Thermal protection implementation of the contact overheadline based on bay controllers of electric transport traction substations in the mining industry
- 1 — Research Engineer Peter the Great Saint Petersburg Polytechnic University ▪ Orcid ▪ Elibrary
- 2 — Ph.D. professor Peter the Great Saint Petersburg Polytechnic University ▪ Orcid ▪ Elibrary ▪ Scopus
- 3 — Ph.D. Head of the Institute of Energy Peter the Great Saint Petersburg Polytechnic University ▪ Orcid
- 4 — Ph.D. Member of the Board Leibniz Institute for Plasma Research and Technology ▪ Orcid
- 5 — Ph.D. Assistant professor Brno University of Technology ▪ Orcid
Abstract
The article presents the principle of thermal protection of the contact overheadlineand substantiates the possibility of practical implementation of this principle for rail electric transport in the mining industry. The algorithm for the implementation of modern digital protection of the contact overhead line as one of the functions of the controller is described. A mathematical model of thermal protection is proposed, which follows from the solution of the heat balance equation. The model takes into account the coefficient of the electrical networktopology, as well as the coefficient of consumption of the current-carrying core of the cable, which determines the reduction in the conducting section from contact erosion and the growth of oxide films. Corrections for air flows are introduced when receiving data from an external anemometer, via telemechanics protocol. The mathematical model was tested by writing a real thermal protection program in the C programming language for the bay controller, based on the circuitry of which is the STM32F407IGT6 microcontroller for the microcontroller unit. Verification tests were carried out on a serial bay controller in 2020. The graphs for comparing the calculated and actual values of temperatures, with different flow rates of the current-carrying conductor of the DC cable, are given. To obtain data, telemechanics protocols IEC 60870-104 and Modbus TCP, PLC Segnetics SMH4 were used.
Introduction
All modern traction electrical substations use digital electronic equipment. The most common mid-level bay controllers are based on microcontrollers with an ARM Cortex-M4 core from various manufacturers. In our country, controllers from ST or Texas Instruments are popular, for example, the TMS320F28335 controller. An example of the implementation of such controllers is considered in the work [23]. Their use is economically justified as they can confidently support a real-time operating system, for example, FreeRTOS. Bay controllers are assigned the tasks of horizontal communication with other controllers and vertical communication with the substation level controller, as well as communication with various lower-level devices. At the middle level of the digital substation system, it is necessary to record alarm oscillograms in the Comtrade format for subsequent download and analysis of the development of the accident in accordance with IEC 60255-24, for example, in publications [25, 29] the oscillograms were obtained as a result of modeling the operation of the telemechanics relay. As a rule, bay controllers implement several protections, for example, current and differential, and in DC systems, thermal protection against overheating of the contact overhead line is also very important [4, 9, 13], causing a decrease in the conductivity cross section from contact erosion and the growth of oxide films of the copper conductor core. Thermal protection of the contact overhead line protects against low short-circuit currents and is designed to disconnect the supply feeder when the design temperature of the contact wire approaches the copper annealing temperature. The main problem of dealing with small short-circuit currents is of particular relevance in the mining industry, since any interruptions in the operation of power supply entail large financial losses and human casualties. Of greatest interest may be the implementation of this algorithm at iron ore enterprises equipped with traction electric locomotive transport with a maximum DC voltage of up to 600 V.
Formulation of problem
The controller continuously measures the feeder load current with a sampling rate of 100 kHz and, on its basis, calculates the temperature of the overhead wire. When the maximum wire temperature is reached, the controller unconditionally disconnects the circuit breaker, which occurs regardless of the selected connection telemechanics control mode, both in local and remote modes. The object of research in this work is the contact overhead line thermal protection (CNTP), where the set point of operation is the calculation of the critical temperature of the current-carrying wire.
The proposed method must be implemented using a microcontroller and have acceptable limitations. In addition, for effective operation in a modern digital substation system, the bay controller must support the IEC 60870-104 and IEC 61850 protocols, since it is prohibited to work without the possibility of integration using these protocols by the departmental orders of the organizations operating the substations. The use of the IEC 61850 protocol requires an ICD file that describes the capabilities of the device using the format. When new equipment is integrated into the sub-station network, new devices are automatically added to the general data exchange structure, which reduces the costs of commissioning.
The article [28] describes an abstract model of the system, implemented in accordance with the IEC 61850 protocol, and also considers the use of a subset of the GOOSE and MMS protocols in the substation communication system. To implement these functions, it is necessary to have a reliable file system on an external NOR Flash medium for the microcontroller. Programming techniques for increasing the reliability of file systems on embedded systems were discussed in the article [27]. The equipment also performs the functions of non-destructive testing. In the article [8] the features of the actual methods of non-destructive testing are considered. In publication [7] methods of managing the process of controlling the hardness of current collectors in non-destructive testing are described, permissible defects in non-destructive testing are discussed in the article [18]. The task of responding to abnormal situations identified by non-destructive testing is described in the article [6]. The power supply of the rectifier units of the DC substation must comply with the standards [2, 10, 12], else it is required to use installations for reactive power compensation [20, 32, 33]. Inthearticle [35] the method of connecting the filtering device to the substation is described. The feeder must be equipped with an arc extinguishing device, the principles of operation of these devices are described in the articles [22, 30, 31]. Mine network requires additional spark protection [5]. Modeling of relay protection devices for overhead contact overhead line is discussed in publications [1, 11, 14]. The issue of synthesis of the measuring triggering device of relay protection and automation is considered in the article [17]. The device must meet the requirements of speed and selectivity [3, 16].
Research methods
Previously, the implementation of thermal protection of the contact overhead line was considered by different authors [21, 24, 34]. Original mathematical models were proposed, but some of them are unnecessarily complicated to implement in practice and organize calculations on a small embedded device. The purpose of calculations used in this paper, under the accepted assumptions, is a method of protection implemented in practice in an embedded system. This means that the result of the work is a ready-made mathematical algorithm for quickly calculating the temperature of the overhead line from the current flowing through the feeder. The task of the research consists, firstly, in deriving a theoretical formula, which in the accepted confidence interval will be sufficient for use in calculations with limited computing resources; secondly, in the use of empirical relationships obtained from experimental studies.
To obtain practical results, the hardware part of a real bay controller with modified firmware was used specifically for testing. The controller measures the feeder current through a current level converter –1000-1000 A to –5-5 mA. A 32-bit microcontroller from ST STM32F407IGT6 is located on the main board of the bay controller. To create a C program, QT Creator and the Carm-none-eabi-gcc language compiler were used as an integrated development environment, where arm-none-eabi-gdb with the OpenOCD program was used as a debugger.
Most modern temperature calculation methods [15, 19, 26] of the wires of the contact overhead line and the permissible current load are based on the solution of the heat balance equation written in differential form per unit of length of the bare wire (1 m) at a fixed value of the current in the wire,
where С– heat capacity of the wire, W∙s/(°C ∙m) (taken independent of temperature); vt – overheating temperature of the wire relative to the ambient temperature, °С; I – current value in the wire, А; R0 – DC resistance of 1 m wire at temperature 20 °С, Ohm/m; α – temperature coefficient of wire resistance, °С–1; t – current time, s; k – coefficient taking into account the heat transfer from the wire to the environment, W/(°С∙m).
After integrating the left and right sides of the equation, the indefinite integrals can be taken, and then a constant term, which can be determined from the initial conditions to the solution, can be added. If the values of the temperature settings of the thermal protection do not exceed 100 °C, then the effect of changing the resistance value from the wire temperature on the calculation error can be considered insignificant. Based on this, it will be considered as α = 0.
Despite the fact that the current in the overhead wire changes continuously, when calculating by a digital method based on the stated mathematical model, during the calculated period of time in the controller the current will be understood as a constant effective value. It will be equivalent to the generation of heat in the wire. It is assumed that the error of the temperature calculation will not affect the efficiency of the overhead protection against high temperatures. The key parameter in this simplification is the value of the duration of the calculation period. When choosing this value, it is necessary to take into account the calculation speed of the controller, the load of the processor with related tasks, on the one hand, and the inertia of thermal processes in the material of the catenary wire, on the other, this ensures the requirement for the speed of protection:
Table 1
Loss factor for different wind speeds
V, m/s |
k |
V = 0 |
3,4 |
0 < V < 2 |
4,9 |
2 < V < 4 |
5,7 |
4 < V < 10 |
7,3 |
10 < V |
8,3 |
Table 2
Transient time constant for major cable brands
V, m/s |
τ MF85 |
τ MF100 |
V = 0 |
86 |
102 |
0 < V < 2 |
60 |
70,8 |
2 < V < 4 |
52 |
61,3 |
4 < V < 10 |
40,3 |
47,5 |
10 < V |
35,4 |
41,8 |
where Irms – rms value of the feeder current in the current calculation cycle; vt, vt+1– the calculated temperature of heating the wire in the previous and current calculation cycles, respectively; R – ohmic resistance 1 m wire; kc – network topology ratio; ki – wire wear factor; k – heat loss coefficient (Table 1); τ – the time constant of the transient process (Table 2).
From expression (1), as a result of mathematical transformations and the previously described simplifications, formula (2) is derived, which can be used in digital calculations on a microcontroller installed on the bay controller.
The magnitude of the current in the feeder is very unstable, mainly due to the fact that the connection of electric transport is made by sliding the current collectors along the overhead wires of the contact overhead line.
As mentioned, in order to perform wire temperature calculations, it is necessary to determine the effective value of the feeder current in one second. It is well known that the effective value is calculated as the effective value of the output current for a given sample. This value is defined as the square root of the sum of the squares of the input values divided by the sample size value. Obtaining the next current value can be a condition for starting the calculation cycle to determine a new current value of the wire temperature.
The heat balance equation takes into account the dissipation of heat energy from the wire in the form of the value of the loss factor k. Losses consist of two main components: convective and radiation losses. Convective losses are formed due to the transfer of heat by a contact method from the surface of the wire to the ambient air. The determining factors of heat transfer in this case are the speed and direction of the air flowing around the wire. Due to the fact that it is technically difficult to obtain these values for specific sections of the contact overhead line with a minimum error, accounting for convective heat losses has to be calculated by an averaged empirical method developed on the basis of experimental data [15]: k = 2.81v0,59+ 3.4, where the first term is formed by the contribution of convective losses, is derived from the criterion equations and substitution of the average value of the radius of the wires considered in Table 2; the second term is formed by the contribution of radiation losses without taking into account the temperature of the ambient air and the wire due to their small number. If we take the emissivity of the wire surface ε = 0.78 (oxidized copper), then kε =3.4, according to the formula from article [15], where it is given as a calculated one to determine the irradiation loss:
To facilitate the calculations of the temperature for a new wire, it is advisable to calculate the values of the loss factor for several ranges of wind speed values and place them in the calculation table (Table 1), which can be used to simplify calculations on the microcontroller. The calculation error with such a simplification can be considered insignificant. Thus, when calculating the temperature, it is necessary to take into account the wind speed and heat capacity, which depends on the mass, i.e. on the wire brand. If by wire consumption we mean a change in the shape of its cross-section due to the erosion effect of current receivers of the rolling stock and the appearance of an oxide film, then two parameters of the wire change, which significantly affect its temperature during operation. A decrease in the cross-sectional area leads to an increase in the resistance to current, and a decrease in mass leads to a decrease in the heat capacity of the wire.
The heat capacity of the wire increases with increasing weight (changing the wire brand) and decreases with increasing wire consumption; accordingly, the time constant of the transient process increases or decreases. A wire with a large cross-section heats up slower, and worn out – faster. The time constant of the transient process depends on the heat capacity of the wire and the heat loss coefficient. Table 2 shows the calculated values of the time constant of the transient process for the main brands of cable when the temperature of the wire changes. This table will be entered into the microcontroller memory to simplify calculations, it is assumed that the wire resistance does not depend on temperature.
The amount of current measured by the feeder bay controller is the sum of the currents flowing through the overhead wires. The actual distribution of currents in each wire depends on many factors that are technically impossible to take into account. In practice, in most sections of the overhead wires, the current value can be significantly less than the current value measured at the controller converter. Therefore, the actual heating of these wires may be less than the calculated value. In this case, the thermal protection may be triggered prematurely. However, by setting the network topology coefficient, it is possible to approximately take into account the design features of this network section to reduce the likelihood of false alarms of thermal protection, thereby ensuring the necessary selectivity requirement. In terms of calculating this coefficient, further improvement of calculation methods for thermal protection of the contact overhead line is possible.
Discussion
To check the above theoretical formula, experimental studies were carried out at the traction substation of urban electric transport. The voltage parameters on the DC buses of the traction substation of urban electric transport fully correspond to the voltage parameters at the iron ore mine (600 V DC), the characteristics of the rolling stock used are approximately equivalent.
The values of air temperature, air flow rate, wire grade, conductor consumption and topology of the contact overhead line, as well as alarm and protection temperature settings must be supplied to the controller from the telemechanics protocol from the corresponding measuring transducers.
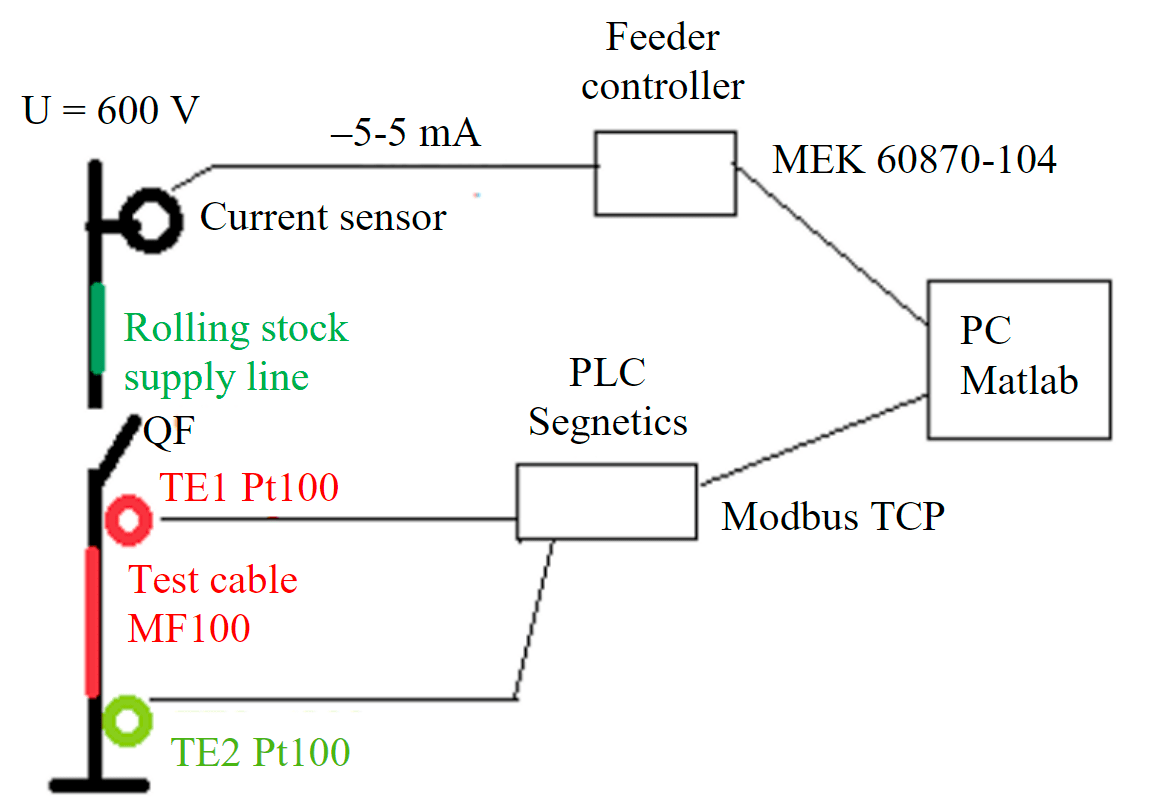
Fig.1. Experiment scheme
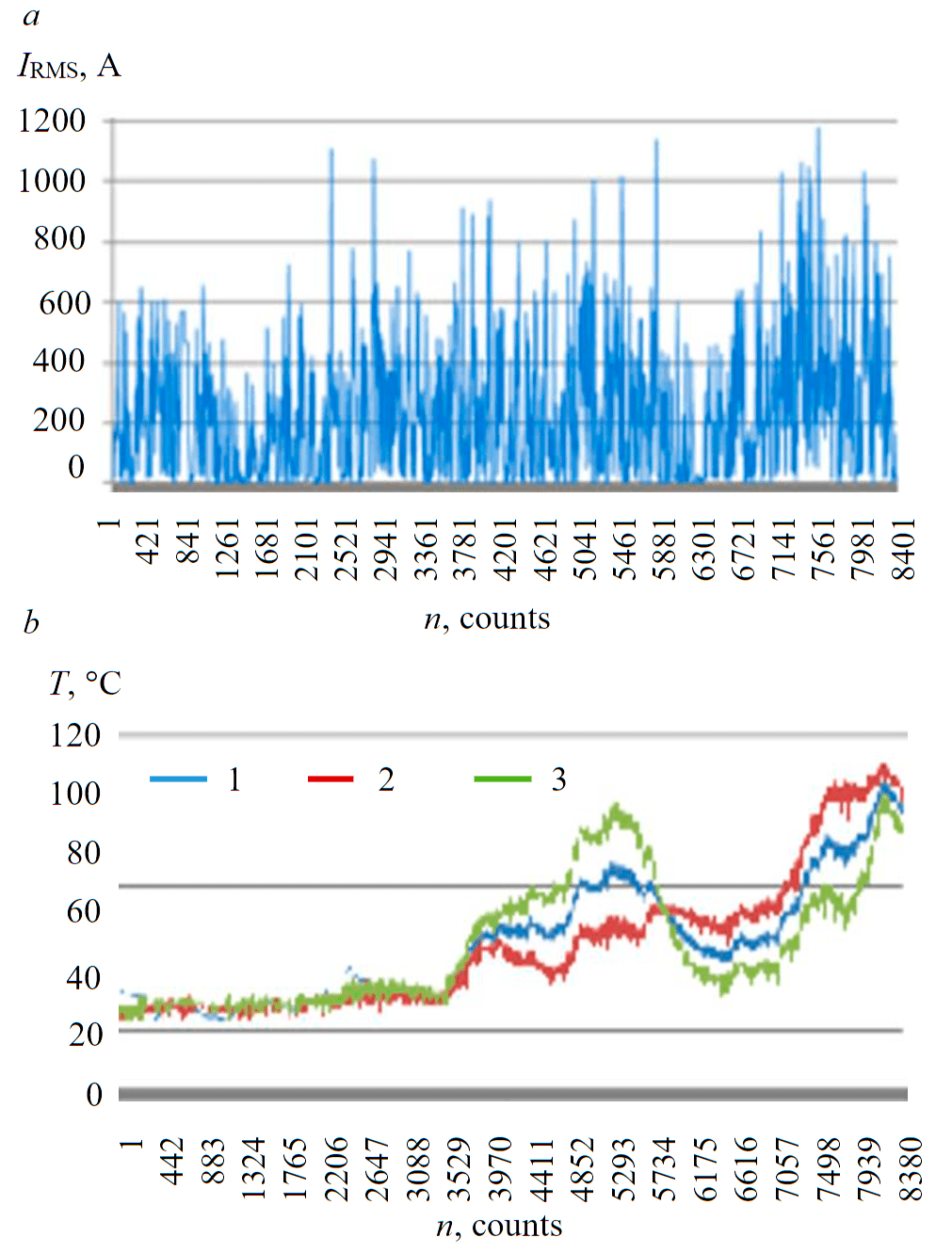
Fig.2. Dependences of the effective value of the current (a), calculated and actual temperatures (b) of the cable from the readings (1 count – 100 ms) 1 – Tmcu; 2 – Tpt100(1); 3 – Tpt100(2)
The test program for the controller is written in the C programming language; formula (2) is used as a method for calculating the temperature by measuring the current. To control the results of the experiment, a wire of the MF100 type was used, two Pt100 contact temperature sensors were connected in different parts of the MF100 cable.
The scheme of the experiment is shown in Fig.1. One contact sensor was installed on a new cable section, the second – on the cable section with a flow rate. These Pt100 sensors were connected to the Segnetics SMH4 PLC to receive data from them via the Modbus TCP protocol, then through the OPC Server to the analysis program on the MATLAB Simulink computer.
The data measured by the device under test was obtained by a program implemented in MATLAB from an OPC server of the IEC 60870-104 protocol implemented on the baycontroller. MATLAB Simulink OPC client received data via Modbus TCP and IEC 60870-104 protocols to receive data in CSV format. The data obtained were used to plot the graphs shown in Fig.2.
In Fig.2, a, the effective value of the current varies unevenly due to the peculiarities of the operation of the equipment installed on electric vehicles. The current surges are explained by the fact that trams start from a place, at the moment of their uniform movement, the current consumption is much lower than the peak values presented in the graph. When braking electric vehicles, recuperation can be observed, in which case the current will be negative. To limit the influence of sharp fluctuations in DC values when implemented on a microcontroller, a median filter was applied in the analog-to-digital conversion module from the measuring channel after reading the values via the SPI bus. Then the recursive Kalman filter was applied. Thus, the transient processes caused by the acceleration modes of traction vehicles were correctly taken into account by the proposed algorithm.
Figure 2, b shows the values of the calculated wire temperature obtained from the baycontroller, and two values of the wire temperature measured by the Segnetics SMH4 PLC using Pt100 sensors, which were installed on the wire at points with different values ki.
Conclusion
Analysis of the graphs (Fig.2) showed that in the first half of the experiment, the calculated temperature Tmcu corresponded to the values of the Pt100 sensor, in the second half, there are some discrepancies between the calculated and actual temperatures, however, to assess the adequacy of the protection operation, it is sufficient that it accurately reproduce the trends, while absolute values are not very important. These discrepancies are explained by the linearity of the Pt100 temperature sensor, as well as different wire wear factors and network topology.
At the end of the experiment, the thermosensitive sensor 2 was forcibly cooled by a fan; therefore, its readings became lower than the calculated temperature, thereby the effect of air flows on the cable was reproduced.
As a result of the experiment, it was found that the main regularities of the conductor core consumption from atmospheric exposure (oxide film growth) and electrical contact erosion, leading to overheating of the conductor, are adapted to the protection system based on the baycontroller used at the digital substation. The obtained absolute errors of indirect measurements do not exceed 10 % with the correct setting of the coefficients for expression (2). The model proposed by the authors has some assumptions, namely: during each cycle of temperature calculations, the values of the current and temperature of the wire are considered constant. Also, the resistance of the wire during the measuring cycle does not depend on the change in its temperature.
An algorithm for calculating the temperature of the overhead line by measuring the current is proposed, and the correctness of the obtained formula for its determination on the basis of practical implementation at a traction substation is proved. The developed method can be recommended for use on traction substation connection controllers in iron ore mines at mining enterprises with direct current contact electric locomotives.
References
- Kukharchuk A.V., Zhdanova D.I., Kvitko Ya.I. et al. Analysis of the use of the software “ELPLEK” for modelling relaying. Fundamental research. 2016. N 11-3, p. 543-547 (in Russian). URL
- Vangin G.Ya. Comment on the new standard for the quality of electric power GOST R 54149-2010 and attributed standards. Industrial power engineering. 2013. N 1, p. 39-43 (in Russian). URL
- Vdovin S., Shalimov A. The enhancement of sensitivity and performance of shunt reactor’s transverse differential current protection with application of dynamic cold load pickup. Relay protection and automation. 2011. N 3 (4), p. 58-61 (in Russian). URL
- Garanin M.A., Blinkova S.A. Approbationof the technology of data collection from the TsZAP and TZKS devices. Vestnik transporta Povolzhya. 2015. N 5 (53), p. 31-36 (in Russian). URL
- Kovalev A.P., Nagornyi M.A., Solenyi S.V., Demchenko G.V. Protection of an electrical mine network with voltage up to 1000 V against sparking in power contact connections. Vzryvozashchishchennoe elektrooborudovanie. 2010. N 1, p. 109-115 (in Russian). URL
- Zvonkov I.V. Providing non-destructive testing of the railway track with limited resources. Transportnaya infrastruktura sibirskogo regiona, 10-13 aprelya 2018, Irkutsk, Rossiya. Irkutskii gosudarstvennyi universitet putei soobshcheniya, 2018. Vol. 1, p. 413-417 (in Russian). URL
- Kirkov I.S., Silvestrov Yu.G. Development of methods for managingthe hardness control process in a non-destructive testing laboratory. Sovremennyi stil upravleniya, 28 oktyabrya 2016, Cheboksary, Rossiya. Chuvashskii gosudarstvennyi pedagogicheskii universitetim. I.Ya.Yakovleva, 2016, p. 590-594 (in Russian).
- Loshkarev I.Yu., Chernyshov A.S. Non-destructive testing. Features of non-destructive testing methods. Aktualnye problemy energetiki APK, 1-30 aprelya 2013, Saratov, Rossiya. Izhevsk: Bukva, 2013, p. 184-186 (in Russian).
- Paranin A.V. Improvement of aerodynamic and thermal calculations of overhead wires: Avtoref. dis. … kand. tekhn. nauk. Ekaterinburg: Uralskii gosudarstvennyi universitet putei soobshcheniya, 2011, p. 24 (in Russian).
- Popov O.Yu., Loginova E.Yu. Determination of permissible deviations of the mains voltage for various approaches to the norms of power quality. Obrazovatelnaya sreda segodnya i zavtra: Sbornik nauchnykh trudov IX Mezhdunarodnoi nauchno-prakticheskoi konferentsii, 30-31 oktyabrya 2014, Moskva, Rossiya. Moskovskii tekhnologicheskii institut, 2014, p. 331-334 (in Russian).
- Pupynin V.N., Subkhanverdiev K.S., Nikolaev M.V. Partially non-selective overhead protection. Lokomotiv. 2015. N 9 (705), p. 40-41 (in Russian).
- Sosnina E.N., Shalukho A.V. To the analysis of power quality standards for local power supply systems. Elektrooborudovanie: ekspluatatsiya i remont. 2013. N 3, p. 50-54 (in Russian).
- Tolstikova A.N., Tolstikov N.G. Thermal protection of electric transport overhead lines.Vostochno-Evropeiskii zhurnal peredovykh tekhnologii. 2010. Vol. 2. N 7, p. 30-32. DOI: 10.15587/1729-4061.2010.2698 (in Russian).
- Umarov U., Bedritskii I.M. Modeling the action of relay protection in overhead line feeders using MATLAB and SimPowerSystems software packages. Molodezh v nauke: novye argumenty, 27 marta 2015, Lipetsk, Rossiya. Lipetsk: Argument, 2015, p. 96-98 (in Russian).
- FigurnovE.P., ZharkovYu.I., PetrovaT.E., Kuusk A.B. Refinements to the basics of the theory of heating wires of overhead power lines. Izvestiya vysshikh uchebnykh zavedenii. Elektromekhanika. 2013. N 1, p. 36-40 (in Russian). URL
- Nagai I.V., Nagai V.I., Sarry S.V. et al. Formalization of the procedure for recognizing emergency modes of electrical networks. Kibernetika energeticheskikh sistem, 25-26 sentyabrya 2018, Novocherkassk, Rossiya. Yuzhno-Rossiiskii gosudarstvennyi politekhnicheskii universitet imeni M.I.Platova, 2018, p. 359-364 (in Russian).
- Sharygin M.V., Kulikov A.L., Petrov A.A. Synthesizing a universal multidimensional relay protection measuring and starting element. Elektrichestvo. 2020. N 1, p. 4-11. DOI: 10.24160/0013-5380-2020-1-4-11 (in Russian).
- Shtefan Yu. Standards for the admissibility of defects in non-destructive and static testing. Upravlenie kachestvom. 2018. N 5, p. 55-58 (in Russian). URL
- Deng Shiyuan, Xin Jianqiang, Zhang Kun et al. Assessment of thermal reliability of thermal protection systems by importance sampling method. Journal of Chongqing University. 2019. Vol. 42. Iss. 2, p. 62-70. DOI: 10.11835/j.issn.1000-582X.2019.02.007 (in Chinese).
- Bystrov A., Lantsev D. Pulse generator of a polygonal design with a high rate of voltage. International Scientific Electric Power Conference, 23-24 May 2019, Saint Petersburg, Russian Federation. IOP Conference Series: Materials Science and Engineering, 2019. Vol. 643. N 012073. DOI: 10.1088/1757-899X/643/1/012073
- Sungwook Kang, Minjae Kwon, J. Yoon Choi, Sengkwan Choi. Development of Testing Environment for Thermal Protective Clothing at Critical Conditions. The Proceedings of 11th Asia-Oceania Symposium on Fire Science and Technology, 22-24 October 2020, Taipei, Taiwan. Springer, 2020, p. 435-449. DOI: 10.1007/978-981-32-9139-3_32
- Ehrhardt A. Arc Fault Protection System in Low-Voltage Installations for Protecting Installations and Persons. Plasma Physics and Technology. 2015. Vol. 2, p. 120-123. URL
- Frolov V., Bystrov A., Neelov A. Imitating model of a microprocessor trip unit of a circuit Breaker. Proceedings of the 2017 IEEE Russia Section Young Researchers in Electrical and Electronic Engineering Conference (ElConRus), 1-3 February 2017, St. Petersburg and Moscow, Russia. IEEE, 2017, p. 838-840. DOI: 10.1109/EIConRus.2017.7910686
- Huang Jie, Yao Weixing. Damage Tolerance Analysis on Thermal Protection System. Journal of Nanjing University of Aeronautics and Astronautics. 2018. Vol. 50. Iss. 4, p. 509-515. DOI: 10.16356/j.1005-2615.2018.04.012 (in Chinese).
- Frolov V., Neelov A., Zhiligotov R., Bystrov A. Identification of the protection parameters of the local electrical network taking into account the detuning of the inrush current. Proceedings of the 2018 IEEE Conference of Russian Young Researchers in Electrical and Electronic Engineering (ElConRus), 29 January – 1 February 2018, Moscow and Saint Petersburg, Russia. IEEE, 2018, p. 626-628. DOI: 10.1109/EIConRus.2018.8317174
- Jupe S., Murphy G., Kazerooni A. De-risking the implementation of real-time thermal ratings. 22nd International Conference and Exhibition on Electricity Distribution (CIRED 2013), 10-13 June 2013, Stockholm, Sweden. CIRED, 2013. DOI: 10.1049/cp.2013.1075
- Lantsev D., Frolov V. Methods of increasing the reliability of external memory of digital substation bay controllers. International Scientific Electric Power Conference, 23-24 May 2019, Saint Petersburg, Russian Federation. IOP Conference Series: Materials Science and Engineering, 2019. Vol. 643. N 012117. DOI: 10.1088/1757-899X/643/1/012117
- Matousek P. Description of IEC61850. Faculty of Information Technology Brno University of Technology 2018. Technical Report N FIT-TR-2018-01.
- Othman M., Ishak A., Wahab N. Modeling and simulation of the industrial numerical distance relay aimed at knowledge discovery in resident event reporting. Malaysia Journal Citation Reports. 2014. Vol. 90. Iss. 6, p. 660-686. DOI: 10.1177/0037549714532961
- Schau H., Ehrhardt A. Proving tripping safety and immunity against malfunctions of the optical arc detection components of a novel electric arc protective system. International Conference on Live Maintenance (10th ICOLIM), 31 May – 2 June 2011, Zagreb, Croatia. Technische Universität Ilmenau, 2011. N 2012200106. URL
- Schau H., Bessei H. The Influence of fuses on arcing fault energy and personal protective clothing required. 9th International Conference on Electrical Fuses and their Applications (ICEFA), 12-14 September 2011, Maribor, Slovenia. ICEFA, 2011, p. 9. URL
- Shklyarskiy Ya.E., Skamyin A.N. Compensation of the reactive power in the presence of higher voltage harmonics at coke plants.Coke and Chemistry. 2016. Vol. 59, p. 163-168. DOI: 10.3103/S1068364X16040062
- Skamyin A.,Belsky A.A. Reactive power compensation considering high harmonics generation from internal and external nonlinear load. IOP Conference Series: Earth and Environmental Science. 2017. Vol. 87. Iss. 3. N 032043. DOI: 10.1088/1755-1315/87/3/032043
- Wojtkowski W. LED Power Supply with Thermal Protection for Automotive Application. VII Lighting Conference of the Visegrad Countries (Lumen V4), 18-20 September 2018, Trebic, Czech Republic. IEEE, 2018. DOI: 10.1109/LUMENV.2018.8521069
- Zamyatin E., Voytyuk I., Zamyatina E. Filter compensating devices connection technique. IEEE Conference of Russian Young Researchers in Electrical and Electronic Engineering (EIConRus), 28-31 January 2019, Saint Petersburg and Moscow, Russia. IEEE, 2019. N 18505271. DOI: 10.1109/EIConRus.2019.8657107