Features of obtaining metallurgical products in the solid-state hydride synthesis conditions
Abstract
A scientific substantiation of solid-phase feedstock choice and preparation has been carried out, and the thermodynamic and kinetic aspects of solid-state hydride synthesis (SHS) of metal products have been analyzed using the nickel dichloride reduction as an example. The preliminary dehydration modes and methods for controlling the complete removal of crystalline water from chloride raw materials and Olenegorsk superconcentrate, which is natural oxide raw material, are described. Conditions, including initial solid chloride particle sizes, are established under which diffusion complications of reduction to metal in methyldichlorosilane vapor are minimized. Thermodynamic estimates of nickel chlorides and oxides reduction possibility, iron and copper with ammonia and methane at temperatures of 400-1000 K in equilibrium conditions have been carried out. It has been shown that the stoichiometric coefficients of the nickel dichloride in ammonia overall reduction reaction calculated by thermodynamic modeling are in agreement with experimental data. In contrast to the copper dichloride reduction, for nickel dichloride the formation of metal monochloride at the intermediate stage is uncharacteristic, which is associated with a higher thermal stability of nickel dichloride. The main kinetic regularities of the reduction of nickel, copper, and iron to metal under SHS conditions in ammonia, monosilane, and methane, as well as the nickel dichloride with methyldichlorosilane vapor and methane successive reduction, are considered. Approximation of experimental data by topochemical equations in a linear form showed that for reduction degrees a up to 0.7-0.8, these data are satisfactorily described by the Roginsky – Schultz equation. For a > 0,8 the “shrinking sphere” model works better, which confirms the localization of the solid-state reduction reaction at the interface, moves deep into the crystal with the formation of a of interlocked metal germs. The importance and prospects of the results obtained for the theory development of metallurgical processes, deep complex processing of natural iron oxide raw materials, metal products and new generation materials production, including superhydrophobic ones, are discussed. The relevance of the study from the point of view of applying the method of physical and chemical analysis to the study of complex heterogeneous metallurgical processes is noted.
Introduction
The energy- and resource-saving technologies development for obtaining high-quality metals is one of the promising areas of modern metallurgy [1, 2]. Production, in which gaseous reagents are used to reduce metal from ore raw materials, in general, are more environmentally acceptable processes than those in which solid reducing agents (coal, shungite, etc.) are used [3, 4]. The industrially used method of reducing iron oxide raw materials with converted natural gas (above 700 °C) is a fairly explosion and fire unsafe process that can cause unwanted gas corrosion of metal [5]. To reduce the metal recovery energy intensity, save material resources, reduce the burden on the environment and improve the environmental friendliness of the resulting metal products, the processes of solid-state hydride synthesis (SHS) of metals are of considerable interest [6, 7]. These processes are carried out, in general, at relatively mild temperatures in the range of 300-600 °С. SHS of metals is based on the reduction in an open flow system of metals solid compounds (ores) by volatile elemental hydrogens (E = N, C, Si, etc.) in the thermal stability area. At present, studies of SHS of metals are being developed within the framework of the Mining University research area. Metal pro-ducts synthesized as a result of the interaction of nickel (II) and copper (II) chlorides with ammonia [8]; chlorides Ni, Cu, and Fe with monosilane [6, 9]; nickel chloride (II) and Ni oxides (II), Cu (II) and Fe oxides (II) with methane (purified natural gas) [8, 10] have been obtained and identified. Of particular interest for the creation of dispersed metallic materials with a protective silicon carbide or carbosiloxane nanofilm on the metal are the processes of successive reduction under SHS conditions of chloride or oxide raw materials with vapors of methyldichlorosilane (alkylhydridesiloxane) and methane. [7]. In 2015, a method for obtaining a surface-nanostructured metallic material was develo-ped and protected by a patent of the Russian Federation N 2570599 [10, 11]. A proposed reduction process feature was that the stages of drying the initial solid-phase raw materials and the first stage of its reduction in organosilicon hydride reagent vapors were carried out in a methane stream. The study of the nickel dichloride reduction in the framework of research on SHS is relevant. It makes it possible to realize the possibilities of promising methods of chlorine metallurgy [12, 13] to reduce environmental problems in the production of nickel from natural metal sulfide raw materials. Note that it is easier to restore metal chlorides (Ni, Fe) [6, 14], than nickel-containing sulfide and oxide concentrates [3, 13], which makes it possible to reduce energy costs compared to traditional production. The industry has long worked out the conditions for the transition from natural iron-nickel pyrite, sulfide copper-nickel concentrate to metal chlorides: chlorination of sulfide raw materials in Cl2, HCl or sintering of other elements (Na, Fe, etc.) with chlorides [13]. The study of obtained SHS metal products structure and properties, the experience of their implementation at the mineral resource complex enterprises are described in detail in the papers [6-8]. However, the scientific substantiation issues of the initial raw materials (metal-containing solid phase, reducing agents, gases used) choice, as well as the thermodynamics and SHS processes kinetics, are insufficiently covered in the scientific literature. The significance and relevance of the listed metals solid-state recovery aspects analysis are determined by their importance for the metallurgical processes theory development [15, 16] and influence on the quality and performance properties (heat resistance, hydrophobicity, strength) of the resulting metal [17-20].
The purpose of the work is to analyze the modes of preparation and characteristics of the solid-phase raw materials, hydride reagents and inert gases, thermodynamic estimates and the ongoing processes kinetics using the example of the reduction of nickel dichloride and natural iron oxide raw materials in SHS conditions.
Research method
Comparative (in different hydride media), SHS of metals, X-ray phase and chemical analysis, control of magnetic flux changes during nickel reduction, XPS (Photoelectron Spectroscopy), thermodynamic modeling, time dependence approximation of the degree of recovery by topochemical equations. Water removal from the initial crystalline hydrate NiCl2·6H2O (chemically pure) or chlorides and oxides of other metals (Cu, Fe) was carried out in an inert atmosphere by heating until a constant sample weight was reached in a flow reactor. High-purity argon and methane from cylinders were dried and purified from oxygen microimpurities by standard methods [8-10] with the final stage of gas purification in a low-temperature (–160 °С) zeolite trap. The reduction degree (α) of nickel dichloride to metal was judged by the decrease in chlorine in the sample, by the increase in magnetic flux in situ by placing the reactor with the sample being reduced in the F5050 microwebermeter inductance coil [8, 10]. The fact of NiCl2 reduction to metal was additionally controlled by X-ray phase analysis and XPS spectroscopy, taking samples at different stages of solid sample reduction. The stoichiometric coefficients of reduction to metal gross reactions were estimated by the method of thermodynamic modeling based on the minimization of the Gibbs energy using the ASTICS software package [6, 17, 21]. To assess the applicability of topochemical reduction processes certain models, the corresponding equations in the linear form were used [8].
Discussion
From the theory of metallurgical processes, it is known that the presence of moisture in the system solid (ore) – reducing gas interferes with the deep reduction of the feedstock to the metal; according to Trepnel, the water content of at least 0.1 volume percent in the system significantly reduces the speed of the process. Therefore, when developing the SHS method, considerable attention was paid to minimizing the moisture content in the initial metal-containing raw material and the gas phase. When using the NiCl2∙6H2O (chemically pure) commercial product as a feedstock, the sample dehydration was achieved by stepwise heating in an argon flow (flow rate 0.25 l/min), according to the modes shown in Fig.1. Modes I and II, which ensure the crystalline water removal, are substantiated by the experimentally obtained mass loss on time dependence (Fig.1). The observed weight loss after 5-6 hours of heat treatment practically coincides with the calculated amount of water contained in the initial sample (0.5 g). Mode II allows you to reach the saturation point than mode I faster. Mode II consists in rapid heating, up to about 220 °С in 0.5 h. Then the temperature is raised to 450 °C and kept in an argon flow for several hours until Δm reaches a constant value. The slower mode I includes the removal of physically sorbed water for 1.5 hours at 80-120 °С. The temperature is then raised to 220 °С, the sample is kept for no more than 0.5 h and then proceed to the final stage of heat treatment at 450 °С. In a few hours, as can be seen from Fig.1, the removal of six water molecules from each nickel dichloride molecule is completed. The choice of the final heat treatment temperature is determined by the hydride reagent type used in the subsequent reduction stage. In the given example, nickel dichloride was dried at 450 °C to be further reduced to metal with gaseous ammonia at 440 °С.
After 6 h of heat treatment in an argon medium, in the obtained samples, as shown by chemical analysis, the Cl/Ni atomic ratio was 2.01 ± 0.02, the Cl/Ni ratio in the surface layer found by X-ray photoelectron spectroscopy was at the level of 2.2±0.1. Thus, elemental analysis shows that the dried solid raw material is nickel dichloride, which is confirmed by X-ray phase analysis. The results of chemical analysis demonstrate the “delicacy” of the heat treatment. Judging by the composition of the dried samples, the removal of water molecules from the nickel halide structure did not cause a noticeable destruction of Ni-Cl bonds due to the chemical interaction of the metal chloride with desorbing water with the elimination of hydrogen chloride molecules, which leads to a partial loss of chlorine in the samples. It is difficult to avoid such processes when drying very hygroscopic Fe (III) and Fe (II) chlorides flooded with water, when there is a real possibility of a part of the metal chloride transforming into the corresponding oxychloride [22, 23].
According to earlier studies [9] a decrease in the maximum drying temperature to 230-400 °С significantly increases the duration of nickel dichloride dehydration: at 230 °С up to 12 hours, at 300 °С up to 10 hours, at 350 °С up to 8.5 hours, at 400 °С up to 7.5 hours. Drying of Ni chloride (II) crystalline hydrate requires not only the removal of physically sorbed water, but also the water retained in the structure of the solid phase by coordination chemical bonds. Therefore, the drying temperature must be raised above 220 °С. Sample drying temperature at 450 °С not only minimizes the time of complete water removal (up to 6 hours), but also allows you to save the transport pores of solid nickel dichloride, which are necessary for the access of molecules of hydride reagents and deep reduction at the subsequent stage of SHS of metal.
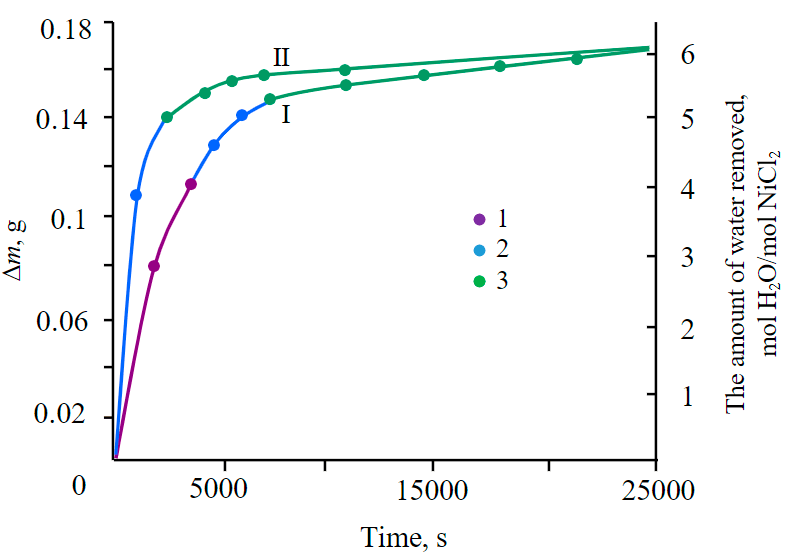
Fig.1. Time dependence of the weight loss of nickel dichloride hexahydrate during heat treatment in a stream of high purity argon 1 – heating to 80-120 °С; 2 – 220 °С; 3 – 450 °С
Methods based on gravimetric measurements of sample mass loss during drying and control of the chemical and phase composition of samples during heat treatment were also used in the preparation of other types of initial metal-containing raw materials: Ni oxide (II), chlorides and oxides of Cu (II) and Fe (II), as well as Olenegorsk superconcentrate, similar in composition to Fe3O4 (up to 99.5 wt.%) [8-10].
Let us consider an example of Olenegorsk superconcentrate drying and recovery. Olenegorsk superconcentrate (OSC) is a magnetite concentrate enrichment product obtained from ore deposits in the North-West of the Russian Federation. The main component of OSC is Fe3O4 (up to 99.5 wt.%), typical impurities are aluminum and silicon (tenths of a percent). OSC is a black powder, the specific surface area is about 10 m2/g. The sorbed moisture removal from the OSC is carried out in temperature mode II (Fig.1), in an environment of purified natural gas, raising the final temperature of the drying stage to 400 °С. At the same temperature, the dried OSC is treated in vapors of methyldichlorosilane or hydrophobizing organosilicon liquid GKZH-94 for at least 1.0-1.5 hours. After that, the supply of organosilicon reducing agent is turned off and the temperature is raised to 500 °C. The sample is kept in a stream of natural gas for deep drying and purification for at least 3 hours until the CO2 release at the reactor outlet stops. It is not recommended to carry out the final reduction annealing at temperatures exceeding 500 °С, since this leads not only to the metal reduction, but also to the partial carbidization of iron with the formation of Fe2C. The composition of the obtained metal sample, wt.%: 94.5±0.5 Fe; 0.8±0.4 Si; 1.5±0.3 C; 3.2±0.8 O. The X-ray diffraction pattern of the sample contains analytical high-intensity diffraction maxima with d = 2.04; 1.43; 1.16, characteristic of metallic α-iron. The binding energy of the Si2p level in the surface layer of the sample is 102.5 eV. Sample heat resistance in air – 0.0001 mg/cm2 (900 °C, 100 h).
The increased interest of the authors in nickel dichloride in the framework of this article is due to high thermal stability, resistance to water vapor during dehydration, extremely low volatility in the range of 350-550 °C (vapor pressure no more than 0.1 μPa) compared to chlorides of other base metals. According to the theory, this guarantees the occurrence of reduction reactions to metal under SHS conditions in the solid phase.
Another feature of nickel dichloride is that its crystalline hydrate has a salad color, and the anhydrous preparation is yellow. This allows you to visually monitor the process of dehydration of the crystalline hydrate during heat treatment by observing the sample through the wall of the Pyrex glass flow reactor, as well as control the onset of reduction and the intensity of transformations of the starting material at subsequent stages of treatment with hydride reagents. When NiCl2 is reduced, it turns black; therefore, one can clearly observe the advancement of the front of the heterogeneous reaction of the reduction of solid chloride over the initial sample volume. This turned out to be especially useful (according to the experience of the authors) for the selection of gas-dynamic modes of nickel reduction in enlarged flow reactors, where not grams of anhydrous nickel dichloride, but large amounts of it in the range of 0.5-1.0 kg were placed on the reactor grid. Another advantage of nickel dichloride is good compressibility in the form of cylinders with a height of 0.05 m and a diameter of 0.03 m on standard presses. The cylindrical blank reduced in ammonia withstood a crushing force of 4 T (reduced from NiCl2 in hydrogen – less than 2 T), had a Brinell hardness HB of about 800, tensile strength σ = 450 MPa, which is not inferior to industrial cast annealed nickel (HB = 740, σ = 400 MPa). Thus, the use of nickel dichloride as a feedstock is of interest not only for the direct production of dispersed nickel from its halide, but also for the production of simple metal products with a significant reduction in energy costs, bypassing melting and minimizing the need for metal processing.
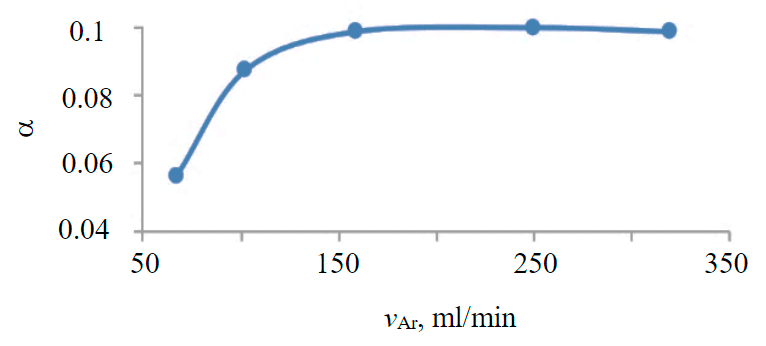
Fig.2. Dependence of the nickel dichloride (fraction 0.6-0.8 mm) recovery degree from argon consumption
To reduce NiCl2 in NH3, SiH4, CH4 medium, fractions with a particle size of the solid phase in the range of 0.3-1.0 mm were selected [3], with this particle size, reduction to metal by relatively small gas molecules (H2, CO, a mixture of H2 and CO) occurs with minimal diffusion complications.
We have established for the first time that the reduction of NiCl2 in vapors of methyldichlorosilane (MDCS), which has molecules larger in size than those of the listed gases, is characterized by an almost constant degree of reduction to metal when using different fractions of the solid phase. Effect of nickel dichloride particle size on the degree of reduction to metal (α) at a flow rate of MDCS vapor carrier gas of 300 ml/min for 100 min: fraction 0.3-0.5 mm – α = 0.58; 0.5-0.8 mm – α = 0.60; 0.8-1.0 – α = 0.63.
The dependence in Fig. 2 indicates that with a particle size from the indicated range, an increase in the flow rate of more than 200 ml/min for the carrier gas (Ar), in the flow of which MDCS vapors are supplied to the reactor, does not lead to an increase in the degree of reduction to metal.
With the characteristics of the dispersion of the solid phase chosen by us and an argon flow rate of more than 200 ml/min, the process of reduction to metal is not limited by the delivery of reducing agent molecules to the surface of the solid phase, and the complications associated with external diffusion are practically eliminated. According to the data of adsorption-structural measurements, the initial surface of the obtained anhydrous NiCl2 is about 10 m2/g, the total porosity is 27.4 %, open porosity 26.8 %, closed porosity (inaccessible pores) is minimal (0.6 %). Upon reduction in SiH4 (350 °C), the open porosity increases to 44 %, and the surface of the solid phase to 40 m2/g. Similar characteristics of the metal product obtained in NH3 (450 °C) are 10.1 and 13 m2/g. These facts testify that under the selected SHS conditions, at least up to 400 °C, the diffusion of reducing agent molecules in pores cannot be a serious factor limiting the rate of reduction to metal.
The stated assumption is confirmed by the values of the apparent activation energy of the process calculated from the data on the reduction kinetics in various hydride media (Table 1).
Table 1
Activation energy values for reduction of nickel dichloride to metal
Reducing agent |
H2 |
CH4 |
NH3 |
SiH4 |
CH3SiHCl2 (MDCS) |
Process activation energy, kJ/mol |
130 |
150 |
200 |
250 |
240 |
The activation energy value of processes with the use of SHS hydride reagents typical, as in the case of the traditional reducing agent, molecular hydrogen, significantly exceeds 100 kJ/mol. From this it follows that the heterogeneous process rate of reduction to the metal as a whole is determined by the rate of chemical interaction in the system.
The importance of deep purification and drying of gaseous media used in SHS is emphasized by the following experiment. In the process of treatment (500-600 °С) of pre-dried nickel dichloride powder with domestic natural gas coming from the city mains, without standard cleaning and passing through a low-temperature trap, the initial sample of solid chloride changed color from yellow to salad green. From this experience, it follows that untreated natural gas containing a mixture of hydrocarbon reducing agents not only does not reduce nickel, but also leads to watering of the original NiCl2 and its gradual transformation into NiCl2∙H2O crystalline hydrate. However, if the applied natu-ral gas is first passed successively through a system of dryers (calcined silica gel, phosphorus pento-xide deposited on a glass nozzle), through activated copper on silica gel at 450 °С to purify the gas from trace oxygen impurities, and through a low-temperature trap filled with zeolite, then the result of the experiment will be completely different.
Visually, blackening of the sample particles is observed, which move in the field of the brought magnet. After removal of chlorine from the sample in the process of reduction with purified natural gas (methane), the X-ray diffraction patterns of the resulting powder contain analytical diffraction maxima corresponding to interplanar distances d (1.246; 1.755; 2.03), which are characteristic of the nickel metal phase [3].
Thermodynamic calculations performed for equilibrium conditions (Fig.3) show that the reduction in gaseous ammonia of Ni (II) and Cu (II) chlorides, as well as copper oxide above 700 K, is characterized by a negative change in the isobaric Gibbs potential (ΔG < 0). This means that the listed processes of reduction to metal of nickel and copper compounds are thermodynamically favorable in the temperature range of SHS: 713-733 K (440-460 °С). Since real SHS processes are carried out far from equilibrium (in a reducing gas flow with the removal of volatile reaction products), in practice it is possible to achieve reduction to NiO metal in CH4 and even Fe (II) oxide by replacing methane with MDCS vapor [8-10].
Upon using of the thermodynamic modeling modern method, it becomes possible not only to estimate the probability of the occurrence of a particular process [24], but also to obtain the matrix of the stoichiometric coefficients of the corresponding chemical reaction [6, 17, 21]. In this work, for the first time, the stoichiometric coefficients of the reaction of nickel reduction to metal in ammonia were calculated in a wide temperature range, including the range characteristic of SHGS (Fig.4).
The experimentally confirmed scheme of the overall reaction of NiCl2 reduction in NH3 in SHS conditions is described by the equation:
The thermodynamic simulation data in Fig.4 generally agree with the stoichiometry according to the scheme. It follows from Fig.4 that, as in the above equation, theoretical calculations show that from every three NiCl2 molecules above 714 K, three nickel atoms, six HCl molecules and one N2 molecule are formed. The results of thermodynamic modeling also do not contradict to known reference data.
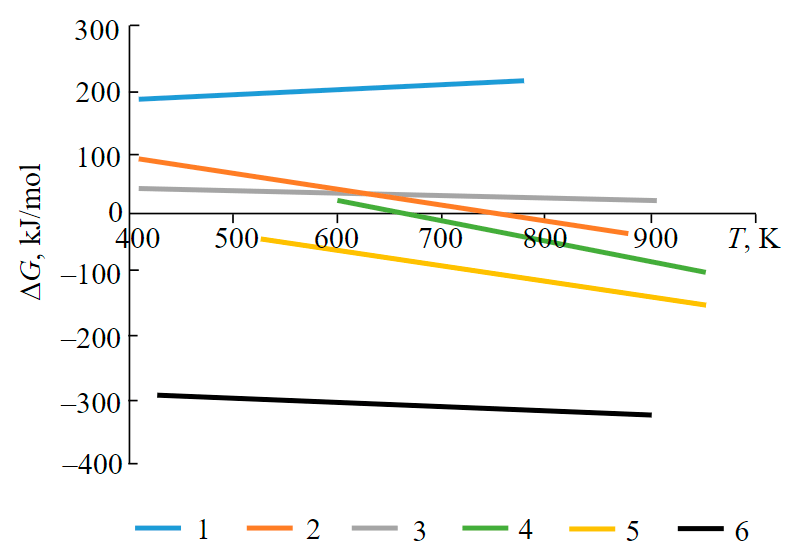
Fig.3. The effect of temperature on the change in the Gibbs potential during the reduction of metal compounds by hydrides 1 –4FeO + CH4 = 4Fe + CO2 + 2H2O; 2 – FeCl2 + 2/3NH3 = Fe + 1/3N2 + 2HCl; 3 – 4NiO + CH4 = 4Ni + CO2 + 2H2O; 4 – NiCl2 + 2/3NH3 = Ni + 1/3N2 + 2HCl; 5 – CuCl2 + 2/3NH3 = Cu + 1/3N2 + 2HCl; 6 – 4CuO + CH4 = 4Cu + CO2 + 2H2O
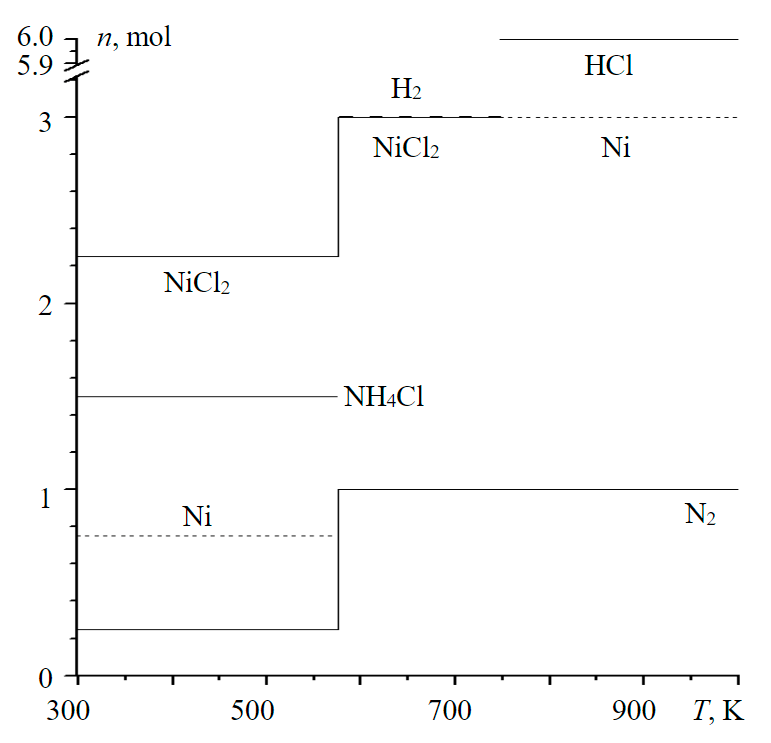
Fig.4. Influence of the temperature factor on the reduction of nickel dichloride in ammonia
For example, the presence of NH4Cl is shown to the left of the temperature interval in Fig.4 which corresponds to the SHS of metals (713-733 K). In the temperature range of SHS, ammonium chloride is no longer present. This corresponds to the thermochemical properties of NH4Cl, which sublimates at a temperature of about 610 K (337 °C) and leaves the reaction zone of the flow unit in SHS conditions. According to the experimental data, the overall reaction scheme for the reduction of CuCl2 in NH3 follows an equation similar to that given above. Thermodynamic modeling data for reduction in NH3 of copper dichloride [6] and nickel dichloride (Table 2) demonstrate good agreement between the calculated and experimental data on the value of stoichiometric coefficients and molar ratios between substances formed as a result of the reduction of metal dichloride (М = Cu, Ni).
Table 2
Molar ratios of reactants in the reduction to metal (M) of copper and nickel dichlorides in ammonia
Initial metal compounds |
[HCl]/[M] |
[M]/[HCl]/[N2] |
||
Calculation |
Experiment |
Calculation |
Experiment |
|
CuCl2 |
2:1 |
2:1 |
3:6:1 |
3:6:1 |
NiCl2 |
2:1 |
2:1 |
3:6:1 |
3:6:1 |
The existing thermodynamic model does not take into account that, in SHS conditions, the dissociation of the N-H chemical bond of ammonia occurs on a solid surface, and the released hydrogen atom binds to the chlorine atom from the metal halide and is released in the form of HCl. Therefore, molecular hydrogen, which is present in Fig.4, obviously does not reflect the details of the physicochemical mechanism of SHS associated with the dissociative chemisorption of the reducing hydride on the surface of the solid phase. The decomposition of ammonia into N2 and H2 in the gas phase is typical for higher temperatures (above 740 K). What is common in the phase model for the reduction of solid nickel and copper chlorides in ammonia is that at low reduction temperatures (up to 640 K), one of the reaction products is ammonium chloride. The main difference is that, according to Fig.4, the reduction of nickel dichloride is not accompanied by the formation of metal monochloride at the intermediate stage, which is typical for the reduction of CuCl2 in ammonia. Perhaps this is due to the greater thermal stability and strength of the M-Cl bond in NiCl2 than in CuCl2 [12, 13].
Time dependences analysis of reduction to metal degree (α) during the treatment of Ni (II) oxide and Fe (II) and Cu (II) chlorides with the simplest hydrides in SHS conditions showed the following. At 0.1 < α < 0.7, experimental data with a linear correlation coefficient of 0.96-0.98 are described by the Roginsky – Schultz equation in a linear form (Fig.5, a). At high degrees of recovery, up to 1, it is preferable to approximate the obtained values α in the coordinates of the “shrinking sphere” equation in a linear form (Fig.5, b). Similar topochemical equations are known in the practice of describing the reduction of metals with traditional reducing gases.
Figure 6 shows a typical dependence of α on time τ for reduction of NiCl2 in CH4 at 500 °С. On the right in Fig.6, the dependence α = f (τ) is placed for a more complex case: approximately up to α = 0.8, the reduction occurs in MDCS vapor (curve 1), then to accelerate the recovery and removal of chlorine, annealing is carried out in CH4 under more stringent temperature conditions (curve 2).
The representation of experimental data in Fig.6 (curve 1) for 0.1 < α < 0.7 in the coordinates of the Roginsky – Schultz equation is satisfactorily approximated by straight line 1 in Fig.7, a. But the kinetic data in Fig.6 for higher α are better described by the “shrinking sphere” equation (line 2 in Fig.7, a). Processing of the experimental results, curve 2 in Fig.6, for α > 0.9, when the sample is already reduced in CH4, shows that a modification of the “shrinking sphere” equation of the form kτ=1-(1-α)1/3 is more successful than modifying the form kτn= α/(1-α), where n = 1 (Fig.7, b).
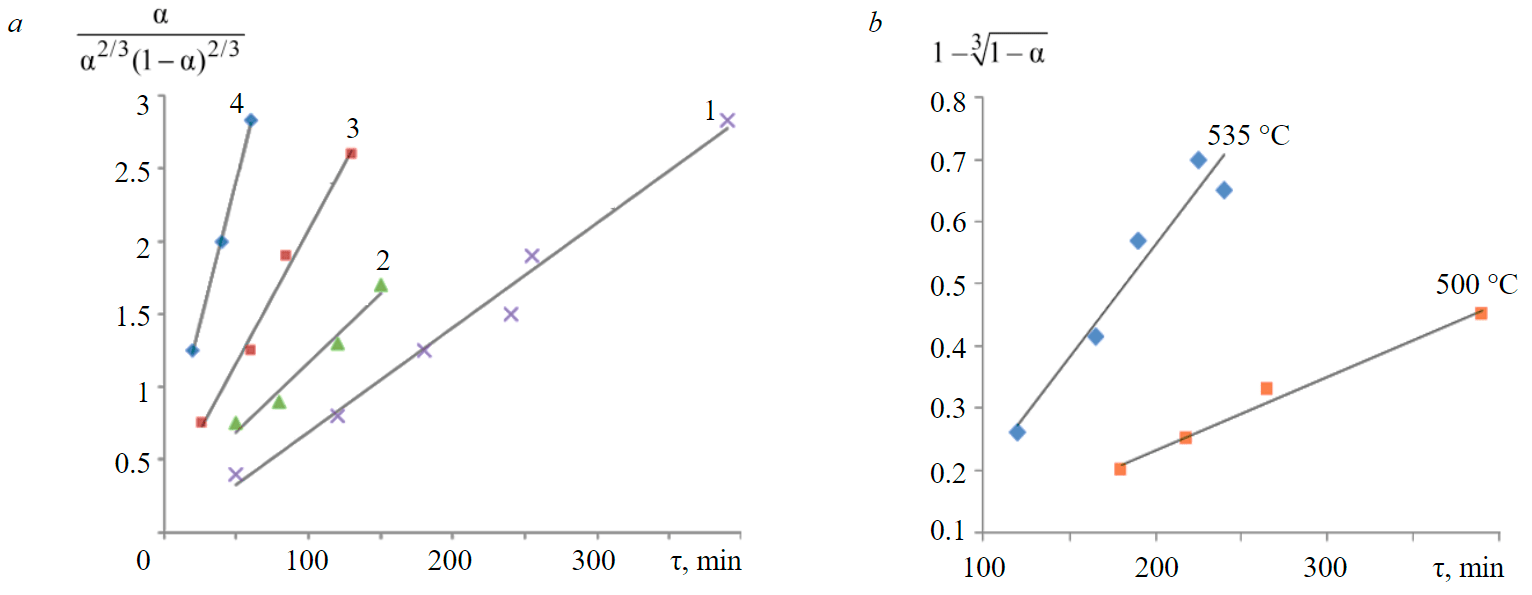
Fig.5. Results of experimental kinetic data approximation of for reduction to metal: а– for reaction 1 – NiO, CH4 (500 °С); 2 – NiO, CH4 (535 °С); 3 – FeCl2, SiH4 (340 °С); 4 – CuCl2, NH3 (450 °С); b – for reaction NiO, CH4
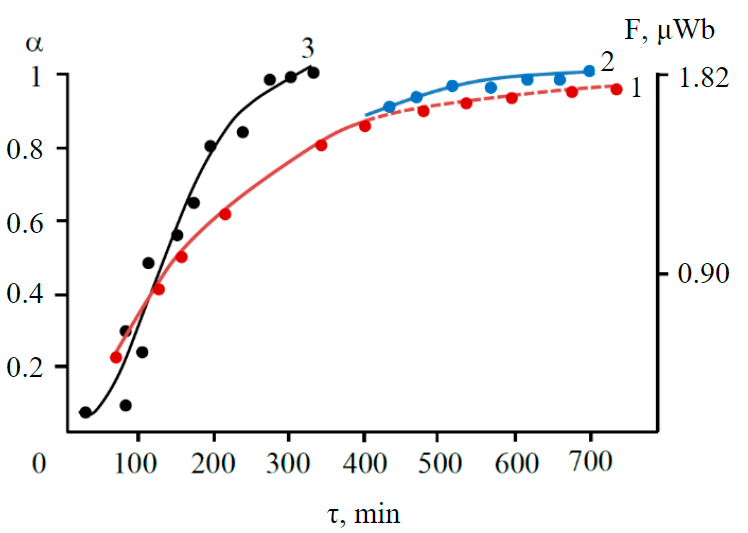
Fig.6. Dependence of a on the time of interaction with MDCS and CH4 at different SHS temperatures 1 – MDCS (340 °С); 2 – СН4 (680 °С); 3 – NiCl2 + CH4 (500 °С)
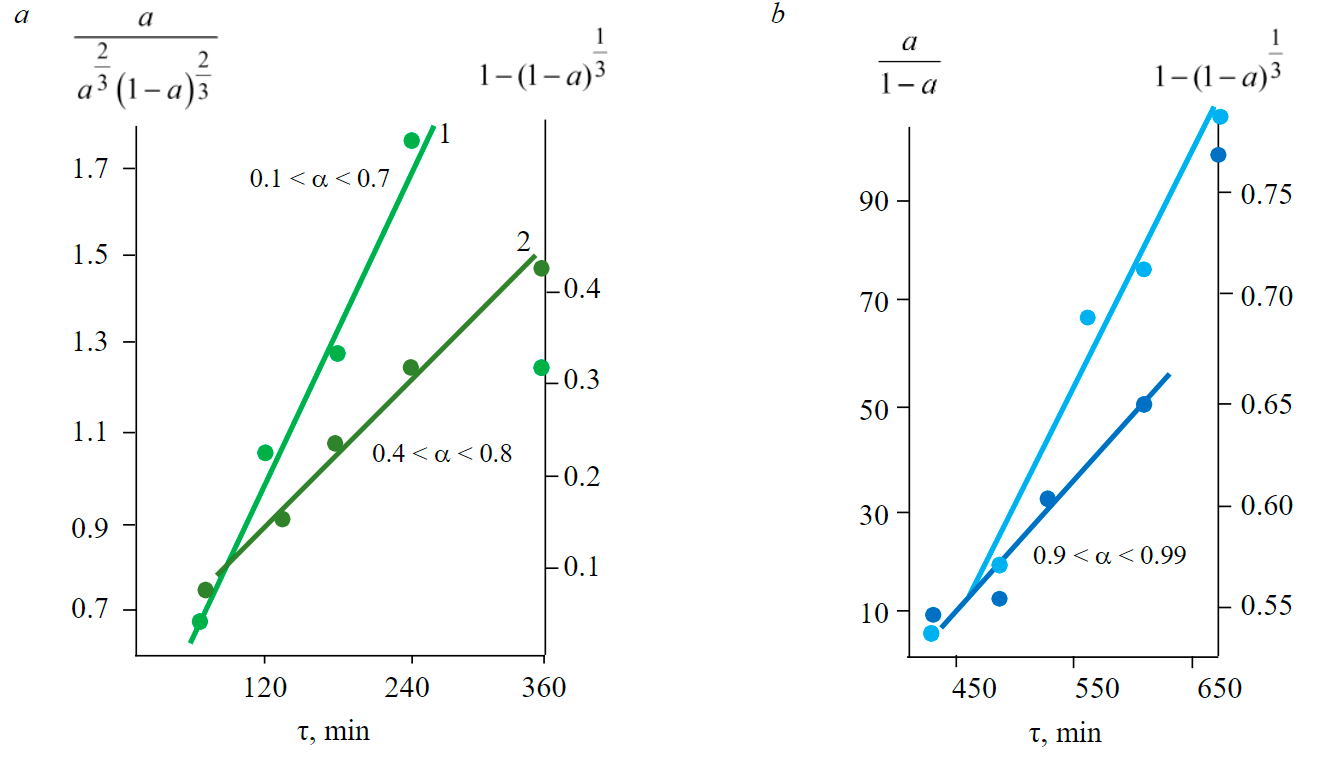
Fig.7. Approximation of experimental data: a – on curve 1 in Fig. 6 by the “shrinking sphere” equation and the Roginsky – Schultz equation; b – of curve 2 Fig.6, equations kτ= α/(1-α), kτ = 1 – (1 –a)1/3
The above expression of α on τ dependence is a special case of the “shrinking sphere” equation. It describes the situation when the formation of nuclei of a new phase is instantaneous and occurs simultaneously over the entire surface. The experimental data approximation results in Fig.7, b indicate that this model is not typical for the real process. The course of the process according to this model is obviously hindered by the inhomogeneity of the surface, which is associated, among other things, with the presence of various pores, confirmed by adsorption-structural measurements [25].
Thus, at the final stage (reduction in CH4), apparently, the main “shrinking sphere” mechanism model takes place. A layer of closed metal nuclei grows. The reaction is localized at the interface, which moves deep into the crystal in the course of the process. It is assumed that the reaction proceeds on a spherical interface, and the radius of the sphere decreases in the course of the process [25]. The thickening of the metal product layer can create an obstacle to the penetration of the reducing gas to the solid metal chloride.
The presented material develops the scientific direction of the Mining University “Nanostructured highly hydrophobic metals and solid-state methods for their production” within the Mining University metallurgists research framework [15, 19]. When studying the SHS of metals, the main emphasis is on the processes of metal reduction from solid chlorides, which are considered as an intermediate product in the chlorination of natural metal sulfide raw materials in the process of metal production. In paper [6, 7] The main attention was paid to the possibilities of SHS by varying the type of hydride reagent to obtain metals with different surface properties and high useful characteristics (heat resistance, hydrophobicity, resistance to salt corrosion). Thus, the study of SHS contributes not only to the theory of new metallurgical processes (direct reduction) using non-traditional reducing modifiers, but also meets modern trends in the production of new generation metal products and materials [26, 27]. Given the importance of creating superhydrophobic surfaces to prevent unwanted corrosion and biological processes on metals [4, 28, 29], the formation of SHS of metal products in the medium of organosilicon hydride reagents and methane is of particular interest [7, 8].
At the end of 2020, 160 years have passed since the birth of the outstanding graduate of the Mining Institute, Academician N.S.Kurnakov, the creator of the method of physical and chemical analysis [30], who stood at the origins of the scientific school of metallurgists of the Mining University in St. Petersburg [3]. “Non-Ferrous Metals” journal dedicated an issue to this event [31]. The considered issues of thermodynamics and kinetics of SHS metals undoubtedly illustrate the application of physicochemical analysis to the study of complex heterogeneous metallurgical processes. The use of the fundamental principle of physical and chemical analysis in identifying the relationship between the physical or chemical properties of substances and their composition is typical for modern studies of alloys and metallic materials [30, 32], various metallurgical processes [6, 19, 34] and composite materials [33, 37], problems of the mineral resource complex [3, 16, 36].
According to the developer’s intention of the SHS of metals and the possibilities of the method, it is focused not on the large-tonnage production of metal products, but on the production of unique materials in relatively small quantities for solving “delicate” problems (creation of porous metallized cold cathodes [7], obtaining metals for the battery sector of the industry, useful dispersed additives for lubricants, polymers, protective coatings [8-10]). According to available estimates, the need for solid SHS products for a metropolis of the scale of St. Petersburg is 250-300 kg/year. Such a modest figure is due to the fact that the addition of surface-modified metal products of SHS in lubricants, enamel, and paint is, as a rule, no more than 1 wt.%. At present, some of the results presented in the article are used as the basis for technological schemes that are officially introduced into the project for the construction of a mining and metallurgical plant at the Kingashskoye cobalt-copper-nickel deposit (Krasnoyarsk Territory).
Conclusion
The choice and preparation modes of the initial solid-phase raw materials and gaseous media for the production of metal products by the SHS method are scientifically substantiated. Particular attention is paid to the practically important processes of reduction to metal of natural iron oxide raw materials (Olenegorsk superconcentrate) and nickel dichloride, a product of chlorination of ores containing nickel sulfide. On the example of solid nickel dichloride, technological operations and methods for controlling the complete removal of crystalline water from chloride raw materials are described and argued. Conditions have been established, including the particle size of the initial solid chloride, which provide minimal diffusion complications of reduction to metal with methyldichlorosilane vapors.
The thermodynamic and kinetic aspects of the various metals compounds (M = Ni, Fe, Cu) reduction in SHS conditions are analyzed. It is shown that the stoichiometric coefficients of the overall reaction of the reduction of nickel dichloride in ammonia calculated by the thermodynamic modeling method correspond to the experimental data. It was found that the reduction kinetics of nickel, copper, and iron in ammonia, monosilane, methane, and methyldichlorosilane in SHS conditions obey topochemical equations. With recovery degrees α up to 0.7-0.8, the process is satisfactorily described by the Roginsky – Schultz equation. For α> 0.8, the experimental data are better approximated by the “shrinking sphere” equation in linear form.
Reduction in SHS conditions is described by equations known for traditional reducing gases (H2, CO), which gives an additional argument in favor of the developed ideas about the SHS mechanism. Implementation of models for the heterogeneous reactions occurrence corresponding to the above topochemical equations indicates that ultrathin (submonolayer) films of hydride reagents chemisorbed on the metal during SHS do not seriously affect the kinetics of the reduction to metal. Thus, the role of reducing agent chemisorption is shown not only in the mechanism of metal formation, but also in the formation of the surface of a metal product, which is important to take into account when reducing with the simplest hydrides (NH3, CH4, SiH4) and their derivatives. The use of treatment with methyldichlorosilane vapor at the first stage of the iron oxide raw materials reduction makes it possible to carry out a deep complex processing of raw materials and facilitate the complete reduction of iron to metal at the final stage in a methane (natural gas) environment in SHS conditions. In fact, by varying the hydride reducing agents and the program for processing the initial solid-phase raw materials by them, it is possible to obtain metal products and dispersed materials of a new generation with controlled surface chemistry and the necessary performance characteristics (corrosion resistance, anti-friction effect, etc.). An innovative combination in the surface layer of similar metal products of roughness at the micro- and nanoscale [12, 19] during chemisorption of hydrophobic reducing agents makes it possible to obtain superhydrophobic dispersed metal products that are practically not wetted by water (the value of moisture sorption does not exceed 0.1 monolayer of water molecules).
References
- Konchus D.A., Sivenkov A.V. A surface structure formation of stainless steel using a laser. Materials Science Forum. 2021. Vol. 102, p. 112-118. DOI: 10.4028/www.scientific.net/MSF.1022.112
- Ponomarenko T., Resheva E., Mosquera A.P. Urbano Assessment of Energy Sustainability Issues in the Andean Community: Additional Indicators and Their Interpretation. Energies. 2022. Vol. 15. Iss. 3, p. 1077. DOI: 10.3390/en15031077
- Quiroz Cabascango V.E., Bazhin V.Yu. Nickel oxide reduction in CO/CO2 gas mixtures in reverberatory furnaces. IOP Conference Series: Metrological Support of Innovative Technologies. 2020. Vol. 1515. N 022028. DOI: 10.1088/1742-6596/1515/2/022028
- Schenck J. Lungen H.B. Potentials of direct and smeltiny reduction processes for an efficient application in Europe. Chernye Metally. 2017. N 2, p. 25-31 (in Russian).
- Duarte P., Becerra J. Production of high-carbon directly reduced iron at Tenova Hyl. Chernye Metally. 2016. N 6, p. 24-30 (in Russian).
- Slobodov A.A., Syrkov A.G., Yachmenova L.A. et al. Effect of Temperature on Solid-state Hydride Metal Synthesis According to Thermodynamic Modeling. Journal of Mining Institute. 2019. Vol. 239, p. 550-555. DOI: 10.31897/PMI.2019.5.550
- Pleskunov I.V., Syrkov A.G. Development of research of low-dimension metal-containing systems from P.P.Weymarn to our days. Journal of Mining Institute. 2018. Vol. 231, p. 287-291. DOI: 10.25515/PMI.2018.3.287
- Kushchenko A.N. Features of the formation of sorption properties and hydrophobicity of metals containing ammonium and organosilicon compounds in the surface layer: Avtoref. dis. … kand. tekhn. nauk. St. Petersburg: Sankt-Peterburgskii gornyi universitet, 2020, p. 22 (in Russian).
- Remzova E.V. Nonlinearity of chemical-physical properties of surface-modified metals and heterogeneous systems based on them: Avtoref. dis. … kand. khim. nauk. Voronezh: Voronezhskii gosudarstvennyi universitet, 2013, p. 20 (in Russian).
- Nazarova E.A. Effect of adsorption of ammonium and arganosilicon compounds on the tribochemical properties of metals (Al, Cu, Ni): Avtoref. dis. … kand. khim. nauk. St. Petersburg: Sankt-Peterburgskii gosudarstvennyi tekhnologicheskii institut, 2016, p. 20 (in Russian).
- Syrkov A.G., Yachmenova L.A., Nazarova E.A. et al. Patent № 2570599 RF. Method for obtaining surface-nanostructured metal material. Publ. 10.12.2015.
- Abouhov M.G., Kovgan P.A. Chloric Metallurgy and Potentials of Reduction of Influence on Environment. Ecology and Industry of Russia. 2009. N 1, p. 10-13 (in Russian).
- Kovgan P.A., Abuov M.G., Edilbaev A.I., Zadiranov A.N. Perspective Direction of Modem Metallurgy – Chloride Metallurgy. Foundry Production аnd Metallurgy. 2009. N 3, p. 321-324 (in Russian).
- Quiroz Cabascango V.E., Bazhin V.Yu. Combustion optimization in gas burners of reverberatory furnaces during the melting of nickel alloys. International Conference on Complex equipment and quality control laboratories (CEQCL), 14-17 April 2020, Saint Petersburg, Russian Federation. Journal of Physics: Conference Series. 2021. Vol. 1728. N 012019. DOI: 10.1088/1742-6596/1728/1/012019
- Brichkin V.N., Vorobiev A.G., Bazhin V.Yu.Mining Institute’s metallurgists: a tradition serving the Country, science and production industry. Tsvetnye Metally. 2020. N 10, p. 4-13 (in Russian). DOI: 10.17580/tsm.2020.10.01
- Brichkin V.N., Sizyakov V.M., Oblova I.S., Fedoseev D.V. Industrial synthesis of finely-dispersed aluminum hydroxide in processing of aluminic raw materials. Tsvetnye Metally. 2018. N 10, p. 45-51 (in Russian). DOI: 10.17580/tsm.2018.10.06
- Slobodov A.A., Ralis R.V., Uspenskii A.B. et al. Development of quality criteria for systems and databases of thermodynamic data for the study of multicomponent physical and chemical natural and technological systems. Izvestiya Sankt-Peterburgskogo gosudarstvennogo tekhnologicheskogo instituta. 2015. N 31 (57), p. 8-12 (in Russian).
- Roduit B., Hartmann H., Folly P. et al. Prediction of thermal stability of materials by modified kinetic and model selection approaches based on limited amount of experimental points. Thermochim Acta. 2014. Vol. 579, p. 31-39. DOI: 10.1016/J.TCA.2014.01.005
- Chistyakov D.G., Golubev V.O., Sizyakov V.M., Brichkin V.N. Raw material composition at rusal achinsk and its impact on the production indicators. Tsvetnye Metally. 2020. N 10, p. 27-34 (in Russian). DOI: 10.17580/tsm.2020.10.04
- Shakhnazarov K.Y. Property Anomalies of Unalloyed Pre-Eutectoid Steel Melts at ~0.5 % C as a Consequence of the Intermediate Fe42C Phase. Steel in translation. 2020. Vol. 50. Iss. 4, p. 261-265.
- Ralys R.V., Uspenskiy A.A., Slobodov A.A. Deriving properties of low-volatile substances from isothermal evaporation curves. Journal of Non-Equilibrium Thermodynamics. 2016. Vol. 41. Iss. 1, p. 3-11. DOI: 10.1515/jnet-2015-0030
- Motovilov I.Yu., Luganov V.A. High temperature hydrolysis of iron(II) chloride. Gornyi zhurnal Kazakhstana. 2016. N 1, p. 41-46 (in Russian).
- Motovilov I.Y., Luganov V.A., Mishra B., Chepushtanova T.A. Oxide powders production from iron chloride. CIS Iron and Steel Review. 2018. Vol. 15, p. 28-32. DOI: 10.17580/cisisr.2018.01.06
- Rotaru A. Discriminating within the kinetic models for heterogeneous processes of materials by employing a combined procedure under TKS-SP 2.0 software. Journal of thermal analysis and calorimetry. 2016. Vol. 126, p. 919-932. DOI: 10.1007/s10973-016-5584-6
- Vigdorovich V.I., Aleksashina E.V. Kinetics of Real Heterogeneous Processes and Nano Condition of Substance. Transactions of the TSTU. 2010. Vol. 16. N 3, p. 664-676 (in Russian).
- Kim S., Suzuki J., Gao X. et al. A Kinetic Model to Simulate the Reaction Between Slag and Matte for the Production of Ferromanganese Alloy from Steelmaking Slag. Journal of Sustainable Metallurgy. 2016. Vol. 2. Iss. 2, p. 141-151. DOI: 10.1007/s40831-016-0042-z
- Bogusz A., Masset P.High Temperature Diffusion Processes at the Metal/Slag Interface. Defect and Diffusion Forum. 2012. Vol. 323-325, p. 115-120. DOI: 10.4028/www.scientific.net/DDF.323-325.115
- Boinovich L.B. Superhydrophobic coatings – a new class of polyfunctional materials. Vestnik Rossiiskoi akademii nauk. 2013. Vol. 83. N 1, p. 10-22 (in Russian). DOI: 10.7868/S0869587313010039
- Schellenberger F., Encinas N., Doris V., Butt H.-J. How Water Advances on Superhydrophobic Surfaces. Physical Review Letters. 2016. Vol. 116. Iss. 9. N 096101. DOI: 10.1103/PhysRevLett.116.096101
- Danilov V.P., Kuznetsov N.T., Novotortsev V.M. Scientific school of physical and chemical analysis of N.S. Kurnakov. Zhurnal neorganicheskoi khimii. 2014. Vol. 59. N 7, p. 836-839 (in Russian). DOI: 10.7868/S0044457X14070058
- Syrkov A.G., Prokopchuk N.R., Vorobev A.G., Brichkin V.N. Academician N.S.Kurnakov as the founder of physical and chemical analysis – the scientific foundation for the development of new metal alloys and materials. Tsvetnye metally. 2021. N 1, p. 77-83 (in Russian).
- Mikhailov A.V., Shakhnazarov K.Yu. Substantiation of the connection between the anomalies of the properties of alloys and the semiconductor component, as well as the features of glass formation with phase equilibrium diagrams. Sbornik nauchnykh trudov Mezhdunarodnogo seminara “Nanofizika i Nanomaterialy”, 25-26 noyabrya 2020, Sankt-Peterburg, Russia. St. Petersburg: Sankt-Peterburgskii gornyi universitet, 2020, p. 217-220 (in Russian).
- Pozhidaeva S.D., Ageeva L.S., Ivanov A.M. Comparative analysis of zinc and tin oxidation with acids at room temperatures. Journal of Mining Institute. 2019. Vol. 235, p. 38-46. DOI: 10.31897/PMI.2019.1.38
- Alexandrova T.N., Romashev A., Potemkin V. Justification of evaluation criteria of gold beneficiation ability by gravitational methods. Journal of Applied Engineering Science. 2020. Vol. 18. N 2, p. 230-237. DOI: 10.5937/jaes18-26076
- Kononova I.E., Kononov P.V., Moshnikov V.A. Atomic-molecular architectonics of porous materials under conditions of self-assembly sol-gel processes. Sbornik nauchnykh trudov Mezhdunarodnogo seminara “Nanofizika i Nanomaterialy”, 25-26 noyabrya 2020, Sankt-Peterburg, Russia. St. Petersburg: Sankt-Peterburgskii gornyi universitet, 2020, p. 170-173 (in Russian).
- Kogan V.E., Shakhparonova T.S. Rational use of science of chemistry as a factor for environmental safety and ensuring ecosystem purity. 17-th International Multidisciplinary Scientific Geoconference SGEM 2017, 29 June – 5 July 2017, Albena, Bulgaria. SGEM, 2017, p. 773-780.
- Popova A.N., Sukhomlinov V.S., Mustafaev A.S. Accounting for Interelement Interferences in Atomic Emission Spectroscopy: A Nonlinear Theory. Applied Science. 2021. Vol. 11. Iss. 23. N 11237. DOI: 10.3390/app112311237