Research and development of technology for the construction of snow airfields for accommodating wheeled aircraft in Antarctica
- 1 — Chief Expert Arctic and Antarctic Research Institute ▪ Elibrary
- 2 — Ph.D., Dr.Sci. Leading Engineer VNIIOkeangeologia ▪ Orcid
Abstract
Construction of a new wintering complex at the Antarctic Vostok Station required prompt delivery of builders and mechanics to Progress Station to move them further to the work area. To solve this major logistical issue, a new landing site, later named Zenit, certified for accommodating heavy wheeled aircraft, was prepared in the Progress Station area from March to August 2022. Its snow pavement slab with a total area of 350 thousand m2 is from 100 to 120 cm high. It was made by applying snow layers with their subsequent compaction by a specially designed compaction platform for snow airfields suitable for heavy wheeled aircraft. As a result, the pavement has a surface hardness of at least 1 MPa. The layer from 30 to 60 cm has a hardness of at least 0.8 MPa, and the bottom layer at least 0.6 MPa. The first Il-76TD-90VD aircraft of the Russian company Volga-Dnepr was accommodated to the new runway on 7 November 2022. The aircraft landed in normal mode. The depth of the chassis wheels track after landing did not exceed 3 cm. The research provided in-depth understanding of the mechanisms for forming the supporting base of the runway from snow and ice in Antarctica. The experience gained can be used to solve similar issues in the Far North.
Introduction
The main reason for creating an airfield in the Russian Progress Station area in East Antarctica is the entry into the main construction phase of the new wintering complex Vostok, which was put into operation in Central Antarctica at the Russian Vostok Station in early 2024 [1]. The importance and relevance of upgrading the Station are related to the study of the subglacial Lake Vostok, to the implementation of Event 21 “Comprehensive studies of the subglacial Lake Vostok and the Earth’s paleoclimate in the area of the Russian Antarctic Station Vostok”, within the framework of the Strategy for the Development of Activities of the Russian Federation in the Antarctica until 2030 approved by the Order of the Government of the Russian Federation dated 21 August 2020 N 2143-r. Construction of the wintering complex will both improve the living conditions of polar explorers [2] and allow studying the aquatic environment of the lake and its bottom sediments [3-5].
During the first stage of construction, ships supplied the Progress Station area with blocks for the Vostok wintering complex, equipment for delivery, and the necessary fuel. The main task for the next stage was the timely transportation of builders and mechanics to the Progress Station area to move them further to the Vostok Station in order to use each day of the short Antarctic summer as efficiently as possible, when weather conditions in the central part of the continent are favourable for work. At this stage, the Vostok wintering complex blocks were delivered from the storage site to the construction site by tractors on sleds, after which the builders began assembling the structures. It should be noted that at the beginning of spring, fast ice off the coast of Antarctica has the greatest thickness, which complicates the use of ships to deliver people and cargo. Therefore, a decision was made to deliver cargo and personnel to the Progress Station by heavy aircraft of the Il-76 type, capable of a non-stop flight from the African continent to Antarctica. To implement the plan, it was necessary to prepare a landing site at Progress Station that would be capable of accommodating wheeled aircraft. The technically complex task was completed, and the landing site was named Zenit. This work is aimed at describing the stages of preparation and construction of this unique facility of the Russian logistics infrastructure.
We should refer to the aviation terminology set out in Article 40 of the current (2022) edition of the Air Code of the Russian Federation, as well as to the Federal Aviation Rules “Requirements for airfields intended for take-off, landing, taxiing, and parking of civil aircraft”, approved by order of the Ministry of Transport of Russia dated 25 August 2015 N 262:
- runway – a specific rectangular section of a land airfield prepared for landing and take-off of aircraft;
- landing site – a section of land, ice, surface of a structure, including the surface of a floating structure, or a water area intended for take-off, landing or for take-off, landing, taxiing, and parking of aircraft;
- airfield – a section of land or water area with buildings, structures, and equipment located on it, intended for take-off, landing, taxiing, and parking of aircraft;
- apron – a specific area of a land airfield intended for the placement of aircraft for the purpose of boarding or disembarking passengers, loading or unloading mail or cargo, refuelling, parking, or technical maintenance of the runway.
It is important to address two more terms – strength and hardness. Strength is the ultimate load at which the medium is destroyed due to exceeding the plasticity limit, i.e. upon reaching the ultimate stress. In this paper, hardness is understood as the ability of the medium to resist penetration by another body until residual deformations occur. Hardness was determined using the method developed in [6], by pressing a stamp into the medium under study. The specified values are expressed in pascals.
As a rule, airfields or landing sites near Stations in Antarctica are built on a glacier or sea ice [7-9]. The situation in the Progress Station area, located in the Larsemann Hills oasis, is no exception. The surface topography of the Station is absolutely unsuitable for an unpaved airfield. The main issue of building a landing site on a glacier in this area is the absence of blue ice zones (areas with no permanent snow cover on the glacier) in reasonable proximity. This significantly complicates the task solution. The site for building the landing site was chosen 6 km from the Progress Station on a glacier. The snow cover height varied from 3 to 10 m, and the surface topography made it possible to choose a site suitable for building a runway at least 3000 m long, required for landing and take-off of Il-76 type aircraft (Fig.1).
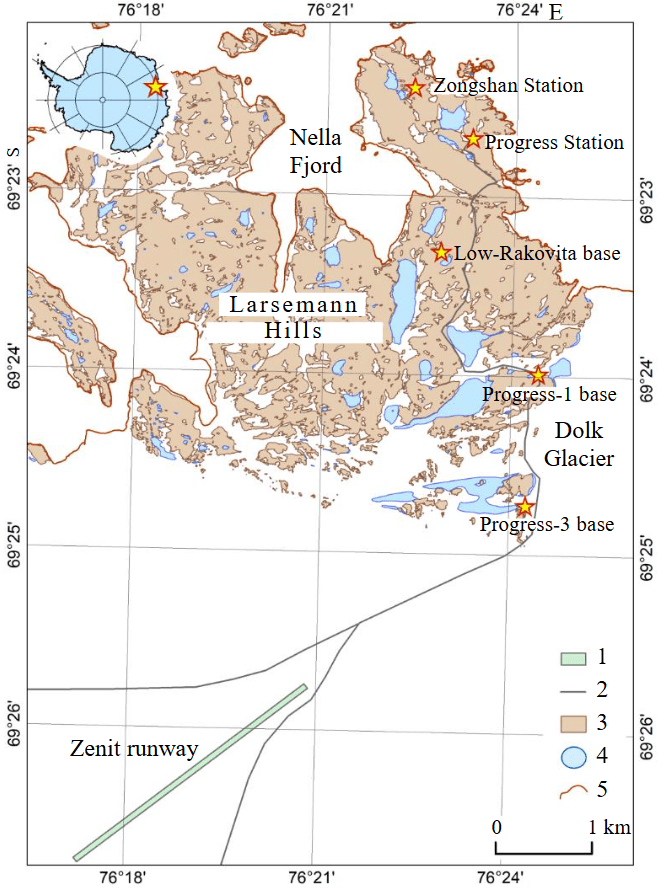
Fig.1. Position of the Zenit landing site
1 – Zenit runway; 2 – sled-caterpillar tracks; 3 – rock outcrops; 4 – water bodies; 5 – coastline (3-5 – according to Antarctic Digital Database (ADD). Cambridge: British Antarctic Survey, 2023. Ver.7.8. URL: www.bas.ac.uk/project/add (accessed 07.10.2024)
The selected area is well studied, as for many years it was the landing site of first the Soviet and then the Russian Antarctic expedition, which accommodated small aircraft on ski chassis. Since the mid-80s of the last century, it has been used to carry out domestic comprehensive geological and geophysical studies [10-12], as well as to deliver cargo and personnel to the Vostok Station by Douglas (Basler) BT-67 and Turbo-67 (DC-3) aircraft. The average annual snow accumulation in this area is about 30 cm, and the average annual speed of glacier movement does not exceed 2 m/year [13]. According to the international classification [14], the glacier section can be classified as an infiltration zone. Previously, episodic crevasses were observed here [15], but, as a rule, no more than half a metre wide, which made it possible to quickly fill them and thus restore the snow-and-ice layer integrity.
In the second half of the last century, with the participation of AARI employees, a metho-dology for constructing a landing site in deep snow to accommodate heavy wheeled aircraft was developed (Instructions for the design, construction, and assessment of the operational suitability of snow and snow-and-ice airfields in Antarctica VSN37-76. Leningrad, 1976) [16]. In particular, it was successfully used to organize a runway at Molodezhnaya Station for many years. The methodology assumed the runway construction for at least two years with at least one mandatory summer season. At this time, the snow surface temperature approaches the phase transition temperature, which significantly facilitates snow compaction. In the case under consideration, the task was to build an airfield in six months, and in the winter period, since the decision to organize it was made at the end of February 2022, and flights to Progress Station were required to begin no later than the early November of the same year.
Methods
The simplest and most effective method of constructing a runway for wheeled aircraft in deep snow is the layer-by-layer snow compaction to the required strength [16, 17]. The newly developed method was based on a comprehensive research conducted at the Vostok Station during the summer field seasons of 2006-2008 [18]. During these works, plate load tests of the snow cover were made to determine the possibility of compacting cold snow to a hardness of 1 MPa or more, which is necessary to withstand the load from the wheels of heavy aircraft. The research resulted in a dependence between the density of the resulting snow and the impact of a stamp with different pressures on the cover for different initial snow properties at a temperature of about –30 °C. It is shown in Fig.2.
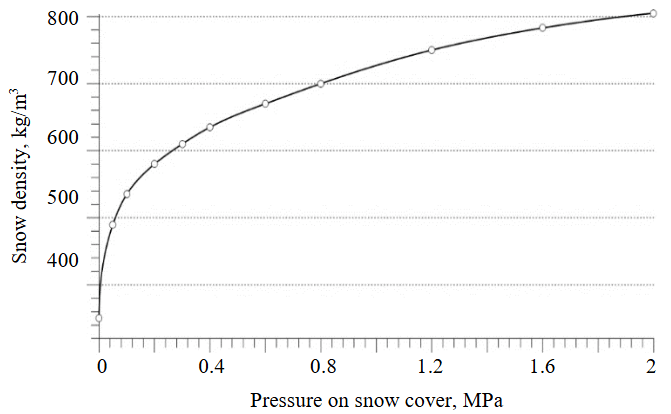
Fig.2. Dependence of the resulting snow density on the stamp pressure at a snow temperature of about –30 °С
When the snow material density reaches 550 kg/m3, its uniaxial compression strength measured at a temperature of –10 °C can reach 0.85 MPa, and at a density above 600 kg/m3 it can exceed 1 MPa. Moreover, the experiments on snow compaction at the Vostok Station revealed a fundamentally important dependence of the change in strength over time. Immediately after compaction, the snow strength can even decrease compared to the initial one [1, 18]. This is due to the rupture of the bonds between the granules and crystals of snow. However, later, under the influence of diffusion sintering of crystals and granules of snow, its strength increases and after several days it reaches a new value exceeding the initial one.
Plate load tests in the Vostok Station area were performed both on natural snow cover and on a snow airfield for aircraft on ski chassis measuring 4000×100 m, where it was possible to select sites with different initial snow properties. A metal plate was used as a stamp, against which a hydraulic jack with a force metre on the rod rested. A heavy vehicle (a tractor unit weighing about 40 t) was used as the upper support for the jack. Then sites with different snow properties (density and hardness) were selected. When the jack impacted the plate, the impact force and the dimension of snow deformation below the plate were recorded. The duration of the impact was about 20 s. Then, after a certain fixed time, a core was taken at the impact site, and the density and strength of the resulting snow compaction were measured in the glaciological laboratory. The hardness of the resulting pavement was also recorded directly at the impact site using a penetrometer.
The load test, the results of which are shown in Fig.2, was conducted at a snow temperature of –30 °C. Strength and density measurements of the compacted snow were conducted on taken cores in the Vostok Station laboratory, where the air temperature, and therefore that of the samples was –10 °C. Hardness was measured with a penetrometer at the load test point, i.e. at an ambient air temperature of –30 °C. Snow density is practically independent of the sample temperature, so the conclusions presented are quite fair.
Moreover, before landing the aircraft, a layer of ice chips up to 4 cm thick was created on the surface of the runway and apron using the Kӓssbohrer PristenBully Polar 300 (РВ-300) milling cutters. This increases the coefficient of wheels adhesion to the surface up to 50 %.
The main device used for compacting the snow layers at the landing site was the compacting platform. It was designed and manufactured specifically for creating landing sites suitable for accommodating heavy wheeled aircraft on deep snow in Antarctica [19]. Fig.3, a shows a fragment of the snow layer compaction using this device.

Fig.3. Fragment of the snow layer compaction using a compaction platform (a) and a crane truck utilized as a test trolley for checking the airfield pavement strength (b)
Snow layers were applied to the runway slab using the blades of the PB-300 transporters. After the layer was applied, the initial density of the snow, equal to 350 kg/m3, increased to approximately 420 kg/m3 as a result of mixing. Application was the most labour-intensive process in the landing site construction. In particular, five PB-300 transporters working 8 h a day applied one snow layer about 30 cm thick to the entire area of the runway for about two weeks. The layers were compacted simultaneously with the applications of other ones.
The most important aspect of landing site preparation is quality control of the created pavement. Strength properties of the created pavement were measured using a penetrometer with a destruction energy of 8.5 J. Detailed specifications of the device are presented in the Instructions for the design... (1976) and in [20]. At the final stage of pavement formation, a test trolley with a wheel load and properties similar to those of aircraft chassis wheels was used (Fig.3, b). The weight of the vehicle with additional ballast increased to 60 t, and the pressure in the wheels to 0.8 MPa. If necessary, the vehicle can be used as an additional self-moving compaction device with a surface pressure of up to 0.8 MPa.
Results
The tests revealed the dependence of the depth of impact on the snow cover on the applied stamp pressure for various initial snow properties. The impact depth is understood to be the depth of the cover layer at which the physical and mechanical properties of the snow changed after the applied mechanical impact. The obtained dependence is an important practical result. Based on the technical capabilities of the compaction device, it enabled to select the maximum height of the applied snow layer to be compacted. A mandatory condition was the compaction of the entire depth of the applied layer, i.e. the layer height should not exceed the impact depth. Plate load tests were also used to assess stress dispersion under the aircraft wheel with depth. For this purpose, a stamp was selected whose dimensions were close to the wheel contact patch area with the surface. This stamp impacted the pre-compacted snow cover with known mechanical properties with different pressures. The depth of impact on the studied snow cover was measured. Fig.4 shows the dependence of the impact depth on the applied pressure for some snow cover properties. The vertical dotted line shows the nominal pressure (P = 0.35 MPa) on the compacted surface of one of the main compacting devices used in the landing site construction.

Fig.4. Depth of impact on snow cover depending on stamp pressure for initial properties of snow cover (ρ – snow density, kg/m3, HB – snow hardness, MPa)
1 – ρ = 420, HB = 0.045; 2 – ρ = 500, HB = 0.2; 3 – ρ = 580, HB = 0.45
A curve of mechanical stress dispersion with depth was obtained for different snow cover properties. As an example, Fig.5 shows a curve for a snow cover with a density of 550 kg/m3 with a stamp size close to the size of the contact patch of the Il-76TD aircraft chassis wheel. The values presented are consistent with similar data (Instructions for the design…, 1976).

Fig.5. Relief of mechanical stress with depth under the aircraft wheel for snow cover with a density of 550 kg/m³
The hardness of the created upper layer of snow cover 30 cm deep was from 1 to 1.5 MPa. Accordingly, for the layer from 30 to 60 cm, not less than 0.8 MPa, and for the lower one from 60 to 100 cm, not less than 0.6 MPa. The uniaxial compression strength of the snow cover was measured on a mechanical press in the core samples taken from the created pavement. It showed similar hardness results. The discrepancy in the values between hardness and strength did not exceed 10 % and was within the measurement error. The snow slab density was determined in a standard way by weighing snow samples of a known size. The average density of the created pavement was about 620 kg/m3. The hardness and compressive strength of the natural snow cover, on which the snow slab of the pavement rests, were also controlled. The minimum hardness of natural snow was not less than 0.15 MPa.
Considering the known dispersion of vertical stress under the aircraft chassis wheels in the snow slab of the runway pavement, shown in Fig.5, and also the fact that the slab rests on a solid base of natural snow cover with hardness not less than 0.15 MPa, the snow slab height was estimated, sufficient to withstand the load from the aircraft chassis wheel with a surface pressure of up to 1 MPa. The estimate is based on the fact that if the dissipated pressure from the aircraft chassis wheel on the lower edge of the snow slab does not exceed the compressive strength of the material on which this slab rests, then no bending deformations will occur in it, and it is guaranteed not to break due to bending. As follows from Fig.5, at a depth of 1 m, the vertical stress in the pavement slab decreases from 1 MPa to approximately 0.08 MPa, i.e. more than by order of magnitude. Thus, a slab height of one metre is sufficient.
In order to prevent the wheel from penetrating into the snow slab, it is sufficient for the pavement surface hardness to be higher than the pressure exerted by the wheel. The hardness of the upper layer of the slab must be at least 0.8 MPa (the pressure in the IL-76 chassis wheels is 0.7 MPa). A similar result was obtained earlier, when the Progress Station runway was developed. Thus, the minimum permissible uniaxial compression strength of the snow runway pavement for the episodic operation of the IL-76 aircraft for the upper layer 30 cm deep must be at least 0.9 MPa, for the layer at a depth of 30 to 60 cm at least 0.75 MPa, and for the lower base layer at a depth of 60 to 100 cm at least 0.4 MPa. The entire snow pavement slab must rest on a natural snow cover with a compressive strength of at least 0.15 MPa.
In addition to having the necessary strength and height of the airfield pavement to withstand the load from the aircraft chassis wheel, the snow slab must withstand the load from the weight of the entire aircraft. The slab’s limit load was computed as an estimate of the maximum permissible aircraft weight for a given geometry of the chassis wheel distribution. In the case of the Il-76, the main weight is concentrated on the two rear groups of chassis wheels, each having 8 wheels. The total contact patch of the chassis wheels is 8×3.2 m. The essence of the estimate is that if the pressure from the aircraft chassis, which is transmitted through the pavement slab to the natural snow cover, does not exceed its compressive strength, then, as a consequence, there will be no pavement slab deformation due to bending, and it is guaranteed not to break.
A noticeable reduction in stress from the aircraft chassis will occur at a depth comparable to the characteristic size of its contact patch with the surface, i.e. at a depth of over 4 m. In the estimations given, it is assumed that there is no stress dispersion inside the pavement slab, and the pressure from the aircraft chassis is completely transferred to the natural snow cover on which the slab rests. Thus, the pressure from the chassis should not exceed the compressive strength of the natural snow cover. The maximum permissible mass of the aircraft in this case is:
where σ is the minimum compressive strength of the natural snow cover on which the pavement slab rests, σ = 0.15 MPa; S is the area of the aircraft chassis support patch, S = 25 m2; g is the acceleration of gravity, m/s2.
Substituting the corresponding values into relation (1), we obtain the estimated value M = 375 t. The pavement can safely support an aircraft with a chassis geometry similar to the Il-76, weighing up to 375 t. Considering that its actual weight is 150 t, there is more than twofold safety margin for the limit load of the prepared snow slab pavement.
One of the threats to any engineering structure located on a glacier is the possibility of crevasses forming near the surface on which the structure is built. A landing site is no exception. The main method for checking for crevasses or voids inside a glacier is ground penetrating radar (GPR) control [21-23]. It should be noted that crevasses forming inside a glacier located in the coastal zone of the Antarctic continent are common, since different parts of the glacier move at different speeds, which causes stress. If it exceed critical values, crevasses form [24, 25]. Before accommodating an aircraft, the landing site readiness check, in addition to checking the physical and mechanical properties of the pavement, also includes GPR control for near-surface crevasses. If they are possibly detected during the analysis of GPR time-sections [15, 26, 27], confirmatory drilling is made at the point to determine the actual dimensions of these features. For further operation of the airfield, it is important to assess the extent to which a crevasse or void found inside the glacier threatens aviation operations. GPR surveys at landing sites are conducted from time to time. The interval for such monitoring depends on specific conditions. In particular, similar work was made at the Zenit runway during the season of the 68th Russian Antarctic Expedition (2022/2023) [28]. The inspection discovered small crevasses, which, however, do not interfere with the runway operation.
Crevasses in the glacier body periodically occur due to its uneven movement [29, 30]. Moreover, the number of crevasses in the future will probably increase due to global climate change and an increase in the speed of glacier movement (spreading) with an increase in its temperature [31]. Therefore, it is advisable to estimate the limit load of a pavement snow slab in the presence of a crevasse or void of a given size underneath it. Let there be an infinite plate made of a material with known properties ΩF, which rests on the underlying snow cover ΩS with a crevasse of a known size ΩC (Fig.6). An aircraft wheel with a known load rests on the plate (in this case, on the snow slab). Let us estimate the maximum permissible width of a crevasse in the snow cover on which the snow slab rests so that it does not break under the specified load.

Fig.6. Design diagram of the snow slab limit load at the Zenit runway pavement in the presence of a crevasse or void of a given size below it
ΩF – compacted snow slab; ΩS – snow cover; ΩC – crevasse
For a simplified assessment, we will imagine a snow slab above a crevasse as a beam with fixed ends, resting on the snow cover on which the slab is located. Let F be the force from the chassis wheel acting on the slab, directed downwards; h is the slab height; σc and σb are the slab strength in uniaxial compression and bending; L is the width of the crevasse under the slab; b is the width of the beam associated with the slab. Then, using Zhuravsky’s formula [32, 33] to estimate the ultimate strength of a beam with fixed ends, we obtain
To estimate the minimum limit load of the slab, we will take b = h and use the known ratio σb ≈ 1/3σc. After transformations, we obtain
In this case, the maximum permissible crevasse width below the pavement slab will be
In the case under consideration, h = 1 m; σc = 1 MPa; F = 100 kN (the force with which the Il-76 aircraft wheel rests on the surface). Using relation (2), we obtain an estimate of the maximum permissible crevasse width L ≈ 2 m.
If the crevasse width is less than the slab height, the problem is reduced to estimating the beam shear failure at the crevasse edges [32]. In this case, we also approximate the slab with a beam of height h and width h. The shear area at each edge of the beam will be h². We assume the worst-case scenario, when the load from the aircraft wheel F is applied to one edge of the beam. We estimate the shear on one side:
where σsh is the shear strength of the slab. Then the formula for estimating the minimum beam thickness that will withstand a load of force F is:
Considering the known ratio σsh = 0.6 σc, we obtain:
Let us estimate the minimum height of the slab that will not break in shear under a given load using relation (3). If σc = 1 MPa and F = 100 kN, then h = 0.4 m. Thus, the formed runway slab 1 m high is guaranteed to withstand the shear and bend load from the Il-76 aircraft wheel with a crevasse width below it of no more than 2 m.
It should be noted that the distance between the chassis wheels is 1 m, and if the crevasse below the snow slab is parallel to the runway centre line, then two chassis wheels can simultaneously press on the beam, which we approximate the slab. In accordance with relation (2), the maximum permissible width of the crevasse below the slab will be 1 m. For guaranteed safety, one should focus on the maximum permissible width of the crevasse below the slab of 1 m.
Discussion
When preparing the foundation for the new wintering complex of the Vostok Station [1], the procedures were developed that were later used in the construction of the new Zenit landing site. In this sense, the procedure is unique since, unlike the previously used one, it allows for the creation of a landing site for wheeled aircraft not only in the coastal but also in the interior regions of Antarctica. The former are characterized by relatively warm summers with intensive near-surface melting of the snow layer. It significantly accelerates snow compaction due to the filtration of melt water into the snow and its subsequent freezing. There is no near-surface melting in the interior regions of Antarctica. Therefore, snow compaction here is slower, which was shown by the work on creating the foundation for the Vostok new wintering complex [1]. Nevertheless, they also demonstrated the fundamental possibility of creating a landing site similar to Zenit.
The previously used technology for creating landing sites of this type required at least two years with the mandatory use of at least one summer season. The new technology made it possible to prepare the runway in less than a year, practically without using the summer melt.
Conclusion
From March to August 2022, the snow slab covering the landing site (runway and apron) with a total area of 350 thousand m2 and 100 to 120 cm high was completely formed. The top 30 cm layer of the pavement has a hardness of at least 1 MPa. The layer from 30 to 60 cm is at least 0.8 MPa, the bottom layer is at least 0.6 MPa. The created landing site was certified to accommodate wheeled aircraft.
The first Il-76TD-90VD aircraft of the Volga-Dnepr company was accommodated at the newly created Zenit landing site on 7 November 2022. Fig.7 shows a photograph of its first landing. The aircraft landed in normal mode. The track depth from the chassis wheels did not exceed 3 cm.

Fig.7. The first landing of the Il-76TD-90VD aircraft on the Zenit landing site
In the summer of 2022-2023, four Il-76TD-90VD flights were made, after which the Zenit landing site was closed for flights until the next season. In early October 2023, after thorough preparation and testing, which included GPR profiling, Il-76TD-90VD flights from Cape Town to Antarctica were resumed. The condition check showed that the snow material hardness increased by almost 20 % over the winter, which is consistent with the previously obtained results on the increase in the strength properties of compacted snow over time [1]. In the 2023/24 season, seven Il-76TD-90VD aircraft were accommodated at the Zenit landing site. All aviation operations proceeded in normal mode.
Thus, the new landing site for accommodating wheeled aircraft opens up new prospects for further exploration of Antarctica and the implementation of plans reflected in the Strategy for the Development of the Activities of the Russian Federation in Antarctica until 2030, approved by the Order of the Government of the Russian Federation of 21 August 2020 N 2143-r. The research provided new data and an in-depth understanding of the mechanisms for the formation of a snow-and-ice runway support base in Antarctica. The presented results are valuable and unique due to their possible practical use in solving similar issues, including in the oil-producing regions in the Far North.
Improving the unique methodology developed for preparing landing sites on snow surfaces to accommodate wheeled aircraft is an important task for strengthening our country’s position both in Antarctica and in the Arctic.
References
- Polyakov S.P., Popov S.V., Klepikov A.V. Main aspects of constructing snow foundations for the new buildings of the Russian Vostok Station, East Antarctica. Arctic and Antarctic Research. Vol. 70. N 4, p. 525-540. DOI: 10.30758/0555-2648-2024-70-4-525-540
- Shevyakova A.A., Shvaubauskas R.I. Design features of Antarctic research Stations. Iskusstvovedenie i dizain v sovremennom mire: traditsii i perspektivy: Sbornik materialov XV Vserossiiskoi nauchno-prakticheskoi konferentsii molodykh uchenykh. Tambov: Derzhavinskii, 2022, p. 75-78 (in Russian).
- Bolshunov A.V., Vasiliev N.I., Timofeev I.P. et al. Potential technological solution for sampling the bottom sediments of the subglacial lake Vostok: relevance and formulation of investigation goals. Journal of Mining Institute. Vol. 252, p. 779-787. DOI: 10.31897/PMI.2021.6.1
- Shishkin E.V., Bolshunov A.V., Timofeev I.P. et al. Model of a walking sampler for research of the bottom surface in the subglacial lake Vostok. Journal of Mining Institute. Vol. 257, p. 853-864. DOI: 10.31897/PMI.2022.53
- Bystramovich A.A., Klepikov A.V. On the development of the Russian Antarctic research. Abstracts of International Scientific Conference “Comprehensive Research of the Natural Environment of the Arctic and Antarctic”, 2-4 March 2020, Saint Petersburg, Russia. Saint Petersburg: Arctic and Antarctic Research Institute, 2020, p. 84-86 (in Russian).
- Oreshko E.I., Utkin D.A., Erasov V.S., Lyakhov A.A. Methods of measurement of hardness of materials (review). Proceedings of VIAM. N 1 (85), p. 101-117 (in Russian). DOI: 10.18577/2307-6046-2020-0-1-101-117
- White G., McCallum A. Review of ice and snow runway pavements. International Journal of Pavement Research and Technology. 2018. Vol. 11. Iss. 3, p. 311-320. DOI: 10.1016/j.ijprt.2017.11.002
- Barthelemy J.L. The Sea-Ice Runway Near McMurdo Station, Antarctica: A Problem of Logistics. The Sixth International Offshore and Polar Engineering Conference, 26-31 May 1996, Los Angeles, CA, USA. OnePetro, 1996. N ISOPE-I-96-150.
- Kozlov A.I., Logvin A.I., Feoktistova O.G. et al. Ice Structures for Airfield Construction. Springer, 2023. p. 118. DOI: 10.1007/978-981-19-6211-0
- Golynsky A.V., Golynsky D.A., Kiselev A.V., Masolov V.N. Russian geomagnetic investigations in Antarctica. Problems of Geography. Vol. 150, p. 175-197 (in Russian).
- Mikhalsky E.V., Leitchenkov G.L. Geological studies in the Antarctic: historical aspects and role of Russian investigation. Problems of Geography. Vol. 150, p. 150-174 (in Russian).
- Popov S. Fifty-five years of Russian radio-echo sounding investigations in Antarctica. Annals of Glaciology. 2020. Vol. 61. Iss. 81, p. 14-24. DOI: 10.1017/aog.2020.4
- Dirscherl M., Dietz A.J., Dech S., Kuenzer C. Remote sensing of ice motion in Antarctica – A review. Remote Sensing of Environment. 2020. Vol. 237. N 111595. DOI: 10.1016/j.rse.2019.111595
- Paterson W.S.B. The Physics of Glaciers. Moscow: Mir, 1984, p. 472 (in Russian).
- Florinsky I.V., Bliakharskii D.P. Detection of crevasses by geomorphometric treatment of data from unmanned aerial surveys. Remote Sensing Letters. 2019. Vol. 10. Iss. 4, p. 323-332. DOI: 10.1080/2150704X.2018.1552809
- Klyuchnikov G. Creation of high-strength snow airfields in the Arctic and Antarctic. Transport Rossiiskoi Federatsii. 2006. N 3, p. 34-36 (in Russian).
- Sharukha A.V., Kukina M.P., Egorov A.L. Prospects for the construction of airfields from snow mass in the Arctic. Nazemnye transportno-tekhnologicheskie kompleksy i sredstva: Materialy Mezhdunarodnoi nauchnoi-tekhnicheskoi konferentsii, 8 fevralya 2019, Tyumen, Rossiya. Tyumen: Tyumenskii industrialnyi universitet, 2019, p. 293-298 (in Russian).
- Polyakov S.P., Ivanov B.V., Klepikov A.V. et al. Physical and mechanical properties of snow-firn cover of the Vostok Station air strip, Ice and Snow. 2010. N 1 (109), p. 119-122 (in Russian).
- Poljakov S.P., Kharitonov V.V. Patent N 2459031 RF. Device to compact snow. Publ. 20.08.2012. Bul. N 23 (in Russian).
- Voitkovskii K.F. Mechanical properties of snow. Moscow: Nauka, 1977, p. 126 (in Russian).
- Arcone S.A., Delaney A.J. GPR images of hidden crevasses in Antarctica. 8th International Conference on Ground Penetrating Radar, 23-26 May 2000, Gold Coast, Australia. Society of Photo-Optical Instrumentation Engineers, 2000. Vol. 4084. p. 760-765. DOI: 10.1117/12.383512
- Popov S.V., Polyakov S.P., Pryakhin S.S. et al. Structure of the upper part of the glacier in the area of the designed snow-runway of Mirny Station, East Antarctica (based on the data compiled in 2014/15 field season). Earth’s Cryosphere. Vol. 21. N 1, p. 67-77. DOI: 10.21782/KZ1560-7496-2017-1(67-77)
- Ground Penetrating Radar: Theory and Applications. Edited by H.M.Jol. Elsevier, 2009, р. 544. DOI: 10.1016/b978-0-444-53348-7.x0001-4
- González-Velázquez J.L. A Practical Approach to Fracture Mechanics. Elsevier, 2021, p. 284. DOI: 10.1016/C2019-0-05011-X
- Jennings S.J.A., Hambrey M.J. Structures and Deformation in Glaciers and Ice Sheets. Reviews of Geophysics. 2021. Vol. 59. Iss. 3. N e2021RG000743. DOI: 10.1029/2021RG000743
- Taurisano A., Tronstad S., Brandt O., Kohler J. On the use of ground penetrating radar for detecting and reducing crevasse-hazard in Dronning Maud Land, Antarctica. Cold Regions Science and Technology. 2006. Vol. 45. Iss. 3, p. 166-177. DOI: 10.1016/j.coldregions.2006.03.005
- Tess X.H. Luo, Wallace W.L. Lai, Ray K.W. Chang, Goodman D. GPR imaging criteria. Journal of Applied Geophysics. 2019. Vol. 165, p. 37-48. DOI: 10.1016/j.jappgeo.2019.04.008
- Sukhanova A.A., Bantsev D.V., Shimanchuk E.V., Popov S.V. Glaciological surveys in the Antarctic Progress Station area during the 68th RAE season. Rossiiskie polyarnye issledovaniya. 2023. N 2, p. 20-22 (in Russian).
- van der Veen C.J. Crevasses on glaciers. Polar Geography. 1999. Vol. 23. Iss. 3, p. 213-245. DOI: 10.1080/10889379909377677
- Rousseau H., Gaume J., Blatny L., Lüthi M.P. Transition Between Mechanical and Geometric Controls in Glacier Crevassing Processes. Geophysical Research Letters. 2024. Vol. 51. Iss. 9. N e2024GL108206. DOI: 10.1029/2024GL108206
- Lenaerts J.T.M., Medley B., van den Broeke M.R., Wouters B. Observing and Modeling Ice Sheet Surface Mass Balance. Reviews of Geophysics. 2019. Vol. 57. Iss. 2, p. 376-420. DOI: 10.1029/2018RG000622
- Zaslavskii B.V. Brief course in strength of materials. Moscow: Mashinostroenie, 1986, p. 328 (in Russian).
- Gorunovich S.B. Multilayer beam strength calculation in transverse bending case by methods of material resistance. Mechanical engineers to XXI century. N 19, p. 246-251 (in Russian).