Improving the efficiency of oil vapor recovery units in the commodity transport operations at oil terminals
- 1 — Ph.D. Associate Professor Saint Petersburg Mining University ▪ Orcid
- 2 — Ph.D. Assistant Lecturer Saint Petersburg Mining University ▪ Orcid ▪ Elibrary ▪ Scopus
Abstract
In this paper the problem of losses from evaporation of light fractions of hydrocarbons during loading operations of tanker fleets vessels is considered. It was found that there is no unified approach to modeling the system “tanker – gas phase pipeline – vapor recovery units” in open sources. The absence of a generally recognized model makes it impossible to scientifically justify the application of instruments to reducing losses and the development of corresponding measures. In work it is showed that the dynamics of growth of pressure in the inner tanker capacity is described by a differential equation, considering for non-stationary essence of the process. This equation is converted to a non-dimensional form and investigated in relation to the similarity criteria of this system. This research has allowed to establish unambiguously the general character of pressure changes in the inner tanker capacity, and to predict the peak values of its growth at the initial stage of the loading operation. The obtained equations were tested on real tanker loading data and showed satisfactory convergence with the experimental data. At different stages of the loading opera-tion the component composition of vapor changes, which is shown by chromatographic analysis of the gas mixture. With the availability of a model of hydrocarbon vapor displacement from the inner of tanker, it is possible to propose measures to minimize the negative impact on the environment and return valuable vapors of the product to the technological chain of transportation.
Introduction
In the process of tanker loading oil or oil products evaporate intensively, which leads to an increase of the excess pressure in their internal space. In case of high loading rates and insufficient capacity of gas venting systems, when the pressure reaches a critical value a part of the gas-air mixture is released into the atmosphere. Venting vapors to the atmosphere through breathing valves or mast riser is undesirable for the following reasons:
- irretrievable loss of valuable materials occurs (for comparison, for a tanker of Aframax class the size of losses during one operation of crude oil loading can make approximately half of the volume of one railway tank);
- a risk of emergency stop of loading due to triggering of automatic systems at the berth because of high gas level;
- evaporation of light fractions worsens quality indicators of oil products;
- pollution of atmospheric basin occurs [1, 2].
The way of controlling losses from vaporization at oil loading terminals is introduction and efficient operation of vapor recovery units (VRU) [3, 4]. If in domestic practice oil loading terminals have just begun to be equipped with such devices since about 2010 (mainly imported), then abroad they have gained a great practical experience of their application [5, 6]. In the world practice of research in this field the leaders are the countries which are characterized by large volumes of tanker traffic: the USA, Japan, Norway, China [7, 8]. Despite the relatively successful use of these units, there is also a negative experience. Research in this area, especially the project VocSim implemented by Norwegian Marine Technology Research Institute [1], despite substantial financing, could not provide a universal solution for modeling system “tanker – gas phase pipeline – vapor recovery unit” [9, 10]. The reasons are the following: oil (or oil products) evaporation process has a complicated non-stationary character; uniqueness of every separate oil terminal and tanker; a great number of influencing factors. Some research in the field of heat transfer in the internal tanker space [11], determination of vapor composition [12, 13], evaporation processes for different products [14, 15], improvement of individual systems and emission reduction means [16, 17] etc. are of a detached type and can not efficiently solve the task of emission reduction and operative control within an oil terminal as a whole [18, 19].
An important issue is the total volume of volatile hydrocarbon emissions through the mast riser. This value is not monitored, there are simply no flow measurement devices installed on the mast riser line, and calculated estimates are impossible or inaccurate due to the lack of a model of pressure changes in the tanker's gas space. The air-gas mixture being vented through the mast riser enters the atmosphere directly, bypassing the vapor recovery unit, which makes it impossible to recover at least part of the vapor. Vapors are vented when the critical pressure is exceeded through the special piping of the tanker. The flow mode is characterized by non-linearity in pressure, and there is also uncertainty in the duration of opening the mast riser. As a rule opening takes place at the direction of the tanker captain for a short period at the moment of peak pressure growth dynamics in order to stabilize it. From the terminal side, these processes are fixed as unavoidable costs of the technological process. Such approach is not quite correct, since it is impossible to exclude irregular situations completely, but it is possible to minimize their negative impact.
The aim of the study is to provide a scientific basis for measures to reduce losses and improve the efficiency of operation of vapor recovery units. The work consistently solved a number of related problems: the dynamics of pressure growth in the gas space of the tanker has been simulated; the obtained solution has been tested on the data of real loading in the port of Kozmino; the quantitative content of hydrocarbons C1-C10 at different stages of the loading operation has been experimentally determined. Within the framework of the given model, estimates were obtained for possible emission reduction reserve in case of prevention of opening of the mast riser.
Methodology
In the part of obtaining experi-mental data on the quantitative content of C1-C10 hydrocarbons at different stages of the loading ope-ration the results of chromatographic analysis of selected samples of the displaced gas-air mixture on the “Chromatec-Crystal 5000” unit were used [20, 21]. The results were obtained from laboratory studies with the author's involvement, and the results were published earlier in the open press [22, 23]. Within the framework of studies of hyd-rocarbon evaporation process the total mass transfer from the surface of oil (oil product) of C1-C10 hydrocarbons is of interest (Fig.1) [24, 25].
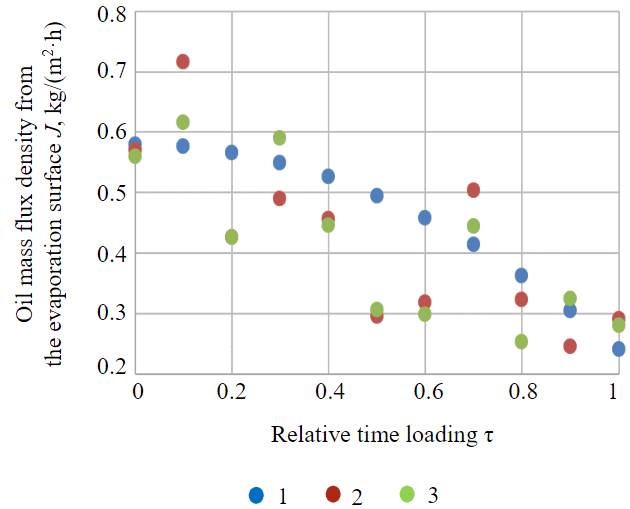
Fig.1. Dynamics of mass transfer from the surface of the oil in the process of tanker loading operation
1 – “ANTONIS”; 2 – “FRONT CASTOR”; 3 – “MASTERA”
Mass transfer decreases over time, as the gas space above the oil (oil product) surface becomes saturated and prevents further evaporation [26, 27]. However, there are a number of secondary effects that can prevent the smooth nature of this function: tanker's motions/rolling; non-uniformity of the gas removal system; internal convective fluxes; changes in temperature [27, 28]. The principal diagram of vapor release during cargo loading provides a line: “tanker gas system – gas phase pipeline – vapor recovery unit – gas vent” (Fig.2) [29, 30].
Values for pressure and temperature in the loading process are taken from data of the automated workstation of the vapor recovery unit dispatcher [31, 32]. Part of the information is obtained from the tanker's automation systems (pressure in tanks, oxygen content, and temperature in tanks) [33, 34]. A representation of oil vapor displacement during tanker loading is shown in Fig.3.
The equation of state of the gas-air mixture in differential form is:
where V – the volume of the tanker’s gas space, m3; P – pressure in the gas space of the tanker, Pa; R – the gas constant for the component mixture (based on the average molar mass of the vapor), J/kmol·K; T – the temperature inside the gas space of the tanker.
As a result of reducing the equation to a non-dimensional form, it is found that the rate of pressure growth in the inner tanker volume capacity is determined by the following differential equation:
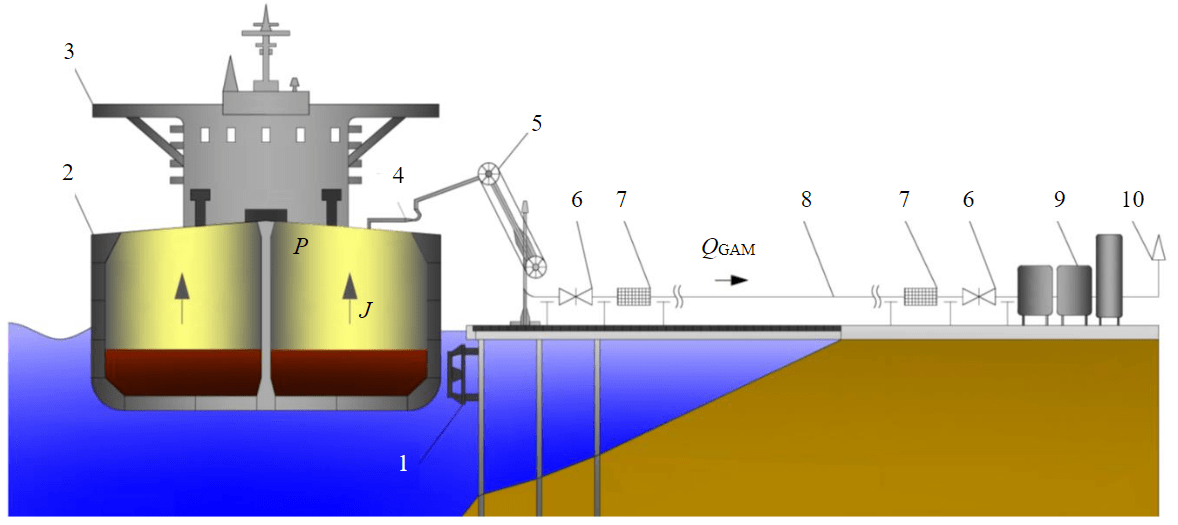
Fig.2. Schematic diagram of gas vent systems of the tanker, coastal and berthing facilities
1 – node protection berthing facilities fender; 2 – double housing; 3 – tanker; 4 – mast riser; 5 – a stander removal of the gas phase; 6 – shut-off and control valves; 7 – detonation arrestor; 8 – the pipeline of the gas phase; 9 – VRU; 10 – gas vent; QGAM – flowrate gas-air mixture; J – mass transfer
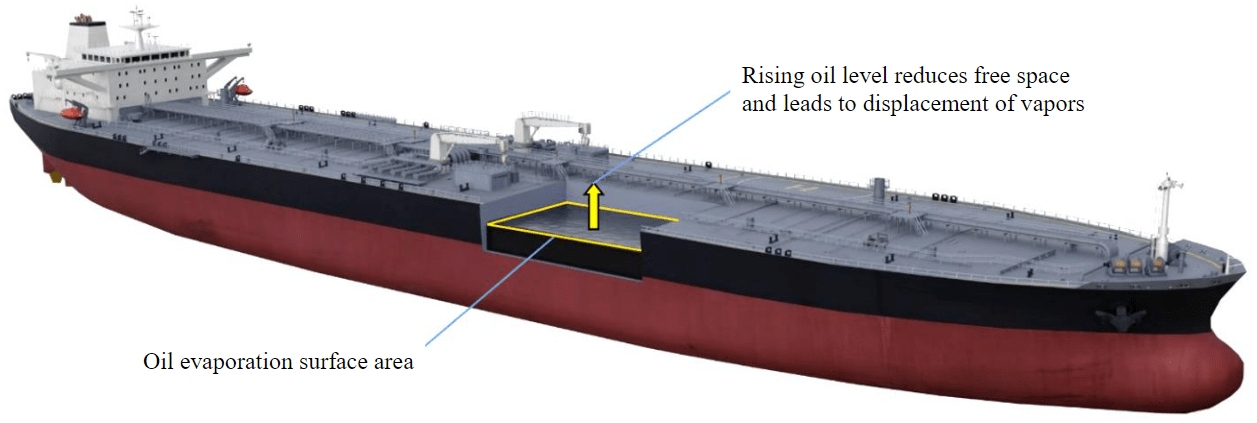
Fig.3. Schematic representation of oil level rise (one compartment is shown in section) and oil vapor displacement during tanker loading
where y – dimensionless pressure; τ – dimensionless time; ψ – similarity criterion for the contribution of mass transfer to the pressure growth dynamics; θ – similarity criterion for the contribution of hydraulic resistance to the pressure growth dynamics; ξ – dimensionless ratio for mass transfer;
Рend – pressure at the endpoint; F – evaporation surface area; Qload – oil filling flow rate of the tanker; λ – hydraulic resistance coefficient; D – pipeline diameter; S – cross-sectional area of the gas phase pipeline; t – the current time since the beginning of loading; τload – full filling time; Jend, Jstart – mass transfer at the final and starting points of time.
From the dimensionless point of view the dynamics of pressure changes are described by a functional dependence of the form:
The dependence (8) can be used as a reference in the construction of bench equipment to test working hypotheses on the operation of vapor recovery systems and gas removal systems on small-scale units in laboratory conditions [35]. The value of hydrocarbon losses at the opening of mast riser should be determined based on the mass flow rate of the gas-air mixture through the ventilation system of the tanker:
where Svent – flow area of the pipeline of the tanker ventilation system; [Pmr] – mast riser opening pressures; Patm – atmospheric pressure; T – gas-air mixture temperature; Leff – effective length inclu-ding local friction drag; Dvent – pipeline’s diameter of the tanker ventilation system; R – universal gas constant; εf – a factor that takes into account the degree of opening of the mast riser.
The mass flow rate is related to the volumetric flow rate by the following equation:
where Qmr – volumetric flow rate of the gas-air mixture through the mast riser; rGAM – gas-air mixture density.
The total hydrocarbon losses through the mast riser per year should be determined from the equation:
where сav – average concentration of hydrocarbons in the emission, g/m3; τmr – average length of time the mast riser is open; Nnum – the number of cases of opening a mast riser per year.
Estimated calculation of damage in value terms:
where σVOC – fee rate for the emission of 1 t of the amount of hydrocarbons C1-C10; Seff – predicted degree of the gas-air mixture refining; σcrude – cost per 1000 m3 of oil.
Discussion of the results
The developed model was tested on the data of real tanker loading, and a number of practical results were obtained (results in Table). Basic data on tanker loading: tanker deadweight – 106208 t; dimensions – 241×44 m; inert gas – exhaust gases; oil density – 0.872 t/m3 at 20 °С; saturated oil vapor pressure – 54.3 kPa; duration of loading – 14.21 h. The results of approbation of the developed model on the data of real loading operation are shown in Fig.4.
Because the model showed satisfactory convergence, (discrepancies do not exceed 10 %) with the data collected during the loading operation, it is proposed to apply its results to estimate losses in case of opening of the mast riser. The highest pressure is reached from two hours after the start of loading at a linearly increasing pumping rate [36]. At these moments it is not rare for tankers to open the mast riser. Calculations are given by the example of operation of the tanker gas removal system and vapor recovery adsorption unit in the port of Kozmino (Fig.5).
Results of approbation of the mathematical model
Time from the beginning of the loading operation, h |
Pressure according to the tanker's automatics systems, Pa |
Pressure in the inner space of the tanker according to simulation results, Pa |
|
0 |
101815 |
101815 |
|
1 |
103596 |
104081 |
|
2 |
103899 |
104159 |
|
3 |
107643 |
108083 |
|
4 |
108681 |
108651 |
|
5 |
108894 |
108544 |
|
6 |
108837 |
108357 |
|
7 |
108702 |
108742 |
|
8 |
108550 |
108730 |
|
9 |
108399 |
108274 |
|
10 |
108253 |
108268 |
|
11 |
104983 |
105313 |
|
12 |
104891 |
104886 |
|
13 |
105585 |
105820 |
|
14 |
103946 |
104236 |
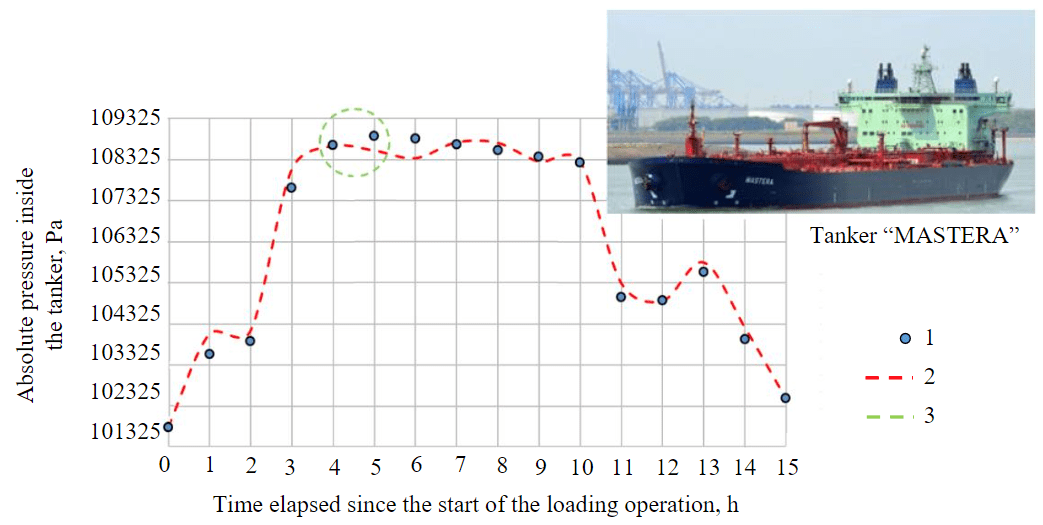
Fig.4.Results of approbation of the mathematical model
1 – automatics data of tanker “MASTERA”; 2 – the results within the developed model; 3 – opening area mast riser
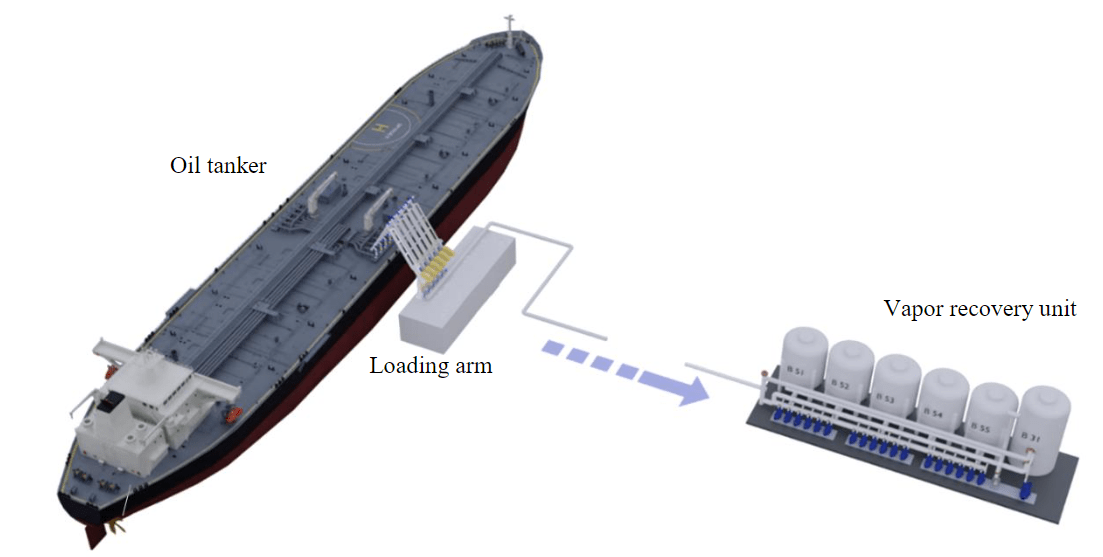
Fig.5. Schematic diagram of vapor displacement from a tanker to a vapor recovery unit
On the basis of the developed technique of the damage estimation, connected with opening of the mast riser, there were made forecast calculations of the given value with the average mass content of hydrocarbons C1-C10 273.52 g/m3 and degree of cleanup of the gas-air mixture of 72.6 % [37, 38].
The results of calculations of damage caused by opening the mast riser (based on 50 mast riser openings per year, which is taken from the average operating data) [39]: estimated hydrocarbon losses per loading – 12.3 t; estimated annual hydrocarbon losses – 615 t; damage in value terms for 1 year (including the value of the irretrievably lost product) – 26.623 million rub.
The damage in cost terms can either be completely eliminated or minimized in the case of operational management of tanker loading and control over the operation of the vapor recovery unit systems [40, 41].
Conclusion
As part of the study, for the first time a generalized model of the dynamics of pressure growth in the gas space of the tanker was obtained, and the resulting solution was tested on the data of real loading in the oil terminal. It was found that the pressure change during the loading operation is non-linear and has a local maximum. In order to avoid the opening of the mast riser, it is necessary to ensure such loading modes, which are outside the area of critical pressures. It has been established experimentally, that the quantitative content of hydrocarbons C1-C10 increases with the process of loading, at its initial stage light components (methane, ethane, propane, butane) evaporate, and at the final stages hexane and higher hydrocarbons C6+ evaporate. Within the framework of the developed model the possible reserve for the reduction of emissions into the environment at the opening of the mast riser was rated. Operational management of tanker loading allows reducing emissions by saving about 26 million rub. per year.
The conducted research provides a scientific basis for the measures to reduce losses and improve the efficiency of vapor recovery units’ operation. In the future, this research will allow not only to increase efficiency of domestic units within the own developments in line with the import substitution programs, but also to provide secure, resource-saving, environmentally friendly operation of oil terminals.
References
- Invernizzi M., Sironi S. Odour Emission Rate Estimation Methods for Hydrocarbon Storage Tanks. Chemical Engineering Transactions. 2021. Vol. 85, p. 67-72. DOI: 10.3303/CET2185012
- Milazzo M.F., Ancione G., Lisi R. Emissions of volatile organic compounds during the ship-loading of petroleum products: Dispersion modelling and environmental concerns. Journal of Environmental Management. 2017. Vol. 204. Part 1, p. 637-650. DOI: 10.1016/j.jenvman.2017.09.045
- Woohyun Kim, Munkyu Yoon, Moonyong Lee, Sunwon Park. CFD Analysis of Cavitation in a Crude Oil Pipeline to an Oil Tanker. Computer Aided Chemical Engineering. 2012. Vol. 31, p. 580-584. DOI: 10.1016/B978-0-444-59507-2.50108-6
- Nwachukwu A.N. Volatile Organic Compounds Characterization: a Case Study of a Tank Farm in the United States. JSM Environmental Science and Ecology. 2015. Vol. 3 (2). N 1019. DOI: 10.47739/2333-7141/1019
- Nwachukwu A.N. Characterization of Volatile Organic Compounds (VOCs) at an Industrial Lagoon Site in North-West England, UK. International Journal of Current Research and Academic Review. 2015. Vol. 3. N 10, p. 164-177.
- Nguyen V.T., Pham T.V., Rogachev M.K. et al. A comprehensive method for determining the dewaxing interval period in gas lift wells. Journal of Petroleum Exploration and Production Technology. 2023. Vol. 13, p. 1163-1179. DOI: 10.1007/s13202-022-01598-8
- Dmitriev M.E., Sadreeva K.K., Pshenin V.V., Gaysin M.T. Determination of the Voc Vapor Relativeflowrate During Tanker Loading Operations. Transport and storage of oil products and hydrocarbons. N 1, p. 10-13 (in Russian). DOI: 10.24411/0131-4270-2019-10102
- Davletjarov R.R., Lapina O.A., Polovkov S.A. Ensuring Environmental Safety around the Oil Loading Port Primorsk. Science & Technologies: Oil and Oil Products Pipeline Transportation. 2015. N 2, p. 84-87 (in Russian).
- Shlekova I.Yu., Ignatenko N.V. Loading hermetic sealing and hydrocarbon vapor recuperation during petroleum product shipment. Bezopasnost gorodskoi sredy: Materialy V Mezhdunarodnoi nauchno-prakticheskoi konferentsii, 21-23 noyabrya 2017, Omsk, Rossiya. Omsk: Omskii GAU, 2018, р. 224-228.
- Cherepovitsyn A.E., Tcvetkov P.S., Evseeva O.O. Critical analysis of methodological ap-proaches to assessing sustainability of arctic oil and gas projects. Journal of Mining Institute. Vol. 249, p. 463-479. DOI: 0.31897/PMI.2021.3.15
- Karbasian H.R., Dae Yeon Kim, Sang Youl Yoon et al. A new method for reducing VOCs formation during crude oil loading process. Journal of Mechanical Science and Technology. 2017. Vol. 31. Iss. 4, p. 1701-1710. DOI: 10.1007/s12206-017-0318-7
- Tokuslu A. Estimating greenhouse gas emissions from ships on four ports of Georgia from 2010 to 2018. Environmental Monitoring and Assessment. 2021. Vol. 193. Iss. 7. N 385. DOI: 10.1007/s10661-021-09169-w
- Virdi S.S., Lee L.Y., Li C., Dev A.K. Simulation of VOC Emission During Loading Operations in a Crude Oil Tanker. International Journal of Maritime Engineering. 2021. Vol. 163. Part A1, p. 1-16. DOI: 10.5750/IJME.V163IA1.1
- Nwachukwu A.N., Uwa C.U., Nwagu K.E., Ephraim B.E. Determination of Volatile Organic Compounds at a Marine Terminal in United States Using in-Borehole Gas Monitoring. Journal of Marine Science and Technology. 2020. Vol. 28. N 3, p. 219-228. DOI: 10.6119/JMST.202006_28(3).0007
- Tamaddoni M., Sotudeh-Gharebagh R., Nario S. et al. Experimental study of the VOC emitted from crude oil tankers. Process Safety and Environmental Protection. 2014. Vol. 92. Iss. 6, p. 929-937. DOI: 10.1016/j.psep.2013.10.005
- Guilin Hu, Butler J., Littlejohns J. et al. Simulation of cargo VOC emissions from petroleum tankers in transit in Canadian waters. Engineering Applications of Computational Fluid Mechanics. 2020. Vol. 14. Iss. 1, p. 522-533. DOI: 10.1080/19942060.2020.1728386
- Poornan P.D., Ali Hasan Ali Abdulla Al Hindi. Takreer's Approach to Minimize Environmental Emissions by Vapor Recovery During Gasoline and Naphtha Ship Loading. Abu Dhabi International Petroleum Exhibition and Conference, 7-10 November 2016, Abu Dhabi, UAE. OnePetro, 2016. SPE-183323-MS. DOI: 10.2118/183323-MS
- Salomone S. Reducing Emissions from Oil & Gas Facilities by Use of Field Proven VOC Technology. SPE Asia Pacific Oil and Gas Conference and Exhibition, 25-27 October 2016, Perth, Australia. 2016. OnePetro, 2016. SPE-182204-MS. DOI: 10.2118/182204-MS
- Litvinenko V.S., Dvoynikov M.V., Trushko V.L. Elaboration of a conceptual solution for the development of the Arctic shelf from seasonally flooded coastal areas. International Journal of Mining Science and Technology. 2021. Vol. 32. Iss. 1, p. 113-119. DOI: 1016/j.ijmst.2021.09.010
- Shammazov A.M., Aminev A.N., Pirogov A.N. et al. Solving problems of reconstruction and development optimization of a pipeline system. Oil Industry. Iss. 8, p. 80-83 (in Russian). DOI: 10.24887/0028-2448-2018-8-80-8
- Hao Xu, Xiafan Xu, Liubiao Chen et al. A novel cryogenic condensation system combined with gas turbine with low carbon emission for volatile compounds recovery. Energy. 2022. Vol. 248. N 123604. DOI: 1016/j.energy.2022.123604
- Pshenin V.V., Korshak A.A., Gaisin M.T. Method of structural minimization of the average risk for identification of mass transfer of evaporating oil at tanker loading. Oil Industry. N 10, p. 108-111 (in Russian). DOI: 10.24887/0028-2448-2019-10-108-111
- Zemenkova M.Y., Chizhevskaya E.L., Zemenkov Y.D. Intelligent monitoring of the condition of hydrocarbon pipeline transport facilities using neural network technologies. Journal of Mining Institute. 258, p. 933-944. DOI: 10.31897/PMI.2022.105
- Sangick Lee, Inhwan Choi, Daejun Chang. Multi-objective optimization of VOC recovery and reuse in crude oil loading. Applied Energy. 2013. Vol. 108, p. 439-447. DOI: 1016/j.apenergy.2013.03.064
- Rogachev M.K., Aleksandrov A.N. Justification of a comprehensive technology for preventing the formation of asphalt-resin-paraffin deposits during the production of highlyparaffinic oil by electric submersible pumps from multiformation deposits. Journal of Mining Institute. Vol. 250, p. 596-605. DOI: 10.31897/PMI.2021.4.13
- Rajabi H., Mosleh M.H., Mandal P. et al. Emissions of volatile organic compounds from crude oil processing – Global emission inventory and environmental release. Science of the Total Environment. 2020. Vol. 727. N 138654. DOI: 1016/j.scitotenv.2020.138654
- Shammazov I., Dzhemilev E., Sidorkin D. Improving the Method of Replacing the Defective Sections of Main Oil and Gas Pipelines Using Laser Scanning Data. Applied Sciences. 2023. Vol. 13. Iss. 1, p. 48-75. DOI: 10.3390/app13010048
- Ilinova А.А., Chanysheva A.F. Algorithm for assessing the prospects of offshore oil and gas projects in the Arctic. Energy Reports. 2020. Vol. 6. N 2, p. 504-509. DOI: 10.1016/j.egyr.2019.11.110
- Yungmeister D.A., Lavrenko S.A., Yacheikin A.I., Urazbakhtin R.Y. Improving the shield machine cutter head for tunneling under the conditions of the Metrostroy Saint Petersburg mines. ARPN Journal of Engineering and Applied Sciences. 2020. Vol. 15. N 11, p. 1282-1288.
- Mayet A.M., Alizadeh S.M., Nurgalieva K.S. et al. Extraction of Time-Domain Characteristics and Selection of Effective Features Using Correlation Analysis to Increase the Accuracy of Petroleum Fluid Monitoring Systems. Energies. Vol. 15. Iss. 6. N 1986. DOI: 10.3390/en15061986
- Aleksandrova T.N., Potemkin V.A. Development of a methodology to assess the hydrocyclone process with account of the rheological properties of the mineral slurry. Journal of Mining Institute. Vol. 252, p. 908-916. DOI: 10.31897/PMI.2021.6.12
- Yoo Youl Choi, Seok Hee Lee, Jae-Cheul Park et al. The impact of corrosion on marine vapour recovery systems by VOC generated from ships. International Journal of Naval Architecture and Ocean Engineering. 2019. Vol. 11. Iss. 1, p. 52-58. DOI: 10.1016/j.ijnaoe.2018.01.002
- Bayirhan İ., Mersin K., Tokuşlu A., Gazioğlu C. Modelling of Ship Originated Exhaust Gas Emissions in the Strait of Istanbul (Bosphorus). International Journal of Environment and Geoinformatics. 2019. Vol. 6. Iss. 3, p. 238-243. DOI: 10.30897/ijegeo.641397
- Alver F., Saraç B.A., Şahin U.A. Estimating of shipping emissions in the Samsun Port from 2010 to 2015. Atmospheric Pollution Research. 2018. Vol. 9. Iss. 5, p. 822-828. DOI: 1016/j.apr.2018.02.003
- Litvinenko V.S., Bowbrick I., Naumov I.A., Zaitseva Z. Global guidelines and requirements for professional competencies of natural resource extraction engineers: Implications for ESG principles and sustainable development goals. Journal of Cleaner Production. 2022. Vol. 338. N 130530. DOI: 1016/j.jclepro.2022.130530
- Pashkevich M.A., Bykova M.V. Methodology for thermal desorption treatment of local soil pollution by oil products at the facilities of the mineral resource industry. Journal of Mining Institute. Vol. 253, p. 49-60. DOI: 10.31897/PMI.2022.66
- Gobbi G.P., Liberto L.D., Barnaba F. Impact of port emissions on EU-regulated and non-regulated air quality indicators: the case of Civitavecchia (Italy). Science of the Total Environment. 2020. Vol. 719. N 134984. DOI: 10.1016/j.scitotenv.2019.134984
- Tokuşlu A., Burak S. Examination of Exhaust Gas Emissions of Transit Ships in the Istanbul Strait. Academic Platform Journal of Engineering and Science. 2021. Vol. 9. Iss. 1, p. 59-66. DOI: 10.21541/apjes.705918
- Mihajlović M., Jovanović M., Pešić R.V. Volatile organic compounds (VOC) policy innovation in petrochemicals river barge transportation. Journal of Cleaner Production. 2016. Vol. 112. Part 2, p. 1559-1567. DOI: 10.1016/j.jclepro.2015.04.080
- Rahman M.M., Canter C., Kumar A.Well-to-wheel life cycle assessment of transportation fuels derived from different North American conventional crudes. Applied Energy. 2015. Vol. 156, p. 159-173. DOI: 10.1016/j.apenergy.2015.07.004
- Barykin S.E., Smirnova E.A., Chzhao D. et al. Digital echelons and interfaces within value chains: End-to-end marketing and logistics integration. Sustainability. 2021. Vol. 13. Iss. 24. N 13929. DOI: 10.3390/su132413929