Laboratory studies of hydraulic fracturing of intersecting boreholes in a non-uniform stress field
- 1 — Ph.D. Senior Researcher Chinakal Institute of Mining, Siberian Branch, Russian Academy of Sciences ▪ Orcid
- 2 — Junior Researcher Chinakal Institute of Mining, Siberian Branch, Russian Academy of Sciences ▪ Orcid
- 3 — Ph.D. Researcher Chinakal Institute of Mining, Siberian Branch, Russian Academy of Sciences ▪ Orcid
- 4 — Research Engineer Chinakal Institute of Mining, Siberian Branch, Russian Academy of Sciences ▪ Orcid
Abstract
This study focuses on the features of hydraulic fracture propagation in intersecting boreholes in polymethyl methacrylate blocks in a non-uniform stress field. Glycerol aqueous solution and plasticine were used as the working fluids. According to linear fracture mechanics, a stress concentrator at the borehole intersection contributes to the beginning of crack formation, with further crack propagation occurring in the plane containing their axes. The relevance of this study is due to the search for innovative approaches and the development of technological solutions to address the issue of effective longitudinal crack formation and its further propagation in a rock mass under unfavourable stress field conditions. This paper provides a scheme of laboratory stand operation and a general view of the sealing packers used to isolate a specified interval when performing tests. The graphs of glycerol pressure versus injection time are presented, and the breakdown pressure in the blocks is specified. The shape of fractures formed during the indentation of plasticine into the borehole system was investigated. The findings of physical modelling indicate that longitudinal cracks are predominantly formed in the boreholes. The deviation of the crack trajectory from the vertical plane containing the borehole axes is primarily affected by the magnitude of the horizontal compressive stress field rather than the increase in the angle between them. In addition, the angles of inclination of the longitudinal crack plane measured at its intersection with the side face of the block are specified.
Funding
The study was supported by the Russian Science Foundation and the Government of the Novosibirsk region, project N 22-27-20061.
Introduction
The emergence and development of hydraulic fracturing (HF) is closely associated with enhanced oil recovery from producing wells [1-4]. This approach is commonly used due to the relatively straightforward underlying principle. The final shape of a crack in rocks largely depends on the direction and magnitude of compressive stresses [5, 6]. During hydraulic fracturing operations conducted at significant depths commonly observed in numerous oil and gas fields, the possible orientation of the resulting cracks is limited by the maximum vertical stress. In such conditions, the initiation of a longitudinal crack in a vertical well or a radial transverse crack in a horizontal well is most often observed.
The implementation of the HF method in mines is complicated by some features. The challenge in accurately predicting the path of cracks to be formed is due to high horizontal stresses [7, 8] as well as the impact of nearby underground workings and inseam boreholes on the stress state of the rocks. Additionally, there are various tasks to be tackled, such as intensifying the methane drainage from coal seams [9-12], controlling hard roof collapse [13-16], protecting underground workings from pressure filtration [17], and conducting in situ stress measurements [18-21]. Of interest are methodological and technical solutions aimed at increasing heavy oil production by hydraulic fracturing in the Yaregskoye field, which is developed using the thermal mining method [22].
Increasing the efficiency of the mine modification of the HF method requires establishing the features of crack propagation in a non-uniform stress field in laboratory conditions. Most testing systems used for these purposes are specifically engineered to analyze the initiation of cracks in a core subjected to axial loading and uniform compression along its side surface [23-25]. Such experimental setups do not accurately replicate the reservoir conditions and do not allow addressing the problems characteristic of underground mining.
The increasing popularity of laboratory units that can subject cubic samples to true triaxial loading is driven by the need for reliable results in hydraulic fracturing physical modelling [26, 27]. Such cubic samples should be sufficiently large, with an edge length of 150-200 mm or more, to exclude the influence of edge effects on crack propagation and to incorporate models of underground working or several boreholes.
The results of previous studies demonstrate that the crack path can be controlled in several ways. For example, it is possible to use various technical means for cutting initiating slots on borehole walls [28], performing directional loading or unloading in the target interval [29, 30], creating additional cracks in advance to alter the local stress field [31], or changing the properties of the working agent [32] and parameters of its injection into the rock mass [33, 34]. In addition, crack growth direction is influenced by various factors, such as the complex geometry perforation of the casing, the specific arrangement of several boreholes of different directions, and the presence of additional sidetracks.
One promising way to create longitudinal cracks is to perform HF in intersecting boreholes. Cracks are assumed to grow in the plane containing their axes. A similar approach was used in the development of directional hydraulic fracturing technology, which involves the creation of several radial boreholes of small diameter from a vertical one and further injection of working fluid into the formed system [35]. It has been shown that a crack is highly likely to initiate in the plane formed by radial boreholes, regardless of the stress field within the massif. Additionally, the influence of the relative position of radial boreholes on fracture propagation was studied [36]. The experimental results demonstrate that increasing the angle between the borehole axis and the direction of maximum stress results in a higher breakdown pressure.
A similar solution for the in-mine hydraulic fracturing of a coal seam yielded a high convergence of the results of mathematical modelling and experimental measurements [37]. The application of the developed technology was found to reduce the breakdown pressure and allow the direction of the initial growth of cracks to be controlled.
This study investigates the possibility of longitudinal crack formation between intersecting boreholes in a stress field unfavourable for its propagation. During the experiments, such a field was created by applying the maximum stress perpendicular to the plane containing the borehole axes.
Methods
A laboratory system was developed and implemented to study the HF process in cubic blocks. This system was installed on the basis of a hydraulic press PG-100. Presented below are the specifics regarding the operation of the system. The sample compression in a horizontal plane in two orthogonal directions is performed using four flat jacks DN10P10 with a load capacity of 10 tf installed in a load-bearing frame. A similar jack is fixed on the upper part of the frame to provide loading along the vertical axis. The sample can be independently loaded in a triaxial fashion by connecting the jacks separately to the high-pressure manual pump. A more comprehensive description of the laboratory system design can be found in [38, 39]. A schematic diagram of the system is illustrated in Fig.1, a.

Fig.1. A schematic diagram of the laboratory system (a) and a plexiglass block in a testing cell prepared for indentation of plasticine (b)
1 – manual pump; 2 – pressure gauge; 3, 8 – collectors; 4 – shut-off valve; 5 – high-pressure pipelines; 6 – hydraulic flat jack; 7 – sample with intersecting boreholes; 9 – pressure sensor; 10 – laptop computer; 11 – data communication channel; 12 – pressure data logger; 13 – mechanical syringe pump
The collection and recording of data during the experiments were conducted using a pressure sensor, specifically the MIDA-PI-51P, which was connected to a data logger through a cable. The logger is equipped with a 24-bit analogue-to-digital converter (ADC), which allows the signal to be transmitted to a laptop via Bluetooth for further processing and visualization [40].
Physical modelling of hydraulic fracturing was performed in artificial blocks made of polymethyl methacrylate (plexiglass) with an edge length of 180 mm. Two factors influenced the choice of materials for this study. The first is optical transparency, which facilitates accurate control of crack growth without the need for additional technical means. The second is the brittle fracture that occurs when a crack propagates in the plexiglass. This fracture is characterized by the absence of any significant plastic component, making it possible to exclude its effect on the final crack path. The analysis can then focus only on the impact of compressive stresses and the angle between intersecting boreholes. The combination of these features and the similarity of the mechanical properties of plexiglass (compressive strength of about 70 MPa) and rock massif, led to its widespread use in HF modeling in laboratory conditions [41-43].
Two intersecting boreholes with a diameter of 14 mm were created in each block. One of the boreholes was vertical, with the other forming an angle γ of 30 or 60 deg. The bottom of the inclined borehole was inside the block, with its head sealed by a device equipped with two rubber rings (Fig.2, a) [44].

Fig.2. Sealing device for isolating an inclined borehole (a) and a double packer tool (b)
Two different working fluids were used in the laboratory experiment: a coloured aqueous solution of distilled glycerol (GOST 6824-96) and plasticine. In the first case, a vertical borehole was drilled through the sample, and the fracturing interval was isolated by a special double packer tool (Fig.2, b). Glycerol was injected using a mechanical syringe pump. In the second case, the distance from the bottom of the vertical borehole to the lower face of the block was approximately 20 mm. The plasticine was pressed by tightening the bolt, with a thread created in the upper part of the borehole (see Fig.1, b). Figure 3 displays the location and type of boreholes in the block, depending on the working fluid used and the direction of compressive stresses [44].
In accordance with the main purpose of laboratory tests, Sxx was specified as the maximum compressive stress in the experiment. The excess of this particular stress over the others affects the rate of rotation and the deviation of the formed longitudinal fracture from the plane defined by the intersecting boreholes. The features of hydraulic fracture propagation in a similar problem statement were investigated using numerical analysis [45] and physical modelling on sand concrete samples [46]. Table 1 provides the angles γ for all manufactured blocks, the loading conditions during the physical modelling process, and the working fluid used for HF [44].

Fig.3. The location and type of boreholes in the block during fracturing with glycerol (a) and plasticine (b) in a compressive stress field
Table 1
The main characteristics of the blocks and experimental parameters
Block number |
Angle γ, deg |
Loading conditions, MPa |
Working fluid |
||
Sxx |
Szz |
Syy |
|||
1 |
30 |
1.3 |
1.0 |
1.0 |
Glycerol |
2 |
60 |
1.3 |
1.0 |
1.0 |
Glycerol |
3 |
30 |
1.3 |
0 |
1.0 |
Plasticine |
4 |
60 |
1.3 |
0 |
1.0 |
Plasticine |
5 |
30 |
1.5 |
0 |
1.0 |
Plasticine |
6 |
60 |
1.5 |
0 |
1.0 |
Plasticine |
Results and discussion
During the hydraulic fracturing of block 1, two independent cracks were formed within the boreholes and partially merged near the stress concentrator (Fig.4, a, b). The resulting fracture exhibited a distinct deviation from the plane encompassing the axes of the boreholes, with glycerol leakage observed on the lower face of the block. The breakdown pressure, Pb, observed during the experiment was 11.9 MPa, with the residual pressure measuring 0.6 MPa at the end of the test.
In block 2, the crack was formed at a fairly high pressure of 33.5-37.2 MPa (residual pressure of 0.81 MPa), which is almost three times higher than that recorded for block 1. This significant discrepancy can be attributed to variations in the borehole wall conditions and the structural features of specific blocks. At the same time, a rather clear longitudinal fracture connecting both boreholes was formed in block 2 due to virtually no differences between the horizontal stresses Sxx and Syy for such a high value of Pb pressure (Fig.4, c, d). With the deviation of the crack plane from the vertical of 10 deg, the crack was visually observed to extend to the side and bottom faces of the block [44].

Fig.4. The photographs of the cracks formed during the injection of glycerol in block 1 (a, b) and block 2 (c, d)
Glycerol injection pressure graphs for the cases described are shown in Fig.5. The injection rate was kept constant at approximately 10 ml/min.
The observed pressure change in block 1 implies that the packers were deformed and compressed from the load chamber before the crack formation, resulting in a minor depressurization of the interval isolated by the packers (Fig.5, a). When a maximum pressure of 37.2 MPa was reached in block 2, the leakage of working fluid from the fracturing interval through the packers was also observed. Following the cessation of the leakage, a subsequent rise in glycerol pressure due to its injection by a mechanical syringe pump produced a crack at 33.5 MPa (see Fig.5, b). A lower pressure value may be associated with irreversible microdestruction of the material around the borehole [47].
In a series of tests, plasticine as the working fluid was indented through the vertical borehole at Szz = 0. The procedure involved placing and tightly packing the plasticine into intersecting boreholes, followed by installing the sealing device into the inclined borehole and tightening the metal bolt along the thread previously cut on the vertical borehole wall. The gradual introduction of plasticine into the cracks caused enough pressure to break the plexiglass. The breakdown pressure was not recorded.
During the experiments conducted on blocks 3 and 4, the compressive stress ratio was found to be Sxx = 1.3Syy. During the injection of plasticine, crack formation began in both boreholes, and then the growing cracks merged into a single longitudinal fracture (Fig.6). Special attention should be given to the intricate geometry of the resulting cracks, their curvature, and twisting around the borehole, with these effects being more pronounced when γ = 60°. The results of other laboratory studies provided evidence for the creation of branched fracture systems from a single borehole with increasing viscosity of the working fluid [48].
According to the test conditions in blocks 5 and 6, the maximum compressive stress Sxx was one and a half times higher than Syy. At the same time, a similar development of cracks was observed as in the previous experiment (Fig.7). In block 5, the heterogeneity and delamination in the horizontal plane owing to the plasticine indentation, the vertical growth of the crack stopped. Previous laboratory experiments have shown similar findings regarding the interplay between created and pre-existing cracks under compressive stresses [49-51]. In block 6, the most challenging conditions were created for the formation of a single longitudinal fracture, with γ = 60°. In this case, an incomplete connection of the boreholes by HF was observed, including due to the rotation of the crack plane growing in the inclined borehole (Fig.7, c).

Fig.5. Glycerol injection pressure graphs as a function of injection time t for block 1 (a) and block 2 (b)
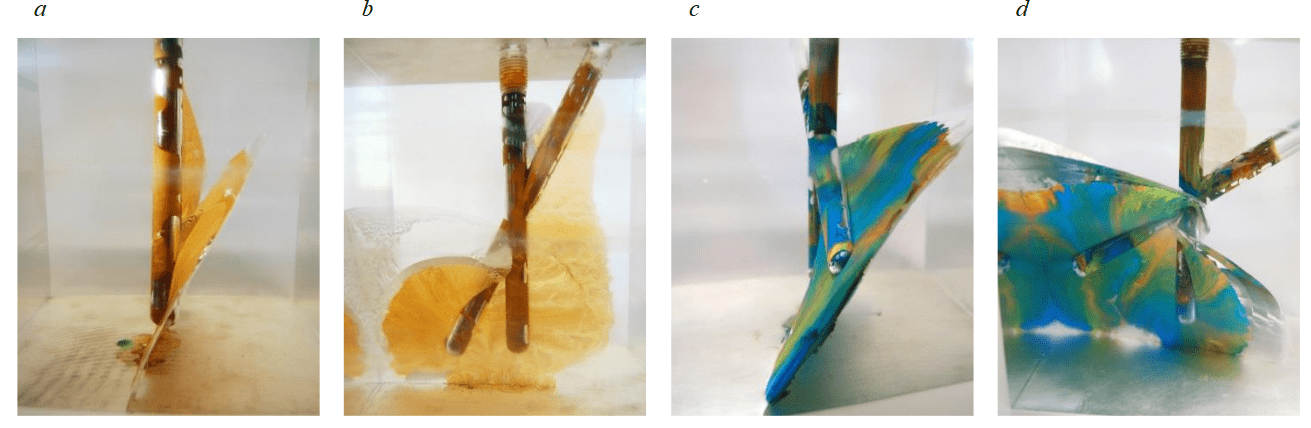
Fig.6. The photographs of the cracks formed during the indentation of plasticine in block 3 (a, b) and block 4 (c, d)

Fig.7. The photographs of the cracks formed during the indentation of plasticine in block 5 (a, b) and block 6 (c, d)
In order to assess the influence of experimental conditions on the final shape of the cracks formed in blocks 3-6, we measured the inclination angle of the longitudinal fracture plane at its exit to the side face of the block. For convenience, the angle measured from the vertical will be referred to as α, with its values given in Table 2.
Table 2
The value of angle α for blocks 3-6
Blocknumber |
Loading conditions, MPa |
Angle γ, deg |
Angle α, deg |
|
Sxx |
Syy |
|||
3 |
1.3 |
1.0 |
30 |
29 |
4 |
1.3 |
1.0 |
60 |
36 |
5 |
1.5 |
1.0 |
30 |
44 |
6 |
1.5 |
1.0 |
60 |
48 |
The findings demonstrate that the crack plane in a non-uniform stress field is more effectively stabilized when boreholes are closely spaced (γ = 30°). The deviation from the vertical plane containing the borehole axes was estimated to be 29° and 44° at Sxx = 1.3 and 1.5 MPa, respectively. The analysis of the angles α obtained during the HF of blocks 4 and 5 revealed the following features. Despite the significantly large distance between the walls of the boreholes far from the concentrator area in block 4 (γ = 60°) and the limited potential of this scheme to keep the crack in a given plane, the angle α was found to be smaller than in block 5 (γ = 30°). These results indicate that the compressive stress field parameters have a stronger influence on the deviation of the longitudinal fracture from the vertical plane containing the borehole axes compared to the increase in the angle γ. The earlier findings demonstrate that, given a uniform stress field, the crack propagation caused by the indentation of plastic substances tends to occur in the plane of the boreholes or along the initially specified direction [52].
The features of crack growth established in the paper can be used in practice when designing HF operations carried out in mine workings. The stresses applied to the cubic sample during tests were limited by the technical capabilities of the laboratory system and were equivalent to the lithostatic pressure of rocks at a depth of about 200 m. This corresponds to many mineral deposits extracted by the underground mining method, including the Yaregskoye field of high-viscosity oil, uranium deposits of the Streltsovskoye ore field, the Khandiza* polymetallic deposit (Uzbekistan), Mezhegeyskoye, Karagaylinskoye coal deposits and others [53-56].
The ratios between maximum and minimum compressive stresses (1.3-1.5) used in the experiments are observed in many mined seams and fields. The results of studies of natural stress state in the upper part of the cross section of domestic and foreign deposits are summarized in [57]. It is noted that horizontal stresses are widely exceeded over vertical ones in both igneous and sedimentary metamorphosed rocks, in some cases by a factor of 10. Similar results are also given in publications [56, 58], describing the distribution of active stresses in coal mines in China.
The success of the in-mine implementation of the approach studied in this article depends on the possibility of forming a stress concentrator in the rock mass due to the intersection of boreholes. In underground workings, this can be achieved by installing an oriented wedge-deflector in a given place of a horizontal in-seam borehole and then cutting a sidetrack from it [59]. The Y-shaped system of the borehole and sidetrack created in this way will have the necessary geometry for solving the existing problem. Then the borehole section with the sidetrack is sealed using a packer and the working fluid is pumped in. The viscosity of the fluid can be increased by special chemical additives or two-component resins with a pre-selected polymerization time [60].
Conclusion
The HF method can be used to significantly improve the development of mineral deposits by creating cracks in a specific direction. In mine environments, the formation of longitudinal cracks can be a viable solution to address specific mining issues. This study aimed to explore the potential for developing longitudinal fractures within a system of intersecting boreholes, especially when the direction of maximum stress was perpendicular to the plane containing their axes.
The experiments revealed the tendency for the cracks to initiate independently in vertical and inclined boreholes. However, with further growth, they combined and were stabilized by the boreholes to form a single fracture, also due to the area close to the concentrator. Under the most unfavourable conditions (Sxx = 1.5Syy, γ = 60°), the incomplete connection of the boreholes by HF was observed upon plasticine indentation, partially due to the rotation of the plane of the crack growing in the inclined borehole. Particular emphasis should be placed on the complex geometry of the resulting cracks, their curvature, and twisting around the boreholes, with these effects more pronounced when γ = 60°.
The physical modelling findings indicate that the parameters of the horizontal compressive stress field have a greater effect on the deviation of the longitudinal crack from the vertical plane containing the borehole axes compared to the increase in the angle between them. Measuring the angle of inclination of the longitudinal crack at its intersection with the side face of the block revealed that closely spaced boreholes (γ = 30°) better stabilize the fracturing plane in a given non-uniform stress field.
References
- Koplos J., Tuccillo M.E., Ranalli B. Hydraulic fracturing overview: How, where, and its role in oil and gas. Journal AWWA. 2014. Vol. 106. Iss. 11, p. 38-46. DOI: 10.5942/jawwa.2014.106.0153
- Bin Chen, Barboza B.R., Yanan Sun et al. A Review of Hydraulic Fracturing Simulation. Archives of Computational Methods in Engineering. 2022. Vol. 29. Iss. 4, p. 2113-2170. DOI: 10.1007/s11831-021-09653-z
- Filippov Е.V., Zakharov L.A., Martyushev D.A., Ponomareva I.N. Reproduction of reservoir pressure by machine learning methods and study of its influence on the cracks formation process in hydraulic fracturing. Journal of Mining Institute. Vol. 258, p. 924-932. DOI: 10.31897/PMI.2022.103
- Bosikov I.I., Klyuev R.V., Mayer A.V. Comprehensive assessment of hydraulic fracturing technology efficiency for well construction during hydrocarbon production. Journal of Mining Institute. Vol. 258, p. 1018-1025. DOI: 10.31897/PMI.2022.98
- Bakhshi E., Golsanami N., Lianjun Chen. Numerical Modeling and Lattice Method for Characterizing Hydraulic Fracture Propagation: A Review of the Numerical, Experimental, and Field Studies. Archives of Computational Methods in Engineering. 2021. Vol. 28. Iss. 5, p. 3329-3360. DOI: 10.1007/s11831-020-09501-6
- Dutler N., Valley B., Gischig V. et al. Hydraulic fracture propagation in a heterogeneous stress field in a crystalline rock mass. Solid Earth. 2019. Vol. 10. Iss. 6, p. 1877-1904. DOI: 10.5194/se-10-1877-2019
- Kang H., Zhang X., Si L. et al. In-situ stress measurements and stress distribution characteristics in underground coal mines in China. Engineering Geology. 2010. 116. Iss. 3-4, p. 333-345. DOI: 10.1016/j.enggeo.2010.09.015
- Lovchikov A.V. Difference in rockburst hazard in ore and coal mines. IOP Conference Series: Earth and Environmental Science. 2018. Vol. 134. N 012039. DOI: 10.1088/1755-1315/134/1/012039
- Qian Li, Yiyu Lu, Zhaolong Ge et al. A New Tree-Type Fracturing Method for Stimulating Coal Seam Gas Reservoirs. Energies. 2017. Vol. 10. Iss. 9. N 1388. DOI: 10.3390/en10091388
- Yubing Liu, Zuxun Zhang, Bozhi Deng, Minghui Li. Liquid carbon dioxide fracturing application and its effect on gas drainage in low permeability coal seams of underground coal mine. Energy Sources, Part A: Recovery, Utilization, and Environmental Effects. 2023. Vol. 45. Iss. 3, p. 6534-6546. DOI: 10.1080/15567036.2019.1675809
- Slastunov S., Kolikov K., Batugin A. et al. Improvement of Intensive In-Seam Gas Drainage Technology at Kirova Mine in Kuznetsk Coal Basin. Energies. 2022. Vol. 15. Iss. 3. N 1047. DOI: 10.3390/en15031047
- Klishin V.I., Opruk G.Y., Tatsienko A.L. Technology and means of a coal seam interval hydraulic fracturing for the seam degassing intensification. IOP Conference Series: Earth and Environmental Science. 2017. Vol. 53. N 012019. DOI: 10.1088/1755-1315/53/1/012019
- Lekontsev Yu.M., Sazhin P.V. Directional hydraulic fracturing in difficult caving roof control and coal degassing. Journal of Mining Science. Vol. 50. N 5, p. 914-917. DOI: 10.1134/S106273911405010X
- Jiangwei Liu, Changyou Liu, Qiangling Yao, Guangyao Si. The position of hydraulic fracturing to initiate vertical fractures in hard hanging roof for stress relief. International Journal of Rock Mechanics and Mining Sciences. 2020. Vol. 132. N 104328. DOI: 10.1016/j.ijrmms.2020.104328
- Wenli Zhai, Fulian He, Liang Li et al. Roof cutting mechanism and surrounding rock control of small pillar along-gob roadway driving in super high coal seam. Bulletin of Engineering Geology and the Environment. 2023. Vol. 82. Iss. 4. N 151. DOI: 10.1007/s10064-023-03189-1
- Yongxin Sun, Yukai Fu, Tao Wang. Field application of directional hydraulic fracturing technology for controlling thick hard roof: a case study. Arabian Journal of Geosciences. 2021. Vol. 14. Iss. 6. N 438. DOI: 10.1007/s12517-021-06790-4
- Shilova T.V., Rybalkin L.A. Study of polymer compositions for formation of impermeable inclusions in rock mass. IOP Conference Series: Earth and Environmental Science. 2022. Vol. 991. N 012008. DOI: 10.1088/1755-1315/991/1/012008
- Serdyukov S.V., Kurlenya M.V., Patutin A.V. Hydraulic fracturing for in situ stress measurement. Journal of Mining 2016. Vol. 52. N 6, p. 1031-1038. DOI: 10.1134/S1062739116061563
- Oldenburg C.M., Dobson P.F., Yuxin Wu et al. Hydraulic fracturing experiments at 1500 m depth in a deep mine: Highlights from the kISMET project. 42nd Workshop on Geothermal Reservoir Engineering, 13-15 February 2017, Stanford, CA, USA. Stanford Geothermal Program, 2017. N SGP-TR-212.
- Rubtsova E.V., Skulkin A.A.Hydraulic fracturing stress measurement in underground salt rock mines at Upper Kama Deposit. IOP Conference Series: Earth and Environmental Science. 2018. Vol. 134. N 012049. DOI: 10.1088/1755-1315/134/1/012049
- Qiang Xu, Qiangling Yao, Changhao Shan, Chuangkai Zheng. A New Hydraulic Fracturing Instrument to Measure In Situ Stress and Its Application in Chahasu Coal Mine. Geotechnical Testing Journal. Vol. 45. Iss.5, p. 901-914. DOI: 10.1520/GTJ20210207
- Serdyukov S.V., Kurlenya M.V. Application of local hydrofrac for the intensification of steam assisted gravity reservoir drainage. XII Mezhdunarodnye nauchnyi kongress i vystavka “Interehkspo GEO-Sibir-2016”: Materialy Mezhdunarodnoi nauchnoi konferentsii “Ehkonomicheskoe razvitie Sibiri i Dalnego Vostoka. Ehkonomika prirodopolzovaniya, zemleustroistvo, lesoustroistvo, upravlenie nedvizhimostyu”, 18-22 April 2016, Novosibirsk, Russia. Novosibirsk: Sibirskii gosudarstvennyi universitet geosistem i tekhnologii, 2016. Vol. 2, p. 8-13 (in Russian).
- Yunzhong Jia, Zhaohui Lu, Qiquan Xiong et al. Laboratory characterization of cyclic hydraulic fracturing for deep shale application in Southwest China. International Journal of Rock Mechanics and Mining Sciences. 2021. Vol. 148. N 104945. DOI: 10.1016/j.ijrmms.2021.104945
- Li Zhuang, Kwang Yeom Kim, Melvin Diaz, Sun Yeom. Evaluation of water saturation effect on mechanical properties and hydraulic fracturing behavior of granite. International Journal of Rock Mechanics and Mining Sciences. 2020. Vol. 130. N 104321. DOI: 10.1016/j.ijrmms.2020.104321
- Bobrova M., Stanchits S., Shevtsova A. et al. Laboratory Investigation of Hydraulic Fracture Behavior of Unconventional Reservoir Rocks. Geosciences. 2021. Vol. 11. Iss. 7. N 292. DOI: 10.3390/geosciences11070292
- Deb P., Düber S., Guarnieri Calò Carducci C., Clauser C. Laboratory-scale hydraulic fracturing dataset for benchmarking of enhanced geothermal system simulation tools. Scientific Data. 2020. Vol. 7. N 220. DOI: 10.1038/s41597-020-0564-x
- Patutin A.V., Serdyukov S.V. Laboratory stands for hydraulic fracturing simulation in a nonuniform stress field. IOP Conference Series: Earth and Environmental Science. 2022. Vol. 991. N 012035. DOI: 10.1088/1755-1315/991/1/012035
- Feiteng Zhang, Xiangyu Wang, Jianbiao Bai et al. Fixed-length roof cutting with vertical hydraulic fracture based on the stress shadow effect: A case study. International Journal of Mining Science and Technology. 2022. Vol. 32. Iss. 2, p. 295-308. DOI: 10.1016/j.ijmst.2021.09.007
- Pavlov V.A., Serdyukov S.V., Martynyuk P.A., Patutin A.V. Optimisation of borehole-jack fracturing technique for in situ stress measurement. International Journal of Geotechnical Engineering. 2019. Vol. 13. Iss. 5, p. 451-457. DOI: 10.1080/19386362.2017.1363347
- Karev V.I., Kovalenko Yu.F., Ustinov K.B. Modeling of geomechanical processes in the vicinity of oil and gas wells. Moscow: Institut problem mekhaniki im. A.Yu.Ishlinskogo RAN, 2018, p. 528 (in Russian).
- Shaohua Gai, Zhihong Nie, Xinbin Yi et al. Study on the Interference Law of Staged Fracturing Crack Propagation in Horizontal Wells of Tight Reservoirs. ACS Omega. 2020. Vol. 5. Iss. 18, p. 10327-10338. DOI: 10.1021/acsomega.9b04423
- Kalam S., Afagwu C., Al Jaberi J. et al. A review on non-aqueous fracturing techniques in unconventional reservoirs. Journal of Natural Gas Science and Engineering. 2021. Vol. 95. N 104223. DOI: 10.1016/j.jngse.2021.104223
- Jiangzhan Chen, Xibing Li, Han Cao, Linqi Huang. Experimental investigation of the influence of pulsating hydraulic fracturing on pre-existing fractures propagation in coal. Journal of Petroleum Science and Engineering. 2020. Vol. 189. N 107040. DOI: 10.1016/j.petrol.2020.107040
- Wenfeng Li, Frash L.P., Carey J.W. et al. Injection Parameters That Promote Branching of Hydraulic Cracks. Geophysical Research Letters. 2021. Vol. 48. Iss. 12. N e2021GL093321. DOI: 10.1029/2021GL093321
- Tiankui Guo, Zhenhua Rui, Zhanqing Qu, Ning Qi. Experimental study of directional propagation of hydraulic fracture guided by multi-radial slim holes. Journal of Petroleum Science and Engineering. 2018. Vol. 166, p. 592-601. DOI: 10.1016/j.petrol.2018.03.102
- Zhaoquan Guo, Shouceng Tian, Qingling Liu et al. Experimental investigation on the breakdown pressure and fracture propagation of radial borehole fracturing. Journal of Petroleum Science and Engineering. 2022. Vol. 208. Part A. N 109169. DOI: 10.1016/j.petrol.2021.109169
- Shaojie Zuo, Zhaolong Ge, Kai Deng et al. Fracture initiation pressure and failure modes of tree-type hydraulic fracturing in gas-bearing coal seams. Journal of Natural Gas Science and Engineering. 2020. Vol. 77. N 103260. DOI: 10.1016/j.jngse.2020.103260
- Rubtsova E.V. Three-axial independent loading bench for physical modeling of hydraulic fracturing for stress measurement. XI Mezhdunarodnye nauchnyi kongress i vystavka “Interehkspo GEO-Sibir-2015”: Materialy Mezhdunarodnoi nauchnoi konferentsii “Nedropolzovanie. Gornoe delo. Napravleniya i tekhnologii poiska, razvedki i razrabotki mestorozhdenii poleznykh iskopaemykh. Geoehkologiya”, 13-25 April 2015, Novosibirsk, Russia. Novosibirsk: Sibirskii gosudarstvennyi universitet geosistem i tekhnologii, 2015. Vol. 3, p. 211-215 (in Russian).
- Rubtsova E., Skulkin A. Physical simulation the process of measurement hydrofracturing in specimen under their non-equicomponent loading. Problems of Subsoil Use. N 2 (13), p. 42-46 (in Russian). DOI: 10.18454/2313-1586.2017.02.042
- Kachalsky V.G., Leontev A.V., Rubtsova E.V. Portable pressure recorder at complex “hydrofracturing” for experimental stress determination in the solid. XV Mezhdunarodnyi nauchnyi kongress “Interehkspo GEO-Sibir”: Materialy Mezhdunarodnoi nauchnoi konferentsii “Nedropolzovanie. Gornoe delo. Napravleniya i tekhnologii poiska, razvedki i razrabotki mestorozhdenii poleznykh iskopaemykh. Ehkonomika. Geoehkologiya”, 24-26 April 2019, Novosibirsk, Russia. Novosibirsk: Sibirskii gosudarstvennyi universitet geosistem i tekhnologii, 2019. Vol. 2. N 4, p. 38-44 (in Russian). DOI: 10.33764/2618-981X-2019-2-4-38-44
- Quan Gan, Elsworth D., Alpern J.S. et al. Breakdown pressures due to infiltration and exclusion in finite length boreholes. Journal of Petroleum Science and Engineering. 2015. Vol. 127, p. 329-337. DOI: 10.1016/j.petrol.2015.01.011
- Khadraoui S., Hachemi M., Allal A. et al. Numerical and experimental investigation of hydraulic fracture using the synthesized PMMA. Polymer Bulletin. 2021. Vol. 78. Iss. 7, p. 3803-3820. DOI: 10.1007/s00289-020-03300-6
- Mouli-Castillo J., Kendrick J.E., Lightbody A. et al. Cyclical hydraulic pressure pulses reduce breakdown pressure and initiate staged fracture growth in PMMA. Geomechanics and Geophysics for Geo-Energy and Geo-Resources. 2024. Vol. 10. Iss. 1. N 65. DOI: 10.1007/s40948-024-00739-z
- Patutin A.V., Skulkin A.A. Hydraulic fracturing of intersecting boreholes in a non-uniform stress field: laboratory studies. Fizicheskaya mezomekhanika. Materialy s mnogourovnevoi ierarkhicheski organizovannoi strukturoi i intellektualnye proizvodstvennye tekhnologii: Tezisy dokladov Mezhdunarodnoi konferentsii, 11-14 September, 2023, Tomsk, Russia. Tomsk: Institut fiziki prochnosti i materialovedeniya SO RAN, 2023, p. 176-177 (in Russian).
- Azarov A.V., Patutin A.V., Serdyukov S.V. Shapes of Hydraulic Fractures in the Vicinity of Borehole-and-Branch Hole Junction. Journal of Mining Science. Vol. 58. N 5, p. 741-753. DOI: 10.1134/S1062739122050052
- Patutin A.V., Skulkin A.A., Prasolova V.S. Physical Modeling of Hydraulic Fracturing in Branched Borehole in Manmade Block. Journal of Mining Science. Vol. 59. N 2, p. 191-198. DOI: 10.1134/S1062739123020023
- Jing-Nan Dong, Guang-Jie Yuan, Xiang-Yang Wang et al. Experimental study of multi-timescale crack blunting in hydraulic fracture. Petroleum Science. 2021. 18. Iss. 1, p. 234-244. DOI: 10.1007/s12182-020-00479-1
- Panov A.V., Kolykhalov I.V. Numerical and experimental modeling of propagation of longitudinal fractures in multi-stage hydraulic fracturing with viscous fluid. XVII Mezhdunarodnyi nauchnyi kongress “Interehkspo GEO-Sibir”: Materialy Mezhdunarodnoi nauchnoi konferentsii “Nedropolzovanie. Gornoe delo. Napravleniya i tekhnologii poiska, razvedki i razrabotki mestorozhdenii poleznykh iskopaemykh. Ehkonomika. Geoehkologiya”, 19-21 May 2021, Novosibirsk, Russia. Novosibirsk: Sibirskii gosudarstvennyi universitet geosistem i tekhnologii, 2021. Vol. 2. N 4, p. 41-51 (in Russian). DOI: 10.33764/2618-981X-2021-2-4-41-51
- Zi-Xiao Xie, Xiao-Guang Wu, Teng-Da Long et al. Visualization of hydraulic fracture interacting with pre-existing fracture. Petroleum Science. 2023. Vol. 20. Iss. 6, p. 3723-3735. DOI: 10.1016/j.petsci.2023.07.014
- Leontiev A., Rubtsova E. Analysis of Crack Formation in Model Specimens During Hydraulic Fracturing in Holes. Trigger Effects in Geosystems. Springer, 2019, p. 247-256. DOI: 10.1007/978-3-030-31970-0_27
- Qiao Lu, EI-Fayoumi A., Adachi J. et al. Laboratory demonstration of the impact of weak interfaces and layered rock properties on hydraulic fracture containment and height growth. Geomechanics and Geophysics for Geo-Energy and Geo-Resources. 2023. Vol. 9. Iss. 1. N 113. DOI: 10.1007/s40948-023-00649-6
- Kyu N.G. Directional Conjugate Fracturing in Rock Mass Using Holes as Plastic Fluid Front Guides. Journal of Mining Science. Vol. 56. N 5, p. 784-792. DOI: 10.1134/S1062739120057117
- Konoplev Yu.P., Demchenko A.G., Demchenko A.A. Oil mine – a technology that is capable of providing half of oil production in the 21st century in the open and developed fields of Russia. Nedropolzovanie XXI vek. N 1 (83), p. 46-55 (in Russian).
- Lizunkin M.V., Beidin A.V. Assessment of the stress-strain state of the rock massif of the Streltsovsky ore field. Geomekhanika v gornom dele: Doklady Vserossiiskoi nauchno-tekhnicheskoi konferentsii s mezhdunarodnym uchastiem, 4-5 June 2014, Ekaterinburg, Russia. Ekaterinburg: Uralskoe otdelenie RAN, 2014, p. 30-38 (in Russian).
- Belov S.V. Geological and engineering mining conditions of coal development at the “Karagaylinskaya mine field”. Mezhdistsiplinarnye podkhody v biologii, meditsine i naukakh o Zemle: teoreticheskie i prikladnye aspekty: Materialy simpoziuma XVIII (L) Mezhdunarodnoi nauchnoi konferentsii studentov, aspirantov i molodykh uchenykh “Obrazovanie, nauka, innovatsii: vklad molodykh issledovatelei”, priurochennoi k 50-letiyu KeMGU, 24-29 April 2023, Kemerovo, Russia. Kemerovo: Kemerovskii gosudarstvennyi universitet, 2023. Iss. 24, p. 118-120 (in Russian).
- Kang H., Zhang X., Si L. et al. In-situ stress measurements and stress distribution characteristics in underground coal mines in China. Engineering Geology. 2010. 116. Iss. 3-4, p. 333-345. DOI: 10.1016/j.enggeo.2010.09.015
- Kozyrev A.A. Modern results of experimental study of natural stresses in the upper part of the Earth's crust and the problem of overburden pressure. Geomekhanika v gornom dele: Doklady Vserossiiskoi nauchno-tekhnicheskoi konferentsii s mezhdunarodnym uchastiem, 4-5 June 2014, Ekaterinburg, Russia. Ekaterinburg: Uralskoe otdelenie RAN, 2014, p. 39-53 (in Russian)
- Peng Li, Meifeng Cai, Qifeng Guo et al. Current stress field and its relationship to tectonism in a coal mining district, central China, for underground coal energy exploration. Energy Reports. 2022. Vol. 8, p. 5313-5328. DOI: 10.1016/j.egyr.2022.04.008
- Serdyukov S.V., Patutin A.V., Azarov A.V., Rybalkin L.A., Shilova T.V. Patent N 2730688 RF. Method of directed hydraulic fracturing of coal bed. Publ. 25.08.2020. Bul. N 24 (in Russian).
- Langbauer C., Tehrani F.F., Mastobaev B. A holistic review on hydraulic fracturing stimulation laboratory experiments and their transition to enhanced geothermal system field research and operations. Liquid and Gaseous Energy Resources. 2021. Vol. 1. Iss. 1, p. 30-63. DOI: 10.21595/lger.2021.22043