Tribodynamic aspects of the resource of electric submersible vane pumps for oil production
- 1 — Ph.D. Leading Researcher A.A.Blagonravov Institute of Mechanical Engineering of the Russian Academy of Sciences ▪ Orcid
- 2 — Ph.D., Dr.Sci. Peoples' Friendship University of Russia named after Patrice Lumumba ▪ Orcid
- 3 — Researcher A.A.Blagonravov Institute of Mechanical Engineering of the Russian Academy of Sciences ▪ Orcid
Abstract
The operation of electric submersible vane pumps for oil production is accompanied by the presence of solid particles, corrosive substances, asphalt-resin-paraffin deposits in the reservoir fluid, leading to changes in performance characteristics and equipment failures. The reduction of the resource as a result of this is accompanied by an increase in the costs of repair and replacement of equipment. The main processes that negatively affect the failure are the wear of the seals of the working stages, the pump plain bearings and vibration, the level of which can significantly exceed the initial level. A test bench and methodology for testing pump sections for wear in water with an abrasive and simultaneous registration of vibration characteristics have been developed. Two main forms of wear of radial seals have been identified – one-sided and equal-dimensional. The one-sided form of sleeve wear is caused by synchronous shaft precession, whereas the equal-dimensional one is an asynchronous precession, and the vibration level increases with increasing wear. The wear distribution of radial seals along the length of the pump correlates with the shape of the elastic shaft line. The wear of the axial seals does not significantly increase the vibration level. During wear the frequency spectrum of vibrations changes; there occurs a frequency that can serve as a diagnostic sign of ultimate wear of the pump. The calculated dependence of the vibration velocity on the wear of the radial seals of the working stages is obtained, which makes it possible to predict the onset of a failure of functioning.
Introduction
Centrifugal vane pumps are widely used in various fields: mining, oil production, water supply. Installations of downhole electric driven vane pumps (ESP) are the main means of mechanized oil production in Russia. The profitability of production depends largely on the reduction of costs during the operation of submersible equipment and its reliability [1]. To increase reliability and increase the resource, a number of measures are used: optimization of the selection of equipment for the well according to operating parameters [2]; development of new technological methods of reservoir stimulation [3, 4]; design and technological improvement [5]; new materials [6]; development of methods and technologies for combating asphalt-resin-paraffin deposits [7]; analysis of the physics of failures [8, 9].
Using repeated-short-term operation modes, an increased rotation speed, etc. leads to non-stationary modes that negatively affect the dynamic and tribological processes of destruction. The operation of the ESP in complicated conditions (mechanical impurities [10-12], high gas content [13], corrosion [14], salt deposition [15]) leads to vibration processes caused largely by wear of the tribological conjunctions and a change in the resulting gaps [16]. The mutual influence of vibration and wear is noted in [17-19]. Observations show that tribodynamic processes determine the conditions for the onset of parametric failure and failure of functioning according to the strength criterion [20, 21]. In general, this is typical for various types of centrifugal vane pumps, including ground [22] and pulp pumps [23].
The performance criteria vary for different types of pumps. For example, in [22], the operating time of a ground pump is estimated by the coefficient of technical condition, which is expressed in terms of the current root mean square (RMS) value of vibration velocity with a degree index equal to 1.1. The increase in vibration parameters is associated with the loss of mass of the impeller due to waterjet wear. An empirical formula for the dependence of vibration on the rotational speed on a stand with an unbalanced mass is obtained [23]. Erosion of equipment due to sand extracted together with oil and gas is a serious problem [24]. The effect of hydroabrasive (erosive) wear of impellers on the vibration of high-flow vane pumps is considered in [25]. In ESP, the abrasive wear of tribological conjunctions is of the greatest importance for the loss of operability [18, 21, 26].
Statement of the problem. ESP is an electromechanical rotary-type system with an uncharacteristic length-to-diameter ratio for most multistage rotary machines, in some cases higher than 500, and low transverse stiffness. The operation of installations in oil wells takes place at great depths in the conditions of information uncertainty in many parameters, including wear. Vibration is measured mainly at the base of the submersible electric motor, not on the body of the pump section, in which the wear of the tribological conjunction (TC). The main factors affecting the dynamic processes of rotary machines usually include: the imbalance of the rotating parts of the rotor [27]; dynamic stiffness [24]; the design of bearing assemblies, etc. Wear is not taken into account when studying the dynamic state of the ESP by calculation methods. Modeling [28] using the two-point “rotor – housing” model in liquids of different viscosities revealed the instability of the rotor already with a two-fold increase in the gap. The increased gaps in the labyrinth seals and journal bearings (JB) due to wear reduced all the stiffness and damping coefficients provided by the JB and seals, which led to stronger vibration. The test results of several sets of selected pumps showed [29] that due to non-linear relationships between damage processes the abrasive wear affects ESP systems in a non-deterministic way. It is noted [8, 30] that there are conditions for the occurrence of an oil vortex in JB, and there is also a precession of the shaft at the first natural frequency of the pump. An oil vortex is a nonlinear phenomenon that is not predicted by linear models of rotor dynamics. In a number of works, the influence of erosive wear on the failure of functioning is noted. This is especially true for vane pumps with high performance. As a result of erosive wear of impellers, the imbalance increases, dynamic processes occur and, as a consequence, the destruction of sealing units occurs [31]. In most works, there is no correct formulation of the problem of the effect of wear of the TC on the vibration characteristics of the installation. A wearable rotor system is geometrically non-linear. Linearization of the corresponding equations can lead to the loss of fundamental properties of the system under consideration [32]. Processing of statistical materials on failures, physical modeling indicate the relationship between the process of wear of TC and vibration.

Fig.1. The form of wear of the radial seals of the impellers of the stages: a – asymmetric wear of the hub; b – symmetrical wear of the hub and catastrophic wear of the axial seal
The main means of studying the processes of dynamics and wear of installations at present is the development of experimental equipment and testing. An experimental setup has been developed [12] for testing a 3-stage pump segment of an ESP assembly in a two-phase and three-phase flow to assess the effect of bearing wear on vibration. There are 50 accelerometers located on the surface of the housing to register transverse and longitudinal vibrations.
A feature of the ESP as a tribodynamic system are two pronounced forms of wear of the radial seals (RS) of the pump stages (PS), depending on the type of shaft rotation – synchronous (Fig.1, a) and asynchronous shaft precession (Fig.1, b) [18, 21, 26]. The form of wear of RS can serve as a diagnostic sign of the type of vibrations. The vibration of the ESP during the wear of the RS is significantly higher than is usually permissible for similar industrial equipment [16].
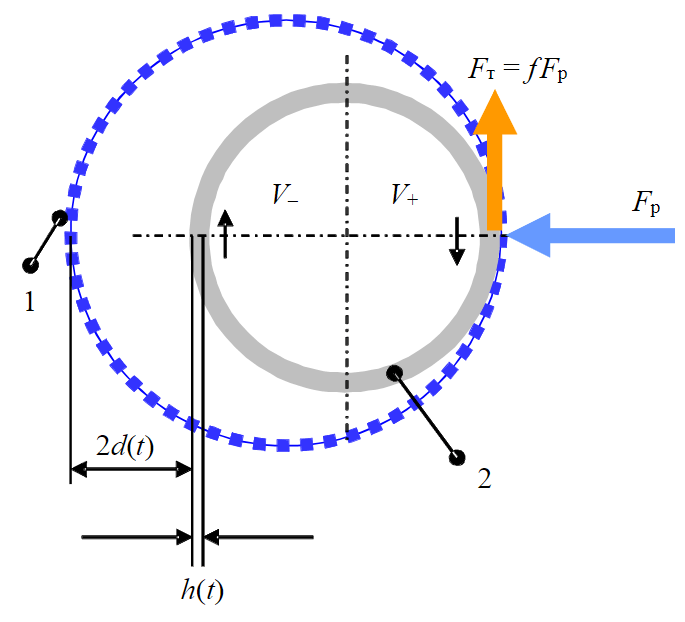
Fig.2. The contact diagram of the radial seal parts 1 – housing; 2 – support sleeve; h – wear value; f – coefficient of friction; t – time; Fr, Ft – radial and tangential force in contact, respectively; V – shaft rotation speed; d – clearance in the seal
Simulation of the wear of the dynamic system
The object of the study is the installation, the standard size of which is the most common in practice, 5-50 ESP: performance 50 m3/day, two pumping sections, electric motor power 32 kW. The finite element technology in the MSC/NASTRAN package was applied. When modeling using finite element technology, the fundamental difficulties arose due to the inability of existing numerical calculation methods to work with rotating deformable bodies. Adaptation of existing packages to this task is required. In this regard, the following calculation concept has been implemented. It is assumed that between the bushings of RS, when contacts occur, there is a large, but finite, contact stiffness. The gap between the shaft sleeve and the housing varies according to a certain wear pattern of the bushings. The simplest law of wear was adopted, which includes structural parameters depending on the properties of the contacting bodies. Power characteristics have the form of threshold functions. Calculations of the dynamic behavior of such a structure are a rather complex nonlinear problem, many parameters of which are set with great uncertainty. Therefore, the study of the dynamic behavior of the structure was carried out sequentially, starting with the determination of the dynamic characteristics of individual units, followed by their unification up to modeling the operation of the structure as a whole.
The basic idea consists in a sequential iterative process in which the gaps are changed in a fictitious time as a function of the distribution of radial reactions on the supports.
The contact of the shaft sleeve and the housing along the length of the pump occurs randomly at the initial period. In some TC there is a gap, in others there is a contact, depending on the distribution of the dimensions of the parts, the curvature of the housing, centrifugal forces, and other factors. We assume that the displacement of the sleeve occurs under the action of force Fr (Fig.2). In contact with the rotation of the sleeve, a friction force Ft occurs. The coefficient of friction f is assumed to be 0.02, characteristic of boundary friction. We believe that there is no wear during liquid friction. Fig.2 conventionally shows the relative position of the RS parts at their contact.

Fig.3. Stationary configuration of the pump shaft axis for both sections
When contact occurs between the surfaces, the center of the shaft is displaced by the value of the existing radial clearance u(t) = d(t). Considering that the wear processes proceed much slower than the characteristic dynamic changes in the system, we assume that the contact surfaces are locally cylindrical. The outer sleeve has a finite radial contact stiffness. There is some fictitious penetration of one surface into another by the value v(t). Since the stiffness of the contact is two orders of magnitude higher than the stiffness of the (local) shaft at a given point, the penetration is negligibly small compared to the gap. We accept the simplest wear model for the contact surfaces of a RS [33]. The value of the coefficient kF is taken from the experimental data when testing the considered materials for wear.
In accordance with this model, it is assumed that the wear of the contact surfaces depends on the change in the radial force in the contact. When calculating for fixed gap values, the iterations determine the stationary configuration of the dynamic system. The establishment process is fictitious, since rotation with a nominal angular velocity is considered without a transient acceleration of the entire installation:
where i is the number of radial seals in two sections; J is the iteration number.
In Fig.3, for example, the axis of the shafts of both sections of the pump is shown with an initial uniform distribution of gaps:
It is conditionally accepted that the upper section of the shaft has a rotation angle equal to zero. Dynamic additions associated with friction effects are small. It is assumed that the system has been operating in wear mode for some time . Then the gap in each node of contact interaction will increase by approximately the value
Since during the entire contact the forces of interaction are distributed unevenly between the bushings, a redistribution of forces and clearances occurs, which is called the evolution of the system. Depending on the parameters of the system, in particular, on the distribution of imbalances and the wear resistance of individual bushings, various laws of the evolution of gaps and the stress-strain state are obtained, which should be understood and analyzed in a statistical sense.
The calculation results showed that the design features of the installation significantly affect the dynamic state. In the region of 10-13 Hz, there are 10-11 natural oscillation frequencies. Operating modes correspond to work in “supercritical” conditions, far in the field of nonlinear dynamics, where properties other than those of linear ideal models become important. The most unfavorable case of loading is the location of imbalances over a significant length of the pumping section in one plane. In the process of wear of RS the synchronous and asynchronous shaft precession is realized. Asynchronous precession frequency is 9.51 Hz. Synchronous precession occurs under the action of a circulating force, the direction of which relative to the shaft does not change during rotation and is associated with a regular arrangement of the centers of mass of the impellers in approximately the same direction and with a low level of damping in the system. The simulation results under the selected assumptions make it possible to determine the stresses in the body parts of the installation depending on the gap in the seals and explain the destruction of the body parts (“flight”), but in real conditions the form of wear differs from the accepted one. Therefore, to obtain a more complete picture, the experimental studies are needed.
Methodology of experimental research
The length of the entire installation can reach 40 m [1, 8], and it is not possible to test it as an assembly. For this purpose most researchers use pump assemblies including several PS [17, 20]. To simulate the vibrational phenomena of rotor systems, it is necessary to ensure the similarity of the model and the full-scale object, expressed in the ratio between the critical rotation frequency and the operating frequency [32]. As a test object, pump sections with a length of 3-5 m and a flow rate of 25-500 m3/day were used, which of all units of the installation are most susceptible to wear, since they operate in an abrasive-containing formation fluid. Their length is sufficient to investigate the main vibration modes of the installation. For experimental studies, a horizontal stand with a model liquid (water + abrasive) was developed (Fig.4). The experiments were carried out with a rotation frequency of 2970 rpm.
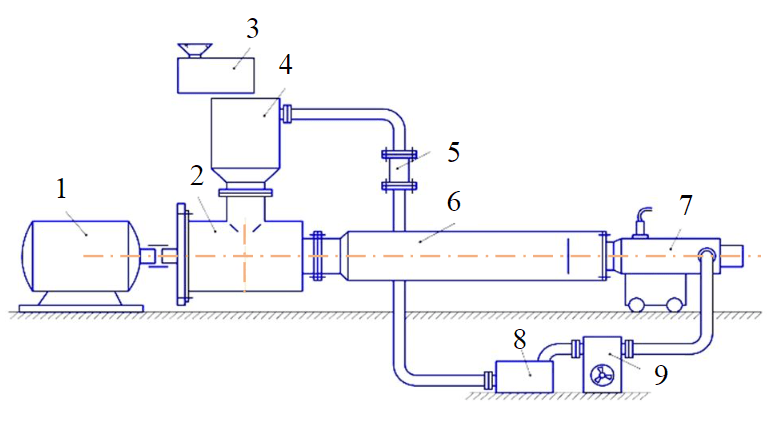
Fig.4. Diagram of the horizontal stand 1 – electric motor; 2 – input module; 3 – abrasive dispenser; 4 – mixing tank; 5 – flow meter block; 6 – pumping section; 7 – output module; 8 – abrasive separator; 9 – heat exchanger
The stand is equipped with sensors and devices for measuring flow, pressure, temperature, and moment characteristics. To measure the moment of resistance, the drive electric motor is made in the form of a motor scale. The test procedure assumed the operation of the stand for a certain time with the measurement of the vibration velocity after 1 hour. At the end of the experiment, the pump sections was disassembled, the parts were measured and the amount of wear of each PS was determined. Quartz sand with a size of 200-300 µm and an average concentration of 1 % by weight was used as an abrasive. The choice of the size of the abrasive particles due to several circumstances. From the preliminary experiments with PS, fine particles smaller than 50 µm have a small abrasive effect. Large particles larger than 500 µm do not fall into the friction zone, since the diametric gap of the RS is less than 300 µm. In real wells, there are wide fractions, including selected sizes.
Before the experiment, eight piezoelectric accelerometers of the vibrator M601A01 of the company PCB Piezotronics type were fixed with clamps on the PS case at equal distances or four pairs of accelerometers at an angle of 90° to each other in the vertical and horizontal planes. The signals from the sensors were processed using a National Instruments measuring complex using PXI technology in a real-time system. The complex included: an SCXI-1531 module for simultaneous signal pickup on eight channels, a PXI-6070 module for digitizing the signals with a sampling rate of 1.25 Ms/s. The built-in PXI-8156B/333RT real-time controller was used to receive, process, and present the measurement results.
The vibration measurement technique included three stages:
- measurement of the natural frequencies of the rotor oscillations (shaft + impellers) in various support conditions based on the spectral analysis of the measured signal when the vibration is excited by impact;
- measurement of the vibration velocity of the pump sections with various variations of the shaft support, in air and in water;
- measurement of vibration characteristics in the process of wear of the pump sections.
After testing for wear, the pump sections were disassembled and the change in the dimensions of each seal of the working stage and bearings was measured.
The results of experimental studies
As an object of study, we used the most common pump section standard size 5-50 with a flow rate of 50 m3/day in a nominal mode and a nominal length of 4 m. Measurements of the natural oscillation frequencies of the pump sections rotor showed that the first three natural frequencies when the shaft is supported by three JB are equal to 5.6; 8.5; 19.8 Hz. Thus, in this case, the rotor operates in the supercritical region. With an increase in the number of JB to five, the third mode of the rotor and the second mode of the pump section have almost the same values – 29.9 Hz, which can cause resonance phenomena. Therefore, the number of bearings affects the values of the natural frequencies of the rotor. In reality, the vibration pattern is more complicated, since the shaft is supported by the housing by means of the RS in a random way.
There is a slight difference in the magnitude of the vibration of the pump sections in the horizontal and vertical planes: the first natural frequency has a value of 9.8 Hz for the horizontal arrangement of the sensors and 9.3 Hz for the vertical one. The presence of water in the PS slightly changes the natural frequency of the rotor from 9.8 to 8.9 Hz due to the effect of the added mass. The natural frequency of the rotor oscillations increases when using polyamide as the material of the impellers.

Fig.5. Measurements results of the section vibration: a – at the beginning of the experiment; b – after 250 min
At the third stage, the pump section was tested for wear with simultaneous measurement of vibration characteristics. The spectrum of vibrations of the new section has natural frequencies, a revolving frequency of ~50 Hz, its harmonics, as well as high-frequency vibrations. At the initial stage, the contribution of natural frequencies of the PS is insignificant or indistinguishable, the revolving frequency prevails.

Fig.6. Graph of changes along the length of the section: vibration velocity (a); wear of RS (b) 1 – hub wear; 2 – hole wear; 3 – total wear; 4 – the assumed shape of the elastic line of the shaft during rotation
The most interesting is the changed spectrum of oscillations during the experiment. From the comparison of the spectra at the beginning of the experiment (Fig.5, a) and in the middle (Fig.5, b), it can be seen that as a result of wear of the RS a frequency of 25 Hz appeared, which has a significant amplitude level exceeding the level of the first and second natural frequencies. After the bench stops, this frequency is absent when the oscillations of the pump sections are excited by the impact. An intermediate disassembly of the pump section after 250 min of the experiment showed that the wear of the RS has an asymmetric shape (see Fig.1, a), which may indicate a synchronous precession of the shaft.
The appearance of this frequency in a worn-out pump can be explained either by an increase in self-oscillations due to an increase in the gap due to wear under the action of gravity, centrifugal forces and friction forces, or by a coincidence of the natural oscillation frequencies of the rotor and the section housing. At the end, after 702 min of the experiment, two new peaks appeared at frequencies of 22.2 and 27.7 Hz instead of a peak at a frequency of about 25 Hz. A frequency of ~25 Hz can be considered as a diagnostic sign of the onset of wear of the RS of a certain value. In immersion measuring systems with a vibration channel, it is possible to determine the occurrence of this frequency, which indicates an increase in dynamics due to wear. A similar nature of the change in the oscillation frequency was revealed when testing the pump assembly at a frequency of 3600 rpm [9]. In the process of wear, a subharmonic peak of 45 Hz appeared in the frequency spectrum that consisted mainly of a rotation frequency of 60 Hz and harmonics.
When testing pump sections with PS made of powder steels, which have a significantly smaller imbalance than PS made of cast iron, an interesting feature was revealed in the nature of the change in the wear of along the RS along the length of the section (Fig.6). In the oscillation node (point A) there is the minimum level of vibration and minimum wear were found. Maximum vibration levels and wear values were recorded at points A1 and A2. The right end bearing had little wear. The shape of the wear of the impeller hub and the guide vane hole is uniform around the circumference, which indicates asynchronous shaft precession.
Based on the test results of pump sections with PS that differ in the magnitude of the initial unbalance, one can notice a certain similarity in the shape of the elastic line of the shaft and changes in wear along the length of the section. With a certain amount of wear of the RS, the shaft loses stability under the action of centrifugal forces and torque and rotates in a deformed state around an imaginary axis passing through the centers of the bearings. There is a further evolution of wear. The deformed shaft makes its motion with “frozen” values of deformations, and, consequently, stresses. This movement in a fixed coordinate system looks like elastic oscillations, in fact it does not contain any elastic oscillations – the deformed shaft rotates around the line of bearings as an absolute rigid body. Radial forces from the rotor are transferred to the pump housing, creating, in certain conditions, the stress of destruction of the end parts.
In addition to wear, the shape of the shaft deformation is also influenced by the number of wear-resistant intermediate bearings, edge effects expressed in fastening conditions, the curvature of the well, etc. The length of the section is of fundamental importance. When testing a pump assembly of several stages, the shaft is “rigid”. Its natural frequency is much higher than the rotation frequency, the similarity criterion of the model sample and the natural product is violated [17]. Often a short shaft has a conical precession during rotation, which is not observed in real operation. When testing short pump assemblies, the wear pattern of RS is almost monotonous with an increase in wear from the pump outlet to the inlet [11].

Fig.7. The dependence of the vibration velocity of the section on the value of radial seals wear
In addition to radial, PS have axial seals. The effect of wear of axial seals on pump vibration was investigated during the operation of pump sections in the left zone of the pressure-flow characteristics at a liquid flow rate less than the nominal. Due to the increase in axial force, the axial seals were completely worn out (wear of more than 2 mm), the disks were also worn out, which is characterized as catastrophic wear (see Fig.1, b). The vibration level at the same time increased slightly, up to 12 mm/s. For comparison, when the RS were worn by 1 mm, the vibration increased to 40 mm/s. The initial vibration level of the new sections was in the range of 2.25-3.9 mm/s.
Tests of several dozens of pump sections with a capacity of 25 to 500 m3/day, of different sizes and designs in terms of wear resistance, made it possible to obtain a generalized dependence of the magnitude of transverse vibration (rms value), which characterizes bending vibrations, on the wear of RS (Fig.7). The test results are confirmed by operation (point on the graph). In the range of average wear up to 1.6 mm along the length of the section, the obtained values are approximated by a linear dependence
where V is the root-mean-square value of the vibration velocity, mm/s; h is the average value of wear of RS, mm.
Radial seal clearance includes initial clearance and wear. In the initial state, the pump sections had a vibration velocity level of ~5.5 mm/s. From the simulation of the dynamic system ESP, which included a submersible electric motor, two pump sections and hydraulic protection, it follows that the kinetics of vibration velocity changes in a more complex way – exponentially. The linear approximation of the experimental results is valid with sufficient accuracy only in the wear range up to 1.6 mm and for reservoir fluid with a high water content (up to 80-90 %), which is an oil-water emulsion, which is typical for wells in Western Siberia. The viscosity of such an emulsion is close to that of water. With an increase in the viscosity of the emulsion at 50-80 % of water, the amplitude of oscillations of the dynamic system decreases, which should be taken into account when determining the limit state. For comparison, the graph (Fig.7) shows a linear dependence of the vibration of mainline pumping units with a rigid rotor on the wear of thrust bearings [34]. The maximum allowable values of vibration velocity in this case do not exceed 11 mm/s according to technical requirements.
Conclusions
- A correlation between the change in wear of radial seals along the length of the pump section and the shape of the elastic shaft line has been established. The rotation of the shaft occurs in the form of synchronous and asynchronous precession.
- The calculated dependence of the vibration velocity on the wear of the radial seals of the working stages is obtained, which makes it possible to predict the onset of failure of functioning in flooded wells. Oil-water emulsions reduce the amplitude of vibrations.
- It is shown that with a certain amount of wear of the radial seals of a horizontally located pump section, bending vibrations occur with a frequency of ~25 Hz, which can be used as a diagnostic sign of the extreme wear of the installation.
- The wear of radial seals and bearings has a decisive influence on the dynamic state of the pumping section. With the wear of 1 mm, the vibration velocity increases 10 times relative to the initial value. The wear of the axial seals has a negligible effect.
References
- Takacs G. Electrical Submersible Pumps Manual: Design, Operations, and Maintenance. Second Edition. Houston: Gulf Professional Publishing, 2018, p. 574.
- Donskoy Yu.A., Sabirov A.A., Ivanovskiy V.N. et al. The Autotechnolog Software and Intellectual Devices On It's Basis. Oil and Gas Territory. N 9-10, p. 20-26 (in Russian).
- Drozdov A. N., Gorelkina Е. I. (2022). Development of a pump-ejector system for SWAG injection into reservoir using associated petroleum gas from the annulus space of production wells. Journal of Mining Institute. Vol. 254, p. 191-201. DOI: 10.31897/PMI.2022.34
- Gorelkina E.I. Investigation of gas bubble coalescence suppression and its effect on the operation of a booster pump as part of a pump-ejector system when pumping water-gas mixtures. SOCAR Proceedings. N 2, p. 33-47 (in Russian). DOI: 10.5510/OGP2022SI200743
- Yakimov S.B. On the Perspectives of Radial Stabilized Compression Electric Submersible Pumps Application for Wells Operation Efficiency Improvement at AB Group of the Samotlor Field Formations. OilandGasTerritory. N 7-8, p. 78-86 (in Russian).
- Krasnyy V.A., Maksarov V.V., Olt J. The use of polymer composite materials in the friction nodes downhole oil pumps. Journal of Mining Institute. Vol. 211, p. 71-79 (in Russian).
- Rogachev M.K., Aleksandrov A.N. Justification of a comprehensive technology for preventing the formation of asphalt-resin-paraffin deposits during the production of highlyparaffinic oil by electric submersible pumps from multiformation deposits. Journal of Mining Institute. Vol. 250, p. 596-605. DOI: 10.31897/PMI.2021.4.13
- Minette R.S., SilvaNeto S.F., Vaz L.A., Monteiro U.A. Experimental modal analysis of electrical submersible pumps. Ocean Engineering. 2016. Vol. 124, p. 168-179. DOI: 1016/j.oceaneng.2016.07.054
- Patil A., Delgado A., Yi Chen et al. Mechanical Reliability of Electrical Submersible Pumps. China Academic Journal Electronic Pablishing Hous. 2018. Vol. 60. N 5, p. 69-77. DOI: 10.16492/j.fjjs.2018.05.0010
- Haiwen Zhu, Jianjun Zhu, Zulin Zhou et al. Experimental Study of Sand Erosion in Multistage Electrical Submersible Pump ESP: Performance Degradation, Wear and Vibration. International Petroleum Technology Conference, 26-28 March 2019, Beijing, China. 2019. N IPTC-19264-MS. DOI: 10.2523/IPTC-19264-MS
- Haiwen Zhu, Jianjun Zhu, Risa Rutter, Hong-Quan Zhang. Experimental Study on Deteriorated Performance, Vibration, and Geometry Changes of an Electrical Submersible Pump (EPS) under Sand Water Flow Condition. Journal of Energy Resources Technology. 2021. Vol. 143. Iss. 8. N 082104. DOI: 10.1115/1.4048863
- Changrui Bai, Dezhi Zheng, Hure R. et al. The Impact of Journal Bearing Wear on an Electric Submersible Pump in Two-Phase and Three-Phase Flow. Journal of Tribology. 2019. Vol. 141. Iss. 5. N 051702. DOI: 10.1115/1.4042773
- Drozdov A.N. Stand Investigations of ESP's and Gas Separator's Characteristics on GasLiquid Mixtures with Different Values of Free-Gas Volume, Intake Pressure, Foaminess and Viscosity of Liquid. SPE Annual Technical Conference and Exhibition, 19-22 September 2010, Florence, Italy. 2010. N SPE-134198-MS. DOI: 10.2118/134198-MS
- Saleh T.A., Sahi S.H., Mohamed L.S. Corrosion of Electrical Submersible Pumps (ESP) In South Rumaila Oil Field. Iraqi Journal of Chemical and Petroleum Engineering. 2015. Vol. 16. N 1, p. 63-69.
- Ibragimov N.G., Khafizov A.R., Shaidakov V.V. et al. Complications in oil production. Ufa: Izd-vo Monografiya, 2003, p. 302 (in Russian).
- Shamkov A., Gorlov A. Sand Influence Analysis on ESP Operation in Salym Petroleum Development. Effective Methods and Procedures for Sand Protection. SPE Russian Petroleum Technology Conference, 22-24 October 2019, Moscow, Russia. 2019. OnePetro, 2019. N SPE-196821-MS. DOI: 10.2118/196821-MS
- Bocharnikov V.F., Petroukhin S.V., Petroukhin V.V. Experimental Researches of Distribution of Vibration on Length of the Case of Module-Section Submerged Centrifugal Electric Pumps with It Is Frequency – Adjustable A Drive. Oil Industry. N 8, p. 80-82 (in Russian).
- Smirnov N.I., Grigoryan E., Smirnov N.N. Wear and Vibration of the Pumping Sections Yetcn. Burenie & neft. N 2, p. 52-56 (in Russian).
- Smirnov N.I., Grigoryan E., Smirnov N.N. Study of the Characteristics of the Vibration Condition of Pump Sections. Burenie & neft. N 1, p. 23-27 (in Russian).
- Paharukov Yu.V., Bocharnikov V.F., Petruhin S.V., Petruhin V.V. Results of Experimental Re-searches of Radial Vibration at Use Of Shock-Absorbers of Steps Submerged the Electrical Submersible Pump. OilIndustry. N 1, p. 99-101 (in Russian).
- Smirnov N.I. Tribological dynamics of centrifugal pumps. Friction & Lubrication in Machines and Mechanisms. N 2, p. 32-36 (in Russian).
- Aleksandrov V.I., Sobota I. Vibrodiagnostics of the technical state slurry pumps. Journal of Mining Institute. Vol. 218, p. 242-250 (in Russian).
- Ovchinnikov N.P., Portnyagina V.V., Dambuev B.I. Specifying the technical state limit value of the pump pulp without disassembling. Journal of Mining Institute. Vol. 241, p. 53-57. DOI: 10.31897/PMI.2020.1.53
- Parsi M., Najmi K., Najafifard F. et al. A comprehensive review of solid particle erosion modeling for oil and gas wells and pipelines applications. Journal of Natural Gas Science and Engineering. 2014. Vol. 21, p. 850-873. DOI: 10.1016/j.jngse.2014.10.001
- Gülich J.F. Centrifugal Pumps. Berlin: Springer, 2008, p. 957.
- Smirnov N.I., Smirnov N.N., Progega M.V. Tribological aspects of rotary pumps reliability. Friction & Lubrication in Machines and Mechanisms. N 3, p. 32-37 (in Russian).
- Marscher W.D. How vibration levels are related to tribological failure in rotating machinery. MFPT 59 Conference, 19-21 April 2005, Virginia Beach, USA. 2005, p. 11.
- Childs D.W., Norrbin C.S., Phillips S. A lateral rotordynamics primer on electric submersible pumps (ESPs) for deep subsea applications. Proceedings of the 43rd Turbomachinery & 30th Pump Users Symposia (Pump & Turbo 2014), 23-25 September, Houston, USA. 2014. DOI: 10.21423/R15K8Q
- Beck D., Nowitzki W., Shrum Electric Submersible Pump ESP Vibration Characteristics Under Wear Conditions. SPE Gulf Coast Section Electric Submersible Pumps Symposium, 13-17 May 2019, Texas, USA. 2019. OnePetro, 2019. N SPE-194388-MS. DOI: 10.2118/194388-MS
- Salas K., Delgado A., Van Dam J. et al. Rotordynamic Characterization of an Electric Submersible Pump Motor. Society of Petroleum Engineers (SPE), ESP Workshop, 22-26 April 2013, Houston, USA.
- Haiwen Zhu, Jianjun Zhu, Risa Rutter, Hong-Quan Zhang. A Numerical Study on Erosion Model Selection and Effect of Pump Type and Sand Characters in Electrical Submersible Pumps by Sandy Flow. Journal of Energy Resources Technology. 2019. Vol. 141. Iss. 12. N 122004. DOI: 10.1115/1.4044941
- Ganiev R.F. Nonlinear resonances and catastrophes. Reliability, safety, and quietness. Moscow; Izhevsk: Regulyarnaya i khaoticheskaya dinamika, 2013, p. 592 (in Russian).
- Silaev B.M. Tribology of machine parts in low-viscosity lubricating media. Samara: Izd-vo Samarskogo gosudarstvennogo aerokosmicheskogo universiteta, 2008, p. 264 (in Russian).
- Belkin A.P. Modeling of the vibration state and forecasting of the residual life of the electric motors of the main pumping units: Avtoref. dis. … kand. tekh. nauk. Ufa: IPEER, 2010, p. 26 (in Russian).