Directions in the technological development of aluminium pots
- 1 — Ph.D., Dr.Sci. Deputy Director of Scientific Center Empress Catherine II Saint Petersburg Mining University ▪ Orcid
- 2 — Ph.D., Dr.Sci. Academician RAS Russian Academy of Sciences ▪ Orcid
Abstract
Directions for the technical and technological development of aluminium industry, existing and promising projects to reduce the energy consumption and the environmental impact are analyzed. The active participation of the state in the organization of financial instruments for the ecological reconstruction of obsolete production facilities is discussed. In spite of the fact that the technology of aluminium pots is developed towards the increase of a single capacity, but with limited potential of reducing energy consumption and greenhouse gases emission, the possibilities for the increase of specific output are practically non-existent. Therefore, such projects like pots, equipped with inert anodes and drained cathodes arise and are under development, the successful completion of which is unlikely after multi-year researches and pilot tests. To continue the works related to inert anodes the decisive answer about the industrial safety of local sources of the massive oxygen emissions to atmosphere is required from competent entities. The drained cathode project, after discussing the existing problems, seems unfeasible. As opposed to the existing technology the development of the pots with vertical electrodes offers great opportunities to the designs of inert anodes and drained cathodes. Positive results of using shaped electrodes, homogenizing their surface and developing the methods for the synthesis of composite cathodes directly during the electrolytic process were obtained in laboratory conditions. It is expected that the combination of these trends and the successive dimensional scaling shall allow using the vertical electrodes at the next level for the fold increase of specific pot capacity and for the decrease of energy consumption and greenhouse gas emissions.
Introduction
To develop the mineral-raw material and fuel-and-energy complexes it is necessary to develop new technical solutions and technologies for the production of science-intensive commercial output [1-3]. It is obvious that the selection of industrial technologies and directions for the modernization shall be guided by best parameters and conceivable mechanisms for their implementation [4-7]. In addition, for the purpose of global energy transition and in pursuit of using carbonless energy sources the need to adapt the production to progressively more stringent environmental restrictions increases [8-10]. In that event the state and industrial companies propose to use the conception of best available technologies that is world-recognized and known from 1960-s [11].
In Russia the elaboration of approaches to the estimation of production efficiency related to resources started up by enacting the special Federal Law N 219-FZ dated 21.07.2014. Its provisions introduced the concept of “best available technology” (BAT) to the regulatory environment for the first time and they established criteria for its achievement. Powers of federal agencies of executive authority, order and rules for BAT definition were evidenced in the Government decree N 1458 of December 23, 2014.According to this decree the exercise of powers within federal budget allocations and its supervision were assigned to the RF Ministry for Industry and Trade and to the Federal Technical Regulation and Metrology Agency. This same decree defines participants of BAT deve-lopment, working conditions for the Bureau for best available technologies (BAT Bureau – Federal State Independent Institution “Research Institute Center of Environmental Industrial Policy”) and working groups to collect, analyze and generate data for information and technical reference books on best available technologies. The rules underlay conditions for the actualization of these reference books in order to renew obsolete data and to introduce new ones. In accordance with milestone sche-dule, approved by RF Government edict N 2178-р dated 31.10.2014, the process of BAT reference-book development started up.
Under this work, the first information and technical reference book for aluminium industry ITS NDT 11-2016 “Aluminium Production” was issued in 2016. Its actualization took place every three years – in 2019 and in 2022. The conception for the definition of normative and technical documentation and rules for the compilation of reference books, adopted by the government, uses the evolutionary development of technical facilities, technologies and materials, i.e. the reconstruction of basic production and environmental protection technologies. From the other side, to provide the development of up-to-date technologies of electrolytic aluminium production the scientific centers of companies work hard on new projects. At the stage of new tendencies planning the accent is made on the reduction of energy consumption and environmental impact, on the increase of aluminium pots capacity and service life. The implementation of the projects, in particular, strategic ones, requires and spends considerable financial resources. Therefore, at the stage of projects planning and during their realization it is very important to be aware of the risks of possible unsatisfactory results and to correct them on time.
In 2014 the mechanism of ecological and technological modernization of obsolete production facilities was started up in Russia. The internal projects of industrial companies gather speed. The time period is rather long in order to discuss and analyze the ecological reconstruction, organized by state entities, and promising trends of modernization, which is initiated and implemented by aluminium producers. Even at this stage it is possible to define perspectives of aluminium industry development and perspectives of existing and promising projects for the decrease of energy consumption and environmental impact by aluminium pots.
The purpose of analytical overview presented is to define most promising technology for the production of aluminium by electrolytic method.
Ecological reconstruction
BAT Information and technical reference books that contain the description of available technologies, production efficiency indices and maximum admissible levels of harmful emissions, are prepared in BAT Bureaus with participation of industry experts, and these reference books are the platform for the decision making on the modernization of obsolete technologies. Reference books of 2019 and 2022 are focused on ecological and environmental protection parameters. As to technical and technological parameters, sections 4 and 5 related to best available technologies, fix parameters of raw material consumption and current efficiency only. Such important parameter like specific consumption of electric energy for the aluminium production is not provided in BAT normative and technical documentation. Upon the results of the consideration of economic aspects of the best available technologies implementation and levels of capital expenses on the modernization, the reference books state “…The conversion of Soderberg technology into the technology of aluminium production using pre-bake anodes shall require at least $ 2-4 thousand of capital investments per 1 ton of aluminium. Taking into account the current price level, production profitability and cost of borrowing, such project shall not be cost-effective”. However, in spring of 2021 UC RUSAL announces the modernization of four Siberian Soderberg smelters. It is said that the project is of environmental protection nature – half of the pots, operating according to the old technology in Krasnoyarsk, Bratsk, Irkutsk, and Novokuznetsk, shall be substituted by most modern ones – РА-550. Under this project RUSAL modernizes pots that produce more than 1.4 Mt of aluminium (35 % from all capacities). As the result, the production volume shall not change but the emission of fluorides from modernized pots shall drop by 73 % and the emission of benzopyrene shall decrease by 100 %. At the same time in April 2021, the company En+ Group (RUSAL) announced the production of aluminium using the inert anode technology and declared the target to achieve the zero level of greenhouse gas emissions by the year of 2050, and by 2030 to reduce reducing them by 35 %.
In 2021 in support of information and technical reference books the decree of RF government approved criteria for RF sustainable development projects, including those for aluminium industry. First of all, it highlights the need to correlate parameters of resource and energy efficiency with parameters, fixed in the reference book of second generation ITS 11-2019 “Aluminium production”. Criteria stipulate current technical and technological parameters of primary aluminium production. It is proposed to use ecological parameters, already achieved:
- direct emissions of greenhouse gases – not more than 1.514 t СО2-equ/t aluminium (Scope 1);
- total emissions from electrolytic reduction process and from electric energy production – 3 t СО2-equ/t Al (current emissions – 2.2 t СО2-equ/t Al for ALLOW brand, Scope 2).
Then, in March 2023 the RF Government decree made alterations to the criteria for RF sustainable development projects. In the new edition the criterion of the necessary correlation of resource and energy efficiency parameters with parameters, fixed in reference books related to best available technologies, is not already mentioned. So, the need in achievement of best indices for energy saving and for increase of the efficiency of resources use, which provide ecological parameters of the production, is excluded from top targets of the projects. In addition, the criterion of compliance “… with lower level of indicative parameter (IP2) of specific greenhouse gas emissions” is established for the processes of electrolytic primary aluminium production in accordance with information and technical reference book on best available technologies “Aluminium Production (ITS 11-2022)”. However, in accordance with this reference book, greenhouse gases are not available in the list of pollutant matters, subjected to the state regulation (RF Government edict N 1316-р dated 08.07.2015). Therefore, we have to acknowledge that to modernize existing electrolytic reduction technologies it is proposed to use current parameters of direct greenhouse gas emissions within 1.5-3.2 t СО2-equ/t Al (Scope 1). As to the parameter of total emissions from reduction facilities and from energy production facilities (Scope 2), it is missing in criteria for sustainable development projects. Consequently, the approval of alterations resulted in that the criteria for sustainable development projects are not such; it means the step back has been made relative to the first 2021 edition of criteria.
Additional criteria for production facilities under modernization and for newly built ones that are listed in the documents of RF government belong entirely to the ecological criteria. Enterprises have to meet one additional criterion at least; for example, promising technologies:
- aluminium production using inert anodes;
- use of the heat of exhaust gases from pyro-metallurgical processes for the production of thermal and electric energy in waste-heat boilers;
- technology for (СО2) – CCS Carbon Capture & Storage.
In other words, the technology of inert oxygen-emissive anode, developed by UC RUSAL in 2004, is under consideration; but in this respect, the promising development of the technology for carbon dioxide capture and storage is prudently offered.
Thus, the best available technologies for the aluminium production are fixed in industrial information and technical reference books as achieved ones. Based on this, the edicts of RF government define criteria for ecological projects in aluminium branch including electrolytic aluminium production. Documents provide the basis for the involvement of “green financing” for the realization of specific projects – green and adaptation projects (jointly, projects of sustainable development); they provide the basis for national infrastructure of responsible investments. In fact, the mutually profitable deal is concluded between the government and metallurgists. An aluminium company raises the finances for the modernization of obsolete production facilities and gets a chance for the technical and technological development. The state regains confidence in providing ecological standards and working places in modern production sectors.
Promising directions
Over the last 120-125 years on the aluminium production the level of greenhouse gas emissions has been almost halved – in average to 1.4 t СО2-equ/t Al, the significant progress in energy consumption reduction was achieved – from 40 to 13.0-135 kWh/kg Al [12, 13]. However, the volume of greenhouse gas emissions remains high, and the energy cost item in the metal cost value – significant (30-40 %) depending on energy source. In addition, the attempts of aluminium companies to increase the specific capacity of the pots are restricted by admissible limits of current density increase and by horizontal configuration of electrodes. These circumstances encourage continuous investigations, developments and tests of new technologies purposing the reduction in specific electric energy consumption and in harmful matters emissions, and the increase of aluminium pots capacity.
Energy consumption
In conditions of up-to-date pot operation under control of automated process control system with maximum available current efficiency and optimal busbar design the reduction in energy consumption is possible by minimization of pot voltage only
where I – pot amperage (in potline); Ri – resistance of electrolytic bath within the space between anode and cathode, resistances of bubble layer, electrodes, contacts and connecting systems in cathode and anode assemblies.
With standard technology management and use of high-quality pre-bake anodes it is difficult or impossible to have in influence on the back electromotive force ЕEMF. In practice a certain reduction in ohmic voltage loss
A lot of attention is paid to voltage losses in cathode blocks: summarized voltage drop in the pot bottom averages about 380 mV; which corresponds to the electric energy consumption of approx. 1200 kWh/t Al. The voltage losses in this unit can be reduced to 250 mV by applying best available coupling technology in the contact between collector bar and block and by selecting cathode blocks with higher content of graphite; i.e. there is a possibility to save about 420 kWh/t Al. However, this achievement could be saved during the whole service life of the pot only in case of successful selection of the cathode assembly design and adequate technological policy for erection and electrolytic process conduction. The word “successful” is quite appropriate here because it is impossible to predict accurately the results of the movements of cathode blocks and block joints during the pot operation, during the infiltration of the melt through the carbon bottom, its accumulation within liquid and solid phases. It is also impossible to predict the state of the collector bar/block contact and other factors.
The main reserve for the energy consumption decrease within the aluminium pot is localized in the narrow space between anode and cathode. Voltage losses take place in the electrolytic bath layer having the specific resistance of about 0.5 Ohm·cm. At the current density of 0.80 A/cm2 and current efficiency of 0.93 % the change of 1 cm in anode-cathode distance corresponds to the voltage of about 400 mV, i.e. to the energy component of about 1300 kWh/t Al. This means that for the potline consisted of 300-600 kA pots, the reduction in the distance between anode and cathode from 4 to 3 cm allows theoretically to decrease the electric energy consumption from 13200 to 11900 kWh per 1t of produced aluminium. It is obvious that even considering the potentials of Automated Process Control System, busbar and lining materials these values shall be limit values for the standard available reduction technology using horizontal electrodes.
The further insignificant reduction of anode-cathode distance and electric energy consumption is only possible by involving cathode materials wettable with molten aluminium. In this case the conditions shall be established to bring the metal level on the wettable bottom from 10-15 to 5-7 cm and thereby to lower the threshold of MHD-instability (Magneto-Hydro-Dynamic). With moderate melt circulation, equal distribution of alumina concentration within electrolytic bath and evacuation of anode gases from the table of electrodes there is a probability for the reduction of anode-cathode distance for another 0.5 cm (to 2.5 cm), i.e. there is a provision for the decrease of energy consumption to 11250 kWh/t Al. Maybe, this is a limit for standard Hall – Heroult technology with elements of innovative cathode materials. Nevertheless, it is necessary to correlate this apparently attainable level of electric energy consumption with costs on the creation of special composite materials.
Inert anode
The conception of inert anodes for the electrolysis of the melts was firstly proposed by C.M.Hall in famous patent of 1886 [19] and extended by A.I.Belyaev and Ya.V.Studentsov in 1930-s [20-22]. C.Hall tried to use copper anodes and Russian researchers – metallic, oxide, and ferrite anodes. Further, a huge amount of papers was related to inert anodes [23-25], which was evidenced in reviews [26, 27], articles [28-30] and reports.
Therefore, for the discussion we propose the direction that was not considered in above mentioned publications. Let us notice right away that it is not the results of our research that are being discussed, but the existing ideas of specialists in industrial safety. The question is about oxygen that is released on the inert anode in amount of 0,9 t while producing 1 t of aluminium; which according to En+ Group company is equivalent to 70 ha of forest. Continuing this arithmetic, the supposed operation of an aluminium smelter with annual capacity of 500,000 t Al is equivalent to the release of about 1230 t of oxygen per day and to the plantation of 35 million ha of forest area over year. Apparent prospects satisfy both potential oxygen producers and local authorities and population around the smelter.
From the other side V.Marshall, a known English scientist in the field of industrial safety insists that the massive release and prolong outflow of gases could result in the formation of gas-vapor clouds [31]. The mixing of the clouds, containing the excess of oxygen, with air retains the excess of oxygen in atmosphere. For example, while mixing 50 % of oxygen with 50 % of air the mixture is formed that contains more than 50 % of oxygen in its composition. Main problem, related to oxygen excess consists in the enhanced combustibility – the threshold of initial flash energy, which initiates combustion, lowers; the burning speed increases; the flame extinguishment becomes difficult [32].
The change in air composition and the concentration of atmospheric pollutants depend on the emission amount and height, on meteorological conditions, atmospheric pressure, wind direction and speed. It is found that in general case the maximum height of the emission source determines its greater dispersion and lesser concentration of impurities. This is facilitated by the stability of atmosphere, by dense high clouds, negative temperature gradient, formation of inversion over the stack or below the emission point.
However, in conditions of strong convective turbulence the undulating plume flame is observed, propagating the emission to the land level where its concentration could be significant (Fig.1). The high concentration of emission is also fixed with smoking plume when the stable air layer is at the small distance over the emission point and the unstable layer is below the emission point. When the unstable air layer reaches the height of the stack, big volumes of emission from the stack are transferred downwind to the land surface. This lasts not more than half an hour, but during this time the ground-level concentration of emissions can achieve high values and keep for a long time (Fig.2).
When with increase of the height the temperature goes up, the temperature gradient is negative and atmospheric conditions are defined as an inversion. The presence of inversion reduces the vertical mixing of emission (oxygen masses); which results in the increase of its concentration in the surface atmospheric air. The repeatability of surface inversions and gentle breeze at continental areas determines the possibility of air blanketing at these areas, the concentration of emissions and their accumulation in the surface layer of the atmosphere.
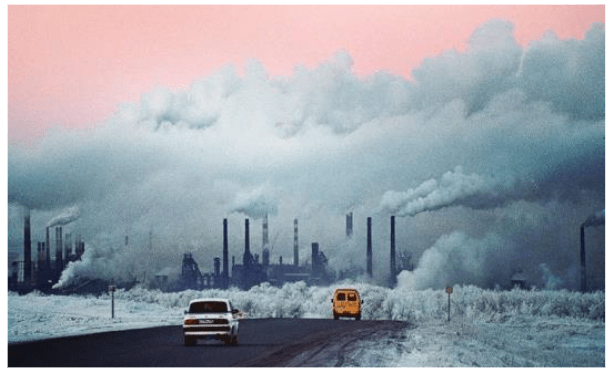
Fig.1. Drifting emission in Novotroitsk
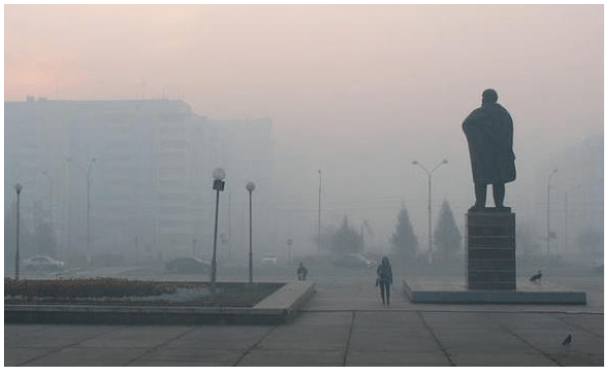
Fig.2. Smoke spread in the main square in Bratsk
Maximum capacities and intensity of inversions are observed in winter. A kind of barrier is formed that prevents the rise of polluted air to upper atmosphere. The degree of atmospheric air contamination is influenced by nebulosity, fogs, radiation regime, and precipitations. Therefore, low nebulosity prevents the turbulent interaction in atmosphere and promotes the emergence of long inversion, under which the concentration of emissions and the quantity of impurities in air increases from 10 to 60 %.
Thus, we attract the attention to the serious problem – presence of local source of massive oxygen emissions to atmosphere. Before to begin the design work on such sources this problem has to be thoroughly examined and analyzed by competent entities, specializing in industrial safety.
Pot with drained cathode
It is supposed that big economic dividends could be received at the startup of the potline consisting of the pots equipped with drained cathodes, i.e. pots having the thin layer of aluminium distributed on the bottom and the anode-cathode distance reduced to 1.5-2 cm. For this purpose, it is necessary to solve a problem of creating the cathode surface wettable with aluminium by involving special materials based on carbides and borides of refractory metals – titanium, zirconium, vanadium, tantalum, columbium, and hafnium.
The conception of applying refractory compounds was developed by British Aluminum Company Ltd (BACO) and Kaiser Aluminum in 1960s [33, 34]. At the same time Kaiser Aluminum developed the technology of drained cathode having an inclined bottom and a thin layer of aluminium formed on the cathode surface [35]. The following products were developed and tested in laboratory and semi-industrial conditions by scientific centers of aluminium and refractory companies:
- compact products from carbides and borides of refractory metals in form of plates, cylinders and T-shaped elements [36, 37];
- composite coatings on the surface of carbon bottom [38];
- titanium diboride-based emulsion coatings [39].
In subsequent years the conception of the pots with drained cathodes allowing to reduce the electric energy consumption and to cut the costs on busbar, was under development in many scientific centers [40-42], but until now the commercial materials for wettable cathodes do not exist. Until now, the task put in the middle of 20th century did not find any solution on the industrial level. However, this idea is so attractive that even now scientific centers of aluminium companies continue to deal with designs of the pots equipped with drained cathode. That is why, it is necessary to consider problems faced by researchers when they tested wettable cathode materials.
Compact products from borides and carbides of refractory metals having a satisfactory corrosion resistance in molten salts and aluminium, are liable to thermal cracking and scaling from current conducting base. Attempts to create products by combining individual compounds, like TiB2-TiC, did not eliminate these defects of pressed materials. The serious obstacle for the development of the technology of wettable cathodes was their value. For example, in 70-80s of last century the price of titanium diboride powder made approx. 55 dol./kg in comparison with traditional carbon compounds, about 1.32 $/kg. At present, the cost of TiB2 makes 500-3000 $/kg depending on the purity and production method [43], while the cost of carbon materials practically did not change. Therefore, for the most part of tests titanium diborid TiB2 combined with carbon [44, 45] or with colloidal solution of aluminium oxide (Tinor and Thicknor [46, 47]) was used as wetting agent. The mixture of TiB2, carbon material and other components was applied as paste with a thick centimeter layer onto the carbon bottom, as it was done in Martin Marietta Aluminum and Comalco, or with a thin millimeter layer of colloidal material – in Moltech. However, in both cases the coatings cracked and degraded. The thick paste layer dissolved forming Al/TiB2 suspension layer on the bottom surface [48]; the thin colloidal layer cracked and scaled further rising to the surface of the melts.
Without denying the prospects of drained cathode development, J.Keniry expresses his critical considerations concerning their feasibility [24]: “Drained cathode exposes the carbon component of the coating to the aggressive impact of the electrolytic bath; which results in its destruction. The degree of wear has to be rather uniform throughout the pot, and any local coating damage caused by particularities of the design, startup or operation methods can have a negative effect on the life circle of the whole pot. Though the pots with drained cathodes proved their feasibility, their industrial application would raise doubt, until the economic profit would be increased to compensate the operational risk”. J.Keniry, employee of private Australian company Alumination Consulting Pty Ltd, was well informed about results of drained cathode testing in Comalco. The key argument in his critical attitude to wettable coating is non-uniform wear degree of the composite coating surface. This disadvantage is difficult to eliminate as it is practically impossible to create a composite layer having the uniform adhesion to the matrix, the density, porosity, electric conductivity, strength, and other operational properties within the whole cathode surface. This is impossible to do both at the stage of erection and layer compaction and during its baking and pot startup. Moreover, the design of the pot with drained cathode is not ecological; it is oriented to the possibility of reducing the energy consumption and increasing the capacity. To provide the energy balance and insufficient heat generation within reduced anode-cathode space the pot design has to be based on the higher current density. This will further exacerbate the negative consequences.
It is recognized that no one of scientific research centers of aluminium producers solved completely and finally these problems. This explains the absence of commercial pots with drained cathode in spite of more than 70-year attempts to develop them. Therefore, most likely the engineering of the pot with drained cathode is unpromising (of little promise) direction due to following reasons:
- There are no any technologies for the creation of coatings wettable with aluminium and having uniform operational properties within their whole areas and volumes. Moreover, there is no any technical and technological possibility to synchronize the movement of cathode block with processes of surface layer shrinkage and expansion.
- There are no any cost-efficient technologies for the creation of massive compact products wettable with aluminium (cathode blocks) with uniform operational properties within their whole areas and volumes.
- The thin layer of aluminium on the cathode surface does not allow to uniformly distributing the current density within the large bottom area, which creates conditions for the uneven distribution of current and potential, for the cathode passivation and for the instability of the process.
- The existing technology of electrolytic reduction with prebake anodes came close to supposed energy consumption of the pots with drained cathode.
- Objectively, there are no prospects for the changes (increase) of specific capacity compared with existing technology.
Pots with vertical electrodes
The history of electrolytic aluminum production began with this direction. In 1854 R.Bunsen and A.Deville first, then such famous scientists of 19th century as F.Lontin, C.Bradley and finally P.Heroult and C.Hall started laboratory experiments in the cells with vertical electrodes [49, 50]. Moreover, first pilot pots of Pittsburgh Reduction Co followed this operation procedure in the beginning, but then they spontaneously switched over to the electrolytic reduction process using horizontal anode and cathode.
Since then attempts to develop the electrolysis of alumina-cryolite melts using solid electrodes continued [51, 52] and are currently ongoing [53, 54]. This persistence, on the one hand, is explained by the desire to minimize the electric energy consumption and by the approach to theoretically possible 6.3 and 9.2 kWh/kg Al when using carbon and inert electrodes accordingly. Such possibility appears if use vertical electrodes with anode-cathode distance of ~ 1.5-2 cm. On the other hand, this layout of the electrodes allows the multi-fold growing of specific capacity in the limited area of the pot.
Specific capacity. The standard capacity depends on the power of aluminium pots, i.e. amperage and on the amount of metal losses caused by low-productive processes and current leakage. In order to increase the capacity, the pot is designed for high amperage, the design provides for the application of structural components and technology allowing the maximum increase of current efficiency. Thus, the single capacity of any pot or enterprise in the whole, expressed in Al kilograms per day or in Al tons per year, can be increased by aluminium companies that accumulated high scientific and engineering potential and gained big experience in operating several generations of the pots.
It is not the case of specific capacity P, which is expressed by mass production of aluminium in 24 h per square meter of occupied area or area of anode/cathode block in the horizontal plane, – kg Al/m2·day. The specific capacity does not practically vary with increase of the pot power as with the increase of amperage the dimensions of the pot increase proportionally in terms of to accommodate electrodes and busbar that provide the design current density and current efficiency. Therefore, the specific capacity is a suitable parameter for the characterization of applied technology and for its comparison with new technologies of aluminium production by electrolytic method or with such technologies being under design.
If associate the standard capacity of any pots with area of anode block in horizontal plane, i.e. with area occupied by production premises (potroom), the specific capacity would have following parameters:
- for pots with horizontal electrodes – ~ 60 kg Al/m2·day;
- for pots with vertical electrodes ~ 450 kg Al/m2·day.
The calculation of the capacity is done for vertical electrodes embedded into the electrolytic bath on 1 m.
This difference in specific capacity (almost 8-fold) is exactly what determines sustained efforts to develop pots with solid vertical electrodes. The unique feature of vertical position of anodes and cathodes consists in multiple reduction of capital expenses on the construction of new smelters. This implies the reduction in expenses not only on building structures, but on the aluminium busbar as well, as there are no any strict requirements to the provision of MHD-stability of the melts in the pot.
However, there are serious constraining factors, limiting the development of solid vertical electrodes; these are absence of commercial wettable cathodes and uneven current distribution on the polycrystalline surface of electrodes.
Cathodes wettable with aluminium. The direction of creating wettable cathode surface as pastes and adhesion coatings is not developing now as experiments proved the rather quick destruction of continuous layer of any thickness on the surface of the block. The point is not just the absence of practical technologies for the creation of coatings (being created on the cathode surface before it is put into operation) with uniform operational properties within the whole area and volume of the block. Uncontrolled movement of cathode block could not be completely synchronized with processes of surface layer shrinkage and expansion. Besides, the cost of mechanically mixed carbon-based compositions with TiB2 powder for coatings and, particularly for cathode blocks is unacceptably high per one pot. Therefore, the direction to synthesize composite cathode products of any configurations and dimensions just during the process of electrolytic aluminium production looks attractive [55, 56]. It is clear that in quoted patents there is no any information about know-how technology.
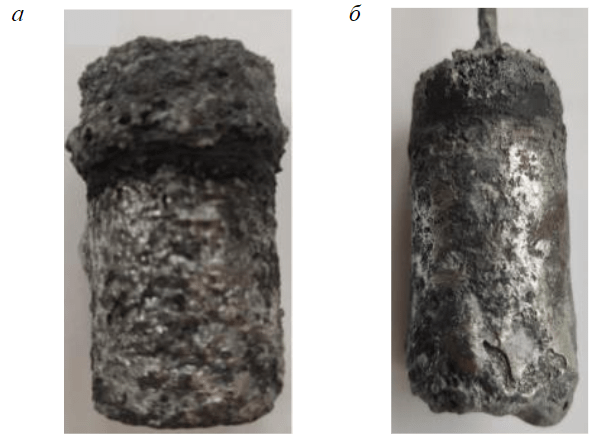
Fig.3. Specimens of composite after electrolysis: а – С-TiC; b – С-TiB2
The Scientific Center “Mineral and anthropogenic resource processing problems” of Empress Catherine II Saint Petersburg Mining University examined the possibility to synthesize composite cathode material carbon – titanium diboride/carbide (C-TiC/TiB2) during the electrolytic process in laboratory conditions. Petroleum coke, titanium and boron oxides and carbon-bearing binding agent were used as initial components for the preparation of electrodes. After pressing and baking at the temperature of 1050 °С the electrodes were installed into the graphite electrolytic cell, containing molten bath of NaF/AlF3 ≈ 2.5 at the temperature of 960 ± 5 °С. Composite electrodes with titanium and boron oxides were subject to the cathode polarization during 24 h.
After taking electrodes out of the cell and cleaning them against bath the layer of aluminium was discovered on the surface; which evidenced the wettability of cathodes with metal (Fig.3). X-ray phase analysis shown that the composition of electrodes contains titanium carbide TiC (Fig.4, a), only titanium oxide was dosed at the preparation. During the creation of initial C-TiO2/B2O3 composite the X-ray phase analysis of final product after electrolysis shown the presence of TiC and titanium borate TiBO3 (Fig.4, b), product of titanium diboride oxidation at the moment of electrode removal from the electrolytic cell. Hereby, the possibility of creating cathode composite material with wetting properties just during the electrolytic process was confirmed. Considering roughly the same range of prices on carbon materials, titanium and boron oxides, the production of composites of any dimensions shall change slightly.
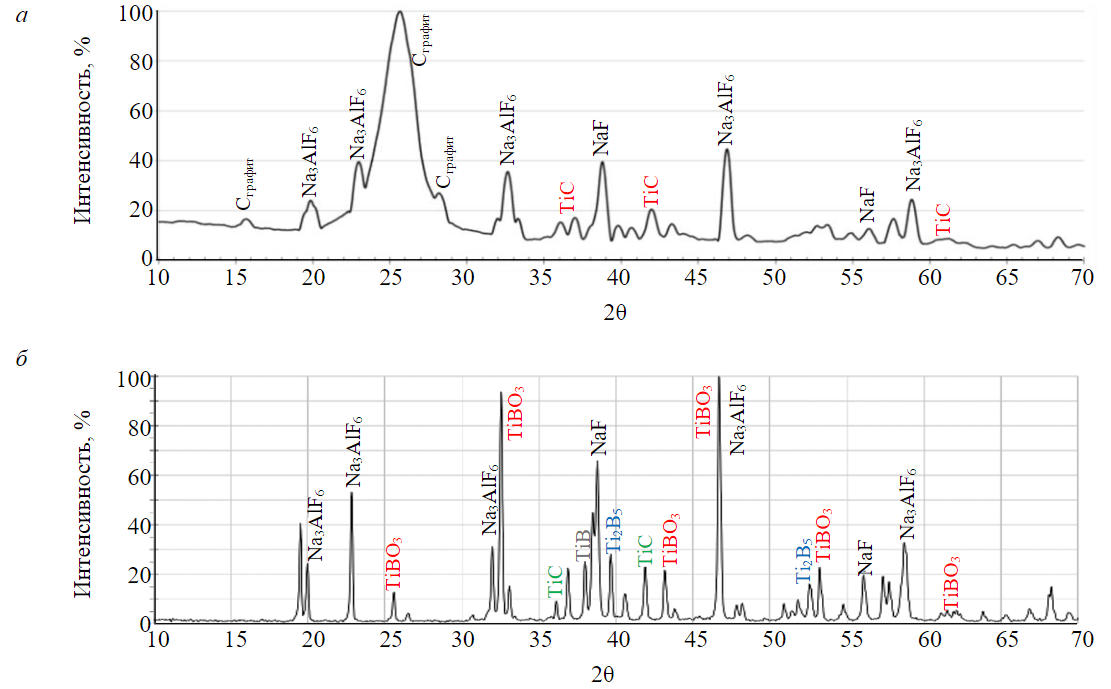
Fig.4. Results of X-ray phase analysis of С-TiC (а) and С-TiB2 (b) electrodes
Uneven current distribution. This problem is not obvious at the visual observation over the electrolytic process when using solid electrodes, but it is expressed by voltage instability in the system, higher consumption of anodes and passivation of cathode by bath components. It is precisely these consequences, but not the causes of the instability of the process, that researchers have tried and are trying to cope with [54, 57]. The destabilization of electrolysis in laboratory conditions occurs when the current density becomes higher than 0.5 A/cm2 [58-60]. Recommendations, proposed for the decrease of electrolytic reduction temperature, corrections in electrolytic bath and electrode compositions do not solve the problem and do not allow starting the development on the commercial basis.
Based on experimental data [61, 62] and numerical investigations [63, 64] it is proposed to consider the physical and chemical heterogeneity of surface structure of polycrystalline electrodes as the cause of these problems and restrictions. During the operation the chemical heterogeneity transforms gradually into physical one. That is right both for coatings and for compact electrode products of any composition – based on carbon, borides/carbides of refractory metals or their compounds.
Current lines at the micro-level would be concentrated on asperities of the rough surface, pores, cracks, scratches. The same effects take place at the macro-level for peripheral areas of electrodes – ribs or sharp edges. At the areas where the current density and potential are higher, the speed of electrode processes increases with the development of concentration polarization and uncontrollable formation of critical electrode potentials for simple and complex ions present. This would result to greater or lesser extent in the release of gas fluorocarbons on the carbon anode and the release of fluorine on the inert anode with corresponding negative consequences, i.e. increase in electrode consumption.
On the wettable cathode the charge of electrically negative impurities and the decomposition of electrolytic bath components take place with subsequent passivation of the surface and progressing destabilization of electrolytic process (these negative consequences are typical for the drained cathode as well). By this means we can distinguish the micro-heterogeneity, related to the rough surface in the entire area, and the macro-heterogeneity of current distribution on the peripheral areas of electrodes (edge effect). This approach determines the development of different technologies for flattering current distribution throughout electrodes.
Elliptical shape of electrodes with adequate increase of anode-cathode distance and electrolytic bath resistance from the center to the periphery allows compensating the edge effect and reducing significantly the macro-heterogeneous current distribution. As opposed to the application of rectangular electrodes, during the whole experiment the proceeding of electrolytic process was stable in the electrolytic cell with metallic anode and cathode of elliptical shape; the passivation of cathode was not observed, the rate of anode corrosion was approx. three times reduced [62].
However, the special shape is not sufficient for the stability of the process using solid electrodes, polycrystalline and cast, one-phase and multi-phase, which a priori have physical and chemical heterogeneities in their volume and surface structures. Therefore, one of feasible methods of surface homogenization directly within the electrolytic process was proposed and realized – electrochemical micro-boriding of cathodes which composition included refractory metals and their oxides [61]. The method is based on the significant, almost twice, difference between standard potentials of the charges of aluminium (Е0р = –1.18 V) and boron (Е0р = –0.63 V). When they are jointly present in the melt, the conditions for the charges in the cavities are favorable for more electrically positive ions. If after the reduction in the cavity boron meets, for example, titanium or its oxide on the surface, the synthesis of titanium diboride shall smooth any heterogeneous surface. This method could be applied to any reactive or inert cathodes, which heterogeneous surface is smoothed by chemical interaction of boron with impurities present, and thereby, the physical state of the surface homogenates.
Thereby it is possible to deduce a simple formula of the electrolytic process procedure in the pot with vertical solid electrodes: complex application of elliptical electrodes and electro-chemical micro-boriding of composite cathodes. This formula in general terms can be used for the prospective development of aluminium industry according to the following roadmap of scaling up technologies:
- technology of electrolytic reduction as per flowchart of vertical elliptical electrodes;
- technology of synthesis of composite cathodes wettable with aluminium directly during the electrolytic process;
- technology of electrochemical micro-boriding of cathode surface.
Combining these technologies into one shall allow taking unique advantages of electrolytic reduction technology using vertical solid electrodes (see Table).
Comparative characteristics of electrolytic reduction technologies
Parameters |
Position of electrodes |
|
Horizontal |
Vertical |
|
Electric energy consumption, kWh/kg Al |
~13.5 |
~11.0 |
СО2 emissions* kg СО2-equ/kg Al |
~ 1.4 |
→ 1.0** → 0*** |
Specific capacity, kg Al/m2∙day |
~ 60 |
~ 450 |
* Direct emissions (Scope 1).
** Composite electrodes.
*** Inert electrodes.
Conclusion
Following conclusions were made based on above-mentioned overview:
- In Russia the process of ecological reconstruction of obsolete production facilities was organized on the governmental level. It supposes the self-financing of the tightening state environmental regulation. At the same time, private companies satisfy their challenging technological and environmental ambitions.
- For existing technology of electrolytic reduction using horizontal electrodes and up-to-date automated process control system, busbar and lining materials, there is a real possibility of energy consumption in amount of`~12000 kWh per 1 t of aluminium produced. The further decrease of specific consumption of electric energy to 11250-11500 kWh/t Al is possible with the use of cathode materials wetted with molten aluminium. These values of energy efficiency are limiting values for existing technology.
- The development of the technology of inert (oxygen evolving) anode requires the thorough examination by competent entities of industrial safety. Under certain climate and meteorological conditions at the area of intensive oxygen emission source the situation with increased fire hazard can emerge.
- The design of the pot with drained cathode is of little promise.
- The most promising technology of alumina-cryolite melt electrolysis is the technology of the pots with vertical electrodes. The use of composite anodes and cathodes with reduced carbon activity can decrease considerably emissions of greenhouse gases. The specific capacity of such pots can be 7-8-fold higher; which means the multiple reduction of capital expenses on the construction of new smelters in comparison with the existing technology using horizontal electrodes.
References
- Litvinenko V.S., Petrov E.I., Vasilevskaya D.V. et al. Assessment of the role of the state in the management of mineral resources. Journal of Mining Institute. 2023. Vol. 259, p. 95-111. DOI: 10.31897/PMI.2022.100
- Zhukovskiy Yu.L., Batueva D.E., Buldysko A.D. et al. Fossil Energy in the Framework of Sustainable Development: Analysis of Prospects and Development of Forecast Scenarios. Energies. 2021. Vol. 14. Iss. 17. N 5268. DOI: 10.3390/en14175268
- Pyagay I.N., Lebedev A.B. Effects of alumina on the stability of ferrite-calcium sinter with dicalcium silicate. CIS Iron and Steel Review. 2023. Vol. 25, p. 10-16. DOI: 10.17580/cisisr.2023.01.02
- Kosolapova S.M., Smal M.S., Rudko V.A., Pyagay I.N. A New Approach for Synthesizing Fatty Acid Esters from Linoleic-Type Vegetable Oil. Processes. 2023. Vol. 11. Iss. 5. N 1534. DOI: 10.3390/pr11051534
- Zubkova O.S., Alexeev A.I., Sizyakov V.M., Polyanskiy A.S. Research of suxfuric acid salts influence on sedimentation process of a clay suspension. ChemChemTech. 2022. Vol. 65. N 1, p. 44-49. DOI: 10.6060/ivkkt.20226501.6447
- Kudinova A.A., Poltoratckaya M.E., Gabdulkhakov R.R. et al. Parameters influence establishment of the petroleum coke genesis on the structure and properties of a highly porous carbon material obtained by activation of KOH. Journal of Porous Materials. 2022. Vol. 29. Iss. 5, p. 1599-1616. DOI: 10.1007/s10934-022-01287-1
- Litvinenko V.S., Dvoynikov M.V., Trushko V.L. Elaboration of a conceptual solution for the development of the Arctic shelf from seasonally flooded coastal areas. International Journal of Mining Science and Technology. 2022. Vol. 32. Iss. 1, p. 113-119. DOI: 10.1016/j.ijmst.2021.09.010
- Khalifa A.A.E.I.A., Bazhin V.Y., Kuskova Y.V. et al. Study the Recycling of Red Mud in Iron Ore Sintering Process. Journal of Ecological Engineering. 2021. Vol. 22. Iss. 6, p. 191-201. DOI: 10.12911/22998993/137966
- Sharikov F.Y., Rudko V.A., Smyshlyaeva K.I. Oxidation thermolysis kinetics of asphaltenes with various chemical prehistory. Thermochimica Acta. 2023. Vol. 726. N 179550. DOI: 10.1016/j.tca.2023.179550
- Zubkova O.S., Pyagay I.N., Pankratieva K.A., Toropchina M.A. Development of composition and study of sorbent properties based on saponite. Journal of Mining Institute. 2023. Vol. 259, p. 21-29. DOI: 10.31897/PMI.2023.1
- Volosatova A.A., Pyatnitsa A.A., Guseva T.V., Almgren R. Best Available Techniques as a Universal Instrument for Improving State Policies. Economics of sustainable development. 2021. N 4 (48), p. 17-23 (in Russian). DOI: 10.37124/20799136_2021_4_48_17
- Haupin W., Frank W. Current and Energy Efficiency of Hall-Heroult Cells. Light Metal Age. 2002. N 5/6, p. 6-13.
- Choate W.T., Green J.A.S. U.S. Aluminum Production Energy Requirements: Historical Perspective, Theoretical Limits and New Opportunities. ACEEE Summer Study on Energy Efficiency in Industry, 29 July – 1 August 2003, New York, USA. Proceedings from the ACEEE Summer Studies on Energy Efficiency in Industry, 2003, p. 12-24.
- Bardel A., Droste C., Ovstetun F. et al. HAL4e – Hydro’s New Generation Cell Technology. TMS Annual Meeting and Exhibition, 15-19 November 2009, San Francisco, CA, USA. TMS Light Metals 2009: Proceedings of the technical sessions presented by the TMS Aluminum Committee at the TMS, 2009, p. 371-376.
- Lange H.P., Holt N.J., Linga H., Solli L.N. Innovative Solutions to Sustainability in Hydro. TMS Annual Meeting and Exhibition, 9-13 March 2008, New Orleans, LA, USA. TMS Light Metals 2008: Proceedings of the technical sessions presented by the TMS Aluminum Committee at the TMS, 2008, p. 211-216.
- Thonstad J., Rolseth S., Rodseth J. et al. The content of sodium in aluminium in laboratory and industrial cells the Content of Sodium in Aluminum in Laboratory and in Industrial Cells. Light Metals: Proceedings of Sessions, TMS Annual Meeting, Warrendale, Pennsylvania, 2000, p. 441-447.
- Makushin D.V. Increase of aluminium reduction efficiency based on the optimization of micro-impurities distribution within the “bath-cathode aluminium” system: Avtoreferat dis. ... kand. tekhn. nauk. St. Petersburg: Sankt-Peterburgskii gornyi institut, 2007, p. 22 (in Russian).
- Meirbekova R., Haarberg G.M., Thonstad J. et al. Effect of Operational Parameters on the Behavior of Phosphorus and Sulfur in Aluminum Reduction. TMS Light Metals. 2015, p. 559-564. DOI: 10.1007/978-3-319-48248-4_93
- Hall C.M. Patent N 400766 US. Process of Reducing Aluminum by Electrolysis. Publ. 02.04.1889.
- Belyaev A.I., Studentsov Ya.E. Electrolysis of alumina using fire-proof (metal) anodes). Legkie metally. 1936. N 3, p. 15-24 (in Russian).
- Belyaev A.I., Studentsov Ya.E. Electrolysis of alumina using fire-proof oxide containing anodes. Legkie metally. 1937. N 3, p. 17-21 (in Russian).
- Belyaev A.I. Electrolysis of alumina using fire-proof ferrite containing anodes. Legkie metally. 1938. N 1, p. 7-20 (in Russian).
- Brown G.D. TiB2 Coated Aluminium Reduction Cells: Status and Future Direction of Coated Cells in Comalco. Proceedings of the 6th Australasian Aluminium Smelter Technology Conference and Workshop, 1998, Queenstown, New Zealand. Kensington, NSW: University of New South Wales, 1998, p. 499-508.
- Keniry J. The economics of inert anodes and wettable cathodes for aluminum reduction cells. JOM. 2001. N 53, p. 43-47. DOI: 10.1007/s11837-001-0209-2
- Kvande H., Haupin W. Inert anodes for Al smelters: Energy balances and environmental impact. The Journal of the Minerals, Metals & Materials Society. 2001. Vol. 53. Iss. 5, p. 29-33. DOI: 10.1007/s11837-001-0205-6
- de Nora V. VERONICA and TINOR 2000: New Technologies for Aluminum Production. The Electrochemical Society Interface. 2002. Vol. 11. Iss. 4, p. 20-24. DOI: 10.1149/2.F02024IF
- Welch B. Inert anodes – The Status of the Materials Science, the Opportunities They Present and the Challenges That Need Resolving before Commercial Implementation. Light Metals 2009: Proceedings of the Technical Sessions Presented by the TMS Aluminum Committee at the TMS 2009 Annual Meeting and Exhibition, 15-19 February 2009, San Francisco, California, USA. 2009. p. 971-978.
- Pawlek R. Inert Anodes: An Update. TMS Light Metals. 2014, p. 1309-1313. DOI: 10.1007/978-3-319-48144-9_219
- Padamata S.K., Yasinskiy A.S., Polyakov P.V. Progress of Inert Anodes in Aluminium Industry: Review. Journal of Siberian Federal University. Chemistry. 2018. Vol. 11. N 1, p. 18-30. DOI: 10.17516/1998-2836-0055
- Gupta A.K., Basu B. Sustainable Primary Aluminium Production: Technology Status and Future Opportunities. Transactions of the Indian Institute of Metals. 2019. Vol. 72. Iss. 8, p. 2135-2150. DOI: 10.1007/s12666-019-01699-9
- Marshall V. Major chemical hazards. Moscow: Mir Publishers, 1989, p. 671.
- Maltsev V.M., Maltsev V.I., Kashporov L.Ya. Main combustion characteristics. Мoscow: Khimiya, 1977, p. 320 (in Russian).
- Ransley C.E. Patent N 802905 GB. Improvements in or relating to electrolytic cells for the production of aluminium. Publ. 15.10.1958.
- Lewis R.A. Patent N 2915442 US. Production of aluminum. Publ. 01.12.1959.
- Lewis R.A., Hildebrandt R.D. Patent N 3400061 US. Electrolytic cell for production of aluminum and method of making the same. Publ. 03.09.1968.
- McIntyre J., Mitchell D.N., Simpson S. Performance Testing of Cathodic Materials and Designs in a 16 KA Cell and a Test Bed. Light Metals; The Minerals, Metals & Materials Society: Proceedings of the Technical Sessions Sponsored by the TMS Light Metal Committee at the 116th Annual Meeting, 24-26 February 1987, Denver, Colorado, 1987, p. 335-344.
- Tucker K.W. et al. Stable TiB2 – Graphite Cathode for Aluminium Production. Light Metals; The Minerals, Metals & Materials Society: Proceedings of the Technical Sessions Sponsored by the TMS Light Metal Committee at the 116th Annual Meeting, 24-26 February 1987, Denver, Colorado, 1987, p. 345-349.
- Joo L.A., Tucker K.W., McCown F.E. Patent N 4376029 US. Titanium diboride-graphite composits. Publ. 08.03.1983.
- Øye H.A., de Nora V., Duruz J.-J., Johnston G. Properties of a Colloidal Alumina-Bonded TiB2 Coating on Cathode Carbon Materials. Essential Readings in Light Metals, Electrode Technology for Aluminum Production. 2016. Vol. 4, p. 1171-1178. DOI: 10.1007/978-3-319-48200-2_155
- Hudson T.J. Cathode Technology for Aluminum Electrolysis Cells. Light Metals; The Minerals, Metals & Materials Society: Proceedings of the Technical Sessions Sponsored by the TMS Light Metal Committee at the 116th Annual Meeting, 24-26 February 1987, Denver, Colorado, 1987, p. 321-325.
- Gessing A.J., Wheeler D.J. Screening and Avaluation Methods of Cathode Materials for Use in Aluminum Reduction Cells in Presence of Molten Aluminum and Cryolite up to 1000 °C. Light Metals; The Minerals, Metals & Materials Society: Proceedings of the Technical Sessions Sponsored by the TMS Light Metal Committee at the 16th Annual Meeting, 24-26 February 1987, Denver, Colorado, 1987, p. 327-334.
- Alcorn T.R. Pilot Reduction Cell Operation Using TiB2-G Cathodes. Light Metals; The Minerals, Metals & Materials Society: Proceedings of the Technical Sessions Presented by the TMS Light Metals Committee at the 119th TMS Annual Meeting, 18-22 February 1990, Anaheim, California, 1990, p. 413-418.
- Efimova K.A., Galevsky G.V., Rudneva V.V. The current status of titanium diboride production: Assessment and determination of the dominant trends and prospects. St. Petersburg Polytechnical University Journal: Physics and Mathematics. 2017. Vol. 23. Iss. 2, p. 144-158. DOI: 10.18721/JEST.230213
- Boxall L.G., Cooke A.V., Hayden H.W. Use of TiB2 Cathode Material Application and Benefits in Conventional VSS Cells. Essential Readings in Light Metals, Electrode Technology for Aluminum Production. 2016, p. 1145-1152. DOI: 10.1007/978-3-319-48200-2_152
- Cooke A.V., Buchta W.M. Use of TiB2 Cathode Material: Demonstrated Energy Conservation in VSS Cells. Essential Readings in Light Metals, Electrode Technology for Aluminum Production. 2016, p. 1153-1163. DOI: 10.1007/978-3-319-48200-2_153
- Sekhar J.A., Vittorio de Nora. Patent N 5364513 US. Electrochemical cell component or other material having oxidation preventive coating. Publ. 15.11.1994.
- Sekhar J.A., Duruz J.-J., Liu J.J. Patent N 6783655 US. Slurry and method for producing refractory boride bodies and coatings for use in aluminium electrowinning cells. Publ. 31.08.2004.
- Watson K.D., Juric D.D., Shaw R.W., Houston G.J. Patent N 5658447 US. Electrolysis cell and method for metal production. Publ. 19.08.1997.
- Richards J.W. Aluminium: Its History, Occurrence, Properties, Metallurgy and Applications, Including Its Alloys. London: Sampston Low, Marston, Searle & Rivington, 1887, p. 346.
- Minet A. The Production of Aluminium and Its Industrial Uses. London: Chapman & Hall, Limited, 1905, p. 266.
- Griswold Jr. T. Patent N 1070454 US. Electrolytic cell. Publ. 19.08.1913.
- Johnson A.F. Patent N 2480474 US. Method of producing aluminum. Publ. 30.08.1949.
- Zaikov Y., Khramov A., Kovrov V. et al. Electrolysis of aluminum in the low melting electrolytes based on potassium cryolite. TMS Light Metals. 2008. N 1, p. 505-508.
- Shengzhong Bao, Dengpeng Chai, Zhirong Shi et al. Effects of Current Density on Current Efficiency in Low Temperature Electrolysis with Vertical Electrode Structure. 147th Minerals, Metals & Materials Society Annual Meeting and Exhibition, 11-15 March 2018, Phoniex, AZ, USA. TMS Light Metals, 2018, p. 611-619. DOI: 10.1007/978-3-319-72284-9_79
- Mirtchi A.A., Bergeron D. Patent N 2232211 RU. Carbon composite materials capable of wetting, erosion\oxidation resistant. Publ. 10.07.2004 (in Russian).
- Polyakov A.A., Gorlanov E.S., Pyagay I.N. et al. Patent N 2793027 RU. Method for producing composite carbon-containing material. Publ. 28.03.2023. Bul. N 10 (in Russian).
- Tkacheva O.Yu. Low-temperature electrolysis of alumina in the melts of fluorides: Avtoref. dis. ... d-ra khim. nauk. Ekaterinburg: Uchebno-metodicheskii tsentr Uralskogo gosudarstvennogo tekhnicheskogo universiteta, 2013, p. 36 (in Russian).
- Suzdaltsev A.V., Nikolaev A.Y., Zaikov Y.P. Towards the Stability of Low-Temperature Aluminum Electrolysis. Journal of the Electrochemical Society. 2021. Vol. 168. N 4. N 046521. DOI: 10.1149/1945-7111/abf87f
- Nikolaev A.Y., Yasinskiy A.S., Suzdaltsev A.V. et al. Aluminum electrolysis in the KF-AlF3-Al2O3 melts and suspensions. Melts. 2017. N 3, p. 205-213 (in Russian).
- Nikolaev A.Y., Suzdaltsev A.V., Zaikov Y.P. Cathode Process in the KF-AlF3-Al2O3 Melts. Journal of the Electrochemical Society. 2019. Vol. 166. N 15, p. D784-D791. DOI: 10.1149/2.0521915jes
- Gorlanov E.S. Alloying of aluminium pot cathodes by method of low-temperature titanium diboride synthesis: Avtoref. dis. ... d-ra tekhn. nauk. St. Petersburg: Sankt-Peterburgskii gornyi universitet, 2020, p. 40 (in Russian).
- Polyakov A.A. Distribution of the current and potential within the surface of vertical electrodes during the electrolytic production of aluminium: Avtoref. dis. … kand. tekhn. nauk. St. Petersburg: Sankt-Peterburgskii gornyi universitet, 2022, p. 20 (in Russian).
- Gorlanov E.S., Polyakov А.А. On the question of using solid electrodes in the electrolysis of cryolite-alumina melts. Part 3. Electric field distribution on the electrodes. iPolytech Journal. 2021. Vol. 25. N 2, p. 235-251. DOI: 10.21285/1814-3520-2021-2-235-251
- Polyakov A.A., Gorlanov E.S., Mushihin E.A. Analytical Modeling of Current and Potential Distribution over Carbon and Low-Consumable Anodes during Aluminum Reduction Process. Journal of the Electrochemical Society. 2022. Vol. 169. N 5. N 053502. DOI: 10.1149/1945-7111/ac6a16