Development of technological solutions for reliable killing of wells by temporarily blocking a productive formation under ALRP conditions (on the example of the Cenomanian gas deposits)
Abstract
Modern field operation conditions are characterized by a decline in gas production due to the depletion of its reserves, a decrease in reservoir pressure, an increase in water cut, as well as due to the depreciation of the operating well stock. These problems are especially specific at the late stage of development of the Cenomanian deposits of Western Siberia fields, where the anomaly factor below 0.2 prevails, while gas-bearing formations are represented mainly by complex reservoirs with high-permeability areas. When killing such wells, the classical reduction of overbalance by reducing the density of the process fluid does not provide the necessary efficiency, which requires the search for new technical and technological solutions. In order to prevent the destruction of the reservoir and preserve its reservoir properties during repair work in wells with abnormally low reservoir pressure, AO “SevKavNIPIgaz” developed compositions of special process fluids. A quantitative description of the process of blocking the bottomhole formation zone is proposed by means of mathematical modeling of injection of a gel-forming solution into a productive horizon. The well killing technology includes three main stages of work: leveling the injectivity profile of the productive strata using three-phase foam, pumping the blocking composition and its displacement with the creation of a calculated repression. Solutions obtained on the basis of a mathematical model allow optimizing technological parameters to minimize negative consequences in the well killing process.
Introduction
The problems of well killing during repair work are most acute in gas fields that are at the final stage of operation, and are most relevant at present in the wells of the Cenomanian deposits of fields in Western Siberia. Gas deposits at such fields as Yamburgskoye, Urengoyskoye, Medvezhye, etc. have a similar geological structure and are confined to a single gas-producing horizon [1-3], which allows us to speak about the need to consider the Cenomanian gas-producing horizon as a single operational facility in order to use and disseminate the already identified patterns and features of its development. With a comparative homogeneity of the lithological composition of rocks, their reservoir properties vary over a very wide range. Taking into account drainage and the presence of highly permeable areas, gas-bearing formations can be attributed to complex reservoirs characterized by the presence of expanded pores and channels, cracks, karst cavities, etc.
Analysis of field data on workover of wells of gas and gas condensate fields in Western Siberia [4, 5] shows that the conventional killing fluids used (solutions of calcium chloride and sodium, hydrophobic emulsions, invert-micellar dispersions, etc.) become ineffective in the initial period of field development when reservoir pressures drop [6, 7]. The high infiltration of these solutions under repression conditions contributes to the formation of a significant zone of their penetration into the formation, which sharply worsens the filtration characteristics of the formation and creates a number of intractable problems in the development of wells after workover. From a of open sources [8-10] review it follows that the methods for controlling hydrodynamic processes in the bottomhole zone of a well during well workover (WO) are very limited.
In this regard, the development of technological solutions for reliable killing of wells using the mathematical modeling methods [11] of the injection of special compositions into the reservoir during repair work in wells with abnormally low reservoir pressure (ALRP) with an anomaly coefficient kan less than 0.2, preventing the destruction of the reservoir and ensuring the preservation of porosity and permeability properties (RP), is an urgent task.
To minimize the negative consequences when working in wells with a low anomaly coefficient, the technologies used for killing should conceptually meet the following conditions:
- prevention liquids absorption by the reservoir during operations, as well as during the blocking screen formation in the reservoir;
- reduction of repressive impact on the formation during well workover;
- use of process fluids, which can be removed with minimal drawdowns;
- implementation of the principle of control of hydrodynamic processes in the bottomhole formation zone (BFZ);
- alignment of the injectivity profile of formations containing highly drained zones (interlayers) [12, 13].
Methodology
Following the general provisions of scientific research methodology, scientific research included theoretical (analysis of scientific and technical literature and physical and chemical processes operating in the systems under study) and empirical research. Laboratory and bench tests to determine the effect of various types of fluids on the change in the natural permeability of the rock were carried out at the UIPC-1M unit using cores from the Cenomanian horizons of Western Siberia fields. In the future, the authors plan to conduct research on an axisymmetric loading unit with the possibility of creating reservoir pore pressure and temperature to increase the reliability of the results obtained.
The effect of liquids on reservoir properties of formations is characterized by the kerosene permeability recovery factor, which was calculated by the formula:
where k1, k2 – initial and restored kerosene permeability of the sample, respectively, m2.
The permeability of the cores was determined in accordance with Darcy's law. The blocking process construction mathematical model was carried out using a three-stage work scheme, including the alignment of the injectivity profile of the productive strata; blocking composition injection; pushing the blocking composition with the creation of the necessary repressure.
The presence of injectivity profile alignment is due to the low energy potential of productive formations with ALRP, the need to prevent contamination by the components of the blocking compositions of the well reservoir that occurs during the formation of the blocking screen in the bottomhole zone, and also as a result of the absorption of significant volumes of the blocking composition by high-permeability interlayers [14].
When working on gas and gas condensate wells in conditions with an anomaly coefficient of less than 0.2 the optimum is the use of three-phase foams as a liquid to equalize the injectivity profile.
Since the hydrostatic pressure of the liquid column does not depend on the area and shape of its cross section, from the point of view of calculating the pressures and related parameters, the simulation was carried out on the example of a more complex research object – wells equipped with packers, with subsequent extrapolation to structurally simpler objects.
A three-stage blocking scheme for the BFZ is shown in Fig.1. The well is equipped with a packer 3, after tying the equipment to the wellhead, the pipe space 1 is opened and liquid 2 (foam) is pumped through the tubing to equalize the injectivity profile in the volume necessary to fill the sub-packer zone 4 (Fig.1, а).
Denote by the function Q1(t) kill fluid reservoir injectivity caused by repression Pinj1(t) – Prp, где Pinj1(t) = f(t) – injection pressure; Prp – reservoir pressure.
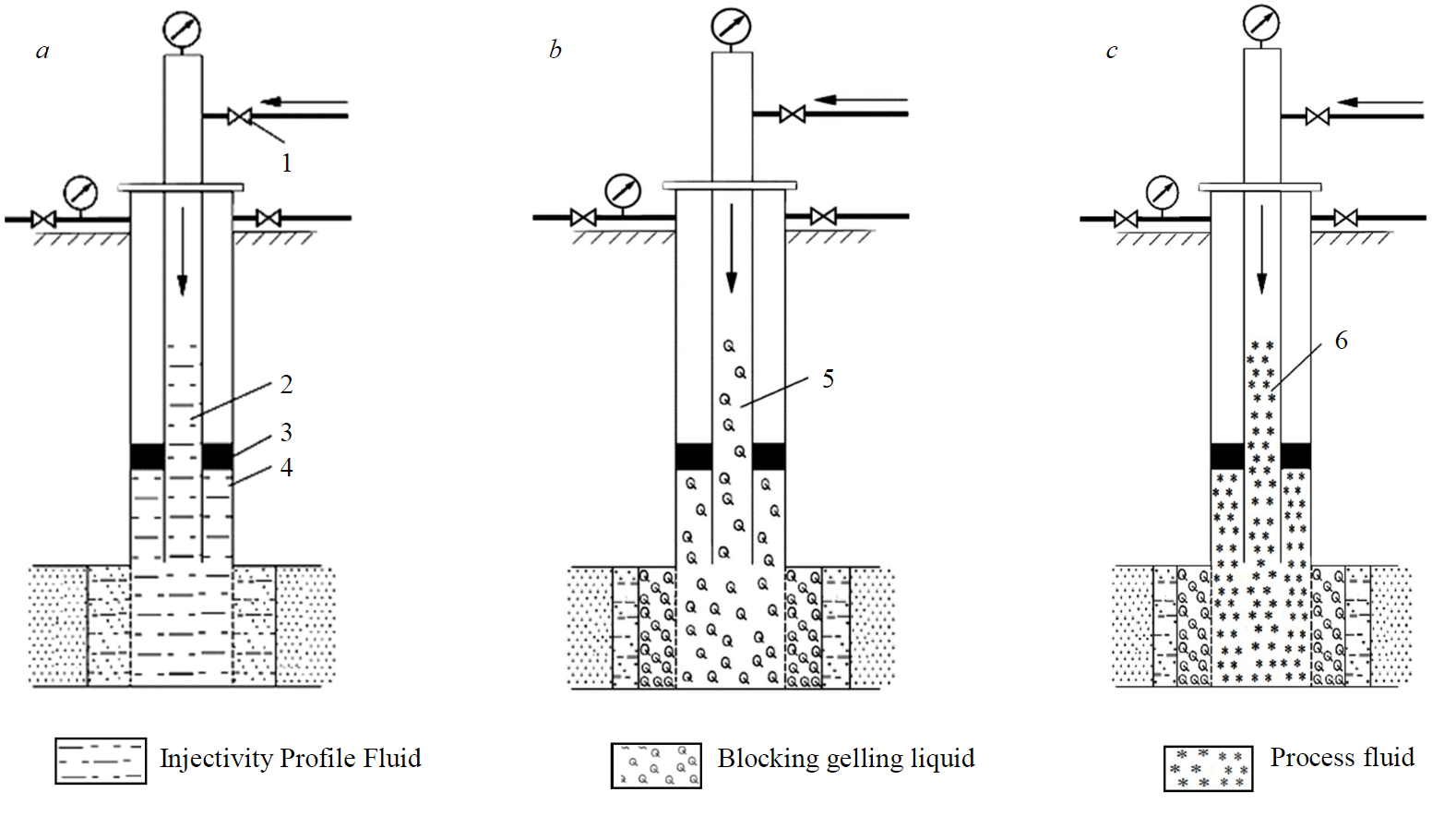
Fig.1. Stages of temporary blocking of a gas well equipped according to the packer scheme: a – the first; b – second; c – third
If the filtration of the killing fluid into the formation obeys the linear Darcy law, then the injectivity Q1(t) at the time point t can be calculated using the Dupuis formula:
where r1(t) – current radius of the “gas – liquid” interface at the first stage of the first well killing fluid injection, m; µ1(t) – fluid dynamic viscosity coefficient, mPa∙s; Rwell – well bottom radius, m; k – reservoir permeability, mD; h – seam thickness, m.
The fluid flowing at the rate Q1(t) into the near-wellbore zone leads to an increase in the clogging radius of the BFZ. Based on this and taking into account the constancy of reservoir pressure, minimization of the radius r(T) of the contaminated zone (colmatation zone) for a given time, so
where din.tub – tubing inner diameter, m; ρliq – foam liquid density, kg/m3; m – formation porosity; Sin.sat – residual water saturation of the reservoir.
A blocking gel-forming liquid 5 is pumped through the tubing string, after which it is forced to the bottom of the well with process liquid 6 in the volume necessary to create the calculated hydrostatic pressure on the formation in the under-packer zone (Fig.1, b, c).
To describe the processes occurring in the system during the second stage of well blocking, we will also use the Dupuis formula, which shows the volume of injected gel-like liquid per unit of time into the wellbore zone at the second stage:
where r2(t) – inner boundary “liquid – liquid” radius, due to the incompressible gel-like liquid entering the near-wellbore zone, m; Pinj2(t) – gel-forming liquid injection pressure, MPa ; P1, 2(t) – pressure at the moving interface between two liquid phases, MPa; μ2(t) – gel-forming liquid dynamic viscosity coefficient, mPa∙s.
The gel-like liquid entering the near-wellbore zone, like a piston, begins to move the previously injected foamy liquid deep into the bottomhole zone. In accordance with the Dupuis formula, we obtain the volumetric velocity of the foamy liquid
Based on these expressions, and taking into account the regularities obtained during the first stage of blocking the reservoir, the following equations were obtained that describe the system under consideration
where qliq2(t) – gel-like well killing fluid delivery to the well tubing rate, m3/s; ρliq2 – gel-like liquid density, kg/m3; V1 – foamy liquid injected at the first stage volume, m 3.
Nonlinear differential equation (10) is integrated by numerical methods. For example, the Runge – Kutta, Adams – Bashfort methods or the implicit multi-step Adams – Multon method together with the obvious initial condition r2(0) = Rwell.
After the gel-forming liquid 5 has been squeezed, the well is closed for technological sludge with periodic bleeding of the gas cap from the tubing to the flare line. The completion of the operation of blocking the productive formation is determined by the pressure at the wellhead (Fig.1, c).
At each stage, a kill fluid with a given dynamic viscosity and density is selected, and the injection pressure Pinj1(t) is controlled. In order to control the pumping pressure, it is necessary to calculate the rate of kill fluid supply to the tubing of the well vliq(t) (Fig.2).
Thus, in relation to each stage, the essence of the problem was to find such a control of the rate of supply of the killing fluid to the well tubing vliq(t), which provides for a given time of killing the well, the minimum radii of the near-wellbore zone of colmatation [15, 16].
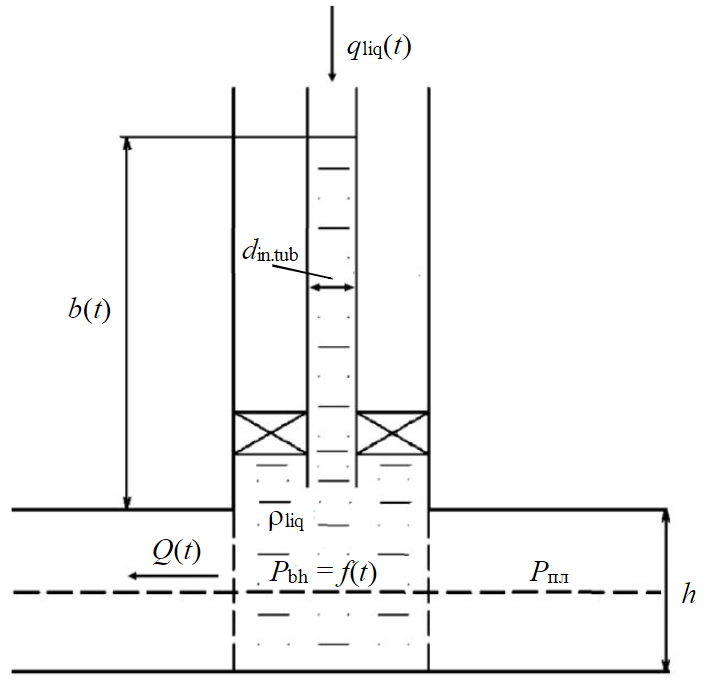
Fig.2. Relationship of injection pressure with the height of the killing liquid column in the tubing and the bottom of the well b(t) – height of the killing fluid column in the tubing
Discussion
Cenomanian reservoirs are weakly cemented and have low resistance to mechanical stress [17]. This is due to the fact that the role of the cementing material between the grains in them is carried out by clay fractions capable of dispersion when exposed to liquids. Capillary forces also have a significant effect on the collector [16-18]. Their occurrence is due to the formation of pendular rings surrounding the contact points of adjacent grains of sand. With an increase in water saturation of the pores, the size and shape of the pendular rings increase, respectively, the capillary attraction force of adjacent sand grains weakens, and under conditions of a sufficiently high water saturation, it may disappear altogether [19-21]. This phenomenon can be observed when the filtrates of process fluids penetrate into the reservoir and, in combination with the dispersion of the cementing clay material, leads to degradation of the well reservoir.
For wells where kan < 0.2, characteristic is the collapse of conductive channels during significant repressions, which is the result of reservoir instability and leads to an irreversible radical deterioration of reservoir properties in the near-wellbore zone.
In addition, the pressure gradient magnitude, as well as its distribution on the walls of the well and, accordingly, the fluid filtration rate, have a significant impact on the destruction of the reservoir frame. Carrying out work on killing and development of wells in a “sparing” mode, i.e. with close to minimum, allowable repressions and drawdowns, taking into account the principles of controlling hydrodynamic processes in the bottomhole zone, is a priority for weakly cemented reservoirs, as it ensures the integrity of their framework [22]. At the same time, the implementation of such an approach is often not feasible, since the blocking compositions used during well killing are not capable of complete removal from the bottomhole zone at low drawdowns. [23-25].
Thus, it is possible to single out the main technological factors that have a negative impact on the efficiency of killing gas wells in Cenomanian reservoirs deposits:
- use of well killing fluids with a density close to that of water or higher, which creates favorable conditions for its absorption;
- use of emulsion solutions or chemically modified hydrocarbon liquids as well killing fluids and blocking fluids, capable of forming stable hydrophobic films on the walls of pore channels with a hydrophilic nature of the surface, which leads to a complication of their geometry and a decrease in effective diameter;
- blocking of formations with blocking fluids that are not subject to destruction, as well as containing solid-phase clogging particles that are not immobilized in terms of liquid volume, which leads to significant contamination of the formation in the process of creating a blocking screen in the bottomhole zone;
- insufficient efficiency of formation blocking as a whole or its separate intervals as a result of significant absorption of the blocking fluid by highly permeable interlayers during the work;
- injection of a blocking fluid with a pressure corresponding to the average data for the reservoir without taking into account the individual characteristics of its individual interlayers.
Analysis of geological and technical conditions for the operation of gas wells in complicated conditions ALRP [26, 27], as well as with the presence of natural and man-made cracks showed that the process fluids used in practice [28-30] significantly worsen reservoir properties of productive formations, which, in turn, leads to a number of problems that are difficult to solve during workover [31]. In this regard, it is necessary to substantiate additional requirements for process fluids for temporary blocking of the bottomhole zone, due to work in the well with kan < 0.2:
- the blocking screen must have a polymer base and not contain chemical reagents that form layers of high-energy chemical bonds with the rock surface;
- to penetrate into the formation pore channels (without losing commonality with the rest of the blocking fluid) with tongues that perform the function of polymeric plugging plugs that have the ability to elastically change the geometric shape with an increase in repression;
- contain reinforcing components firmly bonded to the polymer base of the blocking screen, providing an increase in its mechanical characteristics with minimal impact on the pore space of the collector;
- have an effective destructor that ensures the complete removal of the components of the blocking composition from the productive strata;
- structure-forming components of the blocking composition should self-destruct in reservoir conditions, the time of self-destruction should be at least one and a half times the period of the predicted duration of the repair work;
- increase the efficiency of repair work due to a high level of manufacturability, namely: the ability to control rheological and filtration properties; maintaining the hydraulic conductivity of the bottomhole zone; increasing the reliability and manufacturability of the work carried out under conditions of repression on the reservoir, one and a half to two times higher than reservoir pressures.
Table 1
Results of studies to determine the effect of various fluids types on permeability core samples from Western Siberia fields
Process fluid |
Core material of the Cenomanian horizon |
The filtration experiment result |
||
Initial phase permeability for kerosene k1, 10–3 micron2 |
Final phase permeability for kerosene k2, 10–3 micron2 |
Permeability recovery factor krec, % |
||
water-methanol solution |
Yamburgskoye OGCF |
336 |
303 |
90.3 |
106 |
92 |
87.1 |
||
43 |
37 |
87.2 |
||
3.37 |
3.19 |
94.6 |
||
Invert emulsion solution |
357 |
15 |
4.3 |
|
286 |
51 |
17.9 |
||
97 |
63 |
65.2 |
||
8.61 |
2.77 |
32.2 |
||
Water-methanol solution, invert emulsion solution * |
306 |
1.88 |
0.6 |
|
241 |
1.89 |
0.8 |
||
47 |
0.76 |
1.6 |
||
4.40 |
0.31 |
7.2 |
||
Invert emulsion solution based on vegetable oils |
Urengoy OGCF |
222 |
76 |
34.2 |
169 |
41 |
24.3 |
||
183 |
40 |
21.9 |
||
232 |
83 |
35.8 |
||
210 |
35 |
16.7 |
||
566 |
244 |
43.1 |
||
Zapolyarnoye OGCF |
1578 |
251 |
15.9 |
|
Yubileinoye OGCF |
404 |
156 |
38.6 |
|
310 |
91 |
29.4 |
||
328 |
109 |
33.2 |
||
390 |
77 |
19.7 |
||
592 |
185 |
31.3 |
||
Vyngapurovskoye OGCF |
261 |
51 |
19.5 |
|
465 |
117 |
25.2 |
||
41 |
11 |
26.8 |
||
Polymer-salt based solution potassium chloride |
Yubileinoye OGCF |
308 |
167 |
54.2 |
367 |
162 |
44.1 |
||
359 |
148 |
41.2 |
||
Vyngapurovskoe OGCF |
86 |
41 |
47.1 |
|
94 |
48 |
50.7 |
||
* Solutions were injected sequentially.
The described recommendations are formulated on the basis of an analysis of scientific, technical and field materials, as well as experimental studies by specialists of AO “SevKav-NIPIgaz” to determine the effect of various types of liquids on the permeability of core samples from Western Siberia fields (Table 1). Water-based gel-forming viscoelastic systems (VVS) make it possible to realize the advantages of suspension and single-phase VVS:
- high strength and low water permeability of the blocking screen due to significant mechanical properties of solid phase particles and gel structure;
- small depth of penetration of the composition and its individual components into the formation;
- lack of free water, which prevents complications caused by swelling of the clay material of the reservoir;
- the ability to qualitatively block formations with a permeability of more than 0.5 D and/or containing highly drained interlayers;
- inability to form film structures on the inner surface of the pores of the collector due to the high strength of the binding of the solution molecules with each other, which exceeds the adhesive interaction with the reservoir rock.
Such systems, unlike emulsion-based suspensions, are more cost-effective and have the main distinguishing feature – hydrophilicity. Unlike oil, gas (or gas aerosol in the case of gas condensate deposits) is not able to create any stable structures on the inner surface of the reservoir pores. Therefore, the nature of the wettability of the pore channels is determined by the surface properties of the minerals that make up the productive stratum.
The use of blocking compositions on an emulsion basis during repair work in such wells leads to the formation of adsorption structures on the walls of pore channels, leading to a reduction in their effective diameter.
It is important to note that this problem has two aspects. The films formed as a result of the formation treatment with hydrophobic solutions have a rather large thickness, which is due to the multilayer structure, as well as their swelling due to repulsive forces in the zone of hydrophobic-hydrophilic contact. The second aspect of the problem is related to the low continuity of film coatings formed in this way. The formation of a multilayer structure, in which each layer has a different character of wettability, is energetically very expensive. As a result, the system, including the inner surface of the collector pores and film formations, tends to reduce its energy potential. This is manifested in the thickening of individual sections of the multilayer structure with the subsequent formation of hydrophobic islands on the hydrophilic surface of the collector pores. This leads to complication of the geometry of the pore space and, in combination with low formation pressures, can significantly affect the efficiency of the development of gas and gas condensate wells after workover. These reasons significantly limit the scope of application of emulsion-based suspensions as blocking compositions for killing wells with kan < 0.2.
The proposed method for temporary blocking of the bottomhole zone is based on the use of a killing fluid, blocking and squeezing fluids that do not contain hydrophobic components, as well as other reagents capable of forming stable film coatings with formation rocks that change the type of wettability of their surface (for example, cationic surfactants, polymers, siloxanes). Moreover, a three-phase foam based on a foaming liquid containing a xanthan biopolymer, an anionic surfactant and a solid-phase stabilizer of plant origin is used as a killing fluid and a squeezing fluid. The specified three-phase foam has significant stability over time, a fairly low density, high rheological characteristics, which make it possible to level the formation injectivity profile due to the high resistance when moving in a porous medium, which partly neutralizes the negative consequences of the presence of highly permeable interlayers in the productive formation.
Parameters of foaming fluid for killing wells: density 1010-1020 kg/m3, 7-9 рН, conditional viscosity 20-25 s. Foam parameters: density 300-350 kg/m 3, multiplicity 2.5-3.0, stability 8-12 h.
As a blocking liquid, a composition based on a xanthan biopolymer, a complex of lignosulfonates, a polyvalent crosslinker, a modifying salt additive, and an organo-mineral filler was developed. The main parameters of the VVS are given in Table 2.
The operation principle of the developed composition is based on obtaining a blocking effect when it moves in the reservoir in a structured state. The blocking fluid enclosed in the pore space is a body homogeneous in composition and consistency, which has elastic properties and is integral with the filter cake formed from a polymer gel. Thus, when blocking a formation, the intra-formation part of the blocking screen is represented by plugging plugs located in each pore channel of the reservoir. They have mechanical (elasticity, brittleness, hardness), as well as chemical properties sufficient to prevent the dispersion of their material (gel structure) under external influence, which should be understood as a repressive effect in the process of repair work, and depression – when well development [32, 33].
Table 2
Parameters of the destructuring blocking composition
Technological parameter |
Blocking composition value |
|
Without filler |
With filler |
|
Blocking ability, MPa |
12.9-15.3 |
12.5-15.6 |
Permeability recovery factor, % |
93.9-95.6 |
92.5-95.3 |
Filtration index, cm3/30 min |
5-6 |
3-4 |
Conditional viscosity, s |
38-42 |
55-70 |
Density ρ, kg/m3 |
1010-1020 |
1040-1050 |
Gelation time, h |
1-1.5 |
1-1.5 |
Degree of destruction, %* |
96-98 |
90-92 |
Mechanical strength of the gel, kN/m2 |
40-50 |
* When using an alkaline destructive liquid.
The killing technology developed by AO “SevKavNIPIgaz” aimed at effective temporary blocking of the formation of gas and gas condensate wells in the conditions of ALRP, including at kan < 0.2, consists in the sequential injection of fluid to equalize the injectivity profile of the well and the blocking solution through the tubing, with subsequent pushing of the blocking solution to the bottom of the well with process fluid (three-phase foam). At the same time, the pressure of blocking solution displacement by intervals, based on the simulation results, is determined by the formula:
where µ – plastic viscosity, mPa∙s; t – fluid injection time, min.
The proposed method of mathematical modeling makes it possible to take into account the residual water cut of the interlayers, their porosity and permeability associated with the viscosity of the injected fluid in the calculation. In addition, it is extremely important that during its derivation, the “reservoir-well” system was considered not in a static mode, but in dynamics. This ensures high efficiency of blocking the reservoir as a whole and its individual interlayers with repressions, which make it possible to form a high-quality blocking screen in interlayers with different permeability, blocking the reservoir in a sparing mode.
Depending on the designs of well bottoms, various technologies are used to implement this method using the method of mathematical modeling. One of the options for temporary blocking of a gas well equipped according to the packer scheme is shown in Fig.1, 2. Upon completion of the operation of blocking the productive formation, wellhead pressure is monitored to confirm the killing of the well. In the event of a pressure drop, the blocking operation is repeated (blocking liquid and squeezing foam are pumped in succession) until the desired result is obtained.
In the case of temporary blocking of a multi-layer reservoir, where interlayers have different permeability values and different reservoir pressures, a coiled tubing unit is used to qualitatively create a temporary blocking screen.
Thanks to the proposed mathematical model, it becomes possible, when killing a well, to carry out interval-by-interval injection of a blocking fluid into a multi-layer reservoir in order to ensure a targeted impact on a specific interval of the reservoir, while calculating the injection pressures of the blocking fluid proceeds from the characteristics of a particular interlayer, taking into account its rheological properties.
Thus, the control of hydrodynamic processes during well blocking can be effectively implemented by leveling the injectivity profile of formations with highly drained interlayers under the following conditions:
- foam system with high rheological properties, low density, and also having a significant coefficient of compressibility;
- destructive blocking composition based on gel-forming VVS containing reinforcing additives capable of damping repressive loads on the formation;
- quantitative description of the blocking process by means of mathematical modeling of the blocking composition injection into the reservoir, which allows to estimate the expected parameters of the injection process mode (pressure/flow rate, duration) and make the necessary adjustments to optimize the process parameters and minimize negative consequences in the process of killing the well.
Conclusions
A technology for temporary blocking of a productive formation has been developed using mathematical modeling methods when carrying out repair work in wells with ALRP using the example of the Cenomanian gas deposits (including those with kan < 0.2) of Western Siberian fields, which increases the efficiency of well killing by ensuring the alignment of the profile capacitance of the reservoir with three-phase foam and subsequent blocking of each individual interlayer of the productive horizon with calculated repressions, while maintaining reservoir properties.
A mathematical model is proposed for injection of a blocking composition into a reservoir, which makes it possible to prevent significant absorption of process fluids during the work on killing gas and gas condensate wells under ALRP conditions, taking into account the presence of highly permeable interlayers.
The developed blocking fluid forms a polymeric plugging plug in the pore channels of the formation, consisting of oligomeric units crosslinked into a single structure and characterized by an elastic change in geometric shape with an increase in repression, it can be removed from the pore channels of the formation without destruction and dispersion of the plugging structures, which reduces degree of BFZ contamination during well development.
References
- Kustyshev D.A., Krivenets T.V., Tkachenko R.V. Features of well killing at the final stage of field development. Geologiya, geografiya i globalnaya energiya. 2010. N 3 (38), p. 103-107 (in Russian).
- Litvinenko V.S., Nikolaev N.I. Process fluids to improve the efficiency of construction and operation of oil and gas wells. Journal of Mining Institute. 2011. Vol. 194, p. 84-90 (in Russian).
- Demakhin C.A., Merkulov A.P., Kasyanov D.N. et al. Killing wells in block packs is an effective means of preserving the filtration properties of a productive formation. Neft. Gaz. Novatsii. 2015. N 1 (192), p. 66-69 (in Russian).
- Zejgman J.V., Mukhametshin V.Sh., Khafizov A.R., Kharina S.B. Prospects of Application of Multi-Functional Well Killing Fluids in Carbonate Reservoirs. SOCAR Proceedings. 2016. N 3, p. 33-39 (in Russian). DOI: 10.5510/OGP20160300286
- Iktissanov V.A. Description of steady inflow of fluid to wells with different configurations and various partial drilling-in. Journal of Mining Institute. 2020. Vol. 243, p. 305-312 (in Russian). DOI: 10.31897/PMI.2020.3.305
- Gasumov R.A., Gasumov E.R., Minchenko Yu.S. Analysis of geological features of Oxfordian section to develop a digital model for productive strata. Neftegazovaya Geologiya. Teoriya i Praktika 2021. Vol. 16. N 4, p. 1-24 (in Russian). DOI: 10.17353/2070-5379/41_2021
- Beloglazov I.I., Morenov V.A., Leusheva Е.L., Gudmestad O.T. Modeling of Heavy-Oil Flow with Regard to Their Rheolo-gical Properties. Energies. 2021. Vol. 14. Iss. 2. N 359. DOI: 10.3390/en14020359
- Livescu S., Craig S. A critical review of the coiled tubing friction-reducing technologies in extended-reach wells. Part 2: Vibratory tools and tractors. Journal of Petroleum Science and Engineering. 2018. Vol. 166, p. 44-54. DOI: 10.1016/j.petrol.2018.03.026
- Savari Sh., Whitfill D.L., Walker J. Acid-Soluble Lost Circulation Material for Use in Large, Naturally Fractured Formations and Reservoirs. SPE Middle East Oil & Gas Show and Conference, 6-9 March 2017, Manama, Kingdom of Bahrain, 2017. N SPE-183808-MS. DOI: 10.2118/183808-MS
- Taha A., Amani M. Overview of Water Shutoff Operations in Oil and Gas Wells. Chemical and Mechanical Solutions. Vol. 3 (2), p. 1-11. DOI: 10.3390/chemengineering3020051
- Rogov E.A. Study of the well near-bottomhole zone permeability during treatment by process fluids. Journal of Mining Institute. 2020. Vol. 242, p. 169-173. DOI: 10.31897/PMI.2020.2.169
- Volkov V., Turapin A., Ermilov A. et al.Experience of Gas Wells Development in Complex Carbonate Reservoirs in Different Stages of Development. SPE Russian Petroleum Technology Conference, 22-24 October 2019, Moscow. Russia Society of Petroleum Engineer, 2019. SPE-196915-MS. DOI: 10.2118/196915-MS
- Islamov S.R., Bondarenko A.V., Mardashov D.V.Substantiation of a well killing technology for fractured carbonate reservoirs. Youth Technical Sessions Proceedings: VI Youth Forum of the World Petroleum Council – Future Leaders Forum (WPF 2019), 23-28 June 2019, Saint Petersburg, Russian Federation. London: CRC Press, 2019. P. 256-264.
- Kustyshev A.V., Kustyshev I.A., Kozlov E.N. Some aspects of well killing in the fields of Eastern Siberia. Izvestiya vysshikh uchebnykh zavedeniy. Neft i gaz. 2014. N 5, p. 27-32 (in Russian).
- Islamov Sh.R., Bondarenko A.V., Korobov G.Y., Podoprigora D.G. Complex algorithm for developing effective kill fluids for oil and gas condensate reservoirs. International Journal of Civil Engineering and Technology. 2019. Vol. 10. N 1, p. 2697-2713. N IJCIET_10_01_241.
- Xinong Xie, Jiu Jimmy Jiao, Zhonghua Tang, Chunmiao Zheng. Evolution of abnormally low pressure and its implications for the hydrocarbon system in the southeast uplift zone of Songliao basin, China. AAPG Bulletin. China. 2003. Vol. 87. N 1, p. 99-119. DOI: 10.1306/080602870099
- Blinov P.A. Determining the Stability of the Borehole Walls at Drilling Intervals of Loosely Coupled Rocks Considering Zenith Angle. Journal of Mining Institute. 2019. Vol. 236, p. 172-179. DOI: 10.31897/PMI.2019.2.172
- Ulyasheva N.M., Leusheva E.L., Galishin R.N. Development of the drilling mud composition for directional wellbore drilling considering rheological parameters of the fluid. Journal of Mining Institute. 2020. Vol. 244, p. 454-461. DOI: 10.31897/PMI.2020.4.8
- Al-Anazi A., Al-Kaidar Z., Wang J. Modeling gelation time of organically crosslinked polyacrylamide gel system for conformance control applications. SPE Russian Petroleum Technology Conference, 22-24 October 2019, Moscow, Russia. 2019, p. 1-16. DOI: 10.2118/196775-MS
- Galkin V.I., Martyushev D.A., Ponomareva I.N., Chernykh I.A. Developing features of the near-bottomhole zones in productive formations at fields with high gas saturation of formation oil. Journal of Mining Institute. 2021. Vol. 249, p. 386-392. DOI: 10.31897/PMI.2021.3.7
- Nutskova M.V., Rudiaeva E.Y., Kuchin V.N., Yakovlev A.A. Investigating of compositions for lost circulation control. Youth Technical Sessions Proceedings: VI Youth Forum of the World Petroleum Council – Future Leaders Forum (WPF 2019), 23-28 June 2019, Saint Petersburg, Russian Federation. London: CRC Press, 2019. P. 394-398.
- Mikov A., Kazakova L. Shut it down gently. The use of modified killing fluids during well workover allows maintaining the reservoir properties of the bottomhole formation zone. Nefteservis. 2009. N 3, p. 52-54 (in Russian).
- Legkokonets V.A., Islamov Sh.R., Mardashov D.V.Multifactor analysis of well killing operations on oil and gas condensate field with a fractured reservoir. Proceedings of the International Forum-Contest of Young Researchers: Topical Issues of Rational Use of Mineral Resources, 18-20 April 2018, St. Petersburg, Russian Federation. London: CRC Press. Taylor & Francis Group, 2019, p. 111-118.
- Leusheva E., Morenov V., Liu T. Dependence of the Equivalent Circulation Density of Formate Drilling Fluids on the Molecular Mass of the Polymer Reagent. Energies. 2021. Vol. 14. N 22. N 7639. DOI: 10.3390/en14227639
- Shagiakhmetov A.M., Podoprigora D.G., Terleev A.V. The study of the dependence of the rheological properties of gelforming compositions on the crack opening when modeling their flow on a rotational viscometer. Periodico Tche Quimica. 2020. Vol. 17. N 34, p. 933-939.
- Nikolaev N.I., Leusheva E.L. Development of DrillIng Fluids Composition for Efficiency Increase of Hard Rocks Drilling Journal of Mining Institute. Vol. 219, p. 412-420 (in Russian). DOI: 10.18454/PMI.2016.3.412
- 27. Leusheva E., Morenov V., Tabatabaee Moradi S. Effect of Carbonate Additives on Dynamic Filtration Index of Drilling Mud. International Journal of Engineering. Transactions B: Applications. 2020. Vol. 33. Iss. 5, p. 934-939. DOI: 10.5829/IJE.2020.33.05B.26
- Jafarpour H., Moghadasi J., Khormali A. et al. Increasing the stimulation efficiency of heterogeneous carbonate reservoirs by developing a multi-bached acid system. Journal of Petroleum Science and Engineering. 2019. Vol. 172, p. 50-59. DOI: 10.1016/j.petrol.2018.09.034
- Quintero L., Ponnapati R., Felipe M.J.Cleanup of Organic and Inorganic Wellbore Deposits Using Microemulsion Formulations: Laboratory Development and Field Applications. Offshore Technology Conference, 1-4 May 2017, Houston, Texas, USA. Society of Petroleum Engineer, 2017. DOI: 10.4043/27653-MS
- Korolev M., Rogachev M., Tananykhin D. Regulation of filtration characteristics of highly watered terrigenous formations using complex chemical compositions based on surfactants. Journal of Applied Engineering Science. 2020. Vol. 18. N 1. N 671, p. 147-156. DOI: 10.5937/jaes18-24542
- Kambulov E.Yu., Myazin T.O. Issue of drilling fluids services in the context of import substitution. Oil Industry Journal. 2017. N 9, p. 76-81 (in Russian). DOI: 10.24887/0028-2448-2017-9-76-81
- Binks B.P. Modern aspects Of Emulsion Science. Cambridge: Royal Society of Chemistry, 1998, p. 430.
- Khaibullina K.S., Korobov G.Yu., Lekomtsev A.V. Development of an asphalt-resin-paraffin deposits inhibitor and substantiation of the technological parameters of its injection into the bottom-hole formation zone. Periodico Tche Quimica. 2020. Vol. 17. N 34, p. 769-781. DOI: 10.52571/PTQ.v17.n34.2020.793_P34_pgs_769_781.pdf