Study of the possibility of using high mineralization water for hydraulic fracturing
- 1 — Ph.D., Dr.Sci. Professor Ufa State Petroleum Technological University ▪ Orcid ▪ Elibrary ▪ Scopus
- 2 — Ph.D., Dr.Sci. Director FSBEI of HE "Ufa State Petroleum Technological University", Branch of the University in the City of Oktyabrsky ▪ Orcid
- 3 — Head of the Department LLC “Gazpromneft S&TC” ▪ Orcid
- 4 — Ph.D. Head of the Laboratory NIPI “Neftegaz”, SOCAR ▪ Orcid
- 5 — Head of the Center LLC “Gazpromneft S&TC” ▪ Orcid
Abstract
The results of laboratory studies aimed at developing hydraulic fracturing fluid based on alternative sources of high mineralization water are presented. It is shown that Cenomanian sources have the most stable mineralization parameters, while bottom water and mixed waters collected from pressure maintenance systems differ significantly in their properties, with iron content varying several times, and hardness and mineralization undergoing substantial changes. The quality of the examined hydraulic fracturing fluids based on alternative water sources is confirmed by their impact on residual permeability, as well as residual proppant pack conductivity and permeability. The experimental results show similar values for these parameters. The comprehensive laboratory studies confirm the potential for industrial use of high mineralization water in hydraulic fracturing operations.
Funding
The research was fundedby the Ministry of Science and Higher Education of the Russian Federation under agreement N 075-15-2020-900 as part of the development program of the World-Class Research Center.
Introduction
The increasing consumption of natural resources by humanity, alongside with the increase of production capacities through active engagement in the development of with hard-to-recover deposits [1-3] poses a significant challenge reducing negative environmental impacts. There is a growing interest in solutions that enable optimization of industrial technologies aimed at lowering production costs, while considering both geological and physical properties of reservoirs [4-6] and minimizing environmental impact. Companies focused on technological development strive to offer innovations that meet new environmental requirements in the oil and gas sector.
One direction for optimizing and reducing current costs associated with hydraulic fracturing operations is the use of alternative sources for preparing hydraulic fracturing fluids, such as Cenomanian, mixed, or bottom waters. This solution allows for the optimization of the speed and quality of work performed without wasting resources or time [7-9]. The main objective of this study is to conduct research to determine the most stable guar-based hydraulic fracturing fluid system that allows for hydraulic fracturing operations using water with a high mineralization degree. To achieve this goal, it is necessary to address tasks related to evaluating the viscosity characteristics of fluids depending on various shear rates; assessing residual permeability and conductivity of the proppant pack; and determining the influence of hydraulic fracturing fluid (HF) on rock permeability under reservoir conditions. The aim is to determine hydraulic fracturing fluids with an optimal composition, including stabilizing additives, and to establish criteria for their applicability to real geological and reservoir conditions of fields, taking into account the features of modern hydraulic fracturing equipment. Additionally, methods and criteria for the applicability of stabilizing components will be developed to enable operations using bottom, mixed, or Cenomanian waters. The results obtained will allow for the “regulation” of hydraulic fracturing fluids during field operations to be carried out promptly based on the actual mineralogical composition in a stationary field laboratory, without the need for specialized equipment or costly studies.
Subject and relevance of the research
Hydraulic fracturing is one of the most effective technologies for intensifying production and injection wells operation [10-12]. This geological engineering activity (GEA) is a widely used technology that requires significant technical and material resources, considering the technological solutions conditioned by the particular geological facility [13-15]. It is noteworthy that due to the necessity of involving into development increasingly complex geological facilities [16-18], the hydraulic fracturing technology is evolving [19-21]. This evolution influences the increasing volumes of freshwater used for preparing fracturing fluids, chemical reagents, and technological equipment.
Given the global trend towards reducing production costs [22-24] and minimizing negative environmental impacts, the prospects for using high-mineralization waters for fracturing fluids are being considered. Such an approach can reduce environmental impact factors and lower the cost of extracted hydrocarbons [25-27]. One solution to this issue is the use of alternative (mineralized) water sources for preparing hydraulic fracturing fluids without special preliminary treatment. These sources include bottom waters, mixed waters (a combination of bottom and freshwater), and Cenomanian waters, which are typically utilized in pressure maintenance systems (PMS) of injection well fields [28].
A significant problem in using alternative water sources in hydraulic fracturing fluid systems is their aggressive chemical composition compared to traditional freshwater and, for the most part, surface water sources. This, in turn, necessitates the development of complex stabilizing and auxiliary additives that reduce the negative impact of high mineralization at all stages of preparing the hydraulic fracturing fluid, taking into account the actual composition of the specific source [29-31], and additionally, these additives should not impair the reservoir properties and should feature a simplified preparation technology.
According to the results of previously conducted studies on the influence of the technological fluid injected during hydraulic fracturing on the reservoir filtration-capacity properties (FCP), dependencies have been confirmed that indicate that with an increase in the volume of injected working fluid by 1 m of productive layer, there is a deterioration in FCP due to the clogging caused by the gelling agent present in the fluid system [32]. The development of a complex of auxiliary additives addresses the challenge of conducting HF operations using traditional concentrations of guar gelling agents. This approach allows for the proppant transportation with minimal reservoir and fractures contamination, which is one of the most relevant directions in the technological development of hydraulic fracturing [33]. The choice of working fluid system is always significant, as it affects the geometry of the fracture created, the proppant transportation quality and its placement in the reservoir, as well as the conductivity of the channels created during the operation. Thus, the characteristics of HF fluids are important parameters that require detailed study to achieve stable, predictable, and high-yielding well operations [34, 35].
The physicochemical properties of associated produced water depend on numerous factors, such as the geological structure of the deposit, mineral composition, chemical processes occurring during sediment accumulation, type of hydrocarbons, the activity and species of microorganisms, as well as reservoir temperature and pressure. Associated produced water contains suspended particles and various water-soluble components, representing a mixture of organic and inorganic compounds, some of which are present in formation water. Others emerge during the development and implementation of various geological and technological methods [36-38].
The assessment of water suitability for the preparation of hydraulic fracturing fluids is conducted based on a six-component water analysis, which allows for the rapid determination of the of key critical components content in the water. However, to understand the individual components influence on the properties of the fracturing fluid and to develop a high-quality, stable system, a more in-depth investigation of the source composition is required, utilizing a more comprehensive elemental analysis. The formulations of guar-based fluids are highly sensitive to the quality of the water used, particularly to the content of iron, calcium, and magnesium ions. Therefore, the use of unconditioned mineralized water without prior and costly treatment is not feasible. Previously proposed solutions for the potential use of bottom and Cenomanian waters have provided isolated approaches that do not sufficiently account for these critical factors. To improve the properties of guar-based HF fluids with borate crosslinkers, water-soluble amino alcohols were introduced into their composition, and chelating additives were applied to combat excessive hardness [39]. Most of these solutions are characterized by limitations on the compositions of “suitable” waters; some of them are associated with high costs due to the use of modified gelling agents [15, 40, 41] and/or crosslinkers [42-44].
Methodology
Based on the results of a series of tests, a methodology for the application of additives has been proposed, which allows for the rapid selection of the necessary components for the HF fluids preparation using alternative source waters, without requiring modifications to the primary functional components of the system – guar gelling agents and borate crosslinkers. To implement this task, the following laboratory investigations were conducted:
- Rheological properties investigation. Viscosity characteristics were evaluated depending on various shear rates at room temperature and atmospheric pressure, as well as under conditions approximating reservoir conditions. Such experiments adhere to international industry standards. The properties of the fluids were assessed using an atmospheric rotational viscometer with a coaxial cylinder system and a rotor-bob-spring geometry R1-B1-F1 (ISO 13503-1:2011), as well as high-pressure and high-temperature viscometers with a rotor-bob-spring geometry R1-B5-F1 (ISO 13503-1:2011).
- Assessing residual permeability and conductivity of proppant packs. The pack, contaminated with HF fluids, was studied using specialized equipment in accordance with ISO 13503-5 standards. Observations were made on sandstone core material. The proppant used for all tests was ceramic proppant with a 16/20 mesh size. The testing temperature was set at 90 °C, and readings were taken over a pressure range of 5000-9000 psi in 100 psi increments.
- Filtration studies to determine the HF fluids impact on rock permeability under reservoir-simulating conditions. The rocks were placed in a core holder, and reservoir conditions (pore pressure, temperature) were modeled, followed by oil circulation until stabilization of parameters, and then left to sit for 12 h. Subsequently, oil was pumped through the core column in the direction of reservoir-to-well, determining the working volumetric flow rate, corresponding to a linear flow rate of 3-5 m/day at 3-5 different flow rates, subsequently calculating the initial (base) permeability through oil. In the direction of well-to-reservoir, while maintaining constant repression, a broken gel solution was injected for the time required for HF operations. The system was held in static conditions for 12 h. Measurements of the amount of influent solution/filtrate into the core were taken. Following this, five pore volumes were injected into the core in the reservoir-to-well direction until stabilization pressure drop occurred, and filtration was performed using 3-5 different modes. Afterwards, permeability through oil was recalculated, with intermediate values fixed along the column.
Materials of the experiments
The subjects of the tests were real mineralized waters – Cenomanian, bottom, and mixed waters from the deposits of LLC “Gazpromneft-Khantos.” In total, more than 50 water samples were analyzed from over 15 sampling points (sources) and hydraulic fracturing fluids prepared based on them. Table 1 presents the average values of the main parameters for the three types of investigated waters. According to the test results, it is evident that the examined waters possess high salinity, and the content of the main elements depends on the type of water. The Cenomanian waters exhibit the most stable parameters, whereas the bottom and mixed waters sampled from the main formation-pressure maintenance system pipelines show significant differences in properties, with iron concentration varying considerably, and hardness and total mineralization also undergoing substantial changes. The primary reason for such behavior of the indicated water systems in the formation-pressure maintenance system is the unstable operating modes of the injection well stock, where the flow rates of bottom and fresh waters differ. Thus, the considered bottom, mixed, and Cenomanian waters have high mineralization, with the greatest contribution coming from chloride ions, sodium, calcium ions, and bicarbonates.
Table 1
Avarage individual parameter values depending on the water type
Parameter |
Water type |
||
Bottom |
Bottom + fresh (mixed) |
Cenomanian |
|
pH |
7.9 |
7.9 |
7.8 |
Density at 20 °C, g/cm3 |
1.005 |
1.003 |
1.010 |
Specific conductivity at 20 °C, µS/cm |
207 |
161 |
496 |
Suspended solids, mg/dm3 |
90 |
68 |
81 |
Total Fe, mg/dm3 |
2.5 |
3.0 |
6.5 |
Oil products, mg/dm3 |
4.0 |
3.3 |
0.2 |
Cl–, mg/dm3 |
3450 |
2463 |
9600 |
K+, mg/dm3 |
41 |
28 |
43 |
Na+, mg/dm3 |
3410 |
2175 |
5550 |
Ca2+, mg/dm3 |
263 |
198 |
360 |
Mg2+, mg/dm3 |
15 |
16 |
95 |
Sr2+, mg/dm3 |
7 |
5 |
29 |
Hardness, °dH (degrees of hardness) |
14.4 |
11.2 |
26.2 |
mg/dm3 |
1238 |
970 |
195 |
B+, mg/dm3 |
7.5 |
6.1 |
9.9 |
Total mineralization, mg/dm3 |
8449 |
5876 |
15900 |
Rheological studies of the fracturing fluids were conducted on water samples from the sources of LLC “Gazpromneft-Khantos” (sewage pumping stations for bottom and mixed water, separate wells for Senomanian.) To model the effect of the developed fracturing fluids on the rock permeability, and to evaluate the dynamic transport of the proppant agent, model compositions were prepared from pure salts that simulate bottom and Senoman water (Table 2). Table 3 presents the formulations of the fracturing gels used in complex tests on model mineralized waters. The compositions include auxiliary (stabilizing) additives – a pH buffer (linear gel stabilizer) and a crosslinking stabilizer.
Table 2
Model mineralized waters composition, g/l
Bottom water |
Cenomanian water |
||
Component |
Content |
Component |
Content |
NaHCO3 |
1.7048 |
NaHCO3 |
0.2688 |
NaCl |
4.7699 |
NaCl |
13.9291 |
KCl |
0.0789 |
KCl |
0.0820 |
MgCl2 |
0.0610 |
MgCl2 |
0.3768 |
CaCl2 |
0.7309 |
CaCl2 |
0.9990 |
FeCl3 |
0.0073 |
FeCl3 |
0.0189 |
H3BO3 |
0.0423 |
H3BO3 |
0.0558 |
Mineralization |
7.4 |
Mineralization |
15.73 |
Table 3
Guaro-borat formulation for water modelling
Bottom water |
Cenomanian water |
||
Component |
Concentration |
Component |
Concentration |
Gelling agent, kg/m3 |
3.6 |
Gelling agent, kg/m3 |
3.6 |
Crosslinker, l/m3 |
2.8 |
Crosslinker, l/m3 |
2.8 |
Demulsifier, l/m3 |
1.0 |
Demulsifier, l/m3 |
1.0 |
Biocide, kg/m3 |
0.02 |
Biocide, kg/m3 |
0.02 |
pH buffer, kg/m3 |
1.4 |
pH buffer, kg/m3 |
– |
Crosslinking stabilizer, l/m3 |
1.0 |
Crosslinking stabilizer, l/m3 |
1.0 |
Destructor, l/m3 |
0.5 |
Destructor, l/m3 |
0.5 |
Discussion
Rheological testing and methodology for selecting the design of fracturing fluids from alternative sources
To assess the impact of water from alternative sources composition, a series of rheological tests was conducted to evaluate the stability of a classical guar system with a gelling agent concentration of 3.6 kg/m3 and a borate crosslinker concentration of 3.0 l/m³ at a temperature of 90 °C. The established requirement for the stability time of the system (viscosity above 400 mPa·s), which guided the system development, is set at 100 (±20) min. The test results and the graph of this system using distilled water are presented in Fig.1. According to the provided graphs, the characteristic behavior of the fracturing fluid prepared with mineralized sources without auxiliary additives under the specified conditions can be considered as follows: the absence of crosslinking of the linear gel (Fig.1, a), the initial drop in viscosity (prolonged crosslinking) of the system (Fig.1, b), and insufficient high-temperature stability of the system (Fig.1, c). A combination of these negative manifestations cannot be ruled out. It is important to note the problems associated with the hydration of the guar polymer in mineralized water, as in some cases there is a lack of viscosity build-up of the linear gel, low hydration rates, and viscosity drop. Additionally, with significant concentrations of crosslinking elements in the water, the linear gel may achieve abnormally high viscosity.
To eliminate the aforementioned negative manifestations, targeted or complex actions are necessary to neutralize the negatively influencing components of water from alternative sources. The main elements or parameters of water that need to be neutralized are: increased water hardness (above 500 mg/l – 10 °dH); increased alkalinity (bicarbonate ion concentration above 500 mg/l); elevated iron content (above 8 mg/l); high mineralization (above 1000 mg/l); and the presence of crosslinking ions in the water.
The high content of bicarbonate ions (increased alkalinity) and the presence of divalent and trivalent metal ions negatively affect the hydration parameters of guar. In such cases, a stabilizer for the linear gel is used, which consists of a water-soluble organic acid. The addition of this agent is made to the water before the hydration of the polymer begins.
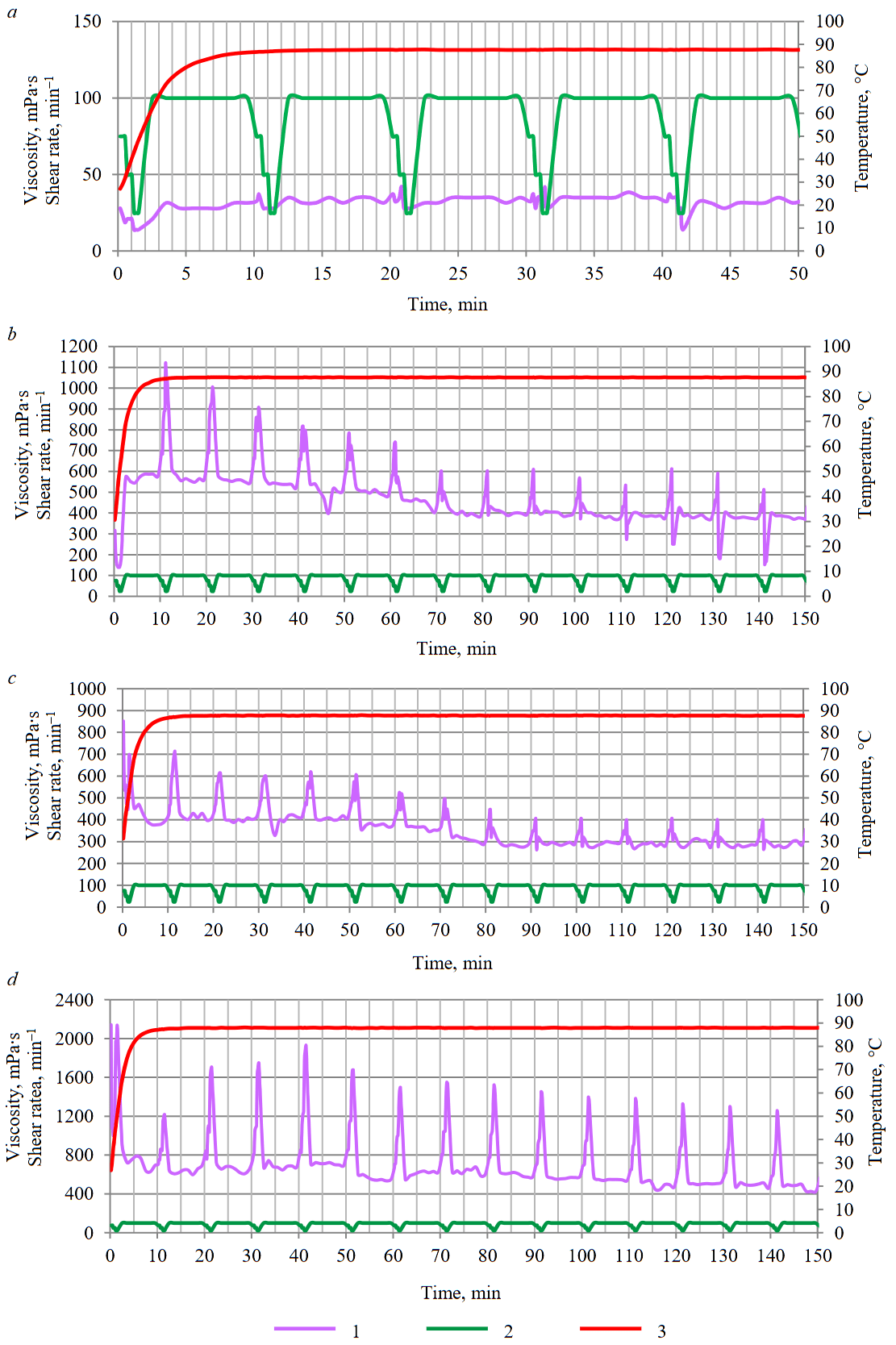
Fig.1. Classical guar system on water from alternative sources behavior: a – bottom water: mineralization 7700 mg/l, hardness 20 °dH, alkalinity 1200 mg/l; b – bottom water: mineralization 6800 mg/l, hardness 4 °dH, alkalinity 1400 mg/l; c – mixed water: mineralization 3300 mg/l, hardness 11 °dH, alkalinity 770 mg/l; d – fresh (distilled) water 1 – viscosity; 2 – shear rate; 3 – temperature
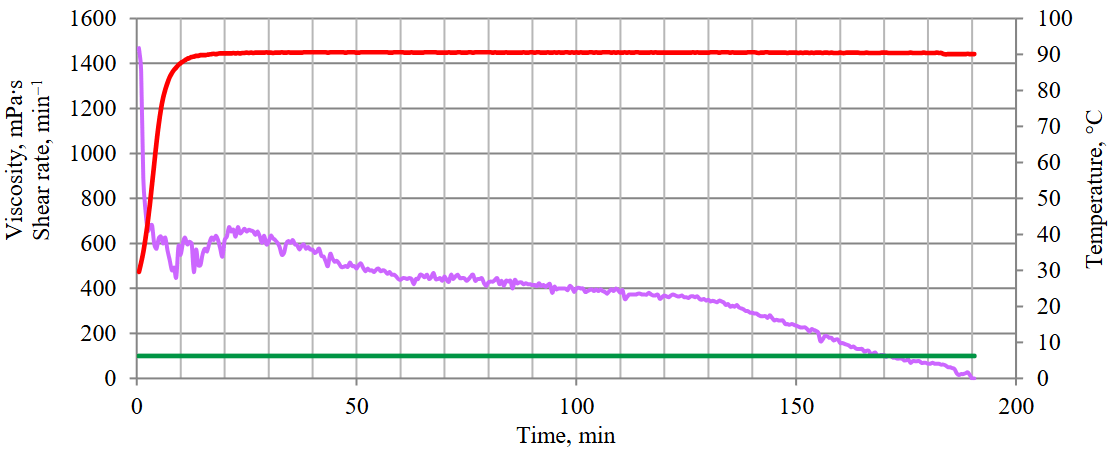
Fig.2. The change in the hydraulic fracturing fluid effective viscosity on the bottom water from the temperature and characteristics of the gels (at a constant value of the shear rate of 100 m/min). See the legend in Fig.1
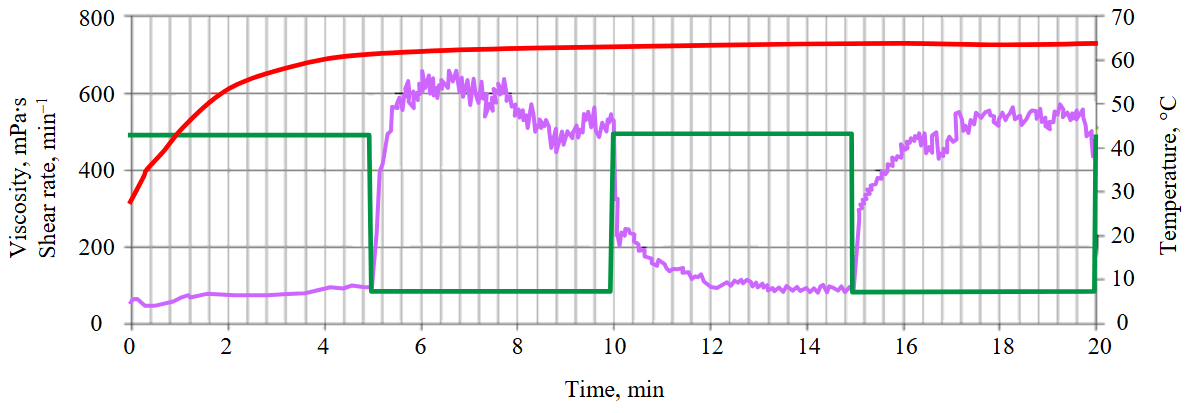
Fig.3. A test to determine the sensitivity of hydraulic fracturing fluid on bottom water to a change in shear load. See the legend in Fig.1
Increased water hardness is another negative parameter limiting the use of alternative sources for standard guar systems. Two directions have been proposed to solve this problem: the use of a chelating additive based on organic salt and the use of a combined crosslinking stabilizer based on amino alcohols. The results of a comprehensive study of the rheological properties of the developed systems in some real waters using the above stabilizers are presented.
- Bottom water – mineralization is 4700 mg/l, hardness is 2.4 °dH, alkalinity is 880 mg/l. Without specialized additives, the cross-linked system shows insufficient stability (about 50 min), which does not meet the criteria given earlier: bactericide is 0.02 l/m3, gel breaker is 2.0 l/m3, gelling agent is 3.6 kg/m3, destructor is 0.4 l/m3, delayed action cross-linker is 3.2 l/m3, crosslinking stabilizer is 1.0 l/m3.
The change in the effective viscosity of the liquid with hydraulic fracturing gels parameters from temperature is shown in Fig.2. The liquid stability at the specified component content is optimal for 100 min, which corresponds to the criteria set in the study: linear gel – viscosity is 26.0 mPa·s, closing temperature is 40 °C, pH value is 8.2; crosslinked gel – closing time of the funnel is 30 s, full crosslinking time is 45 s, pH value is 9.0.
Figure 3 shows the result of testing the sensitivity of the fracturing fluid closed on the bottom water to a change in the shear rate. The restoration of the system to the effective viscosity values after applied shear loads occurs in less than 30 s, which is an acceptable indicator for hydraulic fracturing operations. Static tests for the transportation of a proppant material, a ceramic proppant of fraction 16/20 with a concentration of 400 kg/m3, were carried out at a formation temperature. The results obtained under the same conditions on distilled water (without special additives) were compared. Both tests showed satisfactory results in comparison with freshwater systems. At the end of the hydraulic fracturing fluid rheological tests, a test for complete and rapid destruction was carried out. The viscosity of the destroyed gel was less than 5 mPa·s.
- Mixed water – mineralization is 5400 mg/l, hardness is 12 °dH, alkalinity is 710 mg/l. During the evaluation test, the additive-free system showed no crosslinking. The reason for the lack of crosslinking and the deterioration of the rheological properties of the system is the increased water mineralization, as well as high hardness, which determine the use of a crosslinking stabilizer and a chelating agent for this water. The formulation of the guar system for operation on mixed water is given: bactericide is 0.02 l/m3, demulsifier is 2.0 l/m3, linear gel stabilizer is 1.4 kg/m3, chelating agent is 0.25 kg/m3, gelling agent is 3.6 kg/m3, destructor is 0.5 l/m3, delayed action crosslinker is 2.8 l/m3, stabilizer crosslinking is 0.5 l/m3. The change in effective viscosity from temperature indicates acceptable stability of the system (Fig.4): linear gel – viscosity is 22.0 mPa·s, closing temperature is 40 °C, pH value is 5.6; crosslinked gel – closing time of the funnel is 60 s, full crosslinking time is 65 s, pH value is 8.6. Figure 5 shows the result of testing hydraulic fracturing fluid on mixed water for its sensitivity to shear rate changes.
- Cenomanian – mineralization is 17300 mg/l, hardness is 30 °dH, alkalinity is 190 mg/l. A feature of the behavior of the system at most Cenomanian sources in the case of using no stabilizers is high temperature destruction. To obtain the required properties, the main emphasis is placed on suppressing increased mineralization and hardness in comparison with bottom and mixed sources. The use of a linear gel stabilizer in such cases is either not required at all, or is limited to low dosages. The high water hardness is neutralized by the chelating agent and/or a crosslinking stabilizer introduction into the classical guar system. The results of the work on the fracturing fluid system design selection at the Cenomanian source: bactericide is 0.02 l/m3, demulsifier is 2.0 l/m3, gelling agent is 3.6 kg/m3, destructor is 0.5 l/m3, delayed action crosslinker is 3.0 l/m3, crosslinking stabilizer is 2.0 l/m3. Figure 6 shows the change in the hydraulic fracturing fluid effective viscosity from the temperature with gel parameters: linear gel viscosity is 26.0 mPa·s, closing temperature is 40 °C, pH value is 7.6; crosslinked gel – funnel closing time is 30 s, full crosslinking time is 45 s, pH value is 9.0. Liquid stability at the specified content of the components is the optimal 100 min. Figure 7 shows the system under consideration behavior under shear loads. Of the listed negatively affecting components, it is also necessary to consider the increased iron content and crosslinking ions contained in water. From the practice of hydraulic fracturing operations, compositions of stabilizers are known, for example, based on sugars, which effectively suppress the action of this element. The stabilizing additives noted in rheological tests are also able to effectively affect the excess iron in the waters of alternative sources. The issue of boron ion suppression is solved, as a rule, by introducing crosslinking retarders based on highly soluble sugars into the system.
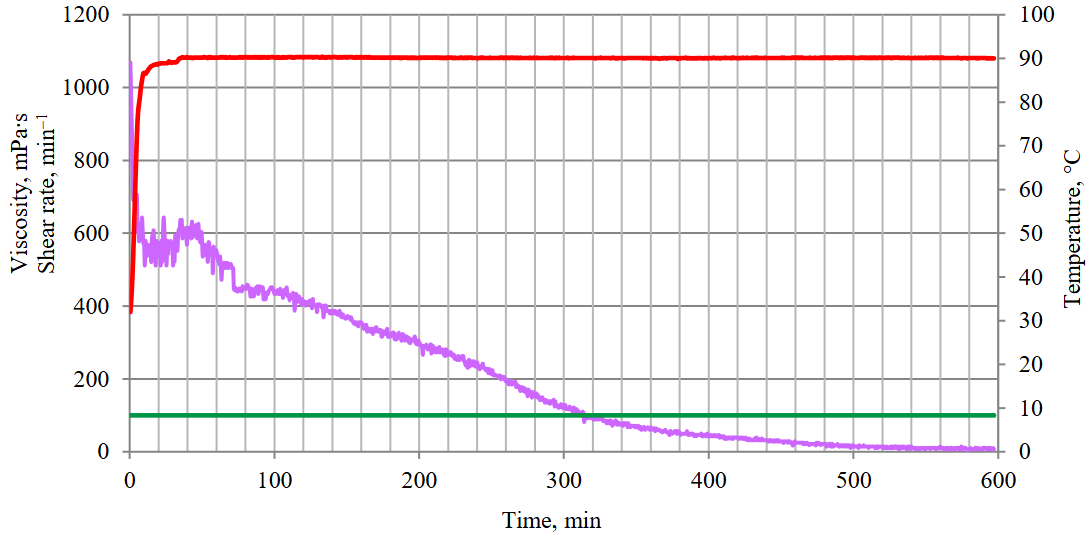
Fig.4. The change in the effective viscosity of the hydraulic fracturing fluid in mixed water from the temperature and gels characteristics (at a constant shear rate value of 100 m/min).
See the legend in Fig.1
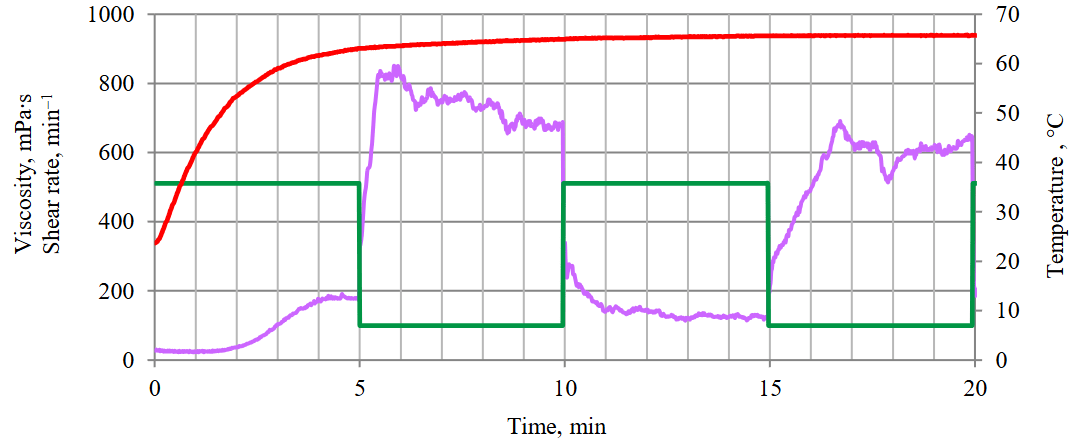
Fig.5. Test to determine the sensitivity of hydraulic fracturing fluid on mixed water to shear load.
See the legend in Fig.1
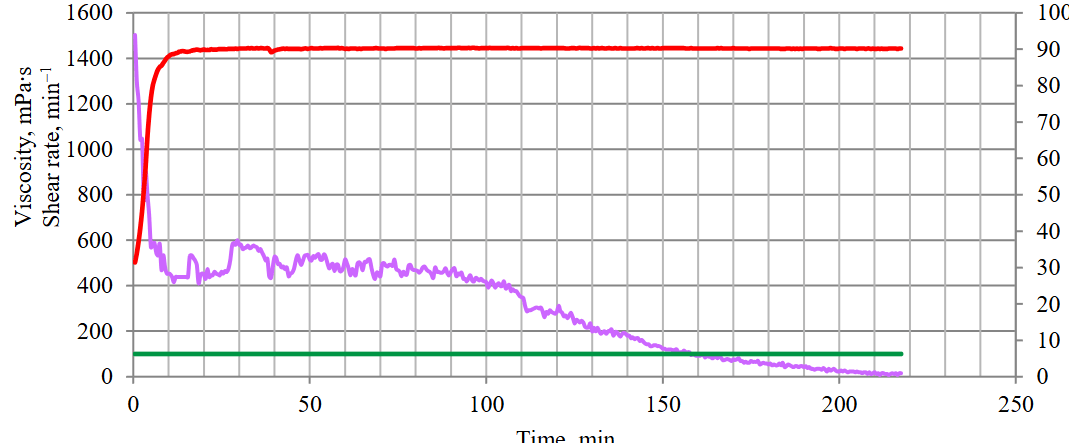
Fig.6. The change in the effective viscosity of the hydraulic fracturing fluid in Cenomanian water from the temperature and gels characteristics (at a constant shear rate of 100 m/min).
See the legend in Fig.1
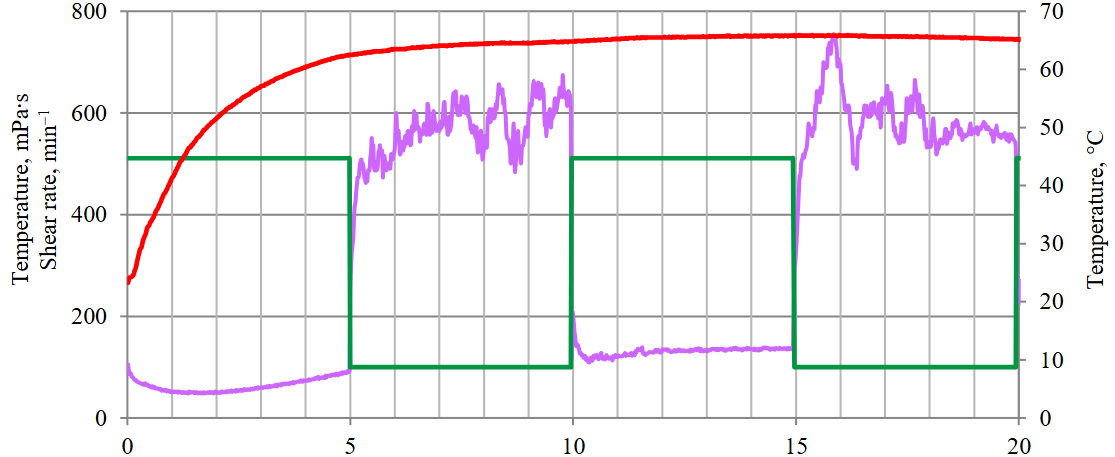
Fig.7. Test to determine the sensitivity of hydraulic fracturing fluid to changes in shear load at the Cenomanian source. See the legend in Fig.1
Core tests
One of the key factors determining the fluid work efficiency after the fracturing
operation is its effect on the rock reservoir properties. As part of a comprehensive study, tests of the developed hydraulic fracturing fluid designs that have successfully passed rheological tests were carried out to assess the impact on the rock properties. The compositions of hydraulic fracturing fluids (Table 3) on mineralized waters (see Table 2) tested on the core material of the Priobsky and Yuzhno-Priobsky deposits (target formation AC12.3-5), which investigated the effect of compositions on the rock permeability under conditions simulating formation conditions. Lithologically, the samples are represented by sandstones and siltstones. The open water porosity, determined from 40 samples, varies from 13.8 to 18.7 % (the average value is 16.4 %). The open porosity of helium,
determined from 104 samples, varies from 2.3 to 18.4 % (the average value is 14.3 %). After that, tests were carried out to assess the effect of hydraulic fracturing fluids on rock permeability (Table 4).
Table 4
Generalized results of determining the hydraulic fracturing fluids effect on reservoir rock permeability
Type of hydraulic fracturing fluid |
Laboratory number of the sample |
Open porosity by water, % |
Absolute |
Residual water saturation Kw, % |
The basic permeability of the oil sample, 10–3mkm2 |
Permeability recovery coefficient after |
Permeability recovery after depression coefficient, % |
Water saturation after operation value, % |
Change in water saturation, % |
Gel 1 Bottom water/ guar system |
28244-10 |
14,4 |
1,23 |
36,6 |
0,334 |
19,7 |
32,1 |
25,0 |
–11,5 |
28229-10 |
16,4 |
1,08 |
44,1 |
0,240 |
23,6 |
45,7 |
35,5 |
–8,6 |
|
23596-18 |
16,5 |
0,91 |
39,4 |
0,197 |
27,8 |
42,6 |
30,5 |
–8,9 |
|
28159-10 |
16,6 |
0,75 |
41,9 |
0,120 |
43,5 |
60,6 |
35,2 |
–6,7 |
|
|
|
15,9 |
0,99 |
40,5 |
0,223 |
28,6 |
45,2 |
31,6 |
–8,9 |
Gel 2 Cenomanian water/ guar system |
28235-10 |
16,5 |
1,14 |
38,6 |
0,255 |
23,1 |
39,7 |
29,4 |
–9,2 |
28242-10 |
15,3 |
1,04 |
37,2 |
0,186 |
21,9 |
43,3 |
29,5 |
–7,7 |
|
28154-10 |
16,1 |
0,87 |
41,7 |
0,127 |
28,3 |
40,3 |
34,0 |
–7,7 |
|
28237-10 |
15,7 |
0,69 |
42,5 |
0,102 |
29,8 |
38,3 |
33,7 |
–8,8 |
|
|
|
15,9 |
0,94 |
40,0 |
0,168 |
25,8 |
40,4 |
31,7 |
–8,4 |
Gel 3 Distilled water/ guar system |
23625-18 |
15,7 |
1,70 |
34,1 |
0,452 |
23,37 |
35,03 |
28,7 |
–5,4 |
According to the results obtained, systems based on alternative sources are not inferior to the guar system in terms of their effect on the residual permeability of the reservoir prepared with distilled water. This is evidenced by permeability recovery coefficients values, which indicate that the permeability during the period from the immediate hydraulic fracturing to the start of commissioning of the well is restored by 1.5 times due to the time of helium composition destruction.
Conclusions
The bottom, mixed, and Cenomanian waters considered in this article have a high mineralization, the greatest contribution to which is made by chlorine ion, sodium ions, calcium and bicarbonates. The determining factor in liquid and stabilizing additive choosing is the composition and properties of water from a single source, which are subject to significant change and depend on many factors such as time and method of selection, temperature, interaction with the environment, etc.
Cenomanian sources have the most stable mineralization parameters, while the bottom and mixed waters selected from the pressure maintenance system have significant differences in properties. For such sources, the amount of iron can vary significantly, and the hardness and overall mineralization also undergo significant changes.
The quality of the considered fracturing fluids based on alternative water sources is confirmed by their effect on the residual formation permeability, as well as the residual permeability and proppant pack permeability. The experimental results presented in this paper show similar values of these parameters. The results of studies on the determination of the remaining conductivity and permeability of the proppant pack at 6000 psi showed that for guar, Cenomanian and fresh waters, the residual conductivity was respectively 38; 37; 36 %, and the residual permeability was 38; 38; 36 %.
The considered hydraulic fracturing fluids based on alternative water sources are a promising direction for industrial use in the oil industry, as they contribute to reducing the produced hydrocarbons cost by minimizing the cost of their preparation and delivery, reducing the negative impact on the environment while maintaining the quality inherent in classical systems of liquid at fresh sources. For the best understanding of the key properties and features of the developed formulations, large-scale pilot tests are necessary, which will consolidate and improve the results achieved at the current stage.
References
- Kontorovich A.E., Burshtein L.M., Livshits V.R., Ryzhkova S.V. Main Directions of Development of the Oil Complex of Russia in the First Half of the Twenty-First Century. Herald of the RAS. 2019. Vol. 89. N 6, p. 558-566. DOI: 10.31857/S0869-587389111095-1104
- Dmitrievsky A.N. Resource-innovative strategy for the development of the Russian economy. Oil Industry Journal. 2017. N 5, p. 6-7 (in Russian).
- Muslimov R.Kh. A new strategy for the development of oil fields in modern Russia is to optimize production and maximize KIN (oil recovery factor). Neft. Gaz. Novatsii. 2016. N 4 (187), p. 8-17 (in Russian).
- Mukhametshin V.Sh., Khakimzyanov I.N., Bakhtizin R.N., Kuleshova L.S. Differentiation and grouping of complex-structured oil reservoirs in carbonate reservoirs in development management problems solving. SOCAR Proceedings. 2021. Special Issue 1, p. 88-97 (in Russian). DOI: 10.5510/OGP2021SI100513
- Mukhametshin V.V., Bakhtizin R.N., Kuleshova L.S. et al. Screening and assessing the conditions for effective oil recovery enhancing techniques application for hard to recover high-water cut reserves. SOCAR Proceedings. 2021. Special Issue 2, p. 48-56 (in Russian). DOI: 10.5510/OGP2021SI200588
- Yang S., Siddhamshetty P., Kwon J. S.-I. Optimal pumping schedule design to achieve a uniform proppant concentration level in hydraulic fracturing. Computers & Chemical Engineering. 2017. Vol. 101, p. 138-147. DOI: 10.1016/j.compchemeng.2017.02.035
- Grishchenko V.A., Rabaev R.U., Asylgareev I.N. et al. Methodological approach to optimal geological and technological characteristics determining when planning hydraulic fracturing at multilayer facilities. SOCAR Proceedings. 2021. Special Issue 2, p. 182-191 (in Russian). DOI: 10.5510/OGP2021SI200587
- Grishchenko V.A., Pozdnyakova T.V., Mukhamadiyev B.M. et al. Improving the carbonate reservoirs development efficiency on the example of the Tournaisian stage deposits. SOCAR Proceedings. 2021. Special Issue 2, p. 238-247 (in Russian). DOI: 10.5510/OGP2021SI200603
- Wijaya N., Sheng J.J. Comparative study of well soaking timing (pre vs. post flowback) for water blockage removal from matrix-fracture interface. Petroleum. 2020. Vol. 6. Iss. 3, p. 286-292. DOI: 10.1016/j.petlm.2019.11.001
- Mukhametshin V.V. Eliminating uncertainties in solving bottom hole zone stimulation tasks. Bulletin of the Tomsk Polytechnic University. Geo Assets Engineering. 2017. Vol. 328. N 7, p. 40-50 (in Russian).
- Khisamiev T.R., Bashirov I.R., Mukhametshin V.Sh. et al. Results of the development system optimization and increasing the efficiency of carbonate reserves extraction of the turney stage of the Chetyrmansky deposit. SOCAR Proceedings. 2021. Special Issue 2, p. 131-142 (in Russian). DOI: 10.5510/OGP2021SI200598
- Jiaxiang Xu, Yunhong Ding, Lifeng Yang et al. Effect of proppant deformation and embedment on fracture conductivity after fracturing fluid loss. Journal of Natural Gas Science and Engineering. 2019. Vol. 71. N 102986. DOI: 10.1016/j.jngse.2019.102986
- Galkin V.I., Koltyrin A.N. Investigation of probabilistic models for forecasting the efficiency of proppant hydraulic fracturing technology. Journal of Mining Institute. 2020. Vol. 246, p. 650-659. DOI: 10.31897/PMI.2020.6.7
- Yakupov R.F., Mukhametshin V.Sh., Khakimzyanov I.N., Trofimov V.E. Optimization of reserve production from water oil zones of D3ps horizon of Shkapovsky oil field by means of horizontal wells. Georesources. 2019. Vol. 21. N 3, p. 55-61 (in Russian). DOI: 10.18599/grs.2019.3.55-61
- Fokker P.A., Borello E.S., Verga F., Viberti D. Harmonic pulse testing for well performance monitoring. Journal of Petroleum Science and Engineering. 2018. Vol. 162, p. 446-459. DOI: 10.1016/j.petrol.2017.12.053
- Grishchenko V.A., Gareev R.R., Tsiklis I.M. et al. Expanding the amount of preferential royalty facilities with hard-to-recover oil reserves. SOCAR Proceedings. 2021. Special Issue 2, p. 8-17 (in Russian). DOI: 10.5510/OGP2021SI200575
- Cheng Jing, Xiaowei Dong, Wenhao Cui et al. Artificial neural network-based time-domain interwell tracer testing for ultralow-permeability fractured reservoirs. Journal of Petroleum Science and Engineering. 2020. Vol. 195. N 107558. DOI: 10.1016/j.petrol.2020.107558
- Yakupov R.F., Mukhametshin V.S., Tyncherov K.T. Filtration model of oil coning in a bottom water-drive reservoir. Periódico Tchê Química. 2018. Vol. 15. Iss. 30, p. 725-733. DOI: 10.52571/PTQ.v15.n30.2018.725_Periodico30_pgs_725_733.pdf
- Fattakhov I.G., Kuleshova L.S., Bakhtizin R.N. et al. Complexing the hydraulic fracturing simulation results when hybrid acid-propant treatment performing and with the simultaneous hydraulic fracture initiation in separated intervals. SOCAR Proceedings. 2021. Special Issue 2, p. 103-111 (in Russian). DOI: 10.5510/OGP2021SI200577
- Kuleshova L.S., Fattakhov I.G., Sultanov Sh.Kh. et al. Experience in conducting multi-zone hydraulic fracturing on the oilfield of PJSC “Tatneft”. SOCAR Proceedings. 2021. Special Issue 1, p. 68-76 (in Russian). DOI: 10.5510/OGP2021SI100511
- Keshavarz A., Yulong Yang, Badalyan A. et al. Laboratory-based mathematical modelling of graded proppant injection in CBM reservoirs. International Journal of Coal Geology. 2014. Vol. 136, p. 1-16. DOI: 10.1016/j.coal.2014.10.005
- Grishchenko V.A., Asylgareev I.N., Bakhtizin R.N. et al. Methodological approach to the resource base efficiency monitoring in oil fields development. SOCAR Proceedings. 2021. Special Issue 2, p. 229-237 (in Russian). DOI: 10.5510/OGP2021SI200604
- Mukhametshin V.V. Improving the Efficiency of Managing the Development of the West Siberian Oil and Gas Province Fields on the Basis of Differentiation and Grouping. Russian Geology and Geophysics. 2021. Vol. 62. N 12, p. 1373-1384. DOI: 10.15372/GiG2021102
- Nurgaliev R.Z., Kozikhin R.A., Fattakhov I.G., Kuleshova L.S. Application prospects for new technologies in geological and technological risk assessment. Gornyi zhurnal. 2019. N 4, p. 36-40 (in Russian). DOI: 10.17580/gzh.2019.04.08
- Temizel C., Canbaz C.H., Palabiyik Y. et al. A Review of Hydraulic Fracturing and Latest Developments in Unconventional Reservoirs. Offshore Technology Conference, 2-5 May 2022, Houston, TX, USA. OnePetro, 2022. N OTC-31942-MS. DOI: 10.4043/31942-MS
- Linsong Cheng, Deqiang Wang, Renyi Cao, Rufeng Xia. The influence of hydraulic fractures on oil recovery by water flooding processes in tight oil reservoirs: An experimental and numerical approach. Journal of Petroleum Science and Engineering. 2020. Vol. 185. N 106572. DOI: 10.1016/j.petrol.2019.106572
- Khuzin R.R., Andreev V.E., Mukhametshin V.V. et al. Influence of hydraulic compression on porosity and permeability properties of reservoirs. Journal of Mining Institute. 2021. Vol. 251, p. 688-697. DOI: 10.31897/PMI.2021.5.8
- Nesic S., Streletskaya V.V. An integrated approach for produced water treatment and injection. Georesources. 2018. Vol. 20. N 1, p. 25-31. DOI: 10.18599/grs.2018.1.25-31
- Kontorovich A.E., Varlamov A.I., Efimov A.S. et al. Stratigraphic Scheme of Cambrian Deposits, South of the Cis-Yenisei Area of West Siberia. Russian Geology and Geophysics. 2021. Vol. 62. N 3, p. 357-376. DOI: 10.15372/GiG2020206
- Stabinskas A.P., Sultanov Sh.Kh., Mukhametshin V.Sh. et al. Evolution of hydraulic fracturing fluid: from guar systems to synthetic gelling polymers. SOCAR Proceedings. 2021. Special Issue 2, p. 172-181 (in Russian). DOI: 10.5510/OGP2021SI200599
- Sergeev V.V., Sharapov R.R., Kudymov A.Y. et al. Experimental research of the colloidal systems with nanoparticles influence on filtration characteristics of hydraulic fractures. Nanotechnologies in Construction. 2020. Vol. 12. N 2, p. 100-107. DOI: 10.15828/2075-8545-2020-12-2-100-107
- Stabinskas A.P. Efficiency estimation of oil well after hydraulic fracturing treatment. Problems of Gathering, Treatment and Transportation of Oil and Oil Products. 2014. N 1 (95), p. 10-20 (in Russian).
- 33.Chenguang Zhang, Xiting Long, Xiangwei Tang et al. Implementation of water treatment processes to optimize the water saving in chemically enhanced oil recovery and hydraulic fracturing methods. Energy Reports. 2021. Vol. 7, p. 1720-1727. DOI: 10.1016/j.egyr.2021.03.027
- Zakharov L.A., Martyushev D.A., Ponomareva I.N. Predicting dynamic formation pressure using artificial intelligence methods. Journal of Mining Institute. 2022. Vol. 253, p. 23-32. DOI: 10.31897/PMI.2022.11
- Krivoshchekov S.N., Kochnev A.A., Ravelev K.A. Development of an algorithm for determining the technological parameters of acid composition injection during treatment of the near-bottomhole zone, taking into account economic efficiency. Journal of Mining Institute. 2021. Vol. 250, p. 587-595. DOI: 10.31897/PMI.2021.4.12
- Khuzin R.R., Andreev V.E., Mukhametshin V.V. et al. Influence of hydraulic compression on porosity and permeability properties of reservoirs. Journal of Mining Institute. 2021. Vol. 251, p. 688-697. DOI: 10.31897/PMI.2021.5.8
- Siddhamshetty P., Mao S., Wu K., Kwon J.S.-I. Multi-Size Proppant Pumping Schedule of Hydraulic Fracturing: Application to a MP-PIC Model of Unconventional Reservoir for Enhanced Gas Production. Processes. 2020. Vol. 8. Iss. 5. N 570. DOI: 10.3390/pr8050570
- Veil J.A., Clark C. Produced Water Volume Estimates and Management Practices. SPE Production & Operations. 2011. Vol. 26. Iss. 3, p. 234-239. DOI: 10.2118/125999-PA
- Sun Huning, Xie Xuan, Gao Guanghui et al. Patent N CN 10275778 B. Fracturing fluid capable of resisting high salinity water quality. Publ. 14.08.2012.
- Rogachev M.K., Mukhametshin V.V., Kuleshova L.S. Improving the efficiency of using resource base of liquid hydrocarbons in Jurassic deposits of Western Siberia. Journal of Mining Institute. 2019. Vol. 240, p. 711-715. DOI: 10.31897/PMI.2019.6.711
- Shlyapkin A.S., Tatosov A.V. Formation of a hydraulic fracture by a high-viscous gel. Geology, Geophysics and Development of Oil and Gas Fields. 2020. N 9 (345), p. 109-112 (in Russian). DOI: 10.30713/2413-5011-2020-9(345)-109-112
- Kakadjian S., Thompson J., Torres R. Fracturing Fluids from Produced Water / SPE Production and Operations Symposium, 1-5 March 2015, Oklahoma City, OK, USA. OnePetro, 2015. N SPE-173602-MS.
- Wang Shi Ben, Guo Jian Chun, Lai Ji et al. Patent N CN 103497753 B. One is applicable to the of the fracturing fluid linking agent of concentrated water. Publ. 30.09.2013.
- Siddhamshetty P., Seeyub Yang, Kwon J.S.-I. Modeling of hydraulic fracturing and designing of online pumping schedules to achieve uniform proppant concentration in conventional oil reservoirs. Computers & Chemical Engineering. 2018. Vol. 114, p. 306-317. DOI: 10.1016/j.compchemeng.2017.10.032