Production of biodiesel fuel from vegetable raw materials
- 1 — Ph.D., Dr.Sci. Head of Department Saint Petersburg Mining University ▪ Orcid
- 2 — Ph.D. Assistant Lecturer Saint Petersburg Mining University ▪ Orcid
Abstract
One way to reduce the amount of harmful emissions from diesel fuel could be the replacement of part of the fuel with biofuel. Research is related to the production of biodiesel fuel in three ways: transesterification of vegetable oils; esterification of fat acids extracted from vegetable oil; and hydroprocessing of vegetable oils using catalysts in the diesel hydrotreatment process. Food and non-food oils, monatomic and diatomic alcohols were used to produce biodiesel fuel. Optimal parameters of vegetable oil transesterification have been determined: temperature; raw material ratio (oil/alcohol); mixing speed; time; type of process catalyst. The characteristics of the obtained biodiesel fuel samples were studied and compared with each other as well as with the requirements of EN 14214 “Automotive fuels. Fat acid methyl ethers for diesel engines. General technical requirements” and EN 590:2009 “EURO diesel fuel. Technical specifications”. With regard to the physical and chemical characteristics of biodiesel fuel, the best way to produce it is by transesterification of vegetable oils. However, all fuels can be used as components of a blended environmentally friendly diesel fuel.
Introduction
Due to the shortage of oil reserves and the low level of oil refining (85 %), there is a need in European countries [1] to create technologies for the production of alternative fuels [2, 3]. Biodiesel is one of the most demanded fuels [4, 5], since most of the countries' transport sector consists of vehicles equipped with a diesel engine. Its main disadvantage is the amount of harmful emissions formed during the combustion of fuel, which is several times higher than the established standard. Therefore, most researchers consider the development of new types and compositions of biodiesel as a priority task.
Ethanol accounts for 74 % of all liquid biofuel, biodiesel for 22 % and green diesel for 4 %. The leaders in consumption of these fuels are the USA (46 %), Brazil (24 %), Europe and others (15 %) [6, 7].
In Russia, vehicles with diesel engine are in less demand than in Europe, but even there this form of transport is gaining popularity due to the obvious advantages of renewable biodiesel [8, 9], such as improved environmental properties (lower emissions of dispersed particles and volatile organic compounds during combustion [10], increased lubricity and high cetane number).
In European countries, the main raw material for biodiesel production is rapeseed oil, in the USA – soybean or corn oil, in Canada – canola oil, and some countries process palm oil to produce motor fuel component. The development of biofuels is increasing every year, for example, Emissions Reduction Alberta is investing in the development of a biodiesel plant in the Canadian province of Alberta.
Biodiesel testing and quality control have a special place in the biodiesel production process [11, 12]. New test methods according to American standards 14105 and ASTM D6584 are considered to be the most promising for assessing fuel quality. If a fuel fails to pass the quality test then it is refined and then retested. According to the European standard EN14214 [13] (Table 1) the following indicators, such as ether content, density, kinematic viscosity, flash point, sulphur content, cetane number, etc. are regulated in biodiesel. These indicators determine the possibility to use this type of fuel in the internal combustion engine: high viscosity impairs its pumping ability in the fuel supply system; low flash point of biofuel prevents timely ignition of the air-fuel mixture in the engine chamber.
Table 1
Basic requirements of EN14214 for biodiesel fuel [14]
Indicator |
Test method |
Maximum |
Minimum |
Ether content, % |
EN 14103 |
– |
96.5 |
Density at 15 °C, kg/m3 |
EN ISO 3675, EN ISO 12185 |
900 |
860 |
Kinematic viscosity at 40 °С, mm2/s |
EN ISO 3104 |
5 |
3.5 |
Flash point in a closed crucible, °С |
ISO/CD 3679 |
– |
120 |
Sulphur content, ppm |
EN ISO 20846, EN ISO 20884 |
10 |
– |
Cetane number, units |
EN ISO 5165 |
– |
51 |
Methodology
The main methods of biodiesel production worldwide are: transesterification of vegetable oils and animal fats; esterification of fat acids extracted from vegetable oils; hydrogenation or hydroprocessing of vegetable oils [12, 15].
The esterification process of fat acids contained in vegetable oil is based on the interaction of organic acids with alcohols using a catalyst, leading to the formation of complex ethers [6]. The reaction follows a nucleophilic substitution mechanism [16-18] (Fig.1).
Organic acids (C15-C17) extracted from sunflower oil were used as raw material for the fuel. The second component for the synthesis was diatomic alcohol (ethylene glycol) and an acidic catalyst was used. After reaction time, the light ether phase (target product) was separated from the heavy phase – glycerol with catalyst [19] – by settling, centrifugation and distillation. After obtaining the fuel, the main characteristics of the product were studied and compared with the properties of raw material (Table 2).
The basic components of the synthesized fuel are ethers of fat acids contained in sunflower oil. Qualitative and quantitative composition for ester part of biodiesel was studied by chromatography-mass spectrometry (Agilent 5973, DB-Petro column, length 100 m) (Table 3). The content of ethers in the product was 77.78 % mass (Fig.2) [20, 21].
Table 3 shows that the best vegetable raw materials for the production of biodiesel are semi-dry oils, as the reacted acids are mainly linoleic, oleic and elaidic, which are contained in maximum quantity in this type of oil.
Table 2
Operational characteristics of fat acids in sunflower oil and biodiesel fuel produced by esterification
Indicator |
Biodiesel fuel |
Fat acids |
Density at 20 °C, kg/m3 |
914.00 |
909.78 |
Viscosity at 40 °C, mm2/s |
23.250 |
27.995 |
Flash point in a closed crucible, °С |
112 |
115 |
Sulphur content, ppm |
71 |
13 |
Lubricity (corrected wear spot diameter) |
202 |
157 |
Table 3
Component composition for the ester part of biodiesel fuel produced by esterification of sunflower oil fat acids with ethylene glycol
Name |
Content, % mass |
Methyl ether of linoleic acid |
1.21 |
Methyl ether of oleic acid |
0.49 |
Ethyl ether of linoleic acid |
1.47 |
2,3-Dihydroxypropyl ether of linoleic acid |
40.12 |
Oxyethyl ether of elaidic acid |
24.48 |
Glycerol ether of elaidic acid |
6.53 |
Oxyethyl ether of stearic acid |
2.75 |
Cetyl ether of tranexamic acid |
0.73 |
Once the synthesis is completed and the heavy phase is removed, the mixture requires additional purification because, in addition to the ester mixture, unreacted acids, alcohol and other compounds remain in the light phase (Fig.2). These substances must be removed as they can corrode engine parts and affect the oxidative stability of the fuel.
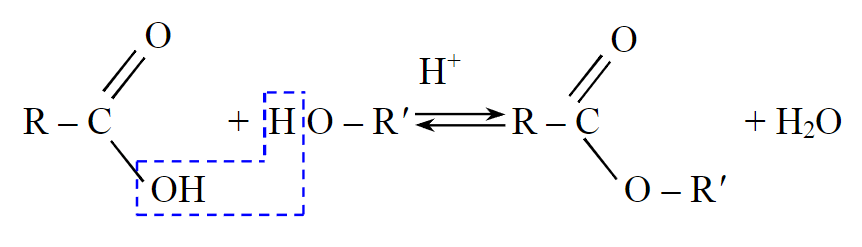
Fig.1. The mechanism for the esterification process of fat acids
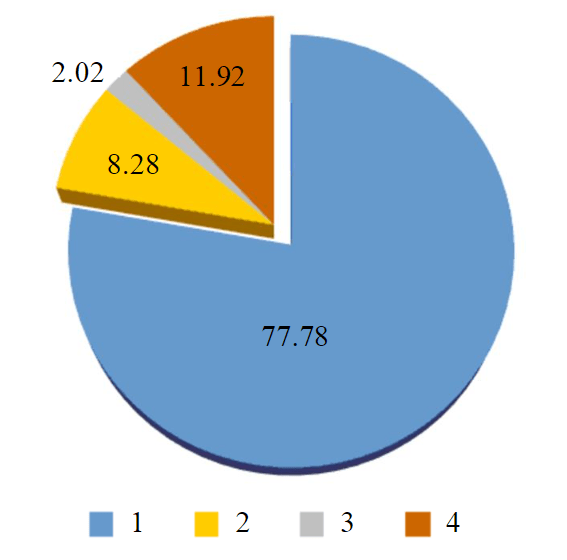
Fig.2. Group composition of biodiesel fuel produced by the esterification of sunflower oil fat acids with ethylene glycol 1 – ethers; 2 – acids; 3 – toluene; 4 – others, %
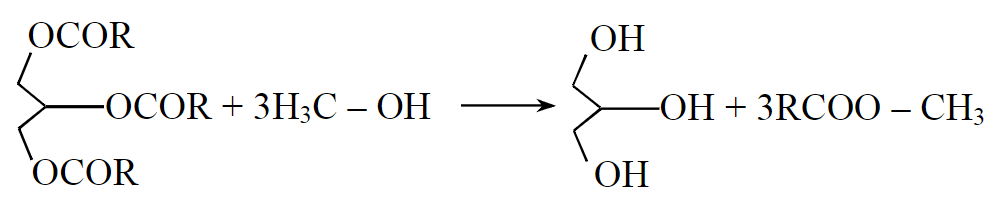
Fig.3. Transesterification process of vegetable oils
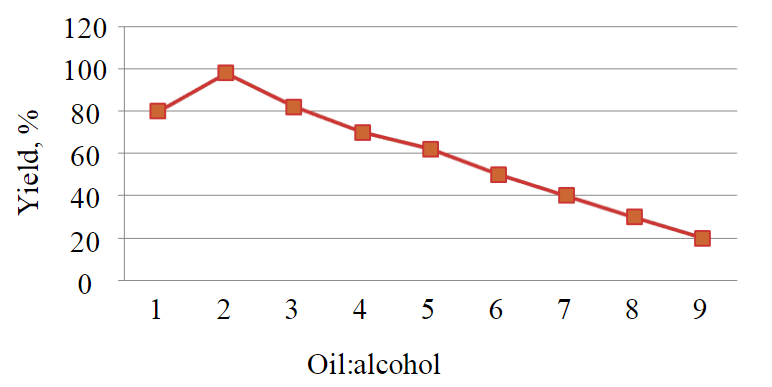
Fig.4. Yield curve of product on fractions of oil per share of alcohol
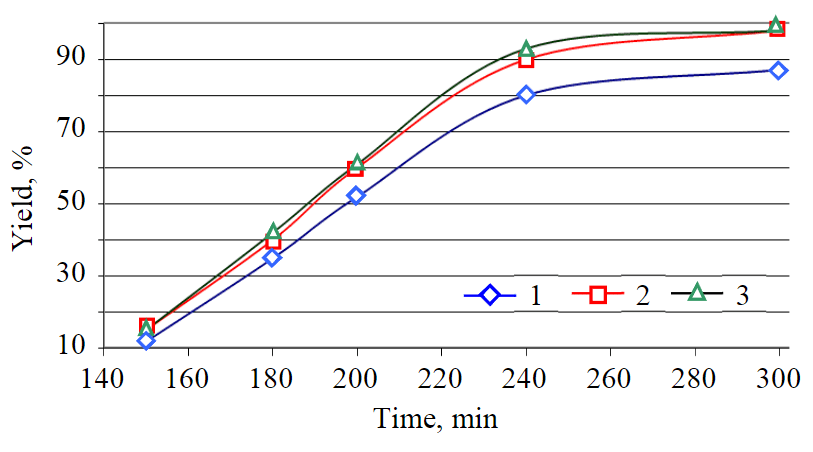
Fig.5. Curves for dependence of reaction rate on the mixing intensity at 195 °С 1 – 200; 2 – 250; 3 – 300 rpm
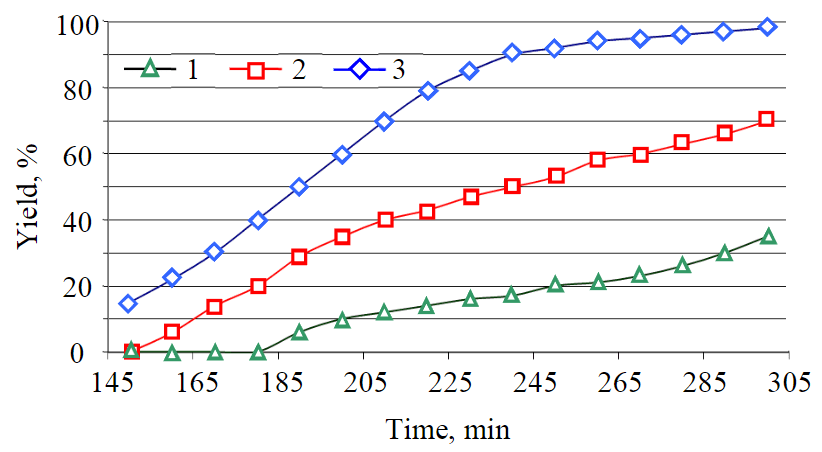
Fig.6. Curves for dependence of product yield on transformation time at a mixing speed of 250 rpm at different temperatures 1 – 140; 2 – 175; 3 – 195 °С
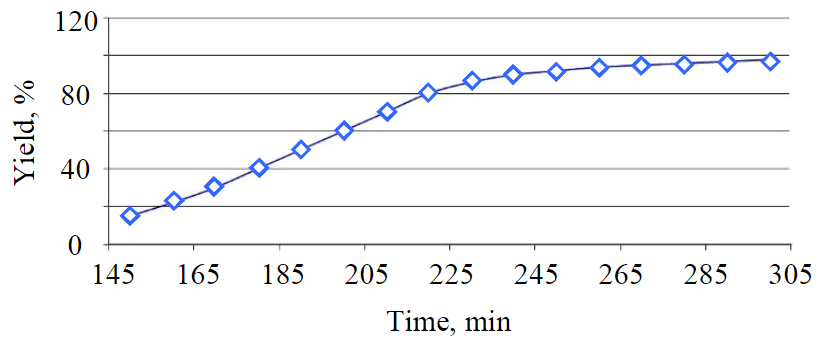
Fig.7. Curve for dependence of raw material conversion rate on mixing time at 195 °С
The second common method of biodiesel production consists of the transesterification of vegetable oils [22], a reaction of the interaction of triglycerides with alcohol leading to the formation of esters and glycerol (Fig.3) [23-25].
For synthesis of esters by transesterification, normal butyl alcohol, non-food raw material (red oil) and food oils (linseed and corn oil) were used. Concentrated sulphuric acid was chosen as a catalyst [1, 18]. The reagent mixture of ethylene glycol and vegetable oil was prepared in three-neck 250 ml flask. To choose the most suitable composition different ratios of the mixture were tried. Dependence of product yield on oil/alcohol ratio is shown in Fig.4.
The unit for the transesterification of vegetable oil consisted of an upper-drive mixer equipped with a water trap, a reverse water cooler, a sand bath and a thermometer. During the method testing for biodiesel production, temperature, mixing speed and time were the varying parameters of the process in addition to the raw material ratio (oil:alcohol). Mixing intensity was adjusted on mixer by setting 200, 250 and 300 rpm (Fig.5).
The transesterification of vegetable oil with diatomic alcohol was carried out at temperatures 140, 175 and 195 °С (Fig.6). The choice of the temperature range is due to the following reasons: at lower temperatures the reaction proceeds very slowly, higher temperatures require higher pressure, because the boiling point of diatomic alcohol is 197 °С.
The product yield also depends on the duration of the transesterification reaction
of vegetable oils. The duration of the experiments was 150, 180, 200, 240 and 300 min (Fig.7).
At the end of the experiments the product mixture was cooled down and settled for 3-4 days, then ether and glycerol phase were separated [5, 26, 27]. The main part of the acid after the reaction is concentrated in the glycerol phase [28]. The remaining part of the acid in the ether phase was neutralized with Na2CO3. The ether was flushed several times with hot water and separated into layers to separate the neutralized acid and water from the ether part. Then the ether was separated from the water in a separating funnel. The dewatered Na2SO4 was added to the separated ether for 60 min to remove any remaining water, followed by filtration.
The esterification products of red, linseed and corn oils were designated n-BERO (normal butyl ether of red oil), n-BELO (normal butyl ether of linseed oil) and n-BECO (normal butyl ether of corn oil), respectively (Table 4).
Table 4
Physical and chemical properties of butyl ether mixture obtained by by transesterification of red, linseed and corn oils
Indicator |
n-BERO |
n-BELO |
n-BECO |
Ether content, % |
96.5 |
95 |
94 |
Density at 20 °C, kg/m3 |
0.8766 |
0.8700 |
0.8758 |
Viscosity at 40 °C, mm2/s |
4.572 |
5.000 |
4.492 |
Flash point in a closed crucible, °C |
150 |
135 |
120 |
Sulphur content, ppm |
5.5 |
6.8 |
8.5 |
Cetane number, units |
56 |
53 |
51 |
Lubricity at 60 °С, µm |
553 |
601 |
592 |
Based on the data of Table 4, the best raw material for biodiesel production by transesterification method should be considered red oil, because n-BERO is characterized by the lowest values of sulphur content (5.5 ppm) and corrected wear spot diameter (553 µm). The mixture also has the highest flash point (150 °C) and cetane number (56 units).
The main components of the synthesized fuels are ethers of fat acids contained in vegetable oils. Qualitative and quantitative composition of ether part of biodiesel produced by transesterification of oil from red oil with n-butanol (Table 5) showed that the ether content in the yield was 60.03 % mass [14].
Table 5
Component composition of the ether part of biodiesel fuel, obtained by transesterification of red oil with n-butanol
Component |
Content, % mass |
|
Butyl ether: |
||
caprylic acid |
0.90 |
|
capric acid |
5.26 |
|
lauric acid |
0.25 |
|
myristic acid |
0.31 |
|
oleic acid |
8.94 |
|
palmitic acid |
10.43 |
|
pelargonic acid |
0.87 |
|
acetic acid |
1.86 |
|
elaidic acid |
8.86 |
|
enanthic acid |
0.86 |
|
Dibutyl ether: |
|
|
glutaric acid |
0.23 |
|
pelargonic acid |
0.49 |
|
sebacic acid |
3.07 |
|
Methyl ether: |
||
linoleic acid |
3.39 |
|
eicosenoic acid |
6.36 |
|
Hexadecene ether of elaidic acid |
6.57 |
|
Dimethylethyl ether of propenoic acid |
0.49 |
|
Ether of Carbamic acid |
0.89 |
Biodiesel fuel synthesized by the transesterification of red oil with n-butanol contains unreacted fat acids, unreacted alcohol and by-products in addition to complex ethers. Residual fat acids can be isolated from this fuel and introduced into anti-wear additives approved for use in Russia.
The third way of biodiesel fuel production consists in hydrocracking of lipids over sulphide or noble metal containing catalysts to form a mixture of hydrocarbons enriched with normal and iso-C15-C18 components. The main advantages of “green diesel” include full compatibility with oil diesel fuel [29], stability during storage because of the absence of oxygen-containing and unsaturated compounds, as well as environmental safety caused by the absence of aromatic
hydrocarbons.
When triglycerides are hydroformed into diesel hydrocarbons, the following reactions take place [30]:
- hydrogenation of unsaturated bonds;
- hydrocracking with the formation of saturated fat acids and propane;
- deoxygenation of fat acids along the reactions of: – decarboxylation Rх – COOH → Rх – H + CO2; – hydrodecarbonylation Rх – COOH + H2 → CO + H2O + Rх – H; – hydrogenation/dehydration Rх – COOH + 3H2 → 2H2O + Rх – CH3, where x = 15, 17;
- hydrocarbon isomerisation n-Rх – CH3 → iso-Rх – CH3;
- hydrocarbon cracking n-Rх – CH3 → n-Ry – CH3 + n-Rz – CH3, where y, z < х.
Sunflower oil was used to produce biodiesel fuel samples using the hydrocracking method. The process was carried out in the boiling temperature range of the main fraction 180-360 °С on a NiMo/Al2O3 catalyst. The product was separated into three main fractions: gas fraction, water fraction and organic fraction. The main fuel characteristics of sample 1 “green diesel” synthesized using sulfide catalyst and sample 2 synthesized using noble metal based catalyst are presented in Table 6.
Table 6
Physical and chemical properties of “green diesel” samples obtained in the process of sunflower oil hydrocracking
Indicator |
Sample 1 |
Sample 2 |
Density at 15 °С, kg/m3 |
786.38 |
784.67 |
Sulphur content, ppm |
50 |
0 |
Flash point in a closed crucible, °С |
79 |
82 |
Lubricity at 60 °С, µm |
582 |
606 |
Kinematic viscosity at 40 °С, mm2/s |
3.4273 |
3.2679 |
Fractional composition: |
|
|
at 250 °С, % vol. |
4 |
4 |
at 350 °С, % vol. |
96 |
98 |
95 % vol. is distilled at a temperature of, °С |
355 |
304 |
Cetane number, units |
79 |
80 |
Pour point, °С |
16 |
4 |
Cloud point, °С |
20 |
9 |
Content of fat acid methyl ethers, % vol. |
– |
– |
Ash content, % mass |
0.0083 |
0.0096 |
The main regulation document, according to which diesel fuel is produced at Russian refineries, is GOST R 52368-2005 “EURO diesel fuel. Technical Conditions”. It meets all the requirements of the European standard EN 590 and limits the sulfur content in diesel fuel to 350 (Euro-3), 50 (Euro-4) and 10 ppm (Euro-5), and increases the cetane number to 51 (not less than 45 according to GOST 305-82).
Table 6 and parameters of the standard EN 590:2009 show that characteristics of samples 1 and 2 of “green diesel” do not meet the requirements of the standard by such indicators as the lubricity (exceeds the norm 1.5 times) and the cloud point of 20 and 9 °С, respectively (the standard is –22 °С). Qualitative and quantitative composition of diesel fraction (boiling range 150-350 °С), which is a part of samples 1 and 2, was studied (Table 7) by the method of gas chromatography (device Chromos, column DB-1, length 100 m).
Table 7
Component composition of diesel fractions for samples 1 and 2 obtained in the process of sunflower oil hydrocracking
Name |
Content, % mass |
Name |
Content, % mass |
|||
Sample 1 |
Sample 2 |
Sample 1 |
Sample 2 |
|||
iso-Decans |
0.36 |
0.44 |
n-Pentadecans |
2.87 |
3.15 |
|
iso-Decan |
0.55 |
0.31 |
iso-Hexadecans |
0.26 |
6.55 |
|
iso-Undecans |
0.30 |
0.48 |
n-Hexadecan |
4.74 |
2.89 |
|
iso-Undecan |
0.39 |
0.28 |
iso-Heptadecans |
1.57 |
24.26 |
|
iso-Dodecans |
0.26 |
0.57 |
n-Heptadecan |
32.36 |
27.63 |
|
n-Dodecan |
0.30 |
0.24 |
iso-Octadecans |
2.94 |
12.94 |
|
iso-Tridecans |
0.17 |
0.59 |
n-Octadecan |
49.22 |
13.43 |
|
n-Tridecan |
0.26 |
0.26 |
iso-Nonadecans |
1.22 |
1.74 |
|
iso-Tetradecans |
0.18 |
0.63 |
n-Nonadecan |
0.44 |
0.42 |
|
n-Tetradecan |
0.28 |
0.22 |
iso-Eicosans |
0.67 |
1.13 |
|
iso-Pentadecans |
0.18 |
1.69 |
n-Eicosan |
0.48 |
0.15 |
|
Total: |
100.00 |
100.00 |
According to Table 7 the diesel fraction of sample 1 is dominated by n-heptadecan and n-octadecane, the content of which is 81.58 % mass. This composition causes high values of pour point (16 °С), cetane number (79 units) and poor lubricity (corrected wear spot diameter 582 µm) of the sample 1 “green diesel”. On the contrary, the diesel fraction of sample 2 is dominated by iso-hexadecans, iso-heptadecans and iso-octadecans, their content reaching 43.75 % mass. Despite practically the same lubricating properties and cetane number, sample 2 has better low-temperature properties (lower pour point is 4 °С and cloud point is 9 °С). The advantage of sample 2 is the almost total absence of sulphur, so it can be used not only in Euro-5, but also in Euro-6 fuels.
Discussion of the results
Analysis of the characteristics of biodiesel fuels (Tables 2, 4, 6), shows that the best method for obtaining this type of fuel is the transesterification of vegetable oils, namely red oil, as almost all physical and chemical properties of this sample meet many requirements of EN 590:2009 standard for diesel fuel. Samples obtained by hydrocracking of vegetable oils need to be refined before they can be used in a diesel engine. Biodiesel fuel produced by the esterification of fat acids complies with the specifications of EN 590:2009. However, when comparing the characteristics of these fuels, it was found that after transesterification the fuel has better characteristics.
In the process of vegetable oil, transesterification with diatomic alcohol (ethylene glycol) in laboratory synthesis it is most rational to use temperature 195 °С, because with increasing of temperature the rate of target reaction is also increasing. However, because boiling point of ethyleneglycol is 197 °С, it is not reasonable to reach it. The longer the reaction time, the higher the selectivity of the process. Thus, time of reaction should be about 240 min, and further increasing of reaction time will make energy expenses considerably higher than target product obtained. The optimum composition is a ratio by mass (oil:alcohol) of 2:1, or 103:50 g.
Biodiesel fuel produced by the transesterification of vegetable oils is reasonable to use in engines in mixture with hydrotreated diesel fuel, otherwise engine reconstruction will be required, or engine life will be reduced, because pure biodiesel fuel has slightly higher viscosity than hydrotreated diesel fuel, and lubricating ability is worse [8, 31]. However, when using biodiesel fuel as a component of commercial diesel fuel [32], this indicator is improved more than twice.
In order to use samples 1 and 2 in a diesel engine as a commercial diesel fuel it is necessary to improve their characteristics to the requirements of EN 590:2009, namely research into improving their lubricating and low-temperature properties by introducing anti-wear and depressor-dispersant additives [33], which is a standard procedure in refineries when preparing commercial diesel fuel. This suggests that the technology will not become more expensive.
When using biodiesel fuel produced by transesterification and esterification, the environmental characteristics of the fuel are improved at the same time [13, 34]: the amount of sulphur remains at Euro-5 levels (less than 10 ppm); the carbon monoxide content in exhaust gases is reduced by 13-71 % at maximum engine load and by 26-48 % at partial load (75 %), depending on the number of rpm; the modified hydrocarbon concentration in exhaust gases is reduced by 5-31 % (at maximum load) and by 31-46 % (at partial load (75 %); exhaust gases smokiness is reduced to 65 %.
Conclusion
The considered ways of biodiesel fuel production from different plant raw materials will allow to expand the field of fuel resources and improve the quality of commercial fuels. One of the alternative options to bring the quality of fuel to the required standards is the compounding of the obtained samples with hydrotreated low-sulphur diesel fuel in a ratio of not less than 50 % mass of hydrotreated diesel fuel [5, 35-37]. Production of biodiesel using food raw materials such as corn and sunflower oil is not sustainable as it poses a great risk of food and fuel competition, leading to higher food prices and the threat of hunger. Non-food raw materials, such as red oil, are considered promising and environmentally friendly for biodiesel production.
References
- Litvinenko V.S., Sergeev I.B. Innovations as a Factor in the Development of the Natural Resources Sector. Studies on Russian Economic Development. 2019. Vol. 30, p. 637-645. DOI: 10.1134/S107570071906011X
- Anchita K. HYDRO-IMP technology for upgrading of heavy petroleum. Journal of Mining Institute. 2017. Vol. 224, p. 229-234. DOI: 10.18454/PMI.2017.2.229
- Kazamia E., Smith A.G. Assessing the environmental sustainability of biofuels. Trends in plant science. 2014. Vol. 19. Iss. 10, p. 615-618. DOI: 10.1016/j.tplants.2014.08.001
- Dvoretsky S.I., Zazulya A.N., Nagornov S.A. et al. Biodiesel Production from Organic Raw Materia. Problems of Contemporary Science and Practice Vernadsky University. 2012. S2 (39), p. 126-135 (in Russian).
- Sultanbekov R., Islamov Sh., Mardashov D. et al. Research of the influence of marine residual fuel composition on sedimentation due to incompatibility. Journal of Marine Science and Engineering. 2021. Vol. 9. Iss. 10. N 1067. DOI: 10.3390/jmse9101067
- Korshunov G.I., Eremeeva A.M., Drebenstedt P. Justification of the use of a vegetal additive to diesel fuel as a method of protecting underground personnel of coal mines from the impact of harmful emissions of diesel-hydraulic locomotives. Journal of Mining Institute. 2021. Vol. 247, p. 39-47. DOI: 10.31897/PMI.2021.1.5
- Pashkevich M.A. Classification and environmental impact of mine dumps. Assessment, Restoration and Reclamation of Mining Influenced Soils. 2017, p. 1-32. DOI: 10.1016/B978-0-12-809588-1.00001-3
- Fernando S., Adhikari S., Kota K., Bandi R. Glycerol based automotive fuels from future biorefineries. Fuel. 2007. Vol. 86. Iss. 17-18, p. 2806-2809. DOI: 10.1016/j.fuel.2007.03.030
- Hajjari M., Tabatabaei M., Aghbashlo M., Ghanavati H.J.R. A review on the prospects of sustainable biodiesel production: A global scenario with an emphasis on waste-oil biodiesel utilization. Renewable Sustainable Energy Reviews. 2017. Vol. 72,
p. 445-464. DOI: 10.1016/j.rser.2017.01.034 - Bezergianni S., Dimitriadis A. Comparison between different types of renewable diesel. Renewable and Sustainable Energy Reviews. 2013. Vol. 21, p. 110-116. DOI: 10.1016/j.rser.2012.12.042
- Smirnova T.N., Podgaetskii V.M. Biodiesel – an alternative fuel for diesels. Dvigatel. 2007. N 2, p. 32-34.
- Dzhevaga N.V., Borisova D.D.Analysis of Air Monitoring System in Megacity on the Example of St. Petersburg. Journal of Ecological Engineering. 2021. Vol. 22. Iss. 4, p. 175-185. DOI: 10.12911/22998993/134076
- Nibin T., Sathiyagnanam A., Sivaprakasam S., Saravanan C. Investigation on emission characteristics of a diesel engine using oxygenated fuel additive. Journal of the Institution of Engineers, Part MC, Mechanical Engineering Division. 2005. Vol. 86, p. 51-54.
- Wong K.C., Tan C.H. Volatile constituents of the flowers of Clerodendron fragrans (Vent.) R. Br. Flavour fragrance journal. 2005. Vol. 20. Iss. 4, p. 429-430. DOI: 10.1002/ffj.1457
- Aghbashlo M., Tabatabaei M., Khalife E. et al. Exergoeconomic analysis of a DI diesel engine fueled with diesel/biodiesel (B5) emulsions containing aqueous nano cerium oxide. Energy. 2018. Vol. 149, p. 967-978. DOI: 10.1016/j.energy.2018.02.082
- Fakas S., Papanikolaou S., Galiotou-Panayotou M. et al. Biochemistry and biotechnology of single cell oil. New horizons in Biotechnology. 2009, p. 38-60.
- Halim R., Danquah M.K., Webley P.A. Extraction of oil from microalgae for biodiesel production: a review. Biotechnology advances. 2012. Vol. 30. Iss. 3, p. 709-732. DOI: 10.1016/j.biotechadv.2012.01.001
- Litvinenko V.S. The Role of Hydrocarbons in the Global Energy Agenda: The Focus on Liquefied Natural Gas Resources 2020. Resourses. 2020. Vol. 9. Iss. 5, p. 59-81. DOI: 10.3390/resources9050059
- Quispe C.A., Coronado C.J., Carvalho Jr. J.A. Glycerol: Production, consumption, prices, characterization and new trends in combustion. Renewable sustainable energy reviews. 2013. Vol. 27, p. 475-493. DOI: 10.1016/j.rser.2013.06.017
- Loizzo M.R., Tundis R., Conforti F. et al. Comparative chemical composition, antioxidant and hypoglycaemic activities of Juniperus oxycedrus ssp. oxycedrus L. berry and wood oils from Lebanon. Food chemistry. 2007. Vol. 105. Iss. 2, p. 572-578. DOI: 10.1016/j.foodchem.2007.04.015
- Ponomarenko T., Nevskaya M., Jonek-Kowalska I. Mineral ResourceDepletion Assessment: Alternatives, Problems, Results. Sustainability. 2021. Vol. 13. Iss. 2. N 862. DOI: 10.3390/su13020862
- Gómez-Cuenca F., Gómez-Marín M., Folgueras-Díaz M.B. Effects of ethylene glycol ethers on diesel fuel properties and emissions in a diesel engine. Energy conversion management. 2011. Vol. 52. Iss. 8-9, p. 3027-3033. DOI: 10.1016/j.enconman.2011.04.017
- Brady S., Tam K., Leung G., Salam C. Zero waste biodiesel: Using glycerin and biomass to create renewable energy. UCR Undergraduate Research Journal. 2008. Vol. 2 (5), p. 5-11.
- De Torres M., Jimenez-Oses G., Mayoral J.A. et al. Glycerol ketals: Synthesis and profits in biodiesel blends. Fuel. 2012. Vol. 94, p. 614-616. DOI: 10.1016/j.fuel.2011.11.062
- Strizhenok A.V., Korelskiy D.S. Estimation and reduction of methane emissions at the scheduled and repair outages of gas-compressor units. Journal of Ecological Engineering. 2019. Vol. 20. Iss. 1, p. 46-51. DOI: 10.12911/22998993/93943
- Lapuerta M., Rodríguez-Fernández J., García-Contreras R. Effect of a glycerol-derived advanced biofuel–FAGE (fatty acid formal glycerol ester) – on the emissions of a diesel engine tested under the New European Driving Cycle. Energy. 2015. Vol. 93, p. 568-579. DOI: 10.1016/j.energy.2015.09.070
- Mota C.J., da Silva C.X., Rosenbach Jr. N. et al. Glycerin derivatives as fuel additives: the addition of glycerol/acetone ketal (solketal) in gasolines. Energy Fuels. 2010. Vol. 24. Iss. 4, p. 2733-2736. DOI: 10.1021/ef9015735
- Saengarun C., Petsom A., Tungasmita D.N. Etherification of glycerol with propylene or 1-butene for fuel additives. The Scientific World Journal. 2017. Vol. 2017. N 4089036. DOI: 10.1155/2017/4089036
- Tóth C., Baladincz P., Hancsók J. Production of bio gas oil containing diesel fuel with upgraded cold flow properties by co-processing. Chemical Engineering Transactions. 2012. Vol. 29, p. 613-618. DOI: 10.3303/CET1229103
- Mohammad M., Hari T.K., Yaakob Z. et al. Overview on the production of paraffin based-biofuels via catalytic hydrodeoxygenation. Renewable and Sustainable Energy Reviews. 2013. Vol. 22, p. 121-132. DOI: 10.1016/j.rser.2013.01.026
- Dabbagh H., Ghobadi F., Ehsan M.R, Moradmand M. The influence of ester additives on the properties of gasoline. Fuel. 2013. Vol. 104, p. 216-223. DOI: 10.1016/j.fuel.2012.09.056
- Burger J., Siegert M., Ströfer E., Hasse H. Poly (oxymethylene) dimethyl ethers as components of tailored diesel fuel: Properties, synthesis and purification concepts. Fuel. 2010. Vol. 89. Iss. 11, p. 3315-3319. DOI: 10.1016/j.fuel.2010.05.014
- Mitusova T.N., Kondrasheva N.K., Lobashova M.M. et al. Influence of dispersing additives and blend composition on stability of marine high-viscosity fuels. Journal of Mining Institute. 2017. Vol. 228, p. 722-725. DOI: 10.25515/PMI.2017.6.722
- Arteconi A., Mazzarini A., Di Nicola G. Emissions from ethers and organic carbonate fuel additives: a review. Water, Air, Soil Pollution. 2011. Vol. 221, p. 405-423. DOI: 10.1007/s11270-011-0804-y
- Sultanbekov R., Nazarova M. The influence of total sediment of petroleum products on the corrosiveness of the metal of the tanks during storage. I International Conference “Corrosion in the Oil and Gas Industry”, 22-24 May 2019, Saint Petersburg, Russia. E3S Web of Conferences. 2019. N 01015. DOI: 10.1051/e3sconf/201912101015
- Sultanbekov R., Nazarova М. Determination of compatibility of petroleum products when mixed in tanks. European Association of Geoscientists & Engineers, 25-29 March 2019, Tyumen, Russia. European Association of Geoscientists & Engineers, 2019. Vol. 2019, p. 1-5. DOI: 10.3997/2214-4609.201900614
- Gendler S.G., Prokhorova E.A. Assessment of the cumulative impact of occupational injuries and diseases on the state of labor protection in the coal industry. Mining Informational and Analytical Bulletin. 2022. N 10-2, р. 105-116 (in Russian). DOI: 10.25018/0236_1493_2022_102_0_105