Analysis of the application and impact of carbon dioxide media on the corrosion state of oil and gas facilities
- 1 — канд. техн. наук Deputy General Director “Gazprom VNIIGAZ” LLC ▪ Orcid ▪ Elibrary ▪ Scopus
- 2 — канд. техн. наук Head of the Corporate Science and Technology Center “Gazprom VNIIGAZ” LLC ▪ Orcid ▪ Elibrary ▪ Scopus
- 3 — Ph.D. Head of Laboratory “Gazprom VNIIGAZ” LLC ▪ Orcid ▪ Elibrary ▪ Scopus
Abstract
Products of several currently operated production facilities (Bovanenkovskoye, Urengoyskoye oil and gas condensate fields, etc.) contain an increased amount of corrosive CO 2 . Effect of CO 2 on the corrosion of steel infrastructure facilities is determined by the conditions of its use. Carbon dioxide has a potentially wide range of applications at oil and gas facilities for solving technological problems (during production, transportation, storage, etc.). Each of the aggregate states of CO 2 (gas, liquid and supercritical) is used and affects the corrosion state of oil and gas facilities. Article analyzes the results of simulation tests and evaluates the corrosion effect of CO 2 on typical steels (carbon, low-alloy and alloyed) used at field facilities. The main factors influencing the intensity of carbonic acid corrosion processes in the main conditions of hydrocarbon production with CO 2 , storage and its use for various technological purposes are revealed. Development of carbon dioxide corrosion is accompanied and characterized by the localization of corrosion and the formation of defects (pitting, pits, etc.). Even alloyed steels are not always resistant in the presence of moisture and increased partial pressures of CO 2 , especially in the presence of additional factors of corrosive influence (temperature, aggressive impurities in gas, etc.).
Introduction
Carbon dioxide (CO2) has applications in various fields and has been used by various oil and gas infrastructure facilities. Recently, at some gas facilities, for example, at Bovanenkovskoye [11], Urengoyskoye [7], Yubileynoye [1] oil and gas condensate fields (OGCF), corrosion problems have arisen due to the increased content of CO2 in the produced products. In this regard, increased attention is paid to the problem of corrosion risks as a result of carbon dioxide corrosion (CDC) and its control [5, 38]. To control the technical condition of gas production and underground storage facilities, a set of measures is used, including geophysical [9], diagnostic investigations [2] and corrosion monitoring [40].
There is a triple point (Pcr = 7.38 MPa and Tcr = 31.1 °С) for the aggregate states of CO2 (gas, liquid and supercritical), which links them. CO2 can transfer from one state to another with a change in pressure and temperature. Supercritical state is characterized by the absence of difference between the liquid and gas phases. CO2 in the supercritical state (SCS) has intermediate characteristics between the properties of gas and liquid: compressibility like gas, and density like liquid. CO2 in SCS is able to dissolve many organic substances. It has a significantly lower viscosity than other compounds in a liquid state. In addition, the diffusion coefficient of CO2 in SCS is several orders of magnitude higher than that of other liquids.
Partial pressure is relatively low at gas production facilities and CO2 is in a gaseous aggregate state. Carbon dioxide is not only a component in the composition of extracted products, but can also be used at oil and gas facilities to solve technological problems, where the special properties of CO2, including in SCS, can be effectively used [3, 10].
One of the promising trends is the use of CO2 as a buffer gas in underground gas storage (UGS) to maintain pressure in the formation [4]. This makes it possible to partially replace the buffer volume of methane (СН4) with СО2 and obtain additional volumes of commercial natural gas. CO2 is often used in liquid form or in SCS, since, being heavier than CH4, it allows CO2 to be located in the lower part of the storage facility, preventing losses during the extraction of commercial gas from UGS [13].
The most proven is the use of CO2 for injection into the formation at the oil fields in order to increase oil production. In recent decades, this technology has been a widespread method for enhancing oil recovery in the world, for example, in the case of developing oil fields with hard-to-recover oil reserves, or when an effective additional development of fields at the late and final stages of hydrocarbon production is required. Application of CO2, including in SCS, is able to provide an effective reduction in oil viscosity in formation conditions and the mutual dissolution of oil and CO2. Regarding some oil formations, which are characterized by thermodynamic conditions that allow CO2 to pass into the SCS, the advantages of its use over the use of reagents and other methods of oil production intensification are obvious. It is noted in the article [14] that in China, tests are being carried out in the field of rheogasochemical technologies for in-situ generation of CO2. CO2 obtained as a result of the reaction has the properties of the directed effect on stagnant zones and weakly drained areas of the formation.
CO2 can be used to increase gas condensate recovery at OGCF by analogy with oil fields, which is another area of its application in oil and gas industry. Article [6] reports on the possibility of using such a technology at the Orenburg OGCF (OOGCF). Authors note that as a result of the hydrocarbons production and watering of wells, gas confinement in porous rocks can occur. At the later stages of development, with a drop in pressure, the gas energy in such a structurally confined gas volume becomes insufficient to break the continuity of the liquid phase (oil, water). In such places, along with gas, liquid hydrocarbons (gas condensate, oil) can be found, which makes the use of CO2 with properties of a good solvent, very promising for intensification of production at the OOGCF. In this case, the products of extraction can be gas, gas condensate and oil, including those from thin rims. According to the authors, application of this technology can significantly increase the gas recovery factor at the Orenburg OGCF, and the use of CO2 will increase both oil recovery and gas production.
Work [8] considers the options for re-injection of either acid gases (a mixture of H2S and CO2, consisting of fluids separated from the fluids produced at the field during treatment of raw materials), or CO2, for the Astrakhan gas condensate field (AGCF). This will improve the efficiency of the gas facility development. Application of this technology is aimed at maintaining reservoir pressure at AGCF to minimize formation losses during gas condensate production.
The issue of reducing anthropogenic emissions into the environment is a topical one. One of the negative factors is the increase in the concentration of greenhouse gases, including CO2. Measures to reduce greenhouse gas emissions, adopted under the Kyoto Agreement, provide a set of solutions. One of the directions is the creation of underground reservoirs to utilize the excess CO2 for long-term storage. Analysis of the world experience in capturing and pumping CO2 into formation systems has shown that this can be a promising way to reduce CO2 emissions into the atmosphere [12].
Transportation of recoverable СО2 (in liquid state or in SCS) to the places of its geological burial in underground storages (carbon capture and storage – CCS) is realized, as noted in [19]. CO2 pipelines are quite long (hundreds of kilometers), which limits the use of corrosion-resistant steel for their manufacture. Carbon steel/low-alloy steel is predominantly used, so it is important to ensure the safe operation of facilities.
For example, gas from the Askeladd, Albatross and Snøhvit fields, developed on the Norwegian shelf using subsea production systems, is transported to the coast 160 km, where it is liquefied. However, the gas contains up to 5-8 % CO2, which needs to be removed to produce liquefied natural gas (LNG) (down to a low level of 50 ppm). Removed CO2 is transported and pumped back into the underground (underwater) storage, into the formation below the productive horizon of the Snøhvit field [27]. For example, according to Russian regulations, the molar fraction of CO2 in LNG should not exceed 0.005-0.03 %. At many fields, the content of CO2 in the produced gas significantly exceeds these standards.
Often, not gas reservoirs, but aquifers are used for CO2 injection [16]. Creation of CO2 storage facilities in underground cavities, for example, after the end of the operation of a gas or oil field, has also become widespread. In addition to various technological risks during their operation, it is necessary to take into account the danger of CDC in case of contact of the increased CO2 quantities transported and pumped into underground reservoirs with equipment and pipelines made of carbon or low-alloy steels. In the presence of an aqueous phase of a condensation or formation nature, its saturation with CO2 will occur, accompanied by acidification, which intensifies the CDC process [30]. More and more projects are being launched in the world to use abandoned oil and gas fields, for example, Weyburn and Midale in Canada [37]. In this regard, it is reported that the corrosion rate can reach 20 mm/year and will depend, among other things, on corrosion products that can contribute to a decrease in the corrosion rate.
CO2 can, under certain conditions, lead to corrosion damage in all considered fields of application. The most dangerous property of CDC is that corrosion effects are not characterized by general (uniform over the entire metal surface) corrosion losses, but mainly by the most dangerous type of local corrosion, with the formation of local defects such as pitting, pits, etc. [40]. In this regard, the article discusses topical issues of assessing the corrosion aggression of carbon dioxide media and the resistance of steel objects in such conditions.
Methodology
Corrosion tests under conditions of moisture condensation were carried out at normal (20-25 °C) temperature. Test methods for moisture condensation, sample processing, assessment of corrosion defects, statistical data processing were carried out according to the procedures [34]. After the tests, the general corrosion rate Kgen was determined by the loss of the sample mass and the local corrosion rate by the depth of corrosion damage (average Kloc.av – by averaging over all local defects, maximum Kloc.max – by the deepest local damage).
Corrosion tests were carried out using the gravimetric method. Partial pressure effect of corrosive gases on the corrosion of the samples was evaluated in an autoclave unit (static conditions), after oxygen was removed by blowing with an inert gas. Exposure time of gravimetric samples in an autoclave unit was 120 h.
Phase composition of the corrosion products was analyzed by the X-ray diffraction method. It is based on recording the dependence of the intensity of the X-ray radiation reflection by the crystal lattices of the compounds on the value of the diffraction angle, followed by the interpretation of the diffraction pattern. Scanning was carried out on an ARL XʼTRA X-ray diffractometer. Identification of crystalline phases was carried out by comparing the array of reflections obtained from the test sample with the reference diffractograms of individual compounds contained in the international database of diffraction standards.
Carbon steels (St20 and X65), low-alloy steels (0.05-0.2 % Cr) and corrosion-resistant steels (12X18H10T) were used during the tests.
Results
It is known [39] that the most metal-consuming and most corrosive type of equipment at gas production facilities are well equipment and field pipelines (well connections, collectors, drags) in contact with untreated gas (until the removal of corrosive gases and moisture). When considering the corrosive aggression of the medium at gas production facilities in conditions of increased CO2 content, it should be taken into account that corrosion can occur in the lower part of the pipe when moisture accumulates (bottom-of-line corrosion, BOL), in the upper part of the pipe in case of moisture condensation (top-of-line corrosion, TOL), in places where moisture accumulates (cracks, gaps, stagnant zones, elevation differences, etc.).
The main reason for the development of corrosion is the presence of moisture, which can interact with steel in the bulk of solution (BOL) or during condensation, in a thin film of moisture on steel (TOL). TOL corrosion, in contrast to the corrosive conditions of oil facilities, occurs only at gas fields. Under the conditions of field transport for wet, untreated gas, when leaving the well water vapor in the gas phase condenses on the inner surface of the pipe due to the temperature difference between the wet gas flow and the environment, which leads to the appearance and development of TOL corrosion. BOL corrosion is typical for sections of the pipeline system when the water phase is in constant contact/movement with the inner surface of the pipeline steel [31, 35].
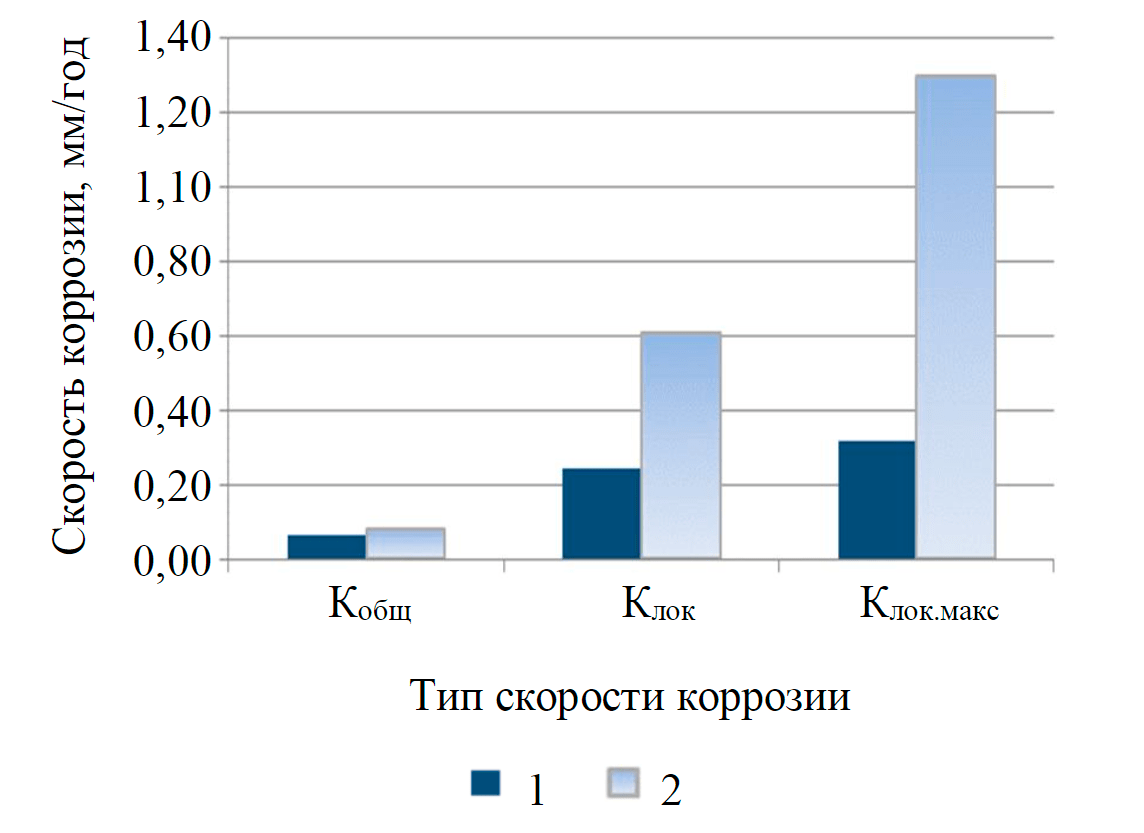
Fig.1. Results of corrosion tests to determine general Kgen and local corrosion rates, calculated by the average Kloc and maximum Kloc.max depth of corrosion damage on steel X65 in a CO2 environment and moisture condensation 1 – parent metal; 2 – weld seam
TOL tests carried out in the presence of CO2 showed that at a low (less than 0.1 mm/year) rate of general corrosion on carbon steel X65 (API 5L), a high local corrosion is observed (Fig.1).
As can be seen, development rate of local defects (0.5-1.5 mm/year) is observed to the greatest extent on specimens from the weld seam. Weld seam, due to their heterogeneity with respect to the parent metal, turned out to be more susceptible to uneven types of corrosion damage.
Analysis of the data obtained shows (Table 1) that low-alloy steels with a low chromium content (0.05-0.2 %) are not resistant to local CDC. Local defects with a depth of 50-84 µm are formed on the samples. Only on the surface of high-alloy steel 12X18H10T there were no corrosion manifestations, either general or local (Table 1).
Table 1
Test results for determining local corrosion rates, calculated by the average Kloc.av and maximum Kloc.max depths of corrosion damage
Sample |
Depth of corrosion damage, µm |
Local corrosion rates Кloc, mm/year |
||
average |
maximum |
by average values Кloc.av |
by maximum values Кloc.max |
|
12Х18Н10Т (18 % Cr) |
– |
– |
– |
– |
– |
– |
– |
– |
|
Steel (0.2 % Cr) |
55 |
78 |
0.669 |
0.949 |
63 |
84 |
0.767 |
1.022 |
|
Steel (0.05 % Cr) |
56 |
66 |
0.681 |
0.803 |
50 |
56 |
0.608 |
0.681 |
After TOL tests, deep pitting damage of the samples are observed on both low-alloy and carbon steels (Table 2). Tested steels are used in various areas of oil and gas facilities – tubing of well equipment, other steels – for the manufacture of field pipelines.
An increase in CO2 pressure can increase the solubility of the gas in the aqueous phase, increasing the corrosion rate. This will primarily relate to the local corrosion rate in the vapor phase. Also, the localized corrosion rate will rise with increasing water content in the test chamber, while general corrosion may remain unchanged. First of all, this is due to moisture condensation: with a lack of air humidity, the dew point will not be reached, and a moisture film will not precipitate on the steel surface. In addition to the content of CO2 and moisture in the vapor phase, other factors can also affect the CDC [33]. Let us consider some of them in more detail.
Corrosion resistance of steel P110 (0.5 % Cr) was investigated in [36] under the following conditions: 3.5 % NaCl, 80 °C and 9.5 MPa CО2. Investigations were carried out in two modes: in an aqueous electrolyte saturated with CO2 in SCS (steel is in contact with the aqueous phase, conditions are similar to BOL corrosion), and in a water-saturated CO2 in SCS (steel is in contact with wet CO2, conditions are similar to TOL corrosion). In the first mode (in an aqueous electrolyte), both general (6.12 mm/year) and local (1.8 mm/year) corrosion rates are equally high. In the second mode, a relatively low general rate (0.35 mm/year), but a high level of local corrosion (1.17 mm/year) is observed. According to the authors, the reason for this is that in the second mode, local corrosion defects are observed only in the places of drops condensation on steel (such as TOL corrosion), corrosion does not spread over the entire surface of the steel.
Table 2
Corrosion rate of steels after testing under conditions of water condensation in the presence of СО2 (0.1 MPa) at temperature 20-25 °С
Steel |
Corrosion rate, mm/year |
Sample appearance after testing |
|||
General |
Local (pitting)* |
General |
Zoomed in |
||
St 20 |
0.04 |
0.32-0.384 |
![]() |
![]() |
|
Steel (0.2 % Cr) |
0.03 |
0.67-1.0 |
![]() |
![]() |
|
Tubing steel |
0.015 |
0.368-0.61 |
![]() |
![]() |
|
Steel (0.05 % Cr) |
0.03 |
0.61-0.8 |
![]() |
![]() |
|
12Х18Н10Т |
0.0001 |
– |
![]() |
– |
*Range of average Кloc.av and maximum Кloc.max values of local corrosion.
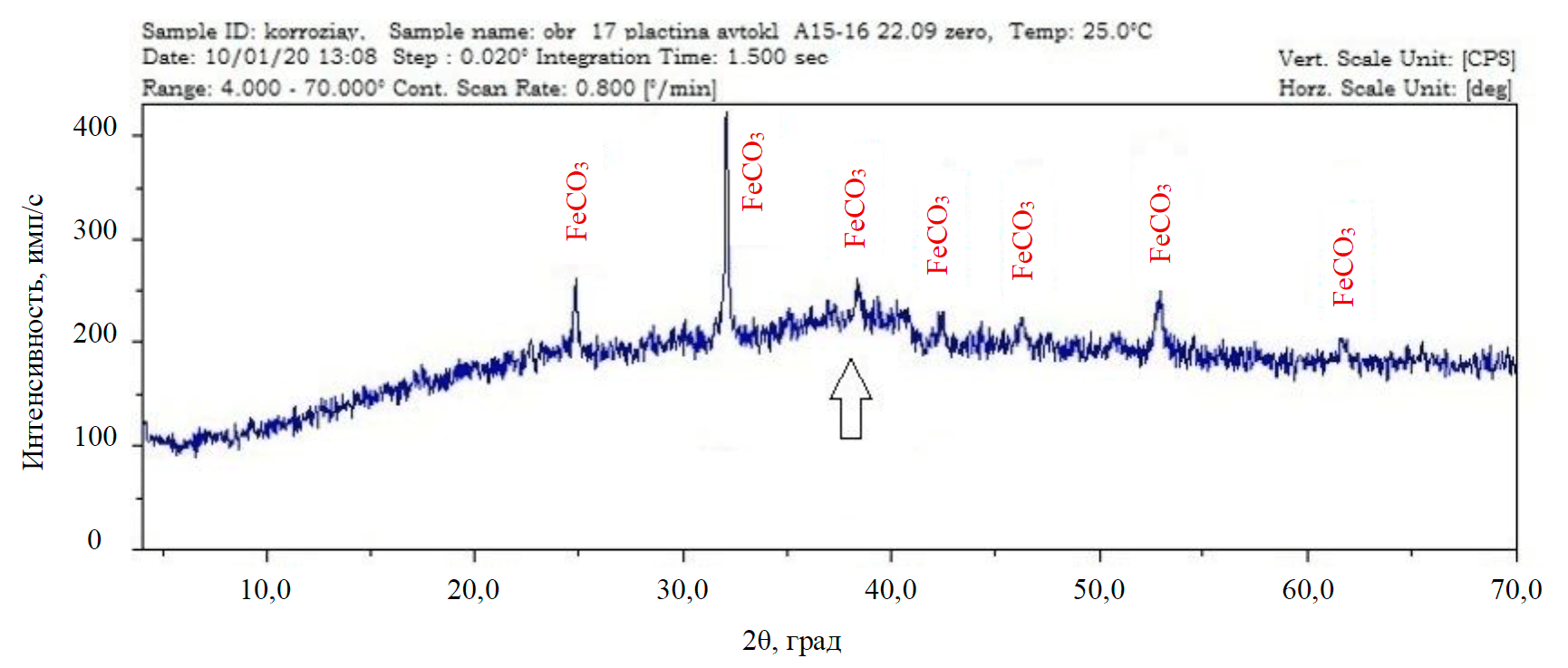
Fig.2. Identified experimental diffraction pattern of corrosion products obtained after autoclave tests on steel X65 at Р (СО2) = 0.8 MPa, T = 80 °С, in 3 % NaCl; the arrow indicates an X-ray amorphous gallo
Test results confirm that gas facilities operated under conditions of the CO2 presence in the extracted products are subject to increased corrosion hazard in the aqueous and vapor phases, especially local corrosion typical for the CDC. Corrosion products formed in the corrosion process on the metal surface play a certain role in the protection of steels from corrosion. Investigations carried out in an aqueous medium (Fig.2) to determine the phase composition of the film formed on steel after autoclave tests showed that crystallized siderite (FeСО3) with a small amount of X-ray amorphous substances is predominantly formed during CDC.
Depending on the phase composition, the precipitate of corrosion products can be either close-packed or porous. More porous corrosion products will be less resistant to the action of chloride anions, which provoke the nucleation and development of pitting, in contrast to the denser siderite layer.
Long-term simulation tests of several pipe steels (containing 1 and 13 % Cr), used in one of the underground CO2 storages in Germany, showed [29] that the model of aquifer water in the presence of CO2 is quite corrosive. General corrosion rate in vapor phase is 0.35 mm/year (13 % Cr) and 0.8 mm/year (1 % Cr). When exposed to the aqueous phase, a thick layer of corrosion products forms on the surface of steels, and pitting up to 4.7 mm deep are observed, which can be explained by the high mineralization of the aqueous medium and the increased content of chloride anions.
A significant acceleration of corrosion processes at 35 °С and 8 MPa CO2 was observed for steels X65 (0.11 % Cr) and 5Cr (5 % Cr) with the addition of 0 to 1000 ppm O2 [24]. Tests were carried out in water-saturated CO2 (SCS). With an increase in O2 concentration, an increase in pitting corrosion occurred: local corrosion rate ranged from 0.2 to 1.4 mm/year for X65 steel, and from 0.3 to 1.4 mm/year for 5Cr steel. An important role in the development of corrosion is played by the fact that the presence of О2 suppresses the formation of siderite (FeCO3), forming a film on the steel surface, mainly consisting of iron oxide (Fe2O3), which has an amorphous structure. The growth of local corrosion on both steels depends on the water saturation of CO2, and corrosion increases with increasing water content.
An important role in the corrosion aggression of CO2 in the SCS is played by the presence of impurities in it, which may be typical for greenhouse gases emitted for injection and storage into underground reservoirs. These gases, in addition to O2, include SO2, NO2, H2S. Results of investigations at a temperature of 35 °С and in SCS (8 MPa CO2) for steels X65 (0.11 % Cr) and 13Cr (13 % Cr) are given in [20]. The addition of two other corrosive gases (SO2 and O2) to CO2 in the presence of moisture leads to a synergistic effect in the development of the corrosion process. General corrosion rate for both steels is equally high: 0.95 mm/year for X65 steel, and 0.65 mm/year for 13Cr steel. Pitting corrosion is even higher for both steels (X65 and 13Cr) and is in the range of 7-80 mm/year. Presence of impurities leads to the formation of other corrosion products: iron oxides and sulfate instead of iron carbonate. Dissolution of SO2 in an aqueous film leads to the formation of extremely corrosive sulfuric acid, the destructive effect of which is enhanced by the presence of a strong oxidant O2. Similar data are given on the corrosion rate of carbon and alloy steels under analogous test conditions in the work of other authors [22]: up to 1 mm/year – general corrosion rate, and about 10 mm/year and more – for local defects. It is reported that localization of corrosion begins when water is present in a concentration of 300 ppm and higher.
Study of steel X65 at 8 MPa CO2 and a temperature of 35 °С showed that in the presence of SO2 less water is required for the development of corrosion than only with CO2. Local corrosion rate reaches 0.5-1.5 mm/year, increasing with the addition and increase of SO2 concentration [25].
Tests of carbon and low-alloy steels at a pressure of 8-12 MPa CO2 and an ambient temperature of 25-80 °C showed that the addition of 200 ppm H2S leads to a significant 50-fold increase in the corrosion rate in the vapor phase of CO2. With moisture condensation, the growth of the corrosion rate is slightly lower (5-10 times), since at CDC it is initially higher than 0.1 mm/year [23].
Data were obtained on the dependence of the corrosion resistance of steels with different chromium content (9, 13, and 25 %) on the partial pressure of CO2 and the temperature of the environment in the study [26]. For example, for steel 9 % Cr, corrosion rate of steel increases with a growth in the partial pressure of CO2: 0.1-0.3 mm/year at 0.1 MPa CO2 in the temperature range 50-250 °С; 0.5 mm/year (50 °С) and 5 mm/year (150 °С) at 0.3 MPa CO2. In this case, for steel 13 % Cr, critical temperatures are 200 °C (at 0.1 MPa CO2) and 150 °С (at 0.3 MPa CO2), when the corrosion rate begins to grow and exceeds 0.1 mm/year. Steel 25 % Cr was the only one that was stable at all the above temperatures and partial pressures of CO2.
Work [14] notes that chemical compositions injected for in-situ CO2 generation and enhanced oil recovery in the process of injection into the formation contact with underground well equipment. This increases the risk of corrosion destruction of metals, for the protection of which anti-corrosion protection should be used.
In such aggressive conditions of CDC, high-alloy steels can be used to protect the steel equipment and pipelines, which, however, in some particularly aggressive conditions also require the use of anti-corrosion protection [15]. Carbon and low-alloy steels that are not resistant to CDC, as well as some alloyed ones, can be protected by inhibitors or coating.
Tests have shown [32] that the corrosion rate of carbon steel at 50 °С and a CO2 pressure of 2-8.5 MPa is 1.87-3.0 mm/year. In the presence of a corrosion inhibitor, which is chemisorbed on steel, it decreases to 0.061-0.137 mm/year. The article [18] reports on the effectiveness of corrosion inhibitor protection under conditions of intensification of oil production at 60 °C and CO2 pressure up to 8 MPa.
Coatings that should be non-porous can also find use in protecting objects from CDC. Experience for the successful use of a metal coating for protection under the conditions of SCS CO2 is presented in the study [21]. Another type of metal coating based on Ni-W (with additions of Y2O3 and ZrO2 nanoparticles), which has a low energy of CO2 adsorption on its surface, remains dense, stable and without pitting after operation under CDC conditions [28]. The work [17] discusses the possibility of using conversion coatings of a complex composition to protect pipelines transporting CO2, including under conditions of acidification by the aqueous phase.
Conclusion
CO2 extracted at oil and gas fields together with fluids has a corrosive effect on steel equipment and pipelines with the formation of local damage. Carbon and low-alloy steels used at hydrocarbon production facilities are unstable in the presence of CO2 and moisture. Corrosion rate of such steels can reach high values. Tests carried out in carbon dioxide media of carbon (St20 and X65) and low-alloy steels (0.05-0.2 % Cr) showed that they undergo corrosion destruction with the formation of deep defects (pitting, etc.) under conditions of water condensation (TOL-corrosion), which can be the most dangerous at gas production and storage facilities. Local corrosion rate of such steels is high and reaches 1 mm/year. Comparative analysis in identical tests for the surface of high-alloy steel 12Х18H10T (18 % Cr) showed that its resistance under CDC conditions is high, no corrosion manifestations of either a general or a local nature appeared on the surface of the sample. CO2 is widely used at some oil and gas facilities for injection into the formation in order to support technological tasks (for stimulation of production, disposal of surplus, underground gas storage, etc.). In such conditions, it can also pose a corrosive hazard to equipment and pipelines due to the increased salinity of the aqueous phase, high pressures and temperatures of the medium, and the presence of impurity gases. Even corrosion-resistant steels (with a chromium content of 13 %) are unstable in these media. To ensure the protection of oil and gas infrastructure facilities, more corrosion-resistant steels or the use of other means of protection against corrosion (corrosion inhibitors or others) are required. It is needed to carry out experimental investigations of corrosion in conditions of SCS CO2.
References
- Baidin I.I. Experience of countering carbon dioxide corrosion at the Yubileinoe OGCF. Nauka i tekhnika v gazovoi promyshlennosti. 2020. N 3 (83), p. 3-8 (in Russian).
- Aslanyan A.M., Aslanyan I.Yu., Kantyukov R.R. et al. Implementation of the Advanced Passive Acoustics Hardware and Software Complex for Well Integrity Diagnostics. Bezopasnost truda v promyshlennosti. 2020. N 11, p. 56-62. DOI: 10.24000/0409-2961-2020-11-56-62(in Russian).
- Ilinova A.A., Romasheva N.V., Stroykov G.A. Prospects and social effects of carbon dioxide sequestration and utilization projects. Journal of Mining Institute. 2020. Vol. 244, p. 493-502. DOI: 10.31897/PMI.2020.4.12
- Garaishin A.S., Bebeshko I.G., Grigorev A.V. et al. Investigation of the possibility of partial replacement of the buffer gas with carbon dioxide in underground gas storages. Vesti gazovoi nauki. 2015. N 3 (23), p. 79-83 (in Russian).
- Kantyukov R.R., Zapevalov D.N., Vagapov R.K. Assessment for the hazard of internal carbon dioxide corrosion in relation to field equipment and pipelines at gas and gas condensate fields. Bezopasnost truda v promyshlennosti. 2021. N 2, p. 56-62. DOI: 10.24000/0409-2961-2021-2-56-62 (in Russian).
- Dmitrievsky A.N., Efimov A.G., Gutman I.S. et al. Matrix oil and residual gas reserves of Orenburg oil-gas condensate field and prospects of their development. Aktualnye problemy nefti i gaza. 2018. N 4 (23), p. 1-20. DOI: 10.29222/ipng.2078-5712.2018-23.art22 (in Russian).
- Koryakin A.Yu., Dikamov D.V., Kolinchenko I.V. et al. Experience of corrosion inhibitors selection to protect the objects of the second site of achimovsky deposits of Urengoy oil and gas-condensate field from carbon acid corrosion. Oborudovanie i tekhnologii dlya neftegazovogo kompleksa. 2018. N 6, p. 48-55. DOI: 10.30713/1999-6934-2018-6-48-55 (in Russian).
- Zhirnov R.A., Derbenev V.A., Lyugai A.D. et al. Prospects for acid gas re-injection into the formation to improve the efficiency of field development (on the example of the Astrakhan GCF). Nauka i tekhnika v gazovoi promyshlennosti. 2020. N 1 (81), p. 32-39 (in Russian).
- Kantyukov R.R., Arbuzov A.A., Soroka S.V., Spirina L.A. Spectral Noise Logging for well integrity analysis in the mineral water well in Asselian aquifer. Georesursy. 2017. Vol. 19. N 2, p. 138-140. DOI: 10.18599/grs.19.2.9 (in Russian).
- Ryazantsev M.V., Lozin E.V. Carbon dioxide flooding: history of world and local investigations. Neftyanoe khozyaistvo. 2020. N 7, p. 100-103. DOI: 10.24887/0028-2448-2020-7-100-103 (in Russian).
- Slugin P.P., Polyanskii A.V. Optimal method for countering carbon dioxide corrosion of pipelines at the Bovanenkovskoye OGCF. Nauka i tekhnika v gazovoi promyshlennosti. 2018. N 2 (74), p. 104-109 (in Russian).
- S.A.Khan, A.N.Dmitrievskii, O.E.Aksyutin et al. Utilization and storage of carbon dioxide: global experience. Moscow: Gazprom VNIIGAZ, 2012, p. 168 (in Russian).
- Khan S.A., Dorokhin V.G., Bondarenko N.P. Using the features of the aggregate states of carbon dioxide to replace part of the buffer volume of underground gas storages. Gazovaya promyshlennost. 2016. N 4 (736), p. 50-54 (in Russian).
- Shakhverdiev A.Kh., Panahov G.M., R.Jiang et al. Efficiency of rheogaschemical EOR Technology based on in-situ CO2 generation a case study on the oil fields of China. Vestnik RAEN. 2012. N 4, p. 73-81 (in Russian).
- Cui G., Yang Z., Liu J., Li Z. A comprehensive review of metal corrosion in a supercritical CO2 environment. International Journal of Greenhouse Gas Control. 2019. Vol. 90. N 102814. DOI: 10.1016/j.ijggc.2019.102814
- Kumar S., Foroozesh J., Edlmann K. et al. A comprehensive review of value-added CO2 sequestration in subsurface saline aquifers. Journal of Natural Gas Science and Engineering. 2020. Vol. 81. N 103437. DOI: 10.1016/j.jngse.2020.103437
- Morks M.F., Corrigan P., Birbilis N., Cole I.S. A green MnMgZn phosphate coating for steel pipelines transporting CO2 rich fluids. Surface and Coatings Technology. 2012. Vol. 210, p. 183-189. DOI: 10.1016/j.surfcoat.2012.09.018
- Hou B.S., Zhang Q.H., Li Y.Y. et al. A pyrimidine derivative as a high efficiency inhibitor for the corrosion of carbon steel in oilfield produced water under supercritical CO2 conditions. Corrosion Science. 2020. Vol. 164. N 108334. DOI: 10.1016/j.corsci.2019.108334
- Onyebuchi V.E., Kolios A., Hanak D.P. et al. A systematic review of key challenges of CO2 transport via pipelines. Renewable and Sustainable Energy Reviews. 2018. Vol. 81. Part 2, p. 2563-2583. DOI: 10.1016/j.rser.2017.06.064
- Hua Y., Jonnalagadda R., Zhang L. et al. Assessment of general and localized corrosion behavior of X65 and 13Cr steels in water-saturated supercritical CO2 environments with SO2/O2. International Journal of Greenhouse Gas Control. 2017. Vol. 64, p. 126-136. DOI: 10.1016/j.ijggc.2017.07.012
- Kim C., Kim S.H., Cha J.-H. et al. Cr diffusion coating to improve the corrosion resistance of an ODS steel in super-critical carbon dioxide environment . Surface and Coatings Technology. 2019. Vol. 374, p. 666-673. DOI: 10.1016/j.surfcoat.2019.06.055
- Xu M., Zhang Q., Wang Z. et al. Cross impact of CO2 phase and impurities on the corrosion behavior for stainless steel and carbon steel in water-containing dense CO2 environments. International Journal of Greenhouse Gas Control. 2018. Vol. 71, p. 194-211. DOI: 10.1016/j.ijggc.2018.02.011
- Choi Y.-S., Hassani S., Vu T.N. et al. Effect of H2S on the Corrosion Behavior of Pipeline Steels in Supercritical and Liquid CO2 Environments. Corrosion. 2016. Vol. 72. Iss. 8, p. 999-1009. DOI: 10.5006/2026
- Hua Y., Barker R., Neville A. The effect of O2 content on the corrosion behaviour of X65 and 5Cr in water-containing supercritical CO2 environments. Applied Surface Science. 2015. Vol. 356. p. 499-511. DOI: 10.1016/j.apsusc.2015.08.116
- Hua Y., Barker R., Neville A. The influence of SO2 on the tolerable water content to avoid pipeline corrosion during the transportation of supercritical CO2. International Journal of Greenhouse Gas Control. 2015. Vol. 37, p. 412-423. DOI: 10.1016/j.ijggc.2015.03.031
- Ikeda A., Mukai S., Ueda M. Corrosion Behavior of 9 to 25 % Cr Steels in Wet CO2 Environments. Corrosion. 1985. Vol. 41. Iss. 4, p. 185-192. DOI: 10.5006/1.3581989
- Maldal T., Tappel I.M. CO2 underground storage for Snøhvit gas field development. Energy. 2004. Vol. 29. Iss. 9-10, p. 1403-1411. DOI: 10.1016/j.energy.2004.03.074
- Cuia G., Bi Z., Liu J. et al. New method for CO2 corrosion resistance Ni-W-Y2O3-ZrO2 nanocomposite coatings. Ceramics International. 2019. Vol. 45. Iss. 5, p. 6163-6174. DOI: 10.1016/j.ceramint.2018.12.093
- Pfennig A., Linke B., Kranzmann A. Corrosion behaviour of pipe steels exposed for 2 years to CO2-saturated saline aquifer environment similar to the CCS-site Ketzin, Germany. Energy Procedia. 2011. Vol. 4, p. 5122-5129. DOI: 10.1016/j.egypro.2011.02.488
- He M., Luis S., Rita S., Ana G. et al. Risk assessment of CO2 injection processes and storage in carboniferous formations: a review. Journal of Rock Mechanics and Geotechnical Engineering. 2011. Vol. 3. Iss. 1, p. 39-56. DOI: 10.3724/SP.J.1235.2011.00039
- Singer М. Study of the Localized Nature of Top of the Line Corrosion in sweet environment. Corrosion. 2017. Vol. 73. Iss. 8, p. 1030-1055. DOI: 10.5006/2222
- Cen H., Cao J., Chen Z., Guo X. 2-Mercaptobenzothiazole as a corrosion inhibitor for carbon steel in supercritical CO2-H2O condition. Applied Surface Science. 2019. Vol. 476, p. 422-434. DOI: 10.1016/j.apsusc.2019.01.113
- Vagapov R.K., Zapevalov D.N. Corrosion activity of operating conditions for the steel equipment and pipelines in the plants extracting CO2-containing gases. Metallurgist. 2021. Vol. 65, p. 50-61. DOI: 10.1007/s11015-021-01132-x
- Vagapov R.K., Ibatullin K.A., Zapevalov D.N. Corrosion Processes on Steel Under Conditions of Moisture Condensation and in the Presence of Carbon Dioxide. Chemical and Petroleum Engineering. 2020. Vol. 56, p. 673-680. DOI: 10.1007/s10556-020-00825-5
- Vagapov R. Top-of-line corrosion in the presence of carbon dioxide for gas production facilities. II International Conference “Corrosion in the Oil & Gas Industry”, 14-16 December, 2020, St. Petersburg, Russia. E3S Web of Conferences. 2021. Vol. 225. N 01002. DOI: 10.1051/e3sconf/202122501002
- Wei L., Gao K., Li Q. Corrosion of low alloy steel containing 0.5 % chromium in supercritical CO2-saturated brine and water-saturated supercritical CO2. Applied Surface Science. 2018. Vol. 440, p. 524-534. DOI: 10.1016/j.apsusc.2018.01.181
- Choi Y.-S., Young D., Nešić S., Gray L.G.S. Wellbore integrity and corrosion of carbon steel in CO2 geologic storage environments: A literature review. International Journal of Greenhouse Gas Control. 2013. Vol. 16. Supplement 1, p. S70-S77. DOI: 10.1016/j.ijggc.2012.12.028
- Yaro A.S., Abdul-Khalik K.R., Khadom A.A. Effect of CO2 corrosion behavior of mild steel in oilfield produced water. Journal of Loss Prevention in the Process Industries. 2015. Vol. 38, p. 24-38. DOI: 10.1016/j.jlp.2015.08.003
- Zapevalov D., Vagapov R. Aspects of protection against carbon dioxide corrosion of gas production facilities. I International Conference “Corrosion in the Oil and Gas Industry”, 22-24 May, 2019, St. Petersburg, Russia. E3S Web of Conferences. 2019. Vol. 121. N 02013. DOI: 10.1051/e3sconf/201912102013
- Zapevalov D., Vagapov R. Possibilities and limitations of the organization of anticorrosion protection at gas production facilities. II International Conference “Corrosion in the Oil & Gas Industry”, 14-16 December, 2020, St. Petersburg, Russia. E3S Web of Conferences. 2021. Vol. 225. N 03002. DOI: 10.1051/e3sconf/202122503002