Oilfield service companies as part of economy digitalization: assessment of the prospects for innovative development
- 1 — Ph.D., Dr.Sci. associate professor Branch of Gazprom VNIIGAZ LLC in Ukhta ▪ ResearcherID
- 2 — Senior Lecturer Ukhta State Technical University
Abstract
The digital transformation of the economy as the most important stage of scientific and technological progress and transition to a new technological structure is becoming one of the determining factors in the development and competitiveness of the domestic upstream sector. Prospects for innovative development of oilfield service companies are the key technological areas within the first project of the Hi-Tech Strategy of the German Government until 2020 – “Industry 4.0”. The purpose of this study is to assess the prospects for innovative development of the domestic oilfield service industry in the context of the digitalization of the oil and gas industry. The subject of the research is the process of the formation of key technological lines of “Industry 4.0” and their impact on the domestic oil and gas sector. The research is based on logical-theoretical and empirical analyses. The main factors that determine processes of digital transformation in the oil and gas industry are considered; the results of digitalization processes in the largest foreign and Russian industry companies of the upstream and oilfield services segments are presented. The information base is made up of data from oilfield service and oil and gas producing companies, presented on the official websites of companies in the public domain on the Internet. It has been proven that, unlike the world's leading companies in oilfield services segment, independent domestic oilfield service companies provide mainly traditional service technologies in a fairly narrow range. The limited scope of functioning and technological capabilities of Russian companies is explained by the lack of necessary investment in development and expansion of business, as well as interest on the part of the state and corporate sectors in the development and replication of domestic technologies and the formation of a full-fledged oilfield services market in Russia.
Introduction. Today foreign and domestic oilfield service companies, as well as oil and gas industry as a whole, face great challenges. The consequences of structural changes in the oil and gas industry have proved to be highly controversial for traditional forms of business organization. Experts note that few industries can witness similar economic, technical, geographic, and operational challenges [21]. At the same time, one of the biggest problems that oilfield service companies currently face is the transition of most of the client base from super-majors to national oil companies, which has significantly changed the competitive landscape of the industry in recent decades [16, 23].
The oilfield services business has focused on technologies to maximize recovery, development, and productivity through aggressive drilling, stimulation and enhanced hydrocarbon recovery programs. The oil and gas sector has also moved into new geographic, geological, and technical boundaries. Despite the difficult financial situation in the oilfield services sector, caused by a sharp decline in oil prices, as a result of which investments in the oil and gas industry have significantly decreased, the oilfield services market is starting to recover. Leading companies Schlumberger, Halliburton, and Baker Hughes a GE Company began to receive large orders from mining companies [24]. Even today, the greatest demand for high-tech services is shown by countries of the Middle East, Africa, post-Soviet territory, as well as the Asia-Pacific region and Canada [20, 22, 25]. Opportunities offered for oilfield service companies are significant, associated with changes in all aspects of business, including technology, products, processes, as well as organizational capabilities and operating models. Traditional strategies based on historical industry cycles can lead, at a minimum, to missed business opportunities and can no longer be considered satisfactory. The main effect of the development and use of science-intensive products, technological developments in the oil and gas business is to increase efficiency of operating activities by reducing operating costs. The global experience of running oil and gas business testifies to development of new technological solutions using large-scale digitalization as the most important way to survive and maintain profitability indicators for “supermajors” and national oil companies. This direction requires a deeper restructuring of the operating model of companies and a change in management philosophy, which is even more important for suppliers and contractors.
The domestic oil and gas business has a powerful, but still unrealized potential. Despite the fact that technology trends in the oil and gas sector are often overlooked, digitalization is becoming increasingly important for the domestic oil and gas industry. Modern solutions in the search, exploration, and production of hydrocarbons (for example, big data, industrial Internet, robotization and artificial intelligence) make it possible to increase the competitiveness of field products, mainly by reducing the cost of hydrocarbon production [5]. It should be noted that the use of advanced capabilities of computer technology in the last decade of the twentieth century and their use in the domestic oil and gas industry led to a reduction in the cost of finding new fields by an average of 40 % (due to the use of 3D seismic models), an increase in proven reserves increment by an average of 2.5 times, an increase in drilling speed by 1.5 times, and an increase in the volume of recoverable oil. According to experts from Deloitte, the use of digital technologies is effective even in depleted fields, since it helps to increase their productivity [6]. The use of approaches, solutions, and technologies based on the principles of intellectualization will reduce operating and investment costs by 10-15 %, and provide an increase in the oil and gas production by 5-15 % [14].
According to the Analytical Center for the Government of Russia [11] only 31 out of 77 represented subjects of the Russian Federation have a digitalization program or a project. Among other priority areas of digitalization within the framework of regional programs “Digital Economy”, oil and gas industry was mentioned by only two subjects: the oil refining sector in the Republic of Bashkortostan and the oil and gas sector in the Tomsk region. Since 2017, the largest domestic oil corporations, – PJSC Gazprom Neft, PJSC Zarubezhneft, PJSC NK Rosneft have not only implemented a number of projects to introduce the latest technological solutions, but have also adjusted their business innovation programs for the future.1
Calculations carried out by Vygon Consulting indicate that in the current tax environment, the digitalization will contribute to an increase in the share of profitable hard-to-recover reserves (HTR reserves) of oil and additional exploration oil assets up to 70-80 % with a potential reduction of drilling costs by 10-15 %. With the transition to digital technologies, the adaptation of innovative technologies for low-permeability reservoirs, the Tyumen formation and high-viscosity oil will be carried out much faster. This will lead to an increase in the oil recovery ratio for this category of assets from 25-30 % to 36 % [5].
However, until now, the implementation of digital transformation process of oil and gas production industry in Russia have been hampered not only by financial, but also by technological, as well as informational risks. Under these conditions, the development and implementation of innovative technological solutions within the digital economy will largely rely on new forms of interaction between mining and service companies. Thus, the development of technological innovations within the digitalization of the oil and gas industry must be considered in direct connection with oil service companies.
The paper discusses the features of digital technologies application in relation to companies in the upstream and oilfield segments. To assess the prospects for the transition of domestic oil and gas producing and oil and gas service companies to digitalization technologies, the authors analyze the process of formation of key technological areas of Industry 4.0, results of the introduction of a number of digital technologies in Russian practice, as well as advantages and risks associated with digitalization of the oil and gas industry.
The main objectives of the study are: to consider the main stages of digitalization of the global oil and gas industry and priority areas of its development; to compare the experience of implementing Industry 4.0 technologies for foreign and domestic oilfield service companies; to evaluate the results of the introduction of digital technologies in the oil and gas production segment.
Research methodology. In the course of the research, general scientific research methods were used (comparison, generalization, analogy), methods of empirical analysis, methods of technical and economic analysis. The research is based on logical-theoretical and empirical analyzes..
Digitalization of the global oil and gas industry: main stages and priority areas of the development. The term “Industry 4.0” was introduced into circulation after the international industrial exhibition in Hannover in 2011. The concept of “Industry 4.0” implies “a transition to fully automated digital production, controlled by intelligent systems in real time in constant interaction with external environment, going beyond the boundaries of one enterprise with the prospect of uniting into the global industrial Internet of things” [5].
Key technological areas of Industry 4.0:
• Big Data as defined by Gartner2, is a variety of data that comes in at an ever-increasing speed and volume.
• IIOT (Industrial Internet of Things) is connection to the Internet of any non-consumer devices, equipment, sensors, receivers, automated process control system, as well as integration of these elements with each other, which leads to the formation of new business models when creating goods and services, as well as their delivery to consumers.3
• Robotization is an active introduction directly into the production process and (or) its maintenance of robots, in particular, visual and measuring control of hard-to-reach objects.
• Digital twins – visualization of objects – are a digital copy of a physical object4, in particular, a model of a field, well, equipment or infrastructure elements, which allows to test and predict the effects of using certain options, as well as visualize the results obtained in a user-friendly form [8];
• Smart materials are materials whose properties change when exposed to any external factors.5
• 3D printing is a technology that allows to create real objects from a digital model, in particular, development projects and field development schemes, as well as create new components for sensors and controllers, pumps and other equipment [8];
• Blockchain (Distributed ledger) is a distributed database that stores information about all transactions of system participants in the form of a “blockchain”.
Despite the fact that terminology of digitalization has spread out relatively recently, the pioneers of this direction were precisely companies of the oil and gas industry. According to Ernst & Young, back in the early 1960s, computers were used for reservoir modeling, gravity measurements, and forecasting. Already in 1973, the first large workstations began processing field data, as a result of which the volumes of hydrocarbon production, albeit insignificantly (by 1 %), nevertheless increased [13].
By the early 1990s, computer-assisted 3D seismic models made it possible to reduce the cost of finding new deposits by an average of 40 %. This led to the fact that over a short period the average increase value in the volume of proved reserves increased 2.5 times. Optimization of hydraulic parameters of the drilling process first carried out with the help of a computer in 1986, made it possible to increase the drilling speed by 1.5 times in the latest decade of the last century. The use of personal computers and mobile devices helped to optimize the process of conducting field operations, and also greatly facilitated the process of performing obtained data in the field of prospecting, exploration and production, processing and marketing of hydrocarbons. Supermajors Shell and ExxonMobil were among the first to implement digital project development control technology using mobile devices. This ensured round-the-clock control over the project implementation and significantly increased the speed of decision-making. It is worth noting that in 2004 Shell, which launched the Smart Fields program, made significant progress in the smart well technology. The gradual increase in the scope of application of digital technologies in the oil and gas industry has acquired a comprehensive, complex and purposeful nature, which subsequently expanded the boundaries and possibilities of their use.
Introduction of innovative technologies helps to increase oil recovery while simultaneously reducing costs and unplanned downtime. According to a study by CERA (Cambridge Energy Research Associates), oil recovery in smart fields operating in the pilot phase is 2-10 % higher than in conventional ones. Taking into account the depletion of traditional reserves and an increase in the share of hard-to-recover oil deposits, subsoil users are trying to increase the number of “smart” fields, first of all, to optimize costs and reduce geological risks [13, 25]. According to experts, the integrated use of IT technologies allows oilmen to increase the oil recovery factor by 2-7 % and, at the same time, reduce operating costs by 25 % [13].
Industry 4.0 technologies used by domestic oilfield service companies. Digital Big Data technologies help to make informed decisions at all stages of field development, allow timely processing of significant amounts of information and provide data, on the basis of which a clear interaction between production and service companies is built [8]. Once the importance of the development of a particular field has been proven and a decision has been made to start its development, the probability of subsequent erroneous decisions remains extremely high. Having formed a nonoptimal field development scheme, a subsoil user will receive significant costs that will reduce the company's profit. The volume of incoming information at this stage of field development is so significant that it is very difficult to evaluate all possible technological development options. Often it takes about two years to design a field development process flow, and the result is only a few proposed field-development options. However, there is no guarantee that the options presented are the best and most optimal.
In the case of implementation of cognitive engineering functions at the enterprise, machine intelligence sorts out a huge number of different combinations of well models, layouts of well clusters, systems for gathering, processing and transporting hydrocarbons, evaluates them for compatibility, and calculates economic efficiency. As a result, the number of intermediate development options increases to a thousand, while the time costs are reduced to six months. By including various constraints in the assessment process (access to financial resources, high technologies, reduction of project time limits), it is possible to obtain the most optimal field development scheme under current conditions.
The most capital-intensive part of oilfield services is exploration and development drilling, as well as subsequent maintenance and support of existing well stock. These areas are critical in the digital transformation process. For example, drilling is a mechanized process that allows to create a mine working in the earth's surface. However, the process itself is accompanied by certain studies that are a direct result of digitalization [8]. The use of digital technologies by oilfield service companies at the stage of well drilling makes possible:
• Physical modeling of stimulation processes and development of stimulation design
• Application of cableless technologies, 4D, HD seismic survey
• Creation of a system for monitoring parameters through interpretation (in-depth data processing) and the use of permanent in-depth monitoring systems
• Remote control of a modern hydraulic fracturing fleet due to an automated control system
• Research of cuttings and gas of drilling mud in mobile laboratories.
If we compare the range of services offered on the world market by Schlumberger, Halliburton, Baker Hughes, and GE Company and Weatherford with the services of leading domestic oilfield service companies, it becomes obvious that foreign companies provide the entire range of services in the oil market (Table 1). However, Russian companies cannot offer the customer a full range of services. For example, Eurasia Drilling (EDC) is focused only on well drilling, while domestic TGT Oil and Gas Services is focused on providing geophysical services. AKROS specializes primarily in service support in drilling and production, RIMERA offers comprehensive solutions for manufacturing equipment for oil production and provision of services. Siberian Service Company (SSK) provides services in the field of drilling. The specificity of Russian companies is that they use traditional well servicing technologies.
Table 1
Comparison of the service line of foreign and domestic companies (based on data from official websites of companies)
Maintenance services, equipment manufacturing | Foreign oil service companies | Russian oil service companies | ||||||||
Schlumberger | Halliburton | Baker Hughesa GE Company | Weatherford | ERIELL | Eurasia Drilling (EDC) | TGT Oil and Gas Services | AKROS | RIMERA | SSK | |
Geophysical well logging | + | + | + | + | + | |||||
Well testing | + | + | + | + | ||||||
Oil and gas wells drilling | + | + | + | + | + | + | + | + | ||
Well finishing | + | + | + | + | + | + | ||||
Well cementing | + | + | + | + | + | |||||
Production intensification | + | + | + | + | + | + | ||||
Mechanized extraction | + | + | + | + | + | |||||
Production management | + | + | + | + | ||||||
Complex (integrated solutions) | + | + | + | + | + | + | ||||
Integrated software solutions | + | + | + | + | ||||||
Wells conservation | + | + | + | + | + | |||||
Consulting services | + | + | + | + | ||||||
Equipment for geology and geophysics | + | + | + | + | ||||||
Well construction equipment | + | + | + | + | ||||||
Mining equipment | + | + | + | + | + |
Industry experts note that a number of Russian oilfield service companies have individual products and services that are in high demand on the market and can be presented at competitive prices. However, often this is known only to producers of these services, while market participants do not know about it.
As a positive example, we will cite the oilfield services company TGT Oil and Gas Services, which has achieved recognition in the global market for providing well survey services using noise and temperature logging. Despite its narrow profile, the company competes in this market segment with the world's leading companies and actively exports Russian technologies [1].
The advantages of owing and using digitalization products are, to a greater extent, shared by service departments of oil companies. The most striking example is the oil services divisions of PJSC NK Rosneft. As part of the Digital Rosneft strategy, this vertically integrated oil company has digitized its main business segments. A corporate data processing center GeoPAK (jointly with General Electric) with an industrial Internet platform GE Predix, digital integrated twin of the IRMA fields and digital space for processing geological and physical data, was put into operation; tests of the use of artificial intelligence in field development and planning of geological and technical measures, the use of machine learning technology to optimize operation of a mining asset in real time, as well as a unique technology for autonomous monitoring of production facilities using drones and machine vision were carried out. The company tested computer vision technology to monitor HSE compliance while drilling and put into commercial operation a corporate hydraulic fracturing simulation module (RN-GRID). The domestic vertically integrated oil company together with BP and WesternGeco is developing a seismic data recording system that has no analogues in the world [2].
Digitalization of the domestic upstream segment: first results. Currently, according to the results of the KPMG study, digital technologies in the oil and gas sector are used in Russia only by half of the companies (see the figure).
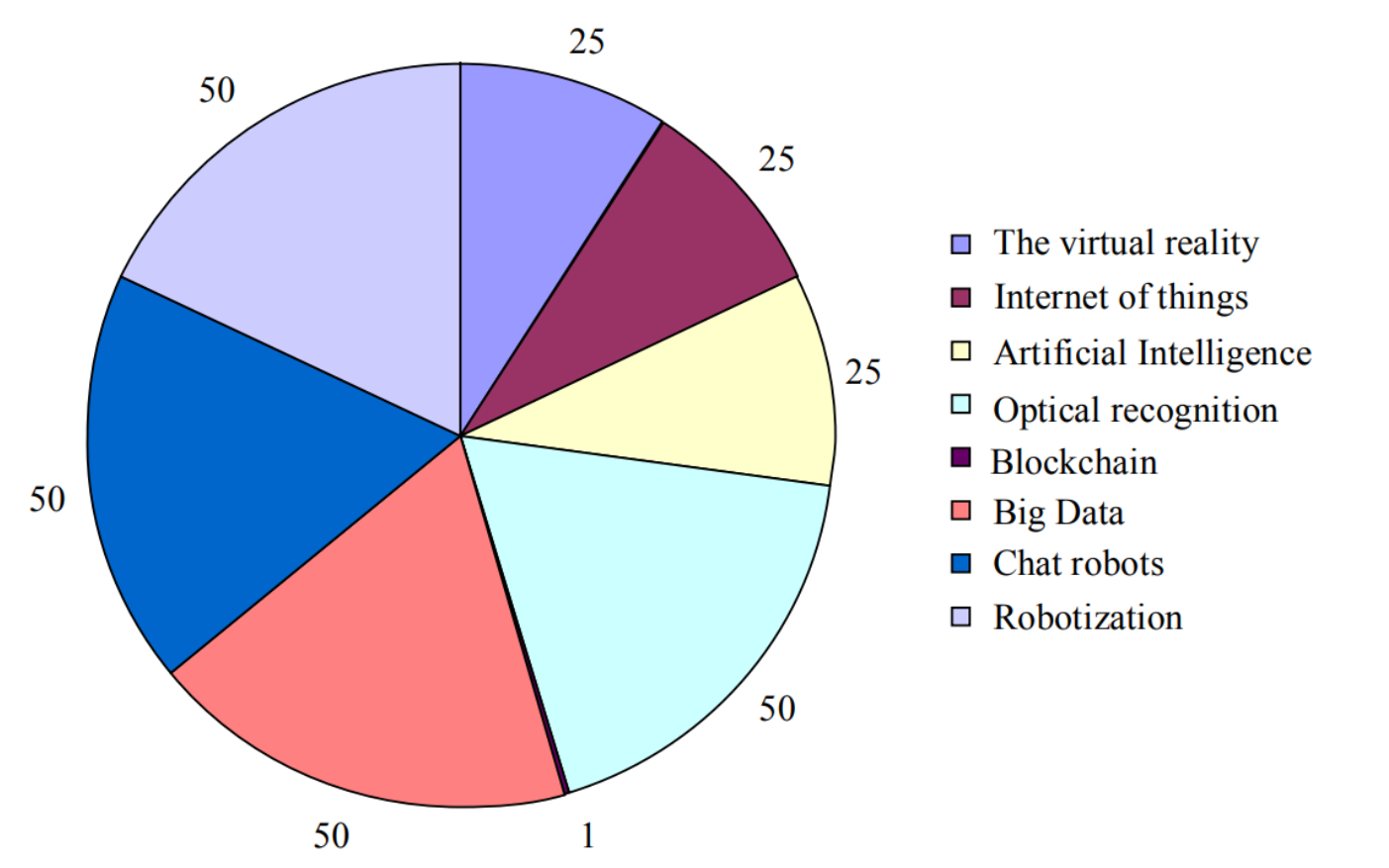
According to the authors, this happens due to insufficient financing of innovative developments within the framework of formation of a new world scientific and technological order, cyber threats to oil and gas assets, as well as sectoral sanctions of foreign countries for the acquisition of advanced technologies [10, 16, 19]. (It should be noted that it was in the fifth technological order that conditions for digitalization of the economy were formed; however, today 30 % of the technologies used in Russia belong to the third technological order, 50 % – to the fourth order, and only about 10 % falls on the technologies of the fifth order).
There is a clear understanding in the oil and gas industry that Industrial Internet of Things technologies are essential to competitiveness, and implementation of concepts such as the Connected Plant and Smart Field have a direct impact on profitability of an enterprise. While implementing digital transformation, we must not forget about the numerous risks that accompany this process. The more “connected” an enterprise becomes, the more acute is the issue of ensuring its security [10]. Within the framework of the St. Petersburg International Economic Forum, participants of the panel discussion “Digital Subsoil Use” expressed the opinion that digital technologies create serious problems with protection of information. Information protection will require investments that are an order of magnitude higher than actual costs of digitalization. Today, the data of domestic subsoil users and service companies are practically not protected; therefore, industry market participants are quite sparingly implementing digital technologies [7]. At the same time, it was noted that without transition to digitalization, Russian companies cannot remain competitive in the global energy market. Therefore, it is necessary to introduce technologies not according to the principle of “digitalization for the sake of digitalization”, but for specific purposes.
We must not overlook the fact that digitalization process can lead to a significant reduction in workplaces as a result of robotization and active use of intelligent artificial intelligence. An analysis of industrial robots introduction into workplaces in the United States in the period from 1993 to 2007 [17] showed that each new robot replaces five or six workers, and each additional robot per 1000 workers reduces the share of total employed population by 0.34 % and reduces wages by 0.5 %. At the same time, there is a reduction in the number of workplaces, which is not accompanied by creation of new ones. The study predicts that the number of industrial robots in the United States will double by 2025, with seven robots per 1,000 workers (Toledo and Detroit already have nine robots per 1,000 workers). Analyzing the dynamics of exploitation of drilling rigs in the United States and the number of workers employed in the oil industry during the current crisis [18], it should be noted that after relative stabilization of oil prices by the beginning of 2016, the number of drilling rigs began to increase again, but the number of workers employed in the industry has remained at about the same level. In other words, the mothballed oil rigs resumed their work, but the previously laid off employees did not return to their previous workplaces. Given that this industry in the Russian Federation is predominantly represented by large corporations and companies (due to the underdevelopment of small and medium-sized entrepreneurship sector), it is highly likely that the digitalization process will create a tense social situation in oil and gas producing regions of the country. As a rule, most of the settlements in the Urals, Northwestern and other federal districts, the population of which is employed in production, transport and processing of hydrocarbons, are single-industry towns. And only the low (by world standards) level of wages, thanks to which the labor of workers costs corporations cheaper than purchasing robots, postpones the digitalization process.
Russian oil and gas companies, like foreign ones, are actively investing in technologies that increase the efficiency of oil production, refining and distribution and help to increase sales profitability. However, digitalization of processes alone is unlikely to drastically affect the efficiency. Oil and gas companies are faced with urgent task of improving the efficiency of management and personnel training. Augmented and virtual reality technologies, as well as systemic digitalization of deposits, can solve most of the problems [3]. For example, augmented reality technologies allow field employees to interact with experts remotely, to consult on troubleshooting methods. In addition, they help to solve the problem of training young specialists. The predictive analytics system, which consists in installing sensors and automating the monitoring of effectiveness of repair teams, will lead to a reduction in the number of repairs, a decrease in equipment downtime, and personnel optimization. Digitalization of the field will provide an opportunity to remotely study the field at all stages of its development, which will significantly reduce the costs of a mining company, including by obtaining more accurate data. Using the Internet of Things and mobile applications will allow to remotely control the modes of equipment at gas stations and receive sales analytics for corporate and retail customers in a wide variety of forms.
УSmart wells and digital fields are products of digitalization of the oil and gas industry. It is in the upstream sector where the most significant results have been achieved, and it is this sector that in the future will play a leading role in organizing systematic work with large data sets [13].
Nowadays there are more than 40 such fields in Russia with the production of about 140 million tons of oil. Intelligent technologies appeared in Russia only in 2000 with the arrival of Shell and BP and were first tested at the Salym group of fields. The leaders in terms of the share of intelligent solutions in production and reserves are the largest PJSC NC Gazprom Neft and PJSC NC Rosneft. For example, in 2017, a production control center (MCC) appeared at Gazprom Neft-Khantos, which makes it possible to comprehensively manage the efficiency of production activities of a subsidiary. One of the key systems of the MCC is a self-learning digital twin, which provides automated selection of the most optimal operating modes for the elements of entire complex and allows to identify emergency situations in advance and propose preventive solutions [4]. PJSC NC LUKOIL, PJSC Tatneft, PJSC NC Surgutneftegaz, and AC Transneft also achieved good results. Recently, the use of software in oil and gas transportation has made it possible to achieve a high level of safety. The introduction of information technology in these areas allows for accurate and operational modeling of the pipeline and development of measures aimed at optimizing the operation of entire pipeline system, taking into account the data obtained during the analysis [15].
PJSC NC LUKOIL has adopted a digital development strategy until 2030 in such areas as digital twins, ecosystem, personnel and robotization. Big Data, the industrial Internet of things, interaction technologies, robots and drones, artificial intelligence, mobile devices, as well as cloud technologies are designated as digitalization tools. Digitalization of production processes has already brought the company an additional million tons of hydrocarbons. The first successful result of PJSC NC LUKOIL was obtained at the Kokuyskoye field in the Perm Region. According to forecasts of the company's management, by 2030 the cost of oil production is expected to decrease by 20-30 % with a simultaneous increase in labor productivity. PJSC TATNEFT through the introduction of digital technologies managed to reduce the cost of production at the Romashkinskoye field by 30 %. PJSC TATNEFT jointly with ChemTech is implementing a project to create a digital twin of the ELOU-AVT-7 primary oil fractionation unit at the Taneko Oil Refinery Complex. As a result of the project, oil refining depth has reached 98.2 %, which is significantly higher than the average for Russia (81.5 %). The data for several years of operation of the installation were processed, a thermodynamic model of the existing production was created, virtual analyzers that predict the composition of technological streams were developed, and possibilities for optimizing the technological regime were determined. Large data processing was carried out on the Azure platform in partnership with Microsoft. Using a ready-made platform allows to scale the project and connect new services, for example, PowerBI analytics tools [4].
In the practice of companies in domestic oil and gas industry, it is possible and necessary to use domestic software from seismic data processing to hydrodynamic studies, including methods of parametric and structural identification, which are based on the use of IT technologies, management of subsoil exploration processes, assessment of oil and gas reserves, and development and operation of hydrocarbon deposits (Table 2).
Developers of Russian software say that it is impossible to take part in tenders for the supply of software in the field of exploration and development of deposits since the largest companies-subsoil users initially prefer foreign developments. According to Vygon Consulting, the share of purchases of foreign software by state-owned companies is 99 %.
According to the assessment of State Expertise Center experts, the cost of foreign software using the Petrel software system, as an example, is about $ 100 million annually. Reducing the cost of acquiring foreign developments can increase profitability and capitalization of domestic companies in the market and thereby help to increase their scientific and technical potential. In addition to oil and gas corporations, engineering and oil service companies could become users of the programs of domestic developers. However, they are forced to abandon Russian developments, since they are subject to the terms of tender documentation obliging them to work on specific programs of foreign manufacturers [15].
Industry experts are confident that domestic technologies can solve up to 80 % of individual problems of processing, interpretation of seismic data and hydrodynamic modeling. The problem is that they are disparate developments, each of which is protected by copyright and represents economic interests of specific intellectual property owners. To solve this problem, it is necessary to integrate the existing software on a single platform, develop additional programs and their logical placement within a single line covering the basic complex of tasks of the exploration sector. Thus, stimulation of the development of oilfield services in Russia should be carried out “on the basis of formation of technological partnerships consisting of production, service companies and science-intensive organizations (research institutes, universities, development bureaus), as well as representatives of government institutions (to establish the necessary interaction and coordination) with the aim of joint development of domestic technologies in the field of oil and gas production” [9].
Table 2
Russian technologies in the field of software*
Oilfield services segment | Technology | Development company | Purpose |
Geology | Prime for 2D/3D/4D/3C/4C seismic interpretation | Yandex Terra | Data processing, 2D/3D/4D/3C/4C seismic interpretation and geological modeling |
Russian software platform Geoplat – Pro | Gpd Gridpoint Dynamics | Interpretation of seismic data, 3D geological modeling and reserves estimation | |
Development of oil fields | Hardware and software complex based on the Elbrus platform created by MCST (Moscow SPARC Technology Center), the Russian CONCORD system, a platform for building corporate information systems IDS X360 | RedSys | Management of development in oil fields, modeling of processes in wells |
Project “Development of an open geological and geophysical software platform based on the principles of free software” | AO Central Geophysical Expedition | ||
Drilling of wells | MarCS Engineer software for complex well drilling projects | Nedra-test Research Center , Gubkin Russian State University of Oil and Gas, OOO PetroEngineering | Analysis of drilling mud parameters, allowing to minimize contamination of oil reservoir during drilling and reduce the risk of accidents |
*Compiled by the authors based on [15].
Conclusion. The analysis and systematization of the results allow to draw the following conclusions..
The experience of technological development of the global oil and gas industry has had a significant impact on digitalization of the industry, forming high-tech companies, primarily in the upstream and oilfield services sectors. Existing developments in the field of “Industry 4.0” allow foreign companies to move to a new stage of technological development, and demonstrate their competitive advantages in the world market.
The process of digital transformation of domestic economy and, in particular, the upstream and oilfield services sectors due to the existing technological mode is at the initial stage of formation. Digitalization of the Russian economy appears to be a long-term trend and its impact on the industry will manifest itself only after 2025.
The lack of a clear strategy for technological development of the industry, insufficient incentives for vertically integrated oil companies to invest in R&D, and weak competitiveness of domestic oil and gas services companies are risk factors for the full functioning of the industry in the face of potential new sanctions from developed countries.
The activities of independent domestic oilfield services companies are carried out in a narrow range of services. The limited scope of operation is associated with insufficient investment in business development and expansion, the lack of interest on the part of the state and corporate sector in creating domestic technologies and a full-fledged oilfield services market in Russia.
Along with undoubted advantages and possibilities of oil and gas business digitalization, there are serious financial, informational and social risks. In particular, the threat of information leakage regarding hydrocarbon reserves and resources may lead to the loss of positions in the country's energy security. Future technological changes will affect the structure of workplaces and the level of employment in the industry. Based on these findings, a number of recommendations can be developed for both government agencies and Russian businesses, including oil and gas and oilfield service companies.
The use of digital technologies is based on the use of innovative technologies, which necessitates an increase in funding for R&D with subsequent implementation and commercialization of the results. While implementing the industry digitalization strategy, it should be borne in mind that no matter how large modern vertically integrated oil companies are, the task of definition, selection of forms and tools of interaction for a radical technological renewal of the industry should be carried out at the federal level. Therefore, to stimulate the development of digital technologies in the domestic oilfield services, it is necessary to create technological partnerships, which will include production, service and scienceintensive companies, under direct coordination of government agencies. At the same time, each project designed to implement the digital program of an enterprise should from the very beginning outline the issues of choice of forces and means of information protection, the amount of necessary investments into employee training. Only in this case it will be possible to form priority areas of development, attract the necessary funding, and incentivize developers and subsoil users to create, implement, and replicate high-tech intellectual property objects.
1Passport of the innovative development program of PJSC Gazprom Neft until 2025. St. Petersburg: PJSC Gazprom Neft, 2018; Passport of the innovative development program of Zarubezhneft JSC for the period of 2016-2020. (with a prospect until 2030). Moscow: JSC Zarubezhneft, 2018; PJSC Rosneft Innovative Development Program. Moscow: PJSC NK Rosneft, 2016.
2What is Big Data – big data. URL (date of access 12.12.2019)
3What is the Industrial Internet. URL (date of access 12.12.2019)
4El Saddik A. Digital twins: the convergence of multimedia technologies // IEEE MultiMedia. 2018. Vol. 25. N 2. P. 87-92.
5“Intelligent materials”. URL (date of access 12.12.2019)
6Blockchain. URL (date of access 12.12.2019)