Направления технологического развития алюминиевых электролизеров
- 1 — д-р техн. наук заместитель директора научного центра Санкт-Петербургский горный университет императрицы Екатерины II ▪ Orcid
- 2 — д-р техн. наук академик РАН Российская академия наук ▪ Orcid
Аннотация
Проанализированы направления технического и технологического развития алюминиевой промышленности, действующих и перспективных проектов уменьшения энергопотребления и экологической нагрузки на окружающую среду. Обсуждается активное участие государства в организации финансовых инструментов экологической реконструкции изношенных производственных мощностей. Несмотря на то, что технология алюминиевых электролизеров развивается в направлении увеличения единичной мощности, но с ограниченным потенциалом уменьшения энергопотребления и выброса парниковых газов, возможности повышения удельной производительности практически отсутствуют. Поэтому возникают и развиваются такие проекты как электролизеры с инертным анодом и дренированным катодом, успешное завершение которых маловероятно после многолетних исследований и полупромышленных испытаний. Для продолжения работ по инертному аноду требуется однозначный ответ от компетентных организаций о промышленной безопасности локальных источников массивных выделений кислорода в атмосферу. Проект дренированного катода после обсуждения существующих проблем кажется неосуществимым. В противоположность действующей технологии, проектам с инертным анодом и дренированным катодом большие перспективы открывает развитие технологии электролизеров с вертикальным расположением электродов. В лабораторных условиях получены положительные результаты применения электродов специальной формы, гомогенизации их поверхности и развития способов синтеза композитных катодов непосредственно в процессе электролиза. Ожидается, что объединение этих направлений и последовательное масштабирование позволит на новом уровне использовать вертикальные электроды для кратного увеличения удельной производительности электролизеров, уменьшения энергопотребления и выбросов парниковых газов.
Введение
Для развития минерально-сырьевого и топливно-энергетического комплексов необходимо создавать новые технические решения и технологии производства наукоемкой товарной продукции [1-3]. Очевидно, при выборе промышленных технологий и направлений модернизации следует руководствоваться передовыми показателями и понятными механизмами их реализации [4-7]. Кроме того, в рамках глобального энергетического перехода и в стремлении к использованию безуглеродных источников энергии нарастает необходимость адаптации производства к непрерывно ужесточающимся экологическим ограничениям [8-10]. В связи с этим государством и промышленными компаниями предлагается использовать известную с 1960-х годов и признанную во всем мире концепцию наилучших доступных технологий [11].
В России формирование подходов к оценке ресурсной эффективности производства началось с принятием в июле 2014 г. специального Федерального закона № 219-ФЗ от 21.07.2014. Его положениями в нормативное поле было впервые введено понятие «наилучшая доступная технология» (НДТ) с установлением критериев для ее достижения. Полномочия федеральных органов исполнительной власти, порядок и правила определения НДТ были зафиксированы постановлением Правительства № 1458 от 23 декабря 2014 г. Реализацию полномочий в пределах средств бюджетных ассигнований федерального бюджета и курирование по этому постановлению было поручено осуществлять Министерству промышленности и торговли РФ и Федеральному агентству по техническому регулированию и метрологии. Этим же постановлением обозначены участники создания НТД, условия работы Бюро наилучших доступных технологий (Бюро НДТ – ФГАУ «НИИ ЦЭПП») и рабочих групп по сбору, анализу и формированию данных для информационно-технических справочников по наилучшим доступным технологиям (ИТС НДТ). Правилами заложены условия актуализации этих справочников для обновления устаревших и внесения новых данных. В соответствии с поэтапным графиком, утвержденным распоряжением Правительства РФ № 2178-р от 31.10.2014, стартовал процесс разработки ИТС НДТ.
В рамках этой работы в 2016 г. для алюминиевой промышленности был подготовлен первый справочник – ИТС НДТ 11-2016 «Производство алюминия». Его актуализация осуществлялась через каждые три года – в 2019 и 2022 годах. Принятая правительством концепция определения НТД и правил составления справочников использует эволюционное развитие техники, технологий и материалов, т.е. реконструкцию базовых производственных и природоохранных технологий. С другой стороны, для обеспечения развития передовых технологий электролитического получения алюминия в научных центрах компаний интенсивно работают над новыми проектами. На стадии планирования новых направлений расставляются акценты на снижение энергопотребления и экологической нагрузки на окружающую среду, на повышение производительности и срока службы алюминиевых электролизеров. При реализации проектов, особенно стратегических, закладываются и расходуются значительные средства. Поэтому очень важно на стадии их планирования и в процессе реализации понимать риски возможных неудовлетворительных результатов и своевременно корректировать.
В 2014 г. в России был запущен механизм экологической и технологической модернизации изношенных производственных мощностей, набирают обороты внутренние проекты промышленных компаний. Достаточно большой срок, чтобы обсуждать и анализировать экологическую реконструкцию, организованную государственными органами, а также перспективные направления совершенствования, инициирование и реализацию которых осуществляют производители алюминия. Уже на этом этапе можно определить горизонты развития алюминиевой промышленности, действующих и перспективных проектов снижения энергопотребления и уменьшения экологической нагрузки на окружающую среду алюминиевыми электролизерами.
Целью представленного аналитического обзора является определение наиболее перспективной технологии производства алюминия электролитическим способом.
Экологическая реконструкция
ИТС НДТ, содержащие описание достигнутых технологий, показателей эффективности производства и максимально допустимых уровней эмиссий вредных веществ, готовятся в Бюро НДТ с участием отраслевых экспертов и являются платформой для принятия решений о реконструкции устаревших технологий. В справочниках 2019 и 2022 годов основное внимание уделено экологическим и природоохранным показателям. Среди технических и технологических параметров в разделах 4 и 5 по наилучшим доступным технологиям фиксируются только расходные коэффициенты по сырью и выход по току. Такой важный показатель как удельный расход электроэнергии на производство алюминия в НДТ не регламентируется. По результатам рассмотрения экономических аспектов реализации наилучших доступных технологий и уровня капитальных затрат на модернизацию в справочниках констатируется, что «…Конверсия технологии Содерберга на технологию производства алюминия с использованием обожженных анодов потребует не менее 2-4 тыс. $ капитальных вложений на 1 т алюминия. С учетом текущего уровня цен, рентабельности производства, сроков модернизации и стоимости заемных средств такой проект не будет окупаться». И тем не менее, весной 2021 г. ОК РУСАЛ объявляет о модернизации четырех сибирских заводов, работающих по технологии Содерберга. Утверждается, что проект носит природоохранный характер – половина электролизеров, работающих по старой технологии в Красноярске, Братске, на иркутском заводе и в Новокузнецке, заменяются на самые современные – РА-550. В рамках этого проекта РУСАЛ модернизирует электролизеры, производящие более 1,4 млн т алюминия (35 % мощностей). Объем производства в итоге не изменится, но выброс фторидов на модернизируемой группе электролизеров уменьшится на 73, а бензапирена – на 100 %. В это же время, в апреле 2021 г., компания En+ Group (РУСАЛ) анонсировала производство алюминия по технологии инертного анода и объявила о цели достичь нулевого уровня выбросов парниковых газов к 2050 г., а к 2030 г. – сократить их на 35 %.
В поддержку ИТС НДТ постановлением правительства РФ в 2021 г. утверждены критерии проектов устойчивого развития РФ, в том числе для алюминиевой промышленности. Прежде всего, указывается на необходимость соответствия показателей ресурсной и энергетической эффективности параметрам, зафиксированным в справочнике второго поколения ИТС 11-2019 «Производство алюминия». Критериями оговариваются текущие технические и технологические параметры производства первичного алюминия. Предлагается использовать уже достигнутые экологические параметры:
- показатель прямых выбросов парниковых газов не более 1,514 т СО2-экв/т алюминия (Scope 1);
- показатель суммарных выбросов от электролиза и производства электроэнергии 3 т СО2-экв/т Al (текущие 2,2 т СО2-экв/т Al для бренда ALLOW, Scope 2).
Затем в марте 2023 г. постановлением правительства РФ внесены изменения в критерии проектов устойчивого развития РФ. В новой редакции уже отсутствует критерий необходимости соответствия показателей ресурсной и энергетической эффективности параметрам, зафиксированным в справочниках по наилучшим доступным технологиям. Таким образом, из приоритетных целей проектов исключается необходимость достижения лучших показателей энергосбережения и повышения эффективности использования ресурсов, которые обеспечивают экологические параметры производства. Кроме того, устанавливается критерий соответствия «…нижнему уровню индикативного показателя (ИП2) удельных выбросов парниковых газов для производственных процессов электролитического получения первичного алюминия согласно информационно-техническому справочнику по наилучшим доступным технологиям «Производство алюминия» (ИТС 11-2022)». Но, в соответствии с этим справочником, парниковые газы отсутствуют в перечне загрязняющих веществ, подлежащих госрегулированию (распоряжение Правительства РФ № 1316-р от 08.07.2015). И тогда мы вынуждены констатировать, что для модернизации производства действующих технологий электролиза предлагается пользоваться текущими показателями прямых выбросов парниковых газов в пределах 1,5-3,2 т СО2-экв/т Al (Scope 1), а показатель суммарных выбросов от электролиза и производства электроэнергии (Scope 2) в критериях проектов устойчивого развития отсутствует. Таким образом, в результате утвержденных изменений критерии проектов устойчивого развития таковыми не являются, т.е. сделан шаг назад относительно первой редакции критериев 2021 г.
Дополнительные критерии для модернизируемых и вновь строящихся производственных объектов, перечисляемые в документах правительства РФ, целиком относятся к экологическим. Предприятия должны удовлетворять, по крайней мере, одному дополнительному критерию, например, перспективным технологиям:
- производство алюминия с использованием инертных анодов;
- использование тепла отходящих газов пирометаллургических процессов для производства тепловой и электроэнергии в котлах-утилизаторах;
- технология улавливания и хранения парниковых газов (СО2) – CCS Сarbon Capture & Storage.
Иными словами, рассматривается технология инертного кислородвыделяющего анода, разрабатываемого в ОК РУСАЛ с 2004 г., но предусмотрительно предлагается перспективная разработка технологии улавливания и хранения диоксида углерода CCS.
Итак, наилучшие доступные технологии производства алюминия зафиксированы в отраслевых информационно-технических справочниках на уровне достигнутых. На этом основании правительством РФ в постановлениях определены критерии экологических проектов алюминиевой отрасли, в том числе электролитического получения алюминия. Документы закладывают основу для привлечения «зеленого финансирования» на реализацию особой категории проектов – зеленых и адаптационных (совместно – проектов устойчивого развития), устанавливают основы отечественной инфраструктуры ответственного инвестирования. Фактически между государством и металлургами заключается взаимовыгодная сделка. Алюминиевая компания получает средства на реконструкцию изношенных производств и возможность для технического и технологического развития. Государство обретает уверенность в обеспечении экологических норм и рабочих мест на современном производстве.
Перспективные направления
В электролитическом производстве алюминия за последние 120-125 лет почти вдвое уменьшен уровень выделения парниковых газов – в среднем до 1,4 т СО2-экв/т Al, достигнут внушительный прогресс в снижении энергопотребления – с 40 до 13,0-13,5 кВт·ч/кг Al [12, 13]. Тем не менее объем выбросов парниковых газов остается высоким, а статья затрат на электроэнергию в себестоимости металла существенной – 30-40 % в зависимости от источника энергии. Кроме того, попытки алюминиевых компаний увеличить удельную производительность электролизеров ограничены допустимыми пределами повышения плотности тока и горизонтальным расположением электродов. Эти обстоятельства стимулируют непрерывные исследования, разработки и испытания новых технологий, направленных на уменьшение удельного расхода электроэнергии и выбросов вредных веществ, повышение производительности алюминиевых электролизеров.
Энергопотребление
В условиях работы современных электролизеров под контролем автоматической системы управления технологического процесса (АСУТП) при максимально достижимом выходе по току и с оптимальной конструкцией ошиновки снижение энергопотребления возможно только за счет минимизации напряжения на электролизере
где I – сила тока на электролизере (в серии); Ri – омические сопротивления электролита в междуполюсном зазоре, пузырькового слоя, электродов, контактов и соединительных систем в катодном и анодном устройствах.
При стандартном ведении технологии и использовании обожженных анодов высокого качества на обратную ЭДС ЕЭДС повлиять сложно или невозможно. Некоторое уменьшение омических потерь напряжения
Большое внимание уделяется потерям напряжения в катодных блоках – суммарный перепад напряжения в подине в среднем около 380 мВ, что соответствует расходу электроэнергии около 1200 кВт·ч/т Al. Потери напряжения в этом узле можно снизить до 250 мВ использованием оптимальной технологии сопряжения в контакте блюмс – блок и выбором катодных блоков с повышенным содержанием графита, т.е. сэкономить около 420 кВт·ч/т Al. Но это достижение может быть сохранено в течение всего срока службы электролизера только при удачном выборе проекта катодного устройства и адекватной технологической политике монтажа и ведения электролитического процесса. Слово «удачный» здесь вполне уместно, поскольку невозможно точно спрогнозировать результаты движения катодных блоков и межблочных швов при работе электролизера, фильтрации через углеродную подину расплава, накопления его в объеме в жидкой и твердой фазах, а также состояние контакта блюмс – блок и другие факторы.
Основной резерв уменьшения энергопотребления в алюминиевом электролизере локализован в узком пространстве междуполюсного зазора. Потери напряжения происходят в слое электролита с удельным сопротивлением около 0,5 Ом·см. При плотности тока 0,80 А/см2 и выходе по току 0,93 % изменение междуполюсного расстояния (МПР) на 1 см соответствует напряжению около 400 мВ, т.е. энергетической составляющей примерно 1300 кВт·ч/т Al. Это означает, что для серии современных электролизеров средней и сверхвысокой мощности (300-600 кА) уменьшение МПР с 4 до 3 см теоретически позволяет снизить расход электроэнергии с 13200 до 11900 кВт·ч на 1 т произведенного алюминия. Очевидно, что даже с учетом возможного потенциала АСУТП, ошиновки и материалов футеровки эти значения являются предельными для стандартной действующей технологии электролиза с горизонтальным расположением электродов.
Дальнейшее незначительное уменьшение МПР и расхода электроэнергии возможно только с привлечением катодных материалов, смачиваемых расплавленным алюминием. В этом случае создаются условия для доведения уровня металла на смачиваемой подине с 10-15 до 5-7 см и, тем самым, уменьшения порога МГД-нестабильности. При умеренной циркуляции расплавов, равномерном распределении концентрации глинозема в объеме электролита и удалении анодных газов с подошвы электродов существует вероятность уменьшения МПР еще на 0,5 см (до 2,5 см), т.е. предполагается возможность снижения энергопотребления до 11250 кВт·ч/т Al. Возможно, это предел для стандартной технологии Эру – Холла с элементами инновационных катодных материалов. Однако необходимо соотносить этот вероятно достижимый уровень расхода электроэнергии с затратами на создание специальных композитных материалов.
Инертный анод
Концепция инертных анодов для электролиза расплавов впервые была предложена Ч.М.Холлом в знаменитом патенте 1886 г. [19] и продолжена А.И.Беляевым и Я.В.Студенцовым в 1930-х гг. [20-22]. При этом Ч.Холл пытался использовать медные аноды, а российские исследователи – металлические, оксидные и ферритовые. В дальнейшем инертным анодам было посвящено огромное количество работ [23-25], которые нашли отражение в больших обзорах [26, 27], статьях [28-30] и отчетах.
Поэтому для обсуждения предлагается направление, которое не рассматривалось в указанных публикациях. Сразу заметим, что обсуждаются не результаты наших исследований, но существующие представления специалистов по промышленной безопасности. Речь идет о кислороде, выделяемом на инертном аноде в количестве 0,9 т при производстве 1 т алюминия, что по утверждению компании En+ Group эквивалентно 70 га леса. Продолжая эту арифметику, предполагаемая работа алюминиевого завода с годовой производительностью 500 тыс. т алюминия равносильна выделению около 1230 т кислорода в сутки и насаждению 35 млн га лесного массива за год. Кажущиеся перспективы удовлетворяют как потенциальных производителей кислорода, так и местные власти с населением вокруг завода.
С другой стороны, В.Маршалл, известный английский ученый в области промышленной безопасности, утверждает, что при массовом выделении и длительном истечении газов могут образовываться парогазовые облака [31]. Смешение облаков, содержащих избыток кислорода, с воздухом сохраняет избыток кислорода в атмосфере. Например, при смешении 50 % кислорода и 50 % воздуха образуется смесь, содержащая в своем составе более 50 % кислорода. Основная проблема, связанная с избытком кислорода, – это повышенная способность к горению – снижается порог первоначальной энергии вспышки, от которой может начаться горение, увеличивается скорость горения, затрудняется тушение пламени [32].
Изменение состава воздуха и концентрация атмосферных загрязнений зависят от величины и высоты выброса, метеорологических условий, атмосферного давления, направления и скорости ветра. Установлено, что в общем случае наибольшая высота источника выброса определяет его большее рассеивание и меньшую концентрацию примесей. Этому способствуют устойчивость атмосферы, плотная высокая облачность, отрицательный градиент температуры, образование инверсии над трубой или ниже выброса.
Однако в условиях сильной конвективной турбулентности наблюдается волнообразный факел с распространением выброса до уровня земли, где его концентрация может быть значительной (рис.1). Также большая концентрация выброса фиксируется при задымляющем факеле, когда устойчивый слой воздуха находится на небольшом расстоянии, над точкой выброса, а неустойчивый – ниже выброса. При достижении неустойчивым слоем воздуха высоты трубы большие объемы выброса из нее переносятся в направлении ветра к поверхности земли. Это длится не более получаса, но в течение этого времени приземная концентрация выбросов может достигать высоких значений и сохраняться долгое время (рис.2).
Когда с увеличением высоты температура повышается, градиент температуры отрицательный, и атмосферные условия определяются как инверсия. Наличие инверсии уменьшает вертикальное перемешивание выброса (кислородных масс), что приводит к увеличению его концентрации в приземном слое атмосферного воздуха. Повторяемость приземных инверсий и слабого ветра в континентальных районах определяет возможность застоя воздуха в этих областях, концентрирования выбросов и их накопления в приземном слое атмосферы.
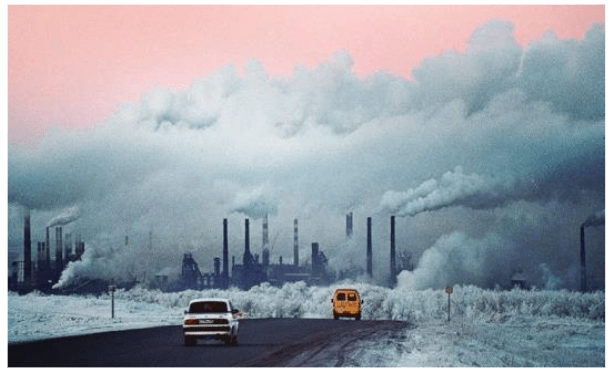
Рис.1. Стелящийся выброс в Новотроицке
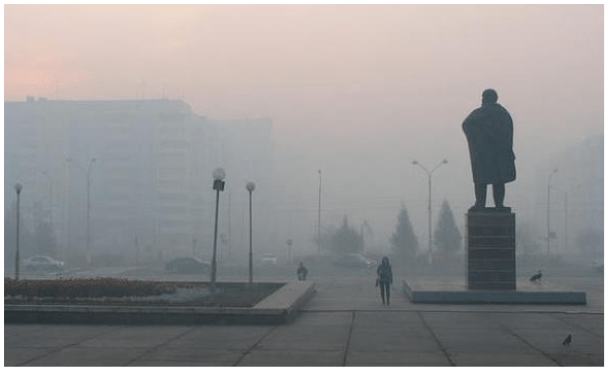
Рис.2. Задымление на главной площади Братска
Максимальные мощности и интенсивность инверсий наблюдаются зимой. Образуется своего рода барьер, препятствующий поднятию загрязненного воздуха в верхний слой атмосферы. На степень загрязнения атмосферного воздуха влияют облачность, туманы, радиационный режим и осадки. Так, низкая облачность препятствует турбулентному обмену в атмосфере и способствует появлению продолжительной инверсии, при которой концентрация выбросов и количество примесей в воздухе увеличивается от 10 до 60 %.
Таким образом, мы обращаем внимание на серьезную проблему – наличие локального источника массивных выделений кислорода в атмосферу. Прежде чем приступать к проектированию таких источников, проблема должна быть тщательно исследована и проанализирована компетентными организациями по промышленной безопасности.
Электролизер с дренированным катодом
Предполагается, что большие экономические дивиденды могут быть получены при запуске в серию электролизеров с дренированным катодом, т.е. с тонким распределенным слоем алюминия на подине и уменьшенным МПР до 1,5-2 см. Для этого необходимо решить проблему создания смачиваемой алюминием катодной поверхности с привлечением специальных материалов на основе карбидов и боридов тугоплавких металлов – титана, циркония, ванадия, тантала, ниобия и гафния.
Концепция применения тугоплавких соединений в 1960-х годах разрабатывалась в British Aluminum Company Ltd (BACO) и Kaiser Aluminum [33, 34]. В это же время компанией Kaiser Aluminum была разработана технология дренированного катода с наклонной подиной и формированием тонкого слоя алюминия на поверхности катода [35]. В научных центрах алюминиевых и огнеупорных компаний в лабораторных и полупромышленных условиях разрабатывались и испытывались:
- компактные изделия из карбидов и боридов тугоплавких металлов в виде пластин, цилиндров и Т-образных элементов [36, 37];
- композитные покрытия на поверхности углеродной подины [38];
- эмульсионные покрытия на основе диборида титана [39].
В последующие годы концепция электролизеров с дренированным катодом, позволяющая снизить расход электроэнергии и уменьшить затраты на ошиновку, развивалась многими научными центрами [40-42], но до сих пор коммерческих материалов для смачиваемых катодных устройств электролизеров не существует. Задача, поставленная в середине 20-го века, до сих пор не нашла своего решения на индустриальном уровне. Однако, эта идея настолько привлекательна, что и в настоящее время научные центры алюминиевых компаний продолжают заниматься проектами электролизеров с дренированным катодом. Поэтому необходимо рассмотреть проблемы, с которыми столкнулись исследователи при испытании смачиваемых катодных материалов.
Компактные изделия из боридов и карбидов тугоплавких металлов, имея приемлемую коррозионную стойкость в расплавленных солях и алюминии, предрасположены к терморастрескиванию и отслаиванию от токопроводящей основы. Попытки создания изделий комбинацией индивидуальных соединений, например TiB2-TiC, не устранили эти недостатки прессованных материалов. Серьезным препятствием для развития технологии смачиваемых катодов была их стоимость. Например, в 70-80-е годы прошлого столетия стоимость порошка диборида титана составляла примерно 55 дол./кг, по сравнению с традиционными углеродистыми композициями около 1,32 дол./кг. В настоящее время стоимость TiB2 составляет 500-3000 дол./кг в зависимости от чистоты и метода производства [43], в то время как стоимость углеродных материалов почти не изменилась. Поэтому для большинства испытаний в качестве смачивающего агента применялись диборид титана TiB2 в композиции с углеродом [44, 45] или на связке коллоидного раствора окиси алюминия (Tinor and Thicknor [46, 47]). Смесь TiB2, углеродного материала и других составляющих в виде пасты наносилась толстым сантиметровым слоем на углеродную подину, как это делали в компаниях Martin Marietta Aluminum и Comalco, или тонким миллиметровым слоем коллоидного материала – компания Moltech. Однако в обоих случаях покрытия растрескивались и деградировали. Толстый слой пасты растворялся с образованием на поверхности подины слоя суспензии Al/TiB2 [48], тонкий коллоидный слой растрескивался и шелушился с последующим всплытием на поверхность расплавов.
Не отрицая перспектив развития дренированных катодов, J.Keniry высказывает критические соображения по их жизнеспособности [24]: «Дренированный катод подвергает углеродный компонент покрытия агрессивному воздействию электролита, что приводит к его разрушению. Степень износа должна быть относительно равномерной по всему электролизеру, а любое локальное разрушение покрытия из-за особенностей конструкции, пуска или методов эксплуатации может неблагоприятно воздействовать на ресурс всего электролизера. Хотя электролизеры с дренируемыми катодами доказали свою жизнеспособность, их промышленное применение вызывает сомнения до тех пор, пока не будет увеличена экономическая прибыль, чтобы компенсировать операционный риск». J.Keniry, сотрудник частной австралийской компании Alumination Consulting Pty Ltd, был хорошо осведомлен о результатах испытаний дренированных катодов в Comalco. Ключевым замечанием в его критическом отношении к смачиваемому покрытию является неравномерная степень износа поверхности композитного покрытия. Этот недостаток трудноустраним, поскольку практически невозможно создать слой композита с равномерными адгезией к основе, плотностью, пористостью, электропроводимостью, прочностью и другими эксплуатационными свойствами по обширной поверхности катода. Это невозможно сделать и на стадии монтажа и уплотнения слоя, и в процессе его обжига и пуска электролизера. К тому же проект электролизера с дренированным катодом не является экологическим, но направлен на возможность уменьшения энергопотребления и увеличения производительности. Для обеспечения энергетического баланса и недостаточного выделения тепла в уменьшенном МПР в проект электролизера необходимо закладывать повышенную плотность тока. Это еще в большей степени усугубит негативные последствия.
Следует признать, что ни в одном из научно-исследовательских центров производителей алюминия обсуждаемые проблемы не решены полностью и окончательно. Это объясняет отсутствие коммерческих электролизеров с дренированным катодом, несмотря на более чем 70-летние попытки их развития. Поэтому проектирование электролизера с дренированным катодом, по всей видимости, является бесперспективным (малоперспективным) направлением по следующим причинам:
- Отсутствуют технологии создания смачиваемых алюминием покрытий с однородными по площади и объему эксплуатационными свойствами. Кроме того, не существует технической и технологической возможности синхронизации движения катодной основы с процессами усадки-расширения поверхностного слоя.
- Отсутствуют рентабельные технологии создания смачиваемых алюминием массивных компактных изделий (катодных блоков) с однородными по площади и объему эксплуатационными свойствами.
- Тонкий слой алюминия на поверхности катода не позволяет равномерно распределить плотность тока по обширной площади подины, что создает условия для неравномерного распределения тока и потенциала, пассивации катода и нестабильного процесса.
- Действующая технология электролиза с обожженными анодами вплотную приблизилась к предполагаемому энергопотреблению электролизеров с дренированным катодом.
- Объективно отсутствуют перспективы изменения (увеличения) удельной производительности относительно действующей технологии.
Электролизеры с вертикальным расположением электродов
С этого направления начиналась история получения алюминия электролитическим способом. В 1854 г. сначала Р.Бунзен и А.Девиль, затем такие известные ученые 19-го века как Ф.Лонтин, Ч.Брэдли и, наконец, П.Эру и Ч.Холл начинали лабораторные эксперименты в ячейках с вертикальным расположением электродов [49, 50]. Более того, по этой схеме начинали работать первые пилотные электролизеры компании Pittsburgh Reduction Co., но затем самопроизвольно перешли на электролиз с горизонтальным расположением катода и анода.
С тех пор попытки развития электролиза криолитоглиноземных расплавов с применением твердых электродов не прекращались [51, 52] и продолжаются в настоящее время [53, 54]. Эта настойчивость, с одной стороны, объясняется стремлением к минимизации расхода электроэнергии и приближению к теоретически возможным 6,3 и 9,2 кВт·ч/кг Al при использовании углеродных и инертных электродов соответственно. Такая возможность появляется с применением вертикально расположенных электродов с МПР ~ 1,5-2 см. С другой стороны, эта схема расположения электродов позволяет кратно увеличить удельную производительность на ограниченной площади электролизера.
Стандартная производительность зависит от мощности алюминиевых электролизеров, т.е. силы тока, и от величины потерь металла на непроизводительные процессы и утечки тока. Для увеличения производительности в проект электролизера закладывается высокая сила тока, конструктивные узлы и технология, позволяющие максимально увеличить выход по току. Таким образом, единичная производительность электролизера или предприятия в целом, выраженная в килограммах Al в сутки или тоннах Al в год, может повышаться алюминиевыми компаниями, накопившими высокий научный и проектный потенциал и имеющими большой опыт в эксплуатации нескольких поколений электролизеров.
По-другому обстоит дело с удельной производительностью P, которую выражают в массовой наработке алюминия за 24 ч с квадратного метра занимаемой площади или площади анодного/катодного массива в горизонтальной плоскости, – кг Al/м2·сут. Удельная производительность практически не изменяется с повышением мощности электролизера, поскольку с увеличением силы тока пропорционально увеличиваются габариты электролизера в плане для размещения электродов и ошиновки, обеспечивающих проектные плотность тока и выход по току. Поэтому удельная производительность является удобным параметром для характеристики применяющейся технологии и ее сравнения с новыми или проектируемыми технологиями производства алюминия электролитическим способом.
Если относить стандартную производительность электролизеров любой мощности к площади анодного массива в горизонтальной плоскости, т.е. к занимаемой площади производственного помещения (корпуса), удельная производительность будет иметь следующие показатели:
- для электролизеров с горизонтальным расположением электродов ~ 60 кг Al/м2·сут;
- для электролизеров с вертикальным расположением электродов ~ 450 кг Al/м2·сут.
Расчет производительности сделан при заглублении вертикальных электродов в электролит на 1 м.
Именно это различие в удельной производительности (почти в восемь раз) и определяет настойчивые попытки разработки и развития электролизеров с твердыми вертикальными электродами (ТВЭ). Уникальная особенность вертикального расположения анодов и катодов означает кратное уменьшение капитальных расходов на строительство новых заводов. Это предполагает снижение расходов не только на строительные конструкции, но и на алюминиевую ошиновку, поскольку отсутствуют жесткие требования на обеспечение МГД-стабильности расплавов в шахте электролизера.
Однако серьезными сдерживающими факторами, ограничивающим развитие ТВЭ, являются отсутствие коммерческих катодов со смачивающими свойствами и неравномерное распределение тока на поликристаллической поверхности электродов.
Направление создания смачиваемой катодной поверхности в виде паст и адгезионных покрытий в настоящее время не развивается, поскольку экспериментально доказана относительно быстрая деструкция сплошного слоя любой толщины на поверхности массивной основы. И дело не только в отсутствии практических технологий создания покрытий (создаваемых на поверхности катода до его пуска в эксплуатацию) с однородными по площади и объему эксплуатационными свойствами. Неконтролируемое движение катодного массива не может быть полностью синхронизировано с процессами усадки-расширения поверхностного слоя. Кроме того, стоимость механически смешанных композиций на основе углерода с порошком TiB2 для покрытий и, тем более, для катодных блоков, неприемлемо высока в расчете на один электролизер. Поэтому привлекательным выглядит направление синтеза композитных катодных изделий любых конфигураций и габаритов непосредственно в процессе электролитического получения алюминия [55, 56]. Очевидно, что в цитируемых патентах отсутствует информация о ноу-хау технологии.
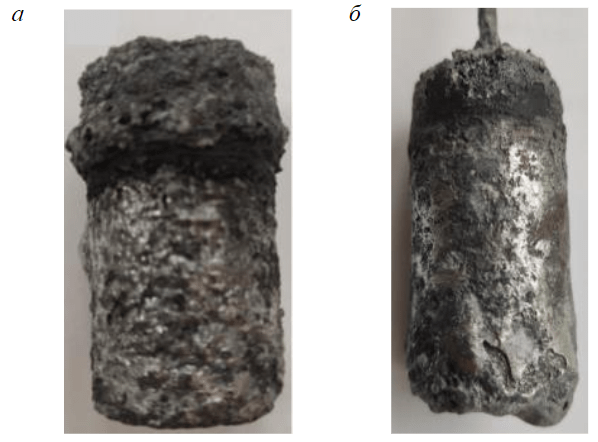
Рис.3. Образцы композита после электролиза: а – С-TiC; б – С-TiB2
В научном центре «Проблем переработки минеральных и техногенных ресурсов» Санкт-Петербургского горного университета императрицы Екатерины II в лабораторных условиях изучалась возможность синтеза композитного катодного материала углерод – диборид/карбид титана (C-TiC/TiB2) в процессе электролиза. В качестве исходных компонентов для подготовки электродов использовался нефтяной кокс, оксиды титана и бора, углеродсодержащее связующее. После прессования и обжига при 1050 °С электроды устанавливали в графитовую электролизную ячейку с расплавленным электролитом состава NaF/AlF3 ≈ ≈ 2,5 при температуре 960 ± 5 °С. Композитные электроды с оксидами титана и бора подвергали катодной поляризации в течение 24 ч.
После извлечения электродов из ячейки и очистки от электролита на поверхности был обнаружен слой алюминия, что свидетельствовало о смачиваемости катодов металлом (рис.3). Рентгенофазовый анализ (РФА) показал в составе электродов карбид титана TiC (рис.4, а), при подготовке дозировался только оксид титана. При создании исходного композита C-TiO2/B2O3 рентгенофазовый анализ конечного продукта после электролиза обнаруживал присутствие TiC и бората титана TiBO3 (рис.4, б), продукта окисления диборида титана в момент извлечения электрода из электролизной ячейки. Таким образом, была подтверждена возможность создания катодного композитного материала со смачивающими свойствами непосредственно в процессе электролиза. Учитывая примерно одинаковый порядок цен на углеродные материалы, оксиды титана и бора, стоимость производства композитных изделий любых габаритов изменится незначительно.
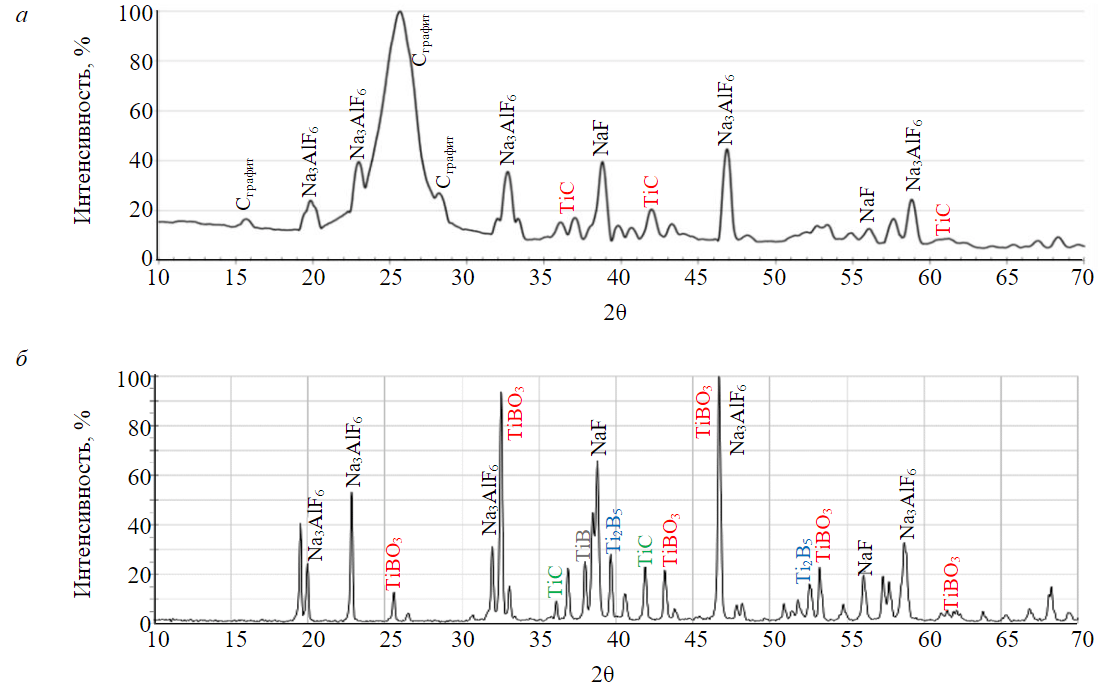
Рис.4. Результаты РФА электродов С-TiC (а) и С-TiB2 (б)
Неравномерное распределение тока
Эта проблема не очевидна при визуальном наблюдении за процессом электролиза с применением твердых электродов, но она выражается нестабильностью напряжения в системе, повышенным расходом анодов и пассивацией катода компонентами электролита. Именно с этими последствиями, но не с причинами нестабильности процесса, пытались и пытаются справиться исследователи [54, 57]. Дестабилизация электролиза в лабораторных условиях наступает при увеличении плотности тока выше 0,5 А/см2 [58-60]. Предлагаемые рекомендации снижения температуры электролиза, корректировки состава электролитов и электродов не решают проблему и не позволяют перейти к развитию на коммерческой основе.
Причиной этих проблем и ограничений на основании экспериментальных данных [61, 62] и численных исследований [63, 64] предлагается принять физическую и химическую неоднородность поверхностной структуры поликристаллических электродов. Химическая неоднородность в процессе эксплуатации постепенно трансформируется в физическую. Это справедливо как для покрытий, так и для компактных электродных изделий любого состава – на основе углерода, боридов/карбидов тугоплавких металлов или их композиций.
Линии тока на микроуровне будут концентрироваться на выступах шероховатой поверхности, пор, трещин, царапин. Этот же эффект реализуется на макроуровне для периферийных участков электродов – ребер или острых краев. На участках с повышенной плотностью тока и потенциалом увеличивается скорость электродных процессов с развитием концентрационной поляризации и неконтролируемого формирования критических электродных потенциалов для присутствующих простых и комплексных ионов. На положительном электроде это будет приводить в той или иной степени к выделению газообразных фторуглеродов на углеродном аноде и фтора на инертном аноде с соответствующими негативными последствиями – повышенным расходом электрода.
На смачиваемом катоде развивается разряд электроотрицательных примесей и разложение составляющих электролита с последующей пассивацией поверхности и прогрессирующей дестабилизацией электролиза (эти негативные последствия характерны и для дренированного катода). Таким образом, различается микронеоднородность, связанная с шероховатой поверхностью по всей площади, и макронеоднородность распределения тока на периферийных участках электродов (краевой эффект). Этот подход определяет разработку различных технологий выравнивания токораспределения по электродам.
Компенсировать краевой эффект и существенно снизить макронеоднородное распределение тока позволяет эллиптическая форма электродов с адекватным увеличением междуполюсного расстояния и сопротивления электролита от центра к периферии. В отличие от использования прямоугольных электродов, на протяжении всего эксперимента в электролизной ячейке с металлическими анодом и катодом эллиптической формы процесс электролиза протекал стабильно, пассивации катода не наблюдалось, скорость растворения анодов сокращалась примерно в три раза [62].
Но специальной формы недостаточно для стабильного ведения процесса с применением твердых электродов, поликристаллических и литых, однофазных и многофазных, априори имеющих в своей объемной и поверхностной структуре физическую и химическую неоднородность. Поэтому был предложен и осуществлен один из возможных методов гомогенизации поверхности непосредственно в процессе электролиза – электрохимическое микроборирование катодов, имеющих в своем составе тугоплавкие металлы и их оксиды [61]. Метод основан на значительном, почти в два раза, различии стандартных потенциалов разряда алюминия (Е0р = –1,18 В) и бора (Е0р = –0,63 В). При совместном присутствии в расплаве условия для разряда во впадинах благоприятны для более электроположительных ионов. И если бор после восстановления во впадине будет встречать на поверхности, например, титан или его оксид, синтез диборида титана будет выравнивать любую неоднородную поверхность. Этот метод может быть применен к любым реактивным или инертным катодам, поверхностная неоднородность которых нивелируется химическим взаимодействием бора с присутствующими примесями и, тем самым, выравнивается физическое состояние поверхности.
Таким образом, выводится простая формула организации электролитического процесса в электролизере с вертикальным расположением твердых электродов: комплексное применение электродов эллиптической формы и электрохимическое микроборирование композитных катодов. Эта формула в общем виде может быть транслирована для перспективного развития алюминиевой промышленности по следующей дорожной карте масштабирования технологий:
- технология электролиза по схеме вертикальных электродов эллиптической формы;
- технология синтеза композитных смачиваемых алюминием катодов непосредственно в процессе электролиза;
- технология электрохимического микроборирования катодной поверхности.
Объединение этих технологий в одну позволит использовать уникальные преимущества технологии электролиза с вертикально расположенными твердыми электродами (см. таблицу).
Сравнительные характеристики технологий электролиза
Параметры |
Расположение электродов |
|
Горизонтальное |
Вертикальное |
|
Расход электроэнергии, кВт·ч/кг Al |
~13,5 |
~11,0 |
Выбросы СО2,* кг СО2-экв/кг Al |
~ 1,4 |
→ 1,0** → 0*** |
Удельная производительность, кг Al/м2∙сут |
~ 60 |
~ 450 |
* Прямые выбросы (Scope 1). ** Композитные электроды. *** Инертные электроды.
Заключение
На основании проведенного обзора были сделаны следующие выводы:
- В России на правительственном уровне организован процесс экологической реконструкции изношенных производственных мощностей, который предполагает самофинансирование ужесточающегося государственного экологического нормирования. В то же время частные компании удовлетворяют свои перспективные технологические и экологические амбиции.
- Для действующей технологии электролиза с горизонтальным расположением электродов, обеспеченной современной АСУТП, ошиновкой и материалами футеровки, просматривается реальная возможность энергопотребления около 12000 кВт·ч на 1 т производимого алюминия. Дальнейшее уменьшение удельного расхода электроэнергии до 11250-11500 кВт·ч/т Al возможно с привлечением катодных материалов, смачиваемых расплавленным алюминием. Эти значения энергоэффективности для действующей технологии являются предельными.
- Развитие технологии инертного (кислородвыделяющего) анода требует тщательного исследования компетентными организациями по промышленной безопасности. При определенных климатических и метеорологических условиях в районе интенсивного источника выделения кислорода возможно создание ситуации с повышенной пожароопасностью.
- Проектирование электролизера с дренированным катодом является малоперспективным предприятием.
- Наиболее перспективной технологией электролиза криолитоглиноземных расплавов является технология электролизеров с вертикальными электродами. При использовании композитных анодов и катодов с уменьшенной активностью углерода возможно значительное сокращение выбросов парниковых газов. Удельная производительность таких электролизеров может быть увеличена в 7-8 раз, что означает многократное уменьшение капитальных расходов на строительство новых заводов относительно действующей технологии с горизонтальным расположением электродов.
Литература
- Литвиненко В.С., Петров Е.И., Василевская Д.В. и др. Оценка роли государства в управлении минеральными ресурсами // Записки Горного института. 2023. Т. 259. С. 95-111. DOI:10.31897/PMI.2022.100
- Zhukovskiy Yu.L., Batueva D.E., Buldysko A.D. etal. Fossil Energy in the Framework of Sustainable Development: Analysis of Prospects and Development of Forecast Scenarios // Energies. 2021. Vol. 14. Iss. 17. № 5268. DOI: 10.3390/en14175268
- Pyagay I.N., Lebedev A.B. Effects of alumina on the stability of ferrite-calcium sinter with dicalcium silicate // CIS Iron and Steel Review. 2023. Vol. 25. P. 10-16. DOI: 10.17580/cisisr.2023.01.02
- Kosolapova S.M., Smal M.S., Rudko V.A., Pyagay I.N. A New Approach for Synthesizing Fatty Acid Esters from Linoleic-Type Vegetable Oil // Processes. 2023. Vol. 11. Iss. 5. № 1534. DOI: 10.3390/pr11051534
- Зубкова О.С., Алексеев А.И., Сизяков В.М., Полянский А.С. Исследование влияния сернокислых солей на процесс отстаивания глинистой суспензии // Известия вузов. Химия и химическая технология. 2022. Т.65. № 1. С. 44-49. DOI: 10.6060/ivkkt.20226501.6447
- Kudinova A.A., Poltoratckaya M.E., Gabdulkhakov R.R. etal. Parameters influence establishment of the petroleum coke genesis on the structure and properties of a highly porous carbon material obtained by activation of KOH // Journal of Porous Materials. 2022. Vol. 29. Iss. 5. P. 1599-1616. DOI: 10.1007/s10934-022-01287-1
- Litvinenko V.S., Dvoynikov M.V., Trushko V.L. Elaboration of a conceptual solution for the development of the Arctic shelf from seasonally flooded coastal areas // International Journal of Mining Science and Technology. 2022. Vol. 32. Iss. 1. P. 113-119. DOI: 10.1016/j.ijmst.2021.09.010
- Khalifa A.A.E.I.A., Bazhin V.Y., Kuskova Y.V. et al. Study the Recycling of Red Mud in Iron Ore Sintering Process // Journal of Ecological Engineering. 2021. Vol. 22. Iss. 6. P. 191-201. DOI: 10.12911/22998993/137966
- Sharikov F.Y., Rudko V.A., Smyshlyaeva K.I. Oxidation thermolysis kinetics of asphaltenes with various chemical prehistory // Thermochimica Acta. 2023. Vol. 726. № 179550. DOI: 10.1016/j.tca.2023.179550
- Зубкова О.С., Пягай И.Н., Панкратьева К.А., Торопчина М.А. Разработка состава и исследование свойств сорбента на основе сапонита // Записки Горного института. 2023. Т. 259. С. 21-29. DOI: 10.31897/PMI.2023.1
- Волосатова А.А., Пятница А.А., Гусева Т.В., Almgren R. Наилучшие доступные технологии как универсальный инструмент совершенствования государственных политик // Экономика устойчивого развития. 2021. № 4 (48). С. 17-23. DOI: 10.37124/20799136_2021_4_48_17
- Haupin W., Frank W. Current and Energy Efficiency of Hall-Heroult Cells // Light Metal Age. 2002. № 5/6. Р. 6-13.
- Choate W.T., Green J.A.S. U.S. Aluminum Production Energy Requirements: Historical Perspective, Theoretical Limits and New Opportunities // ACEEE Summer Study on Energy Efficiency in Industry, 29 July – 1 August 2003, New York, USA. Proceedings from the ACEEE Summer Studies on Energy Efficiency in Industry, 2003. P. 12-24.
- Bardel A., Droste C., Ovstetun F. et al. HAL4e – Hydro’s New Generation Cell Technology // TMS Annual Meeting and Exhibition, 15-19 November 2009, San Francisco, CA, USA. TMS Light Metals 2009: Proceedings of the technical sessions presented by the TMS Aluminum Committee at the TMS, 2009. P. 371-376.
- Lange H.P., Holt N.J., Linga H., Solli L.N. Innovative Solutions to Sustainability in Hydro // TMS Annual Meeting and Exhibition, 9-13 March 2008, New Orleans, LA, USA. TMS Light Metals 2008: Proceedings of the technical sessions presented by the TMS Aluminum Committee at the TMS, 2008. P. 211-216.
- Thonstad J., Rolseth S., Rodseth J. et al. The content of sodium in aluminium in laboratory and industrial cells The Content of Sodium in Aluminum in Laboratory and in Industrial Cells // Light Metals: Proceedings of Sessions, TMS Annual Meeting, Warrendale, Pennsylvania, 2000. P. 441-447.
- Макушин Д.В. Повышение эффективности электролиза алюминия на основе оптимизации распределения микропримесей в системе «электролит-катодный алюминий»: Автореферат дис. ... канд. техн. наук. СПб: Санкт-Петербургский горный институт, 2007. 22 с.
- Meirbekova R., Haarberg G.M., Thonstad J. etal. Effect of Operational Parameters on the Behavior of Phosphorus and Sulfur in Aluminum Reduction // TMS Light Metals. 2015. P. 559-564. DOI: 10.1007/978-3-319-48248-4_93
- Hall C.M. Patent № 400766 US. Process of Reducing Aluminum by Electrolysis. Publ. 02.04.1889.
- Беляев А.И., Студенцов Я.Е. Электролиз глинозема с несгораемыми (металлическими) анодами // Легкие металлы. 1936. № 3. С. 15-24.
- Беляев А.И., Студенцов Я.Е. Электролиз глинозема с несгораемыми анодами из окислов // Легкие металлы. 1937. № 3. С. 17-21.
- Беляев А.И. Электролиз глинозема с несгораемыми анодами из ферритов // Легкие металлы. 1938. № 1. С. 7-20.
- Brown G.D. TiB2 Coated Aluminium Reduction Cells: Status and Future Direction of Coated Cells in Comalco // Proceedings of the 6th Australasian Aluminium Smelter Technology Conference and Workshop, 1998, Queenstown, New Zealand. Kensington, NSW: University of New South Wales, 1998. P. 499-508.
- Keniry, J. The economics of inert anodes and wettable cathodes for aluminum reduction cells // JOM. 2001. № 53. P. 43-47. DOI: 10.1007/s11837-001-0209-2
- Kvande H., Haupin W. Inert anodes for Al smelters: Energy balances and environmental impact // The Journal of The Minerals, Metals & Materials Society. 2001. Vol. 53. Iss. 5. P. 29-33. DOI: 10.1007/s11837-001-0205-6
- de Nora V. VERONICA and TINOR 2000: New Technologies for Aluminum Production // The Electrochemical Society Interface. 2002. Vol. 11. Iss. 4. P. 20-24. DOI: 10.1149/2.F02024IF
- Welch B. Inert anodes – The Status of the Materials Science, the Opportunities They Present and the Challenges That Need Resolving before Commercial Implementation // Light Metals 2009: Proceedings of the Technical Sessions Presented by the TMS Aluminum Committee at the TMS 2009 Annual Meeting and Exhibition, 15-19 February 2009, San Francisco, California, USA. 2009. P. 971-978.
- Pawlek R. Inert Anodes: An Update // TMS Light Metals. 2014. P. 1309-1313. DOI: 10.1007/978-3-319-48144-9_219
- Padamata S.K., Yasinskiy A.S., Polyakov P.V. Progress of Inert Anodes in Aluminium Industry: Review // Journal of Siberian Federal University. Chemistry. 2018. Vol. 11. № 1. P. 18-30. DOI: 10.17516/1998-2836-0055
- Gupta A.K., Basu B. Sustainable Primary Aluminium Production: Technology Status and Future Opportunities // Transactions of the Indian Institute of Metals. 2019. Vol. 72. Iss. 8. P. 2135-2150. DOI: 10.1007/s12666-019-01699-9
- Маршалл В. Основные опасности химических производств. М.: Мир, 1989. 671 с.
- Мальцев В.М., Мальцев В.И., Кашпоров Л.Я. Основные характеристики горения. М.: Химия, 1977. 320 с.
- Ransley C.E. Patent № 802905 GB. Improvements in or relating to electrolytic cells for the production of aluminium. Publ. 15.10.1958.
- Lewis R.A. Patent № 2915442 US. Production of aluminum. Publ. 01.12.1959.
- Lewis R.A., Hildebrandt R.D. Patent № 3400061 US. Electrolytic cell for production of aluminum and method of making the same. Publ. 03.09.1968.
- McIntyre J., Mitchell D.N., Simpson S. Performance Testing of Cathodic Materials and Designs in a 16 KA Cell and a Test Bed // Light Metals; The Minerals, Metals & Materials Society: Proceedings of the Technical Sessions Sponsored by the TMS Light Metal Committee at the 116th Annual Meeting, 24-26 February 1987, Denver, Colorado, 1987. P. 335-344.
- Tucker K.W. et al. Stable TiB2 – Graphite Cathode for Aluminium Production // Light Metals; The Minerals, Metals & Materials Society: Proceedings of the Technical Sessions Sponsored by the TMS Light Metal Committee at the 116th Annual Meeting, 24-26 February 1987, Denver, Colorado, 1987. P. 345-349.
- Joo L.A., Tucker K.W., McCown F.E. Patent № 4376029 US. Titanium diboride-graphite composits. Publ. 08.03.1983.
- Øye H.A., de Nora V., Duruz J.-J., Johnston G. Properties of a Colloidal Alumina-Bonded TiB2 Coating on Cathode Carbon Materials // Essential Readings in Light Metals, Electrode Technology for Aluminum Production. 2016. Vol. 4. P. 1171-1178. DOI: 10.1007/978-3-319-48200-2_155
- Hudson T.J. Cathode Technology for Aluminum Electrolysis Cells // Light Metals; The Minerals, Metals & Materials Society: Proceedings of the Technical Sessions Sponsored by the TMS Light Metal Committee at the 116th Annual Meeting, 24-26 February 1987, Denver, Colorado, 1987. P. 321-325
- Gessing A.J., Wheeler D.J. Screening and Avaluation Methods of Cathode Materials for Use in Aluminum Reduction Cells in Presence of Molten Aluminum and Cryolite up to 1000°C // Light Metals; The Minerals, Metals & Materials Society: Proceedings of the Technical Sessions Sponsored by the TMS Light Metal Committee at the 16th Annual Meeting, 24-26 February 1987, Denver, Colorado, 1987. P. 327-334
- Alcorn T.R. Pilot Reduction Cell Operation Using TiB2-G Cathodes // Light Metals; The Minerals, Metals & Materials Society: Proceedings of the Technical Sessions Presented by the TMS Light Metals Committee at the 119th TMS Annual Meeting, 18-22 February 1990, Anaheim, California, 1990. P. 413-418.
- Ефимова К.А., Галевский Г.В., Руднева В.В. Современное состояние производства диборида титана: оценка, определение доминирующих тенденций и перспектив // Научно-технические ведомости CПбПУ. Естественные и инженерные науки. 2017. Т. 23. Вып. 2. С. 144-158. DOI: 10.18721/JEST.230213
- Boxall L.G., Cooke A.V., Hayden H.W. Use of TiB2 Cathode Material Application and Benefits in Conventional VSS Cells // Essential Readings in Light Metals, Electrode Technology for Aluminum Production. 2016. P. 1145-1152. DOI: 10.1007/978-3-319-48200-2_152
- Cooke A.V., Buchta W.M. Use of TiB2 Cathode Material: Demonstrated Energy Conservation in VSS Cells // Essential Readings in Light Metals, Electrode Technology for Aluminum Production. 2016. P. 1153-1163. DOI: 10.1007/978-3-319-48200-2_153
- Sekhar J.A., Vittorio de Nora. Patent № 5364513 US. Electrochemical cell component or other material having oxidation preventive coating. Publ. 15.11.1994.
- Sekhar J.A., Duruz J.-J., Liu J.J. Patent № 6783655 US. Slurry and method for producing refractory boride bodies and coatings for use in aluminium electrowinning cells. Publ. 31.08.2004.
- Watson K.D., Juric D.D., Shaw R.W., Houston G.J. Patent № 5658447 US. Electrolysis cell and method for metal production. Publ. 19.08.1997.
- Richards J.W. Aluminium: Its History, Occurrence, Properties, Metallurgy and Applications, Including Its Alloys. London: Sampston Low, Marston, Searle & Rivington, 1887. 346 p.
- Minet A. The Production of Aluminium And Its Industrial Uses. London: Chapman & Hall, Limited, 1905. 266 p.
- Griswold Jr. T. Patent № 1070454 US. Electrolytic cell. Publ. 19.08.1913.
- 52. Johnson A.F. Patent № 2480474 US. Method of producing aluminum. Publ. 30.08.1949.
- Zaikov Y., Khramov A., Kovrov V. et al. Electrolysis of aluminum in the low melting electrolytes based on potassium cryolite // TMS Light Metals. 2008. № 1. P. 505-508.
- Shengzhong Bao, Dengpeng Chai, Zhirong Shi et al. Effects of Current Density on Current Efficiency in Low Temperature Electrolysis with Vertical Electrode Structure // 147th Minerals, Metals & Materials Society Annual Meeting and Exhibition, 11-15 March 2018, Phoniex, AZ, USA. TMS Light Metals, 2018. P. 611-619. DOI: 10.1007/978-3-319-72284-9_79
- Патент № 2232211 РФ. Способные к смачиванию и устойчивые к эрозии/окислению углеродсодержащие композитные материалы / А.А. Миртчи, Д. Бергерон. Опубл. 10.07.2004.
- Патент № 2793027 РФ. Способ получения композитного углеродсодержащего материала / А.А.Поляков, Е.С.Горланов, И.Н. Пягай и др. Опубл. 28.03.2023. Бюл. № 10.
- Ткачева О.Ю. Низкотемпературный электролиз глинозема во фторидных расплавах: Автореф. дис. ... д-ра хим. наук. Екатеринбург: Учебно-методический центр Уральского государственного технического университета, 2013. 36 с.
- Suzdaltsev A.V., Nikolaev A.Y., Zaikov Y.P. Towards the Stability of Low-Temperature Aluminum Electrolysis // Journal of the Electrochemical Society. 2021. Vol. 168. № 4. № 046521. DOI: 10.1149/1945-7111/abf87f
- Николаев А.Ю., Ясинский А.С., Суздальцев А.В. и др. Электролиз алюминия в расплавах и суспензиях KF-AlF3-Al2O3 // Расплавы. 2017. № 3. С. 205-213.
- Nikolaev A.Y., Suzdaltsev A.V., Zaikov Y.P. Cathode Process in the KF-AlF3-Al2O3 Melts // Journal of the Electrochemical Society. 2019. Vol. 166. № 15. P.D784-D791. DOI: 10.1149/2.0521915jes
- Горланов Е.С. Легирование катодов алюминиевых электролизеров методом низкотемпературного синтеза диборида титана: Автореф. дис. ... д-ра техн. наук. СПб: Санкт-Петербургский горный университет, 2020. 40 с.
- Поляков А.А. Распределение тока и потенциала по поверхности вертикальных электродов при электролитическом получении алюминия: Автореф. дис. … канд. техн. наук. СПб: Санкт-Петербургский горный университет, 2022. 20 с.
- Gorlanov E.S., Polyakov А.А. On the question of using solid electrodes in the electrolysis of cryolite-alumina melts. Part 3. Electric field distribution on the electrodes // iPolytech Journal. 2021. Vol. 25. № 2. P. 235-251. DOI: 10.21285/1814-3520-2021-2-235-251
- Polyakov A.A., Gorlanov E.S., Mushihin E.A. Analytical Modeling of Current and Potential Distribution over Carbon and Low-Consumable Anodes during Aluminum Reduction Process // Journal of the Electrochemical Society. 2022. Vol. 169. № 5. № 053502. DOI: 10.1149/1945-7111/ac6a16