Study of the pore structure in granite and gabbrodolerite crushed stone grains of various sizes
- 1 — Ph.D. Head of Department Petrozavodsk State University ▪ Orcid
- 2 — Ph.D. Senior Lecturer Empress Catherine ΙΙ Saint Petersburg Mining University ▪ Orcid
Abstract
The results of a study on the pore structure of crushed stone grains of various sizes, obtained through staged disintegration of gabbrodolerite and microcline granite – rocks differing in texture, structure, and mineral composition – are presented. Research conducted using X-ray computed microtomography revealed that disintegration leads to changes in the pore structure of the rocks. The increase in overall porosity and pore concentration in the crushed stone grains is associated with the formation of newly developed pores of various sizes and sphericity. A clear relationship between the porosity of the crushed stone grains and their size is absent, which is due to the textural and structural characteristics as well as the mineral composition of the original rocks. The scale factor is evident only in the case of gabbrodolerite, which is characterized by a fine-grained structure, massive texture, and stable mineral composition. Fine gabbrodolerite grains exhibit lower pore concentration compared to larger grains, which aligns with the statistical theory of rock strength, according to which the probability of defects (pores and microcracks) decreases as the sample size diminishes – the smaller the grain size, the higher its strength. In contrast, for porphyritic granites with an uneven grain size, the trend is reversed – smaller grains are more porous. A study of the porosity of individual rock-forming minerals in granite showed that pores are unevenly distributed in the granite crushed stone grains. The highest concentration of pores is typical for microcline. The presence of brittle and porous microcline inclusions in the granite crushed stone grains leads to the formation of new pores and microcracks, whose number increases with the repeated application of load during staged disintegration.
Introduction
The physical and mechanical properties of rock are determined by its mineral composition, texture, and the characteristics of its pore space – specifically, the size, shape, and spatial orientation of the pores. Virtually all studies on the deformation and destruction of rocks provide data indicating that when a load is applied, a deformation field is created within the rock volume, leading to changes in the structure of the pore space – its size, shape, and the number of defects, such as microcracks and pores [1-3]. In relation to the task of disintegration of construction rocks, this information is fundamental. This is because, unlike ore materials, where effective mineral separation and weakening are important during crushing and grinding for subsequent enrichment, in the disintegration of construction rocks, the goal is to preserve the strength of the crushed stone.
When discussing the strength of crushed stone, it is important to highlight the scale factor – the size of its grains. According to the statistical theory of strength, the larger the volume of a rock sample, the more defects it contains, and therefore, the lower its strength. At the same time, the statistical nature of strength and the number of defects are not the only reasons for the manifestation of the scale factor. In the work by A.F.Ioffe and co-authors [4], it was established that the scale effect is observed during the deformation of materials prone to brittle fracture and is less pronounced in ductile materials. Modern studies on the influence of sample size on the strength properties of rocks have shown that the relationship between strength and sample size is ambiguous. It is necessary to take into account the heterogeneity of the rock’s mineral composition, the characteristics of the pore structure, and the sample's history [5-7]. The latter is of particular importance when interpreting the strength of crushed stone, which has been subjected to blasting operations and staged crushing.
Numerous results from testing commercially produced crushed stone at crushing and screening plants in Karelia indicate the inconsistency of strength across different grain size fractions. In some cases, smaller fractions exhibit greater strength, while in others, the opposite trend is observed. Therefore, in this study, we set a specific task: to examine the influence of the scale factor – the size of the crushed stone grains – on its strength. To a large extent, variations in the strength of different size fractions of crushed stone produced at the same facility can be explained by the varying degree of grain flakiness – when there is a high content of flat and elongated grains, the strength of the crushed stone decreases [8, 9]. However, the increase in flaky grain content is not the only reason for reduced strength. Research [10, 11] has shown that newly formed (secondary) microcracks and pores appear in crushed stone grains, which a priori reduce their strength characteristics. At the same time, the volume of voids does not significantly depend on the grain size of the crushed stone [10]. In study [11], a decrease in crushed stone strength as the grain size decreases was noted, which the authors attributed to an increase in microdamage due to additional loads on smaller fractions during staged crushing. These conclusions were based on microscopic analysis of thin sections [10], and in [11], the strength reduction was inferred through water absorption measurements, which indirectly relate to the material’s porosity and strength. An informative characteristic linking rock strength to its structural defects is porosity, which encompasses all voids within the rock, including pores, pore channels, and microcracks [12-14]. The physical or overall porosity of rock, calculated from known mineral and bulk density values, provides only indirect insights into the transformation of the microstructure during rock destruction. To obtain objective data, it is essential to consider the specific characteristics of the pore structure – such as pore size, shape, and spatial orientation [15-17].
The aim of this study is to investigate the pore structure of crushed stone grains of various sizes, obtained through staged disintegration of rocks differing in texture, structure, and mineral composition.
Methods
The primary methods used for studying and describing the structures and textures, as well as various morphometric characteristics of rocks, are mineralogical-petrographic analysis techniques. Descriptions of thin sections provide only qualitative information about rocks and are limited in terms of obtaining quantitative and volumetric structural-textural characteristics, which can affect the quality of research result interpretations. The advent of new non-destructive methods for studying materials allows for an expanded understanding of the structural-textural characteristics of rocks and complements traditional optical-petrographic studies with quantitative data on structural defects.
To obtain a reliable picture of the three-dimensional distribution of defects, their sizes, shapes, and spatial orientations, methods such as X-ray computed microtomography (X-ray micro-CT), neutron computed tomography, contact laser ultrasonic structuroscopy, transmission electron microscopy, and acoustic spectroscopy are used [18-20]. The research method should provide data characterizing the pore structure of rocks, including total porosity, pore concentration, sizes, and geometrical shapes of pores and microcracks, as well as enable the visualization of the microstructure of the samples to identify potential heterogeneity in pore distribution [21-23]. Furthermore, the method’s sensitivity must be commensurate with the sizes of the structural objects (pores, mineral grains). Among these methods, X-ray computed microtomography (X-ray micro-CT) is the most suitable [24-26].
X-ray computed microtomography is a non-destructive method for studying the internal structure of solid materials, based on the dependence of the linear attenuation coefficient of X-ray radiation on the chemical composition and density of the material. Computer processing of a set of shadow projections obtained by X-ray scanning of samples allows for the visualization of the internal three-dimensional structure of the sample and provides a detailed analysis of morphometric and density characteristics both on individual sections and throughout the entire volume of the studied sample. The promise of this method for solving practical tasks related to rock disintegration lies in its ability to obtain quantitative characteristics of the pore space structure [27-29].
The method is successfully applied to assess changes in the void structure during the disintegration of ores in crushing machines [30], and in the study of the deformation and destruction processes of rocks [31, 32]. Despite significant scientific advances, several questions related to changes in rock strength during disintegration remain unresolved. Almost all studies in this field have been conducted on samples of regular shape under static or dynamic loading conditions [33-35]. The products formed as a result of sample destruction are generally not examined by the authors.
For microtomographic research, samples of crushed stone grains from microcline granite of the Kirjavalahti deposit and gabbrodolerite of the Chevzhavara deposit (Republic of Karelia) were selected. The samples were extracted from crushed stone fractions of 5-20 mm and 20-40 mm, produced under industrial conditions at crushing and screening plants. The 20-40 mm fraction was obtained after the second stage of crushing, while the 5-20 mm fraction was obtained after the third stage. For comparative data on the pore structure of crushed stone grains and the original rock, hand specimens were selected, from which cubic samples with an edge length of 4.0 cm were prepared. The compressive strength limit was determined on similar cubic samples using a standard methodology. The average value of this indicator, calculated from five tested samples, was 121 MPa for granite and 192 MPa for gabbrodolerite.
The structure of the microcline granite samples (Fig.1, a) is uneven-grained, with a porphyritic texture. The main rock-forming minerals are microcline, plagioclase, and quartz. Their content percentages are as follows: microcline – 35-47 %, plagioclase – 25-35 %, and quartz – 20-26 %. Secondary minerals include biotite (1-5 %) and accessory minerals (apatite, titanite) up to 1 %. According to the petrographic description of thin sections, the grain sizes of microcline range from 1.0 to 5.0 mm, plagioclase – from 1.0 to 2.0 mm. Quartz is present as xenomorphic grains up to 1 mm in size, while biotite appears as small scattered flakes (0.1-0.3 mm) in association with titanite. Apatite forms individual rounded grains up to 0.1 mm in size.
The structure of the gabbrodolerite samples (Fig.1, b) is fine-grained, with a massive texture. The primary rock-forming minerals are plagioclase (45-50 %) and pyroxene (47-51 %). The content of quartz is 2-4 %, biotite up to 1 %, and ore minerals (titanite) up to 1 %. Pyroxene is present in the form of prismatic grains ranging in size from 0.1 to 0.8 mm, while plagioclase forms elongated crystals of 0.1-1.0 mm in size.
The main physical and mechanical properties of the crushed stone samples were determined using standard methods as outlined in GOST 8269.0-97 “Crushed stone and gravel from dense rocks for construction works. Methods of physical and mechanical testing” (Table 1). To eliminate the influence of grain shape on the strength (crushability) of the crushed stone, only isometric (cuboidal) grains were selected for testing.
Table 1
Physical and mechanical properties of the crushed stone
Crushing stage |
Fraction size, mm |
Crushability (strength) |
Bulk density, g/cm3 |
Porosity, %
|
|
|
Mass loss after testing, % |
Crushed stone grade by crushability |
|
||||
Crushed stone from granite |
||||||
II |
20-40 |
12.6 |
1,200 |
2.68 |
2.2 |
|
III |
5-20 |
16.2 |
1,000 |
2.60 |
2.8 |
|
Crushed stone from gabbrodolerite |
||||||
II |
20-40 |
5.4 |
1,400 |
2.96 |
0.68 |
|
III |
5-20 |
4.8 |
1,400 |
2.98 |
0.60 |
|
The microstructure of the crushed stone grains was studied using a SkyScan1173 microtomograph (Belgium) with resolutions ranging from 0.5 to 15 µm. The scanning mode was set to a current of 130 mA, a voltage of 61 kV, and X-ray power of 90 W. Scanning was performed with a copper filter 0.1 mm thick and with the averaging of three images. The pixel size at maximum magnification (default resolution) was 0.5 µm, allowing for the identification of pores sized 5 µm and larger. The sample stage rotated 360° with a step of 0.2°. The number of shadow images taken ranged from 2,000 to 2,100. Subsequent reconstruction was performed using the NRecon, CTAn, and CTVol software. To speed up image processing, binarization was carried out, enabling a more detailed examination of the internal void space of the studied samples [36-38]. During the research, pore space parameters were determined, including total porosity (the volume of pores within the sample volume) and pore concentration (the number of pores per unit volume of the sample) (Table 2).
Table 2
Morphometric parameters of initial samples and crushed stone grains from granite and gabbrodolerite based on microtomographic studies
Sample number |
Granite |
Gabbrodolerite |
||||
Sample volume, mm3 |
Porosity, % |
Pore concentration, mm–3 |
Grain volume, mm3 |
Porosity, % |
Pore concentration, mm–3 |
|
Initial rock samples |
||||||
1 |
64,312 |
0.66 |
0.22 |
64,462 |
0.37 |
0.20 |
2 |
64,163 |
0.58 |
0.21 |
64,753 |
0.38 |
0.20 |
3 |
63,954 |
0.54 |
0.19 |
63,556 |
0.38 |
0.21 |
4 |
64,065 |
0.71 |
0.20 |
64,003 |
0.37 |
0.20 |
5 |
64,052 |
0.75 |
0.21 |
63,652 |
0.35 |
0.20 |
Average |
64,109 |
0.65 |
0.21 |
64,085 |
0.37 |
0.20 |
Crushed stone grains 20-40 mm |
||||||
1 |
61,479 |
2.05 |
0.59 |
63,314 |
0.60 |
0.26 |
2 |
51,733 |
1.98 |
0.36 |
41,226 |
0.59 |
0.24 |
3 |
61,669 |
2.21 |
0.83 |
43,658 |
0.62 |
0.26 |
4 |
42,281 |
2.42 |
0.93 |
51,254 |
0.62 |
0.28 |
5 |
54,908 |
1.85 |
0.56 |
31,006 |
0.60 |
0.28 |
Average |
54,414 |
2.10 |
0.65 |
|
0.60 |
0.26 |
Crushed stone grains 5-20 mm |
||||||
1 |
3,453 |
3.30 |
2.31 |
3,168 |
0.50 |
0.27 |
2 |
4,379 |
2.45 |
1.12 |
3,212 |
0.57 |
0.21 |
3 |
3,848 |
2.31 |
1.95 |
4,203 |
0.52 |
0.24 |
4 |
3,953 |
3.20 |
2.08 |
4,185 |
0.55 |
0.26 |
5 |
4,162 |
2.40 |
2.08 |
3,247 |
0.53 |
0.24 |
Average |
3,959 |
2.73 |
1.74 |
– |
0.53 |
0.24 |
Note. Scanning resolution is 0.5 µm.
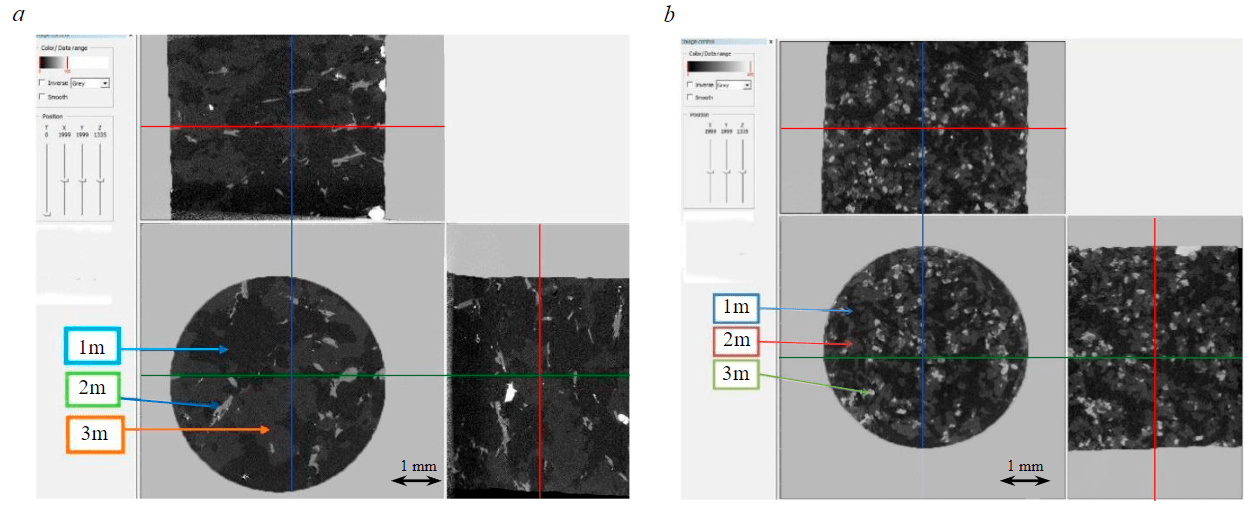
Fig.1. Microtomographic slices of granite (a) and gabbrodolerite (b) samples along three mutually perpendicular planes: a – 1m – microcline, 2m – plagioclase + quartz, 3m – biotite; b – 1m – plagioclase + quartz, 2m – pyroxene, 3m – titanite
Discussion
The analysis of the obtained data shows that the porosity of the original samples, which were not subjected to mechanical stress during blasting and disintegration in crushing machines, is lower than that of the crushed stone grains. This is consistent with conclusions drawn in studies [10, 11]. The increase in porosity of the crushed stone grains is accompanied by the appearance of newly formed defects (pores and microcracks), as evidenced by the growth in their concentration within the volume of the studied grains. This pattern is most pronounced in granite, where porosity increases on average by 3.2-4.2 times (from 0.64 to 2.1-2.73 %), and pore concentration increases by 3.1-8.3 times (from 0.21 to 0.65-1.74 mm–3). The effect is less noticeable in gabbrodolerite, where porosity increases on average by 1.5 times, and pore concentration increases by 1.25 times.
There is no clear dependence of porosity on grain size. In larger granite grains, taken from the 20-40 mm fraction, the average porosity is 2.1 %, while in smaller grains (from the 5-20 mm fraction), this figure is higher, at 2.73 %. In gabbrodolerite grains, the opposite trend is observed, with larger grains being more porous, although the difference in porosity values is less significant – 0.53 and 0.6 %, respectively (Table 2). The increase in porosity in smaller granite grains is associated with a higher pore concentration (an average of 1.74 mm–3 compared to 0.65 mm–3 in larger grains). The pore concentration in gabbrodolerite crushed stone grains is similar between large and small grains – 0.26 mm–3 and 0.24 mm–3, respectively.
In the structure of all the studied crushed stone grains, pores of fine capillary size, up to 40 µm, predominate in quantity (Fig.1, b). The sphericity (the ratio of the shortest to the longest axis) of these pores is high – 0.8-0.9. In small granite grains, the largest pore size is 120 µm, while in gabbro-dolerite, it is 60 µm. Larger grains contain supercapillary-sized voids – up to 240 µm in granite and no more than 160 µm in gabbrodolerite (Fig.2), with only 1-3 such voids per grain. The sphericity of these pores is low – 0.1-0.3. There is no clear orientation of the pores in any specific direction (Fig.3). This feature is typical for all the studied gabbrodolerite crushed stone grains, where porosity ranges from 0.59-0.62 % in large grains and 0.5-0.57 % in small grains, while granite grains are heterogeneous. Their porosity varies from 1.85-2.42 % in large grains and 2.31-3.3 % in small grains, respectively (Table 2).
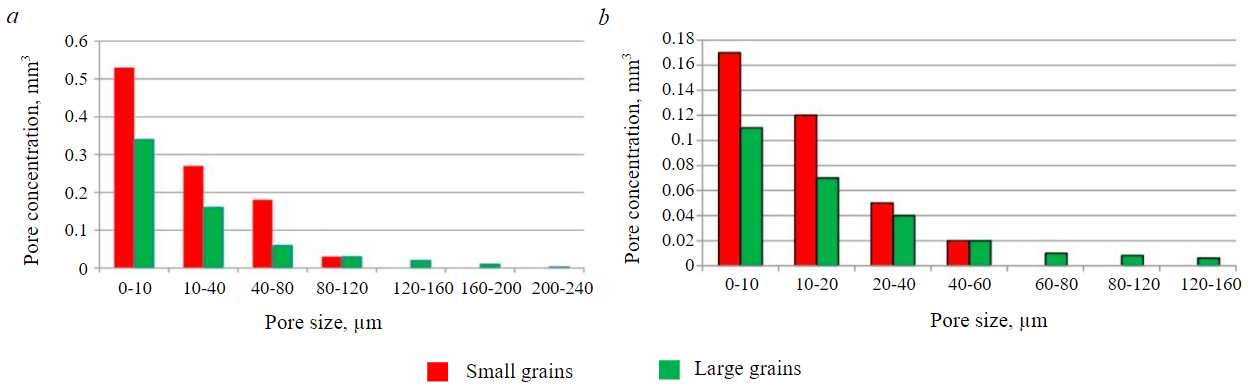
Fig.2. Pore size distribution in granite (a) and gabbrodolerite (b) grains (average values)
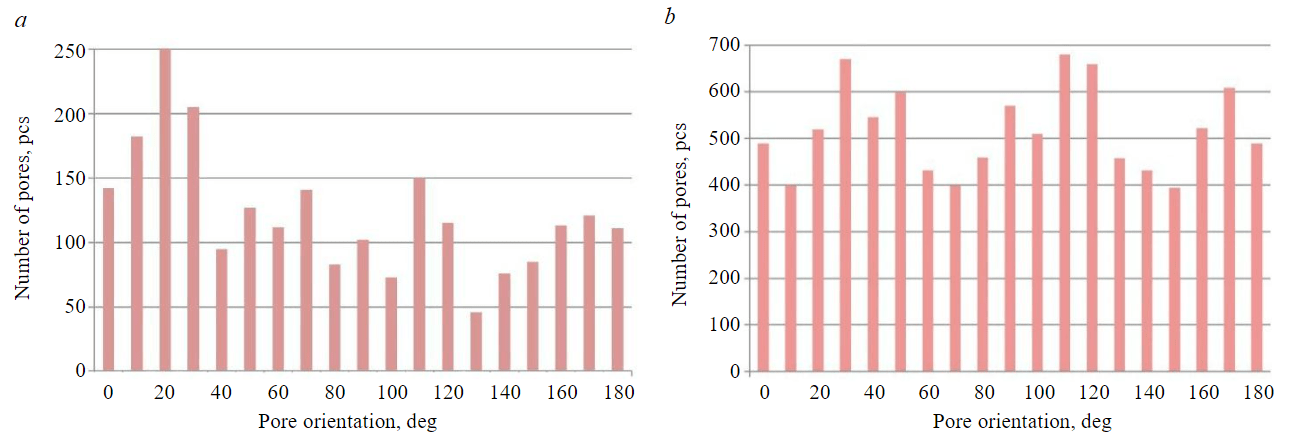
Fig.3. Pore orientation distribution along the longest axis: grain 4 from the 5-20 mm fraction of gabbrodolerite (a), granite (b)
The development of microdamage in rocks depends on the strength properties of the individual rock-forming minerals [39, 40]. Given that some varieties of granite are characterized by wide variations in pore size, shape, and content, which are unevenly distributed throughout its volume [41-43], it is crucial to study the specific features of the pore structure of the minerals that constitute it. Microtomography revealed that pores in the structure of the studied crushed granite grains are unevenly distributed. The highest concentration of pores is found in large microcline grains, where porosity is 1.5 to 2 times higher than the overall porosity of the grains. The pores in microcline are distributed chaotically and have sizes up to 40 µm. The porosity of plagioclase and quartz aggregates is significantly lower. The wide variations in microcline content, ranging from 35.34 to 47.22 %, explain the instability of the porosity in the studied granite grains (Table 3).
Table 3
Characteristics of the main rock-forming minerals in original samples and crushed stone grains from granite, %
Grains number |
Microcline |
Plagioclase + quratz |
||
Content |
Porosity |
Content |
Porosity |
|
Initial granite samples |
||||
Average |
39.82 |
1.2 |
55.31 |
0.3 |
Crushed stone grains 20-40 mm |
||||
1 |
35.34 |
4.1 |
63.00 |
0.90 |
2 |
40.34 |
3.9 |
57.68 |
0.63 |
3 |
42.34 |
4.1 |
55.91 |
0.78 |
4 |
47.22 |
3.3 |
50.38 |
0.66 |
5 |
35.50 |
3.8 |
61.71 |
0.73 |
Average |
40.15 |
3.8 |
57.73 |
0.74 |
Crushed stone grains 5-20 mm |
||||
1 |
39.69 |
4.31 |
58.61 |
0.93 |
2 |
47.09 |
4.12 |
50.71 |
0.90 |
3 |
39.65 |
4.25 |
55.95 |
0.94 |
4 |
46.96 |
6.41 |
50.54 |
0.95 |
5 |
35.29 |
4.48 |
60.89 |
0.96 |
Average |
41.74 |
4.71 |
55.34 |
0.94 |
A comparison of tomographic slices of crushed granite grains of different sizes (Fig.4) shows that the porosity of microcline inclusions in larger grains is higher than in smaller ones. In large granite grains, the porosity of microcline DOI: 1averages 3.8 %, while in smaller grains this figure is higher – 4.71 %. The porosity of plagioclase and quartz in smaller grains is also higher – 0.74 % and 0.94 %, respectively (Table 3). Fig.4 presents the visualization of the sections of the studied samples, while Fig.5 shows the microtomographic slices after binarization for enhanced contrast detailing of the grains. It is logical to assume that the increased porosity of small granite grains is related to additional mechanical stresses on the smaller fractions of crushed stone, which were obtained during the third stage of crushing. The strength of a sample is determined by the strength of its weakest section [44]. Destruction begins at the most brittle areas, which in granite crushed stone grains are the microcline inclusions. Irreversible plastic deformations lead to the formation of newly developed defects, the number of which increases with repeated loading.
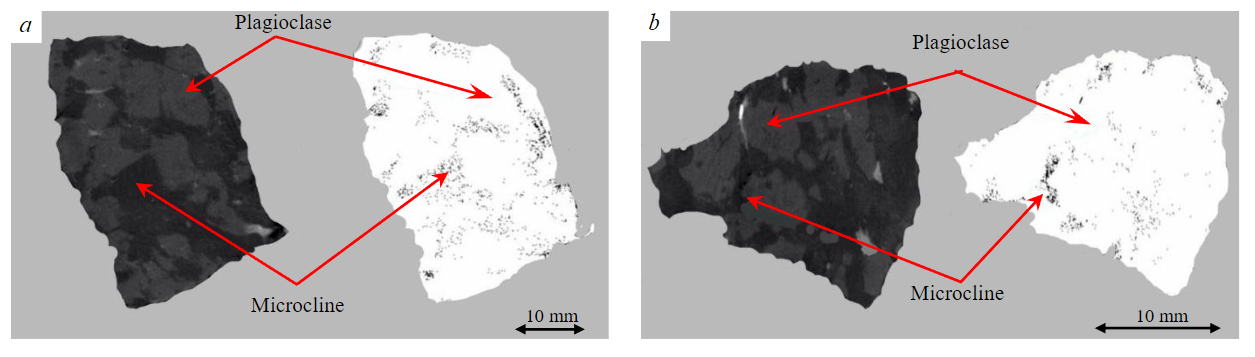
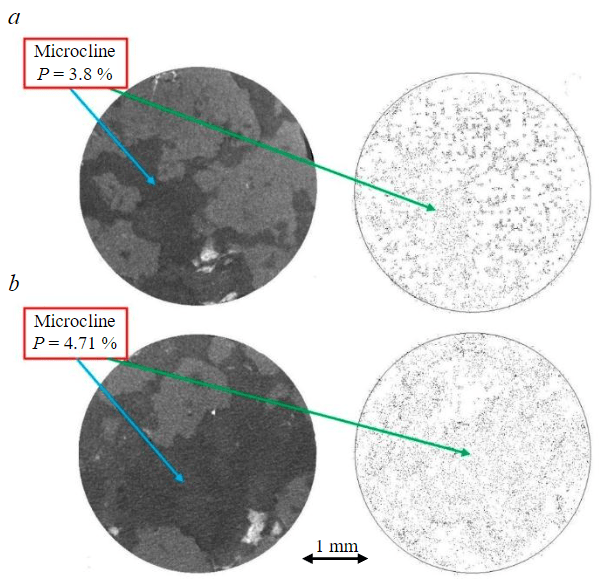
Fig.5. Single sections of granite crushed stone grains, obtained as a result of microtomographic scanning after grain binarization from the fraction 20-40 mm (a), 5-20 mm (b)
The studied samples of granite crushed stone contain quartz in the amount of 20-26 %. In [45], it was noted that the presence of quartz in rock composition significantly influences the formation of microcracks. When subjected to mechanical stresses, brittle and elastic quartz crystals fracture, forming intragranular microcracks [46, 47].
The studied gabbrodolerite crushed stone samples are homogeneous in mineral composition. The content of pyroxene ranges from 46.7 to 50.0 %, and the content of plagioclase and quartz ranges from 47.3 to 50.2 %. Pores are fairly evenly distributed within the aggregates of the main rock-forming minerals – pyroxene and plagioclase – with a slight predominance in plagioclase. In smaller grains, a slight decrease in plagioclase porosity is observed, from 0.69 % in larger grains to 0.62 % in smaller ones. The porosity of pyroxene remains almost identical for both small and large grains, at 0.46 and 0.44 %, respectively (Table 4). The reduction in the overall porosity of gabbrodolerite grains as their size decreases aligns with the statistical theory of rock strength, which posits that the likelihood of defects decreases as sample size reduces – the smaller the grain size, the higher its strength.
Table 4
Characteristics of the main rock-forming minerals in original samples and crushed stone grains from gabbrodolerite, %
Grain number |
Plagioclase + quartz |
Plagioclase |
||
Content |
Porosity |
Content |
Porosity |
|
Initial gabbrodolerite samples |
||||
Average |
50.6 |
0.44 |
46.1 |
0.2 |
Crushed stone grains 20-40 mm |
||||
1 |
50.2 |
0.64 |
46.7 |
0.56 |
2 |
47.9 |
0.68 |
48.3 |
0.30 |
3 |
49.0 |
0.70 |
47.1 |
0.53 |
4 |
49.4 |
0.81 |
48.8 |
0.43 |
5 |
46.8 |
0.63 |
48.3 |
0.57 |
Average |
48.1 |
0.69 |
48.2 |
0.44 |
Crushed stone grains 5-20 mm |
||||
1 |
49.1 |
0.68 |
46.9 |
0.45 |
2 |
48.6 |
0.56 |
49.1 |
0.58 |
3 |
48.1 |
0.65 |
48.4 |
0.40 |
4 |
49.7 |
0.63 |
47.5 |
0.39 |
5 |
47.3 |
0.58 |
50.0 |
0.48 |
Average |
49.0 |
0.62 |
48.2 |
0.46 |
Note. The volumetric content of minerals and their total porosity were determined using X-ray computed microtomography. Scanning resolution is 0.5 μm
Conclusion
Thus, during disintegration, the pore structure of the rock undergoes changes. The total porosity of the crushed stone grains increases due to the formation of newly developed pores. This pattern is most pronounced in granite and less noticeable in gabbrodolerite.
Large and small crushed stone grains differ in terms of total porosity, pore size, and pore concentration. There is no clear relationship between the porosity of the crushed stone grains and their size, which is due to the textural and structural characteristics as well as the mineral composition of the original rocks.
Granite crushed stone grains are heterogeneous in mineral composition, resulting in uneven pore distribution. The presence of brittle and porous microcline inclusions in granite crushed stone grains leads to the formation of new pores and microcracks, whose number increases with repeated loading. Therefore, large crushed stone grains from the 20-40 mm fraction, obtained after the second stage of crushing, are characterized by lower porosity and pore concentration compared to smaller grains from the 5-20 mm fraction, which were crushed during the third stage.
The scale effect is evident only in gabbrodolerite, which has a fine-grained structure and massive texture – where a reduction in the size of the crushed stone grains leads to a decrease in pore size and total porosity.
References
- Viktorov S.D., Kochanov A.N. Some aspects of rock destruction from the standpoint of strength physics and crack mechanics. Aktualnye problemy prochnosti: Materialy 60-i Mezhdunarodnoi konferentsii, 14-18 maya 2018, Vitebsk, Belarus. Vitebsk: Vitebskii gosudarstvennyi tekhnologicheskii universitet, 2018, p. 340-342.
- Quansheng Liu, Qi Liu, Yucong Pan et al. Microcracking Mechanism Analysis of Rock Failure in Diametral Compression Tests. Journal of Materials in Civil Engineering. 2018. Vol. 30. Iss. 6. N 04018082-1. DOI: 10.1061/(ASCE)MT.1943-5533.0002251
- Wen-Ling Tian, Sheng-Qi Yang, Li-Xiang Xie, Zhi-Liang Wang. Cracking behavior of three types granite with different grain size containing two non-coplanar fissures under uniaxial compression. Archives of Civil and Mechanical Engineering. 2018. Vol. 18. Iss. 4, p. 1580-1596. DOI: 10.1016/j.acme.2018.06.001
- Ioffe A.F., Kirpicheva M.V., Levitskaya A.I. Deformation and strength of crystals. Zhurnal russkogo fiziko-khimicheskogo obshchestva. 1924. Vol. 56. N 5-6, p. 489-504.
- Usoltseva O.M., Tsoi P.A., Semenov V.N. Sample size influence on stress-strain properties of rocks. Fundamental and applied issues of mining. 2020. Vol. 7. N 2, p. 53-59 (in Russian). DOI: 10.15372/FPVGN2020070209
- Zaytsev D.V., Kochanov A.N., Panteleev I.A., Panfilov P.Y. Influence of the Scale Effect in Testing the Strength of Rock Samples. Bulletin of the RAS: Physics. 2017. Vol. 81. N 3, p. 337-340. DOI: 10.3103/S1062873817030406
- Latyshev O.G., Prishchepa D.V. Accounting for the scale effect in designing parameters of mining technology. News of the Ural State Mining University. 2017. Iss. 1 (45), p. 59-61 (in Russian). DOI: 10.21440/2307-2091-348 2017-1-59-61
- Vaysberg L.A., Kameneva E.E., Aminov V.N. Assessment of Technological Capabilities of Control over Crushed Stone Quality in the Course of Disintegration of Building Rocks. Stroitelnye materialy. 2013. N 11, p. 30-34 (in Russian).
- Kolotushkin D.M., Algebraistova N.K. Properties of nonmetallic materials and their effect on the quality of end products. Journal of Construction and Architecture. 2016. N 6, p. 226-233 (in Russian).
- Burtan S.T., Mustafin S.K. Composition and properties of the mineral framework in connection with the problem of asphalt concrete quality management. Dorozhnaya derzhava. 2010. N 10, p. 20-27.
- Myasnikova O.V., Schekov V.A. The influence of the natural and the technogenic microjointing on the rock endurance. Mining Informational and Analytical Bulletin. 2009. N 8, p. 321-326 (in Russian).
- Staněk M., Géraud Y. Granite microporosity changes due to fracturing and alteration: secondary mineral phases as proxies for porosity and permeability estimation. Solid Earth. 2019. Vol. 10. Iss. 1, p. 251-274. DOI: 10.5194/se-10-251-2019
- Brigadnov I.A. Direct Methods for Solving the Variation Problem for Multicriteria Estimation of the Bearing Capacity of Geomaterials. Journal of Mining Institute. 2018. Vol. 232, p. 368-374. DOI: 10.31897/PMI.2018.4.368
- Gospodarikov A.P., Trofimov A.V., Kirkin A.P. Evaluation of deformation characteristics of brittle rocks beyond the limit of strength in the mode of uniaxial servohydraulic loading. Journal of Mining Institute. 2022. Vol. 256, p. 539-548. DOI: 10.31897/PMI.2022.87
- Zhukov V.S., Kuzmin Yu.O., Tikhotsky S.A. et al. Changes in fracture porosity during the preparation of rock destruction. Physical-chemical and petrophysical researches in the Earth’s sciences: Proceedings of the twenty-second international conference, 27-29 September 2021, Moscow, Russia. Moscow: Institute of Geology of Ore Deposits, Petrography, Mineralogy and Geochemistry of the RAS, 2021, p. 106-109 (in Russian).
- Rui Song, Lifu Zheng, Yao Wang, Jianjun Liu. Effects of Pore Structure on Sandstone Mechanical Properties Based on Micro-CT Reconstruction Model. Advances in Civil Engineering. 2020. Vol. 2020. Iss. 1. N 9085045. DOI: 10.1155/2020/9085045
- Cheng Z.L., Sui W.B., Ning Z.F. Microstructure characteristics and its effects on mechanical properties of digital core. Chinese Journal of Rock Mechanics and Engineering. 2018. Vol. 37. N 2, p. 449-460. DOI: 10.13722/j.cnki.jrme.2017.1122
- Karch J., Dudák J., Žemlička J. et al. X-ray micro-CT and neutron CT as complementary imaging tools for non-destructive 3D imaging of rare silicified fossil plants. Journal of Instrumentation. 2017. Vol. 12. N 12004. DOI: 10.1088/1748-0221/12/12/C12004
- Kravcov A., Franek O., Morozov N. et al. Laser ultrasonic measurement of mechanical decay in limestone caused by freeze-thaw cycles. Acta Polytechnica. 2020. Vol. 60. N 5, p. 410-414. DOI: 10.14311/AP.2020.60.0410
- Karabutov A.A., Cherepetskaya E.B., Kravcov A.N., Arrigoni M. Methods of studying structure and properties of rocks using samples (short review). Mining Science and Technology (Russia). 2018. N 4, p. 10-20 (in Russian). DOI: 10.17073/2500-0632-2018-4-10-20
- Guntoro P.I., Ghorbani Y., Koch P.-H., Rosenkranz J. X-ray Microcomputed Tomography (µCT) for Mineral Characterization: A Review of Data Analysis Methods. Minerals. 2019. Vol. 9. Iss. 3. N 183. DOI: 10.3390/min9030183
- Bam L.C., Miller J.A., Becker M., Basson I.J. X-ray computed tomography: Practical evaluation of beam hardening in iron ore samples. Minerals Engineering. 2019. Vol. 131, p. 206-215. DOI: 10.1016/j.mineng.2018.11.010
- Withers P.J., Bouman C., Carmignato S. et al. X-ray computed tomography. Nature Reviews Methods Primers. 2021. Vol. 1. N 18. DOI: 10.1038/s43586-021-00015-4
- Rui Song, Yao Wang, Jianjun Liu et al. Comparative analysis on pore-scale permeability prediction on micro-CT images of rock using numerical and empirical approaches. Energy Science & Engineering. 2019. Vol. 7. Iss. 6, p. 2842-2854. DOI: 10.1002/ese3.465
- Yakushina O.A., Khozyainov M.S. Geomaterials study by X-ray computed tomography. Physical-chemical and petrophysical researches in the Earth’s sciences: Proceedings of the twenty-second international conference, 27-29 September 2021, Moscow, Russia. Moscow: Institute of Geology of Ore Deposits, Petrography, Mineralogy and Geochemistry of the RAS, 2021, p. 302-305 (in Russian).
- Pini R., Madonna С. Moving across scales: a quantitative assessment of X-ray CT to measure the porosity of rocks. Journal of Porous Materials. 2016. Vol. 23. Iss. 2, p. 325-338. DOI: 10.1007/s10934-015-0085-8
- Jarzyna J.A., Krakowska P.I., Puskarczyk E. еt al. X-ray computed microtomography – a useful tool for petrophysical properties determination. Computational Geosciences. 2016. Vol. 20. Iss. 5, p. 1155-1167. DOI: 10.1007/s10596-016-9582-3
- Godinho J.R.A., Hassanzadeh A., Heinig T. 3D Quantitative Mineral Characterization of Particles Using X-ray Computed Tomography. Natural Resources Research. 2023. Vol. 32. Iss. 2, p. 479-499. DOI: 10.1007/s11053-023-10169-5
- Callow B., Falkon-Suarez I., Marin-Moreno N. et al. Optimal X-ray micro-CT image based methods for porosity and permeability quantification in heterogeneous sandstones. Geophysical Journal International. 2020. Vol. 223. Iss. 2, p. 1210-1229. DOI: 10.1093/gji/ggaa321
- Lau S.H., Miller J.D., Lin C.-L. 3D mineralogy, texture and damage analysis of multiphase mineral particles with a high contrast, submicron resolution X-ray tomography system. Conference Proceedings of the XXVI International Mineral Processing Congress (IMPC 2012), 24-28 September 2012, New Delhi, India. N 1022.
- Willson C.S., Ning Lu, Likos W.J. Quantification of Grain, Pore, and Fluid Microstructure of Unsaturated Sand from X-Ray Computed Tomography Images. Geotechnical Testing Journal. 2012. Vol. 35. Iss. 6, p. 13. DOI: 10.1520/GTJ20120075
- De Kock T., Boone M.A., De Schryver T. et al. A Pore-Scale Study of Fracture Dynamics in Rock Using X-ray Micro-CT Under Ambient Freeze – Thaw Cycling. Environmental Science & Technology. 2015. Vol. 49. Iss. 5, p. 2867-2874. DOI: 10.1021/es505738d
- Merzlikin A.V., Zakharova L.N. Peculiarities of Kinematics of Rock Mass Shear During Development of Subseismic-scale Faults. Journal of Mining Institute. 2018. Vol. 231, p. 235-238. DOI: 10.25515/PMI.2018.3.235
- Reyes F., Lin Q., Cilliers J.J., Neethling S.J. Quantifying mineral liberation by particle grade and surface exposure using X-ray microCT. Minerals Engineering. 2018. Vol. 125, p. 75-82. DOI: 10.1016/j.mineng.2018.05.028
- Van Geet M., Swennen R., Wevers M. Quantitative analysis of reservoir rocks by microfocus X-ray computerised tomography. Sedimentary Geology. 2000. Vol. 132. Iss. 1-2, p. 25-36. DOI: 10.1016/S0037-0738(99)00127-X
- Jardine M.A., Miller J.A., Becker M. Coupled X-ray computed tomography and grey level co-occurrence matrices as a method for quantification of mineralogy and texture in 3D. Computers & Geosciences. 2018. Vol. 111, p. 105-117. DOI: 10.1016/j.cageo.2017.11.005
- Lin Qingyang, Andrew M., Thompson W. et al. Optimization of image quality and acquisition time for lab-based X-ray microtomography using an iterative reconstruction algorithm. Advances in Water Resources. 2018. Vol. 115, p. 112-124. DOI: 10.1016/j.advwatres.2018.03.007
- Van Offenwert S., Cnudde V., Bultreys T. Pore-Scale Visualization and Quantification of Transient Solute Transport Using Fast Microcomputed Tomography. Water Resources Research. 2019. Vol. 55. Iss. 11, p. 9279-9291. DOI: 10.1029/2019WR025880
- Golovin Y.I., Tyurin A.I., Victorov S.D. et al. Size Effects and Charting the Physical and Mechanical Properties of Individual Phases and Interphases in Polycrystalline Materials. Bulletin of the RAS: Physics. 2018. Vol. 82. N 7, p. 856-859. DOI: 10.3103/S1062873818070201
- Latyshev O.G., Kazak O.O. The influence of the geological material disturbance on its properties and condition. News of the Ural State Mining University. 2017. Iss. 4 (48), p. 62-65 (in Russian). DOI: 10.21440/2307-2091-2017-4-62-65
- Dajun Zhao, Shulei Zhang, Meiyan Wang. Microcrack Growth Properties of Granite under Ultrasonic High-Frequency Excitation. Advances in Civil Engineering. 2019. Vol. 2019. Iss. 1. N 069029. DOI: 10.1155/2019/3069029
- Myasnikova O.V., Trishina O.M., Kovalevskii M.V. et al. Structure and properties of granites from deposits of non-metallic building materials. Trudy Fersmanovskoi nauchnoi sessii Gornogo instituta KNTs RAS. 2009. N 6, p. 226-230.
- Vaisberg L.A., Kameneva E.E., Nikiforova V.S. Microtomographic studies of rock pore space as the basis for rock disintegration technology improvements. Obogashchenie rud. 2018. N 3, p. 51-55 (in Russian). DOI: 10.17580/or.2018.03.09
- Zaytsev D.V., Kochanov A.N., Toktogulov Sh.Zh. et al. Influence of scale effect and heterogeneity of rocks to determine their strength properties. Mining Informational and Analytical Bulletin. 2016. N 11, p. 208-215 (in Russian).
- Kochanov A.N. Cracks in a solid for example rocks. Mining Informational and Analytical Bulletin. 2015. N 7, p. 221-225 (in Russian).
- Kuksenko V.S., Makhmudov Kh.F., Mansurov V.A. et al. Changes in structure of natural heterogenous materials under deformation. Journal of Mining Science. 2009. Vol. 45. N 4, p. 355-358. DOI: 10.1007/s10913-009-0044-3
- Menzhulin M.G., Makhmudov Kh.F., Kuksenko V.S., Sultonov U. Formation and development of focus destruction of natural strain heterogeneous materials. Tambov University Reports. Series Natural and Technical Sciences. 2013. Vol. 18. Iss. 4-2, p. 1667-1668 (in Russian).