Technologies of intensive development of potash seams by longwall faces at great depths: current problems, areas of improvement
- 1 — Ph.D., Dr.Sci. Head of Department Saint Petersburg Mining University ▪ Orcid
- 2 — Postgraduate Student Saint Petersburg Mining University ▪ Orcid
Abstract
The results of the analysis of practical experience in the development of potash seams using longwall mining systems at the mines of OAO “Belaruskali” are presented. Positive changes in the technical and economic indicators of mines and an increase in the safety of mining operations were noted with the introduction of resource-saving technologies without leaving the pillars between the excavation columns or with leaving the pillars between the columns with dimensions at which they are destroyed by mining pressure in the goaf. It is noted that the use of mechanized stoping complexes characterized by high energy capacity, combined with large depths of development, is the main reason for the temperature increase in longwalls to values exceeding the maximum permissible air temperature regulated by sanitary standards. Based on production studies, it was concluded that the temperature regime along the length of the longwall face is determined by the temperature of rocks in the developed longwall space, heat emissions from the equipment of the power train, and the temperature of the rock mass ahead of the longwall. The conclusion has been drawn about the feasibility of using developed technological schemes in deep mining conditions, which provide a reduction in longwall temperature by 6-9 °C or more through isolated ventilation of longwall and power trains, as well as heat exchange between the airflow entering the longwall and the rocks in the developed space.
Introduction
Reducing losses of potassium and potassium-magnesium salts during their extraction, which account for 70 % or more, is one of the most pressing issues in the global mining science. Preconditions for reducing losses of this valuable non-renewable natural resource are created when using technologies for mining potassium seams with longwall methods. The peculiarities of development and directions for improving technological schemes are considered using the example of the mines of OAO “Belaruskali”, where over 45 years of unique global practical experience has been accumulated in the use of various options for longwall mining systems. The share of potassium seam extraction using the longwall mining system in the mines of OAO “Belaruskali” reaches 90 % [1].
Significant contributions to the improvement of technologies for working potassium layers, taking into account changing geological and mining conditions, have been made by the Saint Petersburg Mining University, OAO “Belgorkhimprom”, ZAO “Soligorsk Institute of Resource Conservation Problems with Experimental Production”, and others.
Practical experience in using longwall mining systems has confirmed the concept proposed in 2002-2003 [2, 3] for the development of main productive layers of OAO “Belaruskali”, determining the directions for improving the technological schemes of mines for the next 17-18 years. The basis of this concept was the provision “...on the need to conduct stoping works without leaving pillars between the extraction columns, or with the presence of flexible pillars between them, with dimensions at which their destruction occurs due to rock pressure in the developed space”.
According to the specified concept, currently almost all panels of the lower sylvite layer of the Third Potassium Horizon, which is the main productive layer at the mines of Belaruskali, are being developed and designed for development [4]. This has created conditions for a significant increase (from 60-70 to 85-90 %) [2, 5] in mineral extraction; reducing the likelihood of sudden salt and gas outbursts from the rock layers in the developed space of the lower technological layer, including the 2nd and 3rd sylvite layers [2, 6]; reducing the danger of mining operations and significant irrecoverable production losses associated with dynamic roof rock collapses in the developed space of the lower technological layer [2, 6]. Technological schemes without leaving pillars between the extraction columns or with leaving pillars of dimensions that cause their destruction by rock pressure in the developed space are considered the most promising [5, 7, 8].
The mines of the OAO “Belaruskali” are characterized by:
- dynamic growth of production capacities, which is associated with the implementation of high-performance mechanized stoping complexes;
- increasing the share of mining using resource-saving longwall development systems;
- increasing the temperature of host rocks, which is associated with intensive development of the main productive layers and the transition of mining operations to deeper horizons [9].
The equipment of the new SL series combines with installed electric motor power of 480-550 kW allows increasing the ore extraction from the longwall to 2.0 million t per year [10]. However, the high energy capacity of the stoping equipment, combined with the actual mining conditions [11-13], is one of the main reasons for the elevated air temperature in the ventilation drives [14]. Practically in all panels at depths of productive layers exceeding 500-600 m, the air jet temperature in the mechanized complexes substantially exceeds (by 3-6 °C) the permissible air temperature determined by the factor “providing safe and productive working conditions for miners” and regulated by applicable regulatory documents.
In accordance with SanPiN “Hygienic Requirements for Microclimate in the Design and Operation of Potash Mines” (paragraph 24, chapter 3) and the rules for ensuring industrial safety during the underground development of salt deposits in the Republic of Belarus (paragraph 171), the air temperature in the ventilation workings should not exceed 26 °C. At an air temperature at the workplace equal to 30 °C, the duration of the workday cannot exceed 5 h; at 31 °C – 3 h; at 32 °C – 2 h; at 32.5 °C – 1 h. Similar requirements are imposed on the temperature regime in Russian coal mines in accordance with Articles 209 and 212 of the Labor Code of the Russian Fede-ration. Non-compliance with the requirements of regulatory documents regarding the temperature regime adversely affects the health of miners, contributes to the development of occupational diseases, and increases the risks of occupational injuries [15].
Well-known underground air conditioning systems for reducing the temperature of the air in the longwall [16, 17] have not found widespread use in the mines of OAO “Belaruskali” due to significant economic costs and difficulties in adapting to resource-saving technologies. Taking into account the noted facts and the actualization of social issues, the development of organizational and technical solutions to ensure the thermal regime in the longwall should be considered as one of the main directions for improving the perspective resource-saving technologies for potassium deposits in the mines of OAO “Belaruskali” [9, 10, 18], in accordance with SanPiN “Hygienic requirements for microclimate in the design and operation of potassium mines” and rules for ensuring industrial safety in the development of underground salt deposits in the Republic of Belarus.
The aim of the research is to develop a resource-saving system for working potassium deposits in conditions of deep horizons, which provides a reduction in the temperature of the air in the longwall and is characterized by high energy capacity of the stoping equipment, without using underground air conditioning systems (Fig.1).
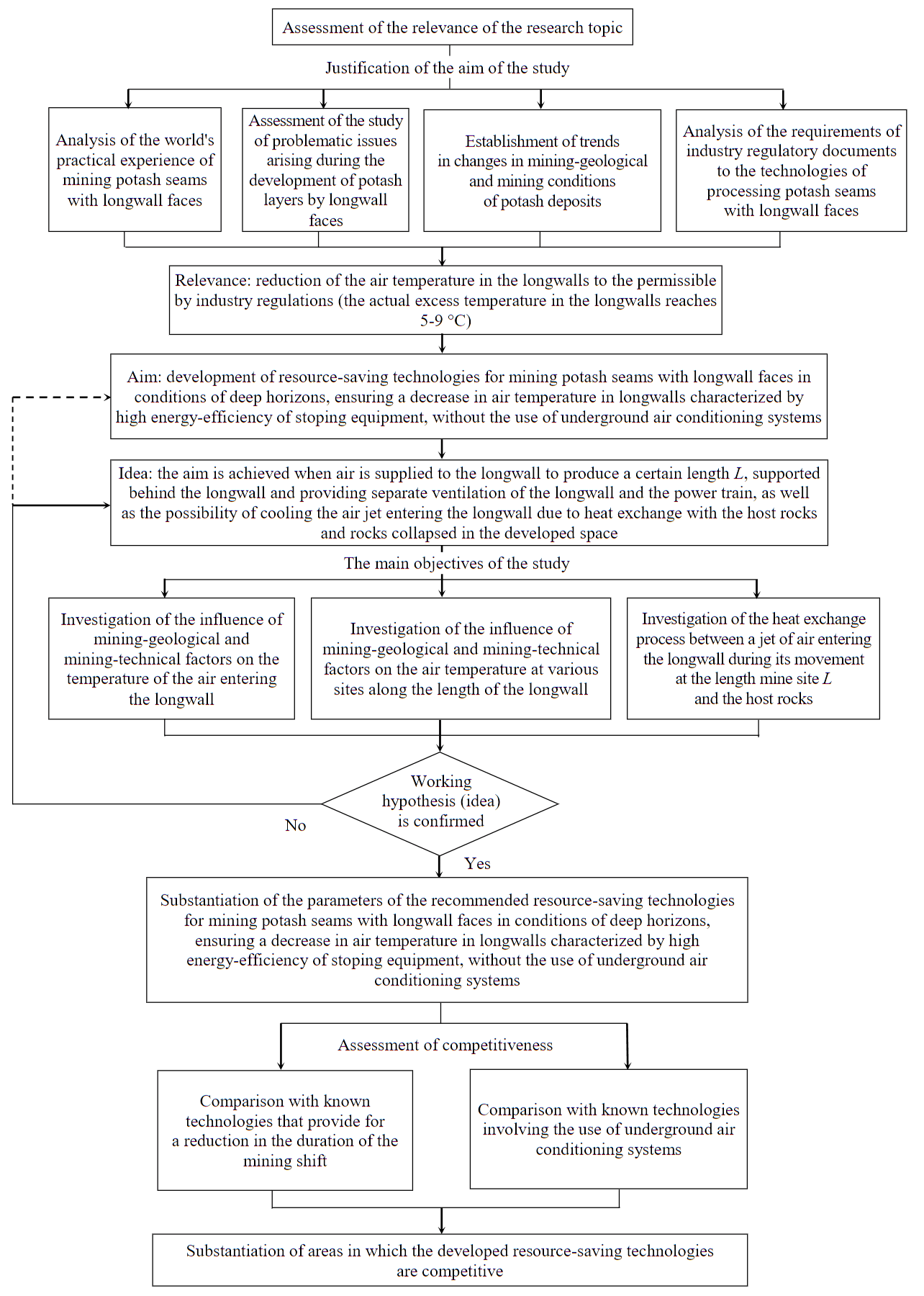
Fig.1. Research algorithm
Additional requirements for the developed technology include:
- easy adaptation to existing technological schemes of mines, ventilation and transportation schemes;
- possibility of pilot-industrial testing and implementation in worked-out sections (panels);
- minimization of temporary and financial costs associated with the implementation of the developed technical solutions.
Methodology
In accordance with the stated goal (Fig.1), the main tasks of mine research were:
- identification of the main reasons for the increase in the temperature in the longwall above the temperature levels regulated by current regulatory documents when using typical resource-saving development systems;
- study of the influence of mining factors on the formation of the temperature of the air flow entering the longwall;
- study of the influence of mining factors on the temperature of the air flow passing through the longwall.
The research was conducted for typical variants of the long pillar mining system (Fig.2). These variants are implemented during the preparation of extraction pillars using transport and conveyor drifts and supplying fresh air flow to the longwall through them (Fig.2, a) or to the lower half of the longwall (Fig.2, b), when drilling a ventilation drift in the middle part of the extraction pillar.
Implementation of the considered variants is possible without leaving intact ore or with leaving pillar between extraction pillars with a width of Z0(Fig.2), at which the pillar is destroyed in the developed space under the influence of rock pressure.
The width of the Z1 pillar (Fig.2, a) should be determined based on the condition of ensuring a technologically satisfactory state of the ventilation shaft, while the length of the dead end longwall face l should be determined based on the condition of ensuring its ventilation. In all investigated cases, the longwalls are equipped with Eickhoff SL-300/480 or Eickhoff SL-300/550 mechanized complexes with installed electric motor power of 480 and 550 kW, respectively.
In favorable mining and geological conditions, the use of these technologies allows to achieve high average daily loads on the longwall faces and ensures low cost of extraction.
Experimental production research was conducted in the following mining and geological conditions. The depth of mining operations from the surface ranged 400-850 m. The main productive lower sylvite formation of the Third Potassium Horizon (Third Potassium Formation) includes six sylvite layers. Layers 2, 3, and 4 have industrial significance. During extraction, the productive formation is divided into two technological layers worked in a descending order. The upper technological layer includes the fourth sylvite layer with a thickness of 1.2 m, while the lower layer includes the second and third sylvite layers, with an intermediate layer of halite 2-3 with a total thickness of about 2.0 m. The thickness of the rock mass between the upper and lower technological layers is 0.9-1.1 m.
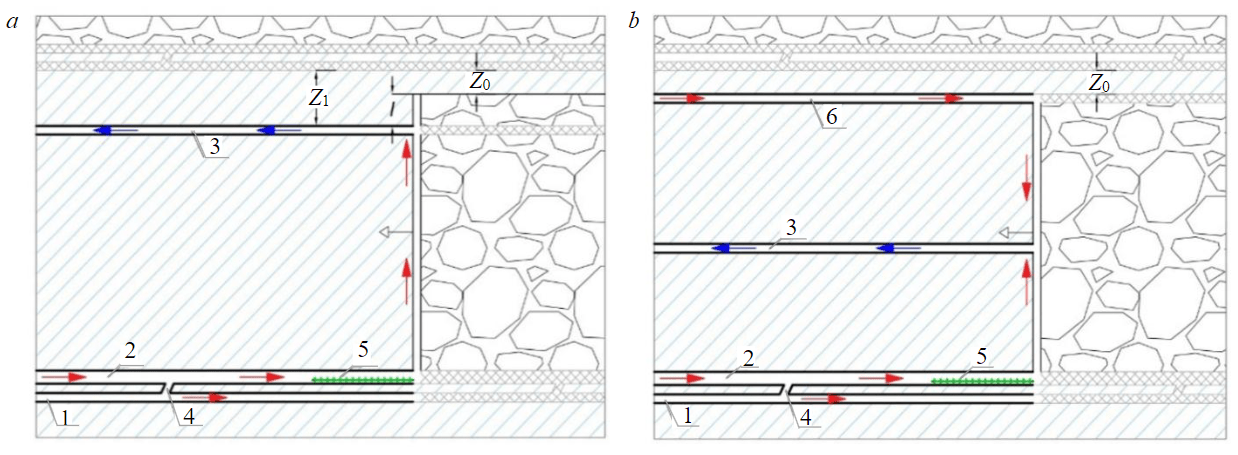
Fig.2. Schematic diagrams of typical resource-saving systems for long-pillar system development
The length of the longwalls ranged from 174-291 m, and the length of the extraction pillars was 4000 m. In all investigated cases, the power train of the longwall was located in the conveyor track in close proximity to the longwall (Fig.2). The length of the gateway section where the power train is located is 80-100 m. It should be noted that this arrangement of the power train relative to the face of the longwall pillar is applied in all mines of OAO “Belaruskali”.
The following parameters were measured during mine investigations:
- air temperature in the ventilation stream intended for ventilation of the longwall along its entire route from entering the transportation and conveyor tracks (Fig.2) to the exit of the stream from the ventilation track into the main directions of the workings;
- temperature of the rocks that collapsed in the developed longwall space;
- temperature of the valuable mineral mass ahead of the pillar face;
- air temperature in the developed longwall space.
Measurements of rock mass, air, and equipment temperature included in the power train were carried out using a contact digital thermometer TK-5.06 (Fig.3). The TK-5.06 electronic thermometer includes an electronic unit and interchangeable probes designed for measuring the temperature of liquid, bulk, and gaseous media, the surfaces of solid bodies, and the relative humidity of gaseous media. The probes use thermoelectric converters with nominal statistical characteristics according to GOST R 8.585 as tempe-rature-sensitive elements. The electronic unit of the thermometer converts the signal from the probe output into measurement information signal, which is displayed on the liquid crystal display. The instrument's error is ±0.5 °C when measuring temperatures in the range from –40 to 100 °C.
The results of research conducted in production conditions show that the formation of the thermal regime in longwall occurs according to a specific scheme, which is the same for all investigated sections. The initial parameters of the air supplied to the shaft are determined by the climatic conditions on the surface and the features of the functioning of the air preparation systems. When moving through the workings near the shaft station and main air supply workings, the air temperature tends to approach the temperature of the virgin rock mass [9, 19]. The alignment of the air temperature to the temperature of the virgin rock mass occurs at a distance of 2500-3000 m from the air supply shafts. Substantial changes in the air temperature occur within the excavation areas (panels) [20].
It has been established that for all considered mining situations and variants of long pillar development systems, the main factors influencing the temperature of the air jet in the longwall are: heat release from the power train; the length of transport and conveyor tracks (see Fig.2); the temperature of the seam ahead of the longwall face and the host rocks; the temperature of the air in the developed space of the longwall. In this case, the first two factors are the main reasons for the formation of high temperatures at the junction of the longwall with the conveyor track (Fig.2).
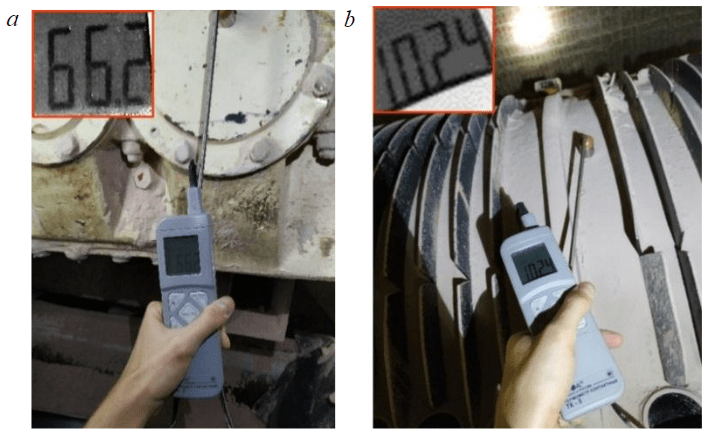
Fig.3. Measuring the temperature of the equipment in the area of the location of the gearbox of the SPSH-1-228 scraper conveyor (a) and transformer substation N 1 (b)
The temperature of the equipment included in the power train (Fig.4) reaches 100 °C or more during mining shifts (see Fig.3). As a result of the heat generation from the equipment within the power train, the increase in the air temperature amounts to 10-15 °C. The equipment within the power train has the most significant influence on raising the air temperature entering the longwall at the location of the installation for cooling electric motors and reducers of the combine, as well as at the location of transformer substations. In these areas, the air temperature reaches 34-35 °C, and in close proximity to the equipment it reaches 40-41 °C (Fig.4).
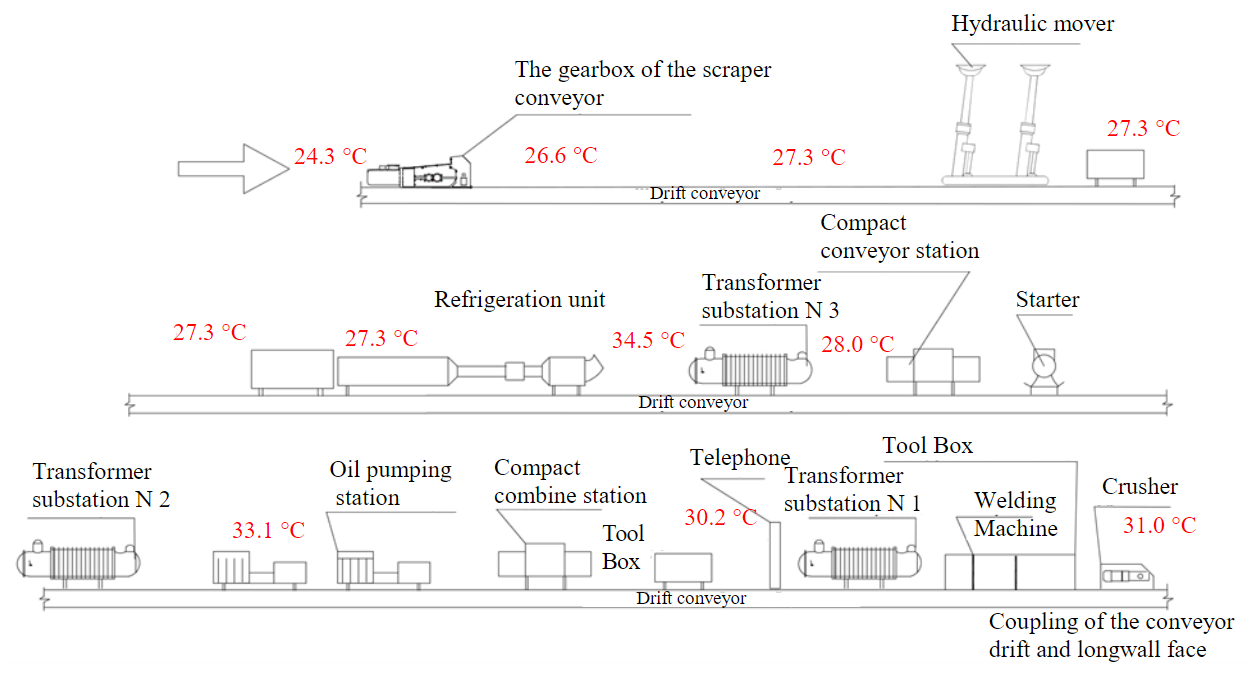
Fig.4. Results of measuring the air temperature along the length of the power train (longwall N 5-1, horizon –440 m, mine 4RU) using a thermometer TK-5.06
In some cases, there are periods of temperature decrease by 2-10 °C and an increase of 1-3 °C in the air temperature between the conveyor track section with the highest temperatures and the longwall. These fluctuations are associated with the inflow of air jets from the transport track (see Fig.2) through bypasses, which have significantly lower temperatures than the air temperature in the conveyor track where the power train is located. The difference between the air temperature at the section with maximum values and the air temperature entering the longwall is 7-9 °C. The temperature of the air jet entering the longwall reaches 32-34 °C or higher.
The air temperature in the transport track mainly depends on the temperature of the rock mass, determined by the depth of mining operations, the length of the transport track, and the location of the considered track section relative to the power train. At the entrance to the transport track (junction of the track with the main workings), the air temperature of the jet is approximately equal to the temperature of the rock mass. In the examples presented in Fig.5, the temperature of the rock mass is about 19 °C. As the jet moves along the transport track, its temperature gradually increases due to the heat generated by the conveyor lines and the inflow of air from the conveyor into the transport track through bypasses (see Fig.2). The maximum temperature increments in the transport track primarily depend on the distance between the longwall and the junction of the transport track with the main workings. In the considered mining conditions, these temperature increments did not exceed 2-3 °C. In some cases, in a section of the transport track (Fig.2) separated from the power train by a width of 3-4 m, an increase in air temperature of 2-3 °C was recorded. However, in all the investigated situations, the air temperature in the transport track did not exceed 25 °C.
After entering the longwall and subsequent movement within the longwall, the air temperature constantly decreases (Fig.5). The temperature decrease follows a law dependent on the temperature of the useful mineral deposit layer, the air, the fallen rocks in the developed space of the longwall, and the air jet entering the longwall. The cooling of the air jet passing through the longwall occurs due to the inflow of air from the developed space into the longwall with a lower temperature. The useful mineral deposit layer also has a lower temperature than the air jet passing through the longwall. The temperature difference between the air jet at the entrance to the longwall and its exit is 6-10 °C. To estimate the air temperature at different sections along the length of the longwall, the following expression can be used
where t0 is the air jet temperature at the junction of the longwall with the conveyor track (see Fig.2); a and b are parameters depending on the specific conditions of mining operations, for the conditions of working the Third Potash Horizon, a = 0.033, b = 0.0004.
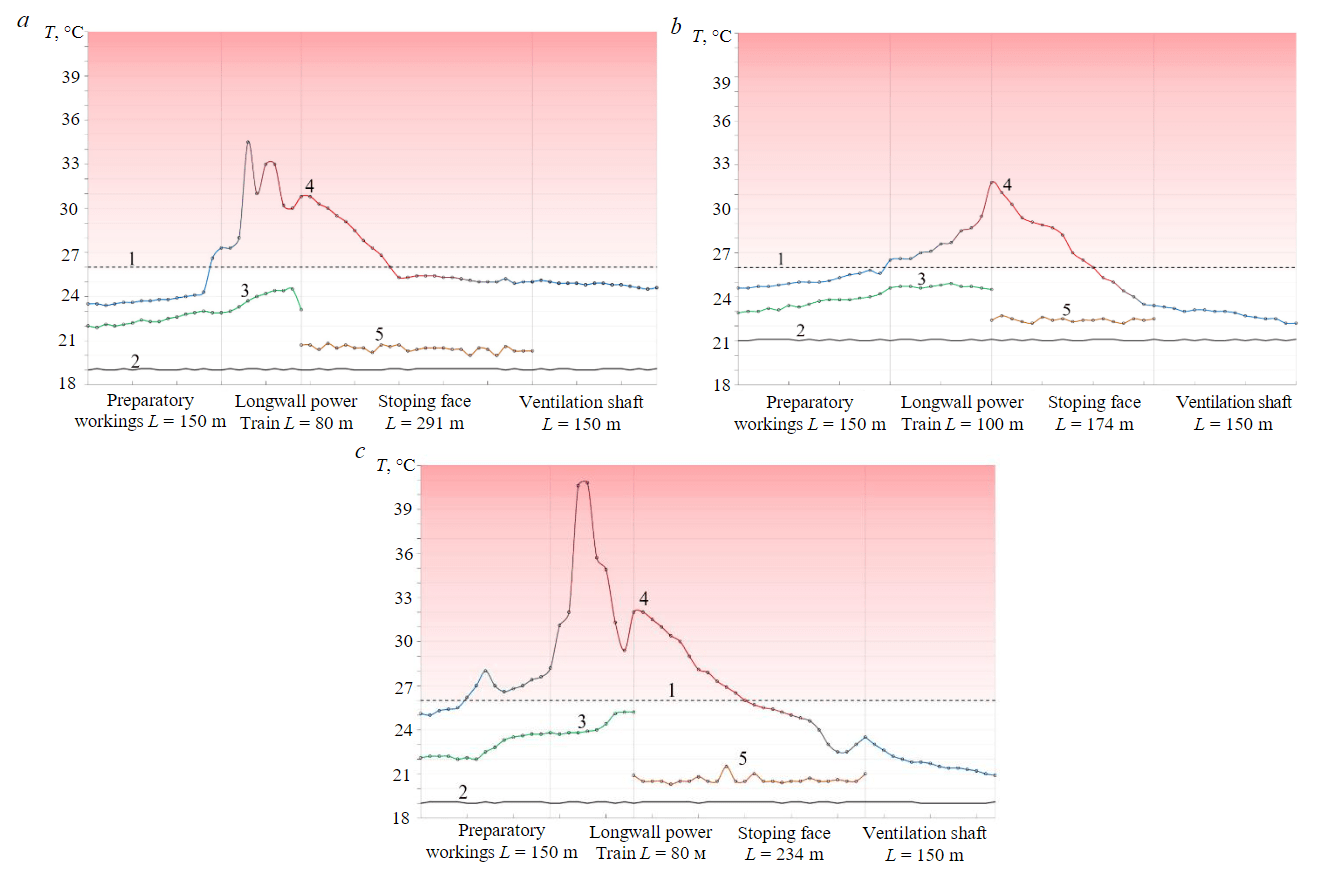
Fig.5. The influence of mining factors on the temperature of the air jet: a – in the conditions of mining 5 of the Northern column of the 4RU mine with longwall N 5-1; b – in the conditions of mining 3a of the Eastern column of the 3RU mine with longwall N 8-h-4; c – in the conditions of mining 2 of the Northern column of the 1RU mine with longwall N 94. 1 – maximum permissible temperature in the longwall according to sanitary standards; 2-5 – the temperature of the host rocks, the air in the transport drift, conveyor and ventilation drifts and the developed longwall space, respectively
The length of the longwall section where the air temperature exceeds 26 °C reaches 60-100 % of the length of the longwall. The length of the section primarily depends on the air temperature at the junction of the conveyor track with the longwall, the method of roof control in the longwall, and the depth of mining operations.
As examples of research results for typical mining situations, data on the change in air jet temperatures along their paths of movement (see Table 1, Fig.5) are provided: in conveyor and transport tracks, longwalls, developed longwall spaces, and ventilation tracks. Mining operations in the longwalls were carried out in layers 1, 1-2, 2 of the Second Potash Horizon, as well as in layers 2, 2-3, 3, and layer 4 of the Third Potash Horizon using mechanized complexes Eickhoff SL-300/480, Eickhoff SL-300/550, and Eickhoff SL-300NE. The depth of work from the surface ranged from 500-800 m, and the length of the longwalls ranged from 174-291 m.
Table 1
Characteristics of production research sites
Longwall number, mine |
Stoping mechanized complex |
Longwall length, m |
Depth of work, m |
Temperature of the host rocks, °С |
Air temperature at the longwall junction with conveyor drift, °С |
The length of the longwall section with a temperature of more than 26 °C, % |
94, 1RU |
Eickhoff SL-300/480 |
234 |
680-700 |
19 |
31-32 |
55 |
5-1, 4RU |
Eickhoff SL-300/550 |
291 |
617-732 |
19 |
31 |
40 |
104, 1RU |
Eickhoff SL-300/480 |
236 |
538-613 |
18 |
29-30 |
35 |
8-n-4, 3RU |
Eickhoff SL-300/480 |
174 |
764-802 |
21 |
31-32 |
65 |
4-v-4 3RU |
Eickhoff SL-300NE |
250 |
733-764 |
21 |
29 |
60 |
In the cases considered, the air temperature at the junctions of the longwalls with the conveyor tracks was 29-32 °C, the temperature of the useful mineral deposit ahead of the longwall face was 18-21 °C, and the air temperature in the developed space ranged from 19-23 °C. By the time it exited the longwall, the temperature of the worked air jet had decreased to 20-25 °C. Further, in a ventilation track section up to 300-350 m in length, the air jet temperature decreased to the temperature of the host rocks, which was approximately 19-23 °C. When conducting instrumental observations at mining depths of up to 850-900 m, temperatures exceeding 23 °C in the rock mass were not recorded. The air jet temperature in the transport tracks increased to 22-25 °C as it approached the longwall.
Discussion
When searching for solutions to achieve the set goal (see Fig.1), particular attention is warranted to the data obtained during production research:
- The main factor exerting a significant influence on the air temperature within the underground workings at the Belarusian Potash Company (OAO “Belaruskali”) mines, which use typical resource-saving long-pillar mining systems (Fig.2), is the heat radiation from the equipment comprising the power train located in the conveyor track in close proximity to the workings. As a result of this factor, the temperature of the air entering the workings increases by 5-9 °C.
- In the considered range of mining depths (500-900 m), the temperature of the host rock mass, the air in the developed space, and the useful mineral deposit ahead of the face are all lower than the permissible air temperature limit (26 °C) within the workings by 2-10 °C. This indicates the potential possibility of using these natural features to reduce the temperature within the
workings.
At the initial stage of the research, various options for mitigating the negative impact of the power train on the thermal regime within the workings were analyzed. This involved considering changes in the location of the power train relative to the incoming air jet into the workings [21, 22]. The analysis showed that placing the power train in workings with outgoing air jets is practically challenging due to several industrial safety constraints and the emergence of additional risks of disrupting continuous production.
The main idea revolves around developing spatial-planning solutions, which include supplying air to the workings along a specific length of the conveyor track supported behind the working face. This approach allows for: independent ventilation of the workings and the power train, eliminating the influence of the power train on the temperature of the air jet entering the workings; reducing the temperature of the air entering the workings through heat exchange with the host rock on the supported track section behind the working face.
When implementing this idea, the ability to regulate the temperature of the air entering the workings to the required level is achieved by adjusting the length of the track section supported behind the working face. The minimum required length of this section is determined by the condition of maintaining the air temperature at the entrance to the workings at 26 °C.
In Fig.6, recommended options for a resource-saving system for mining potassium deposits in deep horizons are presented. These options aim to reduce the air temperature in the workings, which are characterized by the high energy capacity of mining equipment, without using underground air conditioning systems. The primary option, shown in Fig.6, a, is preferred, while the second option (Fig.6, b) is recommended for use when implementing the primary one is not feasible.
In the case of implementing the option presented in Fig.6, a, a stream of air for ventilating the working area and the power train is supplied along the transportation track to the mining face, which is located at a distance of L from the working area. Subsequently, the fresh air flows along the conveyor track section located between the mining face and the working area. At the junction of the working area and the conveyor track, the air stream is divided. The main portion enters the working area and then the ventilation shaft, while the remaining portion goes to the location of the power train. Air with elevated temperature from the power train is diverted to the ventilation shaft through an auxiliary diagonal development. Temporary barriers with windows are installed in the conveyor track and auxiliary diagonal development to regulate the volume of air reaching the power train. The results of the conducted research show that the air temperature entering the working area from the transportation track at depths of mining activities up to 900 m, in the most unfavorable situations related to the inflow of air from the conveyor track to the transportation track, does not exceed 29 °C. The reduction in the air temperature entering the working area is achieved through heat exchange between the incoming air stream and the surrounding rocks during its movement along the L-section of the conveyor track, supported behind the mining face. Considering the variation in air temperature along the length of the working area (see Fig.5), a decrease of at least 3 °C is achieved on the section of the conveyor track supported behind the working area with a distance of 100-120 m. When using the option of the mining system with separate ventilation for the power train and the working area, the air temperature at the entrance to the working area at depths up to 900 m will not exceed 24-26 °C.
Additional reduction in the air temperature in the immediate mining area can be achieved by supplying a certain volume of air from the transportation track to the working area through developed space (Fig.6). However, the feasibility of using this recommendation in each specific case requires additional justification for its compliance with safety regulations.
The stability of the conveyor track section of length L behind the working area can be achieved by using known protection methods (e.g., rock barriers, various structural reinforcements, etc.) [23-28]. The chosen protection method should ensure the preservation of a sufficient cross-section of the track to supply the required amount of air for ventilating the working area and the power train during the time it takes the working area to traverse the distance L. To prevent the complete filling of the track with rock during the construction of the backfill rock mass at the far end of the reinforcement junction, a protective shield is installed.
The parameter L is technically easily adjustable during the column extraction period, allows to consider increasing L as a realistically feasible method to reduce the air temperature entering the cavity, not only when using the scheme with separate ventilation for the cavity and the power train (Fig.6, a) but also with sequential ventilation of the power train and the cavity (Fig.6, b). When determining the minimum necessary length of segment L, at which the temperature of the incoming air stream into the cavity will be less than 26 °C, a method widely used in solving problems of mine thermophysics is adopted, based on the use of the coefficient of non-stationary heat exchange [29, 30]:
where Тa is the average air temperature, °С; Тw (t) is the temperature on the working wall, °С; Тr is the temperature of the rock mass, °С; а is the heat exchange coefficient of the wall with the air.
In relation to the problem under consideration, the minimum required length L of the conveyor drift section supported behind the longwall with sufficient accuracy for practical purposes can be determined by the method given in [31]:
where Pair is the air density, kg/m3; Cair is the specific heat capacity of the air, kJ/(kg × K); Q is the current air flow in the transport drift, for which the temperature change is indicated, m3/s; Р is the perimeter of the cross section of the transport drift, m; kt is the coefficient of non – stationary heat transfer, W/m2; TA is the air temperature at the interface in the transport drift on the line with the longwall face, °С; TB is the air temperature at the interface of the longwall with the conveyor drift after heat exchange with the walls, °С.
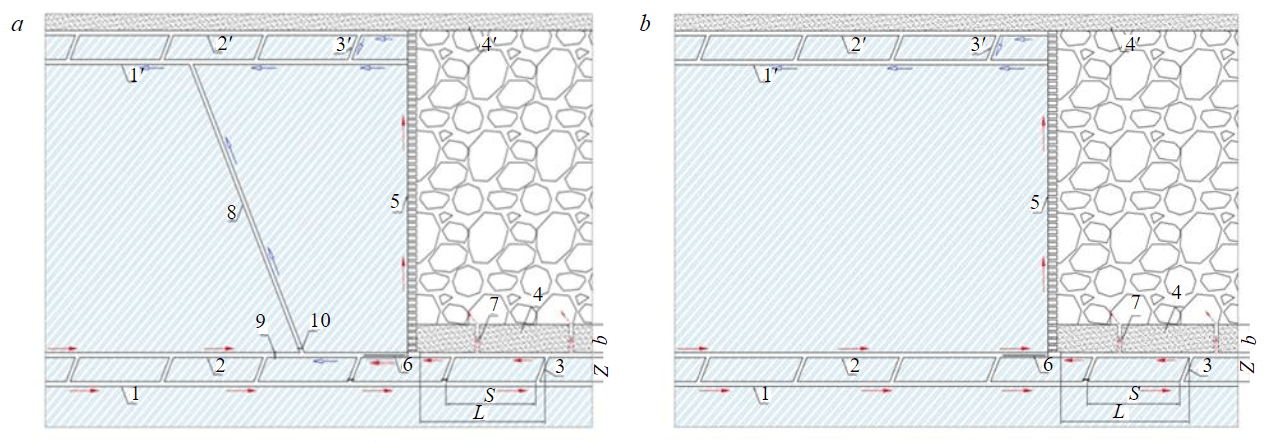
Fig.6. Resource-saving technological schemes recommended for use with high energy capacity of the stoping equipment with separate (a) and sequential (b) ventilation of the power train and longwall. 1 – transport drift; 2 – conveyor drift; 3 – breakthrough; 1' – ventilation drift; 2' – ventilation passage; 3' – ventilation breakthrough; 4 – rock strip; 5 – longwall; 6 – power train; 7 – auxiliary working; 8 – auxiliary diagonal working; 9, 10 – temporary air stopping with windows; Z – the width of the pillar; b – the width of the rock strip
The performed studies have shown (Fig.7) that the temperature of the air entering the
working (see Fig.6, a) and the minimum required length L of the conveyor drift section supported behind the longwall significantly depend on the distance between the longwall and the main air supply drift.
In the technical and economic assessment of alternative ways to ensure the required thermal regime in longwalls, it should be taken into account that the recommended options for long-pillar mining systems (see Fig.6) easily adapt to the actual technological schemes used at the mines of OAO “Belaruskali”, and are characterized by minimal energy costs. These schemes can be used both in the design of new horizons and in the panels being developed.
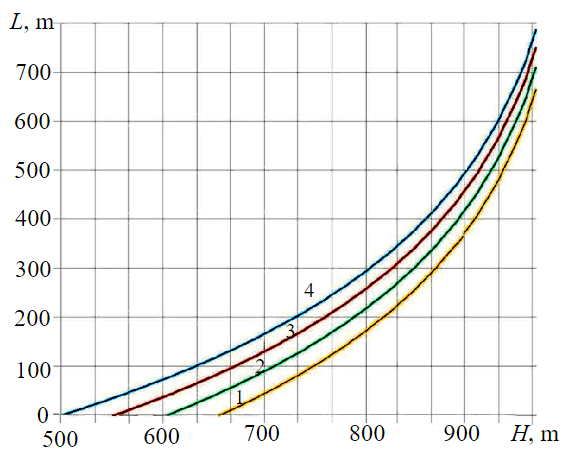
Fig.7. The dependence of the minimum required length of the section of the air supply work supported behind the longwall on the depth of the stoping work at the distance between the longwall and the main air supply drift: 1 – 1000; 2 – 2000; 3 – 3000; 4 – 4000 m
Conclusion
The long-pillar mining systems used at the mines of OAO “Belaruskali” using high-performance stoping equipment with high energy capacity in longwalls do not ensure the creation of a thermal regime in longwalls in accordance with the SanPiN “Hygienic requirements for microclimate in the design and operation of potash mines” and the rules for ensuring industrial safety in the underground development of salt deposits of the Republic of Belarus. The air temperature in the longwall face area operating at depths of more than 500 m, as a rule, exceeds the maximum permissible value of 26 °C.
When using well-known technologies for mining potash seams with longwall faces using high-performance mechanized stoping complexes, the depth of mining operations, the distance from the longwall to the main air supply workings and the location of the longwall power train have a decisive influence on the temperature of the air entering the longwall. In the conditions of the mines of OAO “Belaruskali”, when the power train is located in the conveyor drift ahead of the longwall face, the temperature of the air jet at the entrance to the longwall exceeds by 6-9 °C its maximum permissible values regulated by sanitary norms.
When the air jet moves in the longwall face area, its temperature decreases from the maximum values at the inlet of the jet into the longwall to the minimum values at the outlet of the jet from the longwall. The difference between the minimum and maximum temperatures in the studied conditions is 6-10 °C. The main influence on the regularity of temperature changes during the movement of the jet from the conveyor drift to the ventilation one is exerted by the temperature of rocks in the developed longwall space and the temperature of the mineral mass ahead of the longwall face.
When developing potash seams at depths up to 800-900 m by longwalls characterized by high energy capacity of stoping equipment, a decrease in air temperature in the longwall face area without the use of underground air conditioning systems is achieved by using a developed patentable technology that includes air supply to the longwall along a section of a conveyor drift of a certain length supported behind the longwall and separate ventilation of longwall and power trains. When using this technology, which does not require additional energy costs, the temperature of the air jet at the entrance to the longwall at depths up to 800-900 m does not exceed 24-26 °C.
The application of the developed technology in the mining and geological conditions of the Third potash formation at the mines of OAO “Belaruskali”, compared with the use of options for organizing work in longwalls, providing for a reduction in the duration of the mining shift at an air temperature in longwall exceeding 26 °C, allows to increase the average daily production from longwall by at least 15-17 % and reduce the site cost production by 12-15 %.
References
- Deshkovskii V.N., Danilova A.F., Novokshonov V.N. The displacement of the rock mass as a result of its work-up by the pillar development system in the conditions of the Starobinsky potash salt deposit. Mining Informational and Analytical Bulletin. 2012. N 11, p. 80-86 (in Russian).
- Zubov V.P., Smychnik A.D., Kirienko V.M., Dakuko N.A. The concept of mining the Third potash formation at the mines of RUP PO “Belaruskali”. Gornaya mekhanika. 2005. N 4, p. 66-71 (in Russian).
- Smychnik A.D., Zubov V.P., Kalugin P.A., Kirienko V.M. Technological schemes of PO “Belaruskali” mines: condition, problems, prospects for improvement. Gornyi zhurnal. 2003. N 7, p. 45-50 (in Russian).
- Podlesnyi I.A., Getmanov V.N., Petrovskiy B.I., Nosulya I.E. Multi-slice mining technology for potash seam III at the Starobinsk deposit. Gornyi zhurnal. 2018. N 8, p. 59-63 (in Russian). DOI: 10.17580/gzh.2018.08.08
- OAO “Belaruskali”: mining technology. URL (accessed 29.04.2021) (in Russian).
- Zubov V.P., Smychnik A.D. Sudden outbursts of salt and gas in potash mines and their prevention. Gornyi zhurnal. 1998. N 11-12, p. 85-87 (in Russian).
- Sokol D.G., Le Quang Phuc, Than Van Duy Safety improvement in recycle development headings in potash mines: Current problems and prospects. Mining Informational and Analytical Bulletin. 2020. N 12, p. 33-43 (in Russian). DOI: 10.25018/0236-1493-2020-12-0-33-43
- Kologrivko A.A., Dakuko S.N. Technological schemes of pillarless workings of potash seams in complex geological and mining conditions. Gornaya mekhanika. 2009. N 4, p. 48-59 (in Russian).
- Levin L.Yu., Zaitsev A.V., Butakov S.V., Semin M.A. Normalization of microclimate in deep potash mines. Gornyi zhurnal.2018. N 8, p. 97-102 (in Russian). DOI: 10.17580/gzh.2018.08.14
- Golovaty I.I. Belaruskali – the world’s top producer of potash fertilizers. Gornyi zhurnal. 2018. N 8, p. 4-9 (in Russian).
- Solov'ev D.E., Khokholov Yu.A. Forecast of the thermal regime of the mine, taking into account the dynamics of the mining operations development. Mining Informational and Analytical Bulletin. 2009. N 5, p. 270-275 (in Russian).
- Martynov A.A., Lunev S.G., Yakovenko A.K. Forecasting and development of a set of measures to normalize thermal conditions in the mine workings of deep coal mines on a PC. Mining Informational and Analytical Bulletin. 2003. N 2, p. 130-133. (in Russian).
- Kologrivko A.A. Decrease in geoecological consequences by underground mining of potash fields. Vestnik Polotskogo gosudarstvennogo universiteta. Seriya F. Stroitel'stvo. Prikladnye nauki. 2014. N 16, p. 101-110 (in Russian).
- Manohar Rao A., Ramalingeswarudub S.V.S.S., Venkateswarlu G. Planning of Ventilation Requirements for Deep Mechanised Long wall Faces – A Case Study of Adriyala Longwall Project of The Singareni Collieries Company Limited (SCCL). Procedia Earth and Planetary Science. 2015. Vol. 11, p. 548-556. DOI: 10.1016/j.proeps.2015.06.057
- Brake D.J. The Deep Body Core Temperatures, Physical Fatigue and Fluid Status of Thermally Stressed Workers and the Development of Thermal Work Limit as an Index of Heat Stress. Perth: Curtin University, 2002. 294 p.
- Martynov A.A., Yakovenko A.K., Oleksyuk A.B. Systems and means of local cooling of mine air in mine workings. Mining Informational and Analytical Bulletin. 2007. N S12, p. 132-140 (in Russian).
- Medvedev I.I., Krasnoshtein A.E. Aerology of potash mines. Sverdlovsk: Ural Branch of the USSR Academy of Sciences, 1990. p. 251 (in Russian).
- Alabiev V.R. The main directions of the ways and air cooling means development in the coal mines of the Ukraine. Vestnik Zabaikal'skogo gosudarstvennogo universiteta. 2014. N 6 (109), p. 35-46 (in Russian).
- Zaitsev A.V., Semin M.A., Klyukin Yu.A. Improvement of microclimate conditions rationing criteria in mine airways. Mining Informational and Analytical Bulletin. 2015. N 12, p. 151-156 (in Russian).
- Karelin V.N, Kravchenko A.V., Levin L.Yu. et al. Features of forming microclimatic conditions in mining excavations of deep mines. Gornyi zhurnal. 2013. N 6, p. 65-68 (in Russian).
- Belle B., Biffi M. Cooling pathways for deep Australian longwall coal mines of the future. International Journal of Mining Science and Technology. 2018. Vol. 28. Iss. 6, p. 865-875. DOI: 10.1016/j.ijmst.2018.02.001
- Gangrade V., Schatzel S.J., Harteis S.P. A Field Study of Longwall Mine Ventilation Using Tracer Gas in a Trona Mine. Mining, Metallurgy & Exploration. 2019. Vol. 36. Iss.6, p. 1201-1211. DOI: 10.1007/s42461-019-0096-0
- Chen Jie, Liu Jian-xing, Jiang De-yi et al. An experimental study of strain and damage recovery of salt rock under confining pressures. Rock and Soil Mechanics. 2016. Vol. 37. N 1, p. 105-112. DOI: 10.16285/j.rsm.2016.01.012
- Litvinenko V. Advancement of geomechanics and geodynamics at the mineral ore mining and underground space development. Geomechanics and Geodynamics of Rock Masses. International European Rock Mechanics Symposium, EUROCK 2018, 22-26 May 2018, Saint Petersburg, Russian Federation. London: Taylor and Francis Group, 2018. Vol. 1, p. 3-16.
- Eremenko V.A., Galchenko Yu.P., Kosyreva M.A. Evaluation of the influence of geometric parameters of traditionally used and nature-like systems of underground mining of ore deposits on the initial stress field. Fiziko-tekhnicheskie problemy razrabotki poleznykh iskopaemykh. 2020. N 3, p. 98-109 (in Russian). DOI: 10.15372/FTPRPI20200310
- Prushak V.Ya. Deformation of the edge of the workings of the Starobin deposit of potash salts at different location depths. Reports of the National Academy of Sciences of Belarus. 2016. Vol. 60. N 2, p. 97-101 (in Russian).
- Guorui Feng, Pengfei Wang, Chugh Y.P. A New Gob-Side Entry Layout for Longwall Top Coal Caving. Energies. 2018. Vol. 11. Iss. 5. N 1292. DOI: 10.3390/en11051292
- Zhijun Tian, Zizheng Zhang, Min Deng et al. Gob-Side Entry Retained with Soft Roof, Floor, and Seam in Thin Coal Seams: A Case Study. Sustainability. 2020. Vol. 12. Iss. 3. N 1197. DOI: 10.3390/su12031197
- Shcherban A.N., Kremnev O.A., Zhuravlenko V.Ya. Guidelines for regulating the thermal regime of mines. Мoscow: Nedra, 1977, p. 359 (in Russian).
- Shcherban A.N., Kremnev O.A. The research bases of calculation and regulation of the thermal regime of deep mines: in 2 volumes. Vol. 2. Kiev: Izd-vo AN USSR, 1960, p. 347 (in Russian).
- Krasnoshtein A.E., Kazakov B.P., Shalimov A.V. Modeling of processes of non-stationary heat exchange between mine air and rock mass. Fiziko-tekhnicheskie problemy razrabotki poleznykh iskopaemykh. 2007. N 5, p. 77-85 (in Russian).