Влияние углекислого газа на основные геотехнические критерии качества и стоимость приготовления закладки из цементной пасты
- 1 — Ph.D. старший преподаватель Университет Намибии ▪ Orcid
- 2 — преподаватель Университет Намибии ▪ Orcid
- 3 — лаборант Университет Намибии ▪ Orcid
Аннотация
В настоящее время наблюдается глобальный рост использования цементированной пасты (цементной твердеющей закладки) при выполнении различных горных работ. Поскольку стоимость связующего портландцемента достаточно высока, необходимы решения, позволяющие сократить использование цемента без чрезмерного снижения качества цементополимерных бетонов (ЦПБ). Поскольку диоксид углерода используется в запатентованных процессах формовки песка, данное исследование основано на физико-химической способности CO2 улучшать затвердевание консолидированных неорганических материалов. Оценивались влияние диоксида углерода на одноосное сжатие (UCS) и стоимость подготовки стандартных образцов CPB (ASTM C109). Стоимость подготовки ограничивалась стоимостью портландцемента. Материалом для закладки служили хвосты из кварцевого песка с 4,5 % портландцемента в качестве связующего вещества и водоцементным отношением 7,6. Для контрольных образцов использовалась дистиллированная вода с pH 5,4, а переменное количество углекислого газа растворялось в дистиллированной воде для получения насыщенной углекислым газом воды со значениями pH 3,8; 4 и 4,2. Чем ниже pH насыщенной углекислым газом воды, тем выше концентрация CO2. Испытания UCS проводились на образцах после затвердевания в течение 3, 7, 28 и 90 дней. Наблюдалось увеличение прочности и сокращение времени затвердевания при увеличении концентрации углекислого газа. Образцы, приготовленные на насыщенной углекислым газом воде с pH 3,8, имели почти вдвое большую прочность, чем образцы, приготовленные на дистиллированной воде с pH 5,4. Это означает, что большее количество растворенного CO2 соответствует более высокой прочности ЦПБ, что подтверждается уравнениями линии тренда для графического моделирования зависимости прочности от времени затвердевания. Можно ожидать, что при включении диоксида углерода ЦПБ с гораздо меньшим количеством связующего вещества достигнет требуемого UCS. Экономия затрат равна среднему снижению расхода портландцемента в 0,61 %. При расчете на весь срок эксплуатации рудника это дает значительную экономию в миллионы долларов.
Введение
Твердеющая цементная закладка (цементополимерные бетоны – ЦПБ) – это синтетический инженерный материал, состоящий из хвостов, воды и гидравлических связующих веществ, причем хвосты составляют 65-85 % от общего веса закладки [1-3]. ЦПБ находят широкое применение в горной промышленности, например, для закладки в подземных рудников [4-6], поддержки кровли [7-9], контроля оседания поверхности [10-12] и смягчения последствий кислотного шахтного дренажа [1, 13], и в то же время служат экологически чистым методом управления хвостохранилищами, используемым на многих рудниках по всему миру [14-16], причем область его применения постоянно расширяется [17, 18].
Важнейшим геотехническим критерием качества твердеющей закладки является механическая прочность [10, 19, 20], необходимая для несущих конструкций, таких как кровля и крепление [9] в подземных рудниках, для обеспечения безопасности персонала и предотвращения разубоживания руды [5, 7, 21]. Прочность на сжатие при неограниченном сжатии затвердевшей закладки обычно определяется путем испытания на одноосное (UCS) сжатие для оценки стабильности ЦПБ из-за низкой стоимости испытания и простоты интеграции в стандартные протоколы контроля качества на подземных работах [22-24]. Перед затвердеванием ЦПБ находится в виде суспензии, что предполагает транспортировку по трубопроводам и использование шламовых насосов [25-27]. На этом этапе реологические свойства суспензии ЦПБ имеют решающее значение для своевременного и эффективного осаждения в требуемых точках [28-30]. В работах, посвященных изучению реологии суспензии ЦПБ [2, 7, 31], она характеризуется как неньютоновская жидкость [25, 27, 30], предел текучести которой зависит от массовой доли твердых частиц [32-35]. Этот предел текучести является основным препятствием, которое должна преодолеть система откачки шлама, чтобы ЦПБ текла, это делает его критическим для экономически эффективного размещения ЦПБ в горных выработках [7, 27]. В закладку могут быть добавлены водопонижающие добавки для повышения ее прокачиваемости и улучшения прочности отвержденного ЦПБ [36-38].
ЦПБ является наиболее распространенной технологией закладки в Северной Америке и в некоторых других странах из-за преимуществ перед конкурирующими технологиями [24, 38, 39]. ЦПБ производится путем однородного смешивания трех основных компонентов: хвостов, воды и связующего вещества [12, 40-42]. Связующее вещество обеспечивает твердение в ЦПБ благодаря процессу гидратации [21, 43, 44]. Основным видом связующего вещества, которое наиболее часто используется в горно-добывающей промышленности для производства ЦПБ, является портландцемент в весовых пропорциях 2-7 % из-за его доступности на рынке материалов и гибкости применения [21, 37, 45].
Однако, хотя связующие вещества существенно увеличивают механическую прочность ЦПБ [17, 20, 46], они также могут составлять значительную часть эксплуатационных расходов рудника [2, 8, 37]. Например, портландцементные вяжущие вещества составляют около 50-75 % от общей стоимости ЦПБ [8, 27, 45]. Потребление цемента в горно-добывающей промышленности только в провинции Онтарио оценивается в 5-6 % от общего объема производства портландцемента в Канаде с оценочной стоимостью 75 млн канадских дол. (CA USD) в год на создание засыпки при подземных горных работах [44].
Поскольку расход связующего вещества является наиболее дорогостоящим компонентом при приготовлении ЦПБ, существует необходимость изучения методов снижения расхода связующего вещества при приготовлении цементированной закладки [17, 18, 47]. Один из подходов заключается во включении углекислого газа в цементируемую закладку во время ее приготовления (как это делается для бетона) [48, 49]. Было замечено, что прочность бетона увеличивается в результате карбонизации, которая приводит к образованию и агрегации преципитатов внутри пор цементной матрицы. Частичное закрытие пор или пустот, так называемое рафинирование пор, улучшает прочность на сжатие цемента [48, 49]. Если подобное происходит в ЦПБ, это также может привести к увеличению его прочности на сжатие, тем самым уменьшив расход связующего вещества и связанные с этим затраты. Т.Касап и соавторы [50] рассматривали влияние pH на ЦПБ без преднамеренного изменения pH воды путем растворения CO2, но природный состав различных используемых хвостов был подобран таким образом, чтобы имелись основные и кислые образцы ЦПБ. Поэтому в данной работе основное внимание уделяется оценке влияния карбонизации на прочность на сжатие ЦПБ и потенциальной экономии затрат на его приготовление в результате сокращения использования портландцементного вяжущего.
Методология
Хвосты из кварцевого песка
Природный кварцевый песок (99,8 % по массе SiO2) был использован в качестве основного компонента закладки в руднике, что соответствует более ранним исследованиям [14, 24, 51]. Физические свойства этого песка: Gs 2,7; D10 1,9; D30 9,0; D50 22,5; D60 31,5; D90 88,9; Cu 16,2; Cc 1,3 мкм. Кремнеземный песок можно отнести к средним хвостам, содержащим около 40 % мелких частиц, диаметр которых составляет меньше 20 мкм.
Связующее вещество
Назначение вяжущего в закладке заключается в создании достаточной механической прочности для удовлетворения функций поддержки статической и динамической нагрузок. Портландцемент традиционно используется в качестве вяжущего для твердеющей цементной закладки [45]. Закладка, скрепленная портландцементом, демонстрирует повышенную прочность на сдвиг, растяжение и жесткость [52, 53]. Поэтому в данном исследовании в качестве связующего использовался портландцемент типа I (PCI) в количестве 4,5 % по массе. Химический состав PCI: MgO 2,65; CaO 62,82; SiO2 18,03; Mn2O3 4,53; Fe2O3 2,70; SO3 3,82 % по массе; его плотность составляет 3,15 г/см3.
Смешивание воды
Потребность в воде является критической при приготовлении ЦПБ. В контексте данной работы она занимает второе место (34,2 %) по доле составляющих после кремнеземистых хвостов.
Водоцементное (в/ц) отношение 7,6 (4,5 × 7,6 = 34,2 %) поддерживалось на протяжении всей подготовки образцов ЦПБ. Использовались два типа воды для смешивания: дистиллированная вода без добавления CO2 (DW) и дистиллированная вода с различным количеством CO2 (CW). В качестве растворителя и контроля использовалась чистая дистиллированная вода с pH 5,4. Затем в эту дистиллированную воду добавляли определенное количество CO2 для получения насыщенной углекислым газом воды со значениями pH 3,8; 4 и 4,2 соответственно (табл.1), причем чем выше содержание растворенного CO2, тем ниже pH и, следовательно, тем более кислая CW.
Таблица 1
Коэффициенты смешивания произведенных образцов ЦПБ
Название смеси |
Тип хвостов |
Тип переплета |
Связующее вещество, % по массе |
Соотношение в/ц |
pH |
ЦПБ-3.8 |
ST |
PCI |
4,5 |
7,6 |
3,8 |
ЦПБ-4 |
ST |
PCI |
4,5 |
7,6 |
4,0 |
ЦПБ-4.2 |
ST |
PCI |
4,5 |
7,6 |
4,2 |
ЦПБ-5.4 |
ST |
PCI |
4,5 |
7,6 |
5,4 |
Приготовление смесей ЦПБ
Образцы хвостов из кварцевого песка, цемента и предварительно обработанной воды были однородно перемешаны в двойном спиральном смесителе. 31 образец был подготовлен с фиксированным составом вяжущего 4,5 % по массе и водоцементным отношением 7,6. Полученный ЦПБ был залит в стандартные цилиндрические формы для затвердевания (Æ50 мм и H = 100 мм). Затем заполненные формы герметизировались для предотвращения испарения воды и отверждались при температуре 22 °C в течение 3, 7, 28, 90 дней. Составы различных ЦПБ, приготовленных для данного исследования, представлены в табл.2.
Таблица 2
Плотность компонентов, используемых при подготовке образцов ЦПБ
Компонент |
Значение, г/см3 |
Учредительная часть, % |
PCI |
3,15 |
4,5 |
Дистиллированная вода |
0,9900198 |
34,2 = (4,5 × 7,6) |
Карбонизированная вода |
1 |
34,2 = (4,5 × 7,6) |
Хвосты из кварцевого песка |
1,680 |
61,3 = (100 – 4,5 × 7,6) |
Методы тестирования
Испытания UCS проводились на 31 цилиндрическом образце для оценки их механической прочности через 3, 7, 28 и 90 дней затвердевания. Сначала была приложена начальная нагрузка 10 Н, после чего началось динамическое нагружение со скоростью сжатия 2,5 мм/мин до разрушения (в соответствии с ASTM C109) с использованием компрессионной машины Z050 ZwickRoell с усилием 50 кН.
Результаты и обсуждение
Влияние углекислого газа на прочность ЦПБ
На протяжении всего времени твердения 3, 7, 28 и 90 дней наблюдается увеличение прочности при снижении уровня pH в ЦПБ, особенно между прочностью ЦПБ из DW (с уровнем pH 5,4) и прочностью ЦПБ из DW (с уровнем pH 3,8) (рис.1). Эта тенденция увеличения прочности на сжатие также справедлива при уровне pH от 4 до 4,2, за исключением третьего дня, когда разница между прочностью на сжатие всех образцов не столь значительна (рис.1).
Другое исключение можно наблюдать в период затвердевания на седьмой день, когда прочность на сжатие DW ЦПБ с pH 5,4 выше, чем у CW ЦПБ с pH 4,2. Эти исключения могли быть вызваны трудностями с подготовкой высококачественных образцов ЦПБ [9, 24, 37].

Рис.1. Развитие прочности ЦПБ с CW и DW
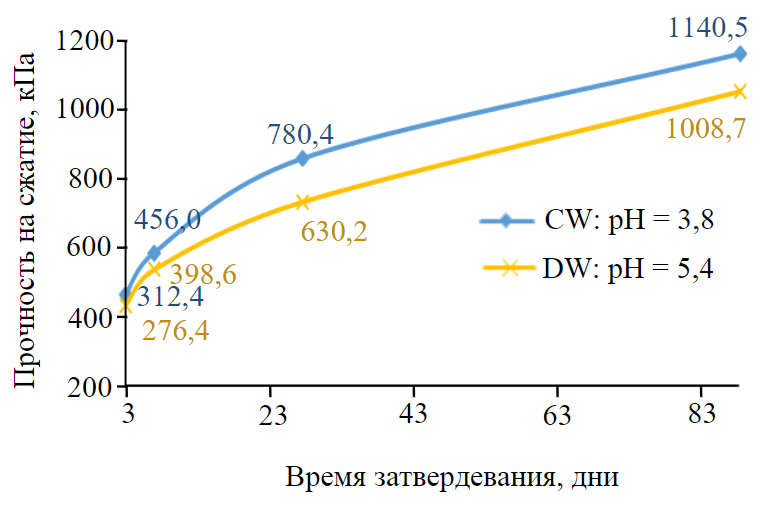
Рис.2. Развитие прочности DW ЦПБ (рН = 5,4) и CW ЦПБ (рН = 3,8)
Поскольку в течение всех изученных периодов затвердевания (дни 3, 7, 28 и 90) наблюдается значительное и явное увеличение прочности на сжатие между образцами DW (pH = 5,4) и CW (pH = 3,8), остальные обсуждения сосредоточены на этих двух особых случаях.
На рис.2 показано увеличение прочности образцов CW ЦПБ с pH 3,8 на 13 % на 3-й и 90-й дни по сравнению с образцами ЦПБ DW с pH 5,4 при одинаковой доле связующего (4,5 % по массе). Однако в другие периоды твердения наблюдается еще большее увеличение прочности.

Рис.3. Линии трендов развития прочности DW ЦПБ (pH = 5,4) по сравнению с CW ЦПБ (pH = 3,8) 1 – DW; 2 – CW; 3 – полиномиальная (DW); 4 – полиномиальная (СW)
Введение CO2 в воду на седьмой день привело к получению раствора с уровнем pH 3,8; UCS образцов ЦПБ увеличилось на 14 % по сравнению с UCS, полученным с использованием только DW (pH = 5,4). Например, на 28-й день прочность ЦПБ, изготовленного с использованием CW с pH = 3,8, достигает 780 кПа (рис.3). Добавление углекислого газа в воду для достижения минимального уровня pH 3,8 увеличивает прочность примерно на 24 %. Это почти в два раза превышает минимальную прочность (400 кПа), требуемую на руднике Матагами, подземном цинковом руднике компании Glencore провинции Квебек, Канада. Фактически прочность конструкции ЦПБ должна достигать 400 кПа через 28 дней. На рис.3 показано, что при том же времени твердения (28-й день) прочность на сжатие ЦПБ, полученного с использованием DW, составила около 630,2 кПа, что ниже, чем у ЦПБ, изготовленного с использованием CW при уровне pH 3,8, но выше промышленного требования к прочности на сжатие UCS на 28-й день твердения. Это может означать, что в условиях цинкового рудника Матагами требуемая прочность затвердевшей пасты (400 кПа) может быть достигнута раньше, чем на 28-й день твердения. Следовательно, это может способствовать повышению эффективности подземных горных выработок соседних забоев, поскольку заложенный штрек уже обеспечит безопасные условия труда шахтеров [4, 32, 38, 46]. Присутствие CO2 в водном растворе для приготовления ЦПБ привело к увеличению прочности на сжатие приблизительно на 16 %, если рассматривать среднее значение всех увеличений прочности на сжатие UCS в течение изученного времени твердения (на 3, 7, 28 и 90-й дни прочность CW ЦПБ повысилась на 13, 14, 24 и 13 % соответственно).
Углекислый газ является одним из основных парниковых газов (ПГ), образующихся в результате деятельности человека. В глобальном масштабе 78 % выбросов CO2 приходится на деятельность, связанную с производством и потреблением энергии [54-57], такую как сжигание ископаемого топлива, выплавка чугуна и стали, производство цемента. Некоторые компоненты этих выбросов разрушают атмосферный озон и создают дыры в озоновом слое [58]. Предлагаемый подход к введению этого вида ПГ в воду затворения для производства пастообразной засыпки предполагает сначала извлечение CO2 из природных месторождений (скважин) или его улавливание и хранение [59-63]. Это означает, что данный подход может стать одним из стратегических способов применения технологии закладки для сокращения выбросов парниковых газов в горно-добывающей промышленности, особенно в секторе хвостохранилищ и водопользования, поскольку он способствует улавливанию, хранению, секвестрации и утилизации CO2 [64]. Следовательно, это поможет в достижении 13-й цели Повестки дня в области устойчивого развития ООН (действия в области климата) – принятии срочных мер для борьбы с изменением климата и его последствиями.
Плотность карбонизированной воды зависит от степени газирования. Единой плотности карбонизированной воды не существует, однако, если известны исходные величины, можно легко рассчитать плотность. Для этого необходимо знать плотности углекислого газа и воды. Углекислый газ имеет плотность 0,00198 г/см3. Плотность воды составляет 1 г/см3. Уравнение для расчета плотности вещества предполагает умножение процентной концентрации одного вещества на его плотность и прибавление к процентной концентрации, умноженной на плотность другого вещества [37].
С помощью математической модели развития прочности ЦПБ, изготовленного с использованием CW с pH = 3,8 в качестве функции времени затвердевания, можно приблизительно определить день, когда затвердевшая закладка достигнет ожидаемых 400 кПа:
Решение уравнения (1), которое представляет собой функцию наилучшего соответствия, полученную с помощью Microsoft Excel при y = 400 кПа, в условиях рудника Матагами даст следующие результаты: x1 = 7,68552; x2 = 0,29005; x3 = 1,76207 дней. Среди этих значений оптимальным временем затвердевания будет 7,7 дней, в то время как два других значения могут быть отклонены, поскольку не соответствуют реальным экспериментальным данным. Это означает, что с добавлением CO2 в воду при производстве ЦПБ ожидаемая механическая прочность (400 кПа) может быть достигнута только через восемь дней вместо 28. Это эквивалентно сокращению времени затвердевания ЦПБ примерно на 71,4 %, что значительно повлияет на экономические параметры рассматриваемой горно-добывающей компании. Кроме того, улучшится график работы всего рудника, что приведет к увеличению денежного потока проекта и, следовательно, будет способствовать эффективному возврату инвестиций и сокращению срока окупаемости проекта эксплуатации:
Аналогично, если уравнение (2) решить в условиях рудника Матагами, когда y = 400 кПа, оптимальное время твердения для ЦПБ DW составит два дня, или будет сэкономлено 93 % времени твердения. Такой высокий темп увеличения прочности ЦПБ, наблюдаемый для растворов CW и DW, можно частично объяснить некоторыми физическими свойствами кремнеземистых хвостов, использованных при изготовлении смеси, особенно плотностью. Это очевидно, поскольку материал хвостов, используемых на руднике Матагами, представляет собой отходы переработки цинковой руды, которые весят меньше, чем кремнеземистые хвосты, используемые в данном исследовании. Это наблюдение подтверждает выводы, сделанные в работах [10, 43, 65], которые сообщили об увеличении прочности заклади при одинаковой пропорции вяжущего (4,5 % по массе) при увеличении плотности хвостов.
Полученные результаты свидетельствуют о значительном повышении прочности закладки при наличии CO2 в воде, предназначенной для приготовления ЦПБ, и о том, что уровень pH = 3,8 обеспечивает самую высокую прочность на сжатие.
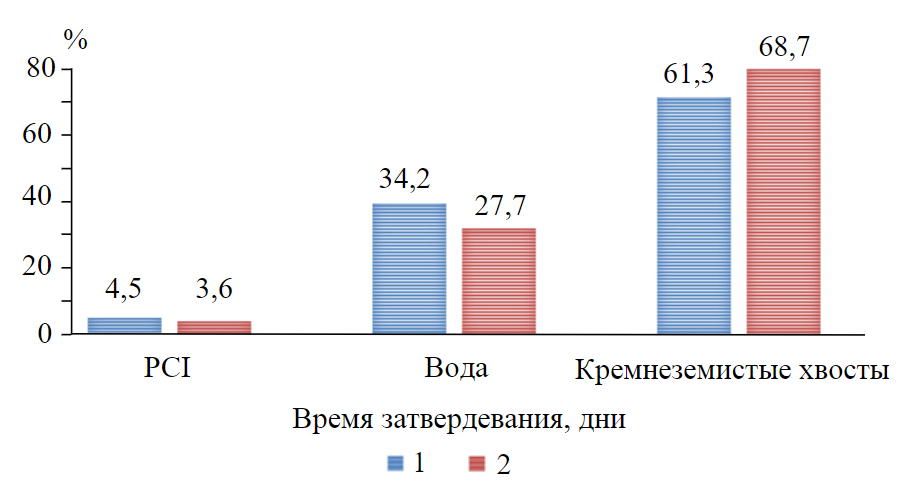
Рис.4. Сравнение порций компонентов в DW ЦПБ и CW ЦПБ, % 1 – порции составляющих DW; 2 – порции CW
Влияние двуокиси углерода на расход связующего вещества
Полученные результаты показывают, что присутствие CO2 в воде для приготовления ЦПБ приводит к значительному увеличению механической прочности этих ЦПБ, при этом рН воды 3,8 обеспечивает оптимальный уровень прочности на сжатие UCS.
Таблица 3
Экономический эффект от включения CO2 в ЦПБ, СА USD
ДДень |
Затраты на связующие компоненты ЦПБ |
Годовой экономический эффект
|
|
DW |
CW |
||
3 |
7473375 |
6626392,50 |
846982,50 |
7 |
7473375 |
6543355,00 |
930020,00 |
28 |
7473375 |
6045130,00 |
1428245,00 |
90 |
7473375 |
6626392,50 |
846982,50 |
Учитывая, что существует линейная пропорциональная зависимость между начальной долей вяжущего (4,5 %), значениями прочности образцов DW и CW при уровне pH 3,8, оптимизированные доли вяжущего можно найти путем умножения этой доли вяжущего на UCS DW и деления на UCS CW при определенном времени твердения. Результаты на 28-й день представлены на рис.4. Таким образом, вводя CO2 в воду, можно, исходя из результатов 28-го дня, сэкономить не только около 1 % вяжущих (PCI), но и около 6,5 % воды при сохранении того же водоцементного отношения (7,6). Это может способствовать достижению 14-й цели Повестки дня в области устойчивого развития ООН (жизнь ниже воды) о сохранении и разумном использовании морских ресурсов для устойчивого развития.
По результатам твердения на 3, 7, 28 и 90-й дни общая экономия, которая может быть достигнута в отношении расхода цемента при приготовлении закладки, составила 0,51; 0,56; 0,86; 0,51 % соответственно. Среднее значение этой экономии составит ~0,61 %.
Использование двуокиси углерода также оказывает значительное влияние на расход хвостов. С введением CO2 (снижением pH) увеличивается потребность в количестве хвостов, используемых в качестве основных компонентов для закладки, около 7,4 % от потребления хвостов на 28-й день твердения. Это означает, что меньшее количество остаточных отходов деятельности рудника может оставаться в окружающей среде, оказывая воздействие на экосистему. Таким образом, данный подход может эффективно способствовать подземному складированию отходов [2, 23, 26]. Следовательно, предложенный подход может также помочь в достижении 15-й цели Повестки дня в области устойчивого развития ООН (жизнь на Земле) о защите, восстановлении и устойчивом использовании наземных экосистем, устойчивом управлении лесами, борьбе с опустыниванием, остановке деградации земель, а также прекращении потери биоразнообразия.
Влияние CO2 на стоимость связующего вещества для ЦПБ
Оптимизация расхода связующего за счет концентрации углекислого газа в воде приводит к важным экономическим результатам, представленным в табл.3.
Полученные данные свидетельствуют о том, что включение углекислого газа в дистиллированную воду, используемую при смешивании и приготовлении ЦПБ, приведет к значительному повышению прочности при равном количестве вяжущего. Это означает, что возможна разработка новых оптимальных рецептов смеси закладки (снижение стоимости вяжущих) и (или) прогноз ее основного механического свойства (прочности) в зависимости от содержания углекислого газа. В результате можно сэкономить 0,51-0,86 % вяжущих веществ, используемых при приготовлении закладки, что окажет большое влияние на производительность и конкурентоспособность рудников, а также на создание рабочих мест.
Рудник, добывающий 7000 т руды в сутки, производит в среднем в сутки 3500 т ЦПБ со средним расходом вяжущего около 3,5 % (иногда 4,5 % или более). Учитывая, что средняя стоимость
Таблица 4
Изменение UCS ЦПБ в зависимости от рН, кПа
pH |
День 3 |
День 7 |
День 28 |
День 90 |
3,8 |
312,4 |
456,0 |
780,4 |
1140,5 |
4 |
298,8 |
427,6 |
685,0 |
1010,0 |
4,2 |
272,6 |
375,9 |
668,3 |
1013,4 |
5,4 |
276,4 |
398,6 |
630,2 |
1008,7 |
составляет около 1,30 СА USD за 1 % вяжущего [26],снижение расхода вяжущего на 0,51-0,86 % приведет к ежегодной экономии от 846983 СА USD (0,51 % × 3500 т × 365j) до 1428245 СА USD. Для рудника со сроком службы 20 лет общий экономический эффект от снижения стоимости цементированной закладки составит около 17 млн СА USD (в случае снижения на 0,23 %) и около 29 млн СА USD (в случае снижения на 0,86 %). Экономический эффект от включения CO2 в ЦПБ на протяжении всего срока службы рудника на 3, 7, 28, 90-й дни составит 17 млн СА USD, 19 млн СА USD, 29 млн СА USD, 17 млн СА USD соответственно.
Уравнения линии тренда UCS ЦПБ в зависимости от рН
С помощью программы Microsoft Excel было определено, что наилучшие функции развития прочности DW ЦПБ (pH = 5,4) и CW ЦПБ (pH = 3,8) в зависимости от времени твердения образцов представляют собой уравнение третьей степени (см. рис.3). Прочность затвердевшей засыпки y повышается с увеличением времени твердения x.
Аналогично были определены математические модели изменения прочности на сжатие в зависимости от уровня pH в растворах CW, которые также приближаются к полиноминальным уравнениям третьей степени. Однако с уменьшением уровня концентрации pH в воде прочность на сжатие затвердевшей закладки увеличивается, R2 = 1 (табл.4):
Выводы
Включение диоксида углерода в воду для приготовления образцов ЦПБ из кремнеземистых хвостов снижает уровень pH, как и ожидалось, из-за кислотной природы CO2, но увеличивает конечную прочность на сжатие UCS ЦПБ на 13 %, при этом сокращая время затвердевания более чем на 70 %. Также снижается расход портландцементного вяжущего приблизительно на 0,51-0,86 % и уменьшаются затраты на приготовление ЦПБ на те же процентные пункты.
Функции наилучшего соответствия развития прочности DW ЦПБ (pH = 5,4) и CW ЦПБ (pH = 3,8) в зависимости от продолжительности твердения образцов представляют собой уравнения третьей степени, а линии тренда имеют схожие показатели, что указывает на одинаковый механизм твердения образцов ЦПБ для обоих вариантов испытаний. Единственное различие заключается в величине коэффициентов, что объясняет более высокие значения прочности на сжатие UCS для образцов CW ЦПБ. Это повышение прочности связано с карбонизацией в результате реакций между углекислым газом, водой и портландцементом, в результате чего образуются мелкодисперсные соединения, которые соединяются внутри пустот в матрице ЦПБ. Это увеличивает эффективную площадь поперечного сечения образцов CW ЦПБ для восприятия сжимающей нагрузки, отсюда и более высокие показатели прочности на сжатие UCS.
Поскольку CO2 является наиболее важным ПГ, его использование для подготовки ЦПБ является стратегическим способом снижения углеродного следа горно-добывающей промышленности, особенно в секторе хвостохранилищ и управления водными ресурсами, поскольку способствует улавливанию, хранению, секвестированию и утилизации CO2. Следовательно, в случае коммерциализации он может внести вклад в достижение 13-й цели Повестки дня в области устойчивого развития ООН (Действия в области климата), которая рекомендует принять срочные меры для борьбы с изменением климата и его последствиями. Этот вклад в смягчение последствий изменения климата фактически является двойным, поскольку потребуется меньше вяжущего для портландцемента, что снизит выбросы парниковых газов от цементного производства.
Таким образом, CO2 в ЦПБ может стать для горно-добывающей промышленности и производства портландцемента одним из путей к достижению нулевых выбросов ПГ к 2050 г.
Дальнейшие исследования ЦПБ могут быть направлены на изучение влияния различных объемов цементного вяжущего на реологические и механические свойства закладки, а также на учет затрат на производство, улавливание, хранение, транспортировку и включение углекислого газа в смесь для производства закладки в экономическом анализе.
Химический состав хвостов обогатительной фабрики влияет на водопотребление и потребность в цементе для ЦПБ, а также на реологические и механические свойства. Это требует проведения дополнительных исследований для различных видов хвостов, используемых для приготовления закладки.
Литература
- Benzaazoua M., Fall M., Belem T. A contribution to understanding the hardening process of cemented pastefill // Minerals Engineering. 2004. Vol. 17. Iss. 2. P. 141-152. DOI: 10.1016/j.mineng.2003.10.022
- Fall M., Benzaazoua M., Saa E.G. Mix proportioning of underground cemented tailings backfill // Tunnelling and Underground Space Technology. 2008. Vol. 23. Iss. 1. P. 80-90. DOI: 10.1016/j.tust.2006.08.005
- Yilmaz E., Belem T., Bussière B. et al. Curing time effect on consolidation behaviour of cemented paste backfill containing different cement types and contents // Construction and Building Materials. 2015. Vol. 75. P. 99-111. DOI: 10.1016/j.conbuildmat.2014.11.008
- Emad M.Z., Mitri H., Kelly C. State-of-the-art review of backfill practices for sublevel stoping system // International Journal of Mining, Reclamation and Environment. 2015. Vol. 29. Iss. 6. P. 544-556. DOI: 10.1080/17480930.2014.889363
- Helinski M., Fahey M., Fourie A. Behavior of Cemented Paste Backfill in Two Mine Stopes: Measurements and Modeling // Journal of Geotechnical and Geoenvironmental Engineering. 2010. Vol. 137. № 2. P. 171-182. DOI: 10.1061/(ASCE)GT.1943-5606.0000418
- Thompson B.D., Bawden W.F., Grabinsky M.W. In situ measurements of cemented paste backfill at the Cayeli mine // Canadian Geotechnical Journal. 2012. Vol. 49. № 7. P. 755-772. DOI: 10.1139/t2012-040
- 7. Belem T., Benzaazoua M. Design and Application of Underground Mine Paste Backfill Technology // Geotechnical and Geological Engineering. 2008. Vol. 26. Iss. 2. P. 147-174. DOI: 10.1007/s10706-007-9154-3
- Fall M., Pokharel M. Coupled effects of sulphate and temperature on the strength development of cemented tailings backfills: Portland cement-paste backfill // Cement & Concrete Composites. 2010. Vol. 32. Iss. 10. P. 819-828. DOI: 10.1016/j.cemconcomp.2010.08.002
- Minefill 2020-2021: Proceedings of the 13th International Symposium on Mining with Backfill, 25-28 May 2021, Katowice, Poland / Ed. by F.Hassani, J.Palarski, V.Sokoła-Szewioła, G.Strozik. London: CRC Press, 2021. 450 p. DOI: 10.1201/9781003205906
- 10. Gaili Xue, Erol Yilmaz, Weidong Song, Shuai Cao. Compressive Strength Characteristics of Cemented Tailings Backfill with Alkali-Activated Slag // Applied Sciences. 2018. Vol. 8. Iss. 9. № 1537. DOI: 10.3390/app8091537
- 11. Qiu-song Chen, Qin-li Zhang, Fourie A. et al. Experimental investigation on the strength characteristics of cement paste backfill in a similar stope model and its mechanism // Construction and Building Materials. 2017. Vol. 154. P. 34-43. DOI: 10.1016/j.conbuildmat.2017.07.142
- Lei Yang, Jingping Qiu, Haiqiang Jiang et al. Use of Cemented Super-Fine Unclassified Tailings Backfill for Control of Subsidence // Minerals. 2017. Vol. 7. Iss. 11. № 216. DOI: 10.3390/min7110216
- Benzaazoua M., Marion P., Picquet I., Bussière B. The use of pastefill as a solidification and stabilization process for the control of acid mine drainage // Minerals Engineering. 2004. Vol. 17. Iss. 2. P. 233-243. DOI: 10.1016/j.mineng.2003.10.027
- Chen Hou, Liujun Yang, Lei Li, Baoxu Yan. Mechanical Characteristics and Stress Evolution of Cemented Paste Backfill: Effect of Curing Time, Solid Content, and Binder Content // Frontiers in Materials. 2022. Vol. 8. P. 1-10. DOI: 10.3389/fmats.2021.812402
- 15. Saedi A., Jamshidi-Zanjani A., Darban A.K. A review on different methods of activating tailings to improve their cementitious property as cemented paste and reusability // Journal of Environmental Management. 2020. Vol. 270. № 110881. DOI: 10.1016/j.jenvman.2020.110881
- Yilmaz T., Ercikdi B., Deveci H. Utilisation of construction and demolition waste as cemented paste backfill material for underground mine openings // Journal of Environmental Management. 2018. Vol. 222. P. 250-259. DOI: 10.1016/j.jenvman.2018.05.075
- 17. Koohestani B., Belem T., Koubaa A., Bussière B. Experimental investigation into the compressive strength development of cemented paste backfill containing Nano-silica // Cement & Concrete Composites. 2016. Vol. 72. P. 180-189. DOI: 10.1016/j.cemconcomp.2016.06.016
- Juanrong Zheng, Xiaoxiao Sun, Lijie Guo et al. Strength and hydration products of cemented paste backfill from sulphide-rich tailings using reactive MgO-activated slag as a binder // Construction and Building Materials. 2019. Vol. 203. P. 111-119. DOI: 10.1016/j.conbuildmat.2019.01.047
- Ercikdi B., Yılmaz T., Külekci G. Strength and ultrasonic properties of cemented paste backfill // Ultrasonics. 2014. Vol. 54. Iss. 1. P. 195-204. DOI: 10.1016/j.ultras.2013.04.013
- Juanrong Zheng, Lijie Guo, Xiaoxiao Sun et al. Study on the Strength Development of Cemented Backfill Body from Lead-Zinc Mine Tailings with Sulphide // Advances in Materials Science and Engineering. 2018. Vol. 2018. № 7278014. DOI: 10.1155/2018/7278014
- 21. Saedi A., Jamshidi-Zanjani A., Darban A.K. A review of additives used in the cemented paste tailings: Environmental aspects and application // Journal of Environmental Management. 2021. Vol. 289. № 112501. DOI: 10.1016/j.jenvman.2021.112501
- Cihangir F., Ercikdi B., Kesimal A. et al. Paste backfill of high-sulphide mill tailings using alkali-activated blast furnace slag: Effect of activator nature, concentration and slag properties // Minerals Engineering. 2015. Vol. 83. P. 117-127. DOI: 10.1016/j.mineng.2015.08.022
- 23. Ercikdi B., Baki H., Izki M. Effect of desliming of sulphide-rich mill tailings on the long-term strength of cemented paste backfill // Journal of Environmental Management. 2013. Vol. 115. P. 5-13. DOI: 10.1016/j.jenvman.2012.11.014
- 24. Grabinsky M., Jafari M., Pan A. Cemented Paste Backfill (CPB) Material Properties for Undercut Analysis // Mining. 2022. Vol. 2. Iss. 1. P. 103-122. DOI: 10.3390/mining2010007
- Boger D.V. Rheology of Slurries and Environmental Impacts in the Mining Industry // Annual Review of Chemical and Biomolecular Engineering. 2013. Vol. 4. P. 239-257. DOI: 10.1146/annurev-chembioeng-061312-103347
- Deb D., Sreenivas T., Dey G.K., Panchal S. Paste Backfill Technology: Essential Characteristics and Assessment of its Application for Mill Rejects of Uranium Ores // Transactions of the Indian Institute of Metals. 2017. Vol. 70. Iss. 2. P. 487-495. DOI: 10.1007/s12666-016-0999-0
- Roshani A., Fall M. Flow ability of cemented pastefill material that contains nano-silica particles // Powder Technology. 2020. Vol. 373. P. 289-300. DOI: 10.1016/j.powtec.2020.06.050
- Liu Lang, Ki-Il Song, Dezheng Lao, Tae-Hyuk Kwon. Rheological Properties of Cemented Tailing Backfill and the Construction of a Prediction Model // Materials. 2015. Vol. 8. Iss. 5. P. 2076-2092. DOI: 10.3390/ma8052076
- Niroshan N., Sivakugan N., Veenstra R.L. Flow Characteristics of Cemented Paste Backfill // Geotechnical and Geological Engineering. 2018. Vol. 36. Iss. 4. P. 2261-2272. DOI: 10.1007/s10706-018-0460-8
- Yonghui Niu, Haiyong Cheng, Shunchuan Wu et al. Rheological properties of cemented paste backfill and the construction of a prediction model // Case Studies in Construction Materials. 2022. Vol. 16. № e01140. DOI: 10.1016/j.cscm.2022.e01140
- 31. Deng X.J., Klein B., Hallbom D.J. et al. Influence of Particle Size on the Basic and Time-Dependent Rheological Behaviors of Cemented Paste Backfill // Journal of Materials Engineering and Performance. 2018. Vol. 27. Iss. 7. P. 3478-3487. DOI: 10.1007/s11665-018-3467-7
- Xin Chen, Xiuzhi Shi, Jian Zhou et al. Effect of overflow tailings properties on cemented paste backfill // Journal of Environmental Management. 2019. Vol. 235. P. 133-144. DOI: 10.1016/j.jenvman.2019.01.040
- Deng X.J., Klein B., Zhang J.X. et al. Time-dependent rheological behaviour of cemented backfill mixture // International Journal of Mining, Reclamation and Environment. 2018. Vol. 32. Iss. 3. P. 145-162. DOI: 10.1080/17480930.2016.1239305
- 34. Qiangqiang Cheng, Yaben Guo, Chaowei Dong et al. Mechanical Properties of Clay Based Cemented Paste Backfill for Coal Recovery from Deep Mines // Energies. 2021. Vol. 14. Iss. 18. № 5764. DOI: 10.3390/en14185764
- Hane I., Belem T., Benzaazoua M., Maqsoud A. Laboratory Characterization of Cemented Tailings Paste Containing Crushed Waste Rocks for Improved Compressive Strength Development // Geotechnical and Geological Engineering. 2017. Vol. 35. Iss. 2. P. 645-662. DOI: 10.1007/s10706-016-0131-6
- 36. Chaoqun Dai, Aixiang Wu, Yan Qi, Zhiqiang Chen. The Optimization of Mix Proportions for Cement Paste Backfill Materials via Box-Behnken Experimental Method // Journal of The Institution of Engineers (India): Series D. 2019. Vol. 100. Iss. 2. P. 307-316. DOI: 10.1007/s40033-019-00180-7
- 37. Ercikdi B., Cihangir F., Kesimal A. et al. Utilization of water-reducing admixtures in cemented paste backfill of sulphide-rich mill tailings // Journal of Hazardous Materials. 2010. Vol. 179. Iss. 1-3. P. 940-946. DOI: 10.1016/j.jhazmat.2010.03.096
- Kesimal A., Yilmaz E., Ercikdi B. et al. Effect of properties of tailings and binder on the short-and long-term strength and stability of cemented paste backfill // Materials Letters. 2005. Vol. 59. Iss. 28. P. 3703-3709. DOI: 10.1016/j.matlet.2005.06.042
- Meggyes T., Jefferis S.A. Mine Paste Backfill–The Behaviour of Thickened Tailings and Pipeline Design // GeoCongress 2012: State of the Art and Practice in Geotechnical Engineering: Proceedings of GeoCongress 2012, 25-29 March 2012, Oakland, California, USA. ASCE, 2012. P. 4116-4125. DOI: 10.1061/9780784412121.423
- Walske M.L., McWilliam H., Doherty J., Fourie A. Influence of curing temperature and stress conditions on mechanical properties of cementing paste backfill // Canadian Geotechnical Journal. 2015. Vol. 52. № 1. P. 148-161. DOI: 10.1139/cgj-2014-0502
- Yilmaz T., Ercikdi B., Karaman K., Külekçi G. Assessment of strength properties of cemented paste backfill by ultrasonic pulse velocity test // Ultrasonics. 2014. Vol. 54. Iss. 5. P. 1386-1394. DOI: 10.1016/j.ultras.2014.02.012
- 42. Li Li. Analytical solution for determining the required strength of a side-exposed mine backfill containing a plug // Canadian Geotechnical Journal. 2014. Vol. 51. № 5. P. 508-519. DOI: 10.1139/cgj-2013-0227
- 43. Ercikdi B., Kesimal A., Cihangir F. et al. Cemented paste backfill of sulphide-rich tailings: Importance of binder type and dosage // Cement & Concrete Composites. 2009. Vol. 31. Iss. 4. P. 268-274. DOI: 10.1016/j.cemconcomp.2009.01.008
- 44. Jafari M., Shahsavari M., Grabinsky M. Drained Triaxial Compressive Shear Response of Cemented Paste Backfill (CPB) // Rock Mechanics and Rock Engineering. 2021. Vol. 54. Iss. 6. P. 3309-3325. DOI: 10.1007/s00603-021-02464-5
- 45. Tariq A., Yanful E.K. A review of binders used in cemented paste tailings for underground and surface disposal practices // Journal of Environmental Management. 2013. Vol. 131. P. 138-149. DOI: 10.1016/j.jenvman.2013.09.039
- 46. Haiqiang Jiang, Fall M. Yield stress and strength of saline cemented tailings in sub-zero environments: Portland cement paste backfill // International Journal of Mineral Processing. 2017. Vol. 160. P. 68-75. DOI: 10.1016/j.minpro.2017.01.010
- 47. Cihangir F., Akyol Y. Effect of Desliming of Tailings on the Fresh and Hardened Properties of Paste Backfill Made from Alkali-Activated Slag // Advances in Materials Science and Engineering. 2020. Vol. 2020. № 4536257. DOI: 10.1155/2020/4536257
- Chi J.M., Ran Huang, Yang C.C. Effects of Carbonation on Mechanical Properties and Durability of Concrete Using Acce-lerated Testing Method // Journal of Marine Science and Technology. 2002. Vol. 10. Iss. 1. P. 14-20. DOI: 10.51400/2709-6998.2296
- Yoon-Moon Chun, Naik T.R., Kraus R.N.Carbon dioxide sequestration in concrete in different curing environments // Proc. Int. Conf: Sustainable construction materials and technologies, 11-13 June 2007, Coventry. Special papers proceedings, 2007. Р. 18-24.
- 50. Kasap T., Yilmaz E., Sari M. Physico-chemical and micro-structural behavior of cemented mine backfill: Effect of pH in dam tailings // Journal of Environmental Management. 2022. Vol. 314. Iss. 4. № 115034. DOI: 10.1016/j.jenvman.2022.115034
- Pokharel M., Fall M. Combined influence of sulphate and temperature on the saturated hydraulic conductivity of hardened cemented paste backfill // Cement & Concrete Composites. 2013. Vol. 38. P. 21-28. DOI: 10.1016/j.cemconcomp.2013.03.015
- Fang K., Fall M. Effects of curing temperature on shear behaviour of cemented paste backfill-rock interface // International Journal of Rock Mechanics and Mining Sciences. 2018. Vol. 112. P. 184-192. DOI: 10.1016/j.ijrmms.2018.10.024
- 53. Raffaldi M.J., Seymour J.B., Richardson J. et al. Cemented Paste Backfill Geomechanics at a Narrow-Vein Underhand Cut-and-Fill Mine // Rock Mechanics and Rock Engineering. Vol.52. Iss.12. P. 4925-4940. DOI: 10.1007/s00603-019-01850-4
- Скобелев Д.О., Череповицына А.А., Гусева Т.В. Технологии секвестрации углекислого газа: роль в достижении углеродной нейтральности и подходы к оценке затрат // Записки Горного института. 2023. Т.259. С. 125-140. DOI: 10.31897/PMI.2023.10
- Шапошников Н.О., Голубев И.А., Хоробров С.В. и др. Автоклавное моделирование коррозионных процессов, происходящих в газопроводе при транспортировке неподготовленной многофазной среды, содержащей CO2 // Записки Горного института. 2022. Т.258. С. 915-923. DOI: 10.31897/PMI.2022.92
- 56. Федосеев С.В., Цветков П.С. Ключевые факторы общественного восприятия проектов захвата и захоронения углекислого газа // Записки Горного института. Т. 237. С. 361-368. DOI: 10.31897/PMI.2019.3.361
- Cherepovitsyn A., Chvileva T., Fedoseev S. Popularization of Carbon Capture and Storage Technology in Society: Principles and Methods // International Journal of Environmental Research and Public Health. 2020. Vol. 17. Iss. 22. № 8368. DOI: 10.3390/ijerph17228368
- Gür T.M. Carbon Dioxide Emissions, Capture, Storage and Utilization: Review of Materials, Processes and Technologies // Progress in Energy and Combustion Science. 2022. Vol.89. №100965. DOI: 10.1016/j.pecs.2021.100965
- 59. Кантюков Р.Р., Запевалов Д.Н., Вагапов Р.К. Анализ применения и воздействия углекислотных сред на коррозионное состояние нефтегазовых объектов // Записки Горного института. 2021. Т. С. 578-586. DOI: 10.31897/PMI.2021.4.11
- 60. Ильинова А.А., Ромашева Н.В., Стройков Г.А. Перспективы и общественные эффекты проектов секвестрации и использования углекислого газа // Записки Горного института. Т. 244. С. 493-502. DOI: 10.31897/PMI.2020.4.12
- Vasilev Yu., Cherepovitsyn A., Tsvetkova A., Komendantova N. Promoting Public Awareness of Carbon Capture and Storage Technologies in the Russian Federation: A System of Educational Activities // Energies. 2021. Vol.14. Iss.5. № 1408. DOI: 10.3390/en14051408
- 62. Пономарев А.И., Юсупов А.Д. Оценка влияния касательного напряжения на стенке технологических трубопроводов газоконденсатного месторождения на интенсивность углекислотной коррозии // Записки Горного института. 2020. Т. С. 439-447. DOI: 10.31897/PMI.2020.4.6
- 63. Череповицын А.Е., Ильинова А.А., Евсеева О.О. Управление стейкхолдерами проектов секвестрации углекислого газа в системе государство – бизнес – общество // Записки Горного института. Т. 240. С. 731-742. DOI: 10.31897/PMI.2019.6.731
- Tcvetkov P. Engagement of resource-based economies in the fight against rising carbon emissions // Energy Reports. 2022. Vol. 8. S. 10. P. 874-883. DOI: 10.1016/j.egyr.2022.05.259
- Yilmaz E., Belem T., Benzaazoua M. Effects of curing and stress conditions on hydromechanical, geotechnical and geochemical properties of cemented paste backfill // Engineering Geology. 2014. Vol. 168. P. 23-37. DOI: 10.1016/j.enggeo.2013.10.024