Justification of the approaches to improve management strategy of the mining system based on the analysis of data on the mining of complex structural rock blocks
- 1 — Junior Researcher Institute of Comprehensive Exploitation of Mineral Resources RAS ▪ Orcid
- 2 — Researcher Institute of Comprehensive Exploitation of Mineral Resources Russian Academy of Sciences ▪ Orcid
- 3 — Ph.D. Head of Laboratory Institute of Comprehensive Exploitation of Mineral Resources RAS ▪ Orcid ▪ Scopus
- 4 — Ph.D. Head of Laboratory Institute of Comprehensive Exploitation of Mineral Resources RAS ▪ Orcid ▪ Scopus
Abstract
Long-term activity of mining enterprises causes the necessity to substantiate the strategies of management of the mining and technical system functioning in terms of improvement of ore quality control, which is determined by its change in the course of field development due to the priority development of the main reserves and, as a consequence, forced transition to the mining of complex structural rock blocks with a decrease in the recovery percentage, which is typical in case the ore component meets the requirements of the feasibility study in terms of grade at substandard capacity. In this case, it is possible to identify the recovery percentage and the potential for its increase by analyzing the long-term activity of the mining and industrial enterprise, namely, by analyzing the data of mining complex structural rock blocks with the subsequent establishment of the relationship between the primary data on mining and geological conditions and information on the quality of the mineral obtained from the technological equipment. Therefore, the purpose of the research was to substantiate the necessity of improving the management strategy of the mining-technical system functioning, which consists in the fact that on the basis of analyzing the mining data of complex structural rock blocks it is possible to determine the ore mass losses and their quantity and to lay the basis for the development of decisions on its extraction. For this purpose, the collected data on the mining of complex structural rock blocks, accounting the geological and industrial type of extracted ores, were considered in modeling the conditions and studying the parameters of technological processes, the implementation of which provides additional products. It was revealed that the ore mass from substandard thickness layers is delivered to the dumps, and ore mass losses have been estimated at 25-40 % per year. It is proved that determination of ore mass losses based on the analysis of data on mining of complex structural rock blocks, as well as timely solution of this issue can significantly increase the production efficiency of mining and technical system. Taking into account for the results obtained, the options for optimizing the production of the mining and engineering system were proposed.
Introduction
The continuous operation of mining enterprises with the priority of mining rich ores gradually leads to the fact that nowadays there is an increase in mining volumes with a simultaneous decrease in the quality characteristics of ore flow [1, 2]. This is one of the urgent problems reducing the production efficiency of the mining system [3, 4]. Since rational management of the qualitative characteristics of the extracted ore mass is the basis for ensuring the production performance of the mining and technical system [5, 6], the solution of this problem will increase the completeness of subsoil development and improve the production performance of mining enterprises as a whole.
The quality characteristics of ore streams are managed in all technological processes along the chain: stripping of the deposit or its parts – preparation for cleaning excavation – loading into vehicles – transportation – shipment and storage for processing – beneficiation. The effectiveness of quality management depends directly on the analysis of data from the rock mass [7, 8] and technological equipment [9].
According to the sources [10, 11], traditional methods and tools of quality management allow identifying problems and optimizing the decision-making process, but a significant disadvantage can be considered a delay in the implementation of corrective actions. In addition, prolonged development of mineral deposits introduces new complexities in technological processes, which is often associated with depletion of reserves or complication of mining and geological conditions and requires new approaches to quality management of ore mass. Information and communications technology make it possible to increase efficiency in quality management by integrating into technological processes various patterns obtained from data analysis and reflecting production efficiency [12, 13], as well as to manage the quality of ore mass in real time, while minimizing losses [11, 14, 15].
Currently, Industry 4.0 technologies such as the Internet of Things (IoT) [16], big data [17], cloud computing, 3D visualization, provide digital transformation of mining enterprises with a number of advantages in terms of production efficiency, product quality and cost reduction [18-20], as well as determination and prediction of various process parameters [21-23]. The authors of the article [24] believe that the key components for effective quality management are the processing of big data and improvement of prescriptive analytics.
The basis of the digital process control system capable of ensuring the required level of efficiency at a mining enterprise [25] is reliable and timely information at all levels of production [26, 27]. However, the highest efficiency indicators can be achieved only with the understanding of the target task, based on which the list of information sources and types of data generated during the implementation of technological processes should be determined. In terms of quality management such sources can be data on the material composition and technological properties of ores, geophysical and geochemical studies [28-30], as well as data from analytical information and automated systems [31], including the automated control system of the mining and transportation complex, automated control system of drilling and blasting control system, quality control system and other systems and types of data that include information on changes in the quality characteristics of the mineral at all stages of field development [32].
In terms of definition of sources of digital data and organization of their collection, the classification of data sources of mining-technical system based on the object of their obtaining, proposed in the paper, [33], is the most suitable, because this classification allows to justify the order of putting the source of information into operation at the design stage for each physical object, to determine the parameters of the received signals and the principles of their transformation into digital form and, if necessary, to establish the requirements for the frequency of the received data, as well as the format, suitable for the data collection. for processing, analysis, long-term storage and conditions for using the data.
Statement of problem
As the authors admit [34], the solution to improve the homogeneity of the quality characteristics of the formed ore streams is the reliable separation of ore deposits in the rock mass with their precise delineation and identification of technological types and grades of ores, ensuring their efficient mining and transportation in the appropriate modes of separation or quality averaging. However, the reliability of such allocation depends on the mining and geological conditions of the fields being developed, based on the analysis of which the industrial value and complexity group of the objects are determined with subsequent justification of the geotechnology of their development [35]. It should be noted that the quality indicators of the extracted ore mass crucially depend on the mining and geological features of the mined deposits, so it is necessary to pay special attention to improving the reliability and processing of data on the rock mass and to interpret the obtained results accounting for the analysis of other data sources.
The problem of ensuring consistent quality is most relevant for mining companies engaged in the development of complex structural deposits of solid minerals [36, 37], where the total volume of the developed deposit has a significant proportion of low-power steeply dipping ore bodies, the effective excavation of which is complicated [38]. As a rule, the main difficulties in ensuring quality characteristics in this case are associated with the lower capacity of the working bodies of the excavation equipment compared to the thickness of ore layers, which results in the ore dilution, leading to a decrease in the quality characteristics of raw materials.
In addition, when developing deposits, mining companies are required to conduct their operations in accordance with the adopted feasibility report of the conditions, which may set limits on both the content of valuable components and the capacity of ore bodies. Thus, for example, the basic block model of the deposit, which is formed accounting for the compliance with the power specifications, is simplified by excluding ore layers whose thickness does not meet the accepted requirements, if within the developed deposit there are ore layers with a thickness of 4 to 5 m, and the specifications are focused on the development of layers with a thickness of more than 6 meters. As a result, the reliability of the real mining and geological situation is reduced, which subsequently leads to a decrease in the productivity of the enterprise due to the planning of mining operations based on an incomplete set of data, leading to significant losses of ore mass entering the dumping facilities. This allows us to formulate a hypothesis on the necessity of finding solutions aimed at identifying possible losses of ore mass and justifying the recommendations that will ensure increased efficiency in quality management in the course of deposit development.
Thus, due to the increasing probability of significant losses of the ore component, corresponding in content to the requirements of the feasibility study at substandard capacity, when mining complex structural rock blocks, a variant of improving the management strategy of the functioning of the mining and technical system is proposed, which differs in that the increase in the completeness of subsoil development can be provided on the basis of analyzing the data on the mining of complex structural rock blocks, namely by identifying the types of possible losses and their quantitative index, which as a result will contribute to the development of solutions aimed at additional extraction of ore mass. Justification of the proposed variant will determine the possibility of revision of the existing quality management systems or their supplementation accounting for the need to increase the productivity of the enterprise and obtain additional marketable products in the form of productive fraction, previously not extracted for objective reasons.
Justification of the improvement of the management strategy for the functioning of the mining and technical system in terms of quality management within mining and industrial enterprises is a considerable task, the solution of which can be realized by obtaining their long-term activity. The study is based on the analysis of big data generated during the functioning of the mining-technical system from each unit of mining equipment, which is the source of formation of data on the indicators of its operation and condition [9, 27, 39]. In this case, to solve the problem of ore flow quality management, special attention should be paid to analyzing data on the mining of complex structural rock blocks with the subsequent establishment of the relationship between the primary data on the mining and geological conditions of the deposit and data on the quality of the mineral obtained from the process equipment.
The aim of the paper is to substantiate the necessity and possibility of improving the management strategies of mining-technical systems based on more adequate block models and mechanisms of ore flow management using modern methods of predictive analytics.
Methodology
Since the highest efficiency indicators of mining system development processes can be achieved only by understanding the target task, it should be taken into consideration that the list of requested data is determined both depending on the availability of data at the enterprise and accounting for the geological and industrial deposit type. For example, when collecting information at an enterprise extracting iron ores, data from both chemical sampling and geophysical methods for determining the quality of the mineral are mandatory.
In order to verify the proposed variant of improving the management strategy for the functioning of the mining-technical system at one of the iron ore mining-industrial enterprises of the country, an audit of the current quality management system was conducted, and retrospective data for the last three years of activity were requested, including information on the processing of complex structural rock blocks obtained from the mining mass and technological equipment.
Modeling of conditions and study of parameters of technological processes, implementation of which can provide extraction of additional marketable products, was carried out in several stages:
- collection and processing of all information received from the enterprise on the mining of complex structural rock blocks received from the mining massif and technological equipment;
- verification of the integrity of uploads from provided databases;
- preparation of initial data presented in the form of distribution of the rock mass structure indicators, elements of working processes of the mining and engineering system, tied to specific points of space and time;
- modeling of conditions and research of technological processes parameters based on the regularities identified at the first stage;
- preparation of conclusions based on the data analysis on possible scenarios for the development of complex structural rock blocks to determine the types of possible losses and their quantitative indicators.
Taking into account the data available to the enterprise, as well as the geological and industrial type of ores to be mined, the list of required data included:
- maps of magnetic iron content distribution by mined blocks, drawn up at the annual planning stage;
- maps of magnetic iron content distribution over mined blocks, based on drill and blast logging data;
- block layout on the pit plan;
- instructions adopted at the enterprise for determining, accounting and standardization of production losses;
- ore control station performance statistics;
- loss reports;
- data on ore types and their characteristics (study);
- data on wells of the exploration stage at the deposit, which are the basis for building the initial block model;
- current ore quality requirements at the beneficiation plant;
- list of attributes (magnetic iron content, sulfur content, enrichment, lithology);
- data on mining, loading and transportation means used;
- dispatching system data (number of machines sent to dump, ore stockpile, SMS with linkage to faces).
At the stage of initial data preparation for modeling, the integrity of database uploads was checked, which consisted in determining the presence of information on spatial position and hole parameters. In addition, a cross-check was performed to verify the consistency of the same information presented in different records of different database tables.
At the initial stage of resource model preparation, it was decided to use data from the enterprise's block model, however, during the analysis of the logging data by blocks, including the search for substandard thickness of interlayers, taking into account the peculiarities of ore depo-sits occurrence and annual mining decline, the discrepancy between the block model data and hole logging results was established (Fig.1). In the course of modeling, this may lead to a mismatch between the actual production volumes and the modeling results.
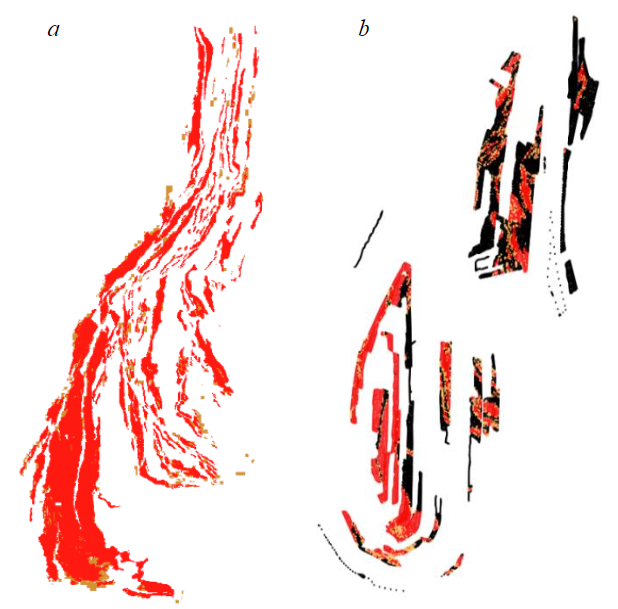
Fig.1. Results of comparing data of hole logs (a) and block model (b)
The second negative point affecting the quality of the final result is the use of interpolation models when building a block model, which increases the smoothness of contours and leads to increased resource costs for processing and analyzing the obtained information. Therefore, it was decided to use as initial information on the geological structure an analog of the block model built from hole logging data without using interpolation (Fig.2). The proposed model is based on A.K.Boldyrev's reserve calculation method and the concept of the nearest area (geometric area of influence of the hole) (Fig.2, b).
At the stage of information processing the selection of initial data for modeling was carried out. Due to the lack of standardization of digital data collection and storage, as well as unstructured data from multiple technological processes, the obtained information on the functioning of the mining and technical system was multi-format, which made it difficult to analyze it using standard methods of mathematical analysis. Since geologic data are generated in the process of research and additional study of the massif under development (frequency of receipt and updating at least once a month), and dispatching data (discreteness – 1 s or more) – due to the operation of process equipment, there is a problem of linking the collected information into a single complementary complex or structure of spatial and temporal data sets. The problem is solved by synchronizing, structuring, transforming and bringing different datasets to a common format that allows the construction of a single spatio-temporal model processed using uniform methods and rules.
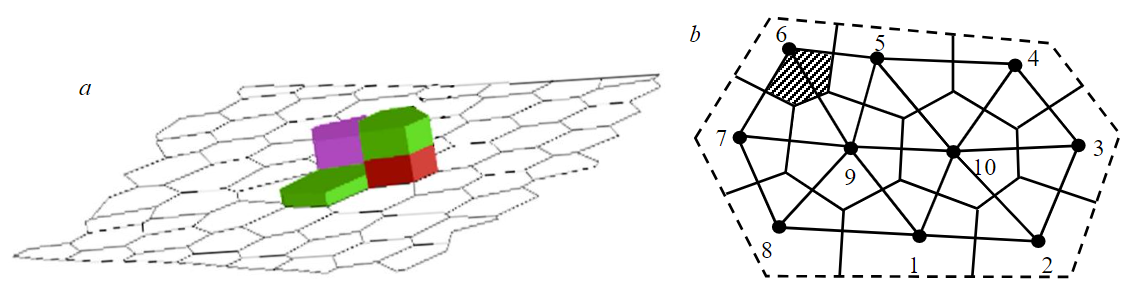
Fig.2. The principle of matching logging data with the nearest area (a) and the principle of constructing the nearest area (b) for holes
Analysis of the initial data at the stage of their preparation allowed us to identify two key sets of factors that have a major impact on the efficiency of the mining and technical system of this enterprise: factors related to the features of the geological structure, and factors related to the operation of the mining and transportation system, which forms the structure of the ore and overburden flow.
The geological component of the geospatial source data set in this case is represented by the description of geological information in the form of simple text and graphic files: graphical representation of the developed block in the form of nearest area sets for each hole in the block, logging data, hole data with areas of constructed nearest areas.
Information on the operation of mining and transportation equipment, including information on the volume of cargo transportation, is represented by a set of basic indicators of the automated dispatching system: average speeds of dump trucks, distances of their movement from blocks to unloading points, the model range of dump trucks by body volume, data on average intervals of loading of one dump truck taking into account the productivity of a particular excavator, data on bucket volumes of the used excavators. The specified set of data as constants and parameters is presented in the form of spreadsheets and was used to obtain different variants of models on the same set of geologic data.
The program part of the database generates output data based on the specified information in the form of sets of files: block card with stocks, dump truck flow with information on each machine, statistics on all generated dump trucks and total statistics on stock data in all blocks included in the model. This data set allows checking the correctness of resource generation for the model by means of simple comparison of data from different files.
Results
Comparison of the two approaches allowed us to draw the following conclusion: the quality of the information presented by the two methods is comparable, but the recommended modeling variant is less costly in terms of time and resources, also when applying various interpolation models smoothing the actual distribution of components, no additional distortion is introduced into the original information, so it is preferable. Figure 3 shows examples of graphical representation of mo-deled blocks.
In order to determine the necessary parameters of the quarry transport system operation, the analysis of the dispatching system data was performed. A total of 3548880 records were checked and processed according to the dispatching data. Corrections in coordinates were made in 391275 records, which is 11 % of the total volume.
Further, the average loading interval was calculated for the analysis and general data on excavator productivity was determined. During the calculations the data on loading time of each dump truck with reference to a specific excavator were analyzed. The analysis was performed for different intervals of statistics accumulation from a minute to a quarter. Figure 4 shows an example of building a graph of dump truck loading intensity.
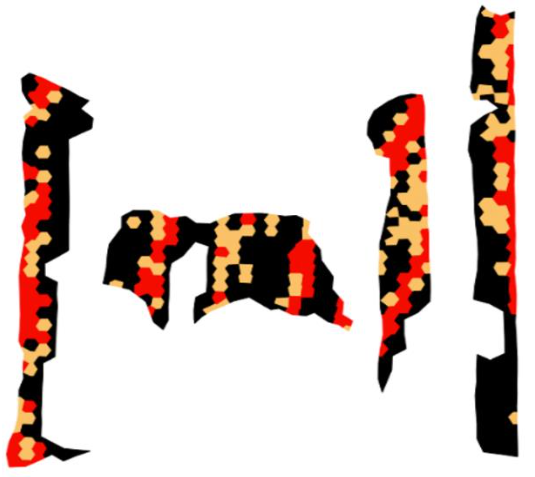
Fig.3. Examples of graphical representation block model when creating a resource database
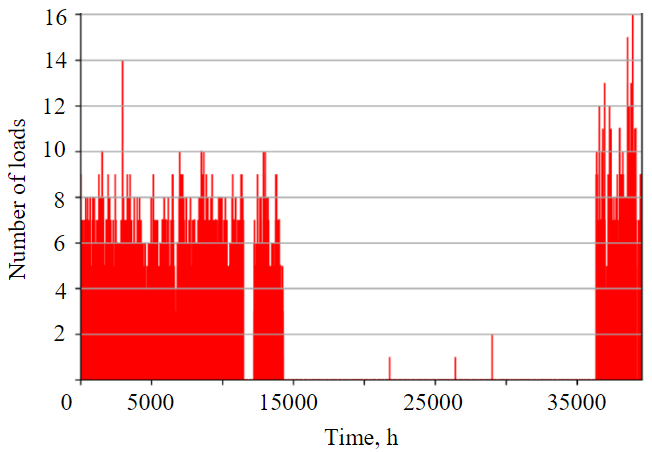
Fig.4. Excavator operation statistics 13 (maximum loadings – 16) during an hour

Fig.5. Chart of continuous operation duration for all excavators
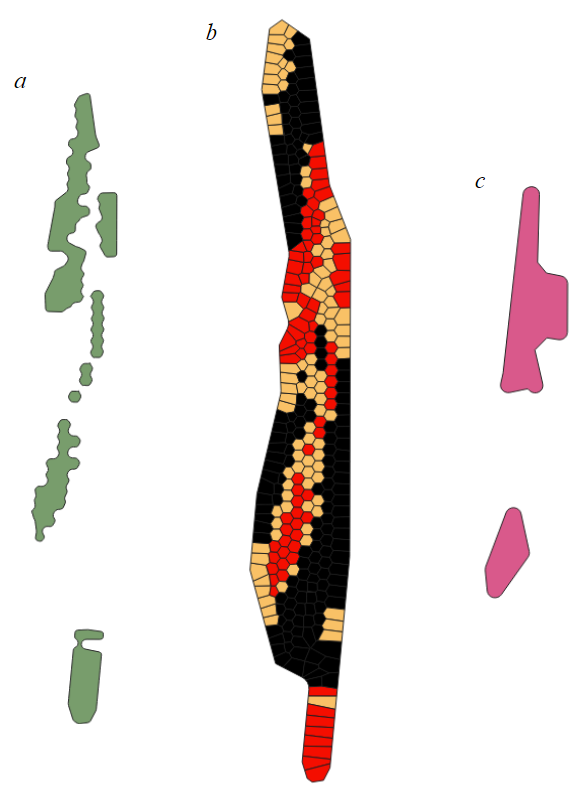
Fig.6. Result of modeling of loading processes and transportation of rock mass from complex structural rock blocks with and without power conditioning: а – unit without power conditioning; b – overview of the complex structural block considering balance (red) and off-balance (yellow) ores; c – power conditioned unit
Analysis of the graphs allowed to determine the average length of intervals between dump truck loading, as well as fluctuations in the length of the interval depending on the intensity of excavator operation. The results of the intervals were compiled into a protocol file, the conclusion of which summarizes the downtime, number and intervals of loading. All information is presented in text with delimiters, which makes it easier to load into spreadsheet editors for further data analysis.
The second direction of the analysis was to estimate the number of simultaneously operating excavators. Analysis of the diagram of the duration of continuous operation for each excavator (Fig.5) allowed to establish that up to 13 excavators work simultaneously at the pit, and the average number of simultaneously working excavators is only seven units.
The obtained data on the operation intervals of mining and transportation equipment can be used as a basis for the ore flow management system to reduce downtime by redirecting transportation equipment. This will improve the strategy for managing the functioning of the mining and technical system by analyzing the data on the operation of mining and transportation equipment during the mining of complex structural rock blocks.
As a result, a resource database was created based on the results of statistical processing of data on the operation of the mining and industrial enterprise over the past few years. Thanks to the collected information it was possible to model the processes of loading and transportation of rock mass from complex structural rock blocks with and without power conditioning (Fig.6). Based on the modeling results, the volumes of ore mass were calculated with and without power conditioning. The difference in volumes determined further allowed us to determine the volumes of ore mass entering the overburden dumps, the values of which amounted to 25-40 % depending on the geological structure of the complex structural rock blocks being mined.
The model was further verified using two main facts – data from the beneficiation plant on the quality of ore flows entering the plant and data on the quality of rock mass sent to the overburden dumps. Comparison of the data obtained in the modeling and the data used for verification confirmed the validity of the modeling.
As a result, the modeling allowed estimating the losses of quality-conditioned and substandard ore mass from 25 to 40 % per year, which confirms the need to improve the strategy of management of the mining and technical system based on the analysis of data on the mining of complex structural rock blocks.
Conclusion
The results of their integrity assessment obtained during the processing of databases available at the enterprise confirmed the need to standardize approaches to processing, collection and analysis of information [34]. The results of their integrity assessment obtained during the processing of databases available at the enterprise confirmed the need to standardize approaches to processing, collection and analysis of information. Standardized approach to the introduction of digital solutions will allow to expand the functionality more effectively and ensure the interface of information with related structural units in the management of mining and engineering system, which in support of the hypothesis will contribute to a rational assessment of possible options to improve the management strategy of the functioning of the mining and engineering system in terms of optimization of technological processes of a particular enterprise.
Comparison of the results of hole logs, which do not consider the minimum thickness of ore layers specified by the conditions feasibility report, and the data of the block model of the enterprise, created with account of all requirements, allowed to determine one of the types of losses: ore mass from low thickness layers of the required grade is delivered to the dumps, but the conditioned thickness of these layers is not provided in accordance with the requirements of the conditions feasibility report.
No doubt, the feasibility report of the conditions was developed considering the practicability and economic efficiency of the development of a certain mineral deposit, which implies regulatory and legal complexities in revising and changing the condition requirements, as well as changing the quality management system as a whole. Therefore, the possibility of adjusting the quality management system of mineral and raw material flows of the enterprise by optimizing the following areas has been determined:
- more detailed information on the structure of the blocks under preparation with the identification of ore bodies that are currently substandard in terms of thickness through the introduction of analytical platforms, which, based on the analysis of historical data and the search for patterns in them, will allow for increased reliability during subsequent sampling;
- improvement of selective ore extraction technologies at the excavation stage in the face to minimize ore dilution;
- in case it is impossible to improve selective excavation technologies, the option of introducing cyclic-flow technology is considered to separate previously unrecoverable ore mass on the conveyor; in this case, cyclic-flow technology will not only ensure optimization of ore mass transportation, but will also allow timely management of ore flow quality by identifying the ore component arriving on the conveyor from complex structural rock blocks and redirecting it to ore stockpiles rather than waste disposal facilities.
Management strategy improvement of the mining-technical system functioning against the background of the tendency of inevitable deterioration of mining-geological and mining-technical conditions of deposits development represents a highly relevant direction of optimization of subsoil development technological processes. Ensuring stable quality indicators of mined minerals is currently becoming an urgent problem of any mining enterprise and can be solved by analyzing the data on the development of complex-structural blocks obtained from the rock mass, environment, technological equipment, as well as automated systems of the mining and industrial enterprise.
REFERENCES
- Kaplunov D.R., Rylnikova M.V., Yun A.B., Terenteva I.V. A new technological policy for integrated subsoil development in the conditions of depleting mineral reserves and resources. Gornyi zhurnal. 2019. N 4, p. 11-14 (in Russian). DOI: 10.17580/gzh.2019.04.02
- Development of resource-saving and resource-replacing geotechnologies for integrated development of mineral deposits. Ed. by K.N.Trubetskoi. Мoscow: Institut problem kompleksnogo osvoeniya nedr RAN, 2014, p. 196 (in Russian).
- Yakovlev V.L. Methodological framework of the strategy for innovative development of mining systems for deep-seated mineral deposits. Mining Informational and Analytical Bulletin. 2021. N 5-1, p. 6-18 (in Russian). DOI: 10.25018/0236_1493_2021_51_0_6
- Cohen M.W., Coelho V.N. Open-Pit Mining Operational Planning using Multi Agent Systems. Procedia Computer Science. 2021. Vol. 192, p. 1677-1686. DOI: 10.1016/j.procs.2021.08.172
- Lomonosov G.G. Improving the quality of products of the mining production as a factor in increasing the effectiveness of the Russian mining and processing complex. Mineral Mining & Conservation. 2015. N 2, p. 51-61 (in Russian).
- Turtygina N.A., Okhrimenko A.V., Tsygankova D.N. Factors affecting the level of variability of the quality of extracted ore raw. Scientific bulletin of the Arctic. 2022. N 13, p. 5-14 (in Russian). DOI: 10.52978/25421220_2022_13_5-14
- Hadjigeorgiou J. Understanding, managing and communicating geomechanical mining risk. Mining Technology. 2020. Vol. 129. Iss. 3, p. 159-173. DOI: 10.1080/25726668.2020.1800909
- Nimmagadda S.L., Murupindy V.V., Reiners V.T. On Digital Opencast Mining Ecosystems (DOME) and Knowledge Management – a Big Data Perspective. 1st Australasian Exploration Geoscience Conference, 18-21 February 2018, Sydney, Australia. ASEG Extended Abstracts, 2018. Vol. 2018. Iss. 1, p. 1-5. DOI: 10.1071/ASEG2018abP086
- Deryabin S.A., Temkin I.O., Zykov S.V. About some issues of developing Digital Twins for the intelligent process control in quarries. Procedia Computer Science. 2020. Vol. 176, p. 3210-3216. DOI: 10.1016/j.procs.2020.09.128
- Ruihan Zhao, Liang Luo, Pengzhong Li, Jinguang Wang. An industrial heterogeneous data based quality management KPI visuali-zation system for product quality control. Assembly Automation. 2022. Vol. 42. Iss. 6, p. 796-808. DOI: 10.1108/AA-05-2022-0139
- Aleksandrova S.V., Vasiliev V.A., Alexandrov M.N. Integration of Quality Management and Digital Technologies. 2019 International Conference “Quality Management, Transport and Information Security, Information Technologies”, 23-27 September 2019, Sochi, Russia. IEEE, 2019, p. 20-22. DOI: 10.1109/ITQMIS.2019.8928426
- Rylnikova M.V., Klebanov D.A., Knyazkin E.A. Data analysis as a basis for improving the efficiency of mining equipment in open pit operations. Russian Mining Industry. 2023. N 1, p. 52-56 (in Russian). DOI: 10.30686/1609-9192-2023-1-52-56
- Cheskidov V.V., Manevich A.I., Lipina A.V. Obtaining and analyzing big data in the practice of monitoring the condition of mining structures. Gornaya promyshlennost. 2019. N 2 (144), p. 86-88 (in Russian). DOI: 10.30686/1609-9192-2019-2-144-86-88
- Rylnikova M.V., Vlasov A.V., Makeev M.A. Justification of conditions for application of automated control systems for surface mining during construction of in pit crushing and conveying system using simulation modeling. Russian Mining Industry. 2021. N 4, p. 106-112 (in Russian). DOI: 10.30686/1609-9192-2021-4-106-112
- Barnewold L., Lottermoser B.G. Identification of digital technologies and digitalization trends in the mining industry. International Journal of Mining Science and Technology. 2020. Vol. 30. Iss. 6, p. 747-757. DOI: 10.1016/j.ijmst.2020.07.003
- Zhukovskiy Y., Batueva D., Buldysko A., Shabalov M. Motivation towards energy saving by means of IoT personal energy manager platform. Journal of Physics: Conference Series. 2019. Vol. 1333. Iss. 6. N 062033. DOI: 10.1088/1742-6596/1333/6/062033
- Erkayaoglu M., Dessureault S. Improving mine-to-mill by data warehousing and data mining. International Journal of Mining, Reclamation and Environment. 2019. Vol. 33. Iss. 6, p. 409-424. DOI: 10.1080/17480930.2018.1496885
- Reis M.S. A Systematic Framework for Assessing the Quality of Information in Data-Driven Applications for the Industry 4.0. IFAC-PapersOnLine. 2018. Vol. 51. Iss. 18, p. 43-48. DOI: 10.1016/j.ifacol.2018.09.244
- Chong-chong Qi. Big data management in the mining industry. International Journal of Minerals, Metallurgy and Materials. 2020. Vol. 27. Iss. 2, p. 131-139. DOI: 10.1007/s12613-019-1937-z
- Cicconi P., Raffaeli R. An Industry 4.0 Framework for the Quality Inspection in Gearboxes Production. Computer-Aided Design & Applications. 2020. Vol. 17. Iss. 4, p. 813-824. DOI: 10.14733/cadaps.2020.813-824
- Zakharov L.А., Martyushev D.А., Ponomareva I.N. Predicting dynamic formation pressure using artificial intelligence methods. Journal of Mining Institute. 2022. Vol. 253, p. 23-32. DOI: 10.31897/PMI.2022.11
- Trofimov A.V., Kirkin A.P., Rumyantsev A.E., Yavarov A.V. Use of numerical modelling to determine optimum overcoring parameters in rock stress-strain state analysis. Tsvetnye Metally. 2020. N 12, p. 22-27 (in Russian). DOI: 10.17580/tsm.2020.12.03
- Zhukovskiy Y.L., Semenyuk A.V., Alieva L.Z., Arapova E.G. Blockchain-based digital platforms to reduce the carbon footprint of mining. Mining Informational and Analytical Bulletin. 2022. N 6-1, p. 361-378 (in Russian). DOI: 10.25018/0236_1493_2022_61_0_361
- Sony M., Antony J., Douglas J.A. Essential ingredients for the implementation of Quality 4.0: A narrative review of literature and future directions for research. The TQM Journal. 2020. Vol. 32. Iss. 4, p. 779-793. DOI: 10.1108/TQM-12-2019-0275
- Roberts F.S., Sheremet I.A. Resilience in the Digital Age. Cham: Springer, 2021, p. 199. DOI: 10.1007/978-3-030-70370-7
- Upadhyay S.P., Askari-Nasab H. Simulation and optimization approach for uncertainty-based short-term planning in open pit mines. International Journal of Mining Science and Technology. 2018. Vol. 28. Iss. 2, p. 153-166. DOI: 10.1016/j.ijmst.2017.12.003
- Rylnikova M.V., Klebanov D.A., Makeev M.A., Kadochnikov M.V. Application of artificial intelligence and the future of big data analytics in the mining industry. Russian Mining Industry. 2022. N 3, p. 89-92 (in Russian). DOI: 10.30686/1609-9192-2022-3-89-92
- Luo Jian-ming, Zhang Qi, Song Bing-tian et al. Application of Integrated Geophysical and Geochemical Data Processing to Metallogenic Target Zone Quantitative Prediction and Optimization. Bulletin of Mineralogy, Petrology and Geochemistry. 2017. Vol. 36. N 6, p. 886-890. DOI: 10.3969/j.issn.1007-2802.2017.06.002
- Cheskidov V.V., Lipina A.V., Melnichenko I.A. Integrated monitoring of engineering structures in mining. Eurasian Mining. 2018. N 2, p. 18-21. DOI: 10.17580/em.2018.02.05
- Zhang Qi, Liu Xuelong. Big data: new methods and ideas in geological scientific research. Big Earth Data. 2019. Vol. 3. Iss. 1, p. 1-7. DOI: 10.1080/20964471.2018.1564478
- Trubetskoi K.N., Pytalev I.A., Rylnikov A.G. Automated systems of ore flow quality control at mines. Marksheiderskii vestnik. 2013. N 6 (98), p. 9-14 (in Russian).
- Rylnikova M.V., Tsupkina M.V., Kirkov A.E. Technologies of big data collection and processing – the basis for increasing the reliability of primary information about rock massifs in the development of mineral deposits and technogenic formations. News of the Tula State University. Sciences of Earth. 2023. Iss. 1, p. 308-327 (in Russian). DOI: 10.46689/2218-5194-2023-1-1-308-327
- Zakharov V.N., Kaplunov D.R., Klebanov D.A., Radchenko D.N. Methodical approaches to standardization of data acquisition, storage and analysis in management of geotechnical systems. Gornyi zhurnal. 2022. N 12, p. 55-61 (in Russian). DOI: 10.17580/gzh.2022.12.10
- Kaplunov D.R., Rylnikov A.G. Generalization of modern approaches to quality management technology a t opera ting mines. News of the Tula State University. Sciences of Earth. 2020. Iss. 4, p. 40-53 (in Russian).
- Shvabenland E.E., Lapteva M.I. Principles of mineral raw material quality management in combined mining complex structural deposits. News of the Tula state university. Sciences of Earth. 2021. Iss. 3, p. 326-335 (in Russian). DOI: 10.46689/2218-5194-2021-3-1-320-329
- Turtygina N.A., Okhrimenko A.V., Kovalchuk A.A., Kalashnikov K.A. Planning of mining works as organizational method of quality management for mineral raw materials in mining system. Mining Informational and Analytical Bulletin. 2018. N S17, p. 3-11 (in Russian). DOI: 10.25018/0236-1493-2018-5-17-3-11
- Kantemirov V.D., Yakovlev A.M., Titov R.S., Timokhin A.V. Improvement of mineral processing methods in mining structurally-complex deposits. Russian Mining Industry. 2022. N 1S, p. 63-70 (in Russian). DOI: 10.30686/1609-9192-2022-1S-63-70
- Teziev T.M., Dzhioeva A.K. The optimal block length when developing compound narrow pitching veins. Vestnik Magnitogorskogo gosudarstvennogo tekhnicheskogo universiteta im. G.I.Nosova. 2015. N 1 (49), p. 5-9 (in Russian).
- Changbin Wang, Guangyao Si, Chengguo Zhang et al. Location error based seismic cluster analysis and its application to burst damage assessment in underground coal mines. International Journal of Rock Mechanics and Mining Sciences. 2021. Vol. 143. N 104784. DOI: 10.1016/j.ijrmm