Impact of carbon dioxide on the main geotechnical quality criteria and preparation cost of cemented paste backfill
- 1 — Ph.D. Senior Lecturer University of Namibia ▪ Orcid
- 2 — Lecturer University of Namibia ▪ Orcid
- 3 — Laboratory Technician University of Namibia ▪ Orcid
Abstract
There is a global upsurge in the use of cemented paste backfill (CPB) for various mining functions. However, the cost of the Portland cement binder is prohibitive, thus warranting strategies to reduce cement usage without overly diminishing the CPB quality. Since carbon dioxide is used for patented sand moulding processes, this study is premised on that physicochemical ability of CO2 to enhance the curing of consolidated inorganic materials. It evaluated the impact of carbon dioxide on the uniaxial compressive strength UCS and preparation cost of CPB standard samples (ASTM C109). The preparation cost was delimited to the purchase cost of the Portland cement. The backfill material was silica sand tailings with 4.5 wt.% Portland cement binder and a water-cement ratio of 7.6. Distilled water of pH 5.4 was used for the control samples while variable amounts of carbon dioxide were dissolved in distilled water to generate carbonated mixing water with pH values of 3.8; 4 and 4.2. The lower the carbonated water pH, the higher is the CO2 concentration. UCS tests were conducted on the samples after curing for 3, 7, 28, and 90 days. There was an observable increase in the UCSs and reduction in curing time with increasing carbon dioxide. Samples prepared with carbonated water of pH 3.8 had almost double the strength of those prepared with pure distilled water of pH 5.4, implying that more dissolved CO2 corresponds to higher CPB strength. This is supported by the trendline equations for the graphical simulation of strength on curing time. Thus, CPB with much less binder can be expected to attain the requisite UCS if carbon dioxide is incorporated. The average reduction in Portland cement consumption was 0.61 %, which translates to a cost saving of the same percentage points. If calculated over the operational life of a mine, this is a massive saving of millions of dollars.
Introduction
Hardened mine backfill or cemented paste backfill (CPB) is a synthetic engineering material composed of tailings, water, and hydraulic binders, with the tailings constituting 65-85 % of the combined paste weight [1-3]. CPB has multiple mining applications such as underground mine backfilling [4-6], roof support [7-9], control of surface subsidence [10-12], and mitigation of acid mine drainage [1, 13], while at the same time serving as an environmentally friendly tailings management method utilized in many mines globally [14-16], with its adoption on the increase [17, 18].
A critical geotechnical quality criterion for cured mine backfill is the mechanical strength [10, 19, 20], which is important for load bearing applications such as roof and goaf support [9] in underground mines to safeguard mine personnel and prevent ore dilution [5, 7, 21]. The unconfined compressive strength (UCS) of the hardened or cured backfill is commonly ascertained via the uniaxial compressive strength test to evaluate the CPB’s stability on demand due to the test’s low cost and ease of integration into standard mine quality control protocols [22-24]. Before curing, the CPB is in slurry form, necessitating transport in pipelines and the use of slurry pumps to convey it to places where it is needed [25-27]. During this phase, rheological properties of the CPB slurry are critical for timely and efficient deposition at points of interest [28-30]. Numerous works such as [2, 7, 31] have studied the rheology of CPB slurry and characterised it as a non-Newtonian fluid [25, 27, 30], whose yield stress is mainly affected by the solids mass fraction [32-35]. This yield stress is the primary shear stress that the slurry pumping system has to overcome in order for the CPB to flow, thus making it critical for cost-effective placement of the CPB in mine workings [7, 27]. Water-reducing admixtures can be added to the paste to augment its pumpability, and improve the strength of the cured CPB [36-38].
CPB is the most extensively used backfilling technology in Northern America, and in some parts of the globe because of a number of advantages over competing technologies [24, 38, 39]. CPB is produced by homogeneously mixing three major constituents: tailings, water, and binder [12, 40-42]. The binder generates cohesion in the CPB due to the hydration process [21, 43, 44]. A major type of binder which is often used in the mining industry for the production of CPB is Portland cement in weight proportions of 2-7 % owing to its market abundance and flexibility of application [21, 37, 45].
However, while binders advantageously increase the mechanical strength of CPB [17, 20, 46], they can also represent a considerable portion of the mine operating cost [2, 8, 37]. For example, Portland cement binders constitute about 50-75 % of the overall cost of CPBs [8, 27, 45]. For instance, the cement consumption of the mining industry in the province of Ontario, Canada alone is estimated between 5-6 % of the total Canadian Portland cement production with an estimated cost of CA USD75 million annually in the consolidation of backfill in underground mining operations [44].
Since binder consumption is the most expensive component in the preparation of CPB, there is a need to explore techniques for reducing the binder consumption of cemented backfill [17, 18, 47]. One approach would be to incorporate carbon dioxide into the cemented backfill during its preparation, as has been reported for concrete [48, 49]. The strength of concrete has been observed to increase due to carbonation, which results in precipitates forming and aggregating inside pores in the cement matrix. The partial closure of the pores or voids, also termed pore refinement improves the cement UCS [48, 49]. If the same phenomenon can occur in CPB, then it may also lead to an increase of its UCS, thereby reducing the binder consumption and affiliated costs. While the study by T.Kasap et al. [50] did consider the effect of pH on CPB, there was no deliberate alteration of the mixing water pH by dissolution of CO2, but the natural composition of the different tailings used was intentionally selected so as to have basic and acidic CPB samples. Therefore, the present work focuses on assessing the impact of carbonation on the UCS of CPB and the potential cost savings in its preparation arising out of reduced Portland cement binder use.
Methodology
Silica sand tailings
Ground silica sand (99.8 wt.% SiO2) was used as the main mine backfill constituent, consistent with earlier studies [14, 24, 51]. The physical properties of this sand: Gs 2.7; D10 1.9; D30 9.0; D50 22.5; D60 31.5; D90 88.9; Cu 16.2; Cc 1.3 μm. The silica sand can be classified as medium tailings having about 40 % fine particles, which have diameters lower than 20 µm.
Binder
The purpose of the binder in paste backfill is to create adequate mechanical strength to satisfy static and dynamic loading support functions. Portland cement is traditionally used as binder for cemented paste backfill [45]. Paste backfill bonded with Portland cement exhibits improved shear strength, tensile strength, and stiffness [52, 53]. Therefore, 4.5 wt.% by weight Portland Cement Type I (PCI) was used as the binder in this study. The chemical constitution of this PCI: MgO 2.65; CaO 62.82; SiO2 18.03; Mn2O3 4.53; Fe2O3 2.70; SO3 3.82 wt.% and it had a density of 3.15g/cm3.
Mixing water
Water demand is critical in the preparation of CPB. In the context of this work, it occupied second position (34.2 %) in terms of portions of the constituents after silica tailings.
A water-cement ratio (w/c) of 7.6 (4.5 × 7.6 = 34.2 %) was maintained throughout the CPB samples preparation. Two types of mixing water were used: distilled water with no CO2 added (DW) and distilled water with varying amounts of CO2 (CW). Pure distilled water of pH 5.4 was used as the solvent and control. Specific amounts of CO2 were then added to this distilled water in order to create carbonated mixing water with pH values of 3.8; 4 and 4.2 respectively (Table 1), such that the higher the dissolved CO2, the lower the pH and hence the more acidic the CW.
Table 1
Mix ratios of the CPB samples produced
Mix name |
Tailings type |
Binder type |
Binder, wt.% |
W/cratio |
pH |
CPB-3.8 |
ST |
PCI |
4.5 |
7.6 |
3.8 |
CPB-4 |
ST |
PCI |
4.5 |
7.6 |
4.0 |
CPB-4.2 |
ST |
PCI |
4.5 |
7.6 |
4.2 |
CPB-5.4 |
ST |
PCI |
4.5 |
7.6 |
5.4 |
Preparation of CPB mixtures
The silica sand tailings, cement and pre-treated water samples were homogeneously mixed in a double spiral mixer. 31 samples were prepared with a fixed binder composition of 4.5 wt.% and water-cement ratio of 7.6. The CPB that was produced was then poured into standard cylindrical curing molds (Æ50 mm and H = 100 mm). The filled moulds were then sealed to prevent vaporization of water and cured at a temperature of 22 °C, for periods of 3, 7, 28 and 90 days. The composition mixtures of the different CPBs prepared for this study are as presented in Table 2.
Table 2
Density of constituents used during the preparation of CPB samples
Component |
Value, g/cm3 |
Constituent portion, % |
PCI |
3.15 |
4.5 |
Distilled water |
0.9900198 |
34.2 = (4.5 × 7.6) |
Carbonated water |
1 |
34.2 = (4.5 × 7.6) |
Silica sand tailings |
1.680 |
61.3 = (100 – 4.5 × 7.6) |
Testing Methods
UCS tests were conducted on all the 31 cylindrical samples in order to evaluate their mechanical strength after 3, 7, 28 and 90 days of curing. An initial load of 10 N was first applied before dynamic loading began at a compression rate of 2.5 mm/min to failure in accordance with ASTM C109 using a 50 kN Z050 ZwickRoell compression machine.
Results and discussion
Influence of carbon dioxide on CPB strength
Figure 1 shows that throughout curing times 3, 7, 28 and 90 days respectively, there is an increase of strength in the CPB when the pH level is decreasing, especially between the strength of CPBs of DW (with pH level of 5.4) and the strength of CPBs of DW (with pH level of 3.8). This trend of the increase of compressive strength is also true when pH level is between 4 and 4.2 except at day 3 where the difference between the compressive strength of all the samples is not that significant (Fig.1). Another exception can also be seen at curing time day 7 where the compressive strength of DW CPB with pH level of 5.4 is greater than the one of CW CPB with pH level 4.2. These two exceptions might have been caused perhaps by the difficulties related to the preparation of high quality CPB samples [9, 24, 37].
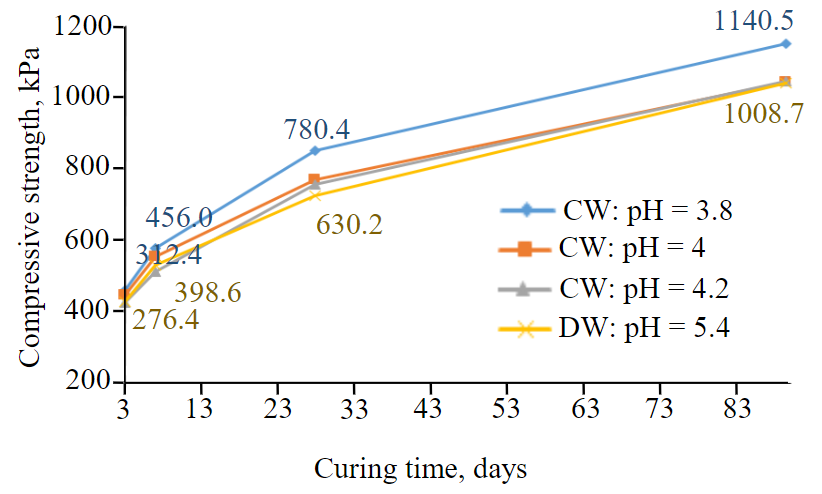
Fig.1. Strength development of CPB with CW and DW
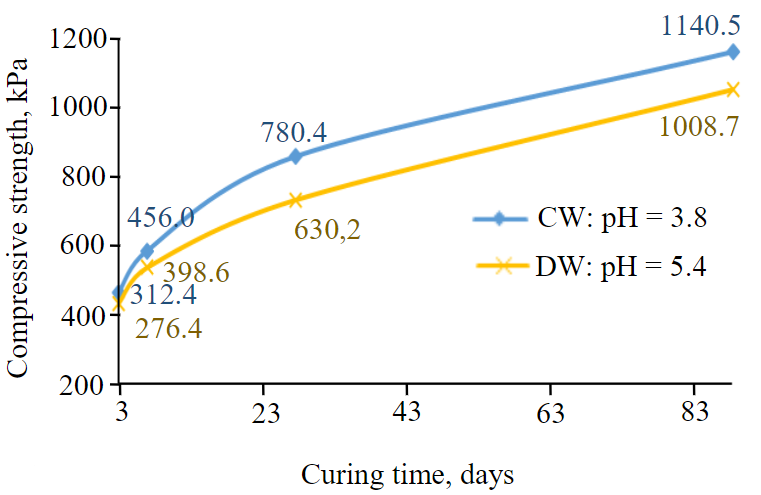
Fig.2. Comparative strength development of DW CPB (pH = 5.4) vs CW CPB (pH = 3.8)
Now since, throughout all the curing times studied (days 3, 7, 28 and 90), there is significant and clear increase of compressive strength between specimen of DW (when pH level is 5.4) and CW (when pH level is 3.8), the rest of the discussions are focused mainly on these two special cases.
At day 3 and day 90 of curing time, Fig.2 shows a 13 % strength increase of CW CPB specimens of pH 3.8 in comparison with the DW CPB specimens of pH 5.4 for the same binder proportion (4.5 wt.%). However, there are even greater strength increases during other curing times.
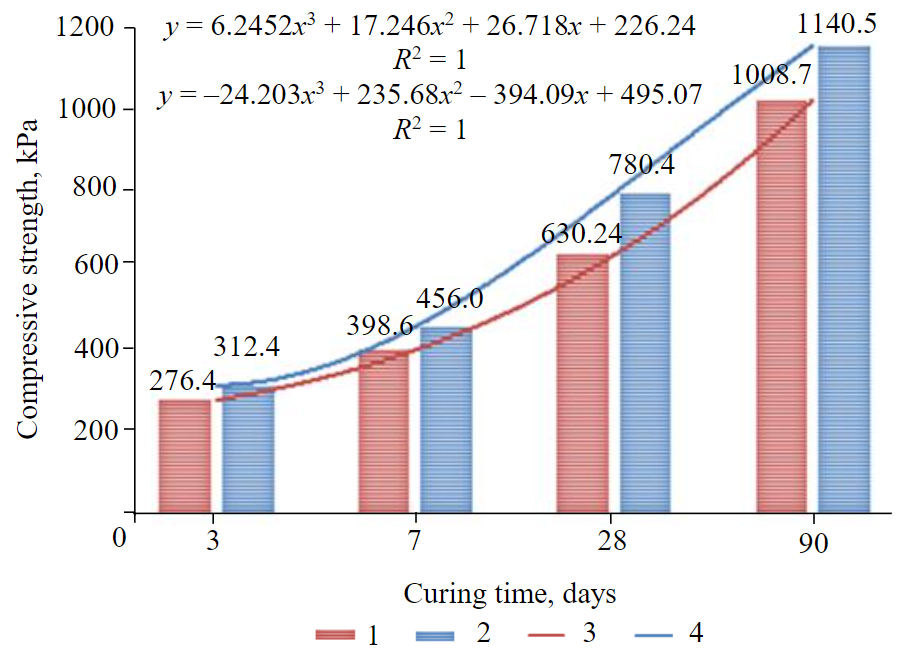
Fig.3. Trendlines of strength development of DW CPB (pH = 5.4) vs CW CPB (pH = 3.8) 1 – DW; 2 – CW; 3 – polynomial (DW); 4 – polynomial (СW)
At “day 7”, with the injection of CO2 into the mixing water resulting in the solution with pH level of 3.8, the UCS of CPB samples increased in 14 % versus the UCS produced with just DW (pH = 5.4). At day 28 for example, it is shown that the strength of CPB made with CW where the pH level is of 3.8 reaches about 780 kPa (Fig.3). The incorporation of carbon dioxide into the mixing water to reach a pH level minimum 3.8 increases the strength by approximately 24 %. That is almost double the minimum strength (400 kPa) required at Matagami Mine, a Glencore underground zinc mine in the province of Quebec, Canada. In fact, the CPB structure strength must reach 400 kPa after 28 days or curing time. At the same curing time (day 28), Fig.3 show that the compressive strength of the CPB obtained using DW was found to be about 630.2 kPa, which is lower than the value of CPB made with CW when pH level is 3.8, yet it is greater than the industrial requirement of UCS at curing day 28 as stated above. This might mean that in the conditions of Matagami Zinc Mine, the required strength of the hardened paste fill (400 kPa) can be developed or reached earlier than the curing time day 28. Consequently, this might therefore contribute to the efficiency of underground mine productions operations of adjacent mine faces since the stope backfilled would have already provided a safe working environment for the miners [4, 32, 38, 46]. Overall, the presence of CO2 in the water solution for preparing CPB caused the compressive strength to increase by approximately 16 % when considering the average value of all the UCSs increases during the curing time studied (incremental strength of CW CPB over DW CPB (days 3, 7, 28 and 90 – 13; 14; 24; 13 % respectivery).
Carbon dioxide is one of the major greenhouse gases (GHG) produced mainly by human activities. Globally 78 % of CO2 emissions come from activities related to production and energy consumption [54-57], such as the burning of fossil fuels, iron and steelmaking, and production of cements. Some components of these emissions attack atmospheric ozone and create holes in the ozone layer [58]. It is important to note that the suggested approach of introducing this type of GHG into mixing water for the production of paste backfill implies first the extraction of CO2 from natural deposits (wells) or its capture and storage [59-63]. This means this approach may eventually become one of the strategic ways of backfill technology for reducing the GHG footprint of the mining industry, particularly in tailings and water management sectors since it promotes the capture, storage, sequestration and utilization of the CO2 [64]. Hence, it might help contribute towards the achievement of United Nations (UN) SDG 13 (climate action) which recommends urgent action to combat climate change and its impacts.
The density of carbonated water is dependent on the degree of carbonation. There is no consistent density for carbonated water; however, if certain parameters are known, then the density can be easily calculated. In order to calculate the density of carbonated water, the density of both carbon dioxide and water. Carbon dioxide has a density of 0.00198 g/cm3. The density of water is 1 g/cm3. The equation to calculate the density of a substance involves multiplying the percentage of concentration of one substance by its density and adding it to the percentage multiplied by the density of the other substance [37].
Now, knowing the mathematical model of the strength development of CPB produced with CW of pH level 3.8 as function of curing time, it is possible to determine the approximate day when the hardened paste fill would cure and reach the expected 400 kPa:
Solving equation (1) which represents the best fit function obtained using Microsoft Excel when y = 400 kPa, under the conditions of Matagami Mine would yield the following results: x1 = 7.68552; x2 = 0.29005; x3 = 1.76207 days. Among these values, the optimum curing time, would be 7.7 days while the other two can be rejected since they are not realistic according to the experimental data. This means that by incorporating CO2 into mixing water for the production of CPB, the expected mechanical strength (400 kPa) can be attained after only 8 days instead of 28 days. This is equivalent to the reduction of the CPB curing time by about 71.4 %, which would have tremendous impact on the economic parameters of the considered mining company. Moreover, the schedule of the entire mine operations would be improved and would there anticipate the cash flow of the project, and therefore contribute effectively to the return on the investments and a shortened payback period of the operation project:
Similarly, if equation (2) is solved considering Matagami Mine conditions when y is equal to 400 kPa, the optimum curing time for DW CPBs would be 2 days or 93 % of the curing time is saved. This high rate of increase of the strength of CPBs observed for both CW and DW solutions can be attributed partially to some physical properties of the silica tailings used, especially density. This is obvious because the tailings material used at Matagami Mine is zinc ore gangue material, which weighs less than the silica tailings used in the present study. The observation confirms the findings of [10, 43, 65] who reported an increase in paste backfill strength for the same binder proportion (4.5 wt.%) when the tailings density increased.
The results obtained demonstrate that there is an important strength improvement when there CO2 is incorporated in the mixing water intended for the preparation of the CPB and that the pH level of 3.8 yields the highest compressive strengths.
Effect of carbon dioxide on binder consumption
The results obtained demonstrate that the presence of CO2 in the mixing water for preparing the CPBs results in considerable augmentation of the mechanical strength of these CPBs, with a water pH of 3.8 yielding the optimum UCS.
Table 3
Economic effect of incorportating CO2 into CPB, СUSD
Day |
Costs of binders of CPB |
Annual Saved Costs on binder |
|
DW |
CW |
||
3 |
7473375 |
6626392.50 |
846982.50 |
7 |
7473375 |
6543355.00 |
930020.00 |
28 |
7473375 |
6045130.00 |
1428245.00 |
90 |
7473375 |
6626392.50 |
846982.50 |
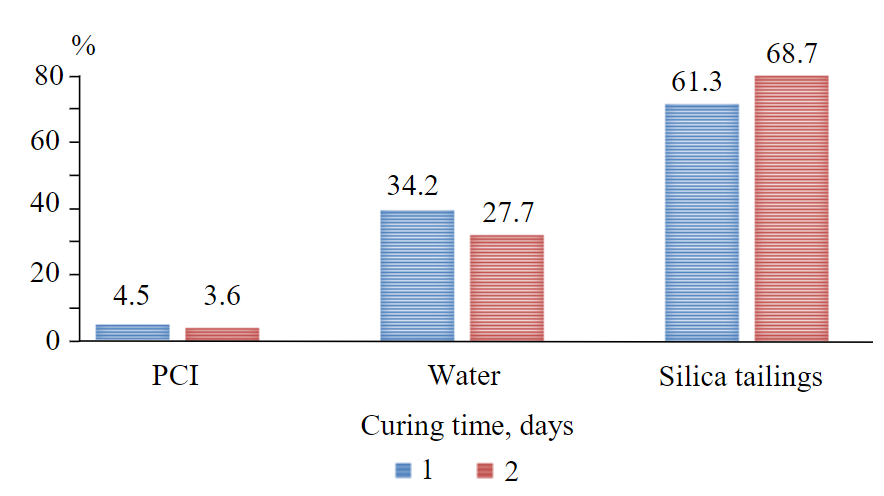
Fig.4. Comparison of consitituents portions of DW CPBs and CW CPBs, % 1 – constituents portions DW; 2 – constituents portions CW
Now, considering that there is a linear proportional relationship between initial binder portions (4.5 %), strength values of DW CPB samples and strength values of CW CPB samples at a pH level of 3.8, the optimized portions of binders can be find by multiplying this binder portion by UCS of DW and divided by the UCS of CW at a specific curing time. Results for day 28 are presented in Fig.4. Therefore, by injecting CO2 into the mixing water, it is possible based on day 28 results to save not only about 1 % of binders’ consumption (PCI), but also about 6.5 % of water consumption while maintaining the same w/c ratio (7.6). This might contribute towards the achievement of United Nations (UN) SDG 14 (Life below water) which advocates for conservation and sustainable use of marine resources for sustainable development.
Based on the results of curing days 3, 7, 28 and 90 respectively, the overall economy that might be achieved in terms of cement consumption in preparing paste fill, can be found within the respective 0.51; 0.56; 0.86; 0.51 % saving figures. The average value of this saving would be ~0.61 %.
The use of carbon dioxide also has another significant effect on the tailings consumption. After introduction of CO2 (decreased pH), there is an increased demand for the tailings quantity to be used as major constituents for the production of paste backfill, about 7.4 % of tailing consumptions at the curing day 28. This means that less mine residual materials may remain in the environment to impact the ecosystem. Therefore, this approach might contribute effectively to underground disposal [2, 23, 26]. Hence, the suggested approach might also help reach the UN SDG 15 (Life on the Land) which promotes the protection, restoration and sustainable use of terrestrial ecosystems, sustainable management of forests, combating desertification, halting and reserving land degradation, as well as halting biodiversity loss.
Effect of CO2 on CPB binder costs
The optimization of the binder consumption due the concentration of carbon dioxide in the mixing water, leads to important economic results as presented in Table 3.
The findings indicate the incorporation of carbon dioxide in the distilled water used for preparation of CPB would result in a significant improvement of the strength for an equal quantity of binder. This means that there is potential for the development of new optimum recipes of mixture of backfill (reduction of cost of binders) and/or the forecast of its main mechanical property (strength) as function of carbon dioxide concentration in the mixing water. As a result, about 0.51-0.86 % of quantities of binders used during the preparation of backfill can be saved which may have a great impact on productivity and competitiveness of the relevant mines, that is to say also on generating employment.
Table 4
Variation of UCS of CPB as a function of pH, kPa
pH |
Day 3 |
Day 7 |
Day 28 |
Day 90 |
3.8 |
312.4 |
456.0 |
780.4 |
1140.5 |
4 |
298.8 |
427.6 |
685.0 |
1010.0 |
4.2 |
272.6 |
375.9 |
668.3 |
1013.4 |
5.4 |
276.4 |
398.6 |
630.2 |
1008.7 |
In fact, a mine which produces 7000 t of ore per day produces an average of 3500 t of CPB per day with an average binder consumption of about 3.5 % (at times 4.5 % or more). Given, that the average cost of binders is about CA USD 1.30 / 1% binder [26], a reduction of the quantity of binder consumption of 0.51-0.86 % would result in annual savings of about CA USD 846.983 (0.51 % × 3500 t × 365j) to CA USD 1.428.245. For a mine that has a lifespan of 20 years, the overall benefit in the reduction of the cost of cemented backfill would be about 17 million (case of 0.23 % reduction) and about 29 million CA USD (case of 0.86 % reduction). The economic effect of incorportating CO2 into CPB throughtout the life span of the mine on 3, 7, 28 and 90 days would be 17 million СA USD, 19 million СA USD, 29 million СA USD, 17 million СA USD respectively.
Trendline equations of CPB UCS as a function of pH
The best fit functions of strength development of DW CPB (pH = 5.4) and CW CPB (pH = 3.8) versus the curing ages of the samples were found using Microsoft Excel to be a third degree equation (see Fig.3). It is shown that the strength y of hardened backfill increases with increasing curing time x.
Similary, mathematical models of the variation of the compressive strength with curing time illustrated in Fig.1, are also third-degree polynomials equations for pH 5.4, 4.2, 4 and 3.8 respectively, R2 = 1. Based on the coefficients for , pH 3.8 corresponds to the optimum CO2 concentration for maximum strength of the CPB. This supports the data in Table 4, which shows that with a decrease of the pH level of the mixing water, the compressive strength of the hardened backfill increases:
Conclusions
The incorporation of carbon dioxide into the mixing water for the preparation of silica tailings CPB samples diminishes the pH level, as expected, due to the acidic nature of CO2, but increases the final UCS of the CPB by 13 %, while cutting the curing time by more than 70 %. It also reduces the Portland cement binder consumption by approximately 0.51-0.86 %, and yields CPB preparation cost savings of the same percentage points.
The best fit functions of strength development of DW CPB (pH = 5.4) and CW CPB (pH = 3.8) versus the curing ages of the samples are both third-degree equations, and the trendlines have similar profiles, implying the same curing mechanism in the CPB samples for either test case. The only diffence is the magnitude of the coefficients, which explains the higher UCSs for the CW CPB samples. This increase in strength is due to carbonation on account of reactions between the CO2, water and Portland cement, producing fine-sized compounds which coalesce inside voids within the CPB matrix. This increases the effective cross-sectional area of the CW CPB samples for compressive load bearing, hence the higher UCSs.
Since CO2 is the most important GHG, using it for CPB preparation is a strategic way for mitigating the carbon footprint of the mining industry, particularly in tailings and water management sector since it promotes the capture, storage, sequestration and utilization of the CO2. Hence, if commercialized it might contribute towards the achievement of United Nations SDG 13 (Climate Action) which recommends the taking an urgent action in order to combat climate change and its impacts. This contribution to climate change mitigation is in fact two-fold, considering that less binder will be required for Portland cement, thus lessening GHG emissions from the cement manufacturing industries.
Therefore, CO2 in CPB can be one of the pathways for the mining and Portland cement manufacturing industries to achieve net zero GHG emissions by 2050.
Future CPB studies can focus on studying the impact of different volumes of the cement binder on the backfill rheological and mechanical properties, and accounting for the costs of carbon dioxide production, capture, storage, transportation, and incorporation into the backfill mixture in the economic analysis.
The chemical composition of the plant tailings has an effect on the water and cement demands of the CPB, as well the rheological and mechanical properties. This warrants replications of this study for different tailings.
References
- Benzaazoua M., Fall M., Belem T. A contribution to understanding the hardening process of cemented pastefill. Minerals Engineering. 2004. Vol. 17. Iss. 2, p. 141-152. DOI: 10.1016/j.mineng.2003.10.022
- Fall M., Benzaazoua M., Saa E.G. Mix proportioning of underground cemented tailings backfill. Tunnelling and Underground Space Technology. 2008. Vol. 23. Iss. 1, p. 80-90. DOI: 10.1016/j.tust.2006.08.005
- Yilmaz E., Belem T., Bussière B. et al.Curing time effect on consolidation behaviour of cemented paste backfill containing different cement types and contents. Construction and Building Materials. 2015. Vol. 75, p. 99-111. DOI: 10.1016/j.conbuildmat.2014.11.008
- Emad M.Z., Mitri H., Kelly C. State-of-the-art review of backfill practices for sublevel stoping system. International Journal of Mining, Reclamation and Environment. 2015. Vol. 29. Iss. 6, p. 544-556. DOI: 10.1080/17480930.2014.889363
- Helinski M., Fahey M., Fourie A. Behavior of Cemented Paste Backfill in Two Mine Stopes: Measurements and Modeling. Journal of Geotechnical and Geoenvironmental Engineering. 2010. Vol. 137. N 2, p. 171-182. DOI: 10.1061/(ASCE)GT.1943-5606.0000418
- Thompson B.D., Bawden W.F., Grabinsky M.W. In situ measurements of cemented paste backfill at the Cayeli mine. Canadian Geotechnical Journal. 2012. Vol. 49. N 7, p. 755-772. DOI: 10.1139/t2012-040
- 7. Belem T., Benzaazoua M. Design and Application of Underground Mine Paste Backfill Technology. Geotechnical and Geological Engineering. 2008. Vol. 26. Iss. 2, p. 147-174. DOI: 10.1007/s10706-007-9154-3
- Fall M., Pokharel M. Coupled effects of sulphate and temperature on the strength development of cemented tailings backfills: Portland cement-paste backfill. Cement & Concrete Composites. 2010. Vol. 32. Iss.10, p. 819-828. DOI: 10.1016/j.cemconcomp.2010.08.002
- Minefill 2020-2021: Proceedings of the 13th International Symposium on Mining with Backfill, 25-28 May 2021, Katowice, Poland / Ed. by F.Hassani, J.Palarski, V.Sokoła-Szewioła, G.Strozik. London: CRC Press, 2021. 450 p. DOI: 10.1201/9781003205906
- 10. Gaili Xue, Erol Yilmaz, Weidong Song, Shuai Cao. Compressive Strength Characteristics of Cemented Tailings Backfill with Alkali-Activated Slag. Applied Sciences. 2018. Vol. 8. Iss. 9. N 1537. DOI: 10.3390/app8091537
- 11. Qiu-song Chen, Qin-li Zhang, Fourie A. et al. Experimental investigation on the strength characteristics of cement paste backfill in a similar stope model and its mechanism. Construction and Building Materials. 2017. Vol. 154, p. 34-43. DOI: 10.1016/j.conbuildmat.2017.07.142
- Lei Yang, Jingping Qiu, Haiqiang Jiang et al. Use of Cemented Super-Fine Unclassified Tailings Backfill for Control of Subsidence. Minerals. 2017. Vol. 7. Iss. 11. N 216. DOI: 10.3390/min7110216
- Benzaazoua M., Marion P., Picquet I., Bussière B. The use of pastefill as a solidification and stabilization process for the control of acid mine drainage. Minerals Engineering. 2004. Vol. 17. Iss. 2, p. 233-243. DOI: 10.1016/j.mineng.2003.10.027
- Chen Hou, Liujun Yang, Lei Li, Baoxu Yan. Mechanical Characteristics and Stress Evolution of Cemented Paste Backfill: Effect of Curing Time, Solid Content, and Binder Content. Frontiers in Materials. 2022. Vol. 8, p. 1-10. DOI: 10.3389/fmats.2021.812402
- 15. Saedi A., Jamshidi-Zanjani A., Darban A.K. A review on different methods of activating tailings to improve their cementitious property as cemented paste and reusability. Journal of Environmental Management. 2020. Vol. 270. N 110881. DOI: 10.1016/j.jenvman.2020.110881
- Yilmaz T., Ercikdi B., Deveci H. Utilisation of construction and demolition waste as cemented paste backfill material for underground mine openings. Journal of Environmental Management. 2018. Vol. 222, p. 250-259. DOI: 10.1016/j.jenvman.2018.05.075
- 17. Koohestani B., Belem T., Koubaa A., Bussière B. Experimental investigation into the compressive strength development of cemented paste backfill containing Nano-silica. Cement & Concrete Composites. 2016. Vol. 72, p. 180-189. DOI: 10.1016/j.cemconcomp.2016.06.016
- Juanrong Zheng, Xiaoxiao Sun, Lijie Guo et al. Strength and hydration products of cemented paste backfill from sulphide-rich tailings using reactive MgO-activated slag as a binder. Construction and Building Materials. 2019. Vol. 203, p. 111-119. DOI: 10.1016/j.conbuildmat.2019.01.047
- Ercikdi B., Yılmaz T., Külekci G. Strength and ultrasonic properties of cemented paste backfill. Ultrasonics. 2014. Vol. 54. Iss. 1, p. 195-204. DOI: 10.1016/j.ultras.2013.04.013
- Juanrong Zheng, Lijie Guo, Xiaoxiao Sun et al. Study on the Strength Development of Cemented Backfill Body from Lead-Zinc Mine Tailings with Sulphide. Advances in Materials Science and Engineering. 2018. Vol. 2018. N 7278014. DOI: 10.1155/2018/7278014
- 21. Saedi A., Jamshidi-Zanjani A., Darban A.K. A review of additives used in the cemented paste tailings: Environmental aspects and application. Journal of Environmental Management. 2021. Vol. 289. N 112501. DOI: 10.1016/j.jenvman.2021.112501
- Cihangir F., Ercikdi B., Kesimal A. et al. Paste backfill of high-sulphide mill tailings using alkali-activated blast furnace slag: Effect of activator nature, concentration and slag properties. Minerals Engineering. 2015. Vol. 83, p. 117-127. DOI: 10.1016/j.mineng.2015.08.022
- 23. Ercikdi B., Baki H., Izki M. Effect of desliming of sulphide-rich mill tailings on the long-term strength of cemented paste backfill. Journal of Environmental Management. 2013. Vol. 115, p. 5-13. DOI: 10.1016/j.jenvman.2012.11.014
- 24. Grabinsky M., Jafari M., Pan A. Cemented Paste Backfill (CPB) Material Properties for Undercut Analysis. Mining. 2022. Vol. 2. Iss. 1, p. 103-122. DOI: 10.3390/mining2010007
- Boger D.V. Rheology of Slurries and Environmental Impacts in the Mining Industry. Annual Review of Chemical and Biomolecular Engineering. 2013. Vol. 4, p. 239-257. DOI: 10.1146/annurev-chembioeng-061312-103347
- Deb D., Sreenivas T., Dey G.K., Panchal S. Paste Backfill Technology: Essential Characteristics and Assessment of its Application for Mill Rejects of Uranium Ores. Transactions of the Indian Institute of Metals. 2017. Vol. 70. Iss. 2, p. 487-495. DOI: 10.1007/s12666-016-0999-0
- Roshani A., Fall M. Flow ability of cemented pastefill material that contains nano-silica particles. Powder Technology. 2020. Vol. 373, p. 289-300. DOI: 10.1016/j.powtec.2020.06.050
- Liu Lang, Ki-Il Song, Dezheng Lao, Tae-Hyuk Kwon. Rheological Properties of Cemented Tailing Backfill and the Construction of a Prediction Model. Materials. 2015. Vol. 8. Iss. 5, p. 2076-2092. DOI: 10.3390/ma8052076
- Niroshan N., Sivakugan N., Veenstra R.L. Flow Characteristics of Cemented Paste Backfill. Geotechnical and Geological Engineering. 2018. Vol. 36. Iss. 4, p. 2261-2272. DOI: 10.1007/s10706-018-0460-8
- Yonghui Niu, Haiyong Cheng, Shunchuan Wu et al. Rheological properties of cemented paste backfill and the construction of a prediction model. Case Studies in Construction Materials. 2022. Vol. 16. N e01140. DOI: 10.1016/j.cscm.2022.e01140
- 31. Deng X.J., Klein B., Hallbom D.J. et al. Influence of Particle Size on the Basic and Time-Dependent Rheological Behaviors of Cemented Paste Backfill. Journal of Materials Engineering and Performance. 2018. Vol. 27. Iss. 7, p. 3478-3487. DOI: 10.1007/s11665-018-3467-7
- Xin Chen, Xiuzhi Shi, Jian Zhou et al. Effect of overflow tailings properties on cemented paste backfill. Journal of Environmental Management. 2019. Vol. 235, p. 133-144. DOI: 10.1016/j.jenvman.2019.01.040
- Deng X.J., Klein B., Zhang J.X. et al.Time-dependent rheological behaviour of cemented backfill mixture. International Journal of Mining, Reclamation and Environment. 2018. Vol. 32. Iss. 3, p. 145-162. DOI: 10.1080/17480930.2016.1239305
- 34. Qiangqiang Cheng, Yaben Guo, Chaowei Dong et al. Mechanical Properties of Clay Based Cemented Paste Backfill for Coal Recovery from Deep Mines. Energies. 2021. Vol. 14. Iss. 18. N 5764. DOI: 10.3390/en14185764
- Hane I., Belem T., Benzaazoua M., Maqsoud A. Laboratory Characterization of Cemented Tailings Paste Containing Crushed Waste Rocks for Improved Compressive Strength Development. Geotechnical and Geological Engineering. 2017. Vol. 35. Iss.2, p. 645-662. DOI: 10.1007/s10706-016-0131-6
- 36. Chaoqun Dai, Aixiang Wu, Yan Qi, Zhiqiang Chen. The Optimization of Mix Proportions for Cement Paste Backfill Materials via Box-Behnken Experimental Method. Journal of The Institution of Engineers (India): Series D. 2019. Vol. 100. 2, p. 307-316. DOI: 10.1007/s40033-019-00180-7
- 37. Ercikdi B., Cihangir F., Kesimal A. et al. Utilization of water-reducing admixtures in cemented paste backfill of sulphide-rich mill tailings. Journal of Hazardous Materials. 2010. Vol. 179. Iss. 1-3, p. 940-946. DOI: 10.1016/j.jhazmat.2010.03.096
- Kesimal A., Yilmaz E., Ercikdi B. et al. Effect of properties of tailings and binder on the short-and long-term strength and stability of cemented paste backfill. Materials Letters. 2005. Vol. 59. Iss. 28, p. 3703-3709. DOI: 10.1016/j.matlet.2005.06.042
- Meggyes T., Jefferis S.A. Mine Paste Backfill–The Behaviour of Thickened Tailings and Pipeline Design. GeoCongress 2012: State of the Art and Practice in Geotechnical Engineering: Proceedings of GeoCongress. 2012, 25-29 March 2012, Oakland, California, USA. ASCE, 2012, p. 4116-4125. DOI: 10.1061/9780784412121.423
- Walske M.L., McWilliam H., Doherty J., Fourie A. Influence of curing temperature and stress conditions on mechanical properties of cementing paste backfill. Canadian Geotechnical Journal. 2015. Vol. 52. N 1, p. 148-161. DOI: 10.1139/cgj-2014-0502
- Yilmaz T., Ercikdi B., Karaman K., Külekçi G. Assessment of strength properties of cemented paste backfill by ultrasonic pulse velocity test. Ultrasonics. 2014. Vol. 54. Iss. 5, p. 1386-1394. DOI: 10.1016/j.ultras.2014.02.012
- 42. Li Li. Analytical solution for determining the required strength of a side-exposed mine backfill containing a plug. Canadian Geotechnical Journal. 2014. Vol. 51. N 5, p. 508-519. DOI: 10.1139/cgj-2013-0227
- 43. Ercikdi B., Kesimal A., Cihangir F. et al. Cemented paste backfill of sulphide-rich tailings: Importance of binder type and dosage. Cement & Concrete Composites. 2009. Vol. 31. Iss. 4, p. 268-274. DOI: 10.1016/j.cemconcomp.2009.01.008
- 44. Jafari M., Shahsavari M., Grabinsky M. Drained Triaxial Compressive Shear Response of Cemented Paste Backfill (CPB). Rock Mechanics and Rock Engineering. 2021. Vol. 54. Iss. 6, p. 3309-3325. DOI: 10.1007/s00603-021-02464-5
- 45. Tariq A., Yanful E.K. A review of binders used in cemented paste tailings for underground and surface disposal practices. Journal of Environmental Management. 2013. Vol. 131, p. 138-149. DOI: 10.1016/j.jenvman.2013.09.039
- 46. Haiqiang Jiang, Fall M. Yield stress and strength of saline cemented tailings in sub-zero environments: Portland cement paste backfill. International Journal of Mineral Processing. 2017. Vol. 160, p. 68-75. DOI: 10.1016/j.minpro.2017.01.010
- 47. Cihangir F., Akyol Y. Effect of Desliming of Tailings on the Fresh and Hardened Properties of Paste Backfill Made from Alkali-Activated Slag. Advances in Materials Science and Engineering. 2020. Vol. 2020. N 4536257. DOI: 10.1155/2020/4536257
- Chi J.M., Ran Huang, Yang C.C. Effects of Carbonation on Mechanical Properties and Durability of Concrete Using Accelerated Testing Method. Journal of Marine Science and Technology. 2002. Vol. 10. Iss. 1, p. 14-20. DOI: 10.51400/2709-6998.2296
- Yoon-Moon Chun, Naik T.R., Kraus R.N.Carbon dioxide sequestration in concrete in different curing environments. Proc. Int. Conf: Sustainable construction materials and technologies, 11-13 June 2007, Coventry. Special papers proceedings, 2007, p. 18-24.
- 50. Kasap T., Yilmaz E., Sari M. Physico-chemical and micro-structural behavior of cemented mine backfill: Effect of pH in dam tailings. Journal of Environmental Management. 2022. Vol. 314. Iss. 4. N 115034. DOI: 10.1016/j.jenvman.2022.115034
- Pokharel M., Fall M. Combined influence of sulphate and temperature on the saturated hydraulic conductivity of hardened cemented paste backfill. Cement & Concrete Composites. 2013. Vol. 38, p. 21-28. DOI: 10.1016/j.cemconcomp.2013.03.015
- Fang K., Fall M. Effects of curing temperature on shear behaviour of cemented paste backfill-rock interface. International Journal of Rock Mechanics and Mining Sciences. 2018. Vol. 112, p. 184-192. DOI: 10.1016/j.ijrmms.2018.10.024
- 53. Raffaldi M.J., Seymour J.B., Richardson J. et al. Cemented Paste Backfill Geomechanics at a Narrow-Vein Underhand Cut-and-Fill Mine. Rock Mechanics and Rock Engineering. 2019. Vol. 52. Iss. 12, p. 4925-4940. DOI: 10.1007/s00603-019-01850-4
- Skobelev D.O., Cherepovitsyna A.A., Guseva T.V. Carbon capture and storage: net zero contribution and cost estimation approaches. Journal of Mining Institute. 2023. Vol. 259, p. 125-140. DOI: 10.31897/PMI.2023.10
- Shaposhnikov N.О., Golubev I.A., Khorobrov S.V. et al. Autoclave modeling of corrosion processes occurring in a gas pipeline during transportation of an unprepared multiphase medium containing CO2. Journal of Mining Institute. 2022. Vol. 258, p. 915-923. DOI: 10.31897/PMI.2022.92
- 56. Fedoseev S.V., Tcvetkov P.S. Key Factors of Public Perception of Carbon Dioxide Capture and Storage Projects. Journal of Mining Institute. Vol. 237, p. 361-368. DOI: 10.31897/PMI.2019.3.361
- Cherepovitsyn A., Chvileva T., Fedoseev S. Popularization of Carbon Capture and Storage Technology in Society: Principles and Methods. International Journal of Environmental Research and Public Health. 2020. Vol. 17. Iss. 22. N 8368. DOI: 10.3390/ijerph17228368
- Gür T.M. Carbon Dioxide Emissions, Capture, Storage and Utilization: Review of Materials, Processes and Technologies. Progress in Energy and Combustion Science. 2022. Vol. 89. N 100965. DOI: 10.1016/j.pecs.2021.100965
- 59. Kantyukov R.R., Zapevalov D.N., Vagapov R.K. Analysis of the application and impact of carbon dioxide media on the corrosion state of oil and gas facilities. Journal of Mining Institute. Vol. 250, p. 578-856. DOI: 10.31897/PMI.2021.4.11
- 60. Ilinova A.A., Romasheva N.V., Stroykov G.A. Prospects and social effects of carbon dioxide sequestration and utilization projects. Journal of Mining Institute. Vol. 244, p. 493-502. DOI: 10.31897/PMI.2020.4.12
- 61. Vasilev Yu., Cherepovitsyn A., Tsvetkova A., Komendantova N. Promoting Public Awareness of Carbon Capture and Storage Technologies in the Russian Federation: A System of Educational Activities. Energies. 2021. Vol. 14. Iss. 5. N 1408. DOI: 10.3390/en14051408
- 62. Ponomarev A.I., Yusupov A.D. Effect of shear stress on the wall of technological pipelines at a gas condensate field on the intensity of carbon dioxide corrosion. Journal of Mining Institute. Vol. 244, p. 439-447. DOI: 10.31897/PMI.2020.4.6
- 63. Cherepovitsyn A.E., Ilinova A.A., Evseeva O.O. Stakeholders management of carbon sequestration project in the state – business – society system. Journal of Mining Institute. Vol. 240, p. 731-742. DOI: 10.31897/PMI.2019.6.731
- Tcvetkov P. Engagement of resource-based economies in the fight against rising carbon emissions. Energy Reports. 2022. Vol. 8. S. 10, p. 874-883. DOI: 10.1016/j.egyr.2022.05.259
- Yilmaz E., Belem T., Benzaazoua M. Effects of curing and stress conditions on hydromechanical, geotechnical and geochemical properties of cemented paste backfill. Engineering Geology. 2014. Vol. 168, p. 23-37. DOI: 10.1016/j.enggeo.2013.10.024