Оценка эффективности водных пылеподавляющих эмульсий на основе акриловых и алкидных полимеров
- 1 — д-р техн. наук заведующий кафедрой Белгородский государственный технологический университет им. В.Г.Шухова ▪ Orcid ▪ Scopus ▪ ResearcherID
- 2 — аспирант Белгородский государственный технологический университет им. В.Г.Шухова ▪ Orcid ▪ ResearcherID
- 3 — канд. техн. наук доцент Белгородский государственный технологический университет им. В.Г.Шухова ▪ Orcid ▪ ResearcherID
- 4 — аспирант Белгородский государственный технологический университет им. В.Г.Шухова ▪ Orcid ▪ ResearcherID
- 5 — научный сотрудник Белгородский государственный технологический университет им. В.Г.Шухова ▪ Orcid ▪ ResearcherID
Аннотация
В настоящее время для понижения уровня запыленности вблизи и на территориях карьеров, горно-обогатительных и других объектов с повышенным содержанием мелкодисперсной пыли перспективным является применение специальных пылеподавляющих реагентов. Выполнен анализ путей понижения пылеобразующей способности неорганических дисперсий с высокой степенью пыления. Из-за отсутствия нормативно-технической документации, посвященной стандартизации методик контроля качества пылеподавляющих составов, возникает необходимость анализа существующих параметров и методов их определения для разработки обязательных методик контроля свойств пылеподавляющих составов, образуемых ими пленок и консолидированных систем. Исследование посвящено обоснованию необходимых методов оценки пылеобразующей способности неорганических дисперсий после обработки различными пылеподавляющим средствами и оценки их эффективности. Рассмотрены параметры и описаны методики количественной оценки определения качества консолидированного слоя образцов пыли при использовании разных пылеподавляющих составов. В результате анализа совокупности значений параметров установлено, что наиболее устойчивым к воздействию негативных факторов за счет формирования более плотной и прочной сетки полимерной матрицы являются образцы пылящей поверхности, обработанные эмульсией алкидной глифталевой смолы на водной основе с высоким агломерирующим действием на частицы неорганической дисперсии и образованием консолидированного слоя с углом смачивания 92,5° и пределом прочности при сжатии 0,56 МПа.
Финансирование
Исследование выполнено за счет гранта Российского научного фонда № 23-19-00796.
Введение
Пылеобразование на промышленных объектах при складировании, хранении и транспортировке сыпучих материалов является одним из основных источников загрязнения воздуха, наносящим непоправимый вред здоровью человека [1] и служащим причиной поломок спецоборудования.
Пыль на промышленных объектах (горнодобывающие участки, карьерные или промышленные дороги [2], отвалы [3, 4], хвостохранилища [5], терриконы [6], сельскохозяйственные угодья и др. [7, 8]) различается по химическому составу и дисперсности. Решающими факторами принято считать погодные и природные явления, вызывающие ветровую эрозию, а также техногенные процессы (образование пылевых облаков при взрывных, пахотных и строительных работах) [9, 10]. Основной принцип решения задачи предотвращения образования пылевого облака заключается в консолидации частиц пыли (их слипании) под действием пылеподавляющих составов (ПС), приводящей к укрупнению и утяжелению частиц неорганической дисперсии аэрозольного типа (пылеобразующая дисперсия) [11-13]. Благодаря этому снижается уровень пыления, так как тяжелые частицы в меньшей степени подвержены эрозии.
Несмотря на важность контроля пылеподавляющей способности того или иного состава, анализ научной литературы, обобщенный в статье [14], показал, что российские и зарубежные исследователи уделяют недостаточное внимание методикам оценки свойств как самого пылеподавляющего состава, так и системы пылеобразующая дисперсия (ПД) – пылеподавляющий состав. Причинами затруднений и, как следствие, малой освещенности темы в научных трудах, можно считать отсутствие нормативно-технических и других регламентирующих документов, посвященных стандартизации методик контроля качества пылеподавляющих составов. Назрела острая необходимость анализа существующих параметров и методик их определения для разработки обязательного перечня методик контроля свойств пылеподавляющих составов, образуемых ими пленок и консолидированных систем.
В настоящее время существуют нормативные документы, отражающие методики определения свойств, способы нанесения, транспортировки, хранения и другие показатели реагентов (эмульсий, растворов, пен), которые используются для оценки качества пылеподавляющих составов: ГОСТ 33290-2015, ГОСТ Р 58952.1-2020, ГОСТ Р 51037-97, ГОСТ Р 52056-2003, ГОСТ 30491-2012. Также можно использовать существующую нормативную документацию, предназначенную для контроля качества лакокрасочных материалов, клеев или грунтовок. Однако важно учитывать, что все предлагаемые методики требуют адаптации под необходимый контрольный образец. Для эмульсий исследователи выделяют следующие основные контролируемые характеристики: удельный расход эмульсии; толщина пленочного покрытия; поверхностное натяжение на границе «пленка пылеподавляющей эмульсии – жидкость»; угол смачивания на поверхности пленки пылеподавляющей эмульсии [14]. Авторы изученных работ предлагают исследовать следующие дополнительные параметры, оказывающие влияние на пылеподавляющую характеристику полимерных растворов, пен и эмульсий на водной основе: смачивающая способность [15-17]; глубина проникновения состава в пылящую поверхность [18]; вязкость [19]; остаток пыли после обработки поверхности пылеобразующей дисперсии [20-22]; морфологические особенности молекул (пузырьков) состава [23] и пленок, образованных после их высыхания [24]; время пылеподавления в зависимости от концентрации частиц пыли [25, 26]; устойчивость к эрозии при изменении температуры [27, 28]; влагоудержание [29]; набухание протекторной резины автотранспорта [30]; физико-механические характеристики пленки [31]; скорость распыления состава на пылеобразующую дисперсию [32]; ИК-спектры пылеобразующей дисперсии до и после обработки составом [33].
Рассмотрены параметры и описаны методики определения качества образцов пыли с консолидированным слоем (КС) при использовании разных пылеподавляющих составов с учетом условий эксплуатации промышленных дорог: способности к агломерации частиц пыли; визуальной оценки устойчивости образцов пыли, обработанных пылеподавляющими составами, в водной среде; прочность образцов с консолидированным слоем на сжатие при температурах 20 и 50 °С; угла смачивания консолидированного слоя образца; структурных особенностей консолидированного слоя обработанной пылящей поверхности.
Методы
Анализ эффективности пылеподавления и качественных характеристик образуемых полимерных пленок проводился с использованием водопроводной воды (распространенный способ обеспылевания в промышленных зонах) и двух образцов водных полимерных эмульсионных систем: эмульсии промышленного образца – акриловой эмульсии Concentrate Polymer (выбран из-за наибольшей схожести как по составу, так и по предполагаемой области ее использования – в качестве ПС) и синтезированной эмульсии алкидной глифталевой смолы. Обработка образцов (размер образца цилиндра 3 ´ 3 см получен прессованием под давления 7,5 кН) модельной дисперсии пылеподавляющими составами проводилась однократным и равномерным нанесением из пульверизатора по всей поверхности цилиндра с расходом 0,75 л/м2.
Состав разработанной авторами эмульсии [34, 35] включает в себя (в пересчете на 100 % по массе) следующие компоненты: дисперсная фаза эмульсии – алкидная глифталевая смола 56,1 %; дисперсионная среда – вода 37,5 %; эмульгатор – АМР-95 (2-амино-2-метил-1-пропанол) – 0,3 %; модификаторы границы раздела фаз – этиленгликоль 6 % и смесь сиккативов кобальта и циркония 0,034 и 0,066 % соответственно. Основные характеристики: динамическая вязкость эмульсии – до 50,7 мПа∙с; срок жизни эмульсии – до 87 сут; размер капель эмульсии – до 3 мкм; время высыхания эмульсии – 19 ч; твердость пленки, образованной после полного высыхания эмульсии – 0,32 у.е.; краевой угол пленки – 97,5°; свободная энергия поверхности – 36,7 мН/м [35]. Экологичность веществ рассматривалась на этапе выбора сырьевых компонентов эмульсии, рекомендуется наносить состав на пылеобразующую дисперсию методом распыления – защитный слой образуется минимальной толщины, что минимизирует негативное влияние на экосферу. При этом содержание органических веществ в разработанной эмульсии не превышает содержания в традиционно используемых ПС.
Для оценки эффективности рассматриваемых эмульсий в качестве образцов пылеобразующей дисперсии использовалась модельная дисперсия в виде смеси пылевидного кварца марки Б (производитель ООО «ОПТ6») и каолиновой глины Латненского месторождения (в сухом виде глина имеет пылеватую структуру) в пропорции 3:1. Компонентный состав пыли, выбранной в качестве образца неорганической дисперсии аэрозольного типа, объясняется повсеместным распространением породообразующих минералов (кварца и каолинита) в составе подавляющего большинства горных пород и почв земной коры, а также из-за характеристики компонентов (минимальная пористость кварца и возможность впитывания воды каолинита).
Степень агломерации частиц пыли устанавливается путем рассева обработанной дисперсии через сита с размером ячеек 0,1-10 мм и определения частного остатка на каждом сите после обработки пылеобразующей дисперсии пылеподавляющими составами.
Визуальная оценка устойчивости образцов с обработанной поверхностью в водной среде не является нормируемым параметром и проводилась для определения возможности дальнейшей оценки водоустойчивости и набухания образцов. Подготовка образцов из глинисто-песчаной смеси осуществлялась по стандартной методике, соответствующей ГОСТ 9128-2013 «Смеси асфальтобетонные, полимерасфальтобетонные, асфальтобетон, полимерасфальтобетон для автомобильных дорог и аэродромов. Технические условия». Образец-цилиндр обрабатывается пылеподавляющим составом поверхностно путем равномерного распыления из пульверизатора.
Изучение прочностных характеристик консолидированного слоя на поверхности образца пыли, образованного после высыхания эмульсии алкидной смолы, проводили согласно методике ГОСТ 30491-2012 «Смеси органоминеральные и грунты, укрепленные органическими вяжущими, для дорожного и аэродромного строительства» при температуре 20 и 50 °С с определением прочности на сжатие образцов-цилиндров. Образец-цилиндр обрабатывается пылеподавляющим составом поверхностно путем равномерного распыления из пульверизатора. Данная методика является косвенной оценкой пылеподавляющих свойств [14], однако метод информативен с позиции оценки связующих свойств эмульсии.
Краевой угол определялся при помощи прибора для измерения контактного угла смачивания Kruss DSA 30 с использованием ПО ADVANCED методом лежачей капли. В качестве тестовой жидкости использовалась дистиллированная вода. Программа ADVANCED на основании всех проведенных измерений контактного угла автоматически выводит среднее значение. Подготовка образцов осуществлялась при помощи прессования смеси пылеобразующей дисперсии под давлением 7,5 кН.
Структурные особенности консолидированного слоя пылеобразующей дисперсии изучались методом растровой электронной микроскопии при помощи сканирующего электронного микроскопа Tescan MIRA 3 LMU.
Характеристики пылеобразующей дисперсии проводили по методикам ГОСТ Р 51037-97 «Покрытия полимерные защитные изолирующие, локализирующие пылеподавляющие и дезактивирующие. Общие технические требования». Исследование выполнено с использованием оборудования Центра высоких технологий на базе БГТУ им. В.Г.Шухова.
Применяемые понятия и их определения:
Пылеобразующая дисперсия (неорганическая дисперсия аэрозольного типа) – смесь неорганических частиц пыли, соответствующая ряду классификаций пыли по дисперсности – 4-му и 3-му; слипаемости (характеристический показатель – разрывная прочность слоя пыли по Е.И.Андрианову) – неслипающаяся; смачиваемости – хорошо смачиваемая.
Пылеподавляющий состав – реагент с высокими пылеподавляющими характеристиками, агрегатное состояние (жидкое или сухое) и морфологическая структура (раствор, пена, эмульсия) которого способны уменьшить степень пылеобразования неорганических дисперсий.
Консолидированный слой – временное защитное покрытие, образованное на поверхности пылеобразующей дисперсии после полного высыхания пылеподавляющего состава.
Обсуждение результатов
С учетом предполагаемой области применения разработанной алкидной эмульсии для обеспылевания (пылящие объекты строительной и горнодобывающей промышленности) необходимо было количественно оценить комплекс показателей консолидированного слоя, образующегося после распределения пылеподавляющего состава. Поскольку разработанная алкидная эмульсия включает продукты лакокрасочной промышленности, а ее основным функциональным назначением является локализация пыли и образование защитного покрытия, при оценке пылеподавляющей эффективности с точки зрения защитного полимерного покрытия целесообразно руководствоваться требованиями ГОСТ Р 51037-97. На основании указанного нормативного документа выбраны показатели, позволяющие установить соответствие пылеподавляющего защитного полимерного покрытия, образованного разработанной эмульсией, регламентируемым требованиями (табл.1). Анализ полученных значений нормируемых характеристик консолидированного слоя показал, что разработанная алкидная эмульсия позволяет получать пылеподавляющее защитное покрытие, по всем показателям соответствующее требованиям ГОСТ Р 51037-97.
Таблица 1
Характеристики пылеобразующей дисперсии по ГОСТ Р 51037-97
Наименование показателя |
Технические требования |
Фактическое значение |
Предварительная подготовка поверхности(температура 5-30 °С, влажность до 95 %) |
Отсутствует |
Отсутствует |
Степень окомкования, % |
>80 |
93 |
Температура поверхности нанесения, °С |
–10 … +50 |
+5 … +25 |
Время выдержки до начала эксплуатации, ч |
<24 |
19 |
Устойчивость при воздействии воды, сут |
> 180 |
198 |
Устойчивость при температуре, °С |
5-30 |
79 |
Срок службы, сут |
> 180 |
180 |
Однако использование методик для определения нормируемых показателей не позволяет в полной мере изучить взаимодействие пылеподавляющего состава с пылеобразующей дисперсией. Это связано с применением нормативных методик для оценки полимерного покрытия на твердой поверхности (стекло или металлическая пластина). Анализ показателей, полученных на монолитных статичных поверхностях, является необходимым, но недостаточным для оценки эффективности составов, наносимых на высокодисперные, условно подвижные материалы.
Ввиду отсутствия единых норм контроля, зафиксированных в нормативных документах, а также единых требований к пылеподавляющим составам, весьма сложно проводить сравнительную оценку эффективности тех или иных видов реагентов и их композиций. На основании анализа применяемых различными научными группами методов и контролируемых параметров был выбран ряд показателей, которые рекомендованы как наиболее информативные для доказательства пылеподавляющей способности алкидных эмульсий.
Основными процессами, обеспечивающими пылеподавление при обработке поверхности составом на полимерной основе, являются укрупнение (склеивание) и пленкообразование. Чем более клейким будет полимерный компонент пылеподавляющего состава, тем лучше будет агломерация частиц. Результатом оценки степени агломерации частиц ПД являлось получение частного остатка после просева (масса вещества на каждом сите). Для обработанной модельной дисперсии характерно отсутствие фракций с частицами менее 0,25 мм (рис.1). Наибольший интерес для оценки способности к агломерации частиц модельной дисперсии после обработки ПС представляет правая часть графика. Так, агломерация частиц водой показала самый худший результат – образование агломератов находится в диапазоне 1-5 мм. Частные остатки на ситах представлены в табл.2.
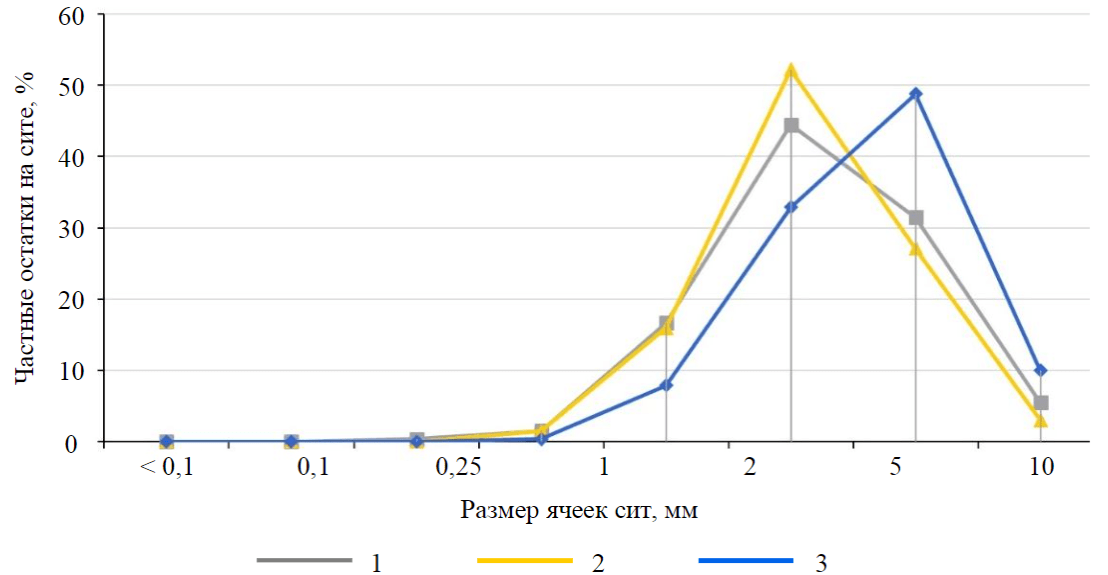
Рис.1. Гранулометрический состав модельной пылеобразующей дисперсии
1 – водопроводная вода; 2 – акриловая эмульсия; 3 – алкидная эмульсия
Таблица 2
Частные остатки на ситах, %
Вид обработки |
Размер ячеек сит, мм |
|||
1 |
2 |
5 |
10 |
|
Вода |
16,7 |
44,4 |
31,5 |
7,4 |
Акриловая эмульсия |
15,9 |
52,2 |
27,1 |
4,8 |
Алкидная эмульсия |
7,9 |
32,9 |
48,8 |
10,4 |
Анализ полученных данных гранулометрического состава обработанной дисперсии различными пылеподавляющими составами, определенного методом ситового анализа, позволяет судить о лучшей способности к агломерации неорганической дисперсии при использовании разработанной эмульсии. Об этом свидетельствует максимальная масса крупных агрегатов на сите с размером ячеек 5 мм, тогда как при использовании воды максимальная масса агрегатов отмечается на сите с ячейками 2 мм. Ее эффективность в агломерации пылящих частиц может объясняться наилучшей пленкообразующей способностью (клейкостью) полимерного компонента эмульсии – алкидной смолы, что свидетельствует о лучшем пылеподавляющем эффекте.
При визуальной оценке образца из глинисто-песчаных частиц, обработанного акриловой эмульсией (рис.2), наблюдалось быстрое впитывание средства в поверхность образца, которая при высыхании остается без изменений. Однако при обработке синтезированной эмульсией наблюдается образование пленки на поверхности (до погружения в воду). Далее обработанные образцы на некоторое время погружались в емкость с водой. Оценка производилась по разрушению образца в водной среде с фиксацией времени.
Для анализа были взяты три образца: образец 1 – модельная дисперсия без обработки ПС; образец 2 – дисперсия, обработанная акриловой эмульсией; образец 3 – дисперсия, обработанная синтезированной эмульсией.
Наблюдение продолжалось до полного разрушения образцов в воде. Образец 1 показал худший результат с полным разрушением через 30 мин. Образец 2 показал частичное разрушение поверхности цилиндра через 30 мин и полное разрушение через час. Образец 3 показал наилучший результат после 30 мин нахождения в воде – ровная поверхность без видимого разрушения. По прошествии часа в образце 3 отмечается разрушение стенок при внутренней сохранности формы. Таким образом, визуальная оценка обработанных образцов из модельной глинисто-кварцевой смеси частиц пыли показала, что наилучшую выдержку в воде имеет консолидированный слой, образованный синтезированной эмульсией из-за образования на поверхности спрессованной дисперсии более прочной полимерной пленки.
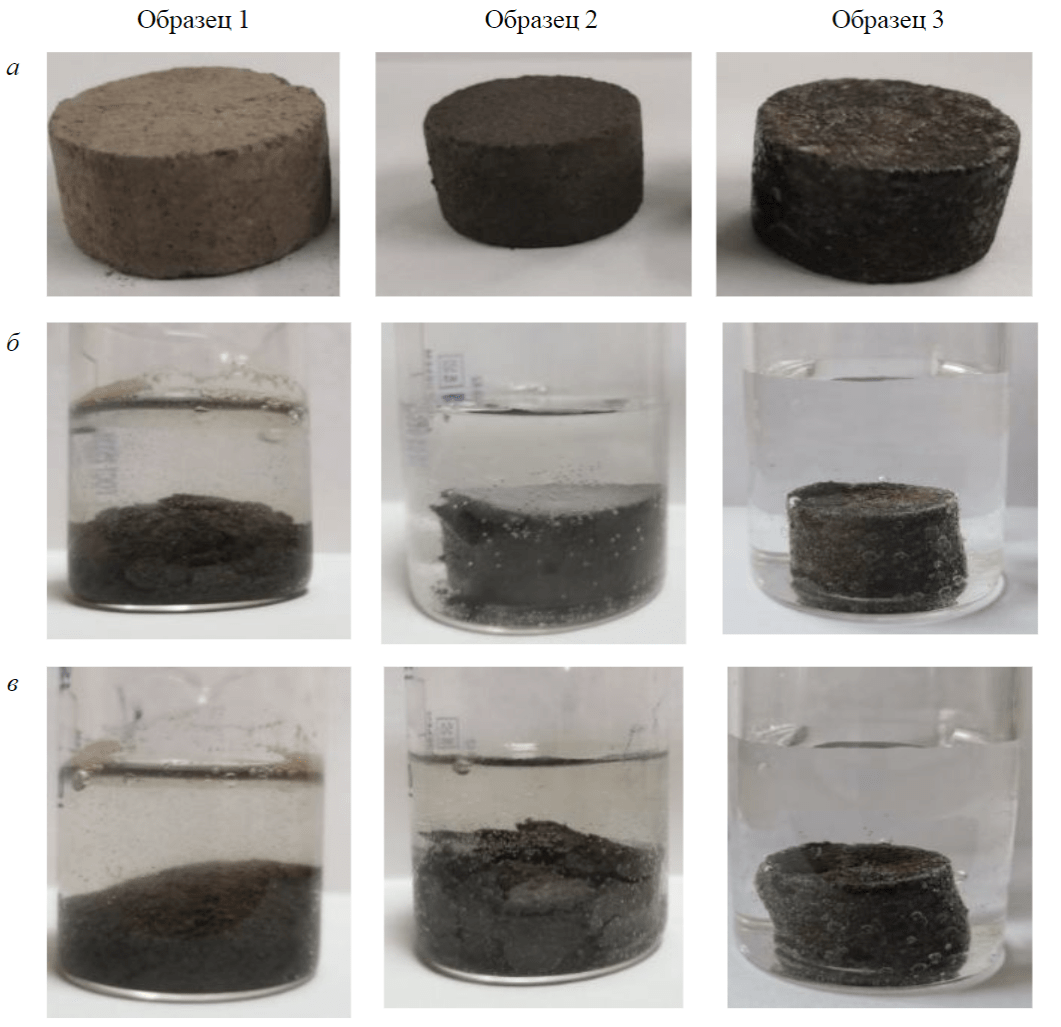
Рис.2. Разрушение образцов из смеси пылеватых частиц, обработанных пылеподавляющими составами до погружения в воду (а); через 30 мин (б); через 60 мин (в)
Анализ предела прочности на сжатие цилиндров, обработанных поверхностно пылеподавляющими составами, показал, что прочность образцов, обработанных полимерными эмульсиями при 20 °С, выше, чем обработанных при 50 °С (табл.3). Однако при сравнении образцов, обработанных эмульсиями, наиболее высокие значения прочности наблюдаются у образцов, консолидированный слой которых был образован после полного высыхания эмульсии алкидной смолы как при 20 °С, так и при 50 °С; по сравнению с образцами, обработанными акриловой эмульсией, на 32 % выше при 20 °С и на 35 % – при 50 °С. Повышение прочности образца, поверхность которого была обработана эмульсией алкидной глифталевой смолы, свидетельствует о формировании более прочной полимерной матрицы, что, вероятно, связано с высокой адгезивностью (липкостью) смолы к частицам пыли.
Таблица 3
Показатели прочности грунта
Вид образца |
Предел прочности при сжатиипри различных температурах, МПа |
|
20 °С |
50 °С |
|
Обработанный акриловой эмульсией «Concentrate Polymer» |
0,38 |
0,13 |
Обработанный эмульсией алкидной глифталевой смолы |
0,56 |
0,2 |
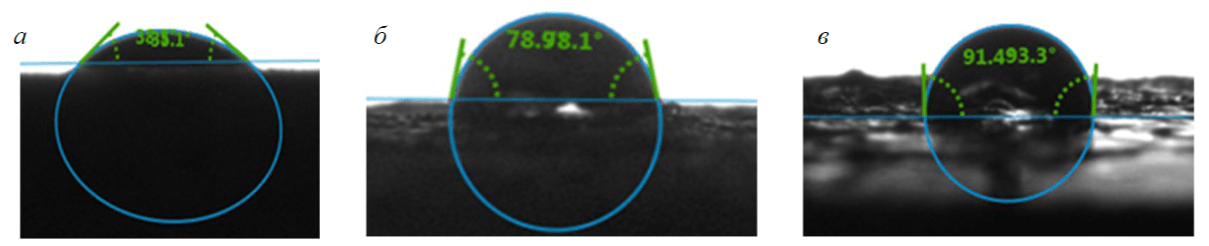
Рис.3. Значения угла смачивания образцов из смеси пылеватых частиц, обработанных пылеподавляющими составами в тестовой жидкости (воде): а – без обработки (38,5°); б – образец, обработанный акриловой эмульсией «Concentrate Polymer» (78,9°); в – образец, обработанный эмульсией алкидной глифталевой смолы (92,5°)
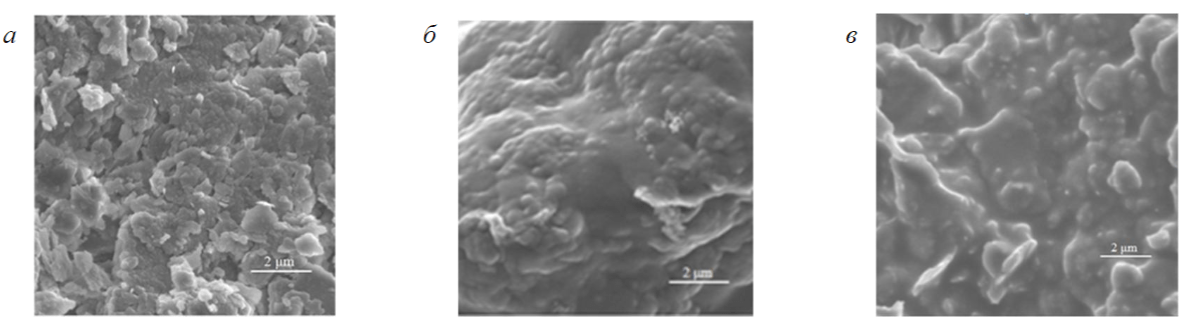
Рис.4. Характеристика поверхности неорганической дисперсии после обработки пылеподавляющими составами: а – образец без обработки (контрольный); б – образец, обработанный акриловой эмульсией «Concentrate Polymer»; в – образец, обработанный алкидной эмульсией
Для изучения эффективности пылеподавляющих пленок, образующихся на обрабатываемой поверхности, и их изолирующей способности исследовали изменение краевого угла смачивания. Чем выше значение угла смачивания, тем выше изолирующая способность получаемой при консолидации пылеватых частиц пленки, выражающаяся в гидрофобизирующей способности.
Анализ полученных значений (рис.3) показал наибольшую эффективность пылеподавляющего состава на основе алкида. Так, значения краевого угла смачивания консолидированного слоя, образованного при использовании алкидной эмульсии, в полтора раза выше, чем при использовании акриловой эмульсии, и в три раза выше, чем у исходного (необработанного) состава. Значения краевого угла смачивания поверхности образца при использовании синтезированной эмульсии более 90° говорят о придании гидрофобности.
Заключительным этапом исследования стало выявление особенностей структурообразования пленок алкидного олигомера на подложке из пылеватых частиц. Анализ структурообразования полимерной пленки проводился после отверждения эмульсии (рис.4). Несмотря на то, что в обоих случаях использовались полимерные эмульсии, структура образца из пылеватых частиц, обработанных акриловой эмульсией (рис.4, б), визуально не отличается от исходного образца без обработки. Вероятно, присутствие полимерной матрицы не фиксируется из-за невысокого содержания полимера или низкой вязкости эмульсии, что требует двух- или трехкратной обработки поверхности. Также это объясняет худшие показатели рассмотренных параметров.
Сравнительная оценка микроструктуры показывает (рис.4, в) эффективность синтезированной эмульсии в качестве средства пылеподавления с точки зрения способности образования защитной пленки на поверхности пылящей модельной системы. В структуре хорошо различаются светлые участки, равномерно распределенные по поверхности образца из смеси пылеватых частиц. Кроме того, отмечается, что при использовании пылеподавляющего синтезированного состава поверхность образца из рыхлой зернистой переходит в более гладкую монолитную. Это объясняется высокой адгезивностью (хорошей липкостью капли смолы к частице модельной дисперсии) выбранного полимерного компонента полученной эмульсии, а также ее высокой (по сравнению с акриловой эмульсией «Concentrate Polymer») вязкостью за счет достижения избытка смолы в составе.
Заключение
Анализ определенных в рамках исследования параметров позволил качественно и количественно определить физико-механические, коллоидно-химические свойства и структурные особенности консолидированного слоя пылеобразующей дисперсии, образованной на поверхности неорганической дисперсии аэрозольного типа после высыхания полимерного состава.
Анализ гранулометрического состава пыли, обработанной различными реагентами, методом ситового анализа показал лучшую способность к агломерации пыли при использовании алкидной эмульсии. Об этом свидетельствует максимальная масса крупных агрегатов на сите с размером ячеек 5 мм, тогда как при использовании воды максимальная масса агрегатов составляет 2 мм. Высокая агломерирующая способность объясняется наилучшей пленкообразующей способностью (клейкостью) алкидной смолы.
Анализ оценки устойчивости к воде образцов пыли, обработанных двумя видами составов, показал, что наилучшую выдержку в воде имеет консолидированный слой, образованный алкидной эмульсией. Это объясняется формированием на поверхности образцов более прочной полимерной пленки, что подтверждено результатами оценки структурных особенностей защитного покрытия и высоким значением угла смачивания (92,5°). Прочность образцов на сжатие при использовании обеих эмульсий при 50 °С снижается в два раза, что свидетельствует о негативном воздействии температуры на прочностные характеристики защитного полимерного слоя и ограниченном температурном диапазоне применяемого состава при его эксплуатации в промышленных зонах, но не об ухудшении пылеподавляющей эффективности эмульсии алкидной смолы.
Литература
- Вишневский А.В. Использование отходов промышленного производства для обеспыливания технологических автомобильных дорог // Вестник Забайкальского государственного университета. 2017. Т. 23. № 11. С. 12-18. DOI: 10.21209/2227-9245-2017-23-11-12-18
- Бурьянов И.А., Логачев К.И., Уваров В.А. Определение основных свойств пылевых частиц заточного участка // Вестник Белгородского государственного технологического университета им.В.Г.Шухова. 2020. Т. 5. № 10. С. 23-32. DOI: 34031/2071-7318-2020-5-10-23-32
- Шувалов Ю.В., Веселов А.П., Бульбашев А.П. и др. Борьба с пылью на горных предприятиях с использованием долго- и короткоживущих пен повышенной кратности // Горный информационно-аналитический бюллетень. 2007. № S С. 171-179.
- Киреева Е.В., Кондрашева Н.К., Зырянова О.В. и др. Пленкообразующие дисперсии на водной основе для пылеулавливающих составов // Лакокрасочные материалы и их применение. 2018. № 7-8. С. 42-45.
- Оспанова Ж.Б., Токтагул С., Тасмагамбетова А., Асадов М. Получение пенообразователей для пылеподавления угольных частиц // Вестник Казахского национального университета. Серия химическая. 2019. Т. № 3. С. 12-18. DOI: 10.15328/cb1071
- Щегольков Ю.С., Колосов А.А., Пасечная В.Ю. Влияние дисперсности производственной пыли на профзаболеваемость работников / Фундаментальные и прикладные научные исследования: актуальные вопросы, достижения и инновации: Сборник статей VIII Международной научно-практической конференции, 15 октября 2017, Пенза, Россия: в 4 частях. Пенза: Наука и Просвещение, 2017. Часть 1. С. 175-177.
- Wu Mingyue, Hu Xiangming, Zhang Qian et al. Study on preparation and properties of environmentally-friendly dust suppressant with semi-interpenetrating network structure // Journal of Cleaner Production. 2020. Vol. 259. № DOI: 10.1016/j.jclepro.2020.120870
- Wenjin Niu, Wen Nie, Mingyue Yuan et al. Study of the microscopic mechanism of lauryl glucoside wetting coal dust: Environmental pollution prevention and control // Journal of Hazardous Materials. 2021. Vol. 412. № DOI: 10.1016/j.jhazmat.2021.125223
- Романченко С.Б., Нагановский Ю.К., Корнев А.В. Инновационные способы контроля пылевзрывобезопасности горных выработок // Записки Горного института. 2021. Т. 252. С. 927-936. DOI: 10.31897/PMI.2021.6.14
- Строкова В.В., Ишмухаметов Э.М., Есина А.Ю. и др. Пылеподавляющие составы на водной основе: анализ состояния и перспективы развития // Вестник Технологического университета. 2021. Т. 24. № 12. С. 5-38.
- Ляшенко В.И., Гурин А.А. Обоснование природоохранных технологий и средств для пылеподавления поверхностей хвостохранилищ гидрометаллургического производства // Горный информационно-аналитический бюллетень. 2018. № С.58-72. DOI: 10.25018/0236-1493-2018-9-0-58-72
- Дабижа О.Н., Бесполитов Д.В., Коновалова Н.А. и др. Применение стабилизирующей полимерной добавки для защиты отвальных массивов вскрышных пород от ветровой эрозии // Вопросы современной науки и практики. Университет им. В.И.Вернадского. 2021. № 1 (79). С. 26-39. DOI: 17277/voprosy.2021.01.pp.026-039
- Jianwei Cheng, Xinrui Zheng, Yadong Lei et al. A compound binder of coal dust wetting and suppression for coal pile // Process Safety and Environmental Protection. 2021. Vol. 147. P. 92-102. DOI: 10.1016/j.psep.2020.08.031
- Jiayi Yan, Wen Nie, Haihan Zhang et al. Synthesis and performance measurement of a modified polymer dust suppressant // Advanced Powder Technology. 2020. Vol. Iss. 2. P. 792-803. DOI: 10.1016/j.apt.2019.11.033
- Kai Wang, Yuchen Zhang, Weiyao Cai et al. Study on the microscopic mechanism and optimization of dust suppression by compounding biological surfactants // Colloids and Surfaces A: Physicochemical and Engineering Aspects. 2021. Vol. 625. № DOI: 10.1016/j.colsurfa.2021.126850
- Строкова В.В., Ишмухаметов Э.М., Есина А.Ю. и др. Оценка влияния эмульгатора на свойства алкидной эмульсии на водной основе // Chemical Bulletin. 2022. Т. 5. № 3. С. 39-48.
- Строкова В.В., Ишмухаметов Э.М., Есина А.Ю. и др. Анализ способов получения алкидной эмульсии на водной основе // Вестник Технологического университета. 2022. Т. 25. № 7. С. 43-48. DOI: 10.55421/1998-7072_2022_25_7_43
- Сачкова О.С., Самойлов В.В., Елин А.М. Исследования по оценке эффективности и безопасности биологического препарата для пылеподавления // Наука и техника транспорта. 2021. № 2. С. 101-107.
- Акимов А.М., Котельникова С.А. Исследование пылезакрепляющих растворов при транспортировании горных масс // Энергетические установки и технологии. 2021. Т. 7. № С. 148-151.
- Qiu Bao, Wen Nie, Changqi Liu et al. The preparation of a novel hydrogel based on crosslinked polymers for suppressing coal dusts // Journal of Cleaner Production. 2020. Vol. 249. № 119343. DOI: 10.1016/j.jclepro.2019.119343
- Евтушенко А.И., Евтушенко И.И., Нор-Аревян С.Л., Бельская Я.В. К вопросу исследования путей повышения эффективности пылеподавления орошением // Инженерный вестник Дона. 2016. №3 (42). 9 с.
- Иванов А.В., Смирнов Ю.Д., Чупин С.А. Разработка концепции инновационной лабораторной установки для исследования пылящих поверхностей // Записки Горного института. 2021. Т. 251. С.757-766. DOI: 10.31897/PMI.2021.5.15
- Xiaobin Wei, Hetang Wang, Ying Xie, Yunhe Du. An experimental investigation on the effect of carboxymethyl cellulose on morphological characteristics of dust-suppression foam and its mechanism exploration // Process Safety and Environmental Protection. 2020. Vol. 135. P. 126-134. DOI: 10.1016/j.psep.2019.12.009
- Алосманов М.С., Атаев М.Ш., Султанзаде С.С. и др. Средство для борьбы с пылью // Вестник науки и образования. 2018. Т. 1. № 2 (38). С. 17-21. DOI: 10.20861/2312-8089-2018-38-003
- Qing Guo, Wanxing Ren, Jingtai Shi. Foam for coal dust suppression during underground coal mine tunneling // Tunnelling and Underground Space Technology. Vol. 89. 2019. P. 170-178. DOI: 10.1016/j.tust.2019.04.009
- Zongqi Liu, Gang Zhou, Jinjie Duan et al. Preparation of composite high-efficiency dust suppressant and relevant molecular dynamics simulation for wetting coal surface // Fuel. 2021. Vol. 296. № 120579. DOI: 10.1016/j.fuel.2021.120579
- Подображин С.Н. Предотвращение пылевыделения в атмосферу разрезов при ветровой эрозии // Безопасность труда в промышленности. 2011. № 6. С. 16-22.
- Ping Chang, Zidong Zhao, Guang Xu et al. Evaluation of the coal dust suppression efficiency of different surfactants: A factorial experiment // Colloids and Surfaces A: Physicochemical and Engineering Aspects. 2020. Vol. 595. № 124686. DOI: 10.1016/j.colsurfa.2020.124686
- Nguyen V.G. Patent № US 8052890 B2. Compositions for dust suppression and methods. Publ. 22.12.2005.
- Rulin Liu, Gang Zhou, Kaili Wang et al. Experimental investigation on highly efficient collection and cleaning for fine coal dust particles by dry-wet mixed chemical method // Journal of Environmental Chemical Engineering. 2021. Vol. 9. Is 5. № 105861. DOI: 10.1016/j.jece.2021.105861
- Anagnostopoulos C.A., Kandiliotis P., Lola M., Karavatos S. Improving Properties of Sand Using Epoxy Resin and Electrokinetics // Geotechnical and Geological Engineering. 2014. Vol. 32. Iss. 4. Р. 859-872. DOI: 10.1007/s10706-014-9763-6
- Hetang Wang, Yunhe Du, Xiaobin Wei, Xinxin He. An experimental comparison of the spray performance of typical water-based dust reduction media // Powder Technology. 2019. Vol. 345. P. 580-588. DOI: 10.1016/j.powtec.2019.01.032
- Guo-Qing Shi, Cong Han, Yan-ming Wang, He-Tang Wang. Experimental study on synergistic wetting of a coal dust with dust suppressant compounded with noncationic surfactants and its mechanism analysis // Powder Technology. 2019. Vol. 356. P. 1077-1086. DOI: 10.1016/j.powtec.2019.09.040
- Kirwin R.C. Patent № EP 0197714 A2. Method for the control of dust. Publ. 15.10.1986.
- Hetang Wang, Xiaobin Wei, Yunhe Du, Deming Wang. Effect of water-soluble polymers on the performance of dust-suppression foams: Wettability, surface viscosity and stability // Colloids and Surfaces A: Physicochemical and Engineering Aspects. 2019. Vol. 568. P. 92-98. DOI: 10.1016/j.colsurfa.2019.01.062