Technological aspects of cased wells construction with cyclical-flow transportation of rock
- Ph.D. Director N.A.Chinakal Institute of Mining of the Siberian Branch of the Russian Academy of Sciences
Abstract
A high-performance technology for constructing cased wells is proposed. Essence of the technology is the advance insertion of the casing pipe into the sedimentary rock mass and the cyclical-flow transportation of the soil rock portions using the compressed air pressure supplied to the open bottomhole end of the pipe through a separate line. Results of mathematical modeling for the process of impact insertion of a hollow pipe into a soil mass in horizontal and vertical settings are considered. Modeling of the technology is implemented by the finite element method in the ANSYS Mechanical software. Parameters of the pipe insertion in the sedimentary rock mass are determined - value of the cleaning step and the impact energy required to insert the pipe at a given depth. Calculations were performed for pipes with a diameter from 325 to 730 mm. Insertion coefficient is introduced, which characterizes the resistance of rocks to destruction during the dynamic penetration of the casing pipe in one impact blow of the pneumatic hammer. An overview of the prospects for the application of the proposed technology in geological exploration, when conducting horizontal wells of a small cross-section using a trenchless method of construction and borehole methods of mining, is presented. A variant of using the technology for determining the strength properties of rocks is proposed. Some features of the technology application at industrial facilities of the construction and mining industry are considered: for trenchless laying of underground utilities and for installing starting conductors when constructing degassing wells from the surface in coal deposits. Results of a technical and economic assessment of the proposed technology efficiency when installing starting conductors in sedimentary rocks at mining allotments of coal mines are presented.
Introduction. Drilling wells in sedimentary rocks is associated with a number of problems, most of which are associated with the stability of the well walls both during drilling and subsequent operation [6]. This applies to horizontal drilling during trenchless laying of underground utilities, as well as to drilling vertical degassing, exploration, and other special wells from the surface [4, 10, 12].
In the case of horizontal drilling, there are a number of technological solutions. If considering the absence of undesirable consequences there are methods that are based on the advance insertion of the casing pipe with an open bottomhole end into the sedimentary rock mass, which completely eliminates the collapse of the well walls, as well as surface deformation over the drilled area [14]. The main limiting factor in the development of such technologies is the lack of a high-performance and low-cost method for removing destroyed rock from the inner cavity of the pipe at any stage of insertion [3].
The most promising is the casing insertion technology for cyclical-flow rock removal using compressed air pressure supplied to the bottomhole through a separate line [9]. The essence of the technology is to supply compressed air to the bottomhole end of the pipe through a separate line. After the formation of a soil plug, compressed air is fed into the inner cavity of the pipe, cuts off a part of the rock and moves it to the unloading window. Cleaning cycles continue until the design depth is reached in the case of a vertical well or until the pipe exits into the receiving pit in the horizontal well.
In the long term, portioned rock removal during horizontal drilling leads to time savings: there is no need to dismantle the impact module with subsequent installation of cleaning equipment in the pit. With the vertical impact insertion of the pipe, the decisive role is played by the continuous maintenance of the borehole walls stability by combining drilling and casing operations.
This article presents the results of theoretical and experimental investigations aimed at improving the reliability of the technology for cleaning a pipe inserted in an elastoplastic mass with cyclical-flow rock removal.
Features of the process in a horizontal setting. When implementing the technology, there are the following difficulties: destruction of the transported rock portions in the process of its movement through the pipe, overconsolidation of soil rock and, therefore, the impossibility of separating a portion for transportation by the trunk pressure of the compressor.
The interaction processes of a sedimentary rock mass with a pipe, which is inserted in the rock by impacting, can be reviewed by analyzing the wave pattern of elastic wave propagation in a pipeline [1] or in a quasi-static statement of the relative displacements of the pipe, rock and total rock mass [20]. The main disadvantage of these approaches regarding the obtaining of the necessary information for solving practical problems is the lack of possibility for determining a rational and accident-free rock removal step.
To determine the removal step of the destroyed rock, mathematical modeling and calculations for the stress-strain state of the sedimentary rock mass were performed in the volumetric (three-dimensional) formulation of the problem. Dynamic computational model for the interaction of an elastoplastic mass with a hollow rigid cylinder inserted in it was built in the ANSYS. The model takes into account the physical non-linearity of the medium behavior and the non-linear nature of the interaction at the contact of the cylindrical element and the mass based on the finite element method. Structural and time analysis of the ongoing processes was carried out with the ANSYS Mechanical APDL solver [18, 19, 21, 22].
To describe the behavior of the mass, averaged indicators were used for sand clay and loam as the most common rocks in the near-surface sedimentary layer: density – 1980 kg/m3, Young's modulus of elasticity – 40 MPa, Poisson's ratio – 0.3; parameters of the Menteri – Vilam model based on the theory of plastic flow: uniaxial compression strength – 9850 Pa, uniaxial tension – 2250 Pa, biaxial compression – 10 kPa, dilatancy angle – 0.25 rad. To describe the pipe, the following indicators were used: density – 7850 kg/m3, Young's modulus of elasticity – 200 GPa, Poisson's ratio – 0.3, tensile and compressive yield strength – 250 MPa, tensile strength – 460 MPa [5, 16, 17, 23].
The calculation is made for pipes with the diameter of 325-730 mm, impact energy 2-6 kJ and average physical and mechanical properties of the rock mass. In all calculations, the wall thickness is assumed 8 mm, and the impact frequency is 100 min–1. The specified range of diameters and impact energies covers practically the entire area of trenchless operations application. Calculation scheme and the division of the model into finite elements are shown in Fig. 1.
The following conditions are accepted as boundary: rigid fixation of the foundation and side walls of the model, contact conditions at the interface between the media of the annular cylindrical element – mass, gravity force, constant static pressure and a series of impacts on the outer end of the annular cylindrical element. In the calculation, it is assumed that at the initial moment of time, the ring element is inserted into the mass to a depth of two pipe diameters, while the surface of the mass inside coincides with the outer surface.
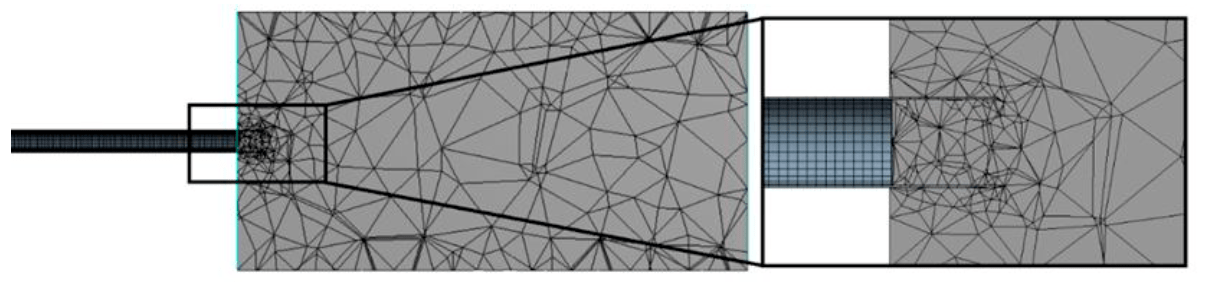
When dividing the computational area, finite elements of variable size were used. In the zone of the expected maximum gradient of deformation, the division was the smallest and increased in regions with a smooth change in deformation (at the boundaries of the computational domain). At the same time, adaptive mesh rebuilding is used to ensure a balance between calculation time and solution accuracy during the advancement of the annular cylindrical element and rock forming.
Table 1 and Fig. 2 show the calculation results in the format of the ratio between the length of the cleaning step and the pipe diameter, at which the stresses in the rock at the point of compressed air supply at a distance of one pipe diameter from the end are equal to 0.6 MPa. System of relative depth measurement of the diameters of the inserted pipe is common in trenchless construction. Specified value of stresses in the rock was selected based on the energy capabilities of the majority of compressor units, the nominal pressure of which is 0.6 MPa.
Table 1
Ratio of insertion length to the pipe diameter
Pipe diameter, mm | Impact energy, J | ||
2000 | 400 | 6000 | |
325 | 6,870 | 7,914 | 10,010 |
426 | 7,317 | 9,206 | 11,363 |
530 | 8,196 | 9,975 | 12,545 |
630 | 11,775 | 13,555 | 14,647 |
730 | 14,585 | 16,770 | 17,299 |
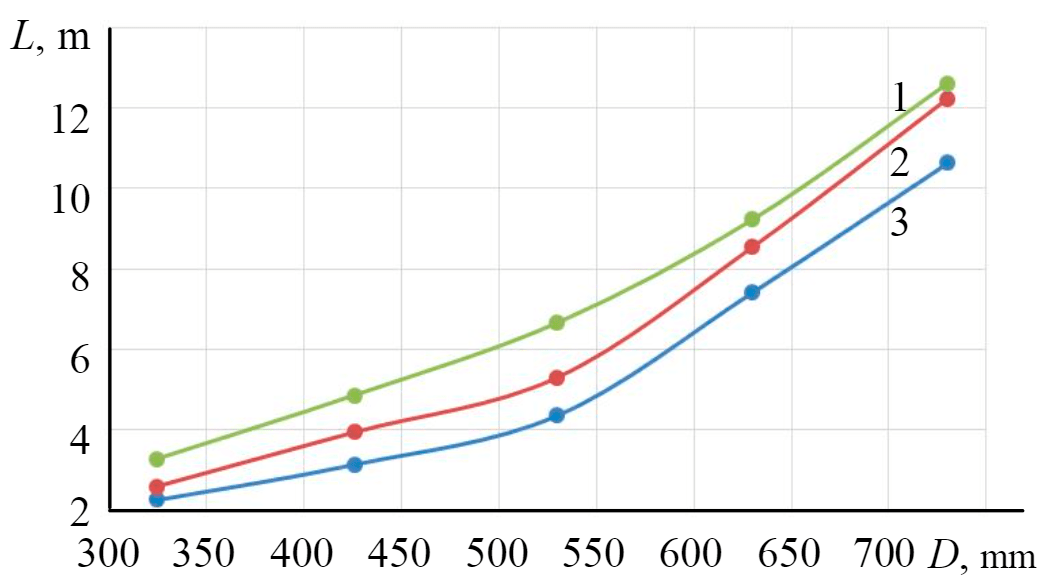
It is seen that a threefold increase in energy leads to an insignificant increase in the cleaning step. Consequently, the ratio of the impact energy and the dimensions of the inserted pipe should be selected only from the position of the guaranteed insertion of the casing pipe to a given depth. The L/D cleaning step increases almost linearly with the diameter of the inserted pipe.
Using the results from Table 1, it should be taken into account that they were obtained for averaged sand clay and loam, as the most common rocks in the near-surface sedimentary layer. It is impractical to carry out a lot of calculations, since the variety of soil types is great and the properties can vary greatly even along the length of one trenchless crossing. When preparing the starting and receiving pits, it is necessary to determine the type of developed soil by the express method, and, if necessary, make an adjustment: if sand particles predominate, then the insertion step should be increased by 1-2 pipe diameters; if there are more clay particles, then the step must be reduced by the same amount.
Features of the process in a vertical setting. In the vertical setting, rock removal is much easier, since the rock is uniformly compacted throughout the entire cross-section, and in the case of working chamber depressurization and loss of the piston effect, the rock falls to the bottomhole and becomes the head of the next portion. Problems arise in determining the impact energy that is sufficient to insert the pipe to the required depth.
The statement of the problem for vertical pipe insertion is similar to the horizontal one. Impact pulse is generated by dropping a load onto the free end of the pipe from a given height. Calculation was made for pipes with a diameter of 325-730 mm, impact energy 2-45 kJ. Pipe length is 72 m, the wall thickness is 8 mm, pipe is smooth along its entire length (no welds). Rock 0.5 m high is inside the pipe. It is assumed that the soil is homogeneous throughout the depth.
For each impact energy, the deviation value (mm) per impact was determined for a pipe length in soil of 15, 40 and 65 m (Table 2).
Performed calculations allow estimating what impact energy will be sufficient to insert the casing conductor to a given depth in the sedimentary rock mass. At the same time, in the earlier stages of insertion, the displacements will be much higher. Calculation results are confirmed by the data for the practical application of the technology for installing the starting conductors, set forth in [15].
Table 2
Dependencies of the deviation for one impact blow for pipes of different diameters at given impact energies
Pipe diameter, mm | Impact energy, J | ||||||||
10000 | 25000 | 45000 | |||||||
Pipe length, m | |||||||||
15 | 40 | 65 | 15 | 40 | 65 | 15 | 40 | 65 | |
325 | 5,537 | 0,746 | 0,277 | 13,411 | 1,649 | 0,638 | 25,967 | 3,191 | 1,271 |
426 | 4,447 | 0,535 | 0,202 | 9,811 | 1,378 | 0,498 | 18,810 | 2,537 | 0,950 |
530 | 3,431 | 0,435 | 0,171 | 8,408 | 0,991 | 0,379 | 15,280 | 1,936 | 0,748 |
630 | 2,947 | 0,370 | 0,137 | 6,495 | 0,868 | 0,346 | 12,854 | 1,715 | 0,642 |
730 | 2,413 | 0,326 | 0,123 | 5,861 | 0,786 | 0,301 | 10,977 | 1,435 | 0,572 |
Technical and economic indicators of the proposed technology and prospects for its use. Considered technology of cased wells construction with cyclical-flow rock removal has a high potential for application in various industries related to well drilling and engineering and geological surveys.
Thus, for example, when conducting geological exploration, the proposed technology can be used for rock removal both in the form of solid-oriented samples and in the form of sludge with a fairly accurate reference to the depth during drilling of sedimentary rocks. To solve the problems of drilling in geological exploration, additional technical and technological support will be required. Special catch boxes for obtaining solid rock samples or preventers and sleeves for rock sampling in crushed form with subsequent transportation to equipment that allows determining the petrographic composition of cut sedimentary rocks will be needed.
An additional function of applying the technology in geological exploration can be the assessment of the strength properties of rocks by the specific displacement of the casing pipe in one impact blow of a pneumatic hammer, which is determined taking into account the actual impact frequency and the energy of a single impact blow of the dynamic loading machine at control intervals of displacement. Consequently, during drilling, a change in the indicator characterizing the resistance of rocks to destruction also makes it possible to determine the boundaries of the rock transition from one category to another [8, 15].
Deviation in one impact blow
where Ki – insertion coefficient; Eim – impact energy, J; А – circumference length of the outer section of the pipe, m; Ki = f (Е, μ, ρ, σcm, σtn, δ) – coefficient that takes into account the strength, deformation, viscosity and other properties of the soil; E – Young's modulus of elasticity; μ – Poisson's ratio; ρ – density; σcm, – uniaxial and biaxial compression strength; σtn – tensile strength; δ – dilatancy parameter.
In accordance with Kп soil masses can be classified according to the applicability of the proposed method for the construction of cased wells, but at this stage of technology development, the amount of experimental data is insufficient. Adequate classification is possible only after the full implementation of the technology in production.
Proposed technology regarding the installation of starting conductors for the construction of degassing wells (Fig.3) was tested in the conditions of the mine allotment named after S.M. Kirov JSC “SUEK-Kuzbass” [11, 15].
Application of the technology made it possible to combine drilling and casing operations, eliminating the problems of stability of the borehole walls in sedimentary rocks. Productivity of the impact insertion technology for the conductor is 54 % higher than that of the existing roller-bit technology.
Current technological cycle for the construction of degassing wells includes cementing of the annulus at all stages. Technological break for cement hardening is 24 hours or two shifts. During this time, using the standard compressor equipment of the drilling rig, it is possible to implement the impact insertion of six casing pipes 15 m long, providing the drilling site with ready-made starting conductors for several months in advance (this is confirmed by the act “On the results of a technical and economic efficiency assessment of technologies for installing conductors in sedimentary rocks” by JSC “SUEK-Kuzbass”).
It was found that the product unit cost when using the technology for impact insertion of the conductor is less by 56 % than that of the existing technology, while the specific monetary funds spent on drilling equipment during the operation of the new technology are less by 54.7 %, the cost of wages for the drilling crew – by 47.4 %, for consumed energy carriers – by 81.5 %, which indicates a higher energy efficiency of impact insertion technology in comparison with the existing one.
In the field of construction (Fig.4), for trenchless laying of communications, the use of the technology in the batch cleaning mode allows reducing energy losses for reconsolidation of the sedimentary rock mass in the bottomhole area of the pipe and ensuring its energy efficient cutting with the casing pipe edge. Technology does not require additional means of mechanization (auger, bailer), which lead to a decrease in productivity with an increase in the length of the well. Information on the cleaning step obtained on the basis of modeling provides a rational and accident-free operation mode during the construction of wells.
It should be specially noted that, on the basis of the proposed technology, it is possible to efficiently construct cased wells in technogenic poorly connected formations, such as ash dumps, tailings, etc. In this case, the proposed technology becomes the only possible one, since it ensures the stability of the cut technogenic mass, which does not have formed natural bonds between particles.
Technical and technological solutions of the considered approach can be widespread in Russia and abroad in the implementation of borehole methods of mining, for example, uranium, gold, tin, copper, etc., in geological exploration, as well as in heap leaching technologies [2, 7, 13].
Conclusion. Based on the results of theoretical and field investigations, it was established:
• in the case of horizontal passing of the well during the preparation of the starting and receiving pits, it is necessary to use the express method to determine the type of the developed soil, and, if necessary, make adjustments – if sand particles predominate, then the insertion step should be increased by 1-2 pipe diameters, if there are more clay particles, then the step must be reduced; when implementing the technology of cyclical-flow removal, the longest possible portion should be formed;
• in the case of vertical passing of the well, the performed calculations allow estimating the impact energy needed to insert the casing conductor at a given depth in the sedimentary rock mass, while at earlier stages of insertion the displacements will be significantly higher;
• proposed technology is universal and can be used when drilling geological exploration wells with oriented rock sampling, when installing starting conductors for degassing wells, for trenchless laying of underground utilities, constructing wells in poorly connected technogenic formations and with borehole technologies for mining raw minerals.