Iron ore tailings as a raw material for Fe-Al coagulant production
Abstract
The paper presents the results of experimental research into the recovery of Fe-Al coagulant from iron ore tailings (IOTs). The variables investigated in the laboratory tests included sulphuric acid concentration, temperature, leaching time, solid/liquid phase ratio (S:L) and the presence of stirring. The experiment determined the composition of the coagulant and the solid residue after leaching. The maximum iron content in the solution after leaching was obtained using 40 % H2SO4 at a temperature of 100 °C (or with stirring at 75 °C) and a contact time of 60 minutes. In this case, the iron yield was at the level of 25 % of the total content in the iron ore tailings. Chemical analysis of the solution obtained after leaching showed Fe and Al sulphate contents of 11 and 2 % respectively. In the next step, the efficiency of the coagulant was evaluated on model solutions of colour. The experimental results showed that the coagulant obtained from the iron ore tailings can be used for wastewater treatment in a wide pH range from 4 to 12 pH units. The solid residue after leaching is a fine-grained powder rich in silica, which can potentially be used as an artificial raw material in the construction industry. The research carried out in this thesis has shown that the extraction of coagulants from iron ore tailings can be considered as a way to extend the production chain of iron ore mining and to minimise the amount of tailings to be stored in tailing ponds. The technical solution presented in this work allows to comprehensively solve the problem of environmental protection by creating new target products for wastewater treatment from IOTs.
Founding This work was carried out within the framework of the state contract of the Ministry of Science and Higher Education of the Russian Federation (FSRW-2024-0005).
Introduction
The storage of mineral processing wastes in tailings ponds has been a significant environmental problem for the mining and processing industries worldwide for many years [1]. The mineral resource sector in the Russian Federation is no exception [2-4]. Despite continuous improvements in iron ore processing technologies [5], the increase in iron ore production has led to a corresponding increase in waste generation. According to the Federal Service for Supervision of Natural Resources, by the end of 2023, approximately 2.5 billion tonnes of iron ore tailings will have accumulated in man-made massifs across the Russian Federation. Meanwhile, only about 15 % of the newly generated IOTs each year is destined for recycling. Therefore, the development of ecologically and economically efficient technologies for the secondary processing of iron ore tailings is becoming increasingly important.
According to «The scientific and technological forecast up to the year 2030», one of the main directions of current state policy is the integrated development of mineral resources and technogenic raw materials on an industrial scale. “The Strategy for the Development of the Industry of Treatment, Utilisation and Neutralisation of Production and Consumption Waste for the Period up to 2030” states that ferrous metallurgy enterprises are among the main types of industrial facilities that generate waste and use processed secondary raw materials in production. Consequently, ferrous metallurgy enterprises are fundamental to the creation of an up-dated system focused on the integration of industrial waste into the economic cycle. The expected result of this policy will be the rational use of the mineral resource base.
In order to address the challenges of iron ore tailings generation and storage, numerous researches have been carried out by scientists worldwide, focusing on the disposal and multipurpose use of IOTs. Both Russian and foreign scientists have explored the potential applications of iron ore tailings in various fields, including fertiliser production [6-8]; wastewater treatment reagents [9-11]; production of building materials – cement [12-14], concrete [15-17], materials for underground construction [15, 18, 19]; road construction [20-22].
However, most of these developments have not been applied in practice, despite the importance of addressing the environmental problems caused by operating and decommissioned technogenic facilities. This is mainly because the processing of IOTs in a market economy must be both efficient and profitable. This can only be achieved by developing zero-waste technologies that extract valuable constituents and utilise tailings to produce marketable products. The main valuable component in iron ore tailings is iron itself, due to the shortcomings of existing technologies. Currently, modern iron extraction technologies are not widely used in our country due to lack of interest from both iron ore concentrate producers and consumers.
A review of the aforementioned utilisation methods for ferrous tailings indicates that existing scientific work has not adequately explored the potential for recovering coagulants from IOTs. Coagulation is a crucial process in water treatment and industrial wastewater purification [23]. The reagents used in this process are generally divided into aluminium-based and iron-based coagulants [24]. Iron (III) salts have several advantages over aluminium salts, including higher coagulation efficiency at low water temperatures, operation over a wide pH range, and a high sedimentation rate of coagulated particles. However, over-dosage of iron-based coagulants can result in iron ions remaining in the treated water. This problem can be mitigated by adding aluminium salts either simultaneously or sequentially. Thus, mixed coagulants containing both aluminium and iron compounds provide optimal water treatment results. Analysis of the composition of tailings from various deposits, according to open sources, shows that aluminium is present in almost all such wastes at levels of a few percent [25-27]. Consequently, iron ore tailings have the potential to be used as a raw material for the production of high-performance coagulants.
Coagulants play a critical role in wastewater treatment worldwide, making the search for alternative materials for their production, including the use of iron ore tailings, an urgent task. Currently, methods for the production of iron-based coagulants from materials such as rolling mill scale, electric arc furnace dust and ferrous metallurgy slag are well known in academia and industry [28-30]. The objective of this study was to produce a Fe-Al coagulant from iron ore tailings and to evaluate its efficiency and environmental safety. To achieve this goal, a series of experimental studies were conducted at the Scientific Centre for the Assessment of Technogenic Transformation of Ecosystems, located at the Empress Catherine II Saint Petersburg Mining University.
Methods
Study of the composition and properties of iron ore tailings
In order to study the composition and properties of iron ore tailings, a composite sample was collected from the tailings dump of a mining and processing plant located within the iron ore basin of the Kursk Magnetic Anomaly. Sampling was carried out during the 2022 field season in accordance with the methodological recommendations.
In the first phase of the laboratory studies, the chemical composition of the iron ore tailings was determined by X-ray fluorescence (XRF) using the Shimadzu XRF-1800 [31]. Based on the chemical composition data, the phase composition was investigated by X-ray diffraction using the Shimadzu XRD-6000 with high temperature chamber NA1001. The phases were searched using the JCPDS international file system [31]. The granulometric analysis of the tails was carried out by laser diffraction on the Horiba LA-950 particle size analyser [32]. For a comprehensive assessment of the studied iron ore tails, the grain morphology was also studied using a JEOL JSM-7001F scanning electron microscope [33].
Obtaining a coagulant using sulfuric acid
At present, the majority of iron-containing coagulants used in industry are produced on the basis of iron chloride and iron sulphate. Considering the disadvantages of hydrochloric acid, such as high volatility, vapour toxicity and cost, in this study it was decided to focus on the leaching process using sulphuric acid. However, despite the aforementioned drawbacks, the production of iron chloride as a coagulant for the purification wastewater from iron ore tailings shows promising prospects and will be further explored by the authors in subsequent research.
The leaching process of iron ore tailings was investigated in laboratory conditions, where various factors were successively studied: acid concentration, temperature, contact time, solid-liquid phase ratio (S:L), and the presence of forced stirring. Each experiment was repeated three times to ensure statistical reliability and the final results presented in the following section are reported as averages.
Theoretical calculations were carried out to determine the amount of sulphuric acid required to dis-solve the iron present in the tailings studied, based on their chemical and phase composition and using the reaction equation:
Fe2O3 + 3H2SO4 → Fe2 (SO4)3 + 3H2O.
For example, the theoretical specific consumption of 30 % sulphuric acid to leach all the iron con-tained in the IOTs is 1 cm3/g, corresponding to an S:L ratio of 1:1. However, not all of the iron in the IOTs studied may be in an accessible and reactive form when in contact with 30 % sulphuric acid. Therefore, experiments were carried out to determine the optimum concentration of sulphuric acid for maximum extraction of iron and aluminium from the IOTs, in the range of their mass concentrations from 20 to 50 %, with an S:L ratio of 1:1. The contact time was 3 hours, without heating or stirring (t = 20 ºC).
Having selected the optimum concentration of sulphuric acid, the next stage of laboratory research focused on investigating the influence of reaction mixture temperature on the yield of iron and aluminium. Temperature is one of the key parameters in leaching reactions and significantly affects the extraction of components [34]. During the experiment, the reaction temperature ranged from 20 to 100 °C, while the contact time and phase ratio were chosen similarly to the previous experiment.
To determine the minimum contact time, leaching experiments were carried out for 15, 30, 60, 120 and 180 min. The acid concentration and temperature of the reaction mixture were set based on the results of previous experiments, while the S:L ratio was kept constant at 1:1.
In addition, a laboratory experiment was carried out with solid-liquid phase ratios of 1:1, 1:3 and 1:5 to confirm the empirically selected optimum phase ratio.
The final external factor investigated under laboratory conditions was the presence of stirring during the leaching process. Stirring significantly increases the surface area of solid particles in contact with the reagent, thereby improving the efficiency of the leaching process. Stirring was performed using an IKA KS 3000 i control laboratory shaker-incubator at a speed of 150 rpm. The experiment was carried out within a temperature range of 20 to 75 °C.
At the end of each leaching experiment, the solution was filtered through a paper filter to separate the unreacted portion of the IOTs, and the filtrate was subjected to quantitative chemical analysis using inductively coupled plasma atomic emission spectrometry on a Shimadzu ICPE-9000 instrument. The aim of this analysis was to evaluate the content of the desired components in the solution and to determine the leaching efficiency, which was determined by comparing the iron and aluminium content transferred to the solution with their content in the IOTs.
Coagulant efficiency evaluation
To test the performance of the solution after leaching, a sample obtained under the optimum leaching parameters established in the previous experimental stages was used as a coagulant.
The evaluation of the coagulation properties of the obtained Fe-Al coagulant was carried out in ac-cordance with GOST R 51642-2000 “Coagulants for domestic drinking water supply. General requirements and method for determining efficiency”. For this purpose, a model colour solution based on sodium humate was prepared. A 50 g of sodium humate was taken and placed in a 2 dm3 flask, to which 1 dm3 of distilled water at a temperature of 40 °C was added. The solution obtained was stirred and kept for 24 hours in a flask with a closed stopper, then filtered through a paper filter. The solution was then diluted with distilled water to obtain a colour equal to 50° on the standard chromaticity scale according to GOST 3351-74 “Drinking water. Methods for determining taste, odor, color, and turbidity”. The chromaticity of the model solution was determined by the spectrophotometric method using the DR5000 from HACH-LANGE. The solution obtained was used as a model colour solution to determine the effectiveness of the coagulant. In accordance with GOST R 51642-2000, the dose of coagulant that reduces the chromaticity from 50 to 20° is considered the minimum dose for the model colour solution.
To determine the minimum dose of coagulant, 1.0 dm³ of the prepared model chromaticity solution was placed in beakers, stirrers were lowered into the beakers and the stirring speed was set at 140 rpm. The samples were thermostated until the suspension reached the test temperature of (20±1) °C. Then the working solution of the coagulant was dosed into them in the range of mass concentrations from 3 to 6 mg/dm3 with a step of 0.5 mg/dm3 in terms of the basic substance (ferric oxide (III). The working solution of the coagulant was prepared by adding an aliquot of the coagulant obtained after leaching, containing 1.0 g of the main substance in terms of ferric oxide (III), to a 1 dm3 flask and making up the volume with distilled water. The model solution was stirred with the working coagulant solution for 3 min, after which the stirring speed was automatically reduced to 40 rpm and the contacting lasted another 15 min. The solution was then allowed to stand for 30 min, filtered and colour measured.
As the efficiency of the coagulant depends significantly on the pH of the treated water, the pH range in which the coagulant obtained was most efficient was determined. For this purpose, 50 cm3 of model colour solution was poured into five glass beakers. An equal dose of coagulant (6 mg/dm3) was then added to each beaker and the pH of the solution was adjusted from 1 to 12 pH units in steps of 1 pH unit using 0.1N NaOH and HCl solutions. The solutions were then stirred for 3 min and filtered. The filtrates were analysed for colour.
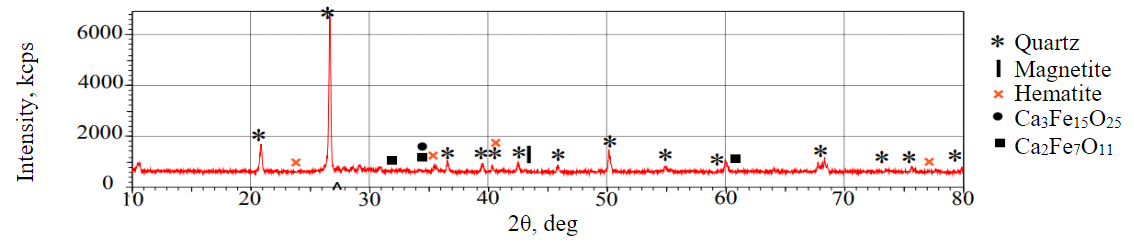
Fig.1. X-ray phase analysis of iron ore tailings
Environmental Safety Assessment of the Coagulant
In order to assess the environmental safety of the coagulant obtained, the qualitative and quantitative identification of matrix and impurity components in the coagulant composition was performed using atomic emission spectrometry on a Shimadzu ICPE-9000. Qualitative and quantitative identification of matrix and impurity components in the coagulant composition was performed by atomic emission spectrometry on the ICPE-9000 of Shimadzu company. Secondary contamination of treated water as a result of coagulant use was then evaluated by chemical analysis of the model colour solution before and after coagulant use. The model solutions were also analysed by atomic emission spectrometry. The results obtained were interpreted by comparing the concentrations of the constituents with the approved water quality standards.
Study of the solid precipitate after leaching
After the leaching products were filtered, a solid precipitate remained on the filter, representing the unreacted portion of the IOTs. The sludge on the filter was washed with distilled water and then air dried. In order to assess the prospects of its further use in industry as a technogenic material, its chemical and particle size distribution was studied by the methods used in the work on the analysis of initial samples of iron ore tailings and described above.
Results discussion
The chemical composition of iron ore tailings according to RFA data: SiO2 – 69.0; Fe2O3 – 18.0; MgO – 4,1; CaO – 3.2; Al2O3 – 2.0; K2O – 0.73; Na2O – 0.62; P2O5 – 0.21; MnO – 0.089; TiO2 – 0.051; LOI – 2.0 wt.%. According to the results of the X-ray fluorescence analysis, the studied IOTs should be classified as high-silicon type, which is one of the most common types of iron ore tailings [35]. In addition, a high iron content and the presence of aluminium at the level of 2 % were noted in the composition, confirming the theoretical studies carried out on the prospects of using processing waste as a raw material for the production of a mixed coagulant.
According to the results of the X-ray phase analysis, as shown in Fig.1, the mineral composition of the IOTs consists mainly of quartz (SiO2), with traces of magnetite (Fe3O4), hematite (Fe2O3) and polymorphic modifications of complex calcium and iron oxide (iron of different valences). The intensity of the diffraction peaks attributed to quartz is significantly higher than those of the other minerals, indicating that quartz is the predominant mineral. This interpretation of the diffractogram is supported by the chemical composition of the sample.
The chemical and phase composition results obtained formed the basis for experimental studies on the production of a Fe-Al coagulant.
The analysis of the particle size distribution showed that the dominant fraction in the IOTs composition is 0.5-1 mm (Table 1). According to the document "Recommendations on the design of tailings facilities of metallurgical industry enterprises", the processing waste in question should be classified as medium-grained. Additional grinding of the IOTs to intensify the leaching process was not carried out.
Table 1
Particle size distribution of iron ore tailings
Indicator |
Fraction, mm |
|||||||
< 0.005 |
0.005-0.01 |
0.01-0.05 |
0.05-0.1 |
0.1-0.25 |
0.25-0.5 |
0.5-1 |
1-3 |
|
Fraction yield, % |
2.41 |
4.45 |
13.5 |
9.98 |
9.6 |
18.4 |
30.1 |
11.5 |
Total yield, % |
2.41 |
6.87 |
20.4 |
30.3 |
39.9 |
58.4 |
88.5 |
100 |
Examination of the sample by scanning electron microscopy (Fig. 2) revealed several noteworthy features in the morphology of the samples. In particular, the particles exhibit angular and irregular shapes (a, d), while closer inspection reveals protrusions and an uneven surface (b, d, e, f). These characteristics contribute to an increase in the specific surface area of the tailings particles and consequently significantly affect the leaching process.
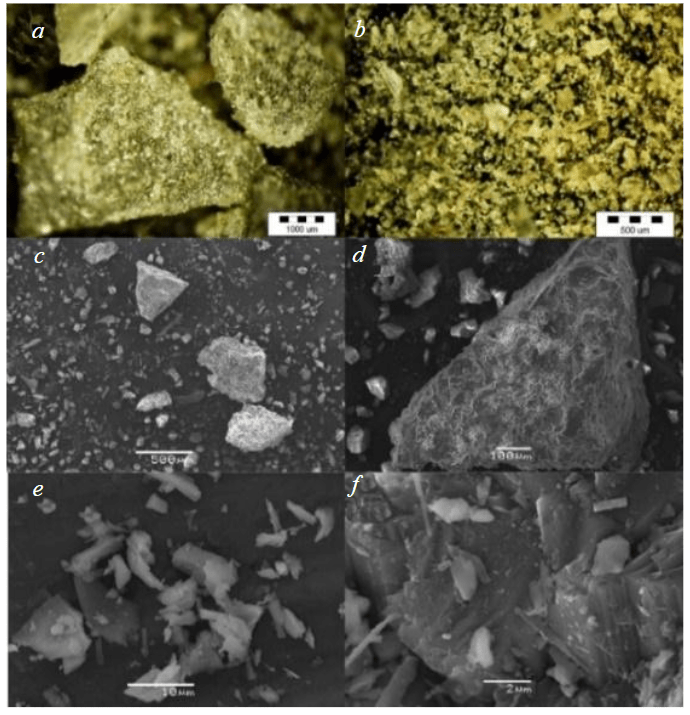
Fig.2. Micrographs of iron ore tailings obtained by scanning electron microscopy
A comprehensive study of the composition of the tailings sample investigated has shown that, un-der suitably selected leaching conditions, a solution suitable for the preparation of a coagulant for wastewater treatment can be obtained.
Experimental investigations to determine the optimum parameters for leaching the desired constit-uents from the IOTs have shown that the highest percentage of iron and aluminium extraction, all else being equal, is observed when sulphuric acid with a mass concentration of 40 % is used (Fig.3).
Investigation of the next key factor, leaching temperature, revealed that the maximum yield of iron and aluminium in solution is achieved at a moderate temperature of 100 °C (Fig.4). Furthermore, increasing the temperature from 75 to 100 °C results in a significant increase, with the efficiency of iron leaching increasing by 10.6 %. Further temperature escalation within the experiment was not pursued due to the proximity to the boiling point of sulphuric acid (113.9 °C).
The results of the experiment to determine the minimum contact time required for the maximum release of iron and aluminium into solution showed a stabilisation of the results after 60 min (Fig.5).
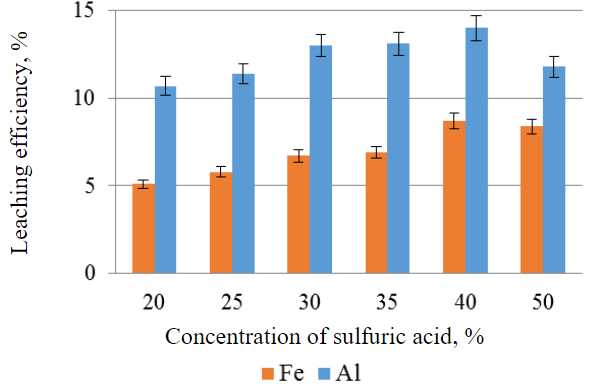
Fig.3. Efficiency of leaching iron and aluminium from IOTs as a function of the sulphuric acid concentration, all other things being equal (leaching time 3 h, solution temperature 20 °C, S:L= 1:1, without stirring)
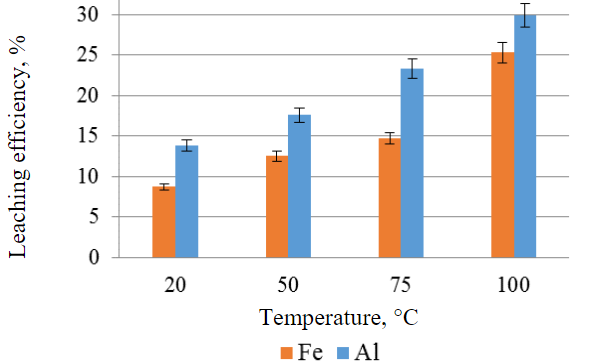
Fig.4. Efficiency of iron and aluminum leaching from the IOTs as a function of temperature, other conditions being equal (sulfuric acid concentration 40 wt.%, leaching time 3 h, S:L 1:1, without stirring)
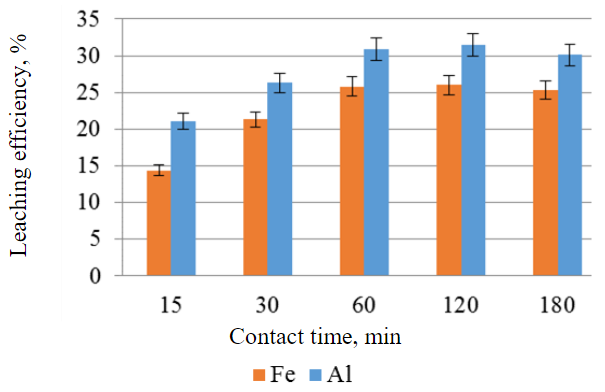
Fig.5. Efficiency of iron and aluminum leaching from the IOTs as a function of contact time under other equal conditions (sulfuric acid concentration 40 wt.%, temperature 100 °C, S:L ratio 1:1, without stirring)
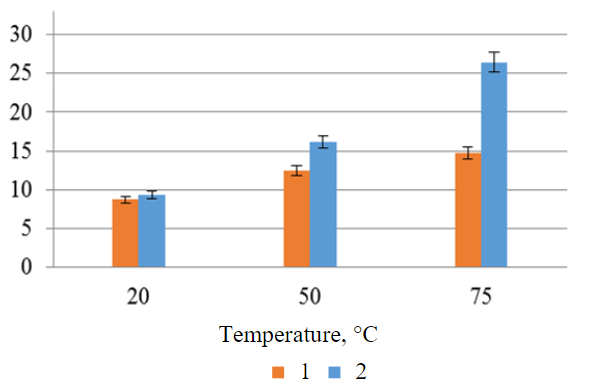
Fig.6. Efficiency of iron leaching from IOTs without stirring (1) and with forced stirring (2) of contacting media at different temperatures (sulfuric acid concentration 40 wt.%, S:L ratio 1:1, leaching time 3 h)
Increasing the liquid phase did not affect the leaching efficiency, as the iron yield remained at 24-25 % at all liquid/solid (S:L) ratios investigated (1:1, 1:3 and 1:5).
Finally, the effect of forced stirring of the contacting media was investigated. Figure 6 graphically shows a comparison of the results obtained in the temperature range of 20 to 75 °C with and without stirring. It can be seen from the figure that forced mixing increased the percentage of extracted iron by almost 2 times at a temperature of 75 °C.
Laboratory research has shown that maximum leaching efficiency is achieved using sulphuric acid at a concentration of 40 wt.%. The minimum contact time at a temperature of 100 °C was 60 min. A comparative evaluation of the leaching efficiency at different S:L ratios showed that this parameter had no influence on the transition of the desired components into solution. Therefore, the S:L ratio of 1:1 was empirically determined as the minimum for media contact and the establishment of reaction conditions. It was also found that mixing the mixture significantly increases the output of components into solution, with the difference becoming substantial as the temperature increases. For example, at a reaction mixture temperature of 75 °C and with forced mixing, a solution was obtained with an iron content comparable to that obtained in the experiment at a temperature of 100 °C without mixing. Due to technical limitations, forced mixing experiments at higher temperatures have not been carried out in laboratory conditions.
According to the results of quantitative chemical analysis, the test sample contains 11 and 2 % of Fe and Al in the form of sulphates. During the test to evaluate the coagulation properties, it was found that the colour of the solution begins to decrease at a working solution dose of 4.5 mg/dm3. The graphical representation of the results of the change in colour of the model solution as a function of the dose of coagulant added is shown in Fig.7. From Fig.7 it can be seen that the minimum dose of coagulant according to GOST R 51642-200055 is 5 mg/dm3 of the working coagulant solution for a model solution with a colour intensity of 50°. To prepare a working solution with such a concentration, 0.12 cm3 of the initial coagulant solution is required per 1 dm3 of purified water.
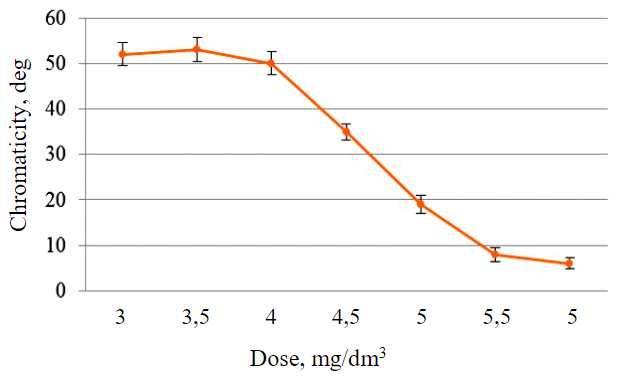
Fig.7. Determination of the minimum coagulant dose in a model solution of colour
The coagulant obtained showed efficacy over a wide pH range from 4 to 12 pH units. It showed the highest efficiency at pH = 7, where a decrease in colour intensity from 50 to 6 degrees was observed. Based on the results of experimental studies, the invention was patented in the Russian Federation [36].
Having established the functionality of the coagulant, its environmental safety was assessed by studying the matrix and impurity composition: matrix elements Mg – 6800; K – 1970; P – 801; Mn – 210; Na – 81; Ca – 57; impurity elements Zn – 7.0; V – 6.9; Cr – 4.8; Cu – 3.2; Sr – 1.3; Ba – 0.8 mg/dm3.
As can be seen, the coagulant contains heavy metals such as Mn, Zn, V, Cr and Cu. Therefore, an assessment of the secondary contamination of the treated water as a result of the use of the working coagulant solution was carried out. The results of the quantitative analysis of the composition of the model colour solution before and after the addition of the minimum dose of coagulant (5 mg/dm3) are presented in Table 2.
Table 2
Chemical composition of the model colour solution before and after water treatment, mg/dm³
Element |
Al |
Ba |
Ca |
Cu |
Fe |
K |
Mg |
Mn |
Na |
|
Sr |
Zn |
Before treatment |
0.022 |
0.003 |
1.36 |
< 0.001 |
0.047 |
1.25 |
0.2 |
0.002 |
0.8 |
1.0 |
0.003 |
< 0.005 |
After treatment |
0.022 |
0.001 |
2.03 |
< 0.001 |
0.052 |
1.89 |
0.7 |
0.009 |
20.7 |
50.7 |
0.014 |
< 0.005 |
PCLb.s. |
0.5 |
0.1 |
– |
1.0 |
0.3 |
– |
– |
0.1 |
– |
– |
7.0 |
5.0 |
PCLf.s. |
0.04 |
0.74 |
180 |
0.001 |
0.1 |
50 |
40 |
0.01 |
120 |
100 |
0.4 |
0.01 |
From Table 2 it can be seen that several components are introduced into the solution after coagulation process. There is a significant increase in the content of Na, Sr and SO42–. However, the recorded concentrations remain below maximum permissible values for all water use categories, indicating the acceptability of using the coagulant obtained as a reagent for wastewater treatment.
The final stage of the laboratory investigations was to examine the composition of the residue after leaching. Chemical analysis of the solid residue after leaching (SiO2 – 79.7; Fe2O3 – 10.5; MgO – 2.7; CaO – 2.5; Al2O3 – 1.5; K2O – 0.45; Na2O – 0.43; P2O5 – 0.059; MnO – 0.048; TiO2 – 0.013; LOI – 2.1 %) showed a significant increase in the proportion of silica compared to the original IOTs. There was also a decrease in the amount of impurities.
Assessing the changes in the particle size distribution of the IOTs before and after leaching, a significant reduction in particle size can be concluded (Table 3). When analysing the content of the fractions, it is worth noting the absence of the largest fraction (1-3 mm) in the precipitate after leaching. In addition, the content of the 0.5-1 mm fraction, which was predominant in the original IOTs sample, has significantly decreased. This is one of the key points to be considered when
discussing possible options for the utilisation of the post-leaching precipitate.
Table 3
Particle size distribution of the solid residue after leaching
Indicator |
Fraction, mm |
|||||||
< 0.005 |
0.005-0.01 |
0.01-0.05 |
0.05-0.1 |
0.1-0.25 |
0.25-0.5 |
0.5-1 |
1-3 |
|
Fraction yield, % |
2.19 |
4.32 |
27.3 |
24.1 |
21.4 |
13.3 |
7.47 |
– |
Total yield, % |
2.19 |
6.50 |
33.8 |
57.9 |
79.2 |
92.5 |
100 |
– |
In addition, the second factor limiting the choice of residue utilisation may be the iron content of 10.5 %. However, a study by the authors [37-39] has shown that the use of technogenic material with a higher iron content, including fine-grained material, in the construction industry is possible if additional laboratory studies are carried out and a formulation is developed on a case-by-case basis. The evaluation of the chemical composition and particle size distribution indicates a high potential for the use of leachate residue as artificial sand.
Conclusion
The continuous development of iron metallurgy, as well as the gradual transition to the development of low-grade ore reserves, leads to an increase in the amount of processing waste each year. For this reason, iron ore tailings as a secondary resource have recently attracted considerable attention from researchers, including the authors of this paper.
In this work, the composition and properties of iron ore tailings were studied on the example of one of the objects of the mineral raw materials complex located in the Kursk Magnetic Anomaly, which indicated the prospects and formed the basis for the development of the formulation of Fe-Al coagulant for wastewater treatment. Thus, the iron ore tailings were characterised by high iron content (18 % in terms of Fe2O3), represented mainly by magnetite and hematite, aluminium content at the level of 2 % (in terms of Al2O3), high content of fine and medium particles, as well as complex particle morphology.
The laboratory studies allowed the determination of the optimum conditions for IOTs leaching to obtain a Fe-Al coagulant: sulphuric acid concentration 40 wt.%, Solution temperature 100 °C without stirring and 75 °C with forced stirring, leaching time 60 min, S:L ratio 1:1.
Tests of the coagulant for efficiency of its use in the process of wastewater treatment on a model colour solution showed a sufficient degree of purification at pH = 4-11. The maximum purification efficiency (88 %) was achieved at pH = 7. In the course of laboratory studies, the minimum dose of coagulant was also determined on the example of a model colour solution according to GOST R 51642-2000.
The assessment of the environmental safety of the use of Fe-Al coagulants showed that, despite the multi-component composition, including the presence of heavy metals, no secondary water pollution occurs due to active precipitation and co-precipitation of components in solution. The maximum increase in concentrations in the model solution after treatment was observed for Na, Sr and SO42–, but the recorded values remained below the level of maximum permissible concentrations for all categories of water use.
A comprehensive study of the post-leach solid sludge allows us to recommend it as a potential raw material for the construction industry, subject to further testing of the material in a specialist construction laboratory.
The study has shown that the production of coagulants from iron ore tailings is a worthy alternative to known methods and has promising prospects as it can be considered as a way of extending the production chain of iron ore mining. In this case, the secondary use of IOT as a technogenic raw material will minimise the amount of waste to be stored in tailings ponds and increase the degree of treatment of discharged and recycled water both in the facilities of the mineral and raw materials complex and in other industries.
References
- Petrova T.A., Rudzisha E., Alekseenko A.V. et al. Rehabilitation of Disturbed Lands with Industrial Wastewater Sludge. Minerals. 2022. Vol. 12. Iss. 3. N 376. DOI: 10.3390/min12030376
- Pashkevich M.A., Kulikova Yu.A. Monitoring and assessment of the negative impact of technogenic massives of the mineral and raw complex. Mining Informational and Analytical Bulletin. 2023. N 9-1, p. 231-247 (in Russian). DOI: 10.25018/0236_1493_2023_91_0_231
- Plokhov A.S., Kharko P.A., Pashkevich M.A. Effect of tailings storage facility on surface water at copper–pyrite deposit. Mining Informational and Analytical Bulletin. 2021. N 4, p. 57-68 (in Russian). DOI: 10.25018/0236_1493_2021_4_0_57
- Nureev R.R., Pashkevich M.A., Kharko P.A. Assessment of the impact of Copper Ore Enrichment Waste on Surface and Groundwater. Geology and Geophysics of Russian South. 2022. Vol. 12. N 4, p. 169-179 (in Russian). DOI: 10.46698/VNC.2022.37.95.013
- Kuskov V.B., Lvov V.V., Yushina T.I. Increasing the recovery ratio of iron ores in the course of preparation and processing. CIS Iron and Steel Review. 2021. N 21, p. 4-8. DOI: 10.17580/cisisr.2021.01.01
- Pan Hu, Yihe Zhang, Yurui Zhou et al. Preparation and effectiveness of slow-release silicon fertilizer by sintering with iron ore tailings. Environmental Progress & Sustainable Energy. 2018. Vol. 37. Iss. 3, p. 1011-1019. DOI: 10.1002/ep.12776
- Ming Lei, Lin Tang, Huihui Du et al. Safety assessment and application of iron and manganese ore tailings for the remediation of As-contaminated soil. Process Safety and Environmental Protection. 2019. Vol. 125, p. 334-341. DOI: 10.1016/j.psep.2019.01.011
- Bing Rao, Likun Gao, Huixin Dai et al. An Efficient and Sustainable Approach for Preparing Silicon Fertilizer by Using Crystalline Silica from Ore. JOM. 2019. Vol. 71. Iss. 11, p. 3915-3922. DOI: 10.1007/s11837-019-03630-5
- Puiatti G.A., Elerate E.M., de Carvalho J.P. et al. Reuse of iron ore tailings as an efficient adsorbent to remove dyes from aqueous solution. Environmental Technology. 2024. Vol. 45. Iss. 12, p. 2308-2319. DOI: 10.1080/09593330.2021.2011427
- Almeida V.O., Schneider I.A.H. Production of a ferric chloride coagulant by leaching an iron ore tailing. Minerals Engineering. 2020. Vol. 156. N 106511. DOI: 10.1016/j.mineng.2020.106511
- Xiaoyu Han, Yaping Wang, Na Zhang et al. Facile synthesis of mesoporous silica derived from iron ore tailings for efficient adsorption of methylene blue. Colloids and Surfaces A: Physicochemical and Engineering Aspects. 2021. Vol. 617. N 126391. DOI: 10.1016/j.colsurfa.2021.126391
- Li Luo, Yimin Zhang, Shenxu Bao, Tiejun Chen. Utilization of Iron Ore Tailings as Raw Material for Portland Cement Clinker Production. Advances in Materials Science and Engineering. 2016. Vol. 2016. N 1596047. DOI: 10.1155/2016/1596047
- Geng Yao, Qiang Wang, Zhiming Wang et al. Activation of hydration properties of iron ore tailings and their application as supplementary cementitious materials in cement. Powder Technology. 2020. Vol. 360, p. 863-871. DOI: 10.1016/j.powtec.2019.11.002
- Xiaoyan Huang, Ravi Ranade, Victor C. Li. Feasibility Study of Developing Green ECC Using Iron Ore Tailings Powder as Cement Replacement. Journal of Materials in Civil Engineering. 2013. Vol. 25. Iss. 7, p. 923-931. DOI: 10.1061/(ASCE)MT.1943-5533.0000674
- Jiangshan Zhao, Kun Ni, Youpo Su, Yunxing Shi. An evaluation of iron ore tailings characteristics and iron ore tailings concrete properties. Construction and Building Materials. 2021. Vol. 286. N 122968. DOI: 10.1016/j.conbuildmat.2021.122968
- Li Gong, Xuelei Gong, Ying Liang et al. Experimental Study and Microscopic Analysis on Frost Resistance of Iron Ore Tailings Recycled Aggregate Concrete. Advances in Materials Science and Engineering. 2022. Vol. 2022. N 8932229. DOI: 10.1155/2022/8932229
- Xingdong Lv, Yuqiang Lin, Xia Chen et al. Environmental impact, durability performance, and interfacial transition zone of iron ore tailings utilized as dam concrete aggregates. Journal of Cleaner Production. 2021. Vol. 292. N 126068. DOI: 10.1016/j.jclepro.2021.126068
- Hongjian Lu, Chongchong Qi, Qiusong Chen et al. A new procedure for recycling waste tailings as cemented paste backfill to underground stopes and open pits. Journal of Cleaner Production. 2018. Vol. 188, p. 601-612. DOI: 10.1016/j.jclepro.2018.04.041
- Daiqiang Deng, Guodong Cao, Youxuan Zhang. Experimental Study on the Fine Iron Ore Tailing Containing Gypsum as Backfill Material. Advances in Materials Science and Engineering. 2021. Vol. 2021. N 5576768. DOI: 10.1155/2021/5576768
- Barati S., Shourijeh P.T., Samani N., Asadi S. Stabilization of iron ore tailings with cement and bentonite: a case study on Golgohar mine. Bulletin of Engineering Geology and the Environment. 2020. Vol. 79. Iss. 8, p. 4151-4166. DOI: 10.1007/s10064-020-01843-6
- Apaza Apaza F.R., Guimarães Rodrigues A.C., Vivoni A.M., Schroder R. Evaluation of the performance of iron ore waste as potential recycled aggregate for micro-surfacing type cold asphalt mixtures. Construction and Building Materials. 2021. Vol. 266. Part B. N 121020. DOI: 10.1016/j.conbuildmat.2020.121020
- Ziyao Wei, Yanshun Jia, Shaoquan Wang et al. Utilization of iron ore tailing as an alternative mineral filler in asphalt mastic: High-temperature performance and environmental aspects. Journal of Cleaner Production. 2022. Vol. 335. N 130318. DOI: 10.1016/j.jclepro.2021.130318
- Zubkova O.S., Alekseev A.I., Zalilova M.M. Research of combined use of carbon and aluminum compounds for wastewater treatment. Russian Journal of Chemistry and Chemical Technology. 2020. Vol. 63. N 4, p. 86-91. DOI: 10.6060/ivkkt.20206304.6131
- Sahu O.P., Chaudhari P.K. Review on Chemical treatment of Industrial Waste Water. Journal of Applied Sciences and Environmental Management. 2013. Vol. 17. N 2, p. 241-257. DOI: 10.4314/jasem.v17i2.8
- Narasimhaiah J., Venkatesh S., Suresh S.B., Annapurna B.P. Study on Substitution of Iron Ore Tailings as Fine Aggregates in Concrete. Gradiva Review Journal. 2021. Vol. 7. Iss. 8, p. 76-89. DOI: 10.37897.GRJ.2021.V7I8.21.297
- Thejas H.K., Hossiney N. Alkali-activated bricks made with mining waste iron ore tailings. Case Studies in Construction Materials. 2022. Vol. 16. N e00973. DOI: 10.1016/j.cscm.2022.e00973
- Changquan Zhang, Suqin Li. Utilization of iron ore tailing for the synthesis of zeolite A by hydrothermal method. Journal of Material Cycles and Waste Management. 2018. Vol. 20. Iss. 3, p. 1605-1614. DOI: 10.1007/s10163-018-0724-7
- Sverguzova S.V., Sapronova Zh.A., Zubkova O.S. et al. Electric steelmaking dust as a raw material for coagulant production. Journal of Mining Institute. 2023. Vol. 260, p. 279-288. DOI: 10.31897/PMI.2023.23
- Shuo Yang, Wang Li, Hongjie Zhang et al. Treatment of paper mill wastewater using a composite inorganic coagulant prepared from steel mill waste pickling liquor. Separation and Purification Technology. 2019. Vol. 209, p. 238-245. DOI: 10.1016/J.SEPPUR.2018.07.049
- Sahu J.N., Kapelyushin Y., Mishra D.P. et al. Utilization of ferrous slags as coagulants, filters, adsorbents, neutralizers/stabilizers, catalysts, additives, and bed materials for water and wastewater treatment: A review. Chemosphere. 2023. Vol. 325. N 138201. DOI: 10.1016/j.chemosphere.2023.138201
- Danilov A.S., Matveeva V.A., Korelskiy D.S., Horttanainen M. Backfill of a Mined-Out Gold Ore Deposit with the Cemented Rubber-Cord and Waste Rock Paste: Environmental Changes in Aqueous Media. Journal of Ecological Engineering. 2021. Vol. 22. Iss. 7, p. 190-203. DOI: 10.12911/22998993/138870
- Pashkevich M.A., Petrova T.A. Recyclability of Ore Beneficiation Wastes at the Lomonosov Deposit. Journal of Ecological Engineering. 2019. Vol. 20. Iss. 2, p. 27-33. DOI: 10.12911/22998993/94919
- Pharoe B.K., Evdokimov A.N., Gembitskaya I.M., Bushuyev Y.Y. Mineralogy, geochemistry and genesis of the post-Gondwana supergene manganese deposit of the Carletonville-Ventersdorp area, North West Province, South Africa. Ore Geology Reviews. 2020. Vol. 120. N 103372. DOI: 10.1016/j.oregeorev.2020.103372
- Lei Tao, Langlang Wang, Kanghuai Yang et al. Leaching of iron from copper tailings by sulfuric acid: behavior, kinetics and mechanism. RSC Advances. 2021. Vol. 11. Iss. 10, p. 5741-5752. DOI: 10.1039/D0RA08865J
- Gongyue Dong, Guangyan Tian, Linlin Gong et al. Mesoporous zinc silicate composites derived from iron ore tailings for highly efficient dye removal: Structure and morphology evolution. Microporous and Mesoporous Materials. 2020. Vol. 305. N 110352. DOI: 10.1016/j.micromeso.2020.110352
- Matveeva V.A., Semenova A.I., Chukaeva M.A., Smirnov Yu.D. Patent N 2818198 RF. Method of obtaining coagulant. Publ. 25.04.2024. Bul. N 12.
- Chuansheng Xiong, Weihua Li, Linhua Jiang et al. Use of grounded iron ore tailings (GIOTs) and BaCO3 to improve sulfate resistance of pastes. Construction and Building Materials. 2017. Vol. 150, p. 66-76. DOI: 10.1016/j.conbuildmat.2017.05.209
- Zhong-xi Tian, Zeng-hui Zhao, Chun-quan Dai, Shu-jie Liu. Experimental Study on the Properties of Concrete Mixed with Iron Ore Tailings. Advances in Materials Science and Engineering. 2016. Vol. 2016. N 8606505. DOI: 10.1155/2016/8606505
- Ali Umara Shettima, Yusof Ahmad, Mohd Warid Hussin et al. Strength and Microstructure of Concrete with Iron Ore Tailings as Replacement for River Sand. E3S Web of Conferences. 2018. Vol. 34, p. 9. DOI: 10.1051/e3sconf/20183401003