Индикаторная оценка надежности функционирования шахтных вентиляционно-дегазационных систем
Аннотация
Управление газовыделением в шахтах осуществляется вентиляционно-дегазационными системами, которые обеспечивают аэрологическую безопасность шахт или минимизируют аэрологические риски. Система вентиляции шахты и отдельных ее участков включает значительное число технических устройств и оборудования, а воздуховодами являются преимущественно горные выработки, состояние которых определяет качество вентиляционной сети (ее пропускную способность) и зависит от ряда горнотехнических факторов. Аналогичным образом одними из важнейших элементов дегазационной системы, включающей свою цепочку технологического оборудования, являются скважины, а в ряде случаев и горные выработки. Таким образом, шахтные системы вентиляции и дегазации нельзя отнести к чисто техническим системам, так как они включают горнотехнические элементы, характеризующиеся высокой изменчивостью определяющих параметров. Для оценки их надежности приходится использовать различные комбинированные методы, включающие дополнительные характеристики применительно к горной составляющей. При этом надежность технических устройств, обеспечивающих функционирование шахтных вентиляционно-дегазационных систем, в значительной степени определяет эффективность (устойчивость и надежность) работы этих систем и, следовательно, влияет на уровень аэрологических рисков. Описанный подход к оценке надежности вентиляционно-дегазационных систем угольных шахт при анализе аэрологических рисков базируется на разработанной системе индикаторов риска по фактору метана и позволит определять динамику риска в автоматическом режиме на основе контроля параметров состояния вентиляционно-дегазационной системы.
Введение
Горнодобывающая промышленность характеризуется наиболее опасными условиями труда, особенно при подземной разработке месторождений, что существенно влияет на технико-экономические показатели добывающих компаний [26]. Обеспечение безопасных и здоровых условий труда – одна из важнейших гарантий государства, закрепленная основными федеральными законами [2]. Управление безопасностью труда [2] предусматривает систему мер организационного и технического характера, включающих контроль и надзор за соблюдением установленных норм и правил [20]. На газообильных высокопроизводительных угольных шахтах основным фактором, ограничивающим нагрузку на очистные и проходческие забои, а также представляющим серьезную опасность, является метановыделение [8]. Переход к риск-ориентированному подходу в контрольно-надзорной деятельности требует разработки системы индикаторов риска, по которым можно оценивать безопасность ведения работ на любом предприятии. Для снижения взрывоопасности в угольных шахтах используется комплекс защитных технологий, который называется управлением газовыделением в угольных шахтах. Этот комплекс осуществляет целенаправленное перераспределение потоков метановоздушной смеси в сети горных выработок или снижение их газообильности инженерными методами. Для оценки эффективности этого процесса с точки зрения его вклада в снижение производственного риска, необходимо иметь систему показателей (индикаторов риска), отражающих степень изменения уровня опасности по отношению к эталонному – минимально возможному или технически достижимому.
Статья посвящена обоснованию такой системы индикаторов, которая позволила бы в автоматическом режиме на основе контроля параметров состояния вентиляционно-дегазационной системы определять динамику риска по фактору метана.
Методология
Переход к риск-ориентированному подходу в осуществлении государственной контрольно-надзорной деятельности предполагает необходимость определения ключевых ценностей, охраняемых государством, а также ключевых рисков и их источников, возможностей воздействия на указанные источники с целью снижения рисков. По выбранным ключевым рискам предполагается разработка укрупненных групп обязательных требований и способов контроля их соблюдения. Аэрологические риски при подземной добыче угля относятся к ключевым [13]. По данным ежегодных отчетов Ростехнадзора (2019 и 2020 гг.), аварийность угольных шахт по аэрологическим факторам остается достаточно высокой. А если рассматривать причины крупных аварий на газовых шахтах, то их катастрофическое развитие всегда обусловлено неудовлетворительным состоянием систем проветривания, дегазации и пылеподавления. Но системы, обеспечивающие аэрологическую безопасность, достаточно сложны и включают в себя множество разнородных элементов, что осложняет организацию контроля определяющих факторов. Важнейшую роль для опасных производств играет государственная система надзора и контроля [2], при этом на эффективность управления безопасностью труда значительно влияет стратегия производственного контроля [28, 32]: при высокой степени жесткости эффективность повышается, но краткосрочно; при более свободном подходе постепенно повышается общая культура безопасности [29]. Поэтому принятый курс изменения политики государственного надзора [11] представляется прогрессивным, но на первой стадии внедрения риск-ориентированного подхода возможен рост производственных рисков для угольных шахт (в первую очередь аэрологических) из-за перехода к контролю укрупненных показателей (индикаторов) безопасности [9].
Общепринятые определения производственного и приемлемого рисков как вероятностных характеристик в горном деле не нашли широкого применения [9] в силу высокой стохастичности горнотехнических факторов производственных рисков и их постоянной изменчивости [13]. Аналогичным образом методы оценки шахтных вентиляционных систем на основе теории надежности, предлагаемые отечественными и зарубежными учеными [25, 31], остались невостребованными. Определение вероятностных оценок требует дополнительных трудозатрат, даже создания соответствующей службы, которая будет заниматься только статистикой и ее анализом. Более целесообразным представляется использование в качестве индикаторов риска тех показателей, которые действительно отслеживаются на предприятиях. Эта идея рассматривается на примере технических систем – наиболее предсказуемом элементе технологической схемы. Предлагается оценивать риски, связанные с работой оборудования, индикаторами, которые определяют надежность работы горной техники.
В отечественной практике технологии обеспечения взрывобезопасности угольных шахт по фактору метановыделения называются управлением газовыделением [12]. Оборудование обеспечивающих систем аэрологической безопасности (вентиляции, кондиционирования, дегазации, мониторинга) – важнейший их элемент, так как его бесперебойная работа и надежность [5] являются залогом поддержания требуемых параметров шахтной атмосферы.
Целью управления газовыделением является соблюдение требований безопасности к концентрациям вредных газов в горных выработках [17] прежде всего выемочных и подготовительных участков, где происходит наиболее интенсивное выделение газов и пыли (в т.ч. взрывчатой). Управление газовыделением обеспечивается различными методами: аэродинамическими (вентиляция), газодинамическими (дегазация) и комбинированными, а также способами их реализации (см. рисунок).
Аэродинамические методы разбавляют опасные газы или перераспределяют их потоки в системе горных выработок участка за счет многоштрековой подготовки для обособленного разбавления составляющих газового баланса участка и изменения направления потока утечек через выработанное пространство [19]. Системы вентиляции шахт не снижают общую газообильность горных выработок, их функция – разбавление и/или перераспределение газовых потоков по выработкам. Аэродинамические методы реализуются посредством системы вентиляции шахты, основными элементами которой являются: шахтная вентиляционная сеть (ШВС), источники тяги, вентиляционные сооружения и регуляторы распределения воздуха. Таким образом, данная система не является чисто технической, поскольку ШВС включает в себя горные выработки и выработанные пространства, являющиеся в данном случае воздуховодами, состояние которых зависит от геомеханических реакций массива на ведение горных работ. Влияние напряженного состояния горного массива на аэродинамическое сопротивление вентиляционной сети не зависит от конструктивных характеристик выработок с той же определенностью, как в механических системах [24]. Поэтому систему вентиляции шахт относят к горнотехническим системам.
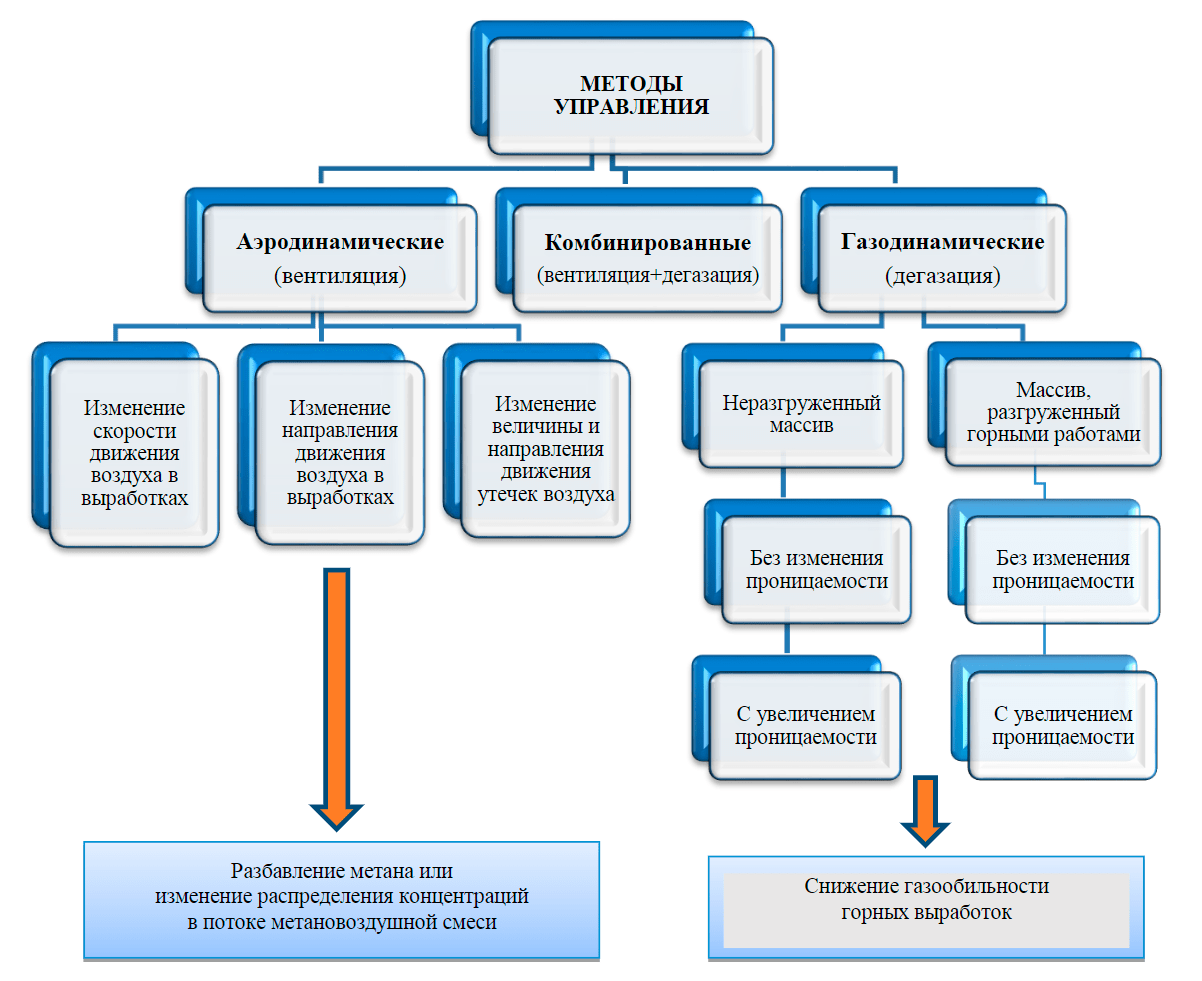
Классификация методов управления газовыделением и способов их реализации
Газодинамические методы снижают газообильность горных выработок шахты за счет целенаправленного и управляемого воздействия на горный массив инженерно-физическими и/или физико-химическими методами. При этом воздействие на массив может производиться как заблаговременно – до начала ведения горных работ (т.е. на неразгруженный массив), – так и в процессе эксплуатации (на горный массив, разгруженный горными работами) [6]. В последнем случае проницаемость массива и газоотдача подработанных угольных пластов существенно повышаются под влиянием выемки полезного ископаемого, дополнительное воздействие может не производиться. Однако в последние годы развиваются технологии повышения эффективности газодинамических методов, в т.ч. и на разгруженных пластах, из подземных выработок. Газодинамические методы реализуются дегазационными системами, обеспечивающими принудительное извлечение из массива и изолированный отвод метана, минуя атмосферу горных выработок; или блокирование метана в порах и микропорах углистого вещества, не допуская его выделения в выработки при проведении проходки или очистной выемки [30].
Дегазационная система (ДГС) включает в себя: скважины или горные выработки, систему дегазационных трубопроводов, вакуум-насосы, пускорегулирующую аппаратуру и устройства. Данная система также не может быть отнесена к чисто технической, поскольку наряду с техническими средствами и устройствами включает горнотехнические элементы (выработки и скважины, выработанные пространства). Сеть дегазационных трубопроводов также сопряжена с ШВС и так же, как ШВС, изменяется во времени и пространстве по мере подвигания очистных и проходческих забоев.
На газообильных шахтах высокая производительность добычи может быть обеспечена только комбинированными методами управления газовыделением, т.е. сочетанием методов вентиляции и дегазации [7]. Для повышения эффективности управления оценка рисков отказа системы управления метановыделением должна осуществляться в режиме непрерывного автоматизированного контроля режимов работы оборудования [27].
Эффективность комбинированной системы управления газовыделением при эксплуатации определяет уровень риска [14] по фактору метана. Показателями, характеризующими эффективность работы этой системы, являются непревышение допустимых по правилам безопасности концентраций метана в шахтной атмосфере, достигнутый коэффициент дегазации каждого источника, а также надежность и устойчивость функционирования каждого элемента данной системы [25]. Первые два показателя определяются в непрерывном режиме системами аэрогазового контроля. В отношении показателей надежности для системы управления газовыделением такой однозначности нет.
Термины и определения, используемые в теории надежности, регламентированы ГОСТ 27.002-2015 «Надежность в технике. Основные понятия. Термины и определения». Надежность –свойство объекта сохранять во времени способность выполнять требуемые функции в заданных режимах и условиях применения, технического обслуживания, ремонтов, хранения и транспортировки. Под объектом, при оценке его надежности, понимается совокупность элементов, связанных между собой структурно так, что выход из строя (отказ) одного из элементов системы может привести к отказу нескольких связанных с ним элементов или системы в целом.
Надежность является комплексным свойством объекта, включающим в себя ряд нижеперечисленных простых свойств: безотказность, ремонтопригодность, восстанавливаемость, долговечность, сохраняемость, готовность. Эти свойства оцениваются статистически на основе вероятностного подхода, кроме последнего. Готовность – способность сохранять состояние, в котором объект может выполнять требуемые функции в заданных режимах и условиях использования. Является производной свойств безотказности, ремонтопригодности и восстанавливаемости и определяется комплексными показателями надежности:
- коэффициентами готовности/неготовности (вероятность, что объект будет/не будет в работоспособном состоянии в данный момент времени);
- оперативной готовностью (вероятность работоспособности в данный момент и безотказной работы в течение заданного времени);
- коэффициентом технического использования (отношение суммарного времени пребывания в работоспособном состоянии к общему времени эксплуатации, включающему простои на ТО и ремонт за тот же период);
- коэффициентом сохранения эффективности (отношение показателя эффективности, указываемого в технической документации на объект, к номинальному значению этого показателя, вычисленного при условии, что отказы объекта в течение рассматриваемого периода эксплуатации не возникают).
Количественные и качественные требования к надежности серийно изготавливаемых технических объектов устанавливаются в нормативно-технической документации, для повторно создаваемых технических систем и объектов – в конструкторской и проектной документациях. Для определения показателей надежности технических систем используют различные методы (ГОСТ 27.002-2015 «Надежность в технике. Основные понятия. Термины и определения»):
- расчетные, предполагающие вычисления по справочным данным о надежности компонентов и комплектующих элементов объекта; по статистическим данным о надежности объектов-аналогов, используемых материалов и другой информации, известной из литературных данных или опыта эксплуатации;
- расчетно-экспериментальные, сочетающие расчетный метод и экспериментальное определение показателей надежности всех или некоторых составных частей объекта;
- экспериментальные, когда показатели надежности определяются на основе статистической обработки данных, полученных при испытаниях или эксплуатации объекта в целом.
Последняя группа методов относится к сложным объектам и техническим системам с большим числом разнородных факторов. Именно в эту группу входят шахтные вентиляционные и дегазационные системы. Отличительной характеристикой этих систем является то, что они постоянно трансформируются во времени и пространстве по мере подвигания фронта горных работ. Сложность их оценки методами теории надежности заключается в значительной изменчивости условий эксплуатации, что не позволяет распространить статистически полученные количественные оценки свойств, определяющих надежность как вероятность безотказной работы, полученные в разные периоды, даже на один и тот же объект. В то же время показатели надежности для технических элементов – машины, устройства, пускорегулирующего оборудования – могут быть определены описанными методами, поскольку данные элементы подвержены прогнозируемому износу, который может оцениваться как расчетным методом (по справочной информации), так и экспериментально. Такие расчеты осуществляются при разработке энергомеханической части проекта шахты или на стадии планирования развития горных работ, если при этом предполагается модернизация оборудования.
Для оценки надежности шахтных вентиляционно-дегазационных систем приходится использовать различные комбинированные методы, включающие дополнительные характеристики применительно к горной составляющей.
Обсуждение
Комплексный индикатор надежности системы вентиляции-дегазации можно представить как безразмерный показатель, соответствующий ее стабильной и безотказной работе с параметрами подачи воздуха и откачиваемой метановоздушной смеси, заданными в проекте и корректируемыми по мере подвигания забоя. Он будет представлять собой сумму индикаторов, отражающих особенности эксплуатации и технического обслуживания ШВС и ДГС, взятыми со своими весовыми коэффициентами:
где НШВС, НДГС – индикаторы надежности систем вентиляции и дегазации соответственно; KШВС,KДГС – коэффициенты, показывающие весовое значение выполнения полного комплекса работ в текущий момент по качеству работы систем вентиляции и дегазации соответственно, д.ед.
Индикаторы надежности НШВС и НДГС принимаются равными единице на момент начала эксплуатации угольной шахты. Это максимально возможное значение, которое соответствует надежности оборудования, определенной проектом. Значения этих индикаторов, если все выполнено в соответствии с проектом, остаются постоянными весь период работы угольной шахты. В случае отклонения от проектных решений их изменение должно соответствовать степени увеличения производственных рисков. Исходя из технического состояния ШВС и ДГС, значения коэффициентов КШВС и КДГС могут изменяться от 0 до 1 в соответствии с реальным положением дел, в зависимости от полноты выполнения обязательных работ по обслуживанию оборудования. Шкала оценки и ее детализация устанавливается предприятием.
Жизнеобеспечение любой угольной шахты напрямую зависит от правильного проектирования, монтажа, эксплуатации и технического обслуживания системы вентиляции, важнейшими элементами которой являются вентиляторы главного проветривания (ВГП) [12, 21, 26].
Надежность любой машины определяется не только ее конструктивными особенностями, но и ее техническим состоянием как объекта в целом, так и отдельных элементов (узлов). Длительная и бесперебойная работа ВГП зависит от правильного выбора типа и марки вентилятора, а также его правильного монтажа, эксплуатации и своевременного технического обслуживания [23]. При создании новых машин, а также при их выборе во время проектирования шахт, показатели надежности их работы определяются расчетными методами. Однако в процессе эксплуатации производить такие трудоемкие расчеты нецелесообразно. Гораздо удобнее и оперативнее можно определять риски отказов машин через индикаторные показатели.
Комплексный индикатор надежности вентилятора главного проветривания можно представить как безразмерный показатель, соответствующий его стабильной и безотказной работе с параметрами подачи воздуха, заданными в проекте и корректируемыми по мере изменения производственной мощности шахты. Он будет представлять собой сумму индикаторов, отражающих особенности эксплуатации и технического обслуживания ВГП, взятыми со своими весовыми коэффициентами:
где Нпм, Нм, Нмво, Но, Нто – индикаторы надежности подготовки к монтажу и монтажа ВГП, монтажа и наладки вспомогательного оборудования, обкатки ВГП, технического обслуживания и ремонта соответственно; Kпм,Kм, Kмво,Kо,Kто– коэффициенты, показывающие весовое значение выполнения полного комплекса работ в текущий момент по подготовке к монтажу ВГП, по монтажу ВГП, монтажу и наладке вспомогательного оборудования, обкатке ВГП, своевременному и полному техническому обслуживанию или ремонту соответственно, д.ед.
Индикаторы надежности Нпм, Нм, Нмво, Но, Нто нужно принимать равными единице на начало эксплуатации ВГП (это наилучшие показатели в соответствии с проектом). Значения этих индикаторов, если все выполнено в соответствии с технологией, остаются постоянными весь период работы ВГП. Значения коэффициентов Kпм,Kм,Kмво,Kо,Kтов зависимости от технического состояния ВГП могут изменяться от 0 до 1, отображая текущее качество обслуживания, – какая доля от запланированных работ выполнена полностью. В данном случае максимальное значение НВГП составит 5. Если какой-то вид работ выполнен не полностью или с нарушениями, то значение этого индикатора уменьшается. Допустимое снижение устанавливается предприятием в соответствии с техническими требованиями к каждому виду оборудования.
Индикатор надежности технического обслуживания и ремонта включает целый ряд показателей, значения которых необходимо постоянно подвергать мониторингу, так как они показывают текущее техническое состояние ВГП. В зависимости от графика проводимого технического обслуживания или ремонта должны контролироваться результаты и сроки выполнения следующих видов работ: ежемесячное, ежесуточное и двухнедельное техническое обслуживание; ежемесячное ремонтное обслуживание; ежеквартальный и полугодовой текущий ремонт; годовая и двухгодичная ревизия и наладка систем автоматизации.
При оценке риска на основе индикаторов показателей надежности отклонение комплексного индикатора от максимально возможного (принимаемого равным единице) на основе приведенной структуры комплексного индикатора легко определить, по какому компоненту необходимы мероприятия, и оперативно принять необходимые управляющие воздействия.
Для обеспечения высокой эффективности и надежности работы ВГП должны качественно, в соответствии с требованиями безопасности и правил технической эксплуатации [1], выполняться следующие виды работ: подготовка к монтажу; монтаж вентилятора; проверка комплектности, сохранности и расконсервация оборудования; установка рам на фундаменте; подливка рам бетонным раствором; монтаж и установка валов ротора; монтаж валов роторов, устанавливаемых на общей раме или на фундамент без рамы; ревизия подшипниковых узлов валов роторов [4]; центрирование валов; монтаж и наладка систем смазки подшипников ротора вентиляторов; монтаж и наладка направляющих аппаратов центробежных вентиляторов; монтаж и регулировка направляющего и спрямляющего аппаратов осевых вентиляторов.
Техническое обслуживание и ремонт вентиляторных установокосуществляется по непрерывному методу, т.е. элементы оборудования осматриваются и ремонтируются не одновременно, а поочередно в установленном порядке. Структура цикла технического обслуживания вентиляторных установок имеет вид: (ТО1) – (ТО2) – (ТО4), где ТО1, ТО2, ТО4 – ежемесячное, ежесуточное и двухнедельное техническое обслуживание соответственно. Структура ремонтного цикла выглядит следующим образом: К – РО1 – Т1 – Т2 – РО1 – Т1 – (Т2 – НРГ) – РО1 – Т1 – Т2 – РО1 – Т1 – НРД – – РО1 – Т1 – Т2 – РО1 – Т1 – (Т2 – НРГ) – РО1 – Т1 – Т2 – РО1 – Т1 – НРД – РО1 – Т1 – Т2 – РО1 – Т1 – (Т2 – НРГ) – РО1 – Т1 – Т2 – РО1 – Т 1 +… – К, где РО1 – ежемесячное ремонтное обслуживание; Т1 и Т2 – ежеквартальный и полугодовой текущий ремонт соответственно; НРГ и НРД – годовая и двухгодичная ревизия и наладка систем автоматизации соответственно; К – капитальный ремонт.
Чтобы своевременно обнаружить и устранить неисправности обслуживающим и ремонтным персоналом производится техническое обслуживание работающей и резервной вентиляторных установок [22]. Текущий ремонт, осуществляемый в процессе эксплуатации, заключается в замене и восстановлении отдельных частей вентиляторной установки и их регулировке, что гарантирует ее работоспособность. Ремонтное обслуживание и текущий ремонт выполняются для установки, принудительно выведенной в резерв.
Таким образом, надежность работы ВГП в процессе эксплуатации определяется качеством технического обслуживания по каждому виду операций (индикатор надежности должен включать показатели, характеризующие правильность монтажа и установки ВГП), а также проведения своевременного планового технического обслуживания, ревизии, наладки и текущих ремонтов. Качество технического обслуживания и ремонтов при эксплуатации зависит от квалификации и дисциплины операционного персонала и инженерного надзора. Таким образом, индикаторы будут отражать и организационные риски.
Аналогично можно определить индикаторы надежности для вентиляторных установок местного проветривания, регуляторов распределения воздуха, состояния вентиляционной сети.
Надежность системы дегазации [16] также значительно влияет на уровень аэрологического риска работы угольной шахты и обеспечивает стабильность работы потребителей шахтного метана [3]. Надежность и эффективность работы дегазационных систем угольных шахт зависит от правильного выбора способа и схемы дегазации, качественного проектирования, монтажа, эксплуатации и технического обслуживания оборудования [10, 15, 18].
Надежность горнотехнической составляющей (способ и схема дегазации, параметры скважин и режимы работы вакуум-насосов) может определяться эффективностью извлечения метана – достижением требуемого коэффициента дегазации. Это один из основных индикаторов надежности системы.
Для технических средств стандартные показатели надежности (ГОСТ 27.002-2015 «Надежность в технике. Основные понятия. Термины и определения») на стадии проектирования могут быть определены расчетными методами теории надежности. На стадии эксплуатации выполнение трудоемких расчетов с неопределенными параметрами входящих в них констант для оперативного управления надежностью функционирования системы – нецелесообразны. Более удобным является применение индикаторов аэрологического риска.
Индикатор надежности ДГС представляет собой безразмерный показатель, соответствующий стабильной и безотказной работе системы с подачей на поверхность шахты метановоздушной смеси с параметрами, заданными в проекте и/или корректируемыми по мере изменения производственной мощности шахты. Длительная и бесперебойная работа дегазационной установки зависит от правильного выбора оборудования, а также его правильного монтажа, эксплуатации и своевременного технического обслуживания.
Индикатор надежности можно представить как сумму индикаторов, отражающих особенности эксплуатации и технического обслуживания ДГС:
где Ндс, Нвнс, Нтр, Нто – индикаторы надежности герметизации дегазационных скважин и эксплуатации вакуум-насосных станций, герметизации подземных дегазационных трубопроводов, технического обслуживания и ремонта оборудования ДГС соответственно; Kдс,Kвнс,Kтр,Kто– коэффициенты, показывающие весовое значение выполнения полного комплекса работ в текущий момент по герметизации дегазационных скважин, эксплуатации вакуум-насосных станций, герметизации подземных вакуумных дегазационных газопроводов, своевременному и полному техническому обслуживанию или ремонту оборудования ДГС соответственно, д.ед.
Индикаторы надежности Ндс, Нвнс, Нтр, Нто принимаем равными 1 на момент начала эксплуатации ДГС. Значения этих индикаторов, если все выполнено в соответствии с проектом, остаются постоянными весь период работы ДГС. Значения коэффициентов Kдс,Kвнс,Kтр,Kтов зависимости от технического состояния ДГС могут изменяться от 0 до 1.
Дегазационная система угольной шахты – сложная многокомпонентная техническая система, надежность которой зависит от многих факторов, поэтому стандартные показатели надежности необходимо определять расчетно-экспериментальными или только экспериментальными методами. Для оперативного управления аэрологическими рисками, связанными с ДГС, целесообразно использовать индикаторы надежности, которые включают показатели, характеризующие качество сооружения скважин, правильность монтажа и эксплуатации ДГС, а также своевременного проведения планового технического обслуживания, ревизии, наладки и текущих ремонтов.
Постоянный мониторинг индикатора надежности ДГС, включающий целый ряд индикаторов элементов ДГС, позволит своевременно обнаружить отклонения в их работе, а также в сроках и качестве выполнения графика технического обслуживания и ремонта оборудования, включающего следующие виды работ: ежесуточное и двухнедельное техническое обслуживание; ежемесячное техническое и ремонтное обслуживание; ежеквартальный и полугодовой текущий ремонт; годовая и двухгодичная ревизия и наладка оборудования.
На многих горных предприятиях существует автоматизированный мониторинг параметров безопасности, характеризующих состояние шахтной атмосферы. В ближайшей перспективе такая система должна стать обязательной для всех компаний, как информационная база для многофункциональных систем безопасности. Данные, по которым вычисляются индикаторы надежности оборудования, должны сохраняться в общей информационной базе. Алгоритмы для их определения должны входить в единую систему интеллектуальной обработки данных для поддержки принимаемых технических решений. Это позволит автоматизировать оперативный контроль обслуживания оборудования вентиляционно-дегазационных систем и повысить его качество, а также выявлять неблагоприятные тенденции снижения эффективности систем, связанные с использованием изношенного оборудования. Сохранение оперативной информации позволит точнее определять причины аварий, в том числе катастрофических (взрывов, пожаров) и выявлять виновных в непринятии мер по снижению рисков при поставарийных расследованиях.
Заключение
На основе результатов исследований предложена структура индикаторов, позволяющая на стадии эксплуатации шахты обеспечить:
- систематическую идентификацию неблагоприятных тенденций изменения надежности оборудования шахтных вентиляционно-дегазационных систем как потенциальной опасности;
- выявление факторов, обусловливающих риск аварий, и слабых звеньев в системе, связанных с работой оборудования;
- выбор мер по снижению риска отказов оборудования вентиляционно-дегазационных систем;
- формирование базы данных для рациональной организации профилактического обслуживания, ремонта и контроля оборудования систем, обеспечивающих аэрологическую безопасность;
- создание базы данных, облегчающих поставарийное расследование аварий и обеспечивающих адресную разработку мер по предупреждению аналогичных аварий.
Данный подход к анализу и управлению надежностью горно-шахтного оборудования может быть рекомендован для использования в текущем планировании производственных процессов шахты. Для его реализации требуется расширение спектра задач, решаемых многофункциональными системами безопасности, которые обеспечат не только формирование баз данных об изменении параметров состояния техники, вентиляционного и дегазационного оборудования, но и их аналитическую обработку, включающую определение динамики отклонений контролируемых параметров от проектных значений и представление информации в удобном для принятия решений виде.
Литература
- Алыменко Н.И. Вентиляторные установки для различных горно-технических условий / Н.И.Алыменко, Д.Н.Алыменко // Горное эхо. 2008. № 3-4. С. 34-41.
- Артемьев В.Б. Безопасность производства (организационный аспект) / В.Б.Артемьев, В.А.Галкин, И.Л.Кравчук. М.: Горная книга, 2016. 144 с.
- Безпфлюг В.А. Опыт утилизации шахтного метана в ФРГ и возможности его утилизации в России // Уголь. 2006. № 8. С. 66-68.
- Герике Б.Л. Распознавание дефектов подшипников качения в редукторах горных машин / Б.Л.Герике, А.А.Мокрушев // Наукоемкие технологии разработки и использования минеральных ресурсов. 2017. № 3. С. 192-197.
- Герике П.Б. Формирование единого диагностического критерия для оценки технического состояния горного оборудования / П.Б.Герике, Б.Л.Герике // Горное оборудование и электромеханика. 2021. № 2 (154). С. 17-22. DOI: 10.26730/1816-4528-2021-2-17-22
- Гидрорасчленение угольных пластов для их эффективной дегазационной подготовки через подземные скважины / С.В.Сластунов, А.В.Понизов, А.П.Садов, А.М.-В.Хаутиев // Горный информационно-аналитический бюллетень. 2020. № 6-1. С. 15-25. DOI: 10.25018/0236-1493-2020-61-0-15-25
- Гражданкин А.И. Анализ опасностей и оценка риска аварий в обосновании промышленной безопасности // Безопасность труда в промышленности. 2013. № 6. С. 90-92.
- Гражданкин А.И. Заменит ли количественная оценка риска выполнение требований промышленной безопасности? / А.И.Гражданкин, А.С.Печеркин, В.И.Сидоров // Безопасность труда в промышленности. 2012. № 10. С. 43-45.
- Гражданкин А.И. Модернизация требований промышленной безопасности. Риск-ориентированный подход / А.И.Гражданкин, М.В.Лисанов // Безопасность труда в промышленности. 2013. № 1. С. 77-79.
- Ермаков А.Ю. Системный подход к обеспечению вентиляции и безопасности угольных шахт по аэрогазодинамическому фактору / А.Ю.Ермаков, Н.М.Качурин, Вал.В.Сенкус // Горный информационно-аналитический бюллетень. 2018. № 7. С. 212-218. DOI: 10.25018/0236-1493-2018-7-0-212-218
- Забурдяев В.С. Технологические схемы подготовки, отработки и управления газовыделением, снижающие риски взрывов метанопылевоздушных смесей в угольных шахтах // Горный информационно-аналитический бюллетень. 2015. № S1. С. 373-381.
- Каледина Н.О. Аэрологическая безопасность угольных шахт / Н.О.Каледина, Д.А.Мещеряков // Горный информационно-аналитический бюллетень. 2011. № 1. С. 227-237.
- Каледина Н.О. Резервы повышения эффективности подземной дегазации угольных пластов с целью улучшения условий труда шахтеров / Н.О.Каледина, В.А.Малашкина // Горный журнал. 2017. № 6. С. 86-89. DOI: 10.17580/gzh.2017.06.17
- Каледина Н.О. Риск-ориентированный подход в обеспечении промышленной безопасности горных предприятий // Горный информационно-аналитический бюллетень. 2020. № 6-1. С. 5-14. DOI: 10.25018/0236-1493-2020-61-0-5-14
- Курта И.В. Управление газовыделением на выемочных участках угольных шахт – ключевой фактор создания безопасных условий труда // Записки Горного института. 2012. Т. 195. С. 108-110.
- Малашкина В.А. Исследование возможностей повышения эффективности подземной дегазации угольных шахт // Горный информационно-аналитический бюллетень. 2019. № 9. С. 131-137. DOI: 10.25018/0236-1493-2019-09-0-131-137
- Малашкина В.А. Мониторинг эффективности системы дегазации угольной шахты – основа безопасного труда горнорабочих // Горный информационно-аналитический бюллетень. 2020. № 6-1. С. 38-45. DOI: 10.25018/0236-1493-2020-61-0-38-45
- Малашкина В.А. Направления повышения эффективности использования систем дегазации угольных шахт // Горный информационно-аналитический бюллетень. 2019. № 6. С. 206-214. DOI: 10.25018/0236-1493-2019-06-0-206-214
- Матвеев В.В. Разработка, исследование и внедрение систем контроля и автоматизации комплексов отвода метана на угольных шахтах // Известия высших учебных заведений. Горный журнал. 2010. № 2. С. 71-77.
- Механизм предотвращения реализации опасной производственной ситуации / В.Б.Артемьев, В.А.Галкин, А.М.Макаров и др. // Уголь. 2016. № 5. С. 73-77. DOI: 10.18796/0041-5790-2016-5-73-77
- Патрушев М.А. Совершенствование проветривания угольных шахт: из опыта разработки и внедрения эффективных схем проветривания / М.А.Патрушев, Е.Я.Самойленко, В.Н.Ус. Донецк: Донбас, 1976. 126 с.
- Сигошин А.В.Анализ основных неисправностей шахтных вентиляторов главного проветривания с истекшим нормативным сроком эксплуатации // Известия Уральского государственного горного университета. 2003. Вып. 16. С. 18-22.
- Сигошин А.В. Проблемы оценки технического состояния вентиляторов главного проветривания // Известия Уральского государственного горного университета. 2003. Вып. 17. С. 343-346.
- 24.Ушаков В.К. Анализ затрат на создание и эксплуатацию шахтных вентиляционных систем с целью повышения безопасности труда // Горный информационно-аналитический бюллетень. 2018. № 6. С. 214-221. DOI: 25018/0236-1493-2018-6-0-214-221
- Ушаков В.К. Динамическая иерархическая сегментация шахтных вентиляционных систем при моделировании способов повышения аэрологической безопасности труда // Горный информационно-аналитический бюллетень. 2019. № 12. С. 76-85. DOI: 10.25018/0236-1493-2019-12-0-76-85
- Чмыхалова С.В. Системный подход к оценке риска, способствующий предотвращению потерь и повышению безопасности горного производства // Горный информационно-аналитический бюллетень. 2020. № 6-1. С. 146-153. DOI: 10.25018/0236-1493-2020-61-0-146-153
- Шершукова К.П. Оценка риска опасных производственных объектов для проектирования автоматических систем безопасности / К.П.Шершукова, А.С.Телюк // Горный информационно-аналитический бюллетень. 2012. № S6. С. 82-89.
- Gi Heung Choi. Effectiveness of direct safety regulations on manufacturers and users of industrial machines: its implications on industrial safety policies in Republic of Korea // Safety and Health at Work. 2017. Vol. 8. Iss. 1. Р. 59-66. DOI: 10.1016/j.shaw.2016.09.005
- Nikulin A. Assessment of occupational health and safety effectiveness at a mining company / А.Nikulin, А.Y.Nikulina // Ecology, Environment and Conservation. 2017. Vol. 23. № 1. Р. 351-355.
- Quantification of methane emission rates from coal mine ventilation shafts using airborne remote sensing data / Т.Krings, К.Gerilowski, М.Buchwitz et al. // Atmospheric Measurement Techniques. 2013. Vol. 6. Iss. 1. P. 151-166. DOI: 10.5194/amt-6-151-2013
- Reliability calculation of mine ventilation network / Luo Wengui, Xie Xianping, Xiao Houzao et al. // Procedia Engineering. 2014. Vol. 84. P. 752-757. DOI: 10.1016/j.proeng.2014.10.492
- Safety management efficiency of China's coal enterprises and its influencing factors – Based on the DEA-Tobit two-stage model / Cheng-lin Miao, Meng-meng Duan, Xin-xiu Sun, Xin-yu Wu // Process Safety Environmental Protection. 2020. Vol. 140. Р. 79-85. DOI: 10.1016/j.psep.2020.04.020