляной кислоты приводит к существенному снижению потерь Zr и РЗЭ до 8,3 и 18,8 %.
Низкие потери циркония и РЗЭ при выщелачивании соляной кислотой определяются минимальным объемом образующегося геля, что, вероятно, связано с активным переходом в раствор катионов Ti, взаимодействующих с молекулами кремниевой кислоты, ограничивая скорость поликонденсации (табл.2). Однако, рекомендовать использование солянокислотного выщелачивания в промышленных условиях проблематично из-за высокой агрессивности соляной кислоты к конструкционным материалам.
Таблица 2
Потери ценных компонентов с силикатным гелем и их концентрация в продуктивных растворах
Кислота |
Потери с гелем, % |
Концентрация, г/дм3 |
||
Zr |
ΣРЗМ |
Zr |
ΣРЗМ |
|
H2SO4 |
29,38 |
85,05 |
4,59 |
0,222 |
HCl |
9,94 |
22,47 |
5,04 |
0,999 |
HNO3 |
53,39 |
55,56 |
2,35 |
0,494 |
HNO3 (УЗ) |
32,25 |
35,03 |
3,12 |
0,637 |
Высокие потери редкоземельных элементов в результате использования в качестве выщелачивающего агента серной кислоты обусловлено осаждением редких земель и титана из продуктивного раствора в виде сульфатов. На рис.5, 6 представлены пластинчатые ромбические сростки кристаллов предположительно REE2(SO4)3 и хорошо ограненные кубические кристаллы двойных сульфатов кальция и титана CaTi(SO4)3. Крупность кристаллов вновь образованных сульфатов 20 мкм и менее, что приводит к захвату значительной массовой доли этих фаз силикатным гелем, определяет высокие потери в нем РЗЭ и, соответственно, низкое (12,3 %) извлечение ∑РЗЭ в продуктивный раствор.
Кроме того, на основе данных рентгенофазового анализа образцов силикатного геля при выщелачивании эвдиалитового концентрата растворами H2SO4, HCl и HNO3 выявлены нанофрагменты основных минералов концентрата, а также ряд новообразованных слабо раскристаллизованных фаз, таких как нитрат натрия, хлорид натрия, гипс.
Потери циркония и РЗЭ с гелем составляют 29,4 и 85,1 % для серной, 53,4, 55,6 % для азотной и 9,9, 22,5 % для соляной кислот (табл.2). В работе [30] предложено выделять ценные компоненты из кека промывкой водой и осаждением Na2CO3.
После удаления геля центрифугированием проведен расчет относительных потерь с ним ценных компонентов от общего извлечения в гель и раствор (табл.2). Относительные потери ценных компонентов с силикатным гелем при выщелачивании азотной кислотой можно объяснить активной сорбцией катионов Zr и РЗЭ за счет их высокого заряда.
Результаты выщелачивания эвдиалитового концентрата азотной кислотой близки к показателям, полученным при солянокислотном выщелачивании Zr – 76,9 % и РЗЭ – 79,6 %. Кроме того, по сравнению с серной кислотой, потери РЗЭ с силикатным гелем сокращаются в 1,6 раза с 70,2 до 44 %.
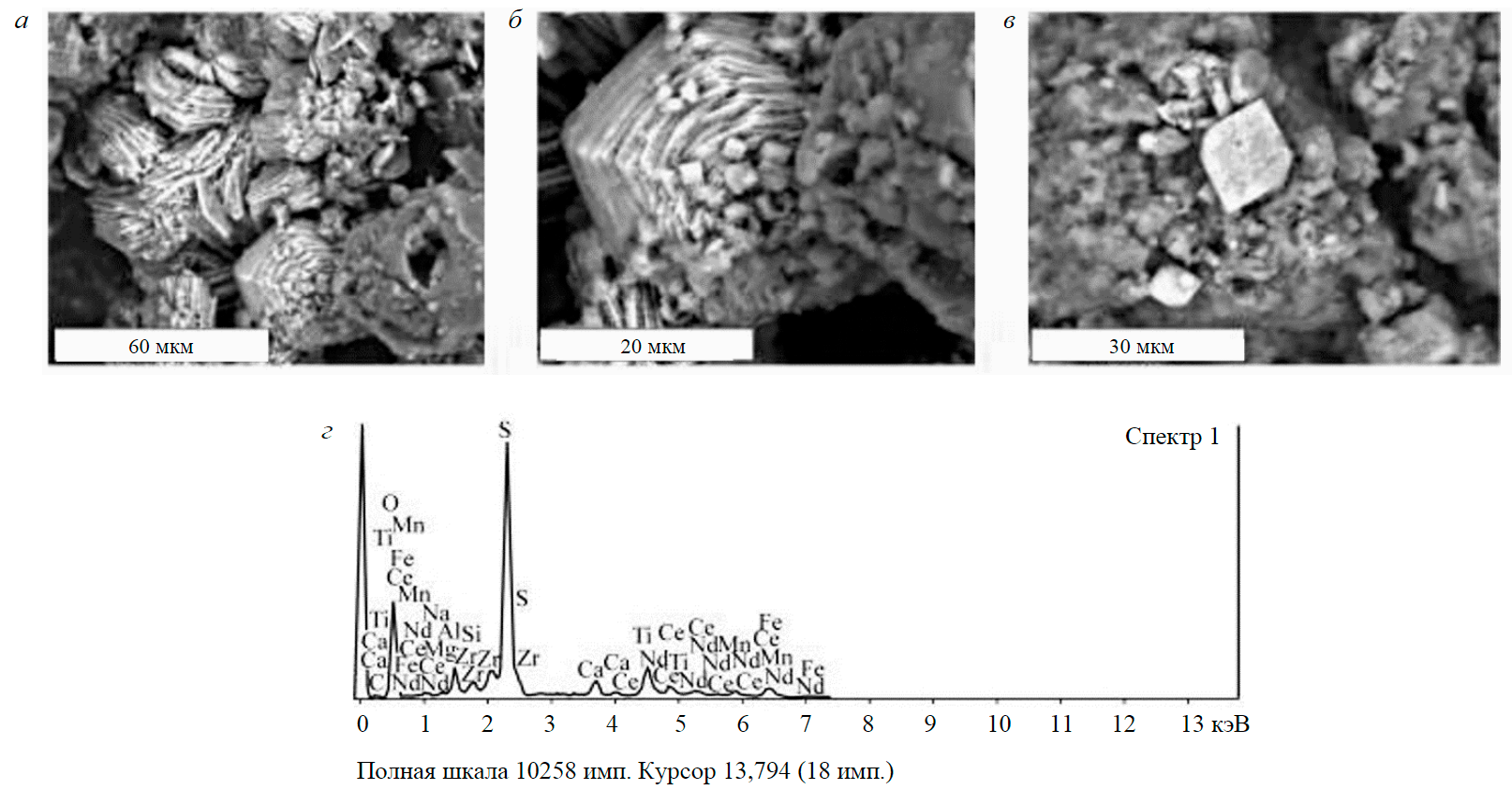
Рис.5. Кристаллы (а), сростки (б, в) и энергодисперсионный спектр (г) REE2(SO4)3
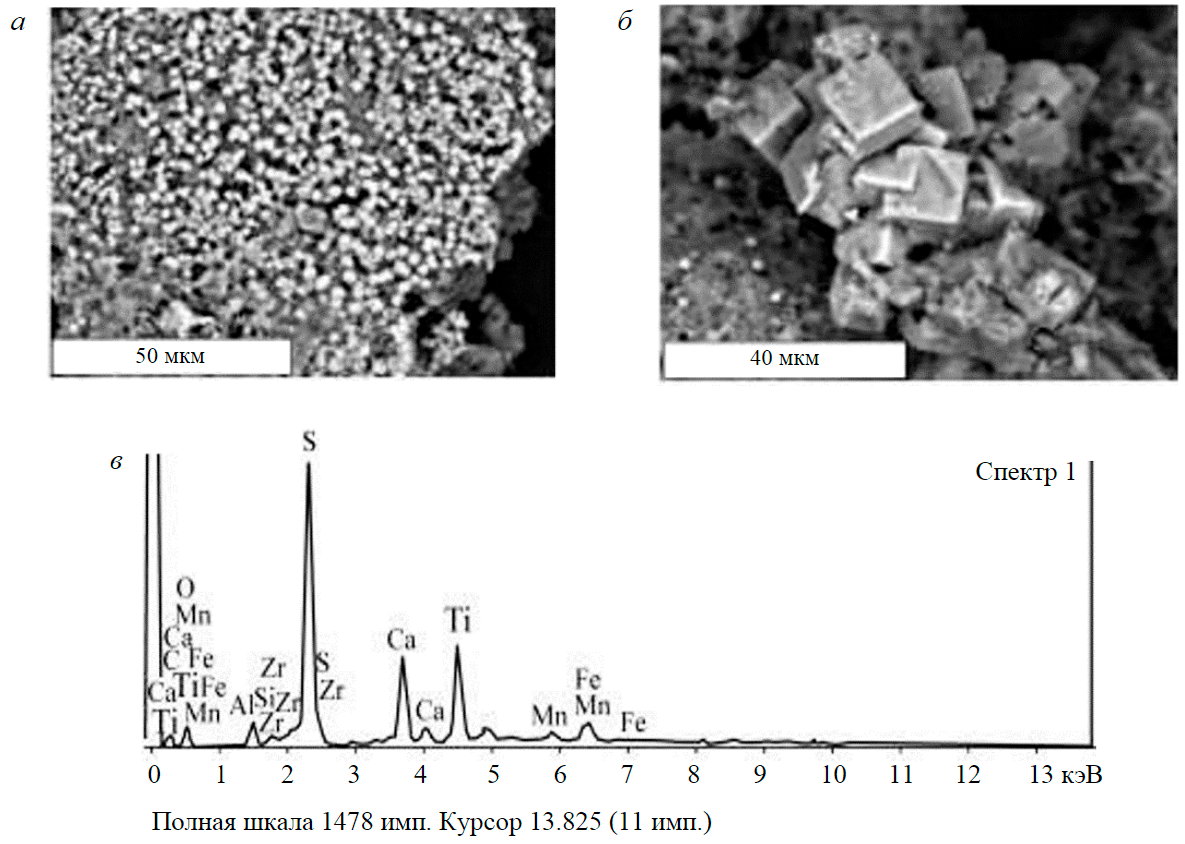
Рис.6. Кристаллы (а, б) и энергодисперсионный спектр CaTi (SO4)3 (в)
Таким образом, установлено, использование азотной кислоты наиболее экономически и технологически целесообразно, так как обеспечивает высокие качественно-количественные показатели выщелачивания эвдиалитового концентрата и сокращение потерь РЗЭ с силикатным гелем, в связи с чем дальнейшие исследования проводились с использованием азотной кислоты.
Влияние энергетических воздействий на структурно-химические свойства, фазовый состав основных минералов эвдиалитового концентрата и эффективность азотнокислотного выщелачивания
Ранее проведенными исследованиями установлена возможность использования энергетических воздействий для направленного модифицирования поверхностных свойств минералов, селективной дезинтеграции и интенсификации процессов вскрытия упорных концентратов [21, 35]. В данной работе изучено влияние энергетических воздействий (ультразвук, низкотемпературная плазма, МЭМИ и электрохимическая обработка) и предварительной механической активации (стандартное измельчение и механоактивация) эвдиалитового концентрата на морфологию, текстурно-структурные особенности, вещественный состав, интенсивность образования (деструкции) силикатного геля и эффективность извлечения ценных компонентов.
По данным рентгенофазового и минералогического анализа преобладающей фазой в исследованных пробах исходного неизмельченного концентрата является эвдиалит. В подчиненном количестве присутствует лампрофиллит и лопарит. Отмечаются единичные знаки эгирина, нефелина, полевых шпатов [30].
После выщелачивания исходного концентрата при всех режимах наблюдается снижение интенсивностей основных диагностических пиков эвдиалита, свидетельствующее об его частичном растворении.
На основе изучения поверхности минералов с использованием атомно-силовой микроскопии выявлено образование на поверхности эвдиалита осадка силикатного геля в результате воздействия азотной кислотой. Объем силикатного геля на поверхности эвдиалита снижается при энергетических воздействиях, главным образом ультразвука (рис.7, в). На поверхность эrирина, полевых шпатов и лопарита азотнокислотное и ультразвуковое воздействия заметного влияния не оказывают.
Электрохимическая обработка суспензии приводит к существенному снижению площади поверхности эвдиалита, покрытой гелем. По элементному составу свободные от геля области поверхности минерала соответствуют исходному эвдиалиту, однако количественно содержание ∑РЗЭ значительно снижается и находится ниже предела обнаружения энергодисперсионного спектрометра.
Ультразвуковая обработка суспензии способствует удалению силикатного геля с поверхности эвдиалита и активному растрескиванию зерен минерала, вплоть до их полного разрушения.
После выщелачивания с предварительной МА наблюдается снижение интенсивностей пиков эвдиалита и нефелина на рентгенограммах проб, подтверждающее их активное растворение
и аморфизацию поверхности. Для эгирина и минералов группы полевых шпатов эти изменения менее заметны [24].
Следовательно, все рассмотренные энергетические воздействия обуславливают образование неоднородной морфологически сложной поверхности частиц, разрушение и удаление силикатного геля с поверхности минералов.
По данным ИСП-МС анализа кека выщелачивания концентрата установлено: электрохимическая обработка суспензии позволяет на 5,1-3,6 % повысить извлечение циркония и суммы РЗЭ; ультразвуковая обработка за счет эффективной очистки поверхности эвдиалита от силикагеля повышает извлечение суммы РЗЭ и циркония на 28,9-43,9 % (табл.3).
Предварительное измельчение концентрата до класса –40 мкм обеспечивает повышение извлечения РЗЭ и циркония на 34,1-40,9 %. Механоактивация эвдиалитового концентрата приводит к увеличению извлечения РЗЭ и циркония на 35,0-44,9 %. Ультразвуковая обработка суспензии после механоактивации снижает извлечение на 3,6-5,7 %, что обусловлено образованием аморфной фазы, сорбирующей из раствора ионы и ионные группировки.
Таблица 3
Извлечение циркония и суммы РЗЭ от вида энергетических воздействий
Вид измельчения |
Энергетические воздействия |
Извлечение, % |
|
Zr |
∑РЗЭ |
||
Без измельчения |
Без обработки |
12,5 |
18,2 |
Без измельчения |
Электрохимическая обработка |
17,6 |
21,8 |
Без измельчения |
Ультразвуковая обработка |
56,4 |
47,1 |
Стандартное измельчение |
Без обработки |
53,4 |
52,3 |
Стандартное измельчение |
Электрохимическая обработка |
75,8 |
64,8 |
Стандартное измельчение |
Ультразвуковая обработка |
76,8 |
68,5 |
Механоактиваuия |
Без обработки |
57,4 |
53,2 |
Механоактиваuия |
Ультразвуковая обработка |
53,8 |
47,5 |
Мощные электромагнитные импульсные воздействия (МЭМИ, ДБР) также оказывают существенное деструктивное влияние на структурное состояние поверхности эвдиалита, что вызывает активацию процесса растворения минеральных частиц в азотной кислоте и повышает эффективность кислотного выщелачивания эвдиалитового концентрата, которую оценивали на основе химического анализа кеков и расчета показателей выщелачивания с учетом материального баланса (табл.4).
Таблица 4
Влияние параметров мощных электромагнитных импульсных воздействий на эффективность выщелачивания эвдиалитового концентрата
Условия обработки |
Извлечение элементов, % |
Суммарное извлечение РЗМ, % |
|||||
Zr |
Ce |
Hf |
La |
Nd |
Y |
||
Без обработки |
86,6 |
87,5 |
84,9 |
86,2 |
88,4 |
89,7 |
87,7 |
МЭМИ (30 с) |
89,9 |
88,4 |
89,9 |
87,2 |
89,9 |
92,4 |
89,5 |
МЭМИ (60 с) |
90,9 |
88,2 |
90,7 |
85,7 |
90,1 |
92,8 |
89,4 |
МЭМИ (90 с) |
90,2 |
87,6 |
89,5 |
85,8 |
89,4 |
92,3 |
88,9 |
ДБР (30 с) |
90,6 |
87,9 |
89,4 |
85,9 |
89,9 |
92,8 |
89,2 |

Рис.7. Поверхность эвдиалита: а – после выщелачивания; б, в – после выщелачивания с электрохимической и ультразвуковой обработкой
В целом предварительная обработка МЭМИ позволила повысить извлечение циркония в продуктивный раствор выщелачивания на 3,4-4,3 %, при использовании ДБР прирост извлечения составил 4,0 %. Максимальный прирост извлечения циркония (4,3 %) был достигнут в результате обработки концентрата МЭМИ в течение tобр = 60 с, что сопоставимо с результатом, полученном при кратковременном (tобр = 30 с) действии барьерного разряда (4,1 %). Повышение суммарного извлечения редкоземельных элементов составило 1,2-1,8 %.
Следовательно, максимальная интенсификация азотнокислотного выщелачивания эвдиалитового концентрата достигается при комбинировании предварительного измельчения концентрата до класса –40 мкм с ультразвуковой обработкой суспензии. Это объясняется увеличением удельной поверхности эвдиалита, очисткой зерен от аморфных фаз (силикатного геля) и формированием дополнительных неоднородностей и дефектов на поверхности минералов, способствующих их более активному растворению.
Рациональные параметры азотнокислотного выщелачивания эвдиалитового концентрата в условиях энергетических воздействий
Для оценки наиболее существенных факторов энергетических воздействий, влияющих на извлечение ценных компонентов в процессе азотнокислотного выщелачивания эвдиалитового концентрата, проведены отсеивающие эксперименты с использованием математической модели (план Плакетта – Бермана) [7].
Анализ полученных экспериментальных данных показал, что наиболее существенными факторами, влияющими на извлечение циркония, являются: ультразвук, температура, время выщелачивания, измельчение. Так, зависимость извлечения Zr в продуктивный раствор от продолжительности ультразвуковых воздействий на минеральную суспензию описывается линейным уравнением и достигает максимальных значений только при постоянной обработке суспензии УЗ. Ультразвуковая обработка суспензии обеспечивает повышение извлечения циркония на 8,5 %, суммы РЗЭ – на 4,3 %, при снижении потерь с силикатным гелем до 29,4 %.
Прирост извлечения циркония обусловлен тем, что в процессе ультразвуковой обработки суспензии происходит интенсивное растрескивание и разрушение частиц эвдиалита. Кроме того, использование ультразвуковой обработки в процессе выщелачивания эвдиалитового концентрата предотвращает образование силикагеля, приводя к снижению его объема на 8,2 % с 55 до 46,8 об.% Использование электрохимической обработки снижает объем силикатного геля на 3,5 % с 55 до 51,5 %.
Предварительное воздействие НТП не приводит к значительному снижению объемов образующего в процессе выщелачивания силикатного геля, объем геля после отстаивания составляет 51,4-55,9 об.%. Общее извлечение Zr и РЗЭ незначительно повышается на 1-2,5 %, а их потери с силикатным гелем снижаются на 4,5-6 %.
Ввиду высоких эксплуатационных затрат на измельчение концентрата и образования большого количества силикагеля в процессе выщелачивания тонкоизмельченного концентрата, операция предварительного измельчения концентрата перед процессом кислотного выщелачивания нецелесообразна.
На первой стадии отработки технологии был опробован двухстадиальный процесс выщелачивания эвдиалитового концентрата, позволяющий повысить извлечение циркония на 9,6 % (с 76,9 до 86,5), РЗЭ на 1,7 % (с 79,6 до 81,3), при этом на 10,3 % (с 55 до 65,3) возрастает суммарный объем образующегося силикатного геля, что, соответственно, приводит к увеличению потерь Zr с 41 до 51,9 %, РЗЭ с 44,2 до 50,8 %. Дальнейшее увеличение количества стадий выщелачивания с двух до трех обеспечивает незначительное повышение извлечения Zr и ΣРЗЭ в продуктивный раствор: для Zr – на 4,6 % с 86,5 до 91,1, для ΣРЗЭ – на 1,9 % с 81,3 до 83,2, тогда как суммарный объем силикатного геля повышается до 69,7 %. Полученные данные (табл.5) подтверждают наличие в нерастворенном остатке после третьей стадии выщелачивания эвдиалитового концентрата в оптимальных условиях незначительной части эвдиалита, а также практически нерастворимых в азотной кислоте полевых шпатов, эгирина и лопарита и, соответственно, нецелесообразность увеличения продолжительности азотнокислого выщелачивания эвдиалитового концентрата свыше 3 ч (трех стадий).
Таблица 5
Массовая доля элементов в исходном (№ 1) эвдиалитовом концентрате и после третьей стадии его кислотного выщелачивания (№ 2)
Концентрат |
Si |
ZrO2 |
TiO2 |
∑SrO, BaO, Ca |
Mn |
Ta2O5 |
Nb2O5 |
∑РЗМ |
H2O |
Прочее |
№ 1 |
22,7 |
8,34 |
3,99 |
5,43 |
1,42 |
0,074 |
0,94 |
2,50 |
0,38 |
47,79 |
№ 2 |
27,0 |
3,15 |
4,83 |
2,56 |
0,53 |
0,13 |
1,45 |
3,13 |
2,71 |
48,36 |
В связи с тем, что наиболее интенсивное растворение эвдиалита и, соответственно, образование силикатного геля происходит на первой и второй стадиях выщелачивания, в работе исследована возможность снижения потерь ценных компонентов за счет уменьшения продолжительности первых двух стадий при увеличении продолжительности третьей стадии выщелачивания (при сохранении общей продолжительности процесса). Сокращение 1-й и 2-й стадий выщелачивания с 60 до 40 мин и увеличение 3-й стадии до 100 мин приводит к повышению уровня извлечения Zr на 5,1 % (с 91,1 до 96,2), РЗЭ – на 9,6 % (с 83,2 до 92,8). При этом объем силикатного геля возрастает всего на 1,6 %, а потери Zr и РЗЭ остаются на прежнем уровне (41,5 и 44,7 %, соответственно). Дополнительное использование на 1-й стадии выщелачивания ультразвуковых воздействий способствует повышению извлечения Zr на 0,9 % (с 96,2 до 97,1), РЗЭ – на 1,7 % (с 92,8 до 94,5) и значительному снижению объема образующего силикатного геля (с 56,6 до 47 %) что приводит к сокращению потерь ценных компонентов до 31,4 и 33,8 %, соответственно.
Таким образом, разработанный трехстадийный процесс азотнокислотного выщелачивания эвдиалитового концентрата с ультразвуковой обработкой суспензии на первой стадии является оптимальным и обеспечивает извлечение циркония до 97,1 % и РЗЭ до 94,5 %.
Извлечение циркония и РЗЭ из продуктивных растворов выщелачивания эвдиалитового концентрата
В существующих технологиях переработки продуктивных растворов РЗЭ для выделения и селективного разделения ценных компонентов применяются как классические реакции избирательного осаждения, так и современные методы, основанные на процессах комплексообразования и ионного обмена с использованием различных типов реагентов (трибутилфосфата, солей четвертичных аммониевых оснований, карбоновых кислот и др.).
Поскольку концентрации циркония и РЗЭ в продуктивных растворах выщелачивания эвдиалитового концентрата, как правило, не превышают 1-10 г/дм3, проведено исследование возможности последовательного химического осаждения циркония и РЗЭ из продуктивного раствора. Данный метод, характеризующийся технологической простотой и низкими эксплуатационными затратами, позволяет получить легкорастворимые в слабокислых растворах осадки Zr и РЗЭ, пригодные для последующей переработки. Концентрация РЗЭ в исходном продуктивном растворе представлена в табл.6.
Таблица 6
Концентрации РЗЭ в исходном продуктивном растворе
Элемент |
Концентрация, мг/дм3 |
Элемент |
Концентрация, мг/дм3 |
Sc |
0,4 |
Gd |
23,1 |
Y |
138,0 |
Tb |
4,1 |
La |
76,7 |
Dy |
23,2 |
Ce |
182,6 |
Ho |
4,8 |
Pr |
22,5 |
Er |
12,9 |
Nd |
66,1 |
Tm |
2,0 |
Sm |
20,1 |
Yb |
11,1 |
Eu |
6,7 |
Lu |
1,6 |
Разделение Zr и РЗЭ с сопутствующей нейтрализацией продуктивных растворов проводили в две стадии. На первой – нейтрализацию азотной кислоты с выделением Zr с примесями Al и Fe обеспечивали повышением значений pH раствора с 0,74 до 4,8-5,0 с использованием углекислого кальция. На второй стадии осаждение РЗЭ достигали за счет повышения значений pH раствора до 6,0-6,4 при использовании углекислого натрия и гидроксида натрия. Подача реагентов и перемешивание раствора осуществлялись в течение 2 ч. Осадки от растворов отделяли центрифугированием при относительном центробежном ускорении (RCF) лабораторной центрифуги не менее 500 g в течение 15 мин, затем осадки промывали дистиллированной водой и высушивали до стабилизации массы.
Анализ зависимости извлечения Zr, Al, Fe в твердый осадок от значений pH среды в изотермических условиях (20 °С) показал, что эффективность осаждения элементов увеличивается с ростом pH и при значении водородного показателя, равном 4,0, цирконий извлекается в осадок на 99,9 %, алюминий на 100 %, железо на 43,8 %, При этом установлено, что извлечение остальных примесей (Na, Mn, Sr, Ti, Mg и K) не превышает 15-35 %, а суммарные потери редкоземельных элементов составляют около 8 %.
Дальнейшее увеличение pH до значений 4,8-5,0 приводит к резкому повышению потерь РЗЭ до 40 % вследствие соосаждения с Zr, что, вероятно, связано с началом их осаждения в виде карбонатов. Последующее химическое осаждение соединений РЗЭ целесообразно проводить с использованием более растворимых соединений, например углекислого натрия и едкого натра (табл.7).
Результаты второй стадии эксперимента показали, что при удельном расходе углекислого натрия 6 г/дм3 (рН 6,1) достигается максимальное извлечение РЗЭ 95,5 % в твердую фазу. При повышении величины рН продуктивного раствора до 6,0 гидроксидом натрия максимальное извлечение РЗЭ в осадок составляет 59,1 %, что подтверждает извлечение значительного количества РЗЭ в твердую фазу в виде карбонатов.
Таблица 7
Извлечение РЗЭ в осадок в зависимости от рН раствора и типа реагента
Реагент |
Na2CO3 |
NaOH |
||
Расход, г/дм3 |
3,0 |
6,0 |
9,0 |
0,01 |
pH |
6,0 |
6,1 |
6,4 |
6,0 |
Извлечение РЗЭ, % |
90,8 |
95,5 |
95,2 |
59,1 |
Таким образом, на основе анализа результатов исследований подтверждена высокая эффективность химического последовательного осаждения циркония и РЗЭ из продуктивного раствора азотнокислотного выщелачивания эвдиалитового концентрата.
Установлено, что повышение величины рН исходного продуктивного раствора на 1-й стадии осаждения углекислым кальцием до 4,0 обеспечивает извлечение циркония в твердую фазу 99,95 % с попутным извлечением металлов примесей: алюминия – 100 %, железа – 43,8 %. При этом суммарные потери РЗЭ с циркониевым продуктом не превышают 8 %. Последующее повышение величины рН продуктивного раствора углекислым натрием до 6,1 обеспечивает извлечение РЗЭ в твердую фазу 87,5 %, при общем извлечении из раствора 95,5 %.
Вывод
На основе комплекса современных методов оптической, аналитической электронной, сканирующей зондовой микроскопии, ИК-Фурье-спектроскопии, РФЭ-спектроскопии и других методов физико-химического анализа получены новые научные данные о морфологии, структуре, химическом и фазовом составе поверхности минералов, механизме образования и деструкции силикатного геля, и разработаны эффективные методы селективного выделения циркония и редкоземельных элементов из продуктивных растворов кислотного выщелачивании эвдиалитового концентрата.
Литература
- Крюков В.А., Толстов А.В., Самсонов Н.Ю. Стратегическое значение редкоземельных металлов в мире и в России // Всероссийский экономический журнал. 2012. № 2 (11). С. 5-16. DOI: 10.30680/ECO0131-7652-2012-11-5-16
- Самсонов Н.Ю., Семягин И.Н. Обзор мирового и российского рынка редкоземельных металлов // Всероссийский экономический журнал. 2014. № 44(2). С. 45-54. DOI: 10.30680/ECO0131-7652-2014-2-45-54
- Чантурия В.А. Научное обоснование и разработка инновационных процессов комплексной переработки минерального сырья // Горный журнал. 2017. № 11. C. 7-13. DOI: 10.17580/gzh.2017.11.01
- Goodenough K.M., Schilling J., Jonsson E. et al. Europe’s Rare Earth Element Resource Potential: An Overview of REE Metallogenetic Provinces and Their Geodynamic Setting // Ore Geology Reviews. 2016. Vol. 72. Part 1. P. 838-856.
DOI: 10.1016/j.oregeorev.2015.09.019 - Johnsen O., Ferraris G., Gault R. et al. The nomenclature of eudialyte-group minerals // The Canadian Mineralogist. 2003. Vol. 41. № 3. P. 785-794. DOI: 10.2113/gscanmin.41.3.785
- Хохуля М.С., Герасимова Л.Г., Николаев А.И. Новые технологические решения подготовки и переработки перовскита // Труды Кольского научного центра РАН. 2018. Т. 9. № 2-1. С. 196-200. DOI: 10.25702/KSC.2307–5252.2018.9.1.196-200
- Cohen J., Cohen P., West S.G., Aiken L.S. Applied Multiple Regression/Correlation Analysis for the Behavioral Sciences. 3rd Edition. New York: Routledge, 2002. 536 p. DOI: 10.4324/9780203774441
- Rastsvetaeva R.K., Chukanov N.V., Pekov I.V. et al. New data on the isomorphism in eudialyte-group minerals. 1. Crystal chemistry of eudialyte-group members with Na incorporated into the framework as a marker of hyperagpaitic conditions // Minerals. 2020. Vol. 10. Iss. 7. № 587. DOI: 10.3390/min10070587
- 9. Мудрук Н.В., Коровина Ю.В., Николаев А.И., Сафонова Л.А. Экстракция редкоземельных элементов из растворов азотнокислотного вскрытия перовскита // Труды Кольского научного центра РАН. 2018. Т. 9. № 2-1. С. 323-327. DOI: 25702/KSC.2307–5252.2018.9.1.323-327
- Balinski A., Wiche O., Kelly N. et al. Separation of rare earth elements from contaminants and valuable components by in situ precipitation during the hydrometallurgical processing of eudialyte concentrate // Hydrometallurgy. 2020. Vol. 194. № 105345. DOI: 10.1016/j.hydromet.2020.105345
- Ma Y., Stopic S., Friedrich B. Hydrometallurgical Treatment of an Eudialyte Concentrate for Preparation of Rare Earth Carbonate // Johnson Matthey Technology Review. 2019. Vol. 63. № 1. P. 2-13. DOI: 10.1595/205651318X15270000571362
- Voßenkaul D., Birich A., Müller N. et al. Hydrometallurgical pro-cessing of Eudialyte Bearing Concentrates to Recover Rare Earth Elements Via Low-Temperature Dry Digestion to Prevent the Silica Gel Formation // Journal of Sustainable Metallurgy. 2016. Vol. 3. P. 79-89. DOI: 10.1007/s40831-016-0084-2
- Локшин Э.П. Сорбционная конверсия – перспективный метод переработки редкоземельного сырья // Труды Кольского научного центра РАН. 2018. Т. 9. № 2-1. С. 154-159. DOI: 10.25702/KSC.2307-5252.2018.9.1.154-159
- Balomenos E., Davris P., Deady E. et al. The EURARE project: development of a sustainable exploitation scheme for europe’s rare earth ore deposits // Johnson Matthey Technology Review. 2017. Vol. 61. P. 142-153. DOI: 10.1595/205651317X695172
- Hoshino M., Sanematsu K., Watanabe Y. REE mineralogy and resources // Handbook on the Physics and Chemistry of Rare Earths. New York: Elsevier, 2016. Vol. 49. P. 129-291. DOI: 10.1016/bs.hpcre.2016.03.006
- Гедгагов Э.И., Тарасов А.В., Гиганов В.Г., Лунькова М.А. Разработка инновационной сорбционно-экстракционной технологии получения высокочистых (99,99%) соединений редкоземельных металлов при переработке суммарных концентратов (на примере легкой группы) // Цветные металлы. 2017. № 8. С. 50-55. DOI: 10.17580/tsm.2017.08.07
- Русаков И.Ю., Буйновский А.С., Софронов В.Л., Агеева Л.Д. Разделение фторидов циркония и гафния сублимационно сорбционным методом // Известия высших учебных заведений. Цветная металлургия. 2016. № 3. С. 20-27. DOI: 10.17073/0021-3438-2016-3-20-27
- Dezhi Qi. Chapter 1. Extraction of Rare Earths from RE Concentrates // Hydrometallurgy of Rare Earths. Amsterdam: Elsevier, 2018. P. 1-185. DOI: 10.1016/B978-0-12-813920-2.00001-5
- Davris P., Stopic S., Balomenos E. et al. Leaching of rare earth elements from eudialyte concentrate by suppressing silica gel formation // Minerals Engineering. 2017. Vol. 108. P. 115-122. DOI: 10.1016/j.mineng.2016.12.011
- Богатырева Е.В., Чуб А.В., Ермилов А.Г., Хохлова О.В. Эффективность щелочно-кислотного способа комплексного выщелачивания эвдиалитового концентрата. Часть 1 // Цветные металлы. 2018. № 7. С. 57-61. DOI: 10.17580/tsm.2018.07.09
- Богатырева Е.В., Чуб А.В., Ермилов А.Г., Хохлова О.В. Эффективность щелочно-кислотного способа комплексного выщелачивания эвдиалитового концентрата. Часть 2 // Цветные металлы. 2018. № 8. С. 69-74. DOI: 10.17580/tsm.2018.08.09
- BalinskiA., AtanasovaP., WicheO. etal. Recovery of REEs, Zr (Hf), Mn and Nb by H2SO4 leaching of eudialyte concentrate // Hydrometallurgy. 2019. Vol. 186. P. 176-186. DOI: 10.1016/j.hydromet.2019.04.007
- Chanturia V.A., Chanturia E. L., Minenko V.G., Samusev A.L. Acid leaching process intensification for eudialyte concentrate based on energy effects // Обогащение руд. 2019. № 3. C. 29-36. DOI: 10.17580/or.2019.03.05
- 24. Chanturia V.А., Minenko V.G., Samusev А.L. et al. lnfluence exerted bу ultrasound processing on efficiency of leaching, structural, chemical, and morphological properties of mineral components in eudialyte Concentrate // Journal of Mining Science. 2018. Vol. 54. Iss. 2. Р. 285-29. DOI: 10.1134/S1062739118023641
- Ma Y., Stopic S., Gronen L., Friedrich B. Recovery of Zr, Hf, Nb from eudialyte residue by sulfuric acid dry digestion and water leaching with H2O2 as a promoter // Hydrometallurgy. 2018. Vol. 181. P. 206-214. DOI: 10.1016/j.hydromet.2018.10.002
- Saveleva I.L. The rare-earth metals industry of Russia: Present status, resource conditions of development // Geography and Natural Resources. 2011. Vol. 32. Iss. 1. P. 65-71. DOI: 10.1134/S1875372811010112
- Артамонов А.В., Смирнова Д.Н., Смирнов Н.Н., Ильин А.П. Извлечение редкоземельных элементов из твердых отходов производства фосфорной кислоты с последующей сорбцией на катионообменных смолах // Известия вузов. Химия и химическая технология. 2017. Т. 60. Вып. 10. С. 87-93. DOI: 10.6060/tcct.20176010.5571
- Турановa А.Н., Карандашев В.К., Баулинc В.Е. и др. Экстракция редкоземельных элементов(III) смесями 1-фенил-3-метил-4-бензоил5-пиразолона и фосфорилсодержащих подандов // Журнал общей химии. 2019. Т. 89. № 9. С. 1431-1438. DOI: 10.1134/S0044460X19090178
- Ma Y., Stopic S., Gronen L. et al. Neural network modeling for the extraction of rare earth elements from eudialyte concentrate by dry digestion and leaching // Metals – Open Access Metallurgy Journal. 2018. Vol. 8. Iss. 4. № 267. DOI: 10.3390/met8040267
- Chanturia V.А., Minenko V.G., Samusev А.L. et al. The mechanism of influence exerted by integrated energy impacts on intensified leaching of zirconium and rare earth elements from eudialyte concentrate // Journal of Mining Science. 2017. Vol. 53. Iss. 5. Р. 890-896. DOI: 10.1134/S1062739117052921
- Chanturia V.A., Bunin I.Z., Ryazantseva M.V. et al. Modification of structural, chemical and process properties of rare metal minerals under treatment by high-voltage nanosecond pulses // Journal of Mining Science. 2018. Vol. 53. Iss. 4. P. 718-733. DOI: 10.1134/S1062739117042704
- Panayotova M., Panayotov V. An electrochemical method for decreasing the concentration of sulfate and molybdenum ions in industrial wastewater // Journal of Environmental Science and Health, Part A. Toxic/Hazardous Substances and Environmental Engineering. 2004. Vol. 39. Iss. 1. P.173-83. DOI: 10.1081/ese-120027376
- Матвеев В.А., Майоров Д.В., Соловьев А.В. Комплексная технология сернокислотной переработки эвдиалитового концентрата // Цветные металлы. 2018. № 1. С. 20-27. DOI: 10.17580/tsm.2018.01.02
- Vaccarezza V., Anderson C. Beneficiation and leaching study of norra kärr eudialyte mineral // Metal Technology. The Minerals, Metals & Materials Series. Cham: Springer, 2018. 340 p. DOI: 10.1007/978-3-319-72350-1_4
- Jha M.K., Kumari A., Panda R. et al. Review on hydrometallurgical recovery of rare earth metals // Hydrometallurgy. 2016. Vol. 165. Part 1. P. 2-26. DOI: 10.1016/j.hydromet.2016.01.003