Improvement of technological schemes of mining of coal seams prone to spontaneous combustion and rock bumps
- 1 — Ph.D. Associate Professor Saint Petersburg Mining University ▪ Orcid ▪ Elibrary ▪ Scopus
- 2 — Ph.D. Associate Professor Saint Petersburg Mining University ▪ Orcid
- 3 — Postgraduate Student Saint Petersburg Mining University ▪ Orcid
- 4 — Ph.D. Associate Professor Saint Petersburg Mining University ▪ Orcid
Abstract
On the example of the Alardinskaya mine, the problem of underground mining of seams prone to spontaneous combustion and rock bumps in the conditions of the Kondomsky geological and economic region of the Kuznetsk coal basin is considered. The contradictions in the requirements of regulatory documents for the width of the inter-panel coal pillars in the mining of seams with longwalls in conditions of endogenous fire hazard and in the mining of seams that are dangerous due to geodynamical phenomena are discussed. These contradictions impede the safe mining of seams using traditionally used layouts with the danger of spontaneous combustion of coal and rock bumps. A mining-geomechanical model is presented, which is used for numerical three-dimensional simulation of the stress-strain state of a rock mass with various layouts for longwall panels using the finite element method. The results of the numerical analysis of the stress state of the rock mass immediately before the rock bump are presented, and the main factors that contributed to its occurrence during the mining of the seam are established. A dangerous degree of stress concentration in the coal seam near the leading diagonal entries is shown, especially in conditions of application of abutment pressure from the edge of panels’ gob. The analysis of the features of stress distribution in the inter-panel pillar at different widths is carried out. Recommendations for improving the layout for the development and mining of coal seams that are prone to spontaneous combustion and dangerous in terms of rock bumps in the conditions of Alardiskaya mine have been developed. The need for further studies of the influence of pillars for various purposes, formed during the mining of adjacent seams, on the stress-strain state of previously overmined and undermined seams is shown.
Introduction
Increasing the reliability and power supply of the longwall mining equipment of coal mines predetermined a significant increase in the productivity of longwall systems during the mining of coal seams in favorable mining and geological conditions and the widespread use of technology for developing seams with long complexly mechanized coal faces using a system of longwall mining with roof collapse and leaving inter-panel coal pillars. The highest rates of underground coal mining are currently achieved when long longwalls are mined in thick and medium-sized flat coal seams at shallow depths (up to 400 m) [1-4] with a methane content up to 10 m3/t, no significant geological faults of the developed areas and significant influence of previously mined out contiguous seams. So, for example, when mining a thick flat 50 seam in the conditions of the V.D.Yalevsky mine in 2017-2018 longwall face productivity records were set. The monthly load on the production face 50-03 in 2017 reached 1.56 million tons, and then a new record was set when the longwall face 50-04 operated – in August 2018, 1.627 million tons were produced [5-7]. At the same time, the daily productivity of the longwall reached 65 thousand tons. At the same time, the influence of even one geological factor that complicates the work in the longwalls can lead to a significant decrease in the efficiency and increase the danger of mining. So, for example, the subsequent mining of the seam 50 in the conditions of the mine V.D.Yalevsky at greater depths was carried out with a gradual, as the methane content of the developed reservoir increased, decrease in the maximum of output rate on the longwall – up to 600 thousand tons per month with a constant increase in the cost of ventilation of the faces and complex gas drainage. It should be noted that the intensive mining of seams with longwalls is accompanied by a constant increase in the depth of mining, which leads to a deterioration in mining and technical conditions. Firstly, the frequency of dangerous manifestations of rock pressure increases [8-10], the methane in gate roads increases, which multiplies risks of accidents, and also causes an increase in production costs and a decrease in labor productivity and, as a result, reduces the competitiveness of the enterprise.
The underground mining with the simultaneous influence of several complicating factors is cha-racterized by the greatest problems. So, for example, the thick seams of the Kondomsky district of Kuzbass are both dangerous in terms of rock bumps and sudden outbursts of coal and gas already from a depth of 300 m, methane-bearing and prone to spontaneous combustion. The simultaneous influence of various hazardous factors increases the frequency of endogenous fires and dynamic ma-nifestations of rock pressure, leading to a significant reduction in technical and economic indicators of coal production. Moreover, the danger of mining is constantly increasing with the depth of mining. At the same time, colossal reserves (about 4 billion tons of coal) and the high value of the produced coking coals do not allow abandoning the mining of seams even in such difficult conditions, ensuring the profitability of coal mining.
However, the unstable situation in the coal markets predetermines the need to reduce production costs, and if this is not possible, the abandonment of the mining of hard-to-recover reserves. In such conditions, in order to increase the competitiveness of the mines of the Kondomsky district of Kuzbass, which are developing in these difficult mining and geological conditions, it is necessary to search, create, and implement the most effective and safe layouts for mining flat coal seams, primarily in conditions of simultaneous danger of rock bumps and the occurrence of endogenous fires, since the experience of mining such layers shows the impossibility of effectively preventing such hazardous phenomena using traditionally used layouts that are successfully applied under the influence of one of the two indicated hazardous factors. So, for example, in the conditions of the Alardinskaya mine, which develops the reserves of the Alardinskoye deposit in the Kondomsky district of Kuzbass, pillarless mining of reserves led to active endogenous fires [11], and subsequent mining, leaving pillars 30-50 m wide, led to rock bumps [12].
The immediate prospects for underground mining of coal seams by Kuzbass mines are associated with an increase in the depth of mining operations and a corresponding increase in the dynamic danger of their development. Moreover, coals, which make up the majority of Kuzbass seams that are pro-mising for mining, are prone to spontaneous combustion. Thus, the simultaneous danger of spontaneous combustion and rock bumps is a real prospect for a number of Kuzbass mines, which, in conditions of high methane abundance, will predetermine a significant increase in the danger of underground coal mining. Research aimed at improving progressive layouts for the mining of seams in conditions of simultaneous danger of rock bumps and spontaneous combustion of coal is relevant not only for the mines of the Kondomsky district of Kuzbass.
The purpose of the study is to establish the main causes of rock bumps and substantiate the parameters of effective layouts that exclude the danger of spontaneous combustion of coal and rock bumps, while ensuring high productivity of coal mining in the Alardinskaya mine.
Formulation of the problem
Russia has accumulated considerable experience in combating endogenous fires [11, 13] and rock bumps [14-16] in coal mines. This experience is summarized in the requirements of regulatory documents aimed at eliminating the conditions for spontaneous combustion of coal, and rock bumps. At the same time, the task of safe mining of seams, which are both dangerous in terms of rock bumps and spontaneous combustion of coal, has not found an unequivocal effective solution, since the prevention of these phenomena in constantly changing mining and geological conditions often encounters conflicting requirements. At the same time, many simultaneously affecting hazardous factors do not allow the effective use of traditionally used layouts to develop and mine panels. In foreign practice, there is not enough experience of successful mining of coal seams in such difficult conditions. The problem of ensuring the dynamic safety of mining operations remains relevant for the leading coal-producing countries of the world – China [17-19] and the USA [20, 21], which is explained by the constant complication of conditions in coal mines as reserves are developed and the depth of mining increases [21-23].
The main contradictions in the requirements of regulatory documents relate to the width of the inter-panel pillars. Thus, to ensure endogenous fire safety during the mining of prone to spontaneous combustion flat seams, it is necessary to ensure reliable isolation of panels’ gob, for which it is required to leave coal pillars with a width of at least 25 m with the construction of explosion-proof brattice in cross-cuts. On the other hand, in order to prevent explosive collapses caused by rock pressure, it is necessary to use mainly yield pillars for the protection of gate roads, which, when mining out coal seams prone to spontaneous combustion, do not provide reliable insulation of mined out areas, since they are not a barrier to air movement.
In the conditions under study, the use of yield pillars of coal makes it possible to solve the problem of rock bumps, but does not exclude air leakage, which increases the risk of spontaneous combustion of coal. On the contrary, the layouts of developing panels with paired entries, which are traditionally used in Russian mines, leaving strong pillars 30-50 m wide, are often a source of not only an increased rock bump hazard caused by stress concentration in the edge parts of such pillars, but also an endogenous fire hazard at – air leaks through cross-cuts that connect paired gate roads. It should be noted that the pillar size optimization design remains a vital mining and technical problem [24-26], the effectiveness of its solution affects the stress state of the pillar and the amount of energy that can be accumulated in the pillar, and subsequently realized during a rock bump [16, 26, 27].
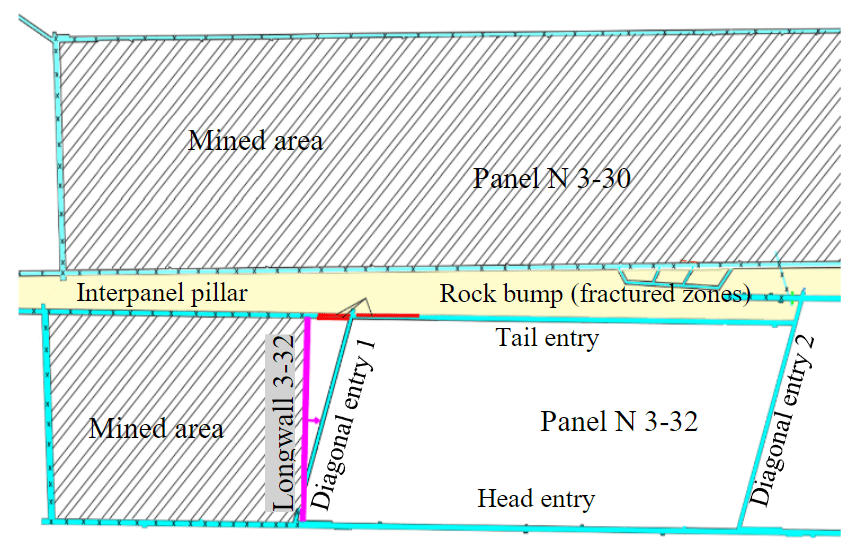
Fig.1. Panel layout for the seam 3-3a
Let us consider as an example the experience of seam mining at the Alardinskaya mine of the Alardinskoye deposit of the Kondomsky district of Kuzbass, the panels of which have repeatedly been the object of rock bumps [12] and endogenous fires [11]. When developing seam 3-3a, leaving wide (more than 30 m) pillars, the first panel N 3-30 was mined out without accidents. Subsequent mining of the adjacent panel N 3-32 was carried out with a longwall with length of 190 m (Fig.1). When the longwall face crossed the first diagonal entry, a rock bump occurred, which caused the complete destruction of the diagonal entry at the inter-panel pillar in a section se-veral tens of meters long (Fig.1). After the restoration of the gate roads, the work of the longwall face was continued, after which another rock bump occurred [12]. It should be noted that in accordance with the existing criteria for assessing the intensity of rock bump type [12], which occurred in mine Alardinskaya rock bump is classified as a “strong”, since the weight of the destroyed coal significantly exceeded 1000 kN. Meanwhile, the rock bump was registered as an incident [12]. A possible reason for this rock bump is the superposition of zones of longwall face abutment pressure and abutment pressure from the hanging of the undermined main roof of the seam from the side of the panel N 3-30 gob and thus creating a dangerous zone of increased abutment pressure when the advance entry (diagonal entry).
Obviously, in order to prevent the imposition of the zone of abutment pressure from the adjacent panel, a pillar should be left between the panels with a width exceeding the width of the zone of transferred abutment pressure. To completely exclude the influence of the abutment pressure from the adjacent panel, the width of the pillar should be at least two values of the width of the abutment pressure zone. As a result, while leaving wide pillars, conditions can be created to minimize the risk of rock bumps and, at the same time, endogenous fires. The possibility of complete exclusion of rock bumps with this approach, the use of very wide (up to 180 m) barrier pillars between the panels, is confirmed by the experience of seam mining in the conditions of mines in Utah in the USA [20, 21]. However, the problem is the significant loss of coal reserves prepared for extraction (up to 50 % of all reserves), which cannot be considered as acceptable when mining thick seams.
To minimize losses, it is necessary to consider the possibility of reducing the width of the barrier pillars to a value that will compensate for the significant effect of the abutment pressure from previous panels’ gob on the edge of the operating panel. To analyze the possibility of implementing such a solution, it is necessary to assess the level of stresses, which are directly related to the possibility of energy accumulation for rock bump. The features of the distribution of the stress state of the edge part of the rock mass for various panel layouts for the developing of panels are studied:
- Implemented at the Alardinskaya mine: development of panel by two single entries with diagonal entries between them and leaving impenetrable inter-panel pillars of coal 30-50 m wide between panels (Fig.2, a).
- Implemented at a mine in Utah (USA): development of panel by two pairs of entries, leaving impenetrable wide (up to 180 m) inter-pillar (barrier) pillars between the panels (Fig.2, b).
- The proposed layout, the parameters of which need to be investigated: development of panels by two pairs of entries, leaving impenetrable wide pillar pillars with a width of 50 to 100 m between the panels (Fig.2, c). An analysis of the stress-strain state of the mass for the first option for the development of panels (Fig.2, a) will make it possible to identify the causes of rock bumps in the conditions of the Alardinskaya mine. A comparative analysis of the second (Fig.2, b) and third (Fig.2, c) layouts will make it possible to establish the degree of influence of the adjacent mined out area with different widths of the inter-panel pillar and determine such a width of this pillar, which will ensure the minimum the influence of the abutment pressure zone from the adjacent gob with the least loss of coal in the inter-panel pillar.
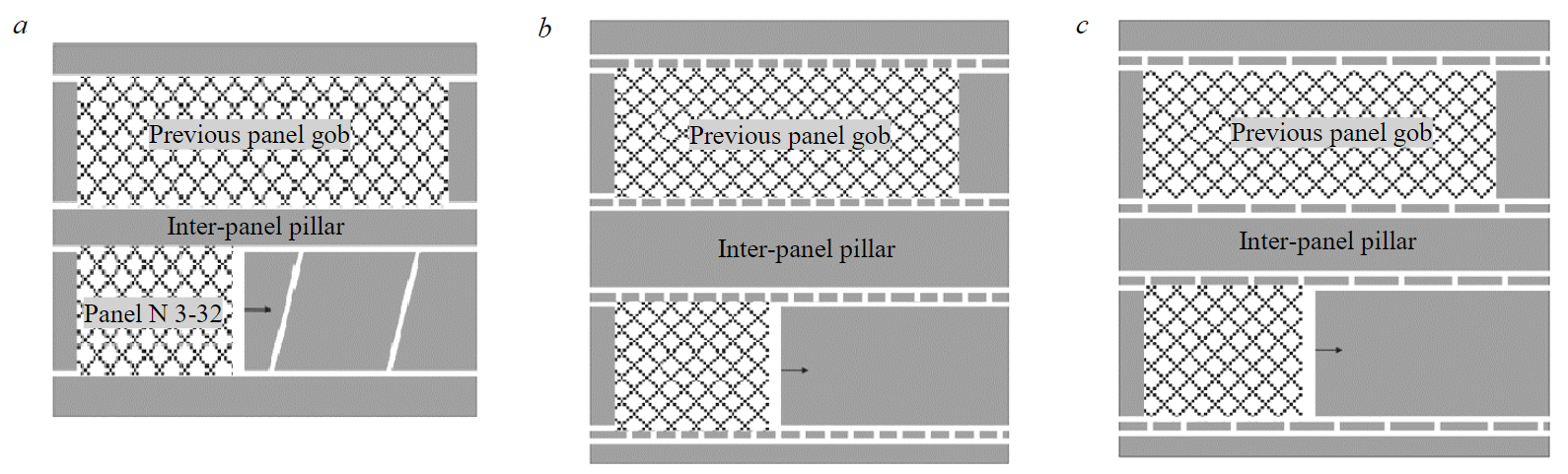
Fig.2. Considered options for developing the panel layout: a – Alardinskaya mine; b – US mine; c – proposed layout
Numerical research technique
To analyze the stress-strain state of the rock mass of the options and develop panel layout (Fig.2), numerical studies were performed using the finite element method, which is widely used in the practice of solving such problems. The method fully ensures the achievement of the set goals related to the assessment of the stress state of the critical elements and zones of the array and the determination of the rational parameters of the inter-panel coal pillars. The studies were carried out using the ANSYS Mechanical software package. The developed three-dimensional model of the rock mass included the following elements: a fragment of two adjacent panels (previous panel gob and operating); system of main head and tail gates; mined out areas.
The rock mass was considered as heterogeneous, isotropic (within individual rock layers and seams) and non-linearly deformable. To describe the behavior of rocks, the widely used Coulomb – Mohr model was applied, which makes it possible to take into account the transition of the edge parts of the mass and pillars to the limit state due to the excess of the tensile or shear strength of the rocks. As the initial conditions for modeling, the stress field formed by gravity (taking into account the density of the rocks) was set. To minimize the influence of boundary conditions, the simulated section of the mass had dimensions of 500×1200×900 m, i.e. the entire undermined and part of the overmined rock mass was modeled. The main properties of the rocks used in the research are presented in the table, the depth was assumed to be 600 m.
Physical and mechanical properties of rocks
Object |
Density, kg/m3 |
Deformation modulus, GPa |
Poisson's ratio |
Adhesion coefficient, MPa |
Angle of internal friction, deg |
|
Coal seam |
1380 |
2.8 |
0.25 |
1.5 |
23 |
|
Adjacent strata |
2600 |
30 |
0.25 |
12 |
25 |
|
Rocks of the main roof |
2700 |
42 |
0.25 |
15 |
25 |
|
Gob |
2000 |
0.03 |
0.4 |
– |
– |
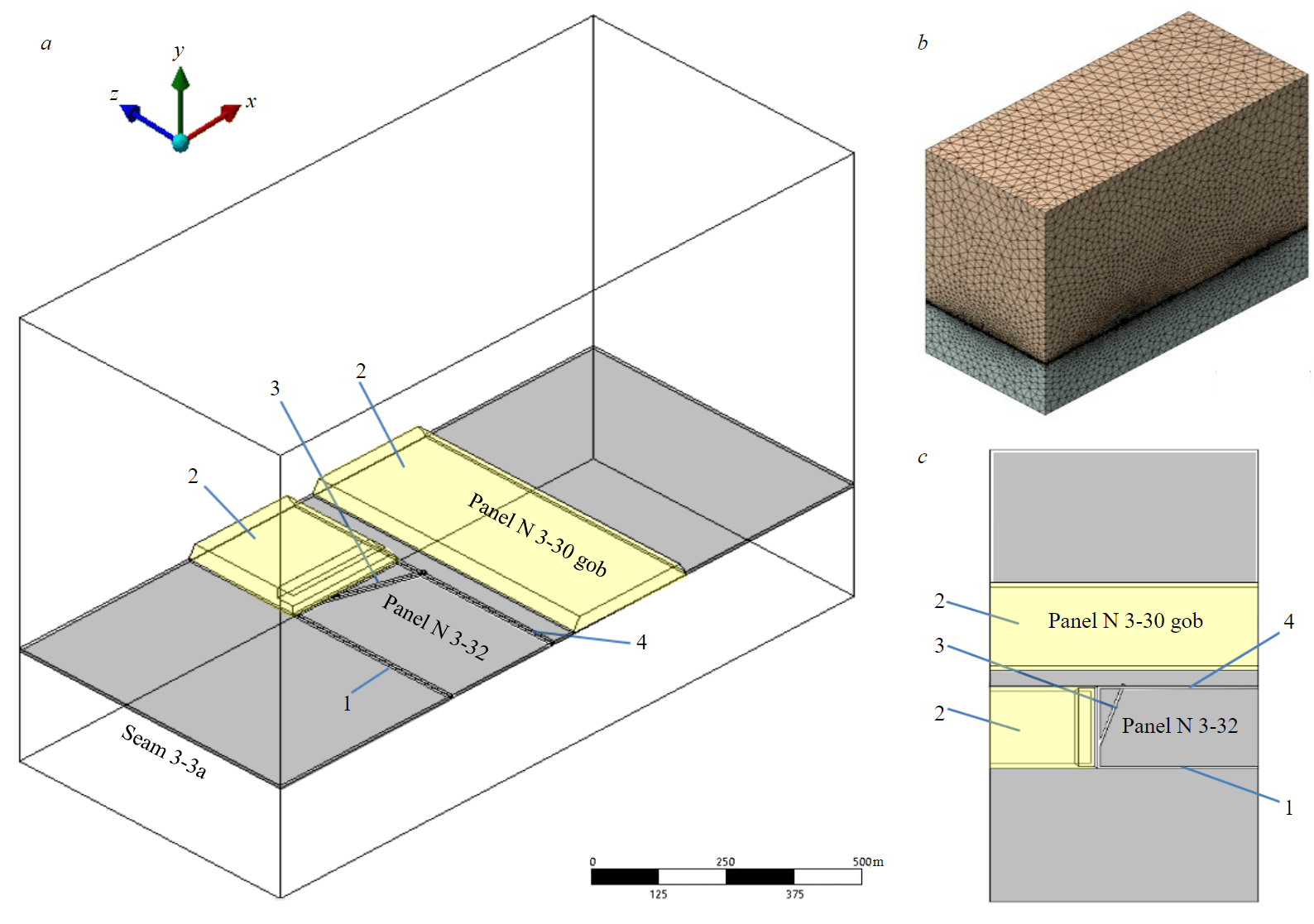
Fig.3. Three-dimensional model of a rock mass: a – wireframe model; b – finite element model; c – section of the wireframe model in the plane of the coal seam
Numerical studies were carried out in two stages. At the first stage, for the conditions of the Alardinskaya mine, an assessment was made of the stress-strain state of the mountain mass rocks in the period preceding the rock bumps in the longwall panel 3-32 (see Fig.1). Figure 3 shows a mass model, which corresponds to the layout for developing the panel, shown in Fig.1 and 2, a. The model contains a coal seam 3-3a, adjacent strata, mined out areas 2 (panel N 3-30 and N 3-32 gob), as well as entries of panel 3-32 (conveyor 4 and head entry 1 and a diagonal entry 3).
At the second stage of the research, a comparative analysis of the stress state of the rock mass for the layout used in the USA (Fig.2, b) and the proposed option (Fig.2, c) was carried out. The width of the inter-panel pillar in the proposed version varied from 50 to 130 m in increments of 10 m. The choice of this range is due to the fact that the width of the inter-panel pillar is less than 50 m, as the accumulated experience of mining of bump prone seams [21] is insufficient to compensate for the abutment pressure from the adjacent panel’s gob and to prevent rock bump. On the contrary, the width of the inter-panel barrier pillar of 180 m, which ensures safe seam mining and is accepted in the USA [20], is completely unacceptable due to the magnitude of the loss of prepared coal reserves in such pillars. Since the width of the yield pillars Zp, according to the requirements of the current regulatory documents, should be at least m + 1, where m is the mineable seam thickness (without taking measures to increase the yield), or should be m + 1 < Zp < 0.1L, where L is the length of the abutment pressure zone. Taking into account the length of the abutment pressure zone of 100 m (determined in accordance with the instructions), the width of the yield pillar should not exceed 5.5 m in the absence of its softening and 10 m when special measures are taken. In the study, the width of the yield pillars was assumed to be 8 m.
Discussion of the results
Figure 4 shows the distribution of stresses in the plane of seam 3-3a near the panel N 3-32 immediately before the rock bump. Before the longwall crosses the diagonal entry, a triangular technological pillar appeared in the seam. The stresses in this triangular pillar at the time of rock bump exceeded the stresses in the front zone of the stope abutment pressure by 1.4-2 times. Maximum stresses in the inter-panel pillar (55 MPa) are observed behind the longwall face – between two mined-out spaces. It can be seen (Fig.4) that the stresses in the pillar between panels N 3-30 and 3-32 increase from 41 to 48 MPa as the longwall approaches. In addition, even before the longwall approach, the stress concentration in the vicinity of the conveyor road N 3-32, which is in the zone of influence of the abutment pressure from the adjacent panel N 3-30 gob, was 1.5 and 1.9 of the values of the initial geostatic level (from the side of the panel N 3-32 and the formed inter-panel pillar, respectively). Thus, the zone of dynamic manifestations of rock pressure is characterized by an increased level of stresses in the triangular pillar, caused by the superposition of abutment pressure zones in front of the active longwall and from the side of the panel N 3-30 gob.
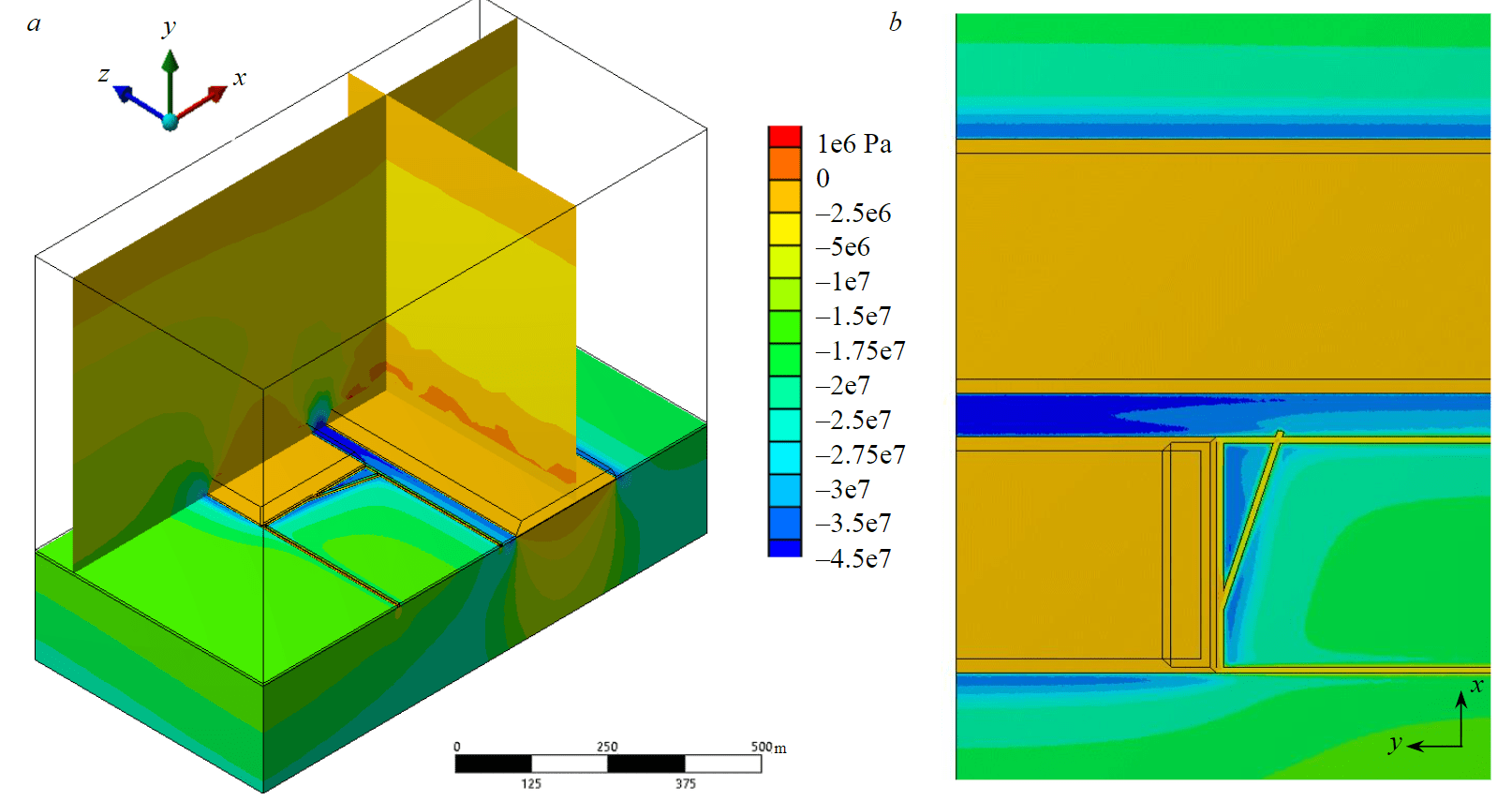
Fig.4. Vertical stress fields before rock burst: a – in a three-dimensional rock mass; b – in the plane of the coal seam 3-3a
It is possible to eliminate the conditions for the formation of significant areas of high stresses by reducing (eliminating) the influence of the abutment pressure from the side of the adjacent previous panel gob by increasing the width of the inter-panel pillar, with the obligatory prevention of the transition of diagonal entries within the working panel. Of course, the use of such diagonal entries is due to the need to comply with the requirements of the safety rules in force in Russia to ensure that in an emergency, people can get out to a fresh air during the operation of the self-rescuer. It is possible to exclude the use of diagonal entries if a fresh air is supplied from each side of the panel, which is successfully implemented when using multi-entry development in the considered variant (see Fig.2, b and c), which provides the paired gate roads on each side of the panel. It can be concluded that the layout for the development of panels, implemented at the Alardinskaya mine (see Fig.1), are characterized by increased rock bump hazard, to reduce which it is proposed to use a multi-entry layout for developing panels (see Fig.2, c). Moreover, the width of the inter-panel pillars for the conditions of the Alardinskaya mine requires justification, taking into account the need to compensate for the abutment pressure of the mined-out area of the panel’s gob and minimize the loss of coal in such a pillar.
Elements of the results of the second stage of research aimed at identifying the rational width of the barrier (wide) inter-panel pillar for the conditions of the Alardinskaya mine are shown in Figs.5 and 6. Vertical stress is distributed along a line passing through the seam parallel to the coal face, crossing the panel outside the zone of influence of the abutment pressure of the active longwall face 3-32, at the extreme values of the values from the considered range of widths of the inter-panel pillar – 50 and 130 m (Fig.5).
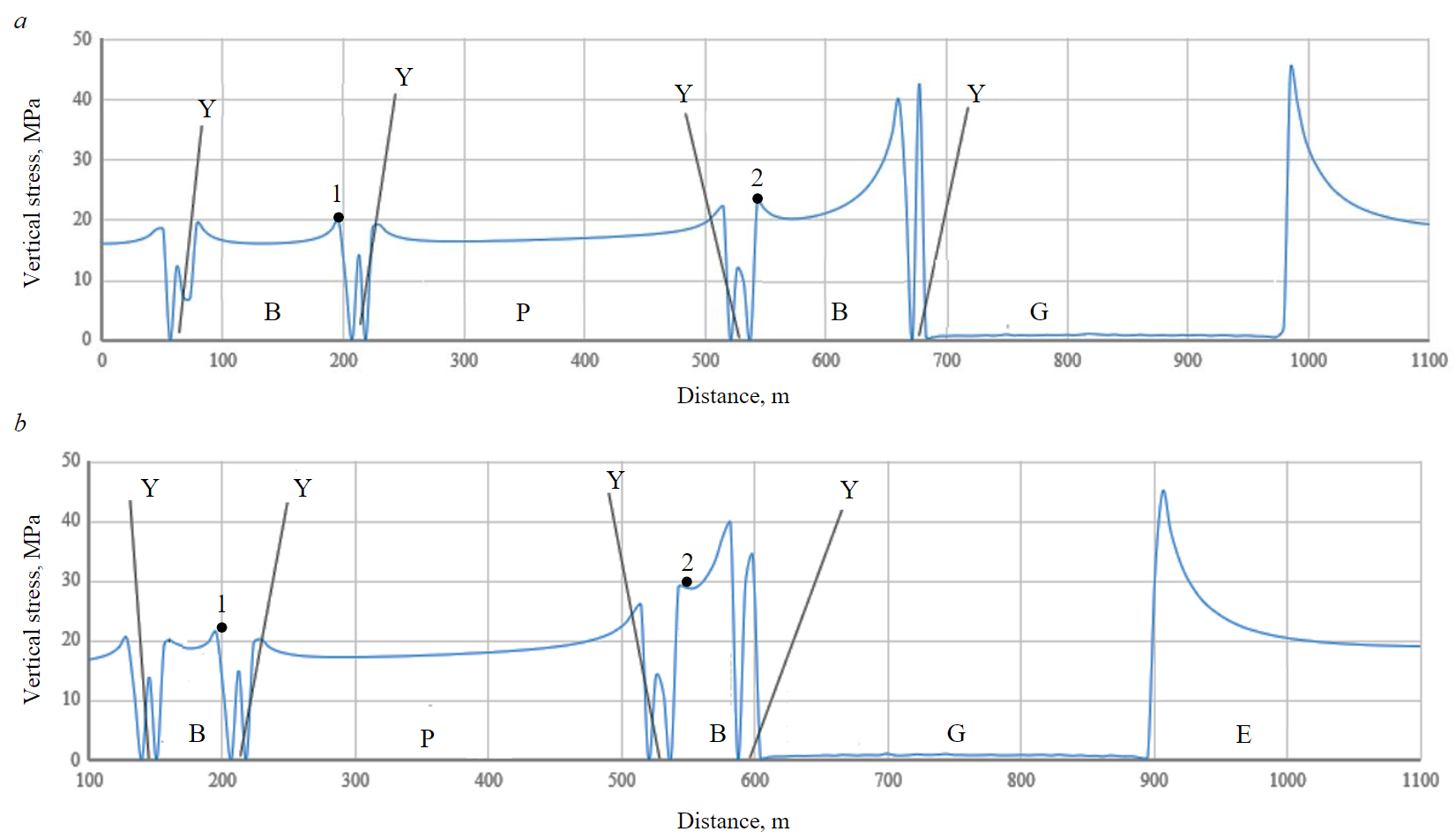
Fig.5. Diagrams of vertical stresses in the coal seam in the zone of abutment pressure from of the active longwall face at different widths inter-panel pillar: a – 130 m; b – 50 m Y – yield pillar; B – barrier pillar; P – panel; G – gob; E – edge of the coal mass
As shown in Fig.5, a, leaving an inter-panel pillar with a width of 130 m does not completely exclude the influence of the abutment pressure from adjacent the panel’s gob, however, the magnitude of the stresses in the edge part of the wide inter-panel pillars located on different sides of the panel (points 1 and 2), differs by less than 10 %. This result contradicts the experience of mining out shock-prone layouts in the USA, where the 130 m wide pillar completely excludes the influence of the abutment pressure. However, the big difference (almost three times) of the extracted seam thickness in the conditions of the Alardinskaya mine compared with the conditional Utah's medium-thickness seam developments accounts for the significant increase in abutment pressure zone. In accordance with the provisions of the current regulatory documents, the width of the abutment pressure zone for a reservoir with a thickness of 1.5 and 4.5 m differs by almost two times (is 62 and 100 m, respectively).
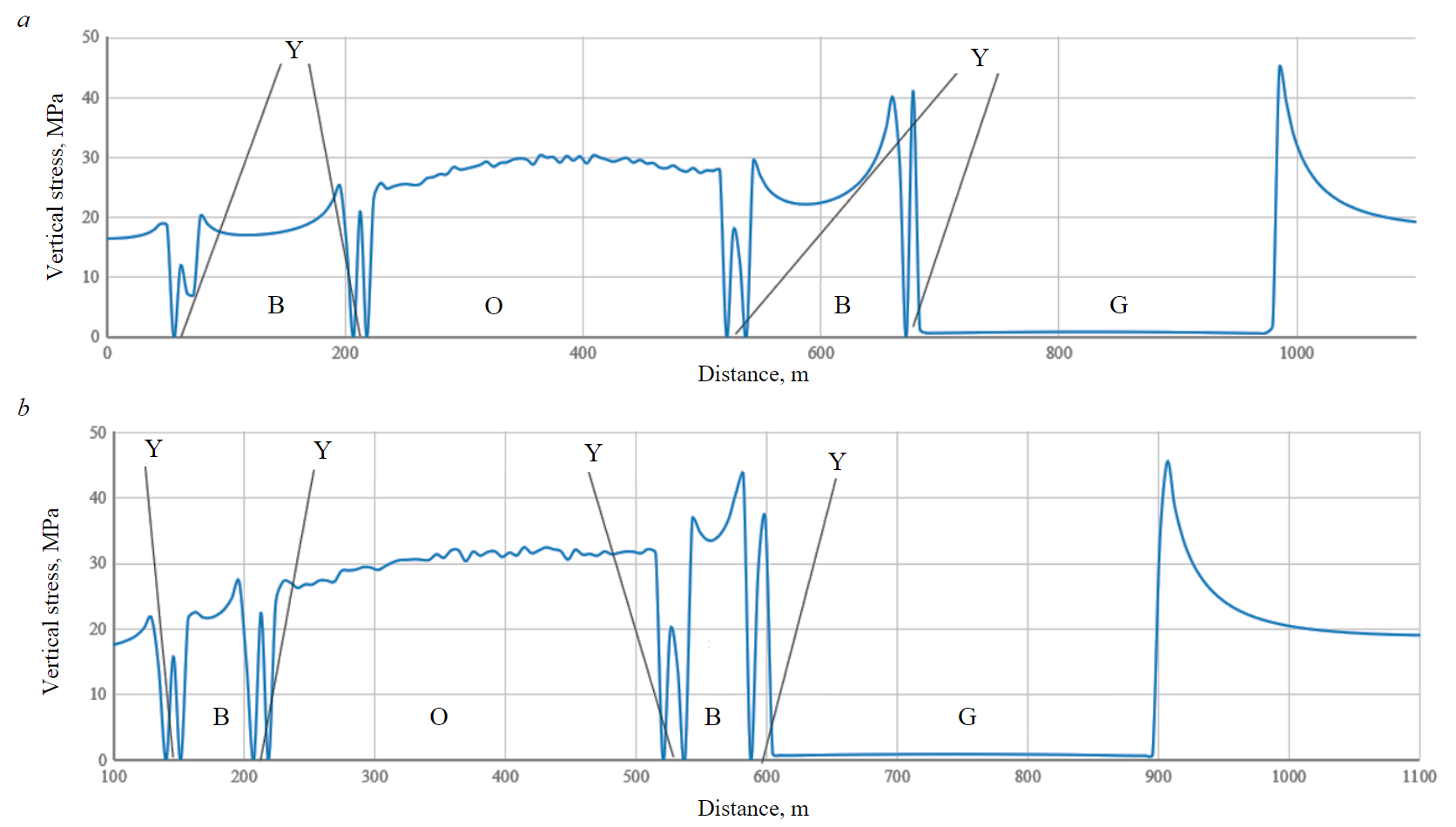
Fig.6. Diagrams of vertical stresses in the coal seam in the zone of abutment pressure from of the operating longwall face at different widths inter-panel pillar: a – 130 m; b – 50 m See the caption of Fig.5; O – operating longwall face
While face advancing, the width of the abutment pressure zone increases by 1.5 times. Howe-ver, it should be noted that in such geological conditions, when applying the layouts using a system of inter-panel pillars (wide and narrow yield), the use of regulatory documents to determine the width of the abutment pressure zone is unacceptable, since these methods are intended to estimate the width of the abutment pressure zone exclusively in the edge part of the array. The calculation of the width of the abutment pressure zone using the instructions made it possible to establish that for the simulated conditions the width of the zone of residual abutment pressure is 93 m, and for a moving face it is 139 m. The obtained results of calculations explain some influence of the abutment pressure from the gob side on entries with a width of the inter-panel pillar of 130 m, which determined by numerical studies.
Figure 5, b shows an increase in the influence of the abutment pressure from the side of the panel’s gob with a decrease in the width of the inter-panel pillar to 50 m: in the edge part of the pillar, the pressure increases to 40 MPa, which is 30 % higher than the stresses at the corresponding point of maximum stress with the width of the inter-panel pillar 130 m (Fig.5, a).
When the longwall face approaches, the zones of abutment pressure are superimposed, as a result, the pressure in a wide inter-panel pillar increase (Fig.6). However, the maximum difference in the stress level for pillars 50 and 130 m wide is 24 %. At the same time, the stress level in yield pillars is significantly lower (19.8 MPa).
The highest stress level in the inter-panel pillar takes place after the longwall face crossing the passage. Figure 7 shows stress diagrams in the inter-panel pillar for various options for developing the panel, corresponding to the layouts shown in Fig.2. The level of loads in the inter-panelf pillar, which has a width of 30 m, in the conditions of the Alardinskaya mine exceeds 50 MPa in a section about 20 m long along the width of the pillar (Fig.7, a). The decrease in the stress level in the edge of the pillar with a width of about 5 m is due to the transition of edge part of the seam to the limit state and the development of plastic deformations. Comparison of Fig.7, b, c makes it possible to estimate the change in the level of loads with the corresponding width of the inter-panel pillar (50 and 130 m), used in conjunction with yield pillars. The use of wide inter-panel (barrier) pillars allows not only to significantly reduce the load on their edge parts to 48 and 40 MPa, respectively, but also to reduce the length (area) of zones with high concentrations.
The analysis of the results of numerical studies made it possible to determine the width of the inter-panel pillar of 60 m as rational, providing compensation for the growth of stresses in the zone of influence of the abutment pressure (by no more than 20 % of the initial geostatic level) with the smallest width of the pillar (loss of coal reserves in the pillars). It should be noted that the result obtained is valid only to a depth of 600 m. Application of the proposed layout for the development of panels by paired entries with the formation of yield pillars 8 m wide between them and leaving inter-panel pillars 60 m wide between the panels leads to a decrease in the sectional recovery factor.
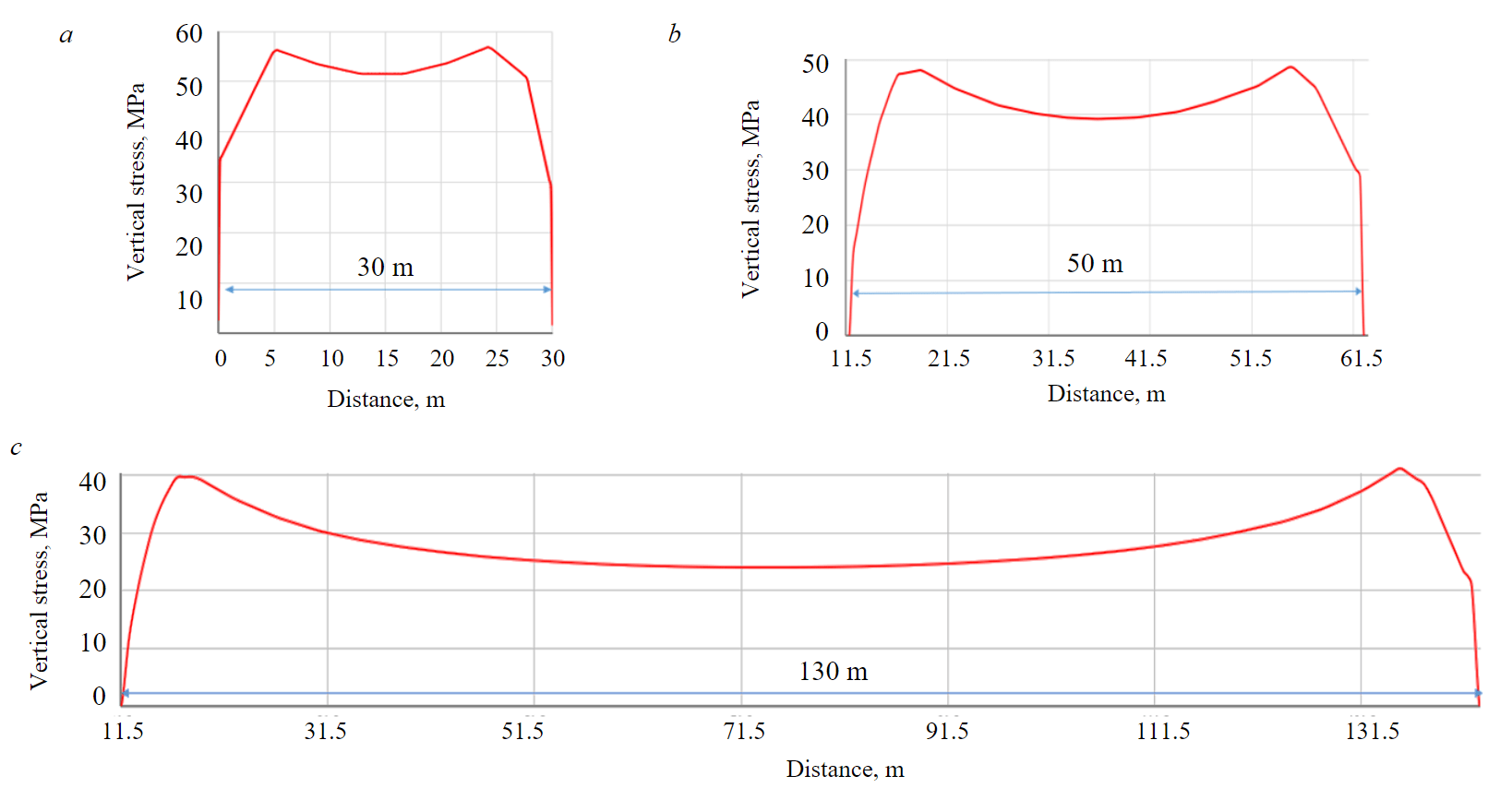
Fig.7. Distribution of vertical stresses in the inter-panel pillar after the passage of the longwall face: a – inter-panel pillar 30 m (without yield pillars); b – inter-panel pillar 50 m and yield pillars 8 m; c – inter-panel pillar 130 m and yield pillars 8 m
It is possible to increase the recovery factor by increasing the length of the longwall from 200 to 400 m or more. The experience of successful operation of longwall faces 400 m or more in length is available both in Russia [27, 28] and abroad [29]. For example, in the United States, more than 30 % of all longwalls have a length of more than 400 m (up to 482 m) [29]. An almost twofold increase in the length of the longwall face for the considered mining and geological conditions will make it possible to fully compensate for the increased losses in the wide inter-panel pillars primarily by reducing the number of such pillars within the mine field. Thus, the proposed layout of multi-entry development in conditions of simultaneous danger of spontaneous combustion of coal and rock bumps makes it possible to eliminate the risk of endogenous fires due to the reliable isolation of panels’ gob and the danger of rock bumps, by minimizing the influence of panels’ gob, as well as the exclusion of diagonal entries.
Conclusion
The simultaneous danger of rock bumps and spontaneous combustion of coal seams do not allow to effectively apply layouts at great depths that are widely used in underground coal mining when developing seams in less difficult conditions: development of panels by pair entries and a longwall system leaving yield or strong pillars (30-50 m wide). The choice and justification of an effective layout in such conditions is complicated by the inconsistency of the approaches traditionally used to ensure geodynamic safety and endogenous fire safety: leaving yield pillars that exclude the accumulation of energy required for rock bump, and leaving wide pillars that provide reliable aerodynamic isolation of mined out areas. The use of traditional technological solutions in such conditions leads to a high accident rate of mining operations, which necessitates the identification of causes and elimination of conditions for geodynamic manifestations and spontaneous combustion of coal.
An analysis of the results of numerical studies allows to conclude that the rock bumps in the conditions of the Alardinskaya mine [12] were facilitated by the simultaneous imposition of the abutment pressure of the active longwall and the abutment pressure from the side of the panel’s gob, which was accompanied by the formation of a pillar with a critical width when the longwall face crossed the diagonal entry.
The exclusion of conditions for rock bumps requires a change in the layout of development of panels, including the refusal to carry out diagonal entries, as well as minimization (exclusion) of the influence of abutment pressure from the adjacent panel’s gob. Such requirements are met by a layout that has found wide application in the conditions of mining at great depths of bump-prone seams in the state of Utah (USA) [20, 21], which provides multi-entry preparation of panels with yield pillars between paired entries, carried out on each side along the length of the panel, and leaving very wide (up to 180 m) inter-panel (barrier) pillars to exclude the influence of panels’ gob, and, as a result, the exclusion of the high stress concentrations from the causes of rock bumps. At the same time, leaving such wide pillars significantly increases the loss of coal reserves in the subsoil and does not correspond to rational reserves usage, which predetermines the need to improve such layouts.
The search for a balance between the coal loss rate in wide pillars and the need to ensure geodynamic safety, according to the authors, is a necessary condition for rational safe deposit usage in the difficult geological conditions. The geomechanical substantiation of the parameters of layouts using the approaches of continuum mechanics (finite element method) makes it possible to simulate the stress-strain state of a rock mass to identify the causes of rock bumps and a comparative analysis of various options for the development and mining panels.
The performed numerical studies have shown the possibility of a significant reduction in the width of the pillars while ensuring the minimum influence of the abutment pressure from the adjacent panel’s gob. For the conditions of the mine, the Alardinskaya width of the inter-panel pillar when mining at a depth of 600 m can be recommended up to 60 m, the width of the yield pillars is 8-10 m. The increase in losses in wide inter-panel pillars when using the layout, which involves leaving wide and yield pillars, can be minimized (or completely eliminated) by increasing the length of the longwall to 300-400 m. Thus, the implementation of proposed layouts in Alardinskaya mine condition prevents explosive collapses with a significant decrease in coal losses [20] in the implementation of layouts with wide (over 100 m) inter-panel pillars, which at the same time provide reliable aerodynamic isolation of mined areas due to independent isolated pillars (there are no ventilation entries between the entries of adjacent panels, and the width of inter-panel pillars significantly exceeds the minimum required for the layout prone to spontaneous combustion of coal seams for the most difficult mining and technical situations[17]).
It is obvious that the variety of mining and geological conditions of underground coal mining and possible mining and technical situations predetermines the need to justify the parameters of the proposed layout for each specific case, however, the basic layout itself, which provides for leaving the system of inter-panel pillars to exclude the dangerous rock bump conditions in the panels, as well as the recommended approach to determining the width of the inter-panel pillars can be used for the conditions of various deposits, characterized by the simultaneous danger of rock bumps and spontaneous combustion of coal.
Further studies will be related to the substantiation of the parameters for the development of overmined adjacent seams in the conditions of the Alardinskaya mine, taking into account the influence of wide pillars, since the complexity of mining of the seams in the considered conditions of the simultaneous influence of several hazardous factors is exacerbated by the proximity of the seams, which predetermines their dangerous mutual influence when leaving strong pillars [30, 31].
References
- Stebnev A.V., Muchortikov S.G., Zadkov D.A., Gabov V.V. Analysis of operation of powered longwall systems in mines of SUEK-Kuzbass. Eurasian Mining. 2017. N 2, p. 28-32. DOI: 10.17580/em.2017.02.07
- Karpov G.N., Leisle A.V. Qualitative Assessment of Strain Stress Distribution of Rock Massif in the Vicinity of Pre-Driven Recovery Room. Journal of Industrial Pollution Control. 2017. Vol. 33. Iss. 1, p. 840-846.
- Peng S.S. Longwall mining. London: CRC Press, 2019, p. 562. DOI: 10.1201/9780429260049
- Reshetnyak S., Bondarenko A. Analysis of Technological Performance of the Extraction Area of the Coal Mine. E3S Web of Conferences. 2018. Vol. 41. N 01014. DOI: 10.1051/e3sconf/20184101014
- Kazanin O.I., Sidorenko A.A., Meshkov A.A. Organizational and Technological Principles of Realization of the Modern High Productive Longwall Equipment Capacity. Ugol. 2019. N 12, p. 4-13 (in Russian). DOI: 10.18796/0041-5790-2019-12-4-13
- Meshkov A.A., Volkov M.A., Ordin A.A. et al. On Record Length and Productivity of Highwall Mining the V.D.Yalevsky Mine. Ugol. 2018. N 7, p. 4-7 (in Russian). DOI: 10.18796/0041-5790-2018-7-4-7
- Nguyen K.L., Gabov V.V., Zadkov D.A. Improving efficiency of cleanup and coal flow formation on conveyor by shearer loader with accessorial blade. Eurasian Mining. 2019. Vol. 2019. Iss. 1, p. 37-39. DOI: 10.17580/em.2019.01.09
- Slastunov S.V., Yutyaev E.P. Justified selection of a seam degassing technology to ensure safety of intensive coal mining. Journal of Mining Institute. 2017. Vol. 223, p. 125-130. DOI: 10.18454/PMI.2017.1.125
- Chemezov E.N. Industrial safety principles in coal mining. Journal of Mining Institute. 2019. Vol. 240, p. 649-653. DOI: 10.31897/PMI.2019.6.649
- Rudakov M.L., Kolvakh K.A., Derkach I.V. Assessment of Environmental and Occupational Safety in Mining Industry during Underground Coal Mining. Journal of Environmental Management and Tourism. 2020. Vol. 11. N 3, p. 579-588.
- Portola V.A., Galsanov N.L., Shevchenko M.V., Lugovtsova N.Yu. Hazard of Endogenous Fires in Kuzbass Coal Mines, Vestnik Kuzbasskogo gosudarstvennogo tekhnicheskogo universiteta. 2012. N 2, p. 44-47 (in Russian).
- Klishin V.I., Opruk G.Yu., Cherepov A.A. Complex Method of Pressure Bump Hazard Mitigation in Coal Mines. Ugol. 2018. N 9, p. 56-62 (in Russian). DOI: 10.18796/0041-5790-2018-9-56-62
- Nagornov D.O., Kremcheev E.A., Kremcheeva D.A. Research of the condition of regional parts of massif at longwall mining of prone to spontaneous ignition coal seams. International Journal of Civil Engineering and Technology. 2019. Vol. 10. Iss. 1, p. 876-883.
- Meleshko A.V. Estimation of the rock bump hazard of inter-drift pillars during the development of coal reserves of the mine “Kotinskaya”. Mining informational and analytical bulletin. 2012. N 3, p. 3-7 (in Russian).
- Meshkov A.A., Popov A.L., Popova Yu.V. et al. Prediction of hazardous phenomena within operating coal seam for the Yalevsky mine field. Mining informational and analytical bulletin. 2020. Vol. 2, p. 22-33 (in Russian). DOI: 10.25018/0236-1493-2020-2-0-22-33
- Tsirel S.V., Shabarov A.N., Prosvetova A.A. Predictive Estimate Geodynamic Hazard Associated with Design of Mining. Mining informational and analytical bulletin. 2015. N 4, p. 323-326 (in Russian).
- Fengqiang Gong, Yunliang Wang, Zhiguo Wang et al. A new criterion of coal burst proneness based on the residual elastic energy index. International Journal of Mining Science and Technology. 2021. Vol. 31. Iss. 4, p. 553-563. DOI: 10.1016/j.ijmst.2021.04.001
- Hongwei Wang, Ruiming Shi, Daixin Deng et al. Characteristic of stress evolution on fault surface and coal bursts mechanism during the extraction of longwall face in Yima mining area, China. Journal of Structural Geology. 2020. Vol. 136. N 104071. DOI: 10.1016/j.jsg.2020.104071
- Xuwei Li, Yanjiang Chai. Determination of pillar width to improve mining safety in a deep burst-prone coal mine. Safety Science. 2019. Vol. 113, p. 244-256. DOI: 10.1016/j.ssci.2018.12.003
- Mark C. Coal bursts in the deep longwall mines of the United States. International Journal of Coal Science & Technology. 2016. Iss. 3, p. 1-9. DOI: 10.1007/s40789-016-0102-9
- Mark C., Gauna M. Pillar design and coal burst experience in Utah Book Cliffs longwall operations. International Journal of Mining Science and Technology. 2021. Vol. 31. Iss. 1, p. 33-41. DOI: 10.1016/j.ijmst.2020.12.008
- Batugin A.S., Lan Tianwei, Zhang Hongwei, Li Sheng. Studies on Geodynamic Conditions of Rock Bursts Development in Coal Mines of Tszinsi Deposit in China. XXI century. Technosphere Safety. 2018. Vol. 3. N 2, p. 10-16 (in Russian). DOI: 10.21285/2500-1582-2018-2-10-16
- Peng-qi Qiu, Jian-guo Ning, Jun Wang et al. Mitigating rock burst hazard in deep coal mines insight from dredging concentrated stress: A case study. Tunnelling and Underground Space Technology. 2021. Vol. 115. N 104060. DOI: 10.1016/j.tust.2021.104060
- Sidorenko A., Alekseev V., Sirenko Y. Investigation of Alardinskaya mine coal bumps causes using computer simulation of rock massif stress conditionals. E3S Web of Conferences. 2021. Vol. 326. N 00008. DOI: 10.1051/e3sconf/202132600008
- Shuai Zhang, Xufeng Wang, Gangwei Fan et al. Pillar size optimization design of isolated island panel gob-side entry driving in deep inclined coal seam – case study of Pingmei N 6 coal seam. Journal of Geophysics and Engineering. 2018. Vol. 15. Iss. 3, p. 816-828. DOI: 10.1088/1742-2140/aaa148
- Junfei Zhang, Fuxing Jiang, Sitao Zhu, Lei Zhang. Width design for gobs and isolated coal pillars based on overall burs-tinstability prevention in coal mines. Journal of Rock Mechanics and Geotechnical Engineering. 2016. Vol. 8. Iss. 4, p. 551-558. DOI: 10.1016/j.jrmge.2015.12.006
- Lan Tianwei, Zhang Hongwei, Batugina I.М. et al. Research on rockburst system energy of coal mine. Mining informational and analytical bulletin. 2015. N 6, p. 287-293 (in Russian).
- Kozlov A.V., Teslya A.B., Chzhan S. Principles of assessment and management approaches to innovation potential of coal industry enterprises. Journal of Mining Institute. 2017. Vol. 223, p. 131-138. DOI: 10.18454/PMI.2017.1.131
- Fiscor S. Longwalls Lead the Way Underground. Coal Age. 2020. Vol. 125. N 1, p. 16-24.
- Kovalski E.R., Karpov G.N., Leisle A.V. Investigation of Underground Entries Deformation Mechanisms within Zones of High Stresses. International Journal of Civil Engineering and Technology. 2018. Vol. 9. Iss. 6, p. 534-543.
- Nikiforov A.V., Vinogradov E.A., Kochneva A.A. Analysis of multiple seam stability. International Journal of Civil Engineering and Technology. 2019. Vol. 10. Iss. 2, p. 1132-1139..