Evaluation of the effectiveness of water dust-suppressing emulsions based on acrylic and alkyd polymers
- 1 — Ph.D., Dr.Sci. Head of the Department Belgorod State Technological University named after V.G.Shukhov ▪ Orcid ▪ Scopus ▪ ResearcherID
- 2 — Postgraduate Student Belgorod State Technological University named after V.G.Shukhov ▪ Orcid ▪ ResearcherID
- 3 — Ph.D. Associate Professor Belgorod State Technological University named after V.G.Shukhov ▪ Orcid ▪ ResearcherID
- 4 — Postgraduate Student Belgorod State Technological University named after V.G.Shukhov ▪ Orcid ▪ ResearcherID
- 5 — Researcher Belgorod State Technological University named after V.G.Shukhov ▪ Orcid ▪ ResearcherID
Abstract
Currently, the use of special dust-suppressing reagents is promising to reduce the level of dust in the vicinity and on the territories of pits, mining and processing plants and other facilities with a high content of fine dust. The analysis of ways to reduce the dust-forming ability of inorganic dispersions with a high degree of dusting is carried out. Due to the lack of regulatory and technical documentation devoted to the standardization of quality control methods for dust-suppressing compounds, it becomes necessary to analyze existing parameters and methods for their determination in order to develop mandatory methods for controlling the properties of dust-suppressing compounds, films formed by them and consolidated systems. The study is devoted to substantiating the necessary methods for assessing the dust-forming ability of inorganic dispersions after treatment with various dust suppressants and evaluating their effectiveness. The parameters are considered and methods for quantifying the determination of the quality of the consolidated layer of dust samples using different dust-suppressing compositions are described. As a result of the analysis of the set of parameter values, it was found that the most resistant to the effects of negative factors due to the formation of a denser and more durable polymer matrix mesh are dusting surface samples treated with an emulsion of alkyd glypthalic resin on a water basis with a high agglomerating effect on particles of inorganic dispersion and the formation of a consolidated layer with a wetting angle of 92.5° and a compressive strength 0.56 MPa.
Funding
The researchwas carried out at the expense of a grant from the Russian Science Foundation N 23-19-00796.
Introduction
Dust formation at industrial facilities during the warehouse, storage and transportation of bulk materials is one of the main sources of air pollution, causing irreparable harm to not only human health [1] and causing breakdowns of special equipment.
Dust at industrial facilities (mining sites, pit or industrial roads [2], dumps [3, 4], tailings dumps [5], landfills [6], agricultural lands, etc. [7, 8]) differs in chemical composition and dispersion. Weather and natural phenomena causing wind erosion, as well as man-made processes (formation of dust clouds during blasting, arable and construction works) are considered to be decisive factors [9, 10]. The main principle of solving the problem of preventing the formation of a dust cloud is the consolidation of dust particles (their adhesion) under the action of dust-suppressing compounds (DC), which leads to the enlargement and weighting of particles of inorganic aerosol dispersion (dust-forming dispersion) [11-13]. This reduces the level of dusting, as heavy particles are less susceptible to erosion.
Despite the importance of controlling the dust-suppressing ability of a particular composition, an analysis of the scientific literature summarized in the article [14] showed that Russian and foreign researchers pay insufficient attention to methods for evaluating the properties of both the dust-suppressing composition itself and the dust-forming dispersion (DD) – dust-suppressing compound. The reasons for the difficulties and, as a result, the low coverage of the topic in scientific papers can be considered the lack of regulatory, technical and other normative documents on the standardization of quality control methods for dust suppression compounds. There is an urgent need to analyze existing parameters and methods for their determination in order to develop a mandatory list of methods for controlling the properties of dust-suppressing compounds, films formed by them and consolidated systems.
Currently, there are regulatory documents that reflect methods for determining properties, methods of application, transportation, storage and other characteristics of reagents (emulsions, fluids, foams) that are used to assess the quality of dust-suppressing compounds: GOST 33290-2015, GOST R 58952.1-2020, GOST R 51037-97, GOST R 52056-2003, GOST 30491-2012. It is also possible to use existing regulatory documentation designed for the quality of paints, adhesives or primers. However, it is important to keep in mind that all the proposed methods require adaptation to the needed control sample. For emulsions, researchers identify the following main controlled characteristics: specific consumption of the emulsion; thickness of the film coating; surface tension at the boundary “film of dust-suppressing emulsion – liquid”; wetting angle on the surface of the film of dust-suppressing emulsion [14]. In each of the studied works, the authors propose to investigate the following additional parameters that affect the dust-suppressing characteristics of polymer solutions, foams and water-based emulsions: wetting ability [15-17]; depth of penetration of the composition into the dusting surface [18]; viscosity [19]; dust residue after surface treatment of dust-forming dispersion [20-22]; morphological features of molecules (bubbles) of composition [23] and films formed after their drying [24]; dust suppression time depending on the concentration of dust particles [25, 26]; resistance to erosion with temperature changes [27, 28]; moisture retention [29]; swelling of the tread rubber of motor vehicles [30]; physical and mechanical characteristics of the film [31]; the rate of spraying of the composition onto the dust-forming dispersion [32]; IR spectra of the dust-forming dispersion before and after treatment with the composition [33].
The parameters are considered and methods for determining the quality of dust samples with a consolidated layer (CL) are described when using different dust-suppressing compounds, taking into account the operating conditions of industrial roads: the ability to agglomerate dust particles; visual assessment of the stability of dust samples treated with dust-suppressing compounds in an aqueous medium; compressive strength of samples with a consolidated layer at temperatures of 20 and 50 °C; the wetting angle of the consolidated layer of the sample; structural features of the consolidated layer of the treated dusting surface.
Methods
The analysis of the effectiveness of dust suppression and the qualitative characteristics of the polymer films formed was carried out using tap water (a common method of dedusting in industrial areas) and two samples of aqueous polymer emulsion systems: an industrial-grade emulsion – Concentrate Polymer acrylic emulsion (chosen because of the greatest similarity both in composition and in the intended area of its use – as a DC) and a synthesized emulsion of alkyd glypthalic resin. The processing of samples (cylinder sample size 3 x 3 cm was obtained by pressing at 7.5 kN pressure) of the model dispersion with dust-suppressing compounds was carried out by a single and uniform spray application over the entire surface of the cylinder with a flow rate of 0.75 l/m2.
The composition of the emulsion developed by the authors [34, 35] includes (in terms of 100 % by weight) the following components: the dispersed phase of the emulsion is alkyd glypthalic resin 56.1 %; the dispersion medium is water 37.5 %; emulsifier – AMP-95 (2-amino-2-methyl-1-propanol) – 0.3 %; phase boundary modifiers are ethylene glycol 6 % and a mixture of cobalt and zirconium siccatives 0.034 and 0.066 %, respectively. Main characteristics: the dynamic viscosity of the emulsion is up to 50.7 MPa·s; the life of the emulsion is up to 87 days; the size of the emulsion droplets is up to 3 microns; the drying time of the emulsion is 19 hours; the hardness of the film formed after complete drying of the emulsion is 0.32 c.u.; the edge angle of the film is 97.5°; free energy the surface area is 36.7 mN/m [35]. The environmental friendliness of the substances was considered at the stage of choosing the raw materials of the emulsion, it is recommended to apply the composition to the dust-forming dispersion by spraying – a protective layer is formed with a minimum thickness, which minimizes the negative impact on the ecosphere. At the same time, the content of organic substances in the developed emulsion does not exceed the content in traditionally used DC.
To evaluate the effectiveness of the emulsions under consideration, a model dispersion was used as samples of dust-forming dispersion in the form of a mixture of pulverized quartz grade B (manufacturer of OOO “OPT6”) and kaolin clay from the Latnenskoe deposit (in dry form, clay has a dusty structure) in a ratio of 3:1. The component composition of the dust selected as an aerosol-type inorganic dispersion sample is explained by the ubiquity of rock-forming minerals (quartz and kaolinite) in the composition of the vast majority of rocks and soils of the earth's crust, as well as due to the characteristics of the components (minimum porosity of quartz and the possibility of water absorption of kaolinite).
The degree of agglomeration of dust particles is determined by sieving the treated dispersion through sieves with a cell size of 0.1-10 mm and determining the partial residue on each sieve after processing the dust-forming dispersion with dust-suppressing compounds.
A visual assessment of the stability of samples with a treated surface in an aqueous medium is not a normalized parameter and was carried out to determine the possibility of further assessment of the waterproofness and swelling of the samples. The preparation of samples from a clay-sand mixture was carried out according to the standard methodology corresponding to GOST 9128-2013 “Mixtures of asphalt concrete, polymerasfalt concrete, asphalt concrete, polymerasfalt concrete for highways and airfields. Technical conditions”. The sample cylinder is treated with a dust-suppressing compound superficially by uniform spraying from a spray gun.
The study of the strength characteristics of the consolidated layer on the surface of the dust sample formed after drying of the alkyd resin emulsion was carried out according to the GOST 30491-2012 method “Organomineral mixtures and soils reinforced with organic binders for road and airfield construction” at temperatures of 20 and 50 °C with determination of the compressive strength of the cylinder samples. The sample cylinder is treated with a dust-suppressing compound superficially by uniform spraying from a spray gun. This technique is an indirect assessment of dust-suppressing properties [14], however, the method is informative from the point of view of evaluating the binding properties of the emulsion.
The edge angle was determined using a Kruss DSA 30 contact wetting angle measuring device using ADVANCED software by the recumbent drop method. Distilled water was used as the test liquid. The ADVANCED program automatically outputs the average value based on all measurements of the contact angle. The samples were prepared by pressing a mixture of dust-forming dispersion at a pressure of 7.5 kN.
The structural features of the consolidated layer of dust-forming dispersion were studied by scanning electron microscopy using a Tescan MIRA 3 LMU scanning electron microscope.
The characteristics of the dust-forming dispersion were carried out according to the methods of GOST R 51037-97 “Polymer protective insulating coatings, localizing dust-suppressing and deactivating. General technical requirements”. The study was carried out using the equipment of the High Technology Center at the BSTU named after V.G.Shukhov.
Applied concepts and their definitions:
Dust-forming dispersion (inorganic dispersion of aerosol type)is a mixture of inorganic dust particles corresponding to a number of dust classifications by dispersion – 4th and 3rd; stickiness (characteristic indicator – breaking strength of the dust layer according to E.I.Andrianov) – non-sticking; wettability – well wetted.
A dust-suppressing composition is a reagent with high dust-suppressing characteristics, the aggregate state (liquid or dry) and morphological structure (solution, foam, emulsion) of which are able to reduce the degree of dust formation of inorganic dispersions.
The consolidated layer is a temporary protective coating formed on the surface of the dust-forming dispersion after complete drying of the dust-suppressing composition.
Discussion of the results
Taking into account the intended field of application of the developed alkyd emulsion for dedusting (dusty objects of the construction and mining industries), it was necessary to quantify the complex of indicators of the consolidated layer formed after the distribution of the dust-suppressing composition. Since the developed alkyd emulsion includes products of the paint and varnish industry, and its main functional purpose is the localization of dust and the formation of a protective coating, when evaluating the dust-suppressing effectiveness from the point of view of a protective polymer coating, it is advisable to follow the requirements of GOST R 51037-97. Based on the specified regulatory document, the indicators were selected to establish the compliance of the dust-suppressing protective polymer coating formed by the developed emulsion with the regulated requirements (Table 1). The analysis of the obtained values of the normalized characteristics of the consolidated layer showed that the developed alkyd emulsion makes it possible to obtain a dust-suppressing protective coating that meets the requirements of GOST R 51037-97 in all respects.
Table 1
Characteristics of dust-forming dispersion according to GOST R 51037-97
The indicator name |
Technical requirements |
The actual value |
Preliminary surface preparation(temperature 5-30 °С, humidity up to 95 %) |
None |
None |
Degree of pelletizing, % |
>80 |
93 |
Application surface temperature, °С |
–10 … +50 |
+5 … +25 |
Holding time before the start of operation, h |
<24 |
19 |
Resistance to water, day |
> 180 |
198 |
Temperature resistance, °С |
5-30 |
79 |
Service life, day |
> 180 |
180 |
However, the use of methods for determining the normalized indicators does not allow to fully study the interaction of the dust-suppressing composition with the dust-forming dispersion. This is due to the use of regulatory techniques for evaluating a polymer coating on a hard surface (glass or metal plate). The analysis of the indicators obtained on monolithic static surfaces is necessary, but insufficient to assess the effectiveness of formulations applied to highly dispersed, conditionally mobile materials.
Due to the lack of uniform control standards fixed in regulatory documents, as well as uniform requirements for dust suppression compounds, it is very difficult to conduct a comparative assessment of the effectiveness of certain types of reagents and their compositions. Based on the analysis of the methods used by various scientific groups and the controlled parameters, a number of indicators were selected that are recommended as the most informative for proving the dust-suppressing ability of alkyd emulsions.
The main processes providing dust suppression during surface treatment with a polymer-based compound are enlargement (gluing) and film formation. The more adhesive the polymer component of the dust-suppressing composition is, the better the particle agglomeration will be. The result of assessing the degree of agglomeration of DD particles was to obtain a partial residue after sieving (the mass of the substance on each sieve). The processed model dispersion is characterized by the absence of fractions with particles less than 0.25 mm (Fig.1). The right part of the graph is of the greatest interest for evaluating the ability to agglomerate particles of the model dispersion after DC processing. Thus, agglomeration of particles with water showed the worst result – the formation of agglomerates is in the range of 1-5 mm. The partial residues on the sieves are presented in Table 2.
Table 2
The partial residues on the sieves, %
Type of processing |
The size of the sieve cells, mm |
|||
1 |
2 |
5 |
10 |
|
Water |
16.7 |
44.4 |
31.5 |
7.4 |
Acrylic emulsion |
15.9 |
52.2 |
27.1 |
4.8 |
Alkyd emulsion |
7.9 |
32.9 |
48.8 |
10.4 |
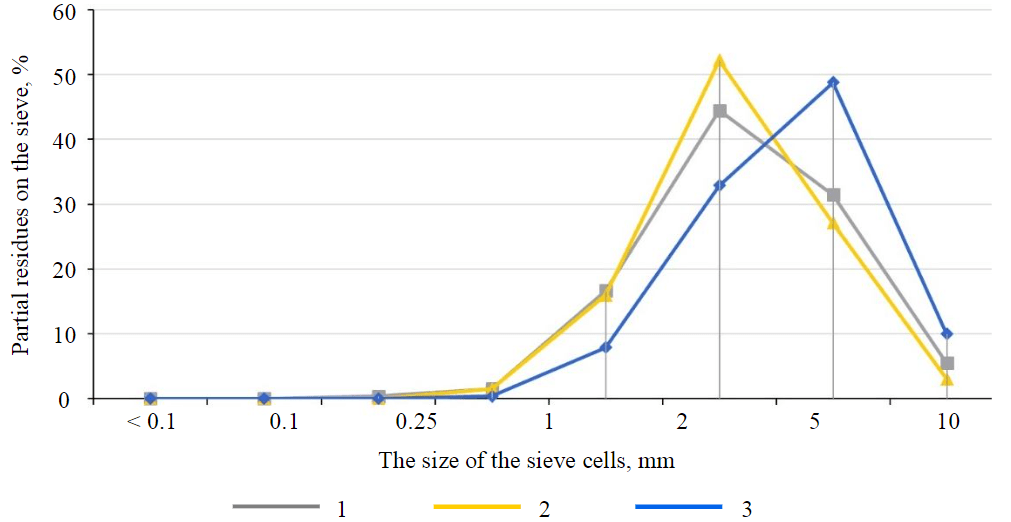
Fig.1. Granulometric composition of the model dust-forming dispersion 1 – tap water; 2 – acrylic emulsion; 3 – alkyd emulsion
The analysis of the obtained data on the granulometric composition of the treated dispersion with various dust-suppressing compositions determined by the sieve analysis method allows to judge the best ability to agglomerate the inorganic dispersion when using the developed emulsion. This is evidenced by the maximum mass of large aggregates on a sieve with a cell size of 5 mm, whereas when using water, the maximum mass of aggregates is noted on a sieve with cells of 2 mm. Its effectiveness in agglomeration of dusty particles can be explained by the best film-forming ability (stickiness) of the polymer component of the emulsion – alkyd resin, which indicates the best dust-suppressing effect.
When visually evaluating a sample of clay-sand particles treated with an acrylic emulsion (Fig.2), rapid absorption of the product into the sample surface was observed, which remains unchanged upon drying. However, when treated with a synthesized emulsion, a film is formed on the surface (before immersion in water). Then the processed samples were immersed in a container with water for a while. The assessment was performed based on the destruction of the sample in an aqueous medium with time fixation.
Three samples were taken for analysis: sample 1 – model dispersion without DC treatment; sample 2 – dispersion treated with acrylic emulsion; sample 3 – dispersion treated with synthesized emulsion.
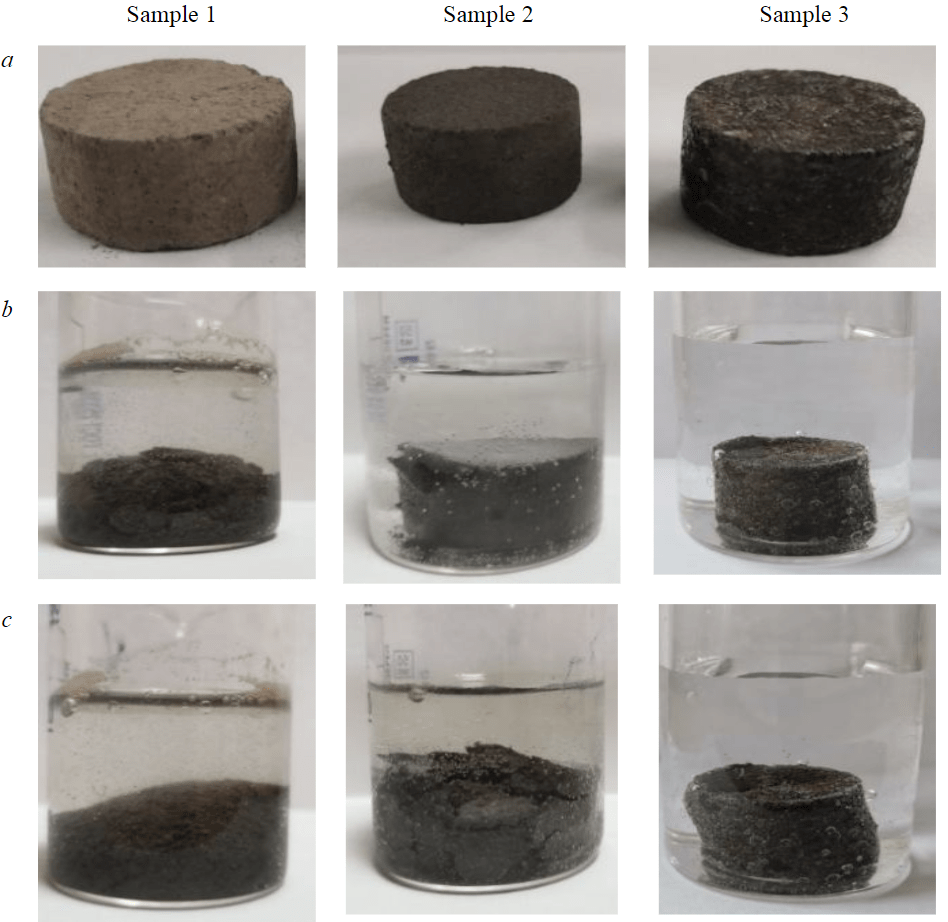
Fig.2. Destruction of samples from a mixture of dusty particles treated with dust-suppressing compounds before immersion in water (a); after 30 minutes (b); after 60 minutes (c)
The observation continued until the complete destruction of the samples in the water. Sample 1 showed the worst result with complete destruction after 30 min. Sample 2 showed partial destruction of the cylinder surface after 30 min and complete destruction after an hour. Sample 3 showed the best result after 30 min in the water – a flat surface without visible destruction. After an hour, the destruction of the walls in sample 3 is noted with the internal preservation of the shape. Thus, a visual assessment of the treated samples from a model clay-quartz mixture of dust particles showed that the consolidated layer formed by the synthesized emulsion has the best exposure in water due to the formation of a more durable polymer film on the surface of the compressed dispersion.
Analysis of the compressive strength of cylinders treated with surface dust-suppressing compounds showed that the strength of samples treated with polymer emulsions at 20 °C is higher than that treated at 50 °C (Table 3). However, when comparing samples treated with emulsions, the highest strength values are observed in samples whose consolidated layer was formed after complete drying of the alkyd resin emulsion at both 20 °C and 50 °C; compared with samples treated with acrylic emulsion, it is 32 % higher at 20 °C and 35 % – at 50 °C. An increase in the strength of the sample, the surface of which was treated with an emulsion of alkyd glypthalic resin, indicates the formation of a more durable polymer matrix, which is probably due to the high adhesion (stickiness) of the resin to dust particles.
Table 3
Soil strength indicators
Type of sample |
Compressive strength at various temperatures, MPa |
|
20 °С |
50 °С |
|
Treated with an acrylic emulsion “Concentrate Polymer” |
0.38 |
0.13 |
Treated with an emulsion of alkyd glypthalic resin |
0.56 |
0.2 |

Fig.3. Values of the wetting angle of samples from a mixture of dusty particles treated with dust-suppressing compounds in a test liquid (water): a – without treatment (38.5°); b – a sample treated with an acrylic emulsion “Concentrate Polymer” (78.9°); c – a sample treated with an emulsion of alkyd glypthalic resin(92.5°)
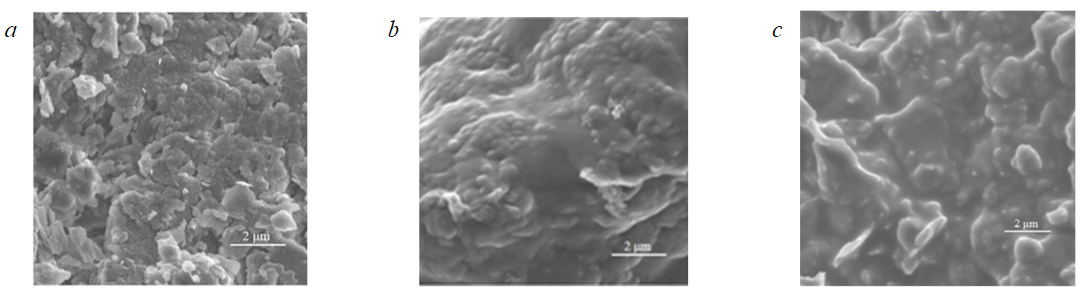
Fig.4. Characteristics of the surface of the inorganic dispersion after treatment with dust-suppressing compounds: a – sample without treatment (control); b – sample treated with acrylic emulsion “Concentrate Polymer”; c – sample treated with alkyd emulsion
To study the effectiveness of dust-suppressing films formed on the treated surface and their insulating ability, a change in the wetting edge angle was investigated. The higher the value of the wetting angle, the higher the insulating ability of the film obtained during the consolidation of dusty particles, expressed in the hydrophobic ability.
The analysis of the obtained values (Fig.3) showed the highest efficiency of the alkyd-based dust suppression compound. Thus, the values of the wetting edge angle of the consolidated layer formed when using an alkyd emulsion are one and a half times higher than when using an acrylic emulsion, and three times higher than that of the original (untreated) composition. The values of the limiting wetting angle of the sample surface when using a synthesized emulsion of more than 90° indicate hydrophobicity.
The final stage of the study was to identify the features of the structure formation of alkyd oligomer films on a substrate of dusty particles. The analysis of the polymer film structure formation was carried out after the emulsion was cured (Fig.4). Despite the fact that polymer emulsions were used in both cases, the structure of the sample of dusty particles treated with acrylic emulsion (Fig.4, b) does not visually differ from the original sample without treatment. Probably, the presence of a polymer matrix is not fixed due to the low polymer content or low viscosity of the emulsion, which requires two or three surface treatments. This also explains the worst indicators of the parameters considered.
A comparative assessment of the microstructure shows (Fig.4, c) the effectiveness of the synthesized emulsion as a means of dust suppression in terms of the ability to form a protective film on the surface of the dusting model system. The light areas are well distinguished in the structure, evenly distributed over the surface of the sample from a mixture of dusty particles. In addition, it is noted that when using a dust-suppressing synthesized composition, the surface of the sample changes from a loose granular to a smoother monolithic one. This is due to the high adhesion (good stickiness of the resin droplet to the particle of the model dispersion) of the selected polymer component of the resulting emulsion, as well as its high viscosity (compared to the acrylic emulsion “Concentrate Polymer”) due to the excess resin in the composition.
Conclusion
The analysis of the parameters determined in the framework of the study made it possible to qualitatively and quantitatively determine the physico-mechanical, colloidal-chemical properties and structural features of the consolidated layer of dust-forming dispersion formed on the surface of an inorganic aerosol-type dispersion after drying of the polymer composition.
The analysis of the granulometric composition of dust treated with various reagents by the sieve analysis method showed a better ability to agglomerate dust when using an alkyd emulsion. This is evidenced by the maximum mass of large aggregates on a sieve with a mesh size of 5 mm, whereas when using water, the maximum mass of aggregates is 2 mm. The high agglomerating ability is explained by the best film-forming ability (stickiness) of the alkyd resin.
An analysis of the assessment of water resistance of dust samples treated with two types of formulations showed that the consolidated layer formed by an alkyd emulsion has the best exposure in water. This is explained by the formation of a more durable polymer film on the surface of the samples, which is confirmed by the results of an assessment of the structural features of the protective coating and a high value of the wetting angle (92.5°). The compressive strength of the samples when using both emulsions at 50 °C is reduced by half, which indicates a negative effect of temperature on the strength characteristics of the protective polymer layer and a limited temperature range of the composition used during its operation in industrial areas, but not a deterioration in the dust-suppressing effectiveness of the alkyd resin emulsion.
References
- Vishnevsky A. The use of industrial wastes for dust control of roads. Transbaikal State University Journal. Vol. 23. N 11, p. 12-18 (in Russian). DOI: 10.21209/2227-9245-2017-23-11-12-18
- Buryanov I.A., Logachev K.I., Uvarov V.A. Determination of the main properties of dust particles in the grinding area. Bulletin of Belgorod State Technological University named after V.G.Shukhov. Vol. 5. N 10, p. 23-32 (in Russian). DOI: 10.34031/2071-7318-2020-5-10-23-32
- Shuvalov Yu.V., Veselov A.P., Bulbashev A.P. et al.Dust control in mining enterprises using long- and short-lived foams of increased multiplicity. Gornyi informatsionno-analiticheskii byulleten. 2007. N S12, p. 171-179. (in Russian).
- Kireeva E.V., Kondrasheva N.K., Zyryanova O.V. et al. Aqueous film-forming dispersions for dust collecting compounds. Lakokrasochnye materialy i ikh primenenie. N 7-8, p. 42-45 (in Russian).
- Ospanova Zh.B., Toktagul S., Tasmagambetova A., Asadov M. Preparation of foaming agents for dust suppression of coal particles. Chemical Bulletin of Kazakh National University. Vol. 94. N 3, p. 12-18 (in Russian). DOI: 10.15328/cb1071
- Shegolkov Y.S., Kolosov A.A., Pasechnaya V.Y. Effect of dispersion of industrial dust on the occupational morbidity of workers. Fundamentalnye i prikladnye nauchnye issledovaniya: aktualnye voprosy, dostizheniya i innovatsii: sbornik statei VIII Mezhdunarodnoi nauchno-prakticheskoi konferentsii, 15 oktyabrya 2017, Penza, Rossiya: v 4 chastyakh. Penza: Nauka i prosveshchenie, 2017. Part 1, p. 175-177 (in Russian).
- Wu Mingyue, Hu Xiangming, Zhang Qian et al.Study on preparation and properties of environmentally-friendly dust suppressant with semi-interpenetrating network structure. Journal of Cleaner Production. 2020. Vol. 259. N 120870. DOI: 10.1016/j.jcle2020.120870
- Wenjin Niu, Wen Nie, Mingyue Yuan et al. Study of the microscopic mechanism of lauryl glucoside wetting coal dust: Environmental pollution prevention and control. Journal of Hazardous Materials. 2021. Vol. 412. N 125223. DOI: 10.1016/j.jhazmat.2021.125223
- Romanchenko S.B., Naganovckiy Yu.K., Kornev A.V. Innovative ways to control dust and explosion safety of mine Journal of Mining Institute. 2021. Vol. 252, p. 927-936. DOI: 10.31897/PMI.2021.6.14
- Strokova V.V., Ishmukhametov E.M., Esina A.Yu. et al. Water-based dust suppressing compositions: analysis of the state and prospects of development. Bulletin of the Technological University. Vol. 24. N 12, p. 5-38 (in Russian).
- Lyashenko V.I., Gurin A.A. Justification of environmental protection technologies and means for dust suppression at tailings ponds of hydrometallurgy. Mining Informational and Analytical Bulletin. N 9, p. 58-72 (in Russian). DOI: 10.25018/0236-1493-2018-9-0-58-72
- Dabizha O.N., Bespolitov D.V., Konovalova N.A. et al. Application of the Stabilizing Polymer Additives for Protection of Dump Overflow from Wind Erosion. Problems of Contemporary Science and Practice. Vernadsky University. N 1 (79), p. 26-39 (in Russian). DOI: 10.17277/voprosy.2021.01.pp.026-039
- Jianwei Cheng, Xinrui Zheng, Yadong Lei et al.A compound binder of coal dust wetting and suppression for coal pile. Process Safety and Environmental Protection. 2021. Vol. 147, p. 92-102. DOI: 10.1016/j.psep.2020.08.031
- Jiayi Yan, Wen Nie, Haihan Zhang et al.Synthesis and performance measurement of a modified polymer dust suppressant. Advanced Powder Technology. 2020. Vol. Iss. 2, p. 792-803. DOI: 10.1016/j.apt.2019.11.033
- Kai Wang, Yuchen Zhang, Weiyao Cai et al.Study on the microscopic mechanism and optimization of dust suppression by compounding biological surfactants. Colloids and Surfaces A: Physicochemical and Engineering Aspects. 2021. Vol. 625. N 126850. DOI: 10.1016/j.colsurfa.2021.126850
- Strokova V.V., Ishmukhametov E.M., Esina A.Yu. Evaluation of emulsifier effect on the properties of water-based alkyd emulsion. Chemical Bulletin. Vol. 5. N 3, p. 39-48 (in Russian).
- Strokova V.V., Ishmukhametov E.M., Esina A.Yu. Analysis of methods for obtaining water based alkyd emulsion. Bulletin of the Technological University. Vol. 25. N 7, p. 43-48 (in Russian). DOI: 10.55421/1998-7072_2022_25_7_43
- Sachkova O.S., Samoilov V.V., Elin A.M. Estimate researches on efficiency and safety of a biological dust suppression preparation. Science and Technology in Transport. N 2, p. 101-107 (in Russian).
- Akimov A.M., Kotelnikova S.A. Investigation of dust-retaining solutions during transportation of rock masses. PowerPlantsandTechnologies. Vol. 7. N 2, p. 148-151 (in Russian).
- Qiu Bao, Wen Nie, Changqi Liu et al. The preparation of a novel hydrogel based on crosslinked polymers for suppressing coal dusts. Journal of Cleaner Production. 2020. Vol. 249. N 119343. DOI: 10.1016/j.jclepro.2019.119343
- Evtushenko A.I., Evtushenko I.I., Nor-Arevyan S.L., Belskaya Y.B. On the question of research ways to improve the effectiveness of dust control irrigation. Engineering Journal of Don. N 3 (42), p. 9 (in Russian).
- Ivanov A.V., Smirnov Yu. D., Chupin S.A. Development of the concept of an innovative laboratory installation for the study of dust-forming surfaces. Journal of Mining Institute. Vol. 251, p. 757-766. DOI: 10.31897/PMI.2021.5.15
- Xiaobin Wei, Hetang Wang, Ying Xie, Yunhe Du. An experimental investigation on the effect of carboxymethyl cellulose on morphological characteristics of dust-suppression foam and its mechanism exploration. Process Safety and Environmental Protection. 2020. Vol. 135, p. 126-134. DOI: 10.1016/j.psep.2019.12.009
- Alosmanov M.S., Ataev M.Sh., Sultanzade S.S. et al. A means for dust control. Herald of Science and Education.1. N 2 (38), p. 17-21 (in Russian). DOI: 10.20861/2312-8089-2018-38-003
- Qing Guo, Wanxing Ren, Jingtai Shi. Foam for coal dust suppression during underground coal mine tunneling. Tunnelling and Underground Space Technology. Vol. 89. 2019, p. 170-178. DOI: 10.1016/j.tust.2019.04.009
- Zongqi Liu, Gang Zhou, Jinjie Duan et al.Preparation of composite high-efficiency dust suppressant and relevant molecular dynamics simulation for wetting coal surface. Fuel. 2021. Vol. 296. N 120579. DOI: 10.1016/j.fuel.2021.120579
- Podobrazhin S.N. Prevention of dust emissions to the mine atmosphere during wind erosion. Occupational Safety in Industry. N 6, p. 16-22 (in Russian).
- Ping Chang, Zidong Zhao, Guang Xu et al. Evaluation of the coal dust suppression efficiency of different surfactants: A factorial experiment. Colloids and Surfaces A: Physicochemical and Engineering Aspects. 2020. Vol. 595. N 124686. DOI: 10.1016/j.colsurfa.2020.124686
- Nguyen V.G. Patent № US 8052890 B2. Compositions for dust suppression and methods. Publ. 22.12.2005.
- Rulin Liu, Gang Zhou, Kaili Wang et al.Experimental investigation on highly efficient collection and cleaning for fine coal dust particles by dry-wet mixed chemical method. Journal of Environmental Chemical Engineering. 2021. Vol. 9. Iss. 5. N 105861. DOI: 10.1016/j.jece.2021.105861
- Anagnostopoulos C.A., Kandiliotis P., Lola M., Karavatos S. Improving Properties of Sand Using Epoxy Resin and Geotechnical and Geological Engineering. 2014. Vol. 32. Iss. 4, p. 859-872. DOI: 10.1007/s10706-014-9763-6
- Hetang Wang, Yunhe Du, Xiaobin Wei, Xinxin He. An experimental comparison of the spray performance of typical water-based dust reduction media. Powder Technology. 2019. Vol. 345, p. 580-588. DOI: 10.1016/j.powtec.2019.01.032
- Guo-Qing Shi, Cong Han, Yan-ming Wang, He-Tang Wang. Experimental study on synergistic wetting of a coal dust with dust suppressant compounded with noncationic surfactants and its mechanism analysis. Powder Technology. 2019. Vol. 356, 1077-1086. DOI: 10.1016/j.powtec.2019.09.040
- Kirwin R.C. Patent № EP 0197714 A2. Method for the control of dust. Publ. 15.10.1986.
- Hetang Wang, Xiaobin Wei, Yunhe Du, Deming Wang.Effect of water-soluble polymers on the performance of dust-suppression foams: Wettability, surface viscosity and stability. Colloids and Surfaces A: Physicochemical and Engineering Aspects. 2019. Vol. 568, p. 92-98. DOI: 10.1016/j.colsurfa.2019.01.062