Integrated development of iron ore deposits based on competitive underground geotechnologies
Abstract
The article presents an analytical review of the current state of the iron ore base of the ferrous metallurgy of Russia and the world, identifies the largest iron ore provinces and iron ore producers. The promising directions of development and improvement of the quality of the iron ore base of Russia and the features of the development of new deposits of rich iron ores are identified. Effective technologies for the development of rich iron ores deposits that ensure an increase in production volumes are proposed. The geomechanical justification of rational technological parameters that are easily adapted to changes in mining and geological conditions has been performed. Based on the results of field studies, the use of an elastic-plastic model with the Coulomb – Mohr strength criterion for modeling changes in the stress-strain state of an ore rock mass during mining operations is justified and recommendations for ensuring the stability of mine workings are developed. Effective engineering and technical solutions for the complex development and deep processing of rich iron ores with the production of fractionated sinter ore, which increases the efficiency of metallurgical processes, the production of high-grade iron oxide pigments and iron ore briquettes, which increase the competitiveness of iron ore companies and the full use of the resource potential of deposits, are presented.
Introduction
There are iron ore deposits in 98 countries with estimated resources of 790.9 billion tons. Estimated reserves are 464.24 billion tons, and confirmed reserves are 206.9 billion tons [2, 4].
According to the US Geological Survey (USGS), in 2019, global iron ore production amounted to 2.5 billion tons. The largest producers of iron ore raw materials are Australia, Brazil and China, Russia ranks fifth (Australia – 930, Brazil – 480, China – 350, India – 210, Russia – 99 million tons). Figure 1 shows countries with production of more than 1 million tons.
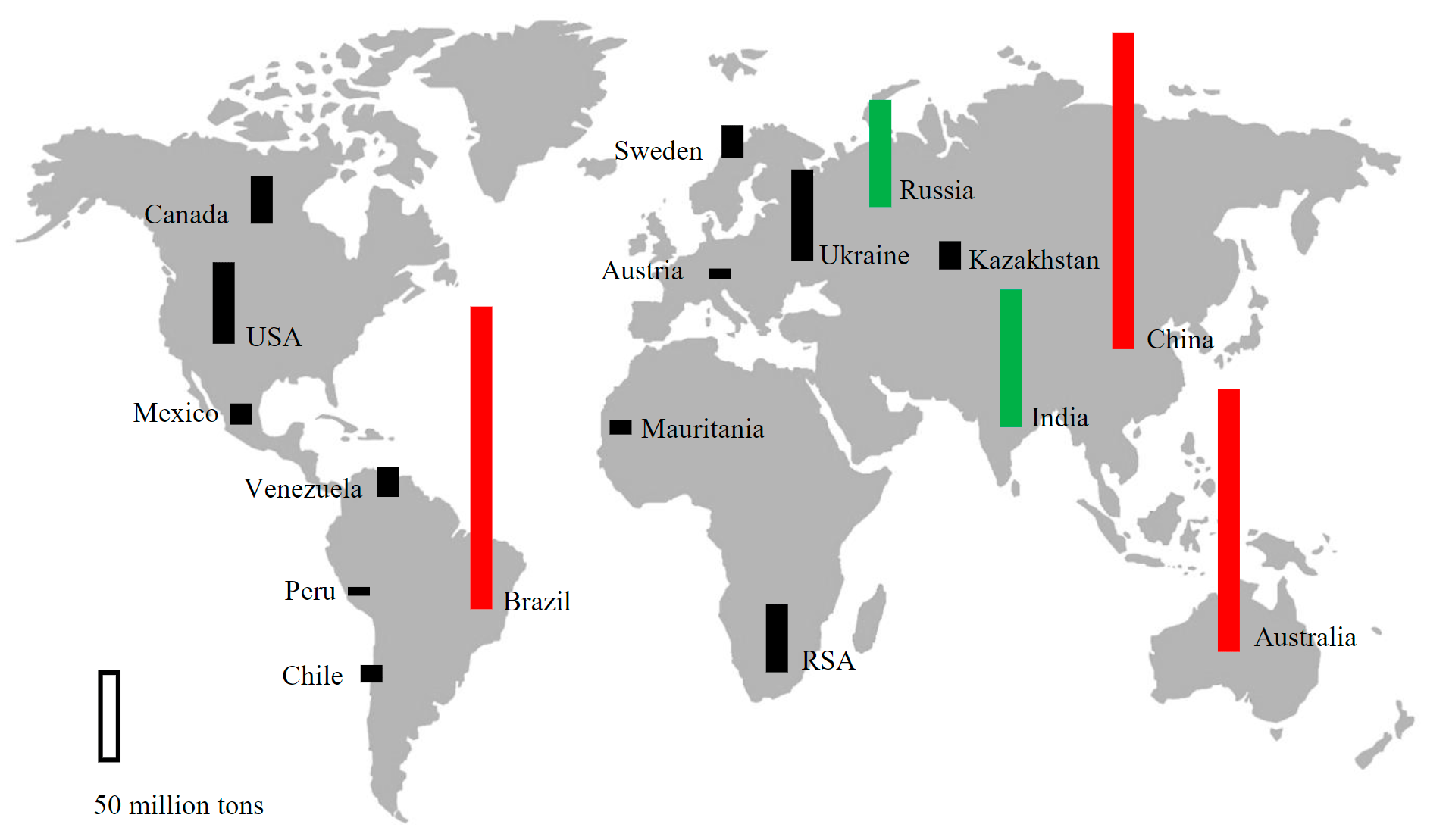
Fig.1. Iron ore mining
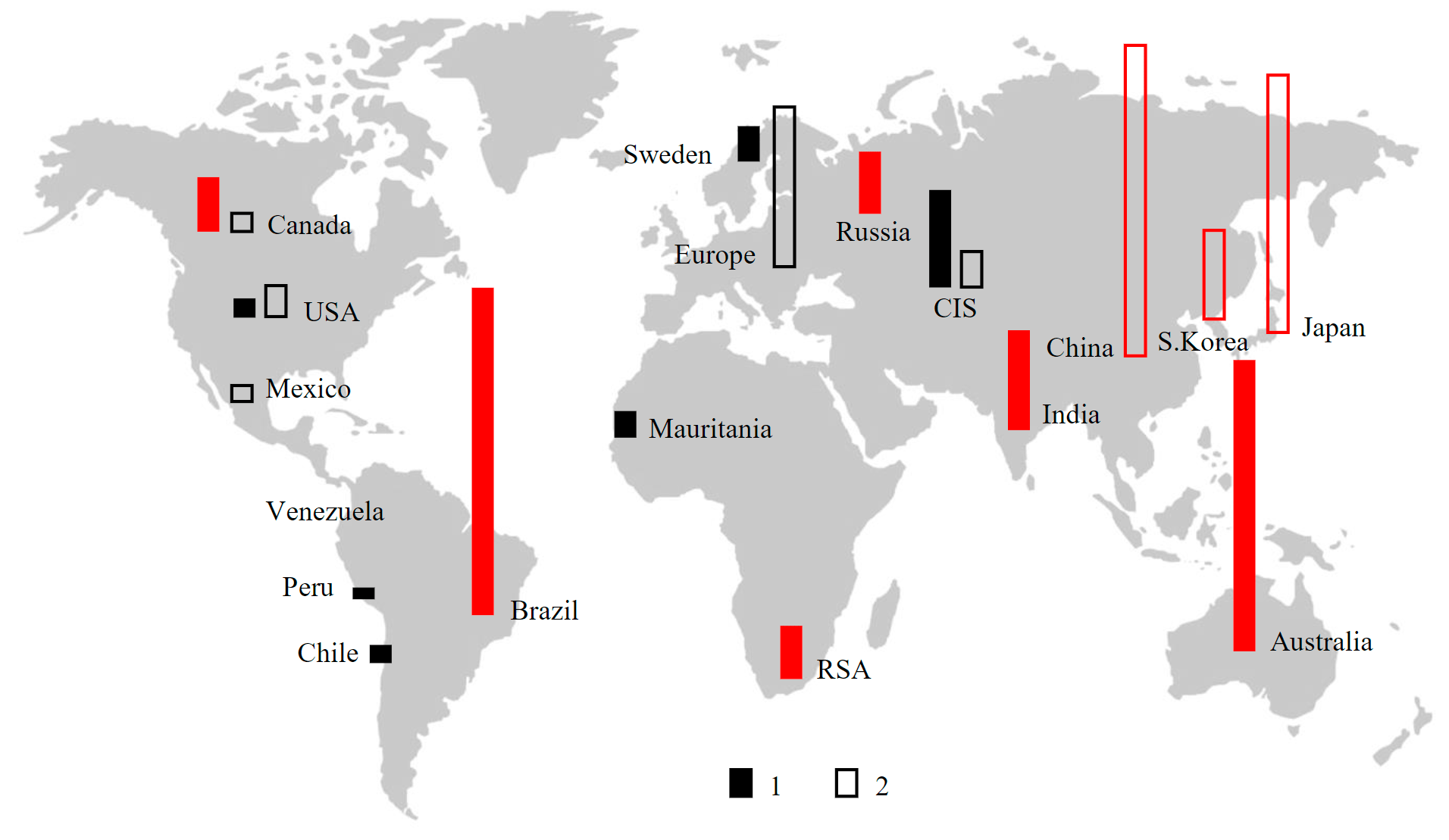
Fig.2. Export (1) and import (2) of iron ores
The largest producers of iron ore (China, Brazil, Australia) produce 65 % of the world's production, the share of Russia is 5.7 % (Fig.2). Poor and medium-quality ores with an iron content of 16-40 % account for 87.5 % of the proven reserves [7, 8, 21].
In Australia, with reserves of 32.2 billion tons (10.4 % of the world's reserves), 90 % of iron ore is concentrated in the provinces of Pilbara and Hamersley, the deposits of which are developed by open-pit mining with high ore quality (from 55 to 64 % iron). The leading companies BHP Billiton and Rio Tinto, which develop the Paraburdu, Mount Welbeck, and Mount Tom Price mines, have 16 iron ore deposits, 4 port terminals and a 1,700 km long railway network. BHP Billiton has its capital assets in Western Australia. In particular, the WAIO complex includes 5 mines and 4 processing enterprises.
Brazil has reserves of 17 billion tons (6.4 % of the world) with production centers of Carajas and Itabira and large deposits of Pico di Itabiritu, Timpopeba, Conceisan. The main producer of iron ore with a high iron content (up to 60 %) in Brazil is the Vale company with an annual production volume of more than 350 million tons.
China has reserves of 9 billion tons (5.2 % of the world's reserves) with the main deposits in the east of the country, most of which are small. More than 2 thousand deposits are being developed with an average iron content of 32-33 % and an increased content of harmful impurities – phosphorus and aluminum. The main producers of iron ores in China are Shougang Group, Gangcheng Group, Tangshan Iron & Steel, China Iron, Anshan Iron and Steel Group Corporation [8].
In Russia, iron ore reserves amount to 43 billion tons (16.9 % of the world's), which is the highest in the world [9]. The richest iron ore province in the world – the Kursk magnetic anomaly includes 4 ore regions: Mikhailovsky, Belgorod, Oryol and Oskol [10]. Both poor ores (with an iron content of 32-38 %) and rich ores (up to 68 %) are deposited on their territory. The KMA deposits are being developed by Metalloinvest, NLMK, Severstal and KMAruda. Metalloinvest produced 40.2 million tons of iron ore, 28.1 million tons of pellets and 7.9 million tons of HBI/DRI in 2019; Stoilensky – 18 million tons of concentrate, 1 million tons of sinter ore and 7 million tons of pellets; KMAruda – 4.8 million tons of iron ore and 2.1 million tons of concentrate.
Severstal owns the Yakovlevskiy deposit on the territory of the KMA, the reserves of which exceed 9 billion tons of ore with a high iron content (up to 68 %) and a low percentage of sulfur and phosphorus. The Yakovlevskiy produces sintering and blast furnace iron ore with a production volume of 1.5 million tons in 2019. By 2023, the plant plans to produce up to 5 million tons of ore per year.
Along with the unique KMA deposits in Russia, there are several other large iron ore provinces. The West Siberian basin with total reserves of 2 billion tons, on the territory of which the Bakcharsky, Kolpashevsky, Parabel, Chuzik and Parbigsky ore nodes are allocated, is developing 15 deposits, mainly represented by magnetite skarn ores with an iron content of 20 to 60 %. Several large ore nodes with total iron ore reserves of 2.8 billion tons have been identified in Karelia and the Murmansk Region. The Ural iron ore region with reserves of 9.3 billion tons includes the Kachkanarsky ore node with the Gusevogorsky and Kachkanarsky deposits with total proven reserves of over 2.9 billion tons. In total, the Kachkanarsky produced 57.9 million tons of iron ore, 3.5 million tons of agglomerate and 6.2 million tons of pellets in 2019. In the East Siberian region, iron ore reserves amount to 5.1 billion tons. 14 deposits have been put on the state balance sheet, which are not being developed in the current market conditions.
In Russia, the leading iron ore regions are the Central Chernozem, Ural and West Siberian regions (Fig.3).
Formulation of the problem
With the achieved level of production, the supply of iron ore to the ferrous metallurgy in Russia is more than 200 years, but the distribution of iron ore deposits across the regions is uneven and has features that make it difficult to develop them. The iron content in the ore in Russian deposits also varies widely. Rich iron ores (more than 60 % of iron) make up only 12.5 % of the proven reserves. Therefore, deposits with poor ores (32-38 % iron) are mainly being developed, the production of which increased by 9 % per year over the past 5 years. Despite this, the demand for iron ore outstripped the supply, and prices for it in 2020 reached 118 US dollars per ton and outstripped gold prices in terms of growth rates [12].
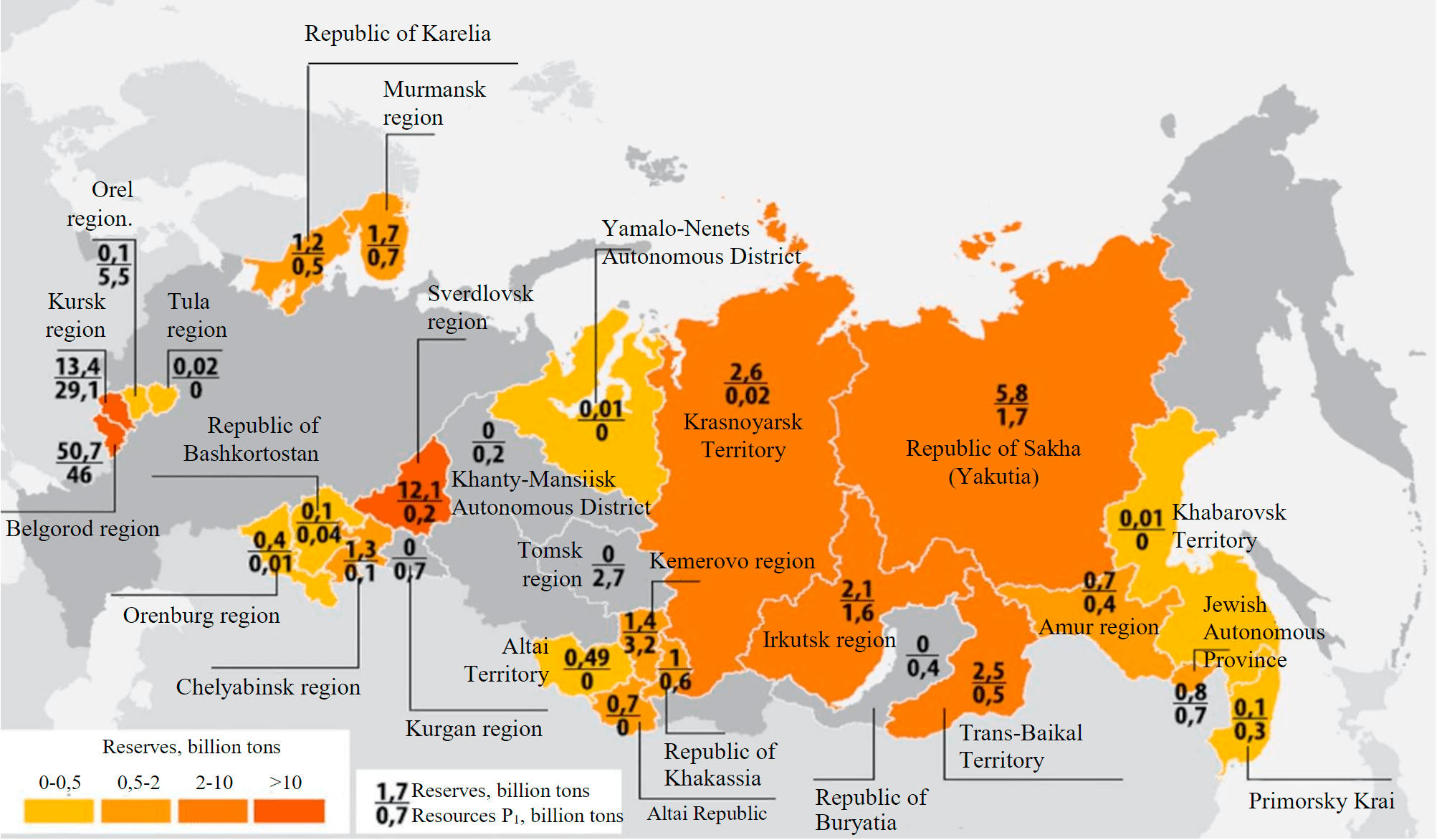
Fig.3. Reserves of iron ore raw materials by regions of the Russian Federation (category P1)
Under the current conditions, the development of rich iron ores deposits of KMA with an iron content of up to 68 % in the ore becomes a promising direction for increasing the quality of the Russia iron ore base. The first of them was the development of the Yakovlevskiy deposit with balance reserves of 9.6 billion tons, but its development at the first stage required the use of low-productivity layer systems with the stowing of the developed space, which significantly increased the cost of production [22]. This was caused by the most difficult mining and geological conditions of the deposit with low strength of rich iron ores (less than 1-2 MPa) and high porosity (up to 25 %), the presence of high-pressure aquifers in the overlying thickness and high environmental requirements in the region. To increase the productivity of stoping mining operations and reduce the cost of production, it is necessary to use more efficient development technologies with increased geometric parameters of stoping workings [28]. A positive experience was obtained at the Aikhal mine, where the transition to polygonal chambers allowed increasing the height of the exposure of the sides of the stoping chambers by 1.6-1.8 times while maintaining stability [6, 18]. When switching to such technologies a geomechanical justification of rational geometric parameters of stoping workings is required to ensure their stability.
Methodology
For the conditions of the Yakovlevskiy mine, a technology was developed and a geomechanical justification was performed for mining reserves with polygonal workings with a staggered order of their conduct (Patent N 2248448. A method for developing thick steeply dipping deposits of weak ores. Publ. 20.03.2005. Byul. N 8. Patent N 2648371. A method for developing thick steeply dipping deposits of unstable ores. Publ. 26.03.2018. Byul. N 9).
The construction of the geomechanical model was carried out taking into account the natural stress field in ore and rock masses and its changes during mining operations, the strength and deformation properties of the host rocks and ores and the decrease in their strength during moistening, the influence of the stowing and sequence of mining operations [22, 26, 31].
To minimize the influence of boundary conditions on the distribution of stresses and deformations when modeling various options for mining reserves, a section of the rock mass with dimensions of 750 m horizontally and 250 m vertically is considered. Vertically, a section with a thickness of 65 m is represented by an ore rock mass (a safety pillar), then a section of 12.5 m is a stowing rock mass.
Vertical stresses σу = 7 MPa and horizontal stresses σx = 4 MPa, determined by the results of experimental studies, are applied on the model sides [25, 26]. The physical and mechanical averaged parameters of ores and host rocks were determined by the Mining University, VIOGEM and VNIMI on the basis of laboratory and field tests (see the table) [19, 26].
According to changes in the physical and mechanical properties of ores, they are divided into three types: loose with a porosity of more than 20 % and a uniaxial compressive strength of 1.0-2.2 MPa, medium density with a porosity of 16-20 % and a tensile strength of up to 7 MPa, and dense with a tensile strength of up to 19 MPa [20]. Loose ores with an iron content of up to 68 % represent up to 60 % of the total reserves. Field studies of changes in the stress-strain state of the ore rock mass and the stability of mine workings during mining operations revealed a decrease in the resistance of the ore rock mass due to high porosity and the tendency of ores to compaction with the plastic deformations development [11, 13, 27].
The main physical and mechanical parameters of the ores of the Yakovlevskiy deposit
Parameters |
Martite ore |
Iron-micaceous-martite ore |
Hydrohematite-martite ore |
||||||
Loose |
Medium density (chloritized) |
Dense (carbonated) |
Loose |
Medium density (chloritized) |
Dense (carbonated) |
Loose |
Medium density (cledgy, chloritized) |
Dense (cledgy, carbonated) |
|
Volume weight, 10 kN/m3 |
3.64 |
3.38 |
3.40 |
3.4 |
3.4 |
3.5 |
3.2 |
3.3 |
3.45 |
Compressive strength, MPa |
1.03 |
5.8 |
20.2 |
1.25 |
5.15 |
16.6 |
2.15 |
6.95 |
19.45 |
Natural humidity, % |
12.32 |
5.03 |
5.53 |
14.3 |
3.26 |
3.8 |
– |
7.96 |
4.54 |
Specific cohesion, MPa |
0.55 |
1.55 |
5.35 |
0.45 |
1.45 |
4.35 |
0.65 |
1.85 |
5.85 |
Modulus of deformation, 103 MPa |
1.53 |
1.86 |
2.67 |
1.85 |
1.93 |
2.25 |
1.75 |
1.91 |
2.43 |
Poisson's ratio |
0.28 |
0.26 |
0.25 |
0.26 |
0.26 |
0.25 |
0.28 |
0.26 |
0.25 |
Internal friction angle, deg |
27.5 |
35.5 |
37.5 |
28.5 |
36.5 |
38.5 |
34.5 |
35.5 |
38.5 |
Porosity, % |
21.3 |
16.4 |
14.5 |
20.5 |
18.85 |
12.45 |
25.85 |
19.35 |
15.15 |
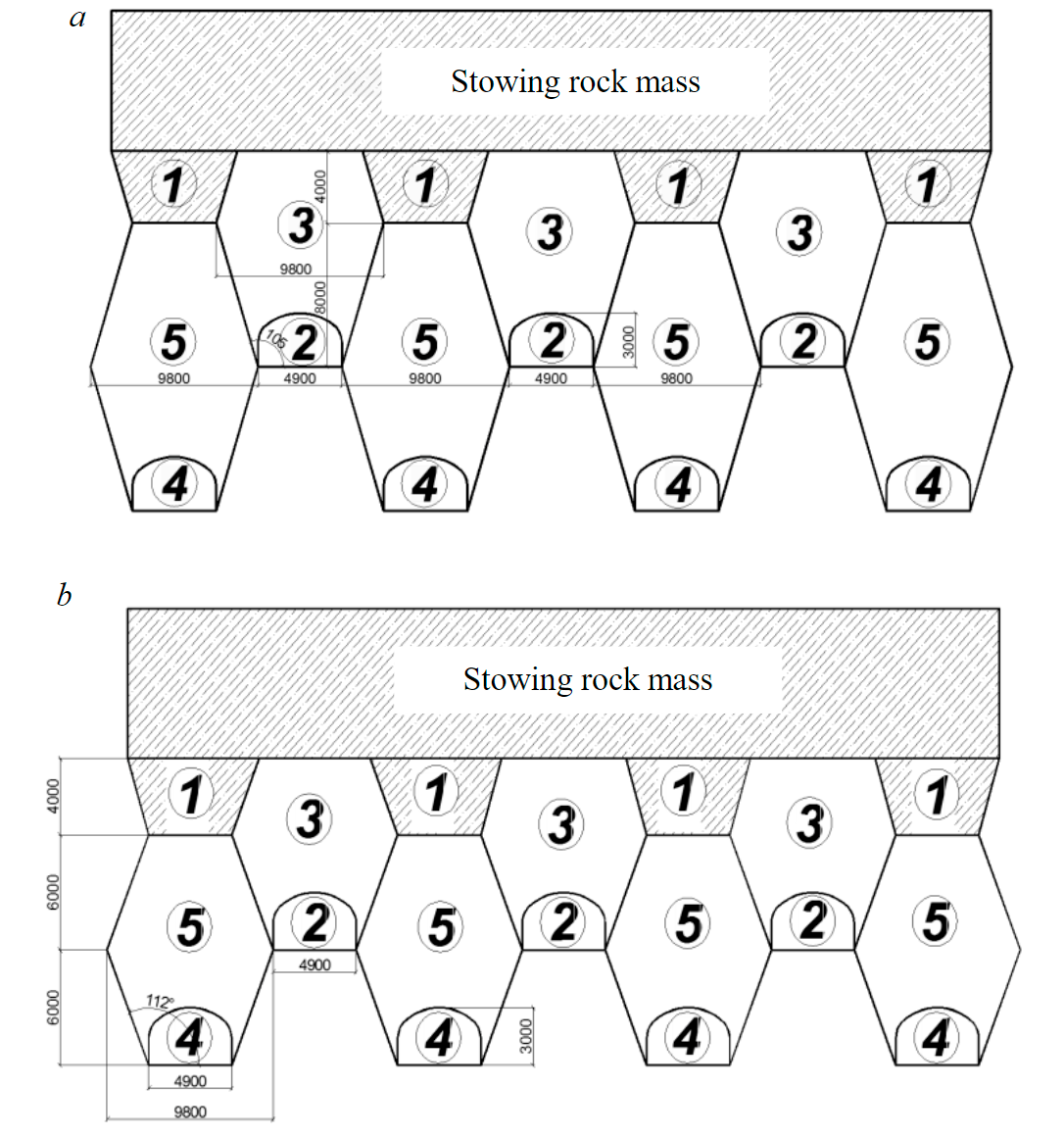
Fig.4. Scheme of ore stoping excavation with a working heightof 12 m (a); 16 m (b); 1-5 – the procedure for conducting mining operations
To describe the ore rock mass, an elastic-plastic model was adopted based on the results of field studies of the stress-strain state and stability of the ore rock mass during mining operations [21, 23].
The criterion of strength is the extreme limit state of the Coulomb – Mohr:
where τs is tangential shear stress; σ is normal stress; c is cohesion; φ is internal friction angle.
The numerical simulation was performed using the finite element method (FEM) implemented in the Simulia Abaqus software package [30]. Two variants of mining of rich iron ore reserves in descending order by polygonal stoping workings with a height of 16 and 12 m during the transition from the layered development system are considered (Fig.4). The formation of polygonal stoping workings begins with workings development at their bottom with a height of 3 m and a width of 4.9 m.
For the integrated use of the resource potential, taking into account the peculiarities of the deposit, the organization of technological chains of deep processing of extracted raw materials with the production of marketable products of a wide range is considered.
Discussion
The results of modeling the stress-strain state of iron-micaceous-martite (loose) ores rock mass during the development of reserves by polygonal shape workings with a height of 12 and 16 m are presented in Fig.5 [24].
The dependences of changes in the fields of vertical and horizontal stresses around the preparatory workings with a decrease in the level of stoping operations and an increase in the capacity of the stowing rock mass are established (Fig.6).
The maximum concentration coefficient of vertical stresses is marked at a distance of 1-2 m from the working circuit, it makes 2.75 for the second layer, and it does not exceed 1.4 for horizontal stresses. With an increase in the stowing capacity, the values of vertical and horizontal stresses in the rock mass decrease, which leads to an increase in the unloading zone of the ore rock mass and a decrease in the size of the limit state zone around the preparatory workings.
The transition to the technology of reserves extraction of dense iron-micaceous-martite and hydrohematite-martite ores is possible without fixing preparatory workings, whereas in loose and medium-density ores, the measures are required to ensure their stability. The reserves extraction of rich iron ores is carried out in a descending order by polygonal shape workings, traversed across the strike of the deposit. Adjacent floors are shifted by half the width of the workings, in the roof of which they leave an under-stowing and form ventilation-stowing orts for airing the chambers due to a general depression. After working out the sublevel, the orts are laid.
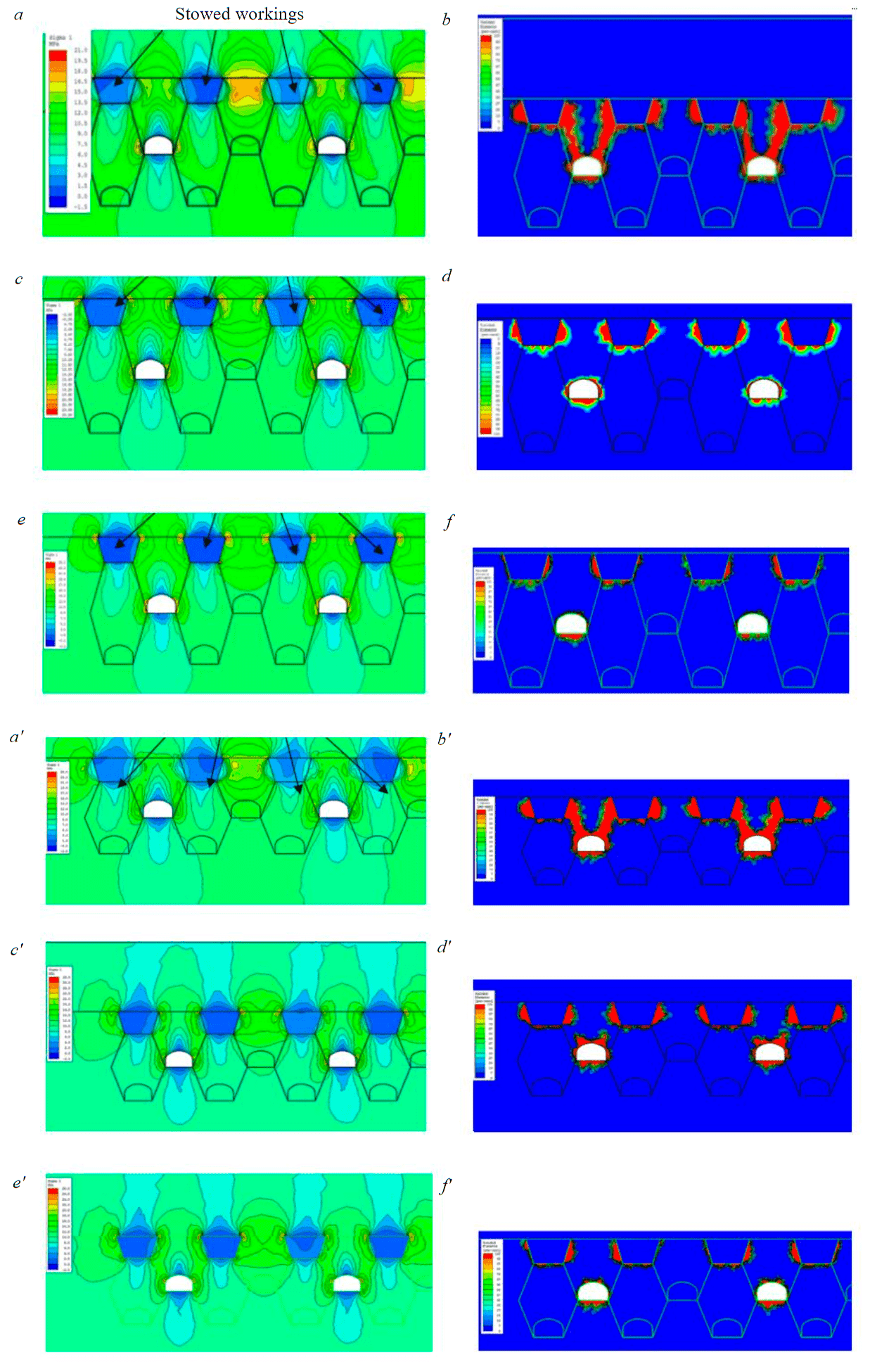
Fig.5. Distribution of normal maximum stress fields in the ore rock mass and formation of limit state zones at the height of the stoping workings of 12 m (a-f) and 16 m (a'-f' ) a, b, a', b' – loose ores; c, d, c', d' – medium density ores; e, f, e', f' – dense ores
With this development technology, the efficiency and safety of mining operations are increased by ensuring the stability of the prepared mine workings and eliminating the presence of workers in the stowing face. The volume of mining and preparatory work is reduced, losses and dilution of ores are reduced, the ventilation scheme is simplified due to the general mine depression and the rejection of the dead-end scheme.
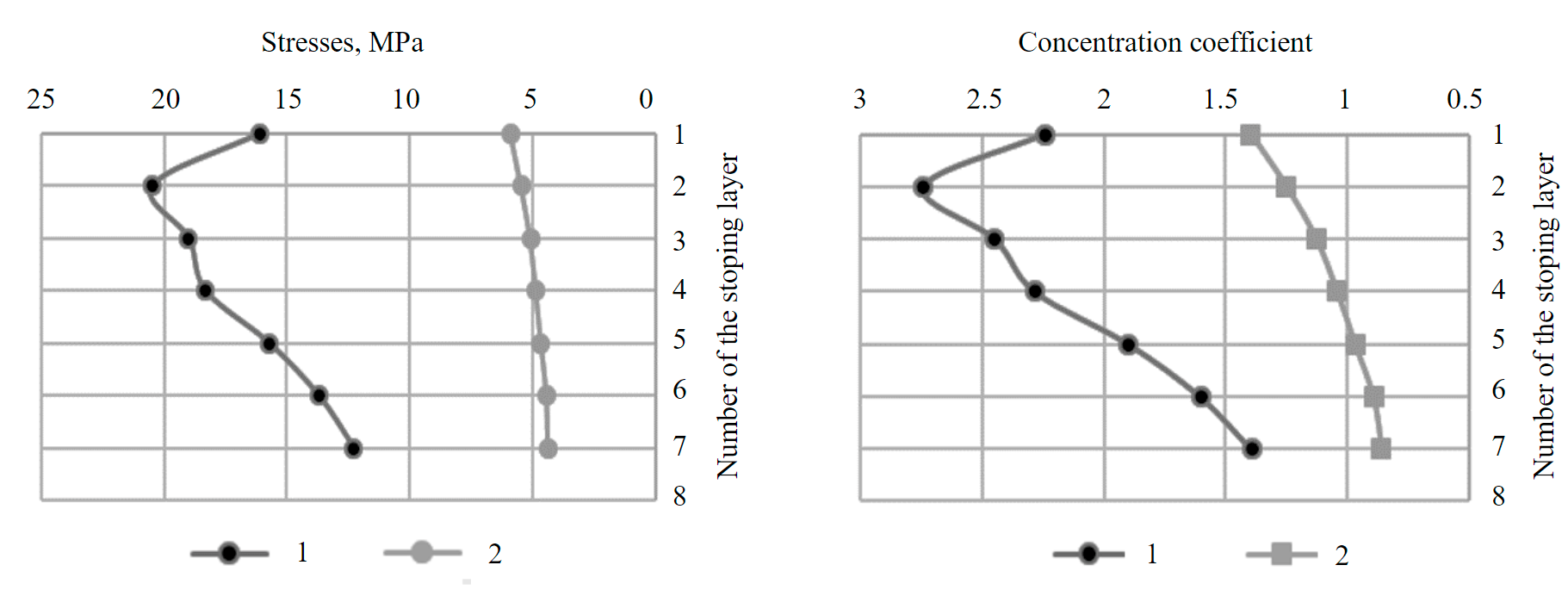
Fig.6. Dependence of the influence of the mining operations depth on the change in the magnitude and concentration coefficient of vertical (1) and horizontal (2) stresses
The technology easily adapts to changes in mining and geological conditions and market conditions due to the possibility of selective ore extraction and quality management of ore flows.
In order to increase the competitiveness of the Yakovlevskiy deposit development, the effective technologies for complex processing of iron ore raw materials have been developed, including: production of iron-rich fractionated sinter ore with high clumping properties; fine grinding of ore with a developed classification system and briquetting by a non-firing method to obtain high-grade pigments and iron ore briquettes; production of three types of mineral waters and mixtures of weakly magnetic iron ores used for balneological purposes.
It has been experimentally established that the sinter ore of the Yakovlevskiy deposit has unique properties, providing not only an increase in the iron content in the agglomerate and a reduction in harmful impurities, but also an improvement in the gas permeability of the agglomeration charge (Patent N 2552218. A method for preparing the agglomeration charge for sintering. Publ. 10.06.2015. Byul. N 16).
An increase in the amount of fractionated sinter ore in the mixture with the concentrate by 10-30 % reduces the gas-dynamic resistance of the charge by 3-4 times, opening up the possibility of a radical increase in the sintering speed and an increase in the productivity of sintering machines by 50 %. The physical and mineral structure of the sintered mass becomes more perfect. The strength of the agglomerate increases. Fuel burns out more completely and its consumption decreases. The productivity of blast furnaces increases by 5-10 % with the saving of expensive coke, which is the basis for increasing the economic efficiency of production and production of high-grade metallurgical products [1, 3, 13, 17].
The production of natural iron-oxidized pigment and briquettes from ore involves its crushing and grinding, wet magnetic separation and ultrasonic oxidative destruction, and then the main and at least two classifications to obtain the finished pigment (Patent N 2476468. A method for processing iron ore to produce pigment and briquettes. Publ. 27.02.2013. Byul. N 6. Patent N 2521380. A method of complex processing of martite-hydrohematite ore. Publ. 27.06.2014. Byul. N 18). The magnetic fraction and the sands of the main classification are briquetted. Cold briquetting of ore has advantages over agglomeration and pelletizing: it does not require high-temperature processes, gives higher strength and consistency of the chemical composition of briquettes, eliminates waste and provides better transportability of briquettes [25, 26].
The value of net discounted income in the production of pigment and iron ore briquettes on an accrual basis is 2745 and 2834 million rubles, respectively. The discounted payback period for the production of red iron-oxidized pigment from the beginning of the project investment is 1.8 and 0.8 years from the beginning of briquette production.
The production of three types of mineral waters corresponding to GOST 13273-88 “Mineral therapeutic and therapeutic-table waters” is provided for by the technology of drained waters utilization of the Yakovlevskiy deposit for subsequent use in the treatment of a wide range of gastrointestinal diseases and purification of the body from heavy metals and radionucleides [5, 14]. The use of mineral waters for therapeutic drinking, for baths and swimming pools in combination with methods of magnetobalneology based on mixtures of weakly magnetic ores allows the development of spa treatment.
The use of large amounts of data about the deposit and indicators of technological processes during its development with the creation of “digital twins” allows to move to the digital transformation of production and significantly improve the technical and economic indicators of iron ore enterprises [29].
Conclusion
Promising areas of technological development and increasing the competitiveness of the iron ore industry are the transition to digital technologies the most complete use of the resource potential of deposits with a high iron content in ore and complex deep processing of iron ore raw materials with the release of marketable products.
The implementation of the concept of complex processing of iron ore raw materials and rational use of the resource potential of the Yakovlevskiy deposit with the production of marketable products of a wide range has shown high economic efficiency.
Further research is planned to continue in the direction of optimizing production processes in general and improving technological indicators of production, ensuring high competitiveness of iron ore enterprises on the world market.
References
- Aleshin E.A. Mathematical model of a charge gas permeability function from its moisture in the agglomerate production. Vestnik Yuzhno-Uralskogo gosudarstvennogo universiteta. 2010. N 2, p. 37-40 (in Russian).
- Yushina T.I., Petrov I.M., Avdeev G.I., Valavin V.S. Analysis of state-of-the-art in iron ore mining and processing in Russian Federation. Gornyi zhurnal. 2015. N 1, p. 41-47. DOI: 10.17580/gzh.2015.01.08 (in Russian).
- Bersenev I.S., Bokovikov B.A., Klein V.I. et al. Gas-dynamic features of the initial sinter burden layer. Stal. 2010. N 9, p. 16-18 (in Russian).
- State report “On the state and use of mineral resources of the Russian Federation in 2018”. Moscow: Vserossiiskii NII mineralnogo syrya imeni N.M.Fedorovskogo, 2019, p. 424 (in Russian).
- Dashko R.E. Mineral water of the Yakovlev deposit of high-grade iron ores (KMA): diagnostics and usability. Izvestiya vysshikh uchebnykh zavedenii. Geologiya i razvedka. 2016. N 1, p. 33-38 (in Russian).
- Dik Yu.A., Kotenkov A.V., Tankov M.S. Geomechanical justification of a chamber development system with a “mine” location of diamond-shaped chambers and the stowing of the developed space. Gornyi zhurnal. 2014. N 9, p. 41-45 (in Russian).
- Iron ore mining in the world and in Russia. Portal for subsurface users dprom.online – 2020. URL (date of access 10.03.2021).
- Iron ore mining in the world. Industrial portal PROMZN.RU – 2017. URL (date of access 11.03.2021).
- 9. Iron ore mining in Russia, the largest deposits and development methods. 2CAD Information support for the mining industry-2021. URL (date of access 12.03.2021).
- Iron ores of Russia. 2017. Business portal NEDRADV – 2017. URL (date of access 12.03.2021).
- Zubov V.P., Malyutin A.S. Increasing the concentration of mining operations during the development of the thick steeply dipping ore bodies by the flatback cut-and-fill method. Gornyi informatsionno-analiticheskii byulleten. 2015. N S7, p. 491-497(in Russian).
- How the iron ore market works: supply and market share (VALE, RIO) – 2021 Talkin go money. Talking of money.com. Financial Magazine – 2021. URL (date of access 12.03.2021).
- Trushko V.L., Utkov V.A., Nurgaliev D.F. et al. To the Problem of the Prospect for the Development of the Sintering Process. Chernaya metallurgiya. 2015. N 7 (1387), p. 45-50 (in Russian).
- Korotkov A.I., Timchenko A.A. The problem of using the waters of the ore-crystalline aquifer for balneological purposes. Journal of Mining Institute. 2006. Vol. 168, p. 223-230 (in Russian).
- Kuskov V.B., Kuskova Ya.V., Kornev A.V. Preparation of iron-bearing materials to metallurgical processing stage. Obogashchenie rud. 2011. N 5, p. 38-40 (in Russian).
- Kuskov V.B., Kuskova Ya.V. Development of technology for the iron oxide pigments production. Metallurg. 2010. N 3, p. 70-72 (in Russian).
- Panychev A.A. Mathematical model of sintering process optimization and automation. Obogashchenie rud. 2006. N 2, p. 29-31 (in Russian).
- Dik Yu.A., Kotenkov A.V., Tankov M.S., Minin V.V., Kulminskii A.S., Arestov O.Yu. Patent N 2012112768/03 RF. A method for developing steeply dipping ore bodies with unstable ores. Opubl. 02.04.2012. Byul. N 13 (in Russian).
- Potemkin D.A. Modeling of the displacement processes of the rock mass in the descending order of the Yakovlevskiy ore body. Journal of Mining Institute. 2006. Vol. 168, p. 137-141 (in Russian).
- Potemkin D.A., Plashchinskii V.F. Parameters of the stress field in the ore-crystal rock mass before the start of mining operations. Journal of Mining Institute. 2006. Vol. 168, p. 123-126 (in Russian).
- Protosenya A.G. Modeling of geomechanical processes in an ore rock mass using a model of a physically nonlinear body. Journal of Mining Institute. 2015. Vol. 214, p. 13-21 (in Russian).
- Protosenya A.G.,Sinyakin K.G. Stress-strain condition of the ore massive within the second working modeling. Journal of Mining Institute. 2011. Vol. 189, p. 240-243 (in Russian).
- Semenov V.I., Rubchevskii Yu.I. Evaluation of stability mine’s exposures in physically nonlinear deformable ore and backfill mass of yakovlevskoye deposit. Sovremennye problemy nauki i obrazovaniya. 2015. N 1. URL (date of access 12.03.2021).
- Sozonov K.V. Stress-strain state assessment of stopes during development of the Yakovlevsky deposit. Izvestiya Tulskogo gosudarstvennogo universiteta. 2016. N 4, p. 229-234 (in Russian).
- Sozonov K.V. Transition technology from cut-and-pill method to room with filling mining. Tekhnicheskie nauki – ot teorii k praktike. 2016. N 5 (53), p. 29-36 (in Russian).
- Trushko V.L., Protosenya A.G., Dashko R.E. Geomechanical and hydrogeological problems оf the Yakovlevsky deposit development. Journal of Mining Institute. 2010. Vol. 185, p. 9-18 (in Russian).
- Barton N. Shear strength criteria for rock, rock joints, rockfill and rock masses: Problems and some solutions. Journal of Rock Mechanics and Geotechnical Engineering. 2013. Vol. 5. Iss. 4, p. 249-261. DOI: 10.1016/j.jrmge.2013.05.008
- 28. Litvinenko V.S. Advancement of geomechanics and geodynamics at the mineral ore mining and underground space development. International European Rock Mechanics Symposium (EUROCK 2018), 22-26 May, 2018, Saint Petersburg, Russian Federation. OnePetro, 2018, p. 3-16.
- Litvinenko V.S. Digital Economy as a Factor in the Technical Development of the Mineral Sector. Natural Resources Research. 2020. Vol. 29, p. 1521-1541. DOI: 10.1007/s11053-019-09568-4
- Protosenya A.G., Karasev M.A., Ockurov V.I. Introduction of the method of fine-discrete elements into the Abaqus/Explict software complex for modeling deformation and fracture of rocks. Eastern European Journal of Enterprise Technologies. 2017. Vol. 6. N 7 (90), p. 11-18. DOI: 10.15587/1729-4061.2017.116692
- Trushko V.L., Protosenya A.G., Trushko O.V. Stress-Strain Behavior of the Workings during the Rich Iron Ores Development under the Confined Aquifers. International Journal of Applied Engineering Research. 2016. Vol. 1. N 23. p. 11153-11164.