Mutual spectral densities calculation of the moments of resistance on the peat milling unit working bodies
- Ph.D., Dr.Sci. associate professor Tver State Technical University ▪ Orcid
Abstract
When performing technological operations in the peat industry, various units with milling-type working bodies are used. They differ in design, layout, number and type of cutting elements, operating modes, and may have one or more working bodies. During operation, random forces and moments act on the cutters, which have a dramatically variable nature, which is associated with the periodic interaction of the knives with the peat deposit, its structural heterogeneity, variations in the milling depth, physical and mechanical properties of peat, the rotational speed of the cutter and the movement speed of the machine. In this case, significant dynamic loads arise in the structural elements, which leads to a decrease in their reliability, deterioration of the energy characteristics of the engine operation and technical and economic indicators of use. In the dynamic analysis of drive elements, when using machines with several working bodies, it is necessary to know both spectral and mutual spectral load densities. For their calculation, expressions were obtained that take into account the physical and mechanical properties of peat, the operating modes of the unit and their probabilistic characteristics, as well as the design features of the working body. The expressions are obtained for the case when there are several working bodies with the same diameters and the number of knives in the cutting plane. In this case, the number of planes, width, type of cutting element and type of cutting (locked, semi-locked, etc.) may differ. As an example of using the developed approaches, the calculation of spectral and mutual spectral densities of moments on cutters and loads in the drive elements of the machine for surface-layer milling MTF-14 is presented.
Introduction
When performing technological operations at various stages of the extraction of peat products, milling units are widely used [7, 28]. During their operation, significant dynamic loads arise in the structural elements, which leads to a decrease in reliability [2, 3], deterioration of the energy characteristics of the operation of machines and their technical and economic indicators.
The main reason for the occurrence of loads is the forces of external resistance on the working bodies, which are dramatically variable and random in nature [13, 17]. This is due to the periodic interaction of cutting elements with the deposit, its structural heterogeneity [8, 27], random variability of operating modes [15] and physical and mechanical properties of peat [9]. Also, the nature of the loading depends on the design and number of cutters, their parameters and operating modes, wear of cutters, vibrations associated with cutting forces and imbalance of working bodies, etc. [1].
Taking into account the random nature of the loads on the cutting elements, the analysis of dynamic loads in the structural elements of the milling unit and the calculation of indicators of its reliability [4, 5] should be based on the methods of probability theory [23] и статистической динамики механических систем [24, 25]. Experience of their application [12, 21, 22, 30] shows that in practice it is possible to confine to considering only one-dimensional and two-dimensional characteristics of processes when solving these problems using both analytical and numerical methods,as well as 3D-modelling [26, 32]. In this case, the probabilistic characteristics of force factors, such as variances and spectral densities, are taken into account. In [17, 18] models of moments on the working bodies of milling units are systematized, and methods for calculating their probabilistic characteristics are considered.
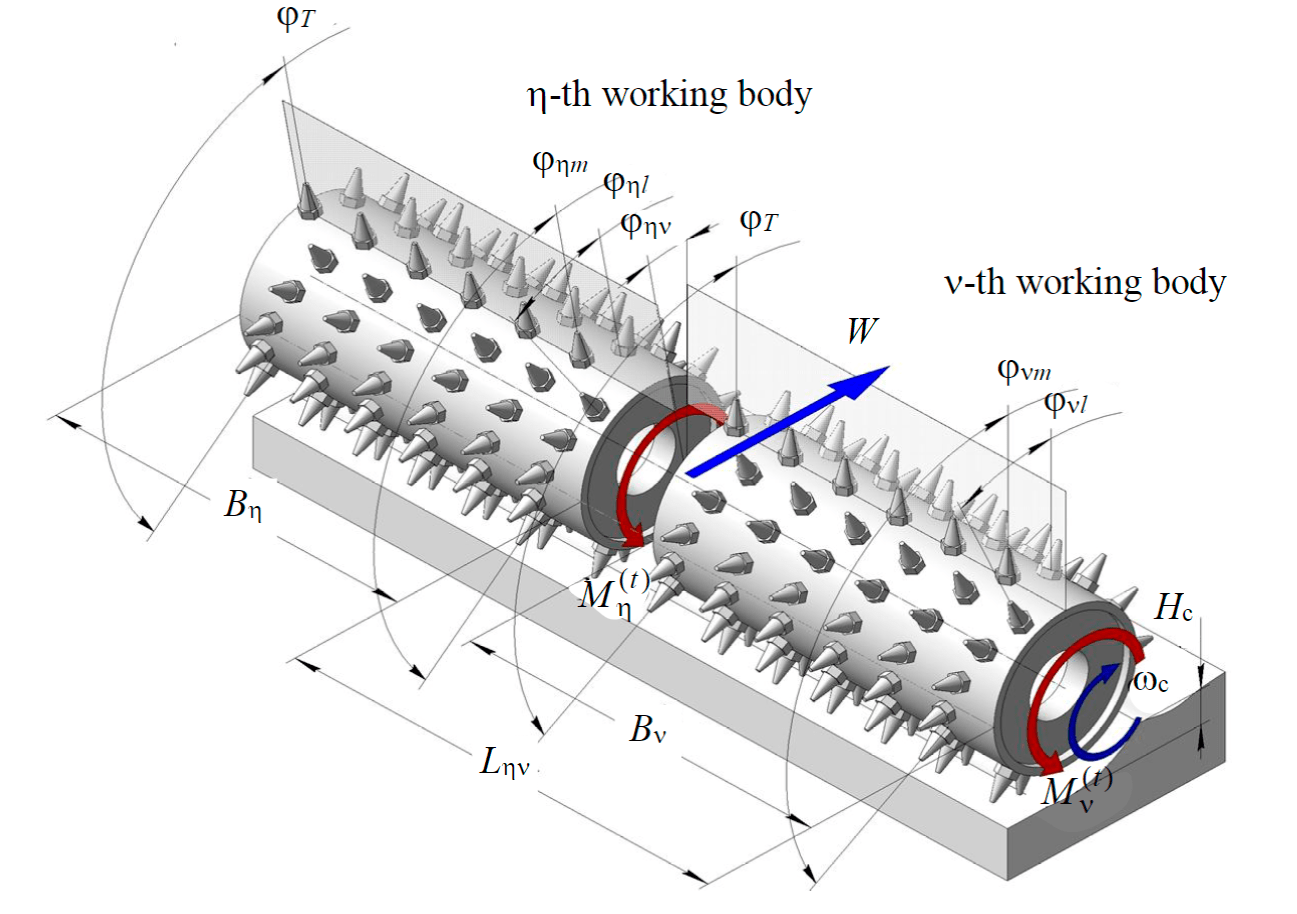
Fig.1. Scheme of the milling unit working bodies interaction with peat deposits
If the unit contains several cutters, during dynamic analysis it is also necessary to know the mutual spectral densities of external loads. When determining them, methods of statistical (simulation) modeling have found wide application. They are universal, but require a lot of machine time when calculating the probabilistic characteristics of loads, especially when choosing the optimal operating modes and design parameters of the milling unit.
Experimental studies of loads in structural elements of milling units using strain gauge means [20] give estimates of the mathematical expectation, variance, correlation functions, spectral densities, distribution densities of moments and forces, as well as characteristics of their mutual statistical relationship.
This approach is time consuming and expensive. In this case, the information obtained characterizes the loading of the machine only under the given specific test conditions.
In [14] an analytical method has been developed for calculating the mutual spectral densities of moments on the working bodies. Peat machines were considered with several cutters having the same type of cutting elements and width, which work under the same conditions. At the same time, many design cases that are often encountered in design were not taken into account.
Improving the reliability, economic and operational performance of peat milling units is an urgent task [10, 16]. Its solution is associated with the ability to predict the nature and magnitude of existing loads in structural elements [11] on the basis of taking into account the specifics of the formation of moments on the working bodies and their probabilistic characteristics at the design stage.
The purpose of the article is to develop expressions for calculating mutual spectral densities based on models of the formation of moments of resistance on cutters of peat machines, taking into account their design, operating modes and probabilistic characteristics of operating conditions
Methodology
A milling unit with several working bodies (Fig.1) is considered, each of which has the same radii of the cutting elements location, the average depth of milling, the number of knives in the cutting plane, placed evenly. Unlike the models considered in [14], the number of cutting planes, the width of the cutters, the distance between them, their type and working conditions, determined by the type of interaction with the peat deposit (blocked, semi-blocked), may differ. The cutters also have different cutting patterns.
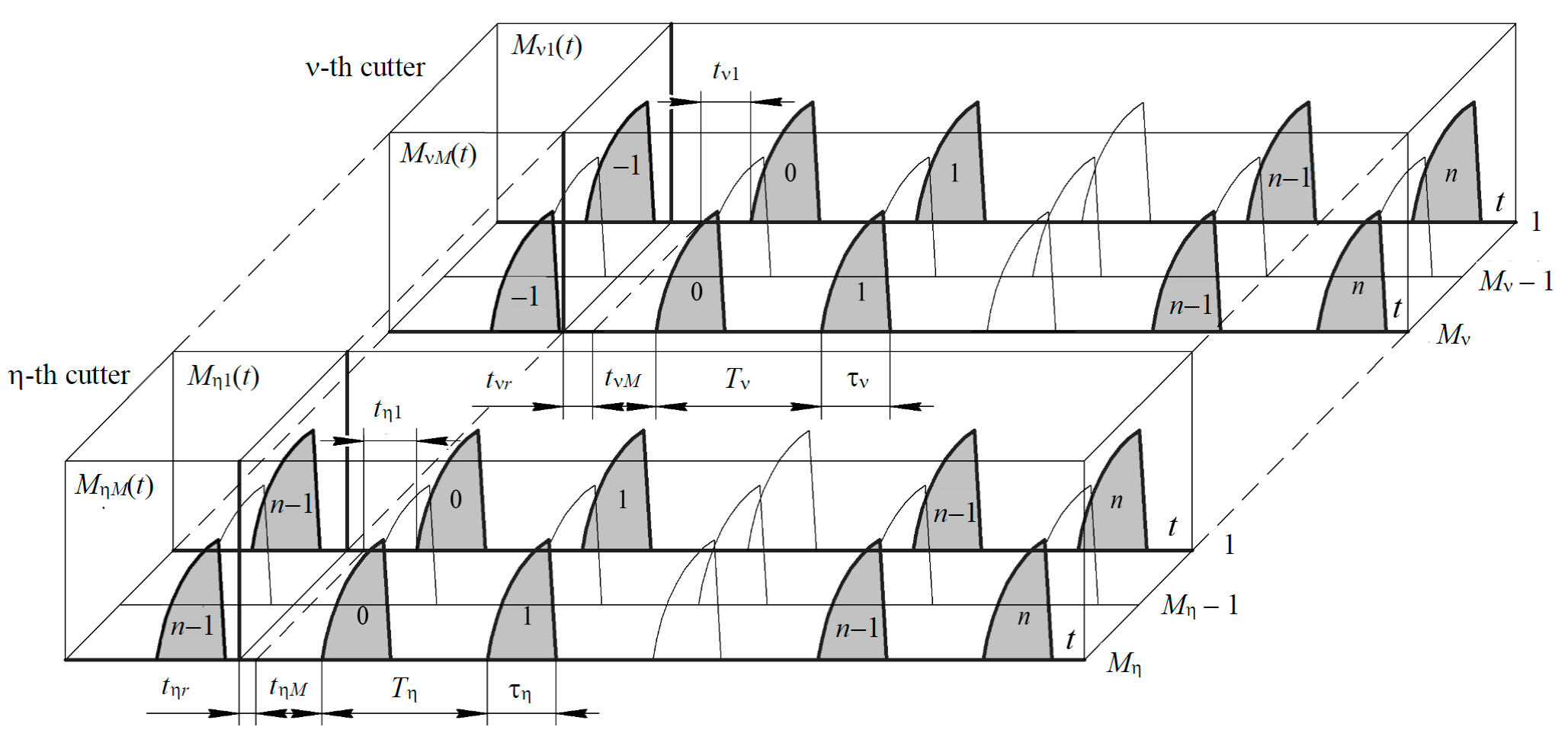
Fig.2. Moments of resistance on cutters formation model
Taking into account the existing designs of cutters and their operating modes, it can be assumed that the speed of the unit, the number of working body revolutions, the depth of milling and the physical and mechanical properties of peat change smoothly (within several feeds per knife) [17]. Models of moments of resistance can be represented in the form of impulse processes with random parameters (Fig.2):
where Mv,Mη – number of cutting planes per n-th and η-th cutters; kvm, kηm – coefficients that take into account the peculiarity of interaction (blocked, semi-blocked, etc.), the type and width of the knife in the m-th plane for the n-th and η-th working bodies; Mmn(t) – loading moment without taking into account the coefficient depending on the type of interaction of the m-th plane in the n-th act of interaction; tvmn, tηmn – time between the origin and the occurrence of the n-th pulse on the m-th plane for the n-th and η-th working bodies; Pvmn, Pηmn – parameters of pulses on the m-th cutting plane for n-th and η-th cutters; tvr, tηr – time shift between knives on n-th, η-th cutters; K – number of cutters.
The mutual spectral densities of random stationary processes are complex functions. They are related to mutual energy spectrum [23]:
where δ(ω) – delta function; Fvη(ω), Fηv(ω) – mutual energy processes spectrum, which can be determined (taking into account that the moments of resistance are pulse sequences with random parameters) as [23]:
T – mathematical expectation of the pulse repetition period; 2N + 1 – number of pulses; m1
For the spectrum of moments (1) containing (2N + 1) pulses on n-th and h-th working bodies, we get:
where S0v(jω;ωс;Pvmn), S0η(jω;ωс;Pηmn) – moment spectrum Mnm(t); φvm, φηm – angles between the initial points for n-th, η-th cutters (each cutter can have its own reference system) and cutters in the m-th plane for the corresponding working bodies; φT – the angle between the knives in the cutting plane (uniform placement of the cutters in the plane); ωс – cutter angular velocity; φvr, φηr – angles between incisors on n-th and η-th working bodies relative to the initial point, respectively, the angle between the knives on n-th and η-th cutters is φηvr = φηr - φvr (see Fig.1);
φvk, φηk – contact angles of knives of n-th and η-th working body with a deposit.
Contact angles φvk and φηk are random and depend on the design of the working body, its angular velocity, the profile of the card surface, the depth of milling and vibrations caused by the cutting forces and imbalance of the cutter.
Taking into account that the mutual spectral densities Svη(ω) и Sηv(ω) are complex conjugate quantities, it is enough to consider only one of them.
Using the approaches presented in [14, 17], substituting (4), (5) into (2), (3) and taking into account the stationarity of the unit (the probabilistic characteristics of the pulse parameters do not depend on the choice of the origin) operating conditions, for the mutual spectral moment densities on n-th and η-th cutters with a constant value of the cutters angular speed, we get:
where Kqsvηml, Kqsvηmlp – mutual correlation moments of pulse parameters for m-th and l-th cutting planes; mq, Dq – mathematical expectations and variances of parameters; p – the difference between the numbers of two pulses (in the direction of movement of the unit), p=n-i.
In the case of stationarity of parameters and smoothness of their change Kqsvηml and Kqsvηmlp are determined by the correlation functions of the working conditions (strength properties of the material, its density and milling depth) at the moments of the knife interaction with the peat deposit:
where m, l – corresponding cutting plane numbers; KPy – correlation functions of random parameters in the direction perpendicular to the movement of the unit; KPxy – correlation functions of random parameters, taking into account the spatial variability of parameters (both in the direction of movement and perpendicular to it); x, y – point coordinates for corresponding parameters; с – cutting element feed; Lηv – distance between η-th and ν-th cutters (Fig.1); hvm – distance from the end of the ν-th working body to the m-th cutting plane; hηl – distance from end of h-th cutter to l-th plane.
With a uniform arrangement of cutting elements along the length of the working bodies, we get:
where h – distance between knives in adjacent cutting planes.
In (6), the values are intoduced:
where * – complex conjugate spectrum value.
Averaging (6) over angular velocity of working body from
where W(ωс) – distribution density , and considering that
for the joint (mutual) energy spectrum of the moments on the cutters, we obtain:
T – the average pulse repetition period in the cutting plane,
With km= 1 formula (7) has the form obtained in the work[14].
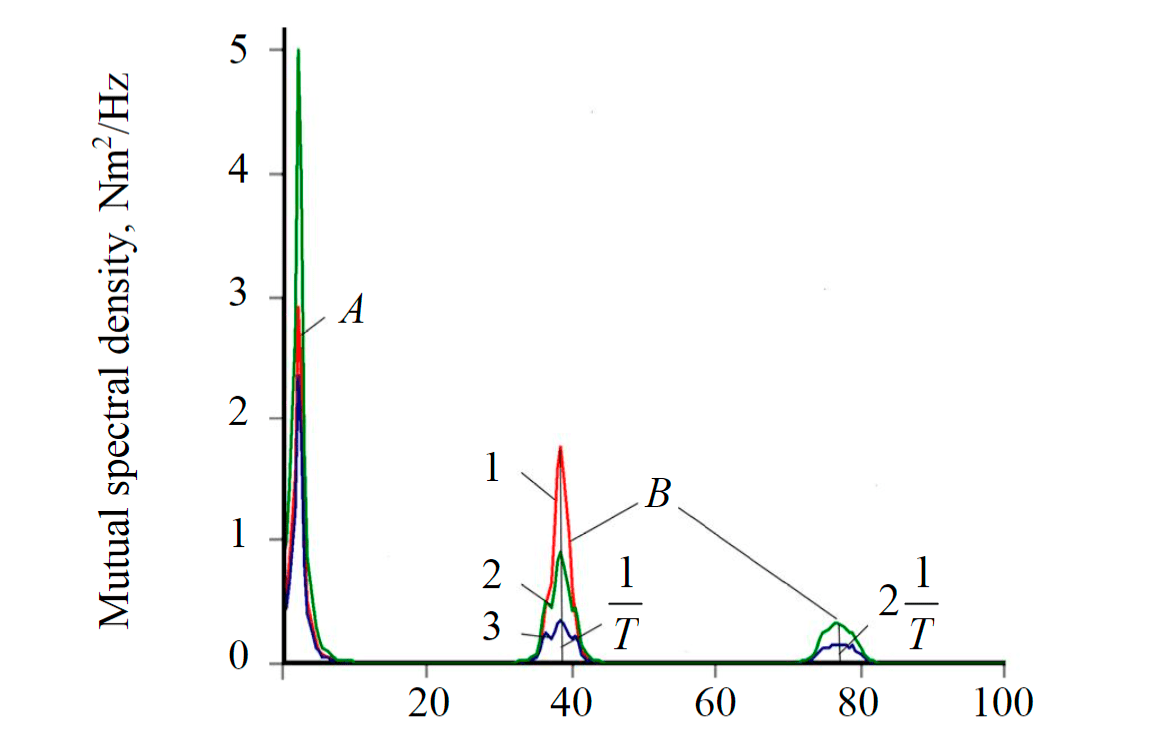
Fig.3. Real parts of the mutual spectral moment densities on the working bodies (calculation) 1 – for adjacent center cutters; 2 – for adjacent middle cutters; 3 – for adjacent center and middle cutters
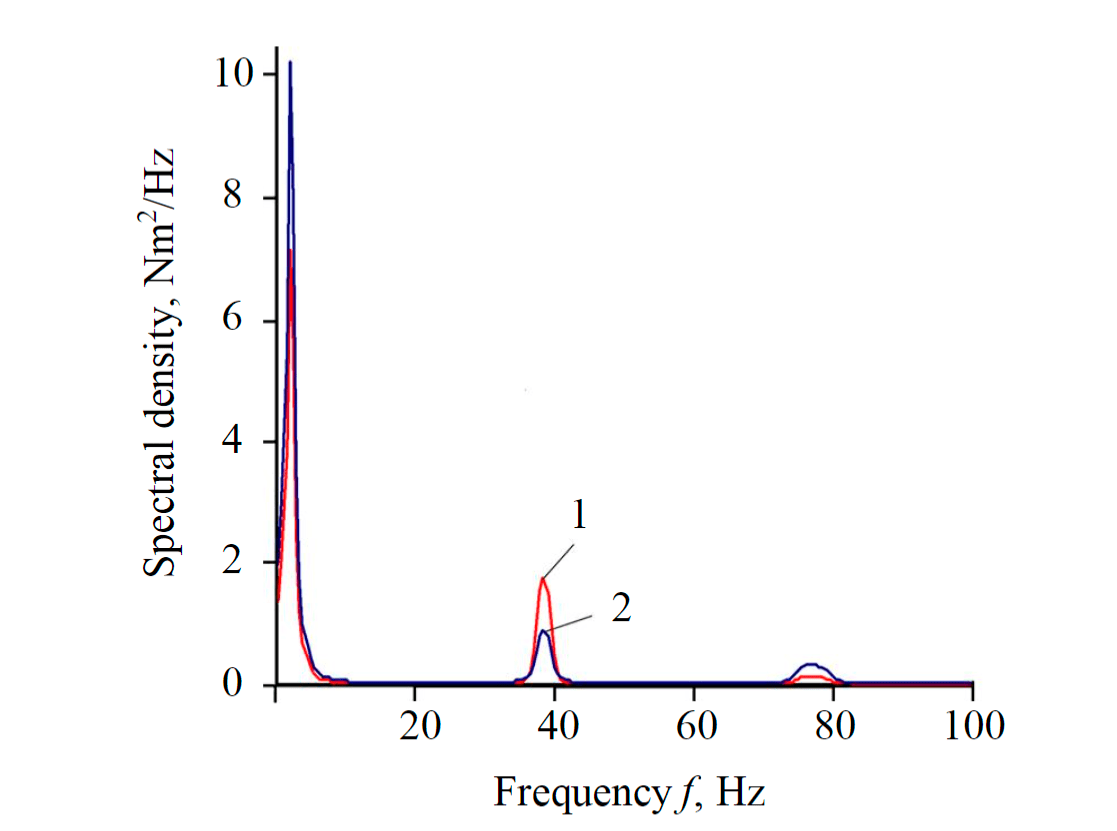
Fig.4. Spectral densities of moments on MTF-14 cutters when interacting with peat (calculation) 1 – central cutter; 2 – end cutter
Dependencies for determining the probabilistic characteristics of loads make it possible to single out a number of their features. Mutual spectral densities have a complex structure and two characteristic frequency zones.
he first part (A in Fig.3) is proportional to the correlation functions of the loading pulses parameters both in the direction of unit movement and perpendicular to it. The type depends on the spectrum of the moments of resistance on the cutters of various working bodies S0v(jω;ωс;Pvm), S0η(jω;ωс;Pηl) and the scheme of their arrangement, the influence of which is determined by the function:
The frequencies of this part are concentrated in the low-frequency zone. This is due to a smooth change in the parameters of load pulses on the knife within several acts of interaction when cutting a peat deposit and a low speed of movement of the unit.
The second part (B in Fig.3) is due to the periodic nature of the interaction of the cutters with peat. Its value depends on the square of the mathematical expectations of the pulse parameters and is a sequence of peaks that lie at the frequencies wk = 2pk/T (k = 1, 2, 3, ...). Their shape is determined by a function that describes the density of the angular velocity distribution of the cutter, the spectrum of the moments S0v(jω;ωс;Pvm), S0η(jω;ωс;Pηl) and the arrangement of cutting elements.
The use of the probabilistic characteristics of the moments on the working bodies makes it possible to analyze the dynamic loads in the structural elements of the peat milling unit at the design stage using the methods of mechanical systems statistical dynamics [31].
Results discussion
The use of the proposed approach is considered on the example of the analysis of dynamic loads in the drive system of the machine for surface-layer milling MTF-14, which is designed to perform the first technological operation in the extraction of milled peat – crushing the top layer of the deposit.
The unit includes a gearbox, working bodies with pin cutting elements, track rollers, a rear support, a trailer and a frame. In a complete set, the router consists of seven sections, equipped with spacer springs, which are hingedly connected to each other. The cutter has three types of sections: the central one consists of a frame, a roller and two cutters 0.628 m long; four inner and two outer sections have a frame, a roller and a working body with a working width of 1.275 m each. The distance between the central cutters is 0.12 m, and the middle and outer cutters are 0.08 m; the peripheral speed is 8.9 m/s. The diameter of the working bodies is 0.221 m, and they have three pins in the cutting plane, and the body diameter is 0.157 m. The distance between the planes is 0.006 m, the shear angle between the cutters in adjacent planes is 24° (offset along the body scan is 0.03286 m). The angles between the cutters on different working bodies jhνr are equal to zero; the knives are the same size and type.
During operation in the MTF-14 drive, significant dynamic loads are formed, which reduces the reliability of its structural elements [12]. The main source of their excitation is the forces arising on the cutters. [12].
The spectral densities of moments during the interaction of working bodies with wood inclusions can be determined using the approaches considered in [12, 19], and when peat is milled – based on the methodology developed in [17].
Mutual spectral densities SCvη(jω) were calculated using (7). In this case, the moment of loading on a single cutter without taking into account the coefficient kvm, depending on the nature of the interaction, is approximated in the form [12]:
where φ1 – the angle of the working body rotation, corresponding to the maximum value of the moment within the arc of contact of the knife with the deposit; Mvmax – pulse peak value,
Bν – width of ν-th cutter; Нc – milling depth; W – unit travel speed; τ – peat shear stress; CT – empirical coefficient; δ – average chip thickness [19]; γ – density of peat in the deposit; φk – angle of contact of the cutter with the deposit, φk=2φ1,
Rc – radius of the working body at the ends of the cutting elements.
The spectrum of the moment of loading on a single cutter (8) is equal to:
The distribution density of the random value of the angular velocity of cutters wc can be determined based on the approaches considered in [25, 31]. The random parameters are: the angle of contact of the knife with the deposit jk which depends on the depth of milling Hc (9); peat density γ and the ultimate shear stress τ of the upper layer of the peat deposit.
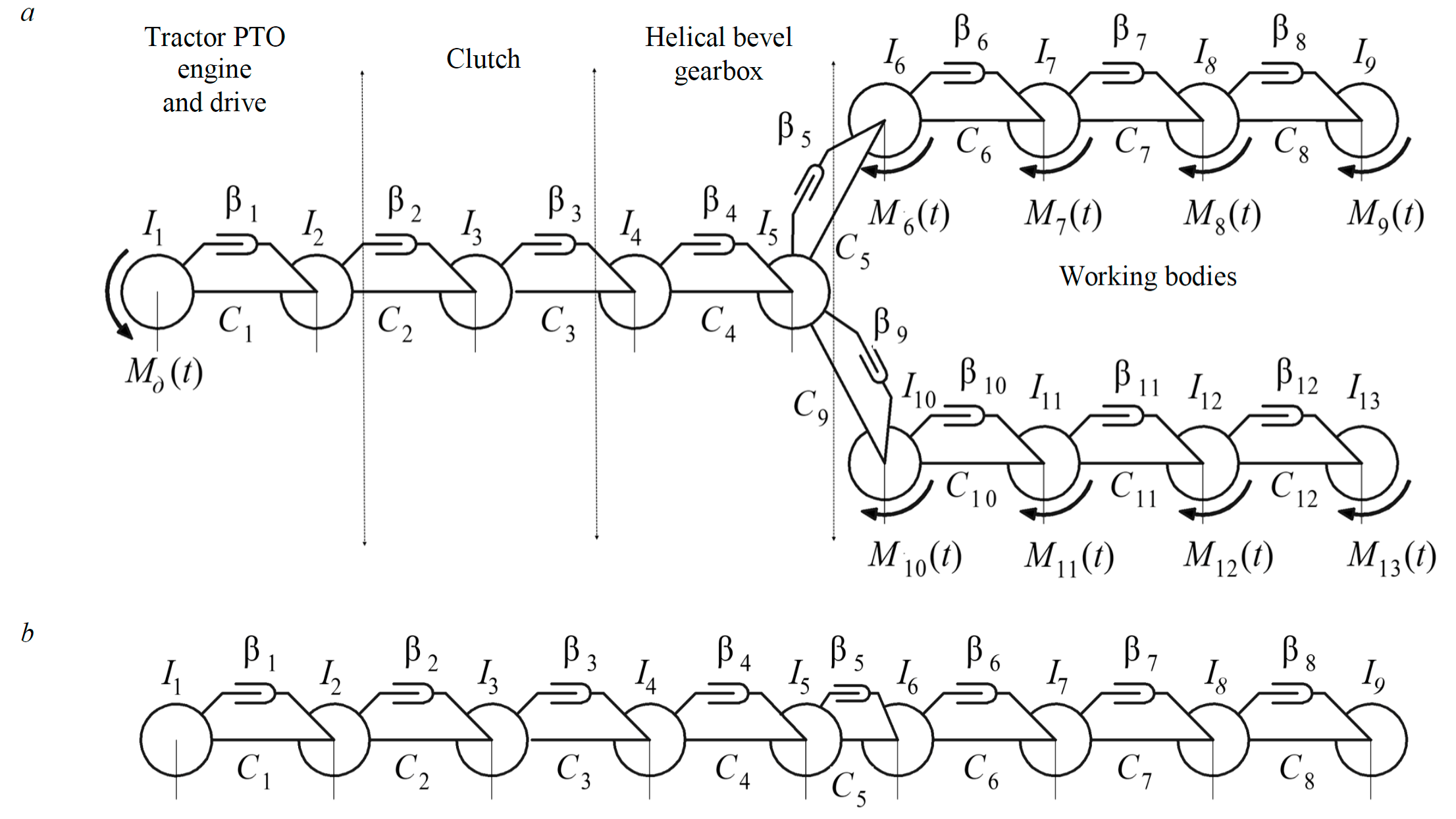
Fig.5. The dynamic design scheme of the MTF-14 drive reduced to the tractor engine shaft: branched design (a) and main reduced (b) schemes
The calculation was carried out under the following operating modes and characteristics of the peat deposit: movement speed W = 1.94 m/s; rotational speed of working bodies wc = 80 s–1; average milling depth – 0.015 m (dispersion 0,25·10–4 m); density of peat in the deposit – 720 kg/m3 (coefficient of variation 15 %); average ultimate shear stress – 45 kPa (coefficient of variation 15 %); the number of wood inclusions per 1 ha is accepted as 500 pcs. Its results are shown in Figs.3 and 4.
The values of spectral densities allow calculating the probabilistic characteristics of dynamic loads in the transmission of the milling unit. For this, a linear model of the MTF-14 drive was used [12], the diagram of which is shown in Fig.5, a. In [12] for the study of dynamic processes, the branched system (Fig.5, a) was replaced by two unbranched – the clamped branch and the main reduced system (Fig.5, b) according to the methods presented in [6, 29]. The model parameters reduced to the tractor engine shaft, the calculated frequency values and relative vibration amplitudes are shown in Tables 1 and 2.
Table 1
Parameters of the reduced dynamic model of the MTF-14 drive
Parameters |
Element number |
||||||||
1 |
2 |
3 |
4 |
5 |
6 |
7 |
8 |
9 |
|
Moment of inertia, kg∙m2 |
3,85 |
0,0096 |
0,026 |
0,017 |
0,032 |
0,173 |
0,204 |
0,204 |
0,2 |
Rigidity, Nm/deg. |
0,29·104 |
0,1·105 |
0,108·107 |
0,97·105 |
0,13·104 |
0,13·104 |
0,13·104 |
0,13·104 |
– |
Table 2
Relative amplitudes and frequencies of natural vibrations of the MTF-14 drive
Element number |
Natural oscillations, с–1 (Hz) |
||||
27,17 (4,32) |
76,27 (12,14) |
120,48 (19,18) |
149,42 (23,79) |
219,07 (34,88) |
|
1 |
–0,15213 |
0,04632 |
–0,03135 |
0,03067 |
–9,83819 |
2 |
–0,00298 |
–0,31141 |
0,57304 |
–0,87884 |
617,059 |
3 |
0,00402 |
–0,41341 |
0,74033 |
–1,23772 |
770,428 |
4 |
0,00406 |
–0,41429 |
0,74162 |
–1,12543 |
770,958 |
5 |
0,04512 |
–0,42372 |
0,75410 |
–1,13955 |
770,373 |
6 |
0,37606 |
–1,06809 |
1,41581 |
–1,56688 |
–183,421 |
7 |
0,67005 |
–0,88568 |
–0,65738 |
2,66139 |
34,3131 |
8 |
0,88638 |
0,10514 |
-1,23316 |
-2,43497 |
-6,38391 |
9 |
1 |
1 |
1 |
1 |
1 |
The spectral density of the moment in the i-th element without taking into account the correlation between the individual natural modes of oscillations (in the case when the system has a low damping, and the natural frequencies are not close to each other) using a linear model of the drive can be calculated as follows [31]:
where Ci –system elements rigidity; bi – damping factors; K, avp, aηp – the number of concentrated masses on which external loads act and their relative vibration amplitudes, respectively; P – number of natural oscillations; aip, ai+1;p– the relative amplitudes of the masses, between which the i-th elastic element is located for the corresponding natural frequency; ReSCvη(jω) – real parts of mutual spectral densities; ωр – p-th natural oscillation;
N – the number of masses of the dynamic model; In – moments of inertia of masses.
Calculated normalized spectral densities on the tractor PTO shaft (second element of the model) and determined experimentally (G.F.Vekoveshnikov, O.A.Golovina) [12] using strain gauge are shown in Fig.6. The dispersion of the moment obtained by calculation and experimentally is 0.053 and 0.0515 kNm2, respectively.
Comparison of calculating results the probabilistic characteristics of the loads in the MTF-14 transmission elements with experimental data confirms the correctness of the assumptions made for the models of the formation of loads on the working bodies, taking into account their mutual statistical relationship, which is characterized by the value of the mutual spectral density.
Conclusion
When performing technological operations, forces and moments act on the working bodies of peat milling units, which have a sharply variable, random nature. This predetermines significant dynamic loads in the structural elements of the machine, decrease in its reliability, and deterioration in technical and economic indicators.
When using the methods of statistical dynamics of mechanical systems for the analysis of dynamic loads at the design stage of a milling unit with several working bodies, it is necessary to know both the spectral and mutual spectral densities of the moments of resistance.
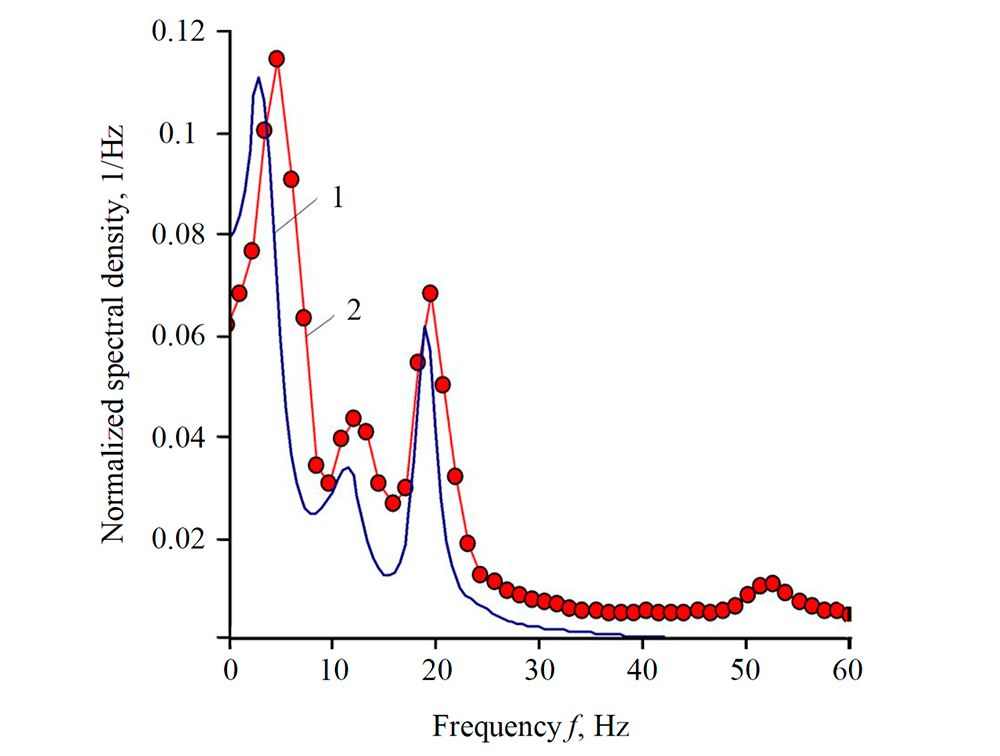
Fig.6. Normalized spectral densities of the moments of the tractor PTO shaft (the second element of the design scheme) 1 – calculation; 2 – experiment [12]
On the basis of the proposed models of moments in the form of pulses with random parameters, the expressions are obtained for calculating their mutual spectral densities. They take into account the physical and mechanical properties of peat, the operating modes of the unit and their probabilistic characteristics, as well as the design features of the working bodies. At the same time, in contrast to the known models, the number of cutting planes, the width of the cutters, their arrangement, the distance between the knives, their type and working conditions, determined by the type of interaction with the peat deposit (blocked, semi-blocked), on each of the working bodies of the unit may differ.
Dependencies for determining the probabilistic characteristics of the loads made it possible to highlight their features. Mutual spectral densities have a complex structure and two frequency zones. The first is proportional to the correlation functions of the parameters of the loading pulses; its form depends on the spectrum of the moments of resistance on the cutters and the scheme of their arrangement for various working bodies. The second part is due to the periodic nature of the interaction of the incisors with peat. Its value depends on the square of the mathematical expectations of the pulse parameters and is a sequence of peaks, the shape of which is determined by the density of the angular velocity distribution of the cutter, as well as the spectrum of the moments and the arrangement of the cutting elements.
As an example of using the developed approaches and in order to assess their reliability, the calculation of spectral and mutual spectral densities of moments on cutters and loads in the drive elements of the machine for surface-layer milling of MTF-14 is presented. Comparison of the calculation results with experimental data confirms the correctness of the assumptions made for the models of the formation of loads on the working bodies, taking into account their mutual statistical relationship.
The mutual spectral densities of the moments of resistance serve as initial information for calculating dynamic loads in the structural elements of a peat milling unit and indicators of its structural reliability.
References
- Fomin K.V., Krylov K.S., Kharlamov V.E., Morozikhin N.N. Influence of the eccentricity of the working body of a peat milling unit on the frequency properties of the moment of resistance. Trudy Instorfa. 2020. N 22 (75), p. 38-42 (in Russian).
- Gorlov I.V. Analysis of operating parameters of a peat machine using a simulation model. Mining informational and analytical bulletin. 2014. N 7, p. 173-177 (in Russian).
- Gorlov I.V., Rakhutin M.G. Influence of stumpiness of deposits on the reliability of peat machines. Mining informational and analytical bulletin. 2017. N 12, p. 139-145. DOI: 10.25018/0236-1493-2017-12-0-139-145 (in Russian).
- Gusev A.S., Shcherbakov V.I., Starodubtseva S.A. Calculation of the fatigue life of structural elements under random loading processes of a complex structure. Vestnik mashinostroeniya. 2015. N 12, p. 20-23 (in Russian).
- Gusev A.S., Zinchenko L.V., Starodubtseva S.A. Statistical dynamics and reliability of mechanical systems with kinematic, force and parametric actions. Problemy mashinostroeniya i nadezhnosti mashin. 2020. N 5, p. 21-28. DOI: 10.31857/S0235711920050065 (in Russian).
- Efimov L.V. Theory and practice of torsional vibrations of power plants using computer technology. St. Petersburg: Nauka, 2007, p. 276 (in Russian).
- Kopenkin V.D., Kopenkina L.V., Samsonov L.N. Development of milling machines in peat production (analysis, prospects). Mining informational and analytical bulletin. 2003. N 10, p. 204-207 (in Russian).
- Mikhailov A.V., Rodionov E.A., Zvonarev I.E. Analysis of conditions for vertical extraction of peat raw materials. Mining informational and analytical bulletin. 2019. N 1, p. 48-54. DOI: 10.25018/0236-1493-2019-01-0-48-54 (in Russian).
- Mikhailov A.V., Lopatyuk A.O., Shishlyannikov D.I. High-speed milling of a peat massif process features. Izvestiya vysshikh uchebnykh zavedenii. Gornyi zhurnal. 2017. N 2, p. 25-32 (in Russian).
- Panov V.V., Misnikov O.S. Development trends of the peat industry in Russia. Gornyi zhurnal. 2015. N 7, p. 108-112. DOI:10.17580/gzh.2015.07.15 (in Russian).
- Asonov S.A., Ivanova P.V., Ivanov S.L., Shishlyannikov D.I. Principles of building a model of the technical state of the transmission of a mining machine during its operation. Mining informational and analytical bulletin. 2017. N 3, p. 15-27 (in Russian).
- Samsonov L.N., Fomin K.V. Methods for analyzing the dynamic loading of peat machine drives by layer-by-layer surface milling. Gornye mashiny i avtomatika. 2004. N 1, p. 20-24 (in Russian).
- Samsonov L.N., Fomin K.V. Determination of the probabilistic characteristics of the loading moment on the the peat milling unit. Izvestiya vysshikh uchebnykh zavedenii. Gornyi zhurnal. 2003. N 3, p. 106-112 (in Russian).
- Samsonov L.N., Fomin K.V. Determination of mutual spectral densities of loads on the peat milling unit working bodies. Mining informational and analytical bulletin. 2002. N 1, p. 223-226 (in Russian).
- Sinitsyn V.F., Kopenkina L.V. Surface maps peat fields computer modeling. Trudy Instorfa. 2019. N 19 (72), p. 18-21 (in Russian).
- Zyuzin B.F., O Misnikov.S., Kopenkina L.V., Panov V.V. Peat industry in Russia: results of the past – a look into the future. Gornyi zhurnal. 2013. N 5, p. 73-76 (in Russian).
- Fomin K.V. Method for estimating the spectrum density of the resistance moment on the working body of a peat milling unit. Journal of Mining Institute. 2020. Vol. 241, p. 58-67. DOI: 10.31897/PMI.2020.1.58
- Fomin K.V. Modeling and analysis of the moment of loading on the working body of a peat milling unit. Mining informational and analytical bulletin. 2002. N 2, p. 222-226 (in Russian).
- Shtin S.M. Research on cutting peat and marsh wood. Mining informational and analytical bulletin. 2012. N 6, p. 374-376 (in Russian).
- Yablonev A.L., Krutov Yu.V. The use of modern digital strain gauging tools in the study of the loading of peat machine elements. Mining informational and analytical bulletin. 2016. N 8, p. 200-205 (in Russian).
- Chun Sheng Liu., De Gen Li, Xiao Ping Chen. Shearer Load Identification of the Load Spectrum of the Pick Based on Chaotic Characteristics. Advanced Materials Research. 2011. Vol. 199-200, p. 111-114. DOI: 10.4028/www.scientific.net/AMR.199-200.111
- Gong Jianchun. Characteristic analysis of random loads on shearer drum. Mining and processing equipment. 2014. Vol. 34. Iss. 8, p. 45-48.
- Howard R.M. Principles of random signal analysis and low noise design: The power spectral density and its applications. Willey, 2004, p. 328. DOI: 10.1002/0471439207
- Lalanne C. Mechanical Vibration and Shock Analysis, Random Vibration (Mechanical Vibration and Shock Analysis (3rd Edition). John Wiley & Sons, 2014, p. 595. DOI: 10.1002/9781118931127
- Lutes L.D., Sarkani S. Random vibrations: analysis of structural and mechanical systems. Butterworth-Heinemann, 2004, p. 650.
- Medolago A., Melzi S. A flexible multi-body model of a surface miner for analyzing the interaction between rock-cutting forces and chassis vibrations. International Journal of Mining Science and Technology. 2021. Vol. 31. Iss. 14, p. R713-R715. DOI: 10.1016/j.ijmst.2021.03.006
- Michailov A.V., Zhigulskaya A.I., Garmaev O.M. An integrated approach to strip mining of peat. International Conference on Innovations and Prospects of Development of Mining Machinery and Electrical Engineering, 24-27 April 2019, Saint Petersburg, Russian Federation. IOP Conference Series: Earth and Environmental Science, 2019. Vol. 378. N 012087. DOI: 10.1088/1755-1315/378/1/012087
- Misnikov O.S. Basic technologies and equipment used for peat deposit development in foreign countries. IIIrd International Innovative Mining Symposium, 3-5 October 2018, Kemerovo, Russian Federation. E3S Web Conference, 2018. Vol. 41. N 01046. DOI: 10.105/e3sconf/20184101046
- Nestorides E.J. Handbook of torsional vibration. Cambridge University Press, 2011, p. 694.
- Xiao Huo Li, Xin Wei Yu, Xiao Hong Ma, Ying Bo Zhao. Simulation and Study of Random Loads on Continuous Miner Cutting Drum. Advanced Materials Research. 2011. Vol. 308-310, p. 1885-1888. DOI: 10.4028/www.scientific.net/amr.308-310.1885
- Svetlitsky V.A. Statistical dynamics and reliability theory for mechanical structures. Springer, 2003, p. 452. DOI: 10.1007/978-3-540-45826-5
- Zhao Li-juan, Ma Yong-zhi. Reability rescearch on shearer cutting unit based on multi-body dynamics. Journal of China Coal Society. 2009. Vol. 34. N 9, p. 1271-1275.